De digitale fabriek aansturen met realtime MES-gegevens
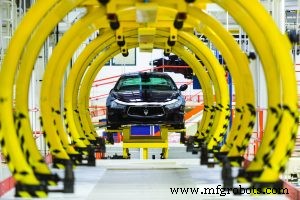
Met de drang naar een volledig digitale fabriek, is MES-software (productie-uitvoeringssystemen) nog nooit zo belangrijk geweest voor fabrikanten van alle soorten. Door gebruik te maken van de nieuwste oplossingen voor snel reagerende productie-uitvoeringssystemen in productieprocessen, kunnen bouwers snelle updates krijgen over tijdgevoelige operationele gegevens die kunnen helpen de fabrieksprocessen te verbeteren en de digitale fabriek dichter bij de realiteit te brengen.
Naarmate de convergentie van productie- en bedrijfssoftwaresystemen vordert, realiseren steeds meer fabrikanten de voordelen die een digitale fabriek biedt, met realtime of bijna realtime gegevensprestaties die veel meer productie-inzicht bieden dan tot hun beschikking was in de Verleden. Fabrikanten worden serieuzer met het implementeren van de infrastructuur die nodig is voor slimme productieoplossingen en het Industrial Internet of Things (IIoT), en meestal vormen cloudgebaseerde MES-systemen de kern van deze technologieën.
“De trend is in de richting van convergentie van bedrijfssystemen om een diepgaande analyse te krijgen van de werking van apparatuur en systemen. We zien dat dataproviders hun krachten bundelen”, zegt Pete Tecos, executive vice president, 5ME (Cincinnati), en wijst op de recente samenwerking van 5ME met SmartWare, waarin Freedom Smart Manufacturing-oplossingen en Smartwares Bigfoot CMMS-platforms (computerized maintenance management system) worden gecombineerd. "Hoe sneller we gegevens verzamelen en delen tussen verschillende systemen, hoe beter we een beter zicht krijgen op de algehele bedrijfsvoering."
De impact van de cloud
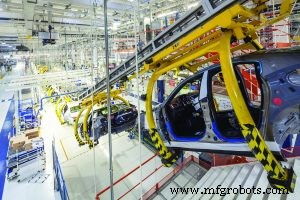
Naarmate meer bedrijven cloudgebaseerde productietechnologie beginnen te gebruiken, komen de mogelijkheden van MES-oplossingen, enterprise resource management (ERP) en gegevensverzamelingssystemen op de werkvloer naadloos bij elkaar en werken ze samen om IIoT- en Industry 4.0-inspanningen effectiever te maken in de winkel vloer.
"Het maakt het nastreven van de 'Holy Grail of Manufacturing' mogelijk:realtime, uitgebreide systeemanalyse door het delen van gegevens", aldus Tecos. "Aanpassingen en/of correcties worden sneller gemaakt en met minder verstoring van de productieactiviteiten."
De huidige productiesoftwareoplossingen bieden een schat aan tools voor het volgen van belangrijke fabrieksstatistieken, waaronder Overall Equipment Effectiveness (OEE) en vele andere, voor de productieonderneming, en deze verrijkte systemen passen goed bij elkaar aangezien ontwikkelaars van deze oplossingen samenwerken om aan de eisen te voldoen van het IoT/IIoT.
"Kortom, je begint op het niveau van de fabriek en communiceert met activa en een verscheidenheid aan productiesystemen, en biedt vervolgens een visualisatielaag [OEE-cockpit] om de prestaties en KPI's te bekijken," zei Tecos. "Tot slot, push real-time informatie stroomopwaarts naar de bedrijfssysteemruimte [ERP, MES, CMMS, kwaliteitssystemen]. Als al deze systemen symbiotisch werken in plaats van in silo's, kun je operaties stimuleren om zeer efficiënte adaptieve productie te bereiken door de uitwisseling van realtime operationele intelligentie - dat is de heilige graal."
Compatibiliteit met andere platforms is de sleutel, voegde Tecos eraan toe. “Gebruiksgemak, gegevensverzamelingsmogelijkheden en veelzijdigheid met machinetypes zijn ook belangrijk. Onze software presenteert gegevens vanuit meerdere perspectieven en verdeelt deze in drie categorieën:frequentie, duur en het genereren van inkomsten. We kijken naar de correlaties hiertussen, waarbij we in feite de frequentie- en duurgegevens gebruiken om een beeld te genereren dat inkomsten genereert
van bewerkingen.'
De resultaten van sommige 5ME-klanten zijn indrukwekkend. Na installatie van de eLog-systemen van 5ME, heeft de fabriek van zware apparatuur Caterpillar's East Peoria, IL, de gemiddelde lengte van de vertragingen gehalveerd en de machine-in-cyclustijden met 30% verbeterd voor de machines waarop Freedom eLog was geïnstalleerd, wat neerkwam op $ 1,2 miljoen verhoging van de toegevoegde waarde. Het bedrijf meldde dat het ontdekte dat de elektronische "op feiten gebaseerde" gegevens veel beter, nauwkeuriger en minder emotioneel waren dan het papieren systeem/handmatige proces dat eerder werd gebruikt.
De ondernemingsvisie nemen
MES-systemen zijn niet langer op zichzelf staande systemen, merkte Stephen Brown op, vice-president, productiepraktijk, Amerika, Siemens PLM Software (Plano, TX). “MES maakt deel uit van een onderling verbonden enterprise IT-infrastructuur. De waarde van MES wordt nu bepaald door hoe goed het MES-systeem integreert in de algehele waardeketen, zowel stroomopwaarts naar productontwikkeling en productie-engineering, als stroomafwaarts naar automatisering,” zei hij.
“Klanten willen de hele waardeketen digitaliseren, van productontwerp tot productieplanning, productie-engineering, productie-uitvoering en vervolgens diensten. We noemen dat de digitale onderneming”, zegt Brown. “Meer specifiek gebruiken we de term Digital Twin. Wij helpen onze klanten bij het maken van een Digital Twin van niet alleen het product, maar ook het productieproces en de fabriek en productieapparatuur. Onze klanten gebruiken vervolgens de Digital Twin om het product en het fabricageproces volledig te simuleren voordat ze zich inzetten voor prototypes, gereedschappen en fysieke activa.”
Deze factoren maken snelle innovatie mogelijk, merkte hij op. “Het gaat niet alleen om het managen van productieactiviteiten. Het gaat om het creëren van een flexibel, responsief en voorspelbaar productieproces dat in staat is te reageren op nieuwe productvereisten.”
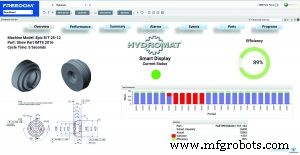
Eenmaal in productie en gekoppeld aan automatisering, kunnen klanten van Siemens beslissingen nemen met behulp van realtime gegevens van de werkvloer, zei Brown. “Voorbeelden zijn onder meer realtime machinebeschikbaarheid of uptime die door de productieplanningssoftware kan worden gebruikt om planningen te optimaliseren, en kwaliteitsproblemen die tijdens de productie worden geïdentificeerd en die in bijna realtime kunnen worden gecommuniceerd aan de engineering voor de dispositie van onderdelen, wat vooral belangrijk is in ruimtevaart”, aldus Brown. "Eindelijk, laag in IoT en data-analyse met Mindsphere, en we sluiten de cirkel over de digitale onderneming.
Siemens beheert het innovatie- en veranderingsproces met zijn Teamcenter PLM en creëert een Digital Twin van het product- en productieproces, zei Brown. “Vervolgens integreren we met onze MOM [manufacturing operations management]-portfolio, sturen we de benodigde product-, productie- en kwaliteitsgegevens naar de werkvloer, en gebruiken we Mindsphere voor IoT en big data-analyse om as-built data vast te leggen, waardoor het product weer inzicht krijgt in het product. en procesontwerp voor continue verbetering.”
Opvoeren voor IIoT
Fabrikanten willen meer gebruikmaken van Big Data en de IoT/IIoT-boom, samen met cloudmobiliteit, zegt Eric Green, vicepresident van Dassault Systèmes-Delmia. "Die hebben tegenwoordig allemaal invloed op fabrikanten, maar totdat er een definitieve businesscase is, bevinden ze zich nog in een verkennend stadium", zei hij.
“Met sommige van de technologieën specifiek rond IIoT en IoT, ontdekken en begrijpen ze nog steeds wat de kansen zijn. Als je nadenkt over IIoT, doen fabrikanten al jaren de voorloper', merkte Green op. “IIoT zorgt voor een nieuwe generatie, een nieuwe evolutie. Maar we hebben klanten met apparatuur die meer dan 20 jaar oud is, en deze nieuwe technologieën moeten de bestaande investeringen in apparatuur kunnen ondersteunen.”
De sleutel voor fabrikanten zal zijn om te vinden waar en hoe ze innovatie kunnen toepassen, voegde hij eraan toe. “Als consumenten creëren we allemaal een ervaring, met de auto’s die we besturen, en de smartphones en slimme apparaten die we hebben. Wat dat doet, is van invloed op hoe bedrijven naar de markt gaan. Het dwingt deze fabrikanten om efficiënter of innovatiever te zijn.”
Voor ontwikkelaars zoals Dassault is het doel om snel en efficiënt opwindende nieuwe producten op de markt te brengen, merkte hij op. "Als je kijkt naar het op de markt brengen van nieuwe producten, van productontwerp tot productie en tot de consument, vereist het innovatieplatform dat je snel kunt samenwerken om het ontwerp op de markt te brengen." Dit gaat verder dan ERP, voegde hij eraan toe, in meer een platform voor bedrijfsinnovatie. Toepassingen zoals MOM, productiebeheer, die het product van ontwerp tot productie brengen via een op samenwerking gebaseerde modelgebaseerde benadering, kunnen de levering van productlanceringen versnellen.
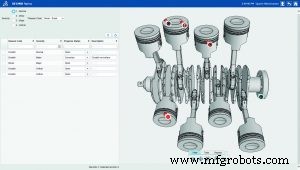
"Voor ons als organisatie zien we dat als een topprioriteit", aldus Green. “MOM is een bredere reeks mogelijkheden dan MES:het omvat meerdere sites, een bredere set en reikwijdte en een breder voorraadbeheer. Wat je ziet is dat verschillende organisaties hun bereik hebben uitgebreid met MOM, en dit sluit aan bij de innovatie die we bieden.”
Het is een belangrijk voordeel om de gebruiker bijna realtime mogelijkheden te bieden. "De waarde die er is omdat we wereldwijde zichtbaarheid hebben, als er wijzigingen zijn, kunnen die wijzigingen worden gepropageerd en worden fouten geëlimineerd."
De Delmia-Apriso-software maakt digitale continuïteit mogelijk, van engineering tot alle aspecten van productie, zei Green. "Het is de mogelijkheid om een virtuele wereld te gebruiken om verschillende scenario's te optimaliseren, zoals modelmix," zei hij. "Door het real-world uitvoeringsmodel en de datum te combineren met de virtuele wereld van engineering, gebruiken we simulatie of optimalisatie om de impact van wijzigingen te beoordelen op basis van echte fabrieksgegevens, voordat we wijzigingen in de fabriek implementeren. Delmia Apriso-software helpt gebruikers zichtbaarheid en controle te bieden over wereldwijde activiteiten om de uitvoering van productie, voorraden en kwaliteit te optimaliseren."
Het Siemens MOM-portfolio omvat MES, Quality, Advanced Scheduling en Manufacturing Intelligence. "Bij deze toepassingen horen oplossingen voor het ontwerp en de simulatie van productiefabrieken, ons Tecnomatix-portfolio en dan natuurlijk IoT en data-analyse met Mindsphere," voegde Brown eraan toe. "We nemen de technische stuklijst en zetten die om in de productiestuklijst en vervolgens een processtuk. Dit is waar MES het overneemt.
"We maken werkinstructies voor elke stap, inclusief kwaliteits- en inspectiestappen, en kunnen die instructies vervolgens naar de operator sturen wanneer een specifiek onderdeel aan de operator op het werkstation wordt gepresenteerd", zei Brown. Of we kunnen specifieke code naar een robotwerkcel sturen op basis van het onderdeel dat aan die werkcel wordt gepresenteerd. In de wereld van massamaatwerk, waar partijgroottes één benaderen, zijn we in staat om cyclustijden en kosten te realiseren die historisch alleen werden gezien met harde automatisering en zeer grote oplagen.”
Siemens heeft ook een nieuwe Automation Gateway-app toegevoegd voor de Simatic IT MES UAF 2.1 die OPC-connectiviteit en directe connectiviteit met Siemens S7-controllers biedt, zei Brown. De app configureert automatiseringsknooppuntobjecten die zijn samengesteld door eigenschappen die zijn verbonden met automatiseringssysteemtags. "Automation Gateway omvat een service die de verbinding met automatiseringssystemen onderhoudt en automatiseringsgegevens synchroniseert", zei hij. "Automatiseringsgegevens worden blootgesteld aan UA-app-opdrachten voor lezen en schrijven, en de app kan zich abonneren op automatiseringsgegevenswijzigingsgebeurtenissen via signaalbeheer."
Meer machine-analyse
Naarmate de vraag naar analyse groeit, zijn er meer keuzemogelijkheden, zoals de nieuwe machineanalyse-oplossingen die Rockwell Automation (Milwaukee) afgelopen najaar op de Rockwell Automation Fair heeft aangekondigd. Deze systemen omvatten Rockwell's FactoryTalk Analytics for Devices en een FactoryTalk for Machines cloudgebaseerde applicatie voor apparatuurbouwers, plus systeem- en bedrijfsanalyses.
Analytics vormt een aanvulling op MES- en ERP-systemen en helpt fabrikanten om de ontluikende gegevens te benutten die afkomstig zijn van sensoren die via het IIoT zijn verbonden. "Mensen blijven praten over Industrie 4.0 en Smart Manufacturing", zegt Todd Montpas, business manager Information Software, Rockwell Automation. "Waar ze echt in geïnteresseerd zijn, is of de technologie uitbreidingen heeft voor de machineprestaties, en waar ze echt om vragen, zijn al die mogelijkheden op het uitvoeringsniveau - we moeten ervoor zorgen dat ze processen hebben die werken."
Veel klanten zijn geïnteresseerd in cloudgebaseerde systemen, voegde hij eraan toe, waarbij hij opmerkte dat sommige grote klanten interesse hebben in de Azure-cloud van Microsoft. “Wat we proberen te doen is een zeer schaalbare aanpak te hebben, met een schaalbare uitvoering, maar ingebouwd in een schaalbare analysestrategie; door er een sensor op te plaatsen, kun je realtime analyses krijgen die je op machineniveau doet, en machine learning om fouten te voorspellen.”
Op de Hannover Messe onthulde GE Digital (Boston) in april haar nieuwe Plant Applications MES-oplossing, gericht op het verbeteren van haar aanbod voor hybride productie-industrieën voor sterk geautomatiseerde productieprocessen. Deze nieuwe versie biedt klanten een nieuwe gebruikersinterface, waarbij gebruik wordt gemaakt van het geavanceerde UX-ontwerp van GE, zodat het operationele personeel de effectiviteit van de apparatuur beter kan analyseren en de onderliggende oorzaken van uitvaltijd kan identificeren.
"Een van de interessante dingen die ik vandaag zie, is dat veel klanten zich willen 'voorbereiden' voor Industrial IoT", zegt Matthew Wells, vice-president Digital Product Management, GE Digital. “Het evolueert, maar het begint zich te nestelen in een concept van een hybride cloud. Het is MES met een Big E [met nadruk op uitvoering]; ze willen dat op locatie draaiende houden. Wat het industriële IoT en de cloud bieden, is een manier om dat aan te vullen.”
Responstijden en de behoefte aan meer dan 99% betrouwbaarheid voor productieactiviteiten hebben fabrikanten ervan weerhouden massaal naar de cloud te gaan, merkte Wells op. “Is 99% betrouwbaarheid genoeg? Veel klanten zullen dat risico voor hun fabrieken niet accepteren, "zei hij. “Wat de cloud echt biedt, is een manier om dieper in de data te duiken. In de cloud kun je geschiedenis opslaan en machine learning doen. Als je de cloud hebt, heb je toegang tot grote hoeveelheden gegevens, en het verhoogt de effectiviteit van je analyses.”
Door op elk moment toegang te krijgen tot meerdere terabytes aan gegevens in de cloud, kunnen fabrikanten volledig gebruikmaken van de Digital Twin, voegde Wells eraan toe, de belangrijkste attractie van het IIoT. "De Digital Twin is een reeks analyses die in feite het gedrag modelleert van machines die constant op de achtergrond draaien en de gegevens aanpassen", aldus Wells. “Dat is echt waar de waarde van het industriële IoT begint. Het is een opkomende markt die snel groeit.”
Automatisering Besturingssysteem
- De digitale fabriek:slimme productie stimuleert industrie 4.0
- Het belang van IIoT in een slimme fabriek
- 5 minuten met PwC over AI en big data in productie
- Knelpunten overwinnen:de kracht van analyses in productie
- Censornet:de toekomst van de maakindustrie veiligstellen
- GE Digital:productie transformeren met Smart MES
- De productie-uitdaging aangaan met data en AI
- GE Digital:operationele inzichten met gegevens en analyses
- De opkomst van digitale platforms in de maakindustrie
- Een vliegende start met digitale transformatie in de productie
- Automatisering en de toekomst van digitale productie?