In de robotachtige loopgraven
Verhalen van fabrikanten die automatisering hebben geïmplementeerd:waarom ze het deden, wat de resultaten waren en advies aan anderen die een nieuwe droid overwegen
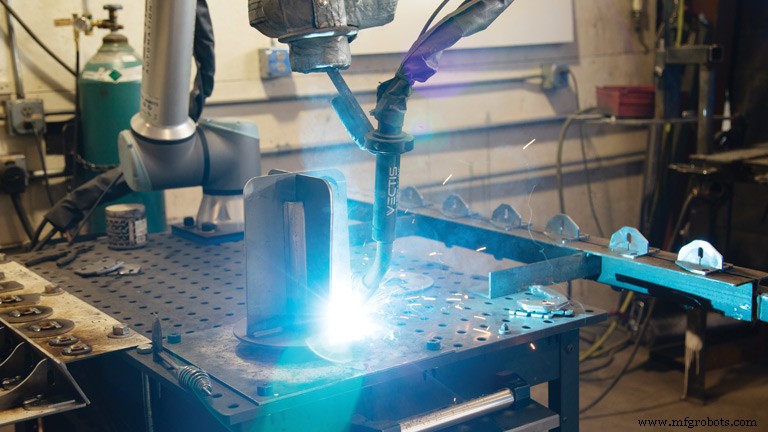
Op zoek naar een nieuwe pick-up truck? Wat dacht je van een vervanging voor die vermoeide trollingmotor, of proberen te beslissen of het Thaise restaurant dat vorige maand is geopend goed is? In deze en talloze andere koopsituaties is het beste advies vaak om met klanten te praten die die producten hebben gekocht of van die twijfelachtige keuken hebben gegeten. Wat waren hun ervaringen? Zijn ze goed geholpen en voldeed het product aan hun eisen? Misschien wel het belangrijkste, zouden ze het opnieuw kopen?
Hetzelfde geldt voor robots. Vooral robotten. Dat komt omdat, gezien het aanhoudende tekort aan arbeidskrachten en de hoopvolle heropleving van reshoring-inspanningen in de VS en elders, robotautomatisering de sleutel is tot de groei en verhoogde efficiëntie van de maakindustrie. Nergens is dit meer waar dan bij kleine bedrijven zoals MT Solar Co. uit Charlo, Mont., waar eigenaar en president Travis Jordan een snelle groei heeft doorgemaakt sinds de oprichting van het bedrijf. Jordan wendde zich onlangs tot collaboratieve robots (cobots) als oplossing. Het bleek dat zijn beslissing een game-changer was.
"We zijn ongeveer 12 jaar geleden begonnen met algemene productie en fabricage, en zijn eind 2014 overgestapt op de zonne-energie-industrie met de lancering van onze eerste vlaggenschipproductlijn", zei Jordan. “We hadden kort daarvoor geïnvesteerd in een CNC-plasmatafel, dus onze workflow bestond toen uit het automatisch snijden van de afzonderlijke stukken en vervolgens met de hand aan elkaar lassen. Die aanpak werkte prima tot een paar jaar geleden, toen de markt voor zonne-energie echt van de grond kwam en we snel moesten groeien. Maar zoals de meeste winkels tegenwoordig, hadden we moeite om geschoolde arbeidskrachten te vinden. We besloten robotica te beschouwen als een manier om de doorvoer van sommige van onze herhaalde laswerkzaamheden te vergroten.”
Ondanks de snelle groei en de torenhoge vraag, wijst Jordan er snel op dat zijn productieteam gefocust is op Lean manufacturing-principes en daarom zijn aanpasbare montagesystemen in kleine batches op een just-in-time basis maakt. Zijn zoektocht naar een schaalbare maar flexibele oplossing leidde hem uiteindelijk naar Ann Arbor, in Michigan gevestigde Universal Robots USA Inc. (UR), waar hij een systeem vond dat kon voldoen aan de behoeften van het bedrijf met een laag volume en een hoge mix. De Cobot Welding Tool van UR-partner Vectis Automation in Loveland, Colorado, is uitgerust met een UR10e-cobot, een geïntegreerde hanger en "DIY-programmeersoftware", en is bevestigd aan een draagbare modulaire opspantafel met ingebouwde voeding van Rhino Cart.
Jordan zei dat ze tijdens hun zoektocht de banden op een aantal hoogwaardige systemen hebben geschopt, maar de meeste waren gericht op hogere productievolumes, niet op de tientallen stuks en kleinere partijgroottes die MT Solar moest verwerken, vaak op uurbasis. De meeste hadden ook veiligheidskooien nodig, een uitgave die Jordan zo mogelijk wilde vermijden. "Onze opspanbehoeften zijn ook veel eenvoudiger dan bij een conventionele robot," zei hij. “Als een onderdeel niet past en met de hand moet worden gelast, kan iemand er gewoon in springen en het op dezelfde tafel doen, waarna de cobot weer aan het werk gaat. Dat is niet mogelijk als je te maken hebt met allerlei afschermende en draaiende draaitafels zoals je ziet bij de meeste geautomatiseerde lascellen.”
Misschien is zijn enige spijt dat hij er geen twee heeft gekocht. "Later dit jaar zijn we van plan om nog een cobot binnen te halen, zodat we er een kunnen wijden aan het opzetten en programmeren en een tweede aan de productie", zegt Jordan. “Dat stelt ons in staat om een continue flow te realiseren, zoals nodig in een Lean-omgeving.”

Tight Quarters
Steve Dillon deelt een soortgelijk cobot-succesverhaal, zij het met een heel andere grondgedachte. Als vice-president van CDP Diamond Products in Livonia, Michigan, behoort hij tot de derde generatie gereedschapsmakers in de Dillon-familie. Maar toen hij zijn broers voorstelde te investeren in robots om hun acht FANUC draadvonkmachines (WEDM) de klok rond te laten draaien, waren ze sceptisch, maar stemden ermee in om het eens te proberen.
Zoals de naam al doet vermoeden, ontwerpt en produceert CDP Diamond Products een breed scala aan op maat gemaakte diamantslijpgereedschappen. Een stap in het proces omvat het laden van het gesoldeerde gereedschap in een draaitafel en het draadsnijden van het gewenste profiel op elke fluit, een bewerking die doorgaans ongeveer drie uur duurt. Om de uptime van de machine te maximaliseren en de doorvoer te verhogen, rustte Dillon de meeste WEDM's uit met een paar draaitafels, maar dit gaf hem slechts zes uur onbeheerd machinaal bewerken. Hij nam contact op met zijn FANUC-distributeur, Methods Machine Tools Inc. in Sudbury, Massachusetts, voor advies.
"In het begin stelden ze meer draaitafels voor, maar die dingen zijn waanzinnig duur, en ik wist dat ik waarschijnlijk een robot zou kunnen krijgen voor ongeveer dezelfde prijs," zei Dillon. “Het probleem was de vloeroppervlakte. Ik had kamers met temperatuurregeling rond de draadmachines gebouwd om de nauwkeurigheid van de onderdelen te maximaliseren, en dat betekende dat er geen ruimte was voor bewaking en kooien en zo. Gelukkig had FANUC rond diezelfde tijd net hun serie collaboratieve robots geïntroduceerd.”
Net als de lasoplossing van MT Solar, voorzag Methods CDP Diamond Products van een verplaatsbare standaard met vakken voor twee dozijn HSK 63 gereedschapshouders. Hieraan hebben ze een FANUC CRX collaboratieve robot bevestigd, die voldoende armbereik heeft om twee machines te onderhouden. Afhankelijk van de gereedschapsmix kunnen Dillon en zijn team nu twee of meer ploegen volledig onbeheerd draaien, en als een operator moet ingrijpen en aan een van de machines moet werken, kan de andere doorgaan zoals het was.
"Het is zo moeilijk om mensen te vinden dat ik, toen mijn zoon op de middelbare school zat, hem vroeg om 's nachts binnen te komen om de machines te voeden", zei Dillon. 'Laatst belde hij van de universiteit, zich afvragend of we werk voor hem hadden. Ik moest hem zeggen:'Sorry, zoon. Je bent vervangen door een robot. Ga nu studeren.'”
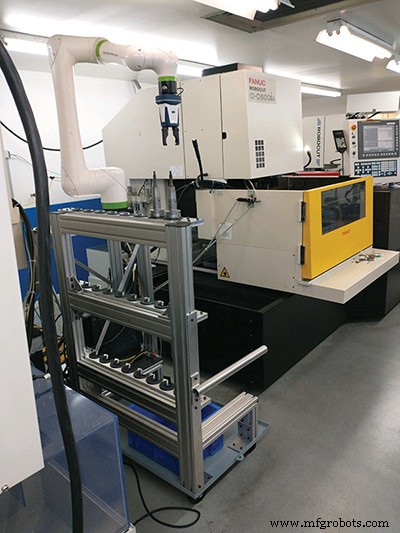
Kooiwedstrijd
Ron Douglas, eigenaar en president van Associated MetalCast LLC uit Oxford, Ala., heeft geen probleem met kooien. Zijn bedrijf installeerde enkele jaren geleden een FANUC-robot op een van zijn Okuma Genos L300 CNC-draaibanken en Douglas is sindsdien een groot voorstander van automatisering geworden. Het bedrijf heeft nu drie van dergelijke cellen en is van plan er in de zomer nog twee te implementeren. Aangezien dit zogenaamde "industriële robots" zijn en niet samenwerken, zijn er kooien nodig om mensen te beschermen, hoewel één cel slechts een lichtgordijn gebruikt. Hoe dan ook, ze hebben allemaal de taak om onderdelen te laden en te lossen, ze schoon te maken in de wasstations van de cellen en in één geval 100 procent inspectie uit te voeren op een geïntegreerde CMM.
Associated MetalCast giet of smeedt geen onderdelen. Douglas richtte het bedrijf op in 1998 en koos de naam vanwege een nauwe samenwerking met gieterijen in het hele land. Het biedt precisiebewerking, schilderen, warmtebehandeling, assemblage en andere processen met toegevoegde waarde voor een reeks industrieën, waaronder landbouw, zwaar materieel en infrastructuur. En hoewel veel van de afgewerkte onderdelen beginnen als giet- of smeedwerk, bewerken Associated MetalCast en zijn 96 medewerkers ook een groot deel van het stafmateriaal en plaatmateriaal, waardoor het zijn klanten een "one-source" productieoplossing biedt.
Op de vraag waarom hij begon met automatiseren, was het antwoord van Douglas niet verrassend. “Gezien onze uitdagingen bij het vinden van geschoolde arbeidskrachten hier in Alabama, zal automatisering een zeer groot deel van onze toekomst blijven uitmaken. Het verhoogt niet alleen de efficiëntie, de verwerkingscapaciteit en de consistentie van de onderdelen, maar het geeft onze medewerkers ook de vrijheid om zich bezig te houden met interessantere taken dan het verzorgen van machines. Dit alles is erg belangrijk in de huidige verspanende wereld.”
Hij merkte nog een belangrijk punt op, namelijk om teamleden aan boord te krijgen bij het starten van een automatiseringsproject. "Verrassend genoeg was dat in het begin best een uitdaging", zei Douglas. “Ik had moeite om de mensen van engineering en productie te overtuigen, omdat het iets nieuws voor hen was en volledig buiten hun bereik. Maar toen ze de resultaten begonnen te zien en zich realiseerden dat automatisering de juiste stap voorwaarts was voor het bedrijf, stonden ze erachter. Tussen hun steun en die van onze robotica-integrator is de uitrol zeer succesvol geweest.”
Breekt met traditie
Duane Manth, algemeen directeur van Manth Manufacturing Co., Tonawanda, N.Y., heeft een lange geschiedenis met robots. In de afgelopen twee decennia heeft hij geïnvesteerd in verschillende vormen van automatisering, waaronder verschillende Wasino-gang-stijl CNC-draaibanken met geïntegreerde portaalladers die hij gebruikte voor enkele van de hogere volumecomponenten van de winkel. En hoewel die machines goed werk voor hem hebben gedaan, wilde hij een robot die flexibeler is dan die twee- en drieassige portalen, en kan worden gebruikt in een cellulaire configuratie met menselijke werknemers.

"In onze 40-jarige geschiedenis hebben we altijd geprobeerd om concurrerender te worden, en waar nodig heeft automatisering daar een rol in gespeeld", zegt Manth. “Dus toen mijn productiemanager Mike Rex en ik begonnen te praten over het verhogen van de doorvoer op een van onze handmatige productiecellen, gebeurde het toeval dat de verkoper van Absolute Machine Tools een paar dagen eerder was gestopt en een flyer voor de OB7 had afgegeven. . Iemand legde het op mijn bureau, en ik bleef het lezen en naar het prijskaartje kijken en al snel belde ik hem en zei:'Vertel me hier meer over.'”
De OB7 is een collaboratieve robot van Productive Robotics Inc., een in Carpinteria, Californië gebaseerde spin-off van ZBE Inc., die robotcamerasystemen voor de filmindustrie bouwt. Het maakte Manth niet uit hoe het 12-jarige bedrijf begon - het enige waar hij om gaf was het verlagen van de arbeidskosten in zijn driepersoonsbewerkingscel. Hij kocht twee OB7's en gebruikte ze om de CNC-draaibanken van de cel te onderhouden, en liet één persoon achter om de cilindrische slijpmachine te bedienen en de cobots in de gaten te houden.
De oplossing was zo effectief dat Rex al snel op zoek ging naar andere OB7-toepassingen en deze uiteindelijk aan het werk zette met hoon- en brootsmachines. "We hebben ook een OB7 die een cilindrische molen in een andere cel voedt, waardoor een van de operators aan andere dingen kan werken", zei Manth. "Ze zijn een enorm succes geweest."
Het voortdurende streven van hem en zijn team naar meer efficiëntie heeft geleid tot de overname van Manth Manufacturing eind vorig jaar door zijn grootste klant, Dynabrade USA uit Clarence, N.Y. in de mogelijkheden van Manth, terwijl we tegelijkertijd werken aan ons eigen automatiseringsaanbod”, zegt bedrijfsdirecteur Mike Buffamonti. “Dynabrade ziet veel mogelijkheden voor robotmateriaalverwijdering en oppervlakteconditionering, en is daarom gaan samenwerken met verschillende cobotfabrikanten om proof-of-concept-oplossingen aan onze klanten te bieden. We zijn erg enthousiast over deze volgende stap in onze evolutie.”
Prioriteiten instellen
Niets van dit alles komt als een verrassing voor Douglas Bingham, senior directeur productietechnologie bij Honeywell International Inc.'s Phoenix-faciliteit. Met vijf divisies, meer dan 100.000 werknemers wereldwijd en een omzet van $ 34 miljard vorig jaar, heeft de in Charlotte, N.C. gevestigde fabrikant uitgebreide ervaring met automatisering. Of het nu gaat om geautomatiseerde rookdetectorlijnen in Triëst, Italië, of robotlascellen in Mexicali, Mexico, dit Fortune 100-bedrijf heeft automatiseringstechnologie geïmplementeerd op honderden productielocaties.
Wat er ontbrak, zei Bingham, is een alomvattende, bedrijfsbrede strategie. “Elke site heeft het in de loop der jaren op zich genomen om alles te automatiseren waarvan ze zagen dat het een redelijk rendement op de investering zou opleveren. En hoewel dat in de meeste gevallen goede resultaten heeft opgeleverd, kan het ook veel efficiënter en kosteneffectiever zijn. Daarom hebben we het Automation Center of Excellence (COE)-team opgericht, dat bestaat uit een toegewijde automatiseringsleider van elk bedrijf.
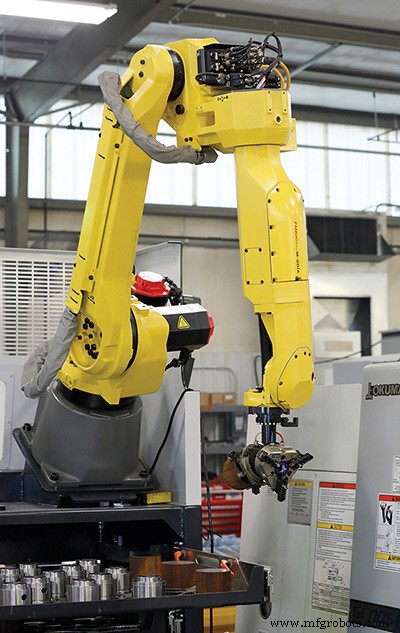
In plaats van het wiel opnieuw uit te vinden telkens wanneer een nieuwe fabriek wordt gebouwd of een product wordt gelanceerd, zullen Bingham en zijn collega's werken aan het standaardiseren van de automatiseringsoplossingen van het bedrijf. Het beoordeelt de activiteiten op belangrijke locaties, identificeert welke productietechnologieën of -processen de juiste zijn om te automatiseren, definieert benchmarks en ontwikkelt modulaire oplossingen, en schaalt die oplossingen vervolgens naar de gebieden waar ze het grootste voordeel opleveren.
Daartoe sprak Bingham onlangs op een bijeenkomst van bijna 200 integratiebedrijven. Hij beschreef het project en de automatiseringsprioriteiten van zijn groep - waaronder lassen, machineonderhoud, ontbramen en inspectie - en deed de volgende missie:"Inzet intelligente automatiseringstechnologieën op belangrijke processen in onze kernvoetafdruk om voorspelbare, veerkrachtige en efficiënte operaties te creëren .”
Vervolgens suggereerde hij dat hun externe expertise nodig zou zijn als Honeywell deze missie zou voltooien, en nodigde hen uit om eventuele ideeën te delen. "We wisten dat het belangrijk was om van tevoren met deze en andere experts in contact te komen om de juiste oplossingen op de best mogelijke manier te maken, en er vervolgens omheen te standaardiseren", zegt Bingham.
Deze standaardisatie is cruciaal, voegde hij eraan toe, evenals gedetailleerde werkoverzichten en nauwkeurige simulaties van voorgestelde oplossingen. “Dat hebben we niet altijd gevraagd bij eerdere automatiseringsprojecten. Nu is het een must. We willen eerst zien hoe de cel werkt voordat we er daadwerkelijk een inkooporder voor plaatsen. Daarbij komt de eis om alleen vooraf goedgekeurde hardware te gebruiken - specifieke merken van PLC en robots bijvoorbeeld - en de ontwikkeling van gestandaardiseerde modules die we vervolgens kunnen kopiëren en plakken in onze verschillende faciliteiten. Dat zal helpen om de potpourri van apparatuur die je momenteel in sommige van onze fabrieken ziet, te elimineren, terwijl automatisering ook eenvoudiger en kosteneffectiever wordt om in te zetten. We zijn vorig jaar pas met dit project begonnen, maar ik moet zeggen dat we volop kansen voor ons zien.”
Automatisering Besturingssysteem
- De vraag over contractonderhoud - deel 2
- De niet-technische kant van betrouwbaarheid
- Het belang van het beheer van de workflow voor robotlassen
- De voordelen van laspistolen met doorlopende arm
- 5 robottoepassingen in de lucht- en ruimtevaartindustrie
- Waarom moeten we eerlijk zijn tegen de klanten?
- Engineering van de stroom van licht
- Wat is de taak van een machinebediener?
- De industriële robotarm - een productieboom
- De toekomst van koffie:een robotkoffiebar
- Robotic Machining:de volgende dimensie