Hoe 3D-printen de voedingsmiddelen- en drankenindustrie transformeert
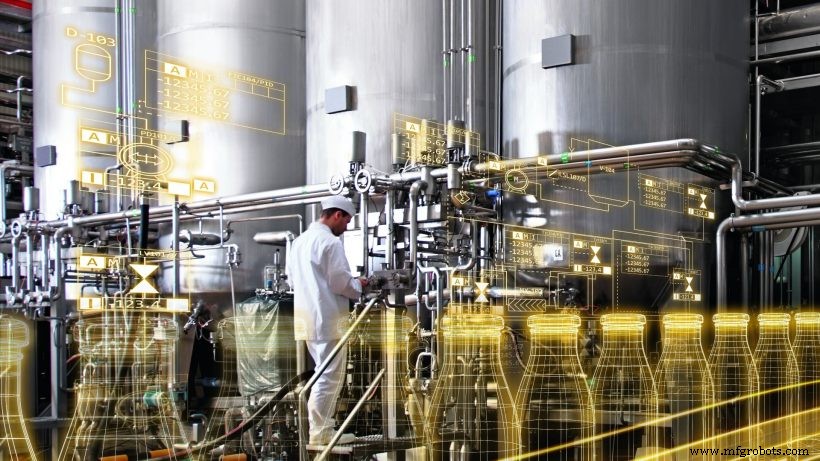
Met steeds veranderende consumenteneisen, instabiliteit van de toeleveringsketen en stijgende kosten, ondergaat de voedings- en drankenindustrie een golf van veranderingen.
Zowel kleine leveranciers, die op zoek zijn naar lagere productiekosten, als grote producenten, die zich richten op nog hogere productievolumes, zijn op zoek naar oplossingen die hen kunnen helpen de dreigende uitdagingen het hoofd te bieden.
3D-printen is een van de technologieën die voedingsmiddelen- en drankenbedrijven integreren in hun productontwikkelingsafdelingen en productielijnen om processen te optimaliseren en kosten te verlagen.
Om u een beter inzicht te geven in de stand van zaken op het gebied van 3D-printen in de voedingsmiddelen- en drankenindustrie, onderzoeken we toepassingsgebieden die het meeste kunnen profiteren van de technologie en lichten we enkele voorbeelden van 3D-printen in actie uit.
Hoe gebruiken voedings- en drankenbedrijven tegenwoordig 3D-printen?
Sneller verpakkingsontwikkeling
In de voedingsmiddelen- en drankenindustrie dienen verpakkingen als de interface tussen een merk en de consument. In wezen trekt een goed verpakkingsontwerp de aandacht van de consument en heeft het invloed op de aankoopbeslissing.
Het ontwikkelen van verpakkingsontwerpen omvat echter meestal meerdere ontwerpiteraties die kostbaar en tijdrovend kunnen zijn. Voedsel- en drankmerken schakelen over op 3D-printen om het ontwikkelingsproces van verpakkingen te versnellen door snellere en economischere productie van ontwerpvariaties.
Dit is mogelijk omdat voor 3D-printen geen mallen of andere hulpmiddelen nodig zijn voor de productie, alleen een ontwerpbestand dat naar een 3D-printer wordt gestuurd en binnen enkele uren wordt vervaardigd.
Vergeleken met conventionele methoden kan 3D-printen bovendien prototypes maken met de kenmerken van het eindproduct en in een verscheidenheid aan kleuren en materialen. Dit stelt voedsel- en drankbedrijven in staat om de look en feel van het eindproduct te testen, waardoor de ontwerpbeoordelingen verder worden verbeterd.
Bijvoorbeeld Thermos, een fabrikant van geïsoleerde voedsel- en drankverpakkingen, gebruikt sinds 2006 3D-printen voor verpakkingsprototypes. Door over te schakelen van het uitbesteden van prototyping-taken naar in-house 3D-printen, verminderde de doorlooptijd voor een prototype van vijf dagen tot enkele uren.
Het bedrijf stelt dat ze met 3D-printen de pasvorm van de dopstopper en de schenkprestaties van hun best verkochte thermosbekers konden optimaliseren.
3D-geprinte reserveonderdelen voor voedsel- en drankfabrieken
Voedsel- en drankbedrijven kunnen de uptime van hun productie verhogen door 3D-printen te gebruiken voor de productie van reserveonderdelen.
De technologie helpt ervoor te zorgen dat bepaalde reserveonderdelen sneller beschikbaar zijn, waardoor ongeplande uitvaltijd wordt voorkomen.
Neem bijvoorbeeld drankvulinstallaties. Dergelijke planten gedijen goed op snelheid, met productiesnelheden tussen 40.000 en 80.000 flessen of blikjes per uur. Dus als een fabriek wordt stilgelegd, neemt de winstgevendheid snel af.
In het ergste geval kan het vinden van het probleem, het aanvragen van een reserveonderdeel, het verzenden en installeren ervan enkele dagen duren. Afhankelijk van de grootte en output van de volledige vullijn, kan een uur productieverlies tussen de $ 4.000 en $ 30.000 kosten.
3D-printen maakt on-demand productie van reserveonderdelen mogelijk, wat helpt om kostbare downtime te verminderen. Door ongeplande uitvaltijd te verminderen, kunnen fabrikanten op hun beurt kostbare investeringen in nieuwe activa uitstellen en de productiviteit verhogen.
Goedkopere ergonomische hulpmiddelen
In-house 3D-printen maakt het mogelijk om gereedschappen voor voedsel- en drankfabrieken sneller te produceren dan met conventionele processen.
Enkele van de tools die geschikt zijn voor 3D-printen zijn:
- Onderhoudstools
- Veiligheidstools
- (de)montagegereedschap
- Ergonomische hulpmiddelen
- Hulpprogramma's voor kwaliteitsborging
- Spacer- en uitlijnhulpmiddelen
Bovendien, aangezien 3D-printen ontwerpflexibiliteit biedt, kunnen gereedschappen ergonomisch worden ontworpen, wat meer gebruiksgemak voor werknemers biedt en de nauwkeurigheid bij het uitvoeren van taken verbetert.
6 voorbeelden van 3D-printen in de voedingsmiddelen- en drankenindustrie
1. 3D-printen helpt Pepsi om verpakkingsontwerp vooruit te helpen
Het wereldwijde merk voor eten en drinken, Pepsi, heeft 3D-printen gebruikt om een replica Black Panther-masker voor frisdrankblikjes te maken als onderdeel van de promotiecampagne voor de film.
Om zo snel mogelijk 250 ingewikkelde maskers te ontwikkelen en te produceren, besloot Pepsi dat het maken van mallen te duur zou zijn. Gezien de ontwerpflexibiliteit en de economische voordelen van kleine oplagen, bood 3D-printen een ideale oplossing.
Door de samenwerking met contractfabrikant Protolabs gebruikte het team materiaalextrusietechnologie om de eerste prototypes van de maskers te maken. Ze hebben enkele wijzigingen aangebracht om ervoor te zorgen dat het ontwerp met de afbeelding op het blik werkte en dat het tijdens verzending veilig zou blijven.
Om de laatste onderdelen te maken, koos het team voor HP's Multi Jet Fusion-technologie vanwege een hoogwaardige oppervlakteafwerking en lagere productiekosten.
In totaal duurde het minder dan zes maanden om van concept tot eindproduct te komen, allemaal dankzij de 3D-printtechnologie. Zowel de Pepsi-blikjes als hun gestroomlijnde 3D-geprinte maskers hebben veel aandacht gekregen voor de film, waarbij de kracht van 3D-printen wordt getoond om innovatieve verpakkingsontwerpen te helpen ontwikkelen.
2. Herontwerp van een onderdeel voor een brouwerijfabriek
Kaspar Schulz, een van de oudste fabrikanten van brouwapparatuur ter wereld, wendde zich tot 3D-printen om de ontwerpflexibiliteit te testen.
In samenwerking met GE Additive heeft Kaspar Schulz een aantal onderdelen geïdentificeerd die zouden kunnen profiteren van een herontwerp. Een daarvan is een onderdeel in een Lauter Tun-vat dat wort - de vloeistof die wordt gewonnen uit het maischen van bier - scheidt van vaste stoffen.
Dit onderdeel wordt de stellingarm genoemd en het team wilde het filtratie-effect van het bed van verbruikte granen in het vat verbeteren.
Om dit doel te bereiken, ontwierpen GE en Kaspar Schulz een dunner mes met interne kanalen, dat de verbruikte granen losmaakt en het water tijdens de rotatie gelijkmatig over het bed verdeelt. Jörg Binkert, hoofd Onderzoek en Ontwikkeling van Kaspar Schulz, gelooft dat deze functie zowel de verwerkingstijd als het rendement zal verbeteren.
Over het algemeen ziet het bedrijf de belangrijkste voordelen van het gebruik van AM bij de functionele integratie van onderdelen, wat helpt het aantal voegen en afdichtingen te verminderen. Deze kansen, ontsloten door de ontwerpflexibiliteit van AM, zullen de weg vrijmaken voor stapsgewijze verbeteringen in het brouwproces.
3. 3D-geprinte grijpers voor een voedselverpakkingslijn
Een andere toepassing voor 3D-printen in de voedingsmiddelen- en drankenindustrie zijn robotgrijpers die worden gebruikt op voedselverwerkingslijnen.
Voedselverwerkingslijnen vereisen vaak oplossingen op maat, en 3D-printen biedt een levensvatbare manier om grijpers te produceren die zijn aangepast aan de specifieke vereisten van deze lijnen.
Bovendien maakt 3D-printen het mogelijk om het gewicht van een grijper te verminderen, wat een reeks voordelen biedt. Een lichtgewicht grijper, met hetzelfde laadvermogen, ondersteunt bijvoorbeeld snellere bewegingen en maakt kortere cyclustijden mogelijk - een belangrijk doel in de productiewereld.
Een bedrijf dat profiteert van 3D-geprinte grijpers is het IJslandse voedselverwerkingsbedrijf Marel. De organisatie werkte samen met het Deense Technologisch Instituut aan de ontwikkeling van nylon grijpers die zijn geïntegreerd in robotarmen die vlees, zoals filets, pakken om het van en van de lopende band te tillen.
Marel ziet het cruciale voordeel van 3D-printen in zijn flexibiliteit:het bedrijf kan grijpers aanpassen voor verschillende klanten zonder de extra kosten van freesgereedschappen. Bovendien kan Marel grijpers bestellen die op aanvraag 3D-geprint kunnen worden, met een levertijd van slechts drie dagen – wat het bedrijf ook helpt om de opslagkosten te verlagen en de wendbaarheid te vergroten.
4. Innovatie van een robotgrijperontwerp
In een ander voorbeeld werkte Langen Group, een leverancier van apparatuur aan een grote Amerikaanse voedselproducent, samen met de 3D-printserviceprovider, Anubis 3D, om lichtgewicht end-of-arm tooling te ontwikkelen.
Deze tool, ontworpen om de robots in staat te stellen verpakte, gestapelde crackers op te pakken en in kartonnen dozen te plaatsen, moest minder dan een kilogram wegen en meerdere verpakkingsvormen en -formaten aankunnen.
Het Anubis 3D-team heeft topologie-optimalisatiesoftware toegepast om een ontwerp te maken dat zowel aan de eisen voldoet als geschikt is voor 3D-printen. Tijdens het optimalisatieproces analyseerden de software-algoritmen spanningen en spanningen op de structuur en pasten de geometrie van een onderdeel aan voor sterkte en lichter gewicht.
Om de grip van het gereedschap verder te vergroten, creëerde het team een nieuw ontwerp, met geprofileerde gaten en kanalen, dat niet conventioneel kon worden vervaardigd.
3D- gedrukt in nylon, met behulp van op poeder gebaseerde 3D-printtechnologie van EOS, bleek het resulterende onderdeel beter dan verwacht. De nieuwe grijper biedt vier keer zoveel grijpkracht als oude vacuümgrijpers, verbruikt minder lucht en heeft meer grijpkracht.
5. Krones ontwikkelt een 3D-geprinte blikjesdraaier
De Duitse fabrikant van verpakkings- en bottelmachines Krones heeft ook laten zien hoe 3D-geprinte onderdelen kunnen worden geïntegreerd in aangepaste machines in de drankenindustrie.
Een voorbeeld van zo'n project betrof een blikjes twister, 3D geprint met een thermoplastisch materiaal. In een brouwerij draait een blikjesdraaier bijvoorbeeld bierblikjes 180 graden verticaal om nadat deze zijn gevuld en gefelst, zodat deze ondersteboven gepasteuriseerd kunnen worden.
Tijdens de ontwikkeling van de 3D- gedrukte component moeten veel verschillende factoren worden geanalyseerd, waaronder de optimale bewegingsvolgorde van de blikken als ze worden omgekeerd.
Het ontwikkelingsteam had verschillende pogingen nodig om een ontwerp te maken dat aan alle vereisten voldeed. Maar dankzij de voordelen van AM was de weg van ontwerp naar daadwerkelijke implementatie kort.
Naast een snellere ontwikkeling, creëert 3D-printen blikjes twisters met een hoge herhaalbaarheid - wat een uitdaging was bij een handmatig bewerkingsproces dat zou resulteren in afwijkingen in de onderdeelgeometrie.
Krones heeft de blikjesdraaier al met succes intern getest, met tot 150.000 blikjes per uur, en verwacht het onderdeel nu te integreren in elk van zijn nieuwe conservenlijnen.
6. Heineken optimaliseert zijn productielijn met 3D-printen
Na ongeveer twee jaar gebruik te hebben gemaakt van 3D-printen, identificeerde Heineken meerdere toepassingen die hielpen de veiligheid en productiviteit van haar activiteiten te verbeteren.
Met behulp van Ultimaker's extrusie 3D-printtechnologie ontdekten de ingenieurs van de Heineken brouwerij in Spanje al snel dat ze veel tijd en geld konden besparen door op maat gemaakte onderdelen en gereedschappen voor de productielijn te 3D-printen .
Een metalen blikjesduwer, die wordt gebruikt om flessen af te wijzen en te sturen, zou bijvoorbeeld aanzienlijk meer kosten en een langere doorlooptijd hebben dan een opnieuw ontworpen plastic 3D-geprint alternatief.
Op dezelfde manier begon het bedrijf met het 3D-printen van een stopper, die de kolommen met geleidingswielen die flesetiketten aanbrengen los en vastmaakt.
Het 3D-printen van de tool resulteerde in een drastische kostenbesparing van 70 procent en een snellere levertijd (van drie dagen tot één) in vergelijking met de vorige methode van CNC-bewerking. Andere, eenvoudigere gereedschappen, zoals een ringkernrubbersnijder, kunnen in minder dan een uur in 3D worden geprint.
Over het algemeen zag de brouwerij verschillende verbeteringen in de productie na de interne invoering van AM. Heineken zei gemiddeld 80 procent snellere levertijden en 80 procent lagere kosten voor onderdelen te ervaren.
3D-printen in de voedingsmiddelen- en drankenindustrie:de aanjager van efficiëntie
De voedingsmiddelen- en drankenindustrie worstelt met veel uitdagingen, en 3D-printen biedt voor sommige daarvan een efficiënte oplossing. Het helpt voedsel- en drankbedrijven om betere verpakkingen te ontwikkelen, wendbaar te blijven met on-demand 3D-printen van reserveonderdelen en gereedschappen, en hun activiteiten te verbeteren met geavanceerde componenten.
In de toekomst zullen we zien dat meer voedsel- en drankbedrijven de technologie onderzoeken om efficiëntie te stimuleren en de uitdagingen van een onzekere toekomst het hoofd te bieden.
3d printen
- De 3 stadia van 3D-printen en hoe ze werken
- De meest voorkomende knelpunten in de 3D-printworkflow - en hoe u ze kunt oplossen
- Hoe verandert 3D-printen de defensie-industrie?
- Hoe verandert 3D-printen de auto-industrie? (2021)
- Hoe 3D-printen de reserveonderdelenindustrie transformeert [update 2021]
- Hoe de 3D-printindustrie helpt de uitdagingen van de coronaviruspandemie aan te pakken
- Een vleugje kleur geven aan de voedingsmiddelen- en drankenindustrie
- Digitalisering en de voedings- en drankenindustrie
- Hoe IoT in de olie- en gasindustrie toe te passen
- Hoe de voedingsmiddelen- en drankenindustrie het chauffeurstekort kan overwinnen
- Hoe 3D-printen wordt gebruikt in de matrijsindustrie