Hoe we 3D-printen gebruikten om de klepontwerpen en het schema voor onze mechanische noodventilator te valideren
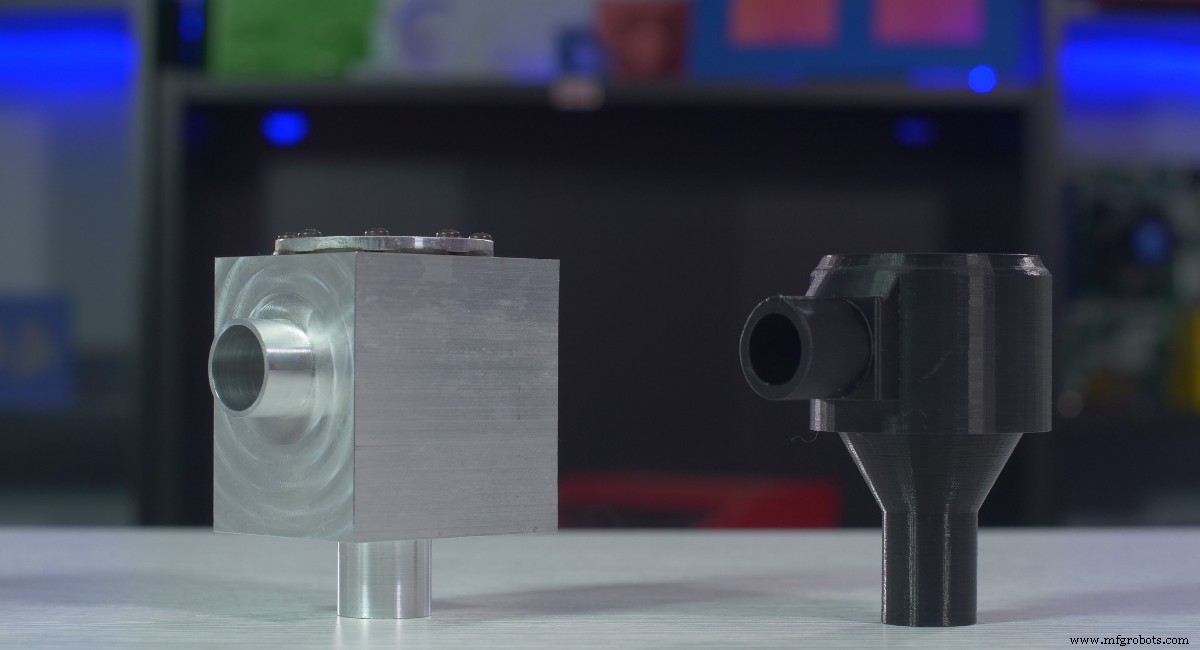
Toen de COVID-19-pandemie begin 2020 een ernstig probleem werd in Noord-Amerika, waren er veel onbekenden. Hoe werd COVID-19 verspreid? Wat waren de symptomen? Kon COVID-19 worden verspreid als er geen symptomen waren? Waren er blijvende nawerkingen, of spin-off ziektes? Hoe ver en hoe snel zou de verspreiding plaatsvinden? Zou het dragen van mondkapjes helpen om de verspreiding tegen te gaan? Wanneer zou een vaccin klaar zijn?
Van al die onbekenden was echter één feit zeker:if de pandemie zich verspreidde en ernstige gevallen exponentieel groeiden, zouden ventilatoren cruciaal zijn om patiënten goed te behandelen. Nog een zekerheid:veel landen, waaronder de eigen thuisbasis van Protocase in Canada, hadden niet voldoende beademingsapparatuur voor een dergelijk scenario.
In de vroege stadia van de COVID-19-pandemie vond de federale overheid Protocase essentieel, vanwege ons klantenbestand van organisaties die actief zijn in innovatie, geneeskunde, ruimtevaart en defensie. Maar naast open en klaar om op maat gemaakte onderdelen en behuizingen van onze klanten te maken, zodat ze konden blijven innoveren en nieuwe technologie konden ontwikkelen, wilde Team Protocase ook zijn steentje bijdragen om de COVID-19-pandemie het hoofd te bieden. Het project? Bouw een functionele, draagbare ventilator dat snel kon worden vervaardigd en geassembleerd.
De uitdaging
Na contact te hebben gehad met een groep medische professionals, waaronder spoedeisende artsen, ademhalingstherapeuten en anderen, om de criteria voor een functionele ventilator te bespreken, heeft ons onderzoeks- en ontwikkelingsteam het pneumatische systeem in kaart gebracht. Een cruciaal onderdeel van het ontwerp van een ventilator zijn de kleppen, die samen met aftakleidingen een circuit vormen voor in- en uitademing. Het team moest drie veelvoorkomende typen kleppen :een terugslagklep, een regelbare drukterugslagklep en een solenoïde.
Eén probleem:er was uitzonderlijk veel vraag naar de kant-en-klare kleppen.
“Iedereen was een beetje aan het springen op de versies van deze onderdelen die geschikt zouden zijn voor ventilatoren en alle verschillende oplossingen voor de pandemie. Er waren enkele onderbrekingen in de toeleveringsketen", zegt Justin Lewis, Mechanical Engineer in het R&D-team van Protocase. “Nadat we een tijdje hadden geworsteld met het bestellen van de kleppen die we nodig hadden, besloten we er zelf een te maken. De uiteindelijk resulterende afsluiters zijn in wezen de versie van die onderdelen die we snel konden maken met wat we in huis hadden zonder te maken te hebben met doorlooptijden.”
De ontwerpen voor de kleppen kwamen snel samen, aangezien het algemene ontwerp (en de dwingende criteria van de functie van een klep) al goed uiteengezet en vastgesteld was.
"Kortom, we kregen een lijst met criteria waaraan de artsen en ademtherapeuten waarmee we overlegden moesten voldoen", zegt Jordan Rose, R&D Mechanical Engineer bij Protocase. “Op basis van het pneumatische ontwerp van het hele systeem kun je afleiden bij welke druk deze dingen moeten werken. Dat is de andere helft van de informatie die we nodig hadden om verder te gaan. We hebben gekeken naar hoe een terugslagklep werkt en bij welke druk en stroomsnelheden deze dingen moeten werken, met behulp van de wiskunde die we op de technische school zouden hebben geleerd."
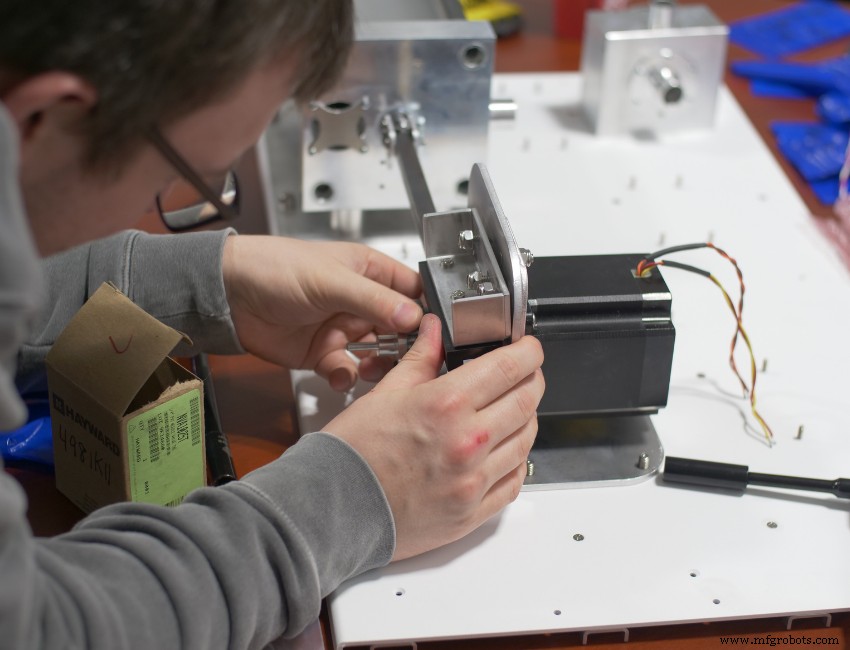
“Het is industrieel Lego. Het gaat erom het totaalbeeld te zien, allemaal opgebouwd uit deze basisblokken", legt Lewis uit. "Dit zijn de basisblokken - we hoeven ze alleen maar te bouwen en ze in de juiste volgorde aan elkaar te klikken, zodat ze allemaal het doel bereiken."
Met de klepontwerpen goed ingeburgerd, evenals de druk- en stroomvereisten, ging het team aan de slag met het bouwen van de eerste prototypen. Voor die taak was 3D-printen de logische eerste stap, omdat het de afmetingen zou valideren en berekeningen voor druk en stroomsnelheden zou verifiëren.
"Omdat het bewerkingsproces aanzienlijk langer is, is het belangrijk om eerst de onderdelen 3D te printen om de specificaties te bevestigen", zegt Rose.
"3D-printen valideerde het hele schema", zegt Lewis. "Het stelde ons in staat om alles samen te voegen en te zeggen:'Oké, dit werkt', voordat we alle tijd en geld investeerden in het bouwen van de juiste machinale onderdelen."
Het team deed een paar iteraties van het 3D-printen van de terugslagklep en de verstelbare terugslagklep, in een poging het ontwerp zoveel mogelijk te stroomlijnen en ervoor te zorgen dat het goed functioneerde. In een vroeg ontwerp van de verstelbare terugslagklep had de klep bijvoorbeeld een cirkel en een naaf aan één kant.
“De reden dat ik dat deed was om te kijken wat voor ondersteuning er nodig was voor die circulaire baas. Omdat je het anders misschien eronder moet ondersteunen, "zegt Rose. “Ik wilde proberen eventuele oppervlakteproblemen te voorkomen, zodat de slang in het pneumatische systeem goed zou passen. Uiteindelijk gingen we naar een rechte buisvorm die prima werkte.”
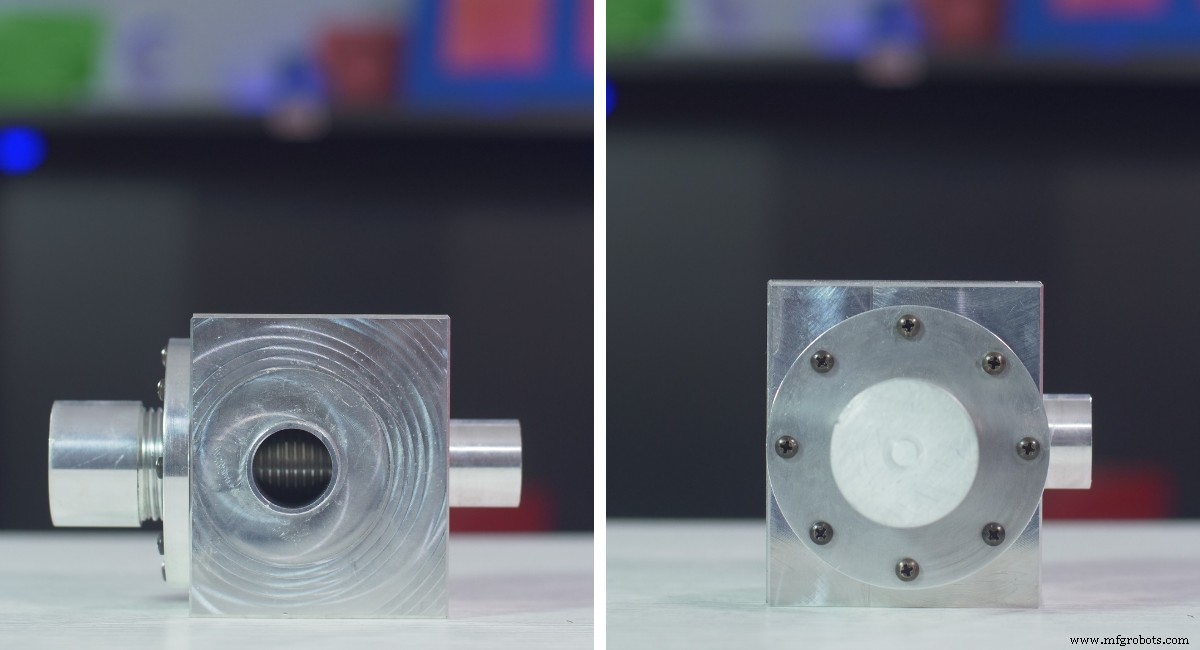
"De algemene theorie was vanaf het begin goed, het ging meer om het correct afdichten ervan, ervoor zorgen dat we de juiste veren hadden", zegt Lewis.
De enige klep die niet 3D-geprint was als een eerste prototype, was de pneumatische solenoïde - en terecht.
"Van de buitenkant ziet het er eenvoudig uit, omdat het gewoon een groot blok metaal is, maar aan de binnenkant zijn er veel verschillende kamers", legt Rose uit. "Het is niet iets dat haalbaar zou zijn om in 3D te printen."
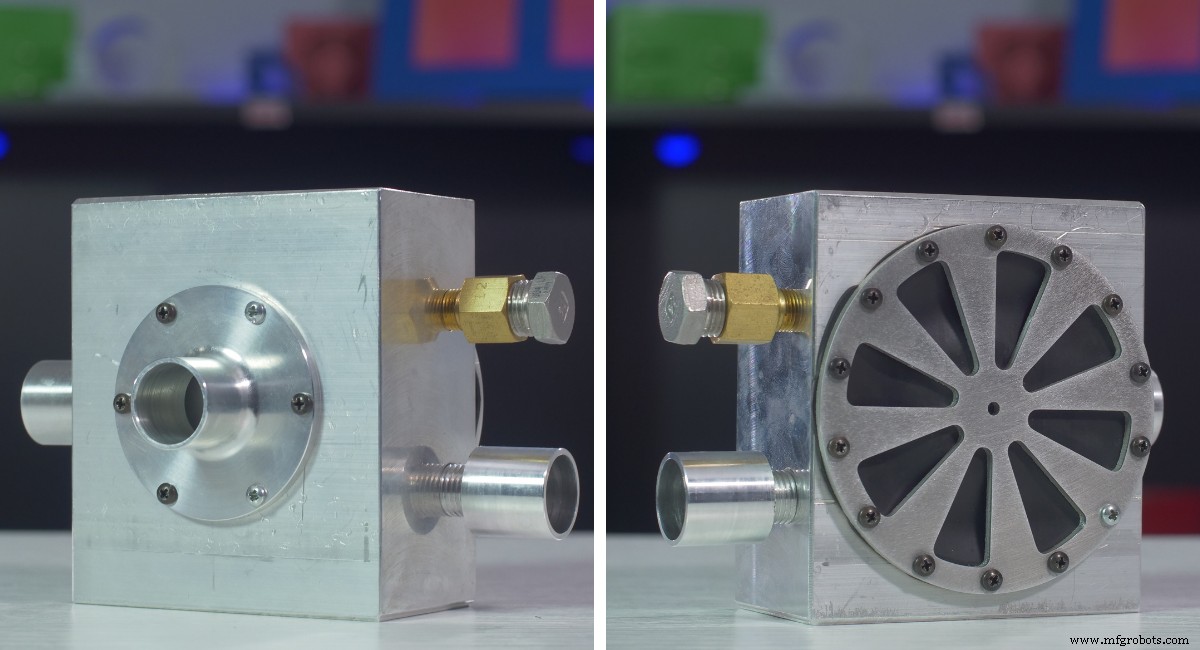
"Met 3D-printen kan het moeilijker zijn om een asafdichting op dat soort materiaal te krijgen", zegt Lewis. "Door de solenoïde te frezen, konden we deze tot een mooie afwerking machinaal bewerken en er een passende as in plaatsen zodat alles goed afdicht."
De pneumatische solenoïde omvat elk aspect van de aangepaste productie van Protocase, met CNC-draaibankonderdelen, gefreesde onderdelen, plaatwerkonderdelen, een 3D-geprint onderdeel en pakkingmateriaal. In plaats van het rubberen pakkingmateriaal in een typische pakking te snijden, sneed het team het rubber in een cirkel met behulp van een CNC-router om een terugslagklepblaas te maken.
Terugkijken – en vooruitkijken
Uiteindelijk was het enorm voordelig om eerst met 3D-printen te beginnen om ervoor te zorgen dat de industriële Lego-stukken in elkaar zouden passen en zouden functioneren zoals het schema, zonder waardevolle, cruciale tijd in beslag te nemen door CNC-bewerking van alle onderdelen.
“Het is gewoon fijn om te weten dat je op de goede weg bent. Je hebt het schema, je legt het allemaal bij elkaar en zegt dan:'Oh wacht, dit is allemaal verkeerd ingedeeld.' Er waren tijden dat we aanpassingen maakten aan hoe het hele systeem was ingedeeld', zegt Lewis. "Je wilt geen stapel geld en tijd besteden aan machinaal bewerkte blokken om dat te doen. Deze 3D-geprinte onderdelen lekten een beetje, maar we wisten dat het totale systeem werkte, zodat we vol vertrouwen konden investeren in de volgende fase.”
Zelfs de definitieve versie van de CNC-gefreesde kleppen is misschien niet de meest gestroomlijnde en misschien onhandig in vergelijking met de kant-en-klare tegenhangers op de markt, maar daar is een reden voor, zegt Rose.
"We hebben ze zo ontworpen dat ze ruim binnen onze mogelijkheden liggen, want als we er ooit 2000 zouden moeten bewerken, zouden we ze snel kunnen doen", legt hij uit. "We hebben actief geprobeerd om niets bijzonders te ontwerpen, of de grenzen van onze bewerking te verleggen."

Zoals bij elk prototype of elke ontwikkeling van een product, kan het nuttig zijn om na te denken over wat goed ging en wat beter kan. Al met al waren zowel Rose als Lewis het erover eens dat het project op een solide basis bleef dankzij de behendige productie die binnen handbereik was om lay-outs te testen en specificaties te bevestigen zonder enige vertraging.
Terugkijkend zien ze echter wel de voordelen van een elektrisch systeem voor de ventilator. Een systeem met een elektrisch systeem kan worden ingeschakeld wanneer u het nodig heeft en uitgeschakeld wanneer u het nodig hebt met behulp van de software. Een pneumatisch systeem daarentegen heeft een vacuümsysteem dat moeilijk kan zijn.
"Deze pneumatische solenoïde is als het bespelen van een muziekinstrument", legt Lewis uit. "Het is geweldig als je het kunt laten afstemmen op de weg naar buiten, maar als er iets verandert, wil je niet dat er iemand in het ziekenhuis moet zijn die echt ingewikkeld weet hoe de machine moet werken. U wilt idealiter iemand die de knop gemakkelijk kan verstellen. In termen van iets in huis dat we snel konden doen, is het systeem dat we hebben ontworpen en gebouwd geweldig, maar wat we sinds maart hebben geleerd, is dat de toevoerleidingen enigszins weer normaal zijn geworden en dat we misschien met een elektrisch systeem hadden kunnen gaan .”
"Destijds was dat het enige dat we niet konden krijgen - een elektrische solenoïde", voegt Rose toe. “Iedereen was in paniek. Ze zijn nu veel gemakkelijker te vinden.
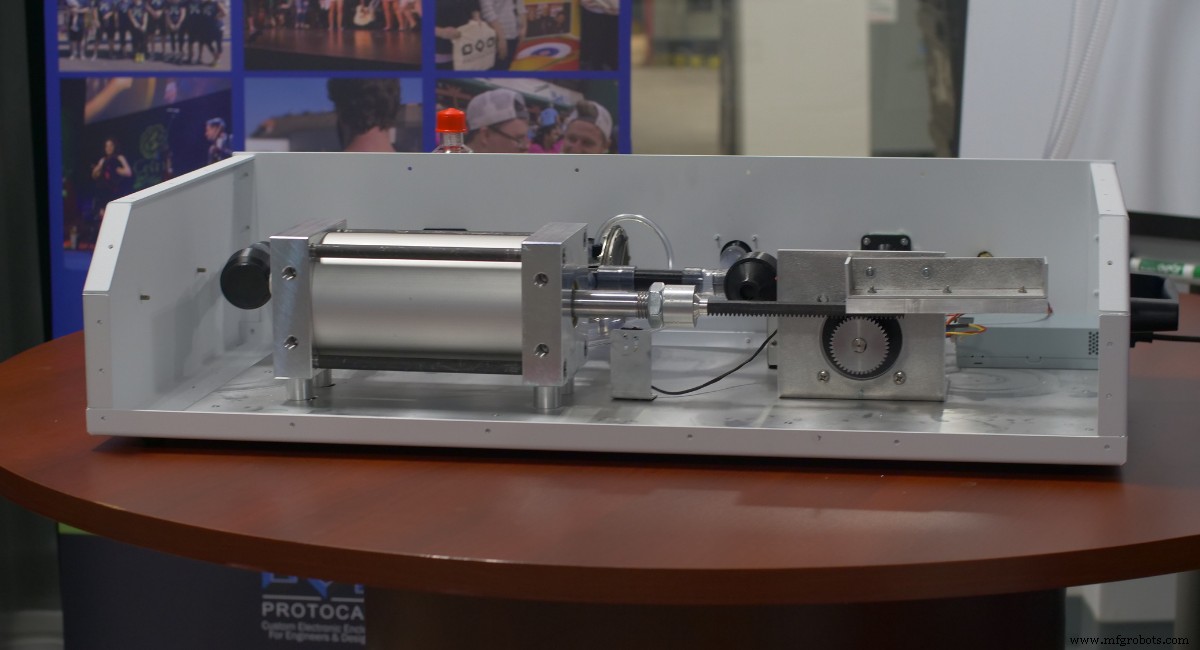
Als we naar het grote geheel kijken, heeft het beademingsproject, inclusief het ontwerp en de fabricage van de drie kleppen, mede vorm gegeven aan het werk van het R&D-team van Protocase.
“Toen dit project ter sprake kwam, bleek het om een wereldwijde noodsituatie te gaan. We lieten al het andere vallen en we kwamen allemaal bij elkaar", zegt Rose. "Wat we ons realiseerden tijdens het doen van dit project, dat we onze andere projecten konden stoppen om ons op slechts een of twee dingen te concentreren, en dingen echt te beperken."
In plaats van zich te dun te verspreiden of geïsoleerd te raken van elkaars werk, richt de Research &Development-groep zich nu op het functioneren als een team.
"We hebben specifieke doelen waar we allemaal samen aan kunnen werken en we kunnen onze middelen bundelen", legt Lewis uit. "Het heeft gewoon de manier veranderd waarop iedereen aan projecten werkt, we behandelen elk project nu bijna als een soort noodsituatie. Dit project was de katalysator voor veel verbeteringen binnen onze R&D-afdeling.”
Industriële technologie
- De koudeketen voorbereiden op de eisen van COVID-19-vaccins
- Hoe Fine Art Logistics de kunstmarkt voorgoed verandert
- Hoe u zich kunt voorbereiden op de volgende verstoring van de toeleveringsketen
- Hoe zorg je voor paraatheid bij noodsituaties in het magazijn
- Wat zijn de voordelen van 3D-printen voor metaalbewerkers?
- Vier nieuwe kansen voor de aluminiumindustrie
- Wat is AutoCAD? Hoe het werkt en waarvoor het wordt gebruikt
- Enkele van de meetinstrumenten die nodig zijn voor de bewerking van mechanische onderdelen
- Hoe 3D-printen wordt gebruikt in de matrijsindustrie
- De zaak voor 3D-printen in de productie
- Wat zijn RFID-tags? Leer hoe RFID-tags werken, waarvoor ze worden gebruikt en enkele van de nadelen van RFID-technologie