Geautomatiseerde koppeling vermindert uitvaltijd van robotlascel
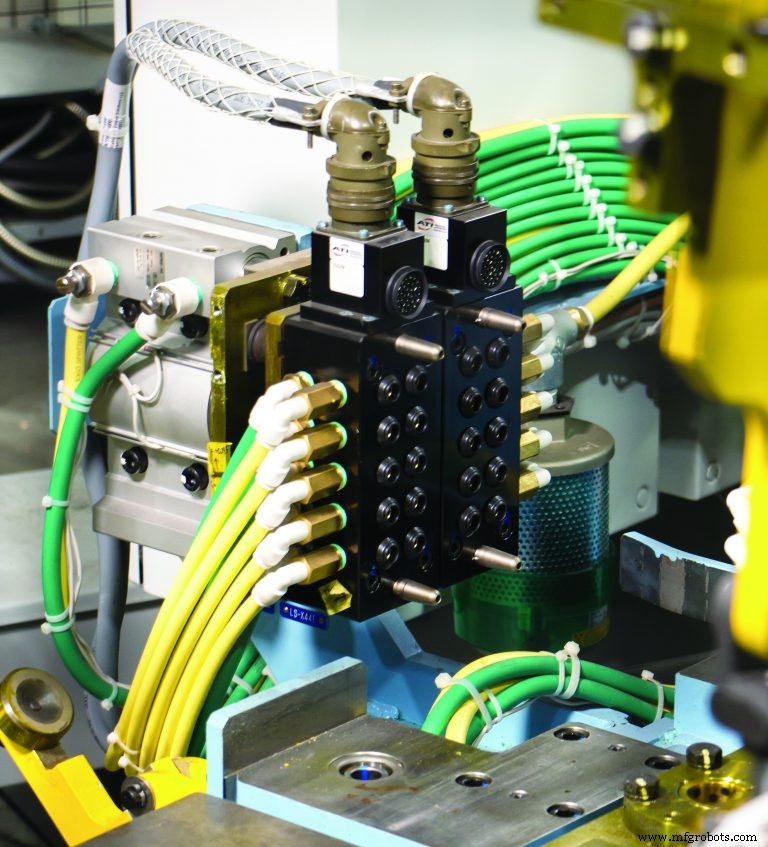
Er is geen betere manier om een probleem op te lossen dan door het volledig te elimineren. Dat is tenminste hoe KTH Parts Industries Inc. (St. Paris, OH) overwoog zijn beslissing om een handmatig proces voor het wisselen van apparatuur voor zijn robotlascellen te automatiseren.
KTH selecteerde GA2-koppelingen voor nutsvoorzieningen van ATI Industrial Automation (Apex, NC) om deze prestatie te volbrengen. Met name de nieuwe automatische koppeling van lucht- en elektriciteitsvoorzieningen aan de cellen elimineerde ongeveer 65 uur per jaar aan uitvaltijd per lijn, verminderde de totale bedrijfskosten en verhoogde het gebruik en de productiviteit van de apparatuur.
KTH Parts Industries, een wereldwijde Tier 1-autoleverancier voor structurele onderdelen voor bodemplaten, heeft meer dan 1100 technische en productiemedewerkers die betrokken zijn bij de vele fasen van de productie van auto-onderdelen, waaronder productontwikkeling, productanalyse, productvormbaarheid, prototyping, productiestempelen, vormen, robotlassen, assemblage en verzending van onderdelen.
Een van de kerncompetenties van KTH is het ontwerp en de implementatie van flexibele laslijnen voor auto-bodemonderdelen. De laslijnen gebruiken complexe armaturen of mallen om de componenten op hun plaats te houden terwijl een robot ze aan elkaar last. Elk automodel vereist een andere mal, wat leidt tot veel wisselingen van uitrusting in de fabriek.
Om de flexibiliteit te vergroten en de beperkte productievloerruimte te optimaliseren, creëerde KTH een dubbelzijdige werkcel met een draaitafel. Het doel van dit ontwerp was om de robot actief te houden en de insteltijd te verkorten. Onderdelen worden aan de ene kant van de draaitafel in de mal geladen, terwijl de robot onderdelen aan de andere kant aan elkaar last.
Vóór de installatie van ATI's GA2-leidingkoppelingen vertrouwde KTH op handenarbeid om kabels aan en los te koppelen en de mallen op de draaitafels te laden. Vermenigvuldig dit met één tot twee omschakelingen per lijn per ploeg, en je hebt een duizelingwekkende hoeveelheid mens-machine-interactie in het proces.
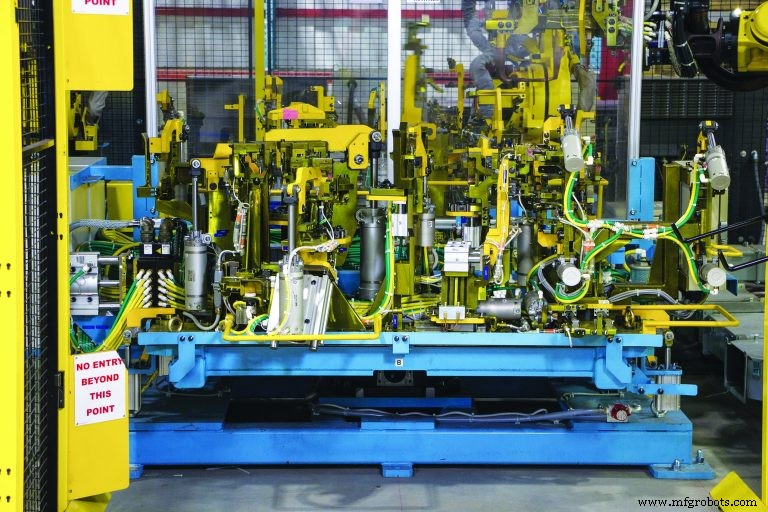
Dave Reed, een projectleider op de lasafdeling van KTH, nam het oude proces aan:“Voordat we de ATI-hulpkoppelingen gingen gebruiken, hadden we een luchtleiding en een verdeelstuk, en moesten ze samen met spanbanden aansluiten. Aan de elektrische kant moesten we de 40-pins ontkoppelingen koppelen door ze handmatig in elkaar te draaien. Dit proces werd vele malen herhaald voor elke malwissel.”
Volgens KTH waren de fysieke arbeidseisen van het oude proces erg hoog, en natuurlijk was er altijd een inherent risico wanneer een medewerker de werkcel betrad. Onder deze omstandigheden was de hoge frequentie van kabelstoringen geen verrassing. Het koppelen en ontkoppelen van de kabels met inconsistente kracht en koppel zorgde voor overmatige slijtage. Verkeerde uitlijning van connectoren leidde tot beschadigde pinnen. Zonder een speciale opslagruimte voor kabels die niet in gebruik waren, werden ze op de vloer of op andere apparatuur in de cel achtergelaten.
"We hadden luchtleidingen die waren doorgesneden en lekten, connectoren die beschadigd waren", zei Reed. "Onderhoud werd gebeld om te proberen het probleem te beoordelen, maar vaak was het gewoon een verbogen pin op een connector die ons uren downtime zou kosten - ongeveer 65 uur per jaar per lijn."
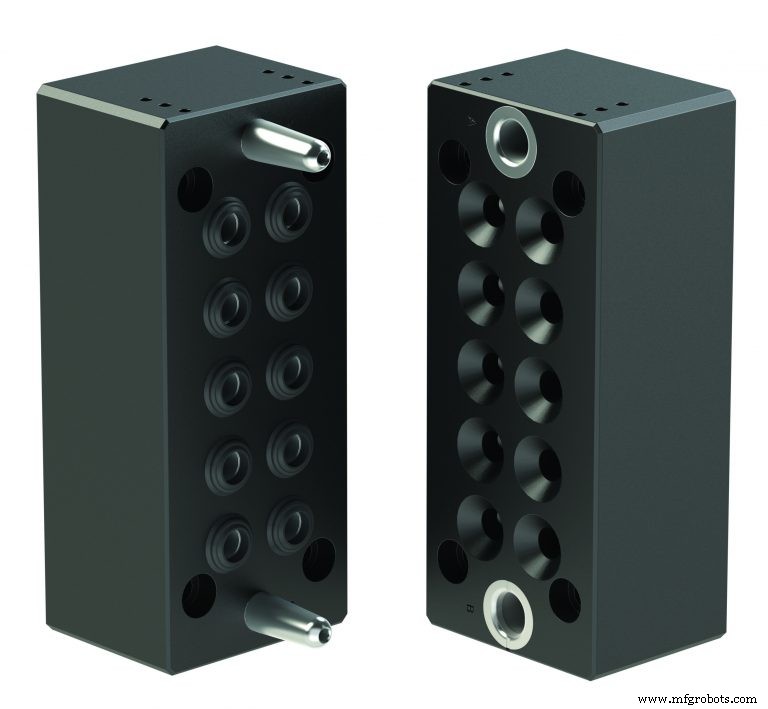
Naast buitensporige menselijke interactie en apparatuurstoringen, was het oude proces een nachtmerrie voor de apparatuurondersteuningsgroep. De sectieleider van de groep, Jonah Strapp, merkte op:"Na de omschakelingen zou je met iets in de cel moeten rommelen om het weer werkend te krijgen. Downtime betekent geldverlies. Als dat gebeurt, is er nogal wat druk om de lijnen aan de praat te krijgen.”
KTH was buitengewoon gemotiveerd om de omschakeling van de lasmal te verbeteren om een vlottere werkstroom mogelijk te maken, de veiligheid van de werknemers te vergroten en het aantal defecten aan apparatuur te verminderen. Matt Myers, stafingenieur van de technische projectgroep van KTH, legt uit:"Tijdens onze normale bedrijfsdag proberen we zoveel mogelijk productie uit de lijn te persen. Elke keer dat we een omschakeling doen, verliezen we productietijd, wat zich vertaalt in een groot financieel negatief in onze boeken. Alles wat we kunnen doen om de hoeveelheid uitvaltijd te verminderen, is waanzinnig belangrijk.”
Dat is precies het punt waarop het gebruik van ATI's nutskoppelingen een efficiënte tijdbesparende oplossing bood. De nutskoppelingen van ATI zijn zeer geschikt voor de omschakeling van de laslijn van KTH. Ze leveren stroom, signaal en pneumatisch. ATI's utiliteitskoppelingen hebben ingebouwde rotatiecompliantie om herhaalbare koppelingen in een duurzaam pakket te bieden. Omdat het ontwerp modulair is, werken de hulpprogramma-koppelingen met ATI's uitgebreide familie van gereedschapswisselaar-hulpprogrammamodules.
Samen bedienen de hulpprogramma-koppelingen en -modules ook een reeks netwerkprotocollen, legde KTH's Myers uit. "Als het gaat om het ontwerpen van nieuwe producten, kan ik vertrouwen op het ATI-engineeringteam om snel een elektrisch of pneumatisch product te ontwerpen dat aan onze behoeften voldoet, of om te verwijzen naar een van de duizenden [beschikbare] producten op hun website." Voor dit specifieke systeem bij KTH heeft ATI een netkoppeling en een 32-pins discrete I/O-elektrische module geconfigureerd die eenvoudig in bestaande lijnen kon worden geïntegreerd.
“Toen we de nutskoppeling voor het eerst uitprobeerden, was het meteen duidelijk dat het een groot verschil zou gaan maken. De nieuwe koppelingen zijn zeer betrouwbaar en handsfree. We hoeven niet met ze te sollen. Ze werken elke keer,' zei Strapp.
Op de vraag hoe KTH ATI als hun leverancier heeft gekozen, antwoordde Myers:"Op basis van onze eerdere relatie met de klantenservice, de snelle levertijden en onze lokale accountmanager was het een gemakkelijke beslissing om voor ATI te kiezen." KTH is een oude gebruiker van ATI's robotgereedschapswisselaarproducten, dus de overgang naar automatische koppeling met ATI's utility-koppelingen werkte goed.
Dave Reed bevestigde de prestaties van de ATI GA2 utility coupler:"Ik heb het afgelopen jaar waarschijnlijk honderden van deze mallen veranderd, en ik heb nog nooit een probleem gehad met het ATI-systeem. Je zet de mal erop, je drukt op de knop , het drukt naar binnen, klemt zich vast, je pinnen zijn allemaal gekoppeld, je hebt nul tolerantie voor het krijgen van verbogen pinnen of gebroken luchtleidingen. Het is vrijwel een onberispelijk product. Het maakt het leven een stuk eenvoudiger."
Automatisering Besturingssysteem
- Verbeter de prestaties met geautomatiseerd lassen
- 4 manieren om de prestaties van robotlassen te verbeteren
- Hoe robotlassen de zware fabricage verandert
- Robotisch lassen:veelvoorkomende oorzaken van ongeplande uitvaltijd voorkomen
- Onderhoud robotlassen:meer ROI en minder uitvaltijd
- Geautomatiseerde productie van olie-boorkoppelingen
- Robotische cellen maken automatisch onderhoud van onderdelen mogelijk
- FastArc-gestandaardiseerde cellen vergemakkelijken de toegang tot robotlassen
- Zware robotlascellen kunnen een geweldige eerste stap zijn
- Geautomatiseerde weerstandslasser:een evolutie
- Een inleiding tot geautomatiseerde weerstandslasser