VMC-technologie breidt toepassingen uit, productiviteit
Geavanceerde modellen blijven het VMC-bereik op de werkvloer vergroten.
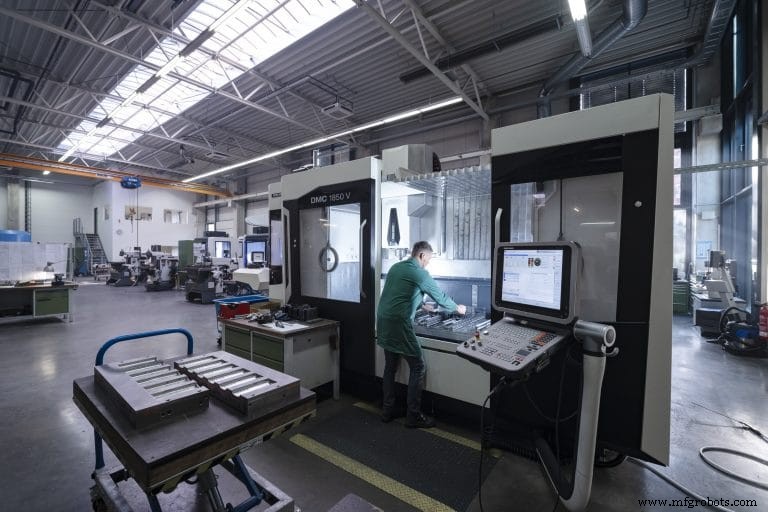
Verticale bewerkingscentra met geavanceerde kenmerken en functies verdienen hun sporen als productievere leden van het CNC-apparatuurarsenaal van machinewerkplaatsen. De VMC's van tegenwoordig dagen het idee uit dat ze moeten worden verzonden naar een zelden bezochte donkere hoek van de winkel, of beperkt moeten worden tot secundaire bewerking. VMC's zijn traditioneel lager geprijsd in vergelijking met horizontale bewerkingscentra, maar zonder de productiecapaciteit.
Tot op zekere hoogte hebben de meest recente toevoegingen van geavanceerde technologie VMC's in staat gesteld om de productiviteitskloof te dichten en een concurrentievoordeel te verzekeren in high-speed, high-precision toepassingen die uiteenlopen van ruimtevaart, medische, energie en vergelijkbare veeleisende industrieën. De functionaliteit van VMC's is aanzienlijk verbeterd met de toevoeging van tafel-op-tafel- en tapconfiguraties op de vierde en vijfde as, meerdere palletwisselaars, meer gereedschappen en hogesnelheidsspindels. VMC's zijn in staat om de meest complexe werkstukken te bewerken, zoals rotorbladen met bladen voor straalmotoren, turbinebladen voor energieopwekking, grote lucht- en ruimtevaartcomponenten en precisievorm- en matrijswerk.
Mold and Die VMC Case Study
Werkzeugbau Leiss GmbH wordt beschouwd als een van 's werelds toonaangevende en meest succesvolle producenten van extrusieblaasmatrijzen en rekblaasmatrijzen. In nauwe samenwerking met zijn klanten ontwikkelt het bedrijf uit Ludwigsstadt, Oberfranken, Duitsland nieuwe verpakkingsontwerpen voor de voedings-, farmaceutische, chemische, automobiel- en cosmetische industrie, evenals matrijzen en matrijzen die zijn ontworpen en vervaardigd door zo'n 65 ervaren Leiss medewerkers.
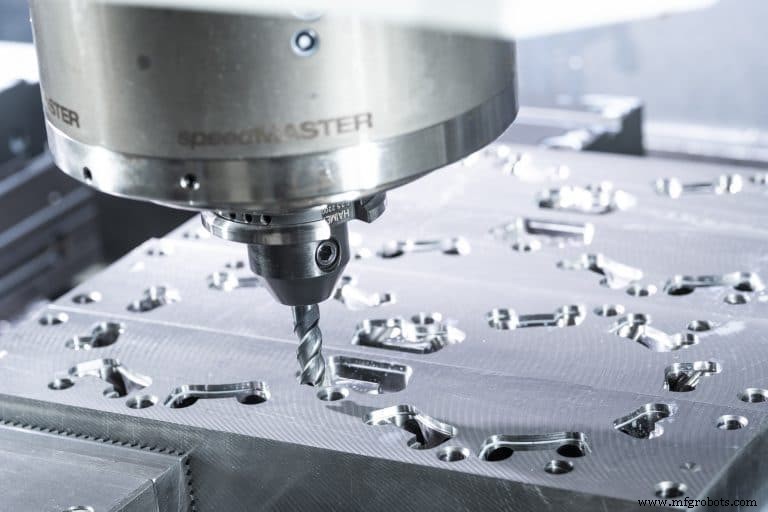
"Als dienstverlener op het gebied van ontwerp en constructie van gereedschappen zien we onszelf als een partner voor onze klanten", zegt Daniel Leiss, die de strategie van het bedrijf uitlegt. Hij leidt het bedrijf samen met zijn vader Fritz Leiss. De nauwe samenwerkingen met klanten beginnen vaak met de ontwikkeling van nieuwe verpakkingsontwerpen. "Hoe eerder we het proces helpen met onze ervaring, hoe zuiniger de fabricage van de matrijzen is voor alle betrokkenen."
Dit maakt het voor Werkzeugbau Leiss mogelijk om 250 nieuwe matrijzen per jaar te vervaardigen met in totaal ongeveer 1.000 holtes, evenals perifere componenten, zoals blaaspennen, maskers/ponsen of matrijzen/pennen.
Werkzeugbau Leiss beheert zijn grootschalige productie in zijn grote en moderne faciliteiten. Precisiebewerking wordt gedaan door een krachtig machinepark, waaronder tien CNC-machines van DMG Mori. Naast twee CTX-draaimachines omvat het machinepark vijf verticale bewerkingscentra uit de DMG Mori DMC V-serie. Dit omvat de DMC 1150 V, de DMC 1450 V en ook de nieuwe DMC 1850 V.
De machines werken op volle capaciteit en bewerken de uiterst nauwkeurige extrusieblaasvormen, die 80 procent van de productie van Leiss uitmaken. Hun productieprocessen variëren van boren en frezen van de koelsystemen tot voorbewerken en afwerken. "We profiteren van de hoge stabiliteit en nauwkeurigheid van de machines, waardoor we het nabewerkingswerk tot een minimum hebben kunnen beperken, vooral op het gebied van grote matrijzen voor machines met een lange slag", zegt Daniel Leiss, verwijzend naar het daaropvolgende polijsten van de mallen.
Het grootste model van de DMC V-serie werd in juli 2018 als veldtestmachine geïnstalleerd, wat Daniel Leiss als de perfecte aanvulling beschouwt:“Met de DMC 1850 V heeft DMG Mori een beproefd machineconcept aangepast aan de toenemende kwaliteitseisen bij het bewerken van grotere en zwaardere componenten.” Het verticale bewerkingscentrum breidt zich uit tot 1850 mm verplaatsingspaden in de X-as, en respectievelijk 700 mm en 550 mm in de Y-as en Z-as. Het maximale laadvermogen is 3.000 kg.
Volgens Daniel Leiss voldoet de DMC 1850 V perfect aan de eisen van de mal- en matrijzenmaker. “Machinestabiliteit geldt zowel voor 2.5D-bewerking en boren als voor 3D-voorbewerken. Met zijn nauwkeurigheid en dynamiek is de machine ook indrukwekkend voor 3D-fijnafwerking en is daarom geschikt voor gebruik in alle fasen van de gereedschapsproductie”, zei hij. Na slechts een paar maanden veldtesten werd de DMC 1850 V gebruikt in een tweeploegendienst en presteert sindsdien betrouwbaar.
VMC met kanteltafel
Mazak Corp., Florence, Ky., blijft zijn in Kentucky ontworpen en gebouwde VMC-lijn uitbreiden met het VC-500A/5X Vertical Machining Center met een kanteltafel in tapstijl. De VMC is ontworpen voor nauwkeurige, kosteneffectieve verwerking van kleine, complexe onderdelen via volledige vijfassige bewerking. De VC-500A/5X voegt zich bij Mazak VMC's die drie-, vier- en vijfassige bewerkingsmogelijkheden omvatten met on-board tasten voor onderdeellocatie en functie-inspectie. De VC-500A/5X is uitgerust met de Mazatrol SmoothX CNC, waardoor het eenvoudig is om programma's te genereren voor de productie van complexe onderdelen.
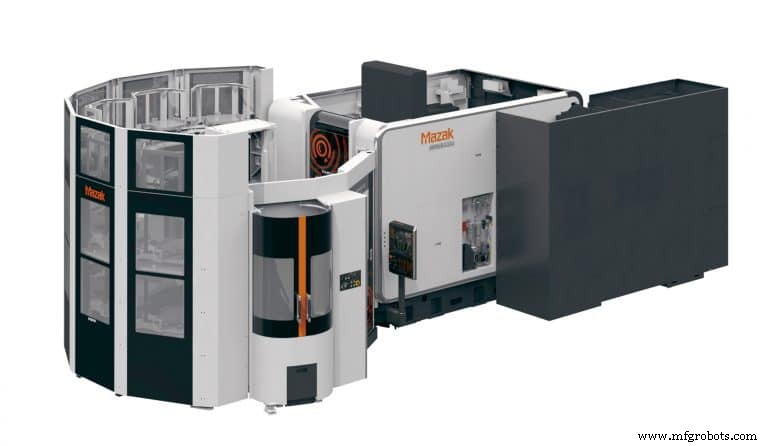
Geavanceerde functies van de VC-500A/5X stellen hem in staat om de kortst mogelijke bewerkingscyclustijden te garanderen, vooral in fijne oplopende programma's voor gelijktijdige vijfassige bewerkingen en free-form-matrijsbewerking, aldus het bedrijf. Deze functies omvatten high-gain feed forward-regeling, hoge rotatie-assnelheden, variabele acceleratieregeling en intelligent kamerfrezen. Speciale tandwielontwerpsoftware en een meeteenheid kunnen worden geïntegreerd in een gesloten tandwielbewerkingsproces.
De aswegen van de VC-500A/5X zijn geschikt voor onderdeelafmetingen tot 19,88″ (505 mm) in diameter en 12″ (305 mm) in hoogte. De ijlgangsnelheden voor deze drie lineaire assen zijn 1181 ipm (30 m/min). De VC-500Z/5X is uitgerust met een hoogwaardige CAT-40-spil met 12.000 tpm voor het bewerken van alle gangbare materialen, waaronder staal, aluminium en gietijzer. Optionele spiltoerentallen van 15.000 tpm en 20.000 tpm zijn beschikbaar.
Een ATC met 60 gereedschappen helpt de insteltijd te verkorten, maakt redundante gereedschappen mogelijk en zorgt voor meer onbemande, ononderbroken operaties. Dit proces geeft werkplaatsen een zeer nauwkeurige en kosteneffectieve optie om tandwielen van kleine tot middelgrote batches te bewerken met standaard gereedschap.
Automatisering van één machine
Met een hoge winkelvloeroppervlakte, worden machines met een kleine voetafdruk alom gewaardeerd, net als automatisering die de beschikbare vloeroppervlakte kan optimaliseren. Automatiseringssystemen voor één machine voor verticale bewerkingscentra bieden een productieve oplossing voor kleine werkplaatsen die kunnen voldoen aan veranderende productie-eisen met uitbreidbare, kosteneffectieve systemen. Ze hebben een minimale vloerruimte nodig en werken zonder licht, waardoor de spindels van de machine in de snede blijven terwijl operators vrij zijn om nieuwe onderdelen te laden, kwaliteitscontroles uit te voeren of verschillende andere winkeltaken uit te voeren.
Als het op automatisering aankomt, realiseren OEM's van machinegereedschappen, zoals Mazak, zich dat one size niet voor iedereen past en blijven ze schaalbare automatiseringssystemen ontwikkelen. Dergelijke systemen zijn schaalbaar in omvang, kosten en capaciteit, maar bieden toch de typische voordelen van elke vorm van automatisering:meer output van machines en arbeid, waardoor ze in wezen meer doen met minder.
Hier leest u hoe Mazak de voordelen van automatisering van één machine opsomt. Vergeleken met uitgebreidere automatiseringssystemen, hebben automatiseringssystemen met één machine een aanzienlijk kleinere voetafdruk, en in veel gevallen van werkplaatsen is dat alles wat nodig is.
De huidige automatiseringssystemen met één machine zijn doorgaans gestandaardiseerde oplossingen, maar toch flexibel en uitbreidbaar. Het automatiseringssysteem Multi Pallet Pool (MPP) van Mazak geeft winkels bijvoorbeeld de keuze uit drie verschillende configuraties, met een capaciteit van 6, 12 of 18 pallets. Het systeem werkt met verschillende productiemethoden en de operator kan het MPP-systeem zo instellen dat het onderdelen met een lage mix/hoog volume of onderdelen met een kleine oplage met frequente omschakelingen uitvoert.
In eerste instantie zou een winkel kunnen beginnen met een MPP van zes pallets bestaande uit twee rijen van drie pallets. Dit systeem met twee niveaus kan worden uitgebreid tot zes pallets op elke rij voor een totale pool van 12 pallets. Voor een 18-palletsysteem zou de MPP uitgroeien tot drie rijen van zes pallets. Ongeacht de configuratie blijft het formaat van de MPP klein, wat waardevolle winkelvloerruimte bespaart.
Een MPP-wisselaar voor zes pallets in combinatie met een Mazak Variaxis i-600 vijfassige VMC gebruikt bijvoorbeeld 29 procent minder vloeroppervlak dan een lineair systeem met zes pallets, terwijl het dezelfde capaciteit biedt. Vergeleken met een 12-palletsysteem vermindert de MPP de benodigde vloeroppervlakte met 44 procent. En wanneer gebruikt met een Mazak Variaxis i-700 vijfassige VMC, is een MPP met zes pallets 44 procent kleiner dan een lineair gerangschikt systeem met zes pallets, en hebben de 12- en 18-palletsystemen van de MPP minder dan de helft van de ruimte nodig.
In tegenstelling tot andere automatiseringssystemen gebruikt de MPP echte machinepallets in plaats van extra die bovenop de bestaande pallet van een machine worden geplaatst. De MPP van de Variaxis i-600 heeft een pallet van 400 m² met een maximale belasting van 300 kg bij afmetingen tot 600 mm in diameter en 425 mm in hoogte.
De Variaxis i-700 MPP pallet is 500 mm vierkant en heeft een draagvermogen van 400 kg. De MPP werkt met hetzelfde palletklemsysteem als een typische tweepalletwisselaar die op een werktuigmachine is geïnstalleerd. Binnen de MPP pakt en plaatst een servo-aangedreven robot pallets in en uit de machine.
De MPP gebruikt dezelfde Smooth PMC-software die Mazak's uitgebreide Palletech-automatiseringssysteem voor meerdere machines bestuurt. De besturing van de bewerkingsmachine geeft de software weer die op een afzonderlijke celbesturingseenheid draait. Smooth PMC-software maakt het gemakkelijk om het geautomatiseerde bewerkingssysteem bijna overal te bewaken met behulp van een smartphone, pc of tablet. Met de software kunnen winkels ook hun schema's on-the-fly wijzigen, programmabestanden voor onderdelen beheren, de levensduur/breuk van het gereedschap volgen en instructies naar de werkvloer sturen.
Sneller van afdruk naar onderdeel
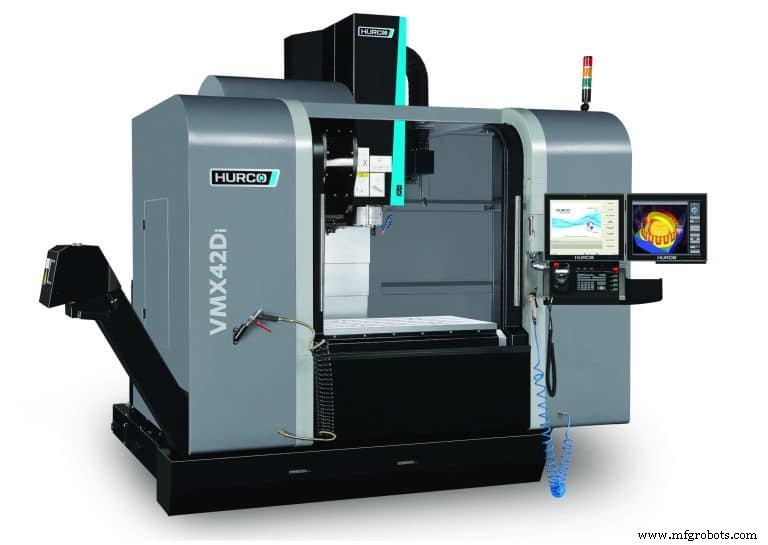
Je zou verwachten dat Hurco Companies Inc., de uitvinder van conversatieprogrammering, een leider zou zijn in het stroomlijnen van het proces om sneller van print naar onderdeel te gaan met CNC-bewerkingscentra. En dat is het ook.
Hurco VMC's lopen uiteen, van het VM CNC VMC compacte voetafdrukwaardemodel tot VMX vijfassige serie machines, en voor de grootste ruimtevaartonderdelen de DCX-serie van dubbelkoloms bewerkingscentra met 2- en 3-m X-assen. De VMC's van Hurco worden gebruikt om onderdelen te vervaardigen voor de automobiel-, ruimtevaart-, medische apparatuur-, energie-, injectiegereedschap- en matrijzen-, transport- en elektronica-industrie.
Op zijn geavanceerde CNC-bewerkingscentra biedt Hurco dual-screen bediening voor snellere, eenvoudigere verwerking. Een Data Block Search helpt operators bij het bewerken van een onderdeelprogramma om bijvoorbeeld een functie te corrigeren. In plaats van door regels code te zoeken, gebruikt de programmeur het grafische scherm om de onderdeelfunctie te selecteren die moet worden bewerkt en de bijbehorende coderegel verschijnt op het andere scherm, zodat de wijziging snel kan worden doorgevoerd.
Hurco's functie voor gelijktijdig programmeren is verbeterd met de bediening op twee schermen. Terwijl het bewerkingscentrum een onderdeel draait, kan de operator het volgende onderdeel programmeren zonder de bewerkingscyclus te onderbreken.
Met DXF Transfer kan de operator de CAD-afbeelding importeren, de gewenste functies selecteren en de WinMax CNC-besturing maakt automatisch het programma. Het onderdeelprogramma kan op het scherm worden gecontroleerd met Hurco's grafische verificatiesysteem, dat een solide 3D-weergave van het gereedschapspad met dynamische rotatie en realtime gereedschapsweergave omvat, zodat het onderdeel vanuit elke hoek kan worden bekeken zonder gedwongen te worden het opnieuw te tekenen .
Recente Hurco-besturings- en softwarefuncties zijn ontworpen om alles te stroomlijnen, van het optimaliseren van de cyclustijd tot het vastleggen van gereedschapsinformatie. UltiMotion verkort de cyclustijd tot 30 procent, wat volgens Hurco de kwaliteit van de oppervlakteafwerking aanzienlijk verhoogt.
UltiMonitor maakt bewaking op afstand van de machine mogelijk vanuit elke webbrowser, of het is mogelijk om het bedieningsscherm of de video van een USB-camera op de machine te zien. Dankzij de absolute gereedschapslengte kan de gereedschapsinstelling onafhankelijk zijn van het onderdeel en de machine. Als gevolg hiervan hoeft gereedschapsinformatie slechts één keer te worden vastgelegd, waardoor het gereedschap op andere bewerkingscentra kan worden gebruikt, wat het gebruik van een offline gereedschapsvoorinstelling vergemakkelijkt. Bovendien analyseert Tool Change Optimization het onderdeelprogramma en vermindert automatisch het aantal gereedschapswisselingen door het programma te herschikken voor optimale efficiëntie.
Volledige VMC-mogelijkheden
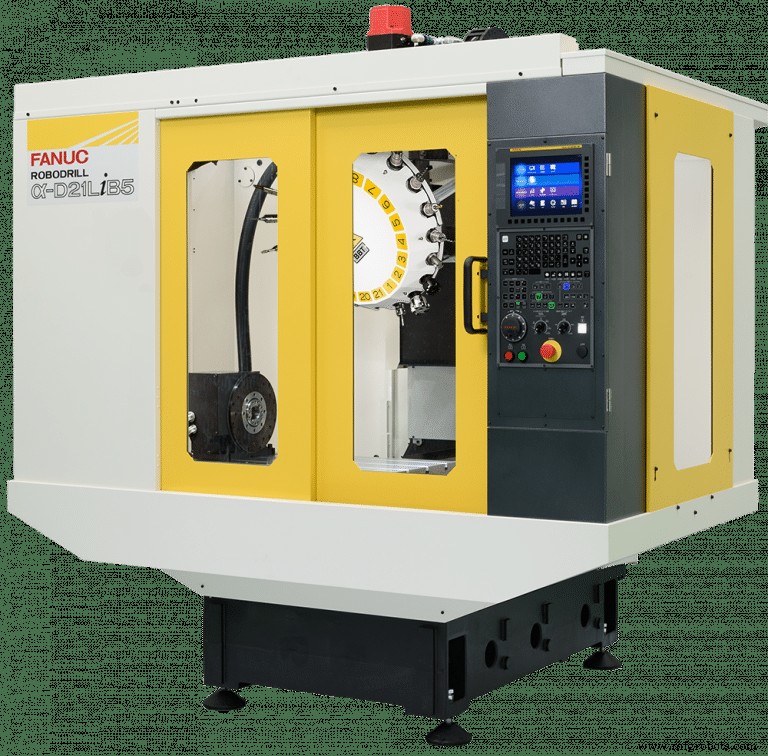
De bekende FANUC RoboDrill bootst het vermogen van een verticaal bewerkingscentrum na om te frezen, boren, tappen, vlakken, holtes maken en sleuven maken - alles wat een VMC kan doen, zegt Ken Corklin, RoboDrill productmanager, Methods Machine Tools Inc., Sudbury, Mass.
“De RoboDrill concurreert heel goed met 20 x 30″ en 20 x 40″ VMC's en kan dezelfde hoeveelheid werk doen als een 40-taper 20 x 30″ VMC en 15-50 procent sneller. Redenen zijn snelle gereedschapswisseling, snel in- en uitschakelen van de spil en motoren met een hoge acceleratiesnelheid. Zelfs als een 40 taper wat zwaarder voorbewerken kan doen, verslaat de RoboDrill ze in sleuven, tappen, boren, pocketing en circulaire interpolatie. Bij voorbewerken is de RoboDrill meestal 15 procent sneller; zonder voorbewerken maar liefst 20-40 procent hoger,” zei hij.
Er zijn meer dan 7.000 RoboDrills geïnstalleerd in Noord-Amerika, waarvan ongeveer de helft in jobshops en de andere helft in branchespecifieke shops. Toepassingen zijn onder meer hogesnelheidsbewerking van aluminium voor ruimtevaartonderdelen, titanium en kobaltchroom voor medische onderdelen en pistoolonderdelen, evenals algemene engineering.
"BIG Plus-spiltechnologie heeft de RoboDrill met 30 taps toelopende C-frame-stijl het oppervlaktecontactgebied gegeven dat hem in staat stelt om zwaardere zaagsneden van hoge kwaliteit te maken en dit razendsnel te doen - iets waar 40-taps machines moeite mee hebben," zei Corklin. "RoboDrill is bijvoorbeeld in staat om typisch vorm- en matrijswerk of medische toepassingen uit te voeren met een hogesnelheidskogelfrees met voedingssnelheden van 200 ipm (50 m/min) of meer vanwege de hoge acceleratie-/vertragingssnelheden."
RoboDrill is verkrijgbaar in drie maten:kort bed, medium bed en lang bed met de nieuwste FANUC 31i-B5 Nano CNC-besturing. X/Y/Z-uitslagen in het model met kort bed zijn 300 x 300 x 300 mm; 500 x 400 x 330 mm in het medium model; en 700 x 400 x 330 mm in het lange bed. De ijlgangsnelheden zijn 2.125 ipm (54 m/min) in alle drie de modellen. BIG Plus-spindels zijn 10.000 tpm en 24.000 tpm met een ATC met 21 gereedschappen.
De nieuwste toevoegingen aan de RoboDrill omvatten een servomotor voor de revolver, die de cyclustijd verkort, evenals functies zoals Ai Overlap, die boogradiusbewegingen in de Z-as mogelijk maakt voor een kortere cyclustijd in plaats van 90º-hoeken die een stop vereisen. Een iHMI-bediening met touchscreen van FANUC maakt een groeiend gebruik van apps mogelijk, zoals Renishaw's Go Probe.
RoboDrills zijn ontworpen om naadloos aan te sluiten op FANUC-robots voor standaard automatiseringspakketten of voor aangepaste automatiseringsoplossingen. Methods heeft een aantal standaard “bolt-on” automatiseringsoplossingen in de nieuwe Plus Serie, waaronder de Plus K.
Met de Plus K kan de RoboDrill zonder toezicht door een uitgebreide automatische gereedschapswisselaar en een geautomatiseerde palletwisselaar lopen. Automatiseringsoplossingen op maat zijn volgens het bedrijf al jaren een aandachtspunt van Methods Automation.
Met de FANUC 31iB5-besturing is de RoboDrill geschikt voor vijf assen. Opties zoals AICCII en lookahead met duizend blokken maken het in staat om op hoge snelheid contouren en bewerkingen uit te voeren. Zijn afmetingen en acceleratie van 1,5 g maken hem zeer wendbaar en in staat om de cyclustijd met 15-50 procent te verkorten in vergelijking met standaard VMC's, aldus Corklin.
Lineaire en Box Way VMC's
Veel machinebouwers leunen nu uitsluitend op lineaire geleidingsmachines. Maar Doosan Machine Tools America, Pine Brook, N.J., biedt zowel lineaire als box-way VMC's, met een breed scala aan bewerkingsopties.
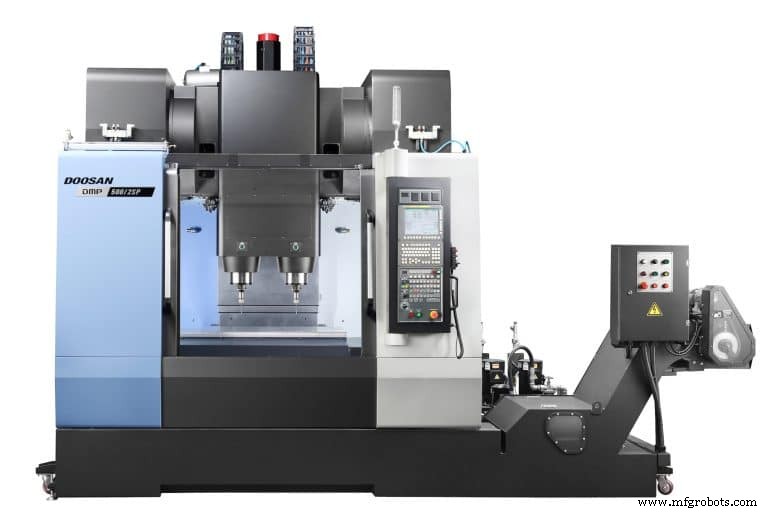
De DNM-serie beschikt over lineaire geleidingen, BIG Plus 40- en 50-tapspindels (die standaard worden geleverd op Doosan VMC's) en spilsnelheden van 8.000-15.000 tpm. Het S-model is uitgerust met 15.000 tpm en snellere stroomversnellingen. De verplaatsingen op de X-as variëren van 20,5″ tot 85″ (520-2.160 mm) in de modellenreeks.
Voor zwaardere bewerkingen in hardere materialen heeft de Mynx-serie een box-way-ontwerp, BIG Plus 40- en 50-tapspindels met een tandwielkast of directe aandrijving, afhankelijk van het model, en een bereik van 6.000 tot 12.000 tpm.
Voor productiewerkplaatsen zijn de modellen de VC-serie met roterende palletwisselaars en de DMP 500/2SP met dubbele spindels en twee gereedschapswisselaars. De DMP heeft een tafel van 47,2 x 20,5″ (1.200 x 520 mm) en een magazijn voor maximaal 40 gereedschappen dat toegankelijk is voor elke spil in ongeveer dezelfde voetafdruk als een machine met één spil. Elke spindel kan iets worden aangepast met de W-as om de noodzaak van een perfecte uitlijning van werkstukopspanning of opspanhoogten te voorkomen.
Doosan's vijfassige verticalen omvatten de DNM met tweeassige taptafels geïntegreerd in het machineplatform. Met een draaitafel in combinatie met een 40-taps spindel met directe aandrijving en 12.000 tpm, biedt de machine een stap hoger dan een standaard VMC.
Ten slotte bieden DVF-machines met vijf assen een vollediger geïntegreerde oplossing, met een tafel met vijf assen in cantileverstijl of een tafel in tapstijl. VCF-serie vijfassige vaste tafel VMC's bieden meer deelbereik omdat de machinebewegingen en de tafelafmetingen groter zijn. De extra assen bevinden zich in de B-as roterende kopspindel of in de ingebouwde, boven tafel roterende as.
Checklist voor het evalueren van geavanceerde VMC's
De nieuwste modellen van verticale bewerkingscentra die op de markt komen, hebben geavanceerde functies, constructiekenmerken en componenten die bijdragen aan betrouwbaarheid en efficiëntieniveaus die nooit voor mogelijk werden gehouden op een VMC. Volgens Ellison Technologies, een leverancier van bewerkingsoplossingen voor Noord-Amerikaanse metaalbewerkingsbedrijven en hun wereldwijde filialen, zijn hier enkele van de nieuwere kenmerken en mogelijkheden die u in uw volgende VMC wilt opnemen.
Voor een bespreking van gunstige VMC-kenmerken raadpleegt u "Nieuwe generatie VMC's zijn productiever en efficiënter dan ooit", Manufacturing Engineering, juni 2017, waarin de volgende informatie staat:"Bekijk hoe de machine is gebouwd, zodat over 10, 15, misschien zelfs 20 jaar , het werkt nog steeds net zo nauwkeurig als de dag dat u het installeerde. Controleer of de fabrikant eindige elementenanalyse (FEA) gebruikt om de gietstukken voor de spilkop, basis, kolom en zadel te ontwerpen. Het idee is om de natuurlijke harmonischen van de structuur buiten het operationele bereik van de machine te krijgen.
“Zorg er ook voor dat de gebruikte gietmethode is gelicentieerd door de Meehanite Worldwide-organisatie. Dit gepatenteerde proces vereist ijzerproductieprocedures van de hoogste kwaliteit, die zorgen voor langdurige stijfheid, zwaar snijvermogen en goede trillingsdemping gedurende de levensduur van de machine.
“Andere constructieve hoogtepunten van een kwaliteitsmachine zijn onder meer een gebogen piramidekolom die met de hand op het bed wordt geschraapt, waardoor de twee gietstukken zich bijna als één geheel gedragen, wat ook zorgt voor een strakke machinegeometrie die de nauwkeurigheid van de onderdelen weerspiegelt. Hoogwaardige keramische spindellagers, dubbel verankerde voorgespannen kogelomloopspillen en lineaire rolgeleidingen zijn onder andere constructieaspecten waarmee rekening moet worden gehouden. Rolgeleiders hebben drie keer de stijfheid en twee keer de levensduur van kogelgelagerde bewegingsgeleiders.
“Kijk bij een degelijke constructie naar aanvullende componenten, zoals spindels, het koelsysteem en het spanentransportmechanisme. Deze dragen allemaal bij aan efficiëntie. Zoek naar functies zoals een spil met dubbel contact (conus/vlak) zoals BIG Plus, bewaking van de gereedschapsbelasting, koelvloeistof door de spil en adaptieve voedingssnelheidsregeling voor een optimale gereedschaptoepassing en cyclustijd. Begrijp verder hoe de machine is ontworpen om met warmte om te gaan. De grootste vooruitgang van de afgelopen jaren is misschien wel de toepassing van een verscheidenheid aan thermische stabiliteitsverbeteringen.”
Automatisering Besturingssysteem
- Wat is VMC-bewerking?
- Toepassingen van 3D-afdruktechnologie van titaniumlegering
- Weet hoe precisie CNC-bewerkingen bijdragen aan productiviteit
- Delrin bewerken:tips, voordelen en toepassingen
- PEEK verspanen:tips, voordelen &toepassingen
- Teflon/PTFE bewerken:tips, voordelen &toepassingen
- Bewerkingscentrum toepassingen. Modellen &Toepassingen?
- Inleiding tot verticale bewerking of CNC VMC
- VMC 5-assige machine nodig?
- Hoe VMC Machine uw productiviteit verhoogt
- CNC-bewerkingscentrumtechnologie