Hoe verandert 3D-printen de auto-industrie? (2021)
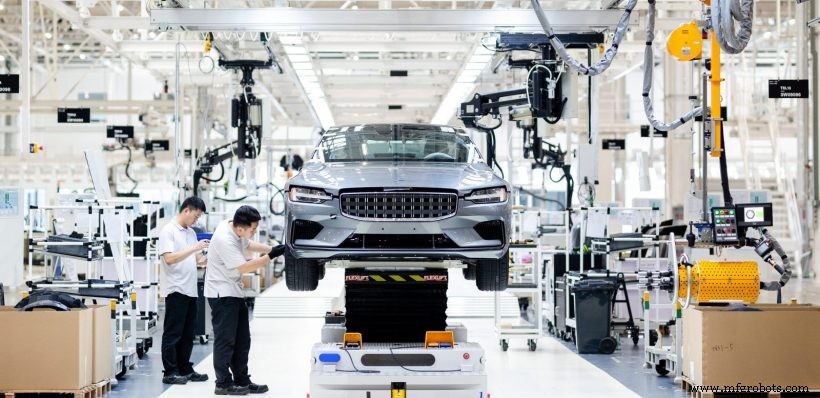
De dagen van 3D-printen als een snelle prototyping-tool voor de auto-industrie zijn voorbij. Vooruitgang in additive manufacturing (AM) betekent dat autofabrikanten tegenwoordig steeds meer 3D-printen in hun productielijnen integreren.
In feite is 94 procent van de belanghebbenden in de automobielsector van plan om hun 3D-printmogelijkheden uit te breiden, zo blijkt uit het onderzoek van Jabil dat in 2018 werd uitgevoerd.
In dit artikel gaan we in op de voordelen die 3D-printen autofabrikanten biedt en onderzoeken we hoe de technologie tegenwoordig wordt geïntegreerd in autoproductieprocessen. Bovendien zullen we kijken naar de huidige uitdagingen van het adopteren van 3D-printen voor auto-onderdelen voor eindgebruik, evenals naar wat de toekomst in petto heeft voor 3D-printen in de automobielsector.
De voordelen van 3D-printen voor de auto-industrie
1. Ontwerpinnovatie
3D-printen kan worden gebruikt om complexe, ingewikkelde ontwerpen te maken die anders niet mogelijk zouden zijn met traditionele productiemethoden. Deze mogelijkheid is met name handig bij het maken van op maat gemaakte functionele onderdelen.
Aangezien gewichtsvermindering een belangrijk aandachtspunt is voor OEM's in de automobielindustrie - lichtere voertuigen hebben doorgaans een lager brandstofverbruik - kunnen ontwerpingenieurs ook profiteren van de combinatie van 3D-printen met tools zoals topologie-optimalisatie en generatief ontwerp. Deze kunnen worden gebruikt om materiaal in bepaalde gebieden te verwijderen en onderdelen te maken met een geoptimaliseerd gewicht en optimale prestaties.
2. Vereenvoudigde montage
Gedeeltelijke consolidatie is een andere manier waarop OEM's in de auto-industrie kunnen profiteren van 3D-printen. Aangezien traditionele productiemethoden de ontwerpvrijheid van 3D-printen missen, moeten er doorgaans meerdere componenten worden geproduceerd om een definitief onderdeel te creëren.
Met onderdeelconsolidatie kunnen meerdere onderdelen van een component in de ontwerpfase in één component worden geïntegreerd. Vanwege de complexiteit kan het geconsolideerde ontwerp vaak alleen worden geproduceerd met behulp van 3D-printen.
Met deze aanpak kan 3D-printen het assemblageproces vereenvoudigen door het aantal benodigde componenten in de assemblagefase te verminderen. Het overwinnen van de behoefte aan meerdere onderdelen helpt zowel het materiaalgebruik als de montagetijd of -kosten te verminderen.
3. Maatwerk
Nu de productie steeds verder neigt naar massaaanpassing, moeten OEM's in de auto-industrie steeds meer manieren vinden om voertuigen te maken die zijn afgestemd op de behoeften van hun klanten. 3D-printen biedt een kosteneffectieve en flexibele manier om op maat gemaakte onderdelen te produceren.
Binnen het luxe- en motorsportsegment van de industrie gebruiken bedrijven de technologie al om gepersonaliseerde onderdelen te produceren voor zowel het interieur als het exterieur van een voertuig.
Het aanbieden van aanpassingsopties aan klanten is een van de manieren waarop autofabrikanten de klantervaring willen verbeteren en hun concurrentievoordeel willen vergroten.
Een segment van de auto-industrie dat 3D-printen heeft geadopteerd voor maatwerk, is dat van luxe voertuigen. In een segment waar kleine oplagen de norm zijn, kan 3D-printen worden gebruikt om in relatief korte tijd onderdelen te maken, toegespitst op specifieke klantwensen.
Mini is een goed voorbeeld:de Duits-Britse automaker schakelde over op 3D-printen om klanten in staat te stellen op maat gemaakte onderdelen te bestellen, zoals sierdelen en deurgrepen.
Porsche 3D-prints op maat gemaakte stoelen
In een ander voorbeeld heeft Porsche een nieuw concept voor sportwagenstoelen geïntroduceerd dat gebruikmaakt van 3D-printen voor maatwerk.
De nieuwe stoelen zijn voorzien van polyurethaan 3D-geprinte centrale zit- en rugleuningkussensecties, die kunnen worden aangepast met drie stevigheidsniveaus:hard, medium en zacht.
Porsche is van plan om al in mei 2020 40 prototypestoelen te printen voor gebruik op Europese racebanen, waarbij feedback van klanten wordt gebruikt om de definitieve straatlegale modellen voor medio 2021 te ontwikkelen.
Over de hele linie wil Porsche de stoelaanpassing verder uitbreiden dan stevigheid en kleur, door de stoel aan te passen aan de specifieke lichaamscontouren van de klant.
Printen heeft het potentieel om het productontwerpstadium te transformeren, waarbij klanten meer inspraak hebben in hoe hun voertuigen eruit zullen zien.
3D-printmaterialen voor automobieltoepassingen
Veel automobieltoepassingen vereisen materialen die taaiheid en vervormbaarheid combineren met hitte- en chemische bestendigheid. 3D-printen met zeer sterke polymeren (nylon, PEEK), kunststoffen (ABS, ASA) en metalen (aluminium, staallegeringen, titanium) zijn daarom de meest voorkomende opties voor het produceren van functionele auto-onderdelen en tooling.
Nu is er ook de mogelijkheid van 3D-printen met koolstofvezelcomposieten, wat een nieuwe deur opent naar het maken van nog lichtere auto-onderdelen.
Integreren van 3D-printen in het autoproductieproces
Productontwikkeling en validatie
Met de mogelijkheid om meerdere ontwerpiteraties in een kortere tijd (en tegen weinig extra kosten) te produceren, is 3D-printen een effectief hulpmiddel voor productontwikkeling. Doorgaans moet een onderdeel verschillende ontwerpcycli doorlopen voordat overeenstemming wordt bereikt over het definitieve ontwerp.
Met 3D-printen kan deze fase drastisch worden versneld. Bovendien kunnen kostenefficiënte ontwerpverbeteringen relatief snel worden doorgevoerd, aangezien de technologie geen dure gereedschappen vereist om een prototype te produceren.
Het gebruik van 3D-printen voor prototyping, testen en prestatievalidatie is momenteel een van de meest populaire toepassingen van de technologie binnen de auto-industrie.
Lage productiekosten, mogelijk gemaakt door 3D-printen, betekenen dat ontwerpingenieurs eerst de pasvorm en functie van een onderdeel kunnen controleren voordat ze investeren in dure en typisch arbeidsintensieve matrijzen voor de productie van eindonderdelen.
Ontwerpverificatie met 3D-printen bij Audi
Voordat een nieuw voertuig in productie gaat, bouwt het Audi Pre-Series Center in Ingolstadt fysieke modellen en prototypes voor het merk, om nieuwe ontwerpen en concepten te kunnen evalueren.
Het gebruik van polymeer 3D-printen is een integraal onderdeel geworden van het auto-ontwerpproces in het Audi Pre-Series Center, waardoor het team beperkingen van conventionele processen kan overwinnen en de ontwerpverificatie kan versnellen.
Neem bijvoorbeeld achterlichtkappen. Traditioneel worden de prototypes van deze onderdelen geproduceerd door middel van frezen of gieten. De grootste uitdaging bij deze productietechnieken is dat de meerkleurige afdekkingen van de achterlichtbehuizing afzonderlijk moeten worden geproduceerd en vervolgens moeten worden gemonteerd. Dit verhoogt de doorlooptijden voor ontwerpverificatie en vertraagt vervolgens de time-to-market.
Door gebruik te maken van de meerkleurige 3D-printtechnologie van Stratasys, kan het team volledig transparante, meerkleurige achterlichtafdekkingen maken in een enkele print, waardoor de noodzaak voor wat voorheen een meerstapsproces was, overbodig werd.
Om achterlichtkappen te produceren, verwacht Audi de doorlooptijd van prototypes met wel 50 procent te verkorten, dankzij 3D-printen.
Tools
Hoewel prototyping de primaire toepassing van 3D-printen binnen de auto-industrie blijft, wint het gebruik van de technologie voor tooling snel aan populariteit.
De assemblagefabriek van Volkswagen Europa gebruikt AM al om in eigen huis gereedschapsuitrusting te produceren, in plaats van deze in te kopen bij externe leveranciers.
Het bedrijf begon in 2014 met het gebruik van 3D-printen voor tooling, voor een proefproject. Het succes van de pilot overtuigde Volkswagen om een groot deel van zijn productie van tooling over te schakelen naar 3D-printen.
Het gebruik van de technologie voor deze applicatie brengt veel voordelen met zich mee.
Door zijn gereedschap intern te produceren, worden de productiekosten van gereedschap voor de autofabrikant met 90 procent verlaagd - en worden de doorlooptijden teruggebracht van weken tot slechts enkele dagen. Om een voorbeeld te noemen:een tool als een badge voor de achterklep zou naar verluidt 35 dagen nodig hebben om te worden ontwikkeld met behulp van traditionele productie en zou tot 400 euro kunnen kosten. Met 3D-printen kan dezelfde tool in vier dagen worden geproduceerd voor slechts € 10.
Het gebruik van 3D-printen voor tooling zou Volkswagen in 2017 bijna € 325.000 hebben bespaard, terwijl de ergonomie, productiviteit en tevredenheid van de machinist zijn verbeterd.
Als het gaat om fabricagehulpmiddelen, groeit 3D-printen snel als alternatief voor meer gevestigde manieren om gereedschappen te vervaardigen. Over een paar jaar zullen we waarschijnlijk meer OEM's in de auto-industrie zien overstappen op 3D-geprinte tooling om de efficiëntie van hun productie en de prestaties van hun tools te verbeteren.
Reserveonderdelen
Autofabrikanten kunnen de voordelen van 3D-printen benutten om on-demand reserveonderdelen te maken.
Met hoge voorraadkosten die gepaard gaan met het opslaan van reserveonderdelen (en vaak zelden bestelde) onderdelen, biedt 3D-printen een kosteneffectieve manier om onderdelen die nodig zijn op tijd en op afroep te produceren, wat leidt tot verbeterde levertijden, lagere voorraadkosten en een vereenvoudigde toeleveringsketen.
Daimler Buses wil reserveonderdelen 3D printen
Begin 2020 maakte Daimler Buses zijn plannen bekend om een nieuw businessmodel te ontwikkelen:het rechtstreeks in eigen huis produceren van reserveonderdelen voor klanten via 3D-printen.
Momenteel onderzoekt het competentiecentrum voor 3D-printen van Daimler Buses meer dan 300.000 reserveonderdelen voor bussen in detail voor dergelijk printen. Tot nu toe zijn er ongeveer 200 geschikt bevonden, zoals deksels, handgrepen en een breed scala aan beugels.
Een van de belangrijkste drijfveren om over te stappen op 3D-printen voor dergelijke onderdelen is de mogelijkheid om de productie en levering van onderdelen te versnellen. Daimler Buses stelt dat deze processen slechts enkele dagen duren in plaats van enkele maanden.
Een bijkomend voordeel van 3D-printen, genoemd door Daimler Buses, is een verbeterde materiaalefficiëntie:de technologie produceert aanzienlijk minder afval en al het ongebruikte materiaal kan onmiddellijk worden gebruikt voor de volgende 3D-printopdracht.
Einddeel productie
Recente ontwikkelingen in AM-technologie en materialen hebben 3D-printen ontgrendeld om kleine en middelgrote onderdelen voor eindgebruik te produceren. Volgens Jabils onderzoek van 2018 onder OEM's in de auto-industrie, denkt 40 procent dat 3D-printen zal helpen bij de productie van auto-onderdelen voor eindgebruik.
3D-geprinte auto-onderdelen voor eindgebruik kunnen variëren van externe componenten tot interne onderdelen, zoals balgen, complexe leidingen, montagebeugels en motorcomponenten.
Een voorbeeld is Ford:vorig jaar kondigde het bedrijf de start aan van de 3D-printproductie van structurele componenten.
De onderdelen in kwestie zijn onder meer Ford Focus HVAC (verwarming, ventilatie en koeling) hefboomarmserviceonderdelen, Ford F-150 Raptor-hulpstekkers en Ford Mustang GT500 elektrische parkeerrembeugels.
Deze componenten zijn geproduceerd met behulp van Carbon's Digital Light Synthesis (DLS) 3D-printtechnologie en EPX (epoxy) 82-materiaal en voldoen aan alle prestatienormen en -vereisten van Ford.
3D-printen in de autosport
Het gebruik van AM als concurrentievoordeel voor de ontwikkeling van racewagens is tegenwoordig de standaardpraktijk.
In de autosport is 3D-printen een onmisbaar hulpmiddel geworden voor het produceren van duurzame en nauwkeurige onderdelen voor windtunneltests. Een ander voordeel is snelheid:als een ontwerpwijziging nodig is, maakt AM het veel sneller om componenten te produceren die in de windtunnel kunnen worden getest.
Veel raceautoteams onderzoeken ook 3D-printen bij de productie van auto-onderdelen voor eindgebruik. Het Alfa Romeo Sauber F1-team 3D print bijvoorbeeld een metalen rolbeugel - een kritieke veiligheidsstructuur die de bestuurder beschermt in geval van een koprol.
Dit onderdeel is met name gemaakt van Scalmalloy, een lichtgewicht metaal dat speciaal voor AM is ontwikkeld. Door dit materiaal te combineren met Selective Laser Melting (SLM)-technologie, kan Sauber F1 een veel lichtere rolbeugel produceren met complexe interne kenmerken voor structurele integriteit. Het is er ook in geslaagd de doorlooptijden van de productie met ongeveer 25 procent te verkorten.
3D-printuitdagingen in de auto-industrie
Massaproductie
Terwijl OEM's in de auto-industrie steeds vaker AM-systemen opnemen in ontwikkeling en productie, vormen de productievolumes een uitdaging voor een bredere acceptatie. Met alleen al in 2019 meer dan 92 miljoen geproduceerde auto's, is de auto-industrie sterk afhankelijk van massaproductie.
In het huidige stadium kan 3D-printen geen onderdelen produceren met het volume en de snelheid die de auto-industrie vereist. De technologie mag daarom geen vervanging zijn voor traditionele productiemethoden, die geschikt zijn voor massavolumes, maar als een aanvullend hulpmiddel voor productie op maat met een lager volume.
Dat gezegd hebbende, ontwikkelen hardwarefabrikanten voor 3D-printen productiemethoden voor grotere volumes om aan de eisen van de auto-industrie te voldoen. Een daarvan is metal binder jetting, ontwikkeld door onder meer HP, Desktop Metal, ExOne en ook GE Additive.
Naast metaal kunnen binder jetting 3D-printers poedervormige materialen, zoals plastic, zand en keramiek en een bindmiddel, gebruiken om snel een onderdeel laag voor laag op te bouwen met behulp van gegevens uit een digitaal ontwerpbestand.
In tegenstelling tot een 3D-printer, die een laser of een elektronenstraal gebruikt en één of twee onderdelen tegelijk maakt, kan een binderjetting-machine bijvoorbeeld tientallen haakjes tegelijk maken, omdat het printoppervlak veel groter is en de lagen veel sneller opgebouwd.
Metaalbinderstralen bevindt zich echter pas in de beginfase van de toepassing ervan in de auto-industrie. Volgens Matthias Schmidt-Lehr, een managing partner bij adviesbureau Ampower GmbH &Co, is de technologie voor binderjetting tussen vijf en tien jaar verwijderd van het kunnen produceren van onderdelen op autovolumes.
Bouwmaten
Een andere uitdaging voor autofabrikanten is de beperkte bouwgrootte van veel AM-systemen. Hoewel grotere onderdelen kunnen worden geproduceerd met 3D-printtechnologie, moet dit in de vorm van modulaire onderdelen. Deze moeten op hun beurt momenteel worden geassembleerd of bevestigd via andere processen, zoals lassen.
Grootschalige additieve fabricage is echter een belangrijk en groeiend onderzoeksgebied, waarbij technologieën die grotere bouwgroottes kunnen ondersteunen, zoals Wire Arc Additive Manufacturing (WAAM) en Big Area Additive Manufacturing (BAAM), actief worden onderzocht en ontwikkeld.
AM-vaardigheidskloof
Extra investeringen in het ontwikkelen van AM-specifieke vaardigheden moeten ook worden aangepakt, wil de technologie een grotere vlucht nemen. Ontwerpen voor AM, evenals de bediening en het onderhoud van AM-systemen, materialen en nabewerking, zijn allemaal essentiële vaardigheden die moeten worden ontwikkeld en gekoesterd.
Hoewel er veel is gezegd over de huidige vaardigheidskloof voor AM, zijn partnerschappen met universiteiten en interne trainingsprogramma's een manier om te zorgen voor een pool van bekwaam talent dat kan werken met de specifieke kenmerken van AM-technologie.
3D-printen in de auto:de weg vooruit
Terwijl autofabrikanten nieuwe toepassingen voor 3D-printen blijven vinden, is één ding duidelijk:het gebruik van 3D-printen voor de productie van eindonderdelen wint steeds meer terrein. Het laatste rapport van SmarTech Analysis, een onderzoeksbureau voor 3D-printen, ondersteunt deze trend door te stellen dat het gebruik van AM voor de autoproductie tegen 2030 een omzet van $ 10 miljard zal worden.
In deze context zal de auto-industrie waarschijnlijk getuige zijn van nog meer 3D-geprinte functionele componenten, zoals beugels, behuizingen en zelfs motoronderdelen.
En misschien een visie op een verre toekomst, het vooruitzicht om een hele auto in 3D te printen is misschien niet zo vergezocht.
De Amerikaanse autofabrikant Local Motors heeft al een 3D-geprinte, autonome elektrische shuttle getest, Ollie genaamd, die is ontworpen voor lokaal vervoer op lage snelheid.
De meeste componenten van Ollie zijn 3D-geprint, inclusief het dak en de onderkant van het voertuig.
Hoewel het enige tijd zal duren om volledig 3D-geprinte voertuigen op de weg te zien, kunnen projecten zoals Ollie van Local Motors ons een stap dichter bij die opwindende mogelijkheid brengen.
3d printen
- 4 manieren waarop 3D-printen de medische industrie transformeert
- Hoe verandert 3D-printen de defensie-industrie?
- Hoe 3D-printen de reserveonderdelenindustrie transformeert [update 2021]
- 10 spannende voorbeelden van 3D-printen in de auto-industrie in 2021
- Hoe de 3D-printindustrie helpt de uitdagingen van de coronaviruspandemie aan te pakken
- Hoe de automobiellogistiek de strijd aangaat met COVID-19
- Hoe IoT-technologie toezicht houdt op activiteiten in de auto-industrie
- Hoe 3D-printen wordt gebruikt in de matrijsindustrie
- 5 manieren waarop 3D-printen de auto-industrie verandert
- Toepassing van 3D-printen in de auto-industrie
- Wat is de grafische industrie?