FRACAS:het geheim van betere activabetrouwbaarheid
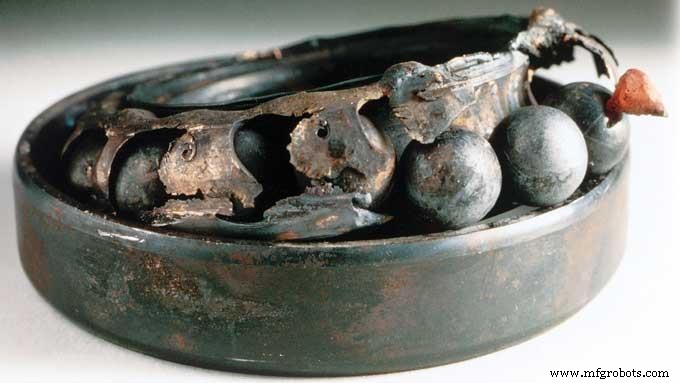
In de kern gaat betrouwbaarheidsengineering over het voorspellen en voorkomen van storingen. Door alle manieren op te sommen waarop een systeem kan falen, wordt het mogelijk om alle manieren uit te werken waarop een storing kan worden opgespoord, uitgesteld of gestopt voordat het zelfs maar echt kan beginnen.
Het storingsrapportage-, analyse- en corrigerende actiesysteem (FRACAS) is een georganiseerde methode om de mogelijke middelen voor het falen van activa te sorteren en terug te werken naar alle mogelijke hoofdoorzaken. Het eindproduct fungeert als een kaart voor alle manieren waarop dingen kunnen mislukken, waardoor een plan kan worden opgesteld om problemen op te lossen wanneer ze zich voordoen, en voor het elimineren van chronische problemen vanaf het begin.
Het FRACAS-proces zou inzicht moeten bieden in de kriticiteit van componenten in het hele systeem en moet gebruik maken van ervaren planners, onderhouders en operators bij het opsommen van alle talloze manieren waarop een machine faalt.
Mislukking
Falen kan het best worden gedefinieerd als elke andere bedrijfstoestand dan ideaal. De meesten zouden falen beschouwen als een toestand van totale onbruikbaarheid, maar werken in een gedegradeerde toestand moet toch als een mislukking worden beschouwd. Ik was onlangs in een fabriek waar een machine was omgebouwd om met een hogere snelheid te werken dan oorspronkelijk was ontworpen. De operators en onderhoudsbedrijven in dat specifieke deel van de fabriek beschouwden het als een groot succes dat hun systeem zo goed werkte, maar uiteindelijk was er geen rekening gehouden met de overvoeding en liep het product eruit bij de volgende pompbeurt punt, waardoor een grote stapel afval ontstaat. Falen kan dus iets zijn dat beter werkt dan het hoort, maar ook slechter werkt.
De beste manier om verder te gaan is om alle manieren op te sommen waarop een machine kan falen door deze op te splitsen in kleinere subcomponenten die ofwel zouden worden bewerkt of vervangen als onderdeel van reparatie. Het subcomponentniveau kan helemaal naar beneden gaan tot bouten en moeren of tot "kant-en-klare" apparatuur die gemakkelijk kan worden vervangen, zoals een kleine motor of sensor. Het is erg handig om toegang te hebben tot het materiaalinventarisatieprogramma dat uw site gebruikt.
Dit kan al gekoppeld zijn aan het in gebruik zijnde CMMS of kan een apart systeem zijn. Het gebruik van het materiaalinventarisatieprogramma zal later tijdens het gedeelte met corrigerende maatregelen opnieuw nuttig zijn om te bepalen hoeveel reserveonderdelen en verbruiksartikelen in voorraad moeten worden gehouden.
Rapportage
Een ander woord dat hier goed zou passen, is opnemen. De slogan van mijn eerste onderhoudsmanager was "je moet het opschrijven". Het is belangrijk om alles op een gestructureerde, georganiseerde manier te loggen. Er zijn veel software-opties die kunnen worden gekocht om op dit gebied te helpen, maar voor een kleinere fabriek of systeem kunt u overwegen om Projecten of een spreadsheet te gebruiken. Het hebben van een gestructureerde cascade van subcomponenten en storingstypen is belangrijk omdat patronen en herhalingsmethoden van falen zullen optreden. Theoretisch zijn er oneindig veel manieren waarop iets kan mislukken, maar in de praktijk zul je veel van dezelfde dingen steeds weer tegenkomen.
Een andere manier van rapporteren is het gebruik van een oorzakenkaart voor elk systeem. Dit is een meer grafische benadering en kan moeilijker elektronisch worden vastgelegd zonder enige ervaring in dat proces, maar in veel gevallen zorgt het voor een beter begrip van wat er gebeurt door anderen buiten het FRACAS-proces. Een eenvoudige versie zou een basistekening of afbeelding zijn van het systeem of de machine in kwestie met tekstvakken die uit de punten van storing komen. Deze dozen kunnen zich vervolgens vertakken in andere oorzaken of gevolgen, waardoor een soort wolk van storingswijzen ontstaat rond de apparatuur in het midden.
Analyse
Doordat alle faalmethoden op een georganiseerde manier zijn opgesomd, kan een team van materiedeskundigen nu trends beoordelen en opmerken. Door een ervaren groep de gegevens te laten beoordelen, kan ook een behoorlijke hoeveelheid geschiedenis in het spel komen. Elke fabriek heeft ten minste één machine met een bewezen staat van storing en het hebben van een team van mensen die het meest bekend zijn met dit soort incidenten is van vitaal belang voor een succesvolle analysefase.
Daarbij is het ook belangrijk om onderscheid te maken tussen chronische storingen en eenmalige gebeurtenissen. Er kan een neiging zijn om zich te concentreren op opmerkelijke of bijzonder catastrofale gebeurtenissen en te proberen te voorkomen dat dezelfde specifieke reeks omstandigheden zich opnieuw voordoen. Hoewel het belangrijk is om alle mogelijkheden te overwegen, is materiële mislukking soms zo'n buitenissige gebeurtenis dat er geen praktische les te leren valt.
Parallel aan de faalanalyse is het uitvoeren van een kriticiteitsbeoordeling. In combinatie met de gestructureerde cascade van apparatuur, subcomponenten en storingsmodi, zal een kritische beoordeling helpen bepalen hoe gedetailleerd het analyseteam moet gaan bij het toewijzen van corrigerende maatregelen. Kritiek moet worden gedefinieerd door een combinatie van prijs voor reparatie of vervanging, arbeidskosten voor reparatie of vervanging en het effect van uitvaltijd op het systeem of de fabriek als geheel.
In de lean/Six Sigma-wereld is er een sterke focus geweest op het verminderen van de voorraad en het hebben van just-in-time leveringen van producten of materiaal om te besparen op opslagkosten. Door een kritische analyse op uw systeem toe te passen, kunt u zien welke machines of componenten kant-en-klare vervangingen op de plank nodig hebben en welke het zich kunnen veroorloven om direct te worden besteld. Dit helpt ook om te beslissen hoe lang een falende machine in die staat kan blijven werken.
Overweeg een machine waarvoor het hele systeem moet worden afgesloten, maar die in twee dagen kan worden gerepareerd met een onderdeel al bij de hand, in plaats van datzelfde systeem tegen het einde van de maand voor 90 procent te laten werken terwijl u wacht op een vervangende machine die kan arriveren. ogenblikkelijk worden ingewisseld. Negentig procent efficiëntie lijkt de beste keuze, maar het volledige gebruik van het systeem gedurende 28/30 dagen is meer dan 93 procent, een niet onbelangrijke toename van de fabrieksoutput voor die periode. Een grondige beoordeling van de kriticiteit helpt bij het opsommen van dit soort acties die moeten worden afgewogen tegen de uiteindelijke lijst met corrigerende acties.
Corrigerende actie
De eenvoudigste corrigerende actie om voor elke storing op te sommen, is het vervangen van het defecte onderdeel. Iets ingewikkelder is om het te repareren. Maak een lijst van alle mogelijke corrigerende maatregelen voor elke storing, maar voeg ook een bedrag in dollars toe dat rekening houdt met zowel het onderdeel als de arbeid die nodig is om te repareren of te vervangen. Vooraf geschreven werkorders kunnen voor beide gevallen worden geschreven en in het CMMS worden opgeslagen voor gebruik in het geval dat er een storing optreedt.
Een mogelijke corrigerende actie die kan worden vermeld, kan "run to failure" zijn. Er is geen echte one-size-fits-all oplossing om elke faalmodus te voorkomen of te corrigeren, maar door het Pareto-principe toe te passen, ontstaat er een eenvoudig te beheren lijst met activiteiten en acties die snel kunnen worden toegepast. Met andere woorden, het zal waarschijnlijk blijken dat de meeste chronische problemen die een systeem beïnvloeden, afkomstig zijn uit een kleinere, beheersbare lijst met fouten en kunnen worden gecorrigeerd door een vergelijkbare beheersbare lijst met vervolgacties.
Systeem
Het belangrijkste onderdeel van FRACAS is dat het als systeem wordt onderhouden. Herhaalbaarheid van dit proces is van vitaal belang voor het toevoegen van extra systemen, nieuwe apparatuur, opkomende technologieën en zelfs nieuw personeel in de fabriek. Zorg voor een plan om de effectiviteit van corrigerende maatregelen te beoordelen en om nieuwe leden aan de analysegroep toe te voegen om een licht te laten schijnen op elk deel van de fabriek dat geen duidelijke verbetering in uptime lijkt te vertonen.
Een ander systematisch onderdeel van dit proces ligt in het opleiden van andere leden van de plant. Dit vergroot het eigenaarschap van het proces voor personeel dat niet betrokken is bij de eerste analyse en kan een cultuuropbouwend evenement zijn. Door anderen vroeg in het proces te trainen, kunnen ze zien dat het proces onbevooroordeeld is en ook openstaat voor het opnemen van hun ideeën.
Falen is willekeurig, maar kan in de meeste gevallen worden opgespoord, vertraagd of helemaal voorkomen met een systematische aanpak. Het verzamelen en beoordelen van gegevens door ervaren fabriekspersoneel is van cruciaal belang, evenals het berekenen van een bedrag in dollars voor elke mogelijke actie of uitkomst om het uiteindelijke corrigerende proces te begeleiden. Door deze methoden in de loop van de tijd methodisch toe te passen en de basisprincipes van het proces aan andere teamleden aan te leren, zal de cultuur helpen verbeteren en de algehele betrouwbaarheid van activa vergroten. Onthoud dat je een FRACAS wilt hebben, geen fracas.
Onderhoud en reparatie van apparatuur
- Het pleidooi voor mobiel onderhoud:Fiix stopt bij de podcast Asset Reliability @ Work
- FRACAS:hoe je apparatuurstoringen tot je vriend kunt maken
- Wat is de rol van de betrouwbaarheidsingenieur?
- De nr. 1 sleutel tot betrouwbaarheidssucces
- HR:de ontbrekende schakel naar betrouwbaarheid
- De niet-technische kant van betrouwbaarheid
- Het belang van trends in de betrouwbaarheid van elektromotoren
- De waarde van betrouwbaarheid als een service
- Het geheime systeem dat de hele IoT-industrie zal ondersteunen
- Hoe verbetert IIoT de levensvatbaarheid van een asset monitoring systeem?
- De voordelen van hydraulische systemen