Interview met experts:Scott DeFelice van Oxford Performance Materials over de evolutie van hoogwaardige polymeren voor 3D-printen
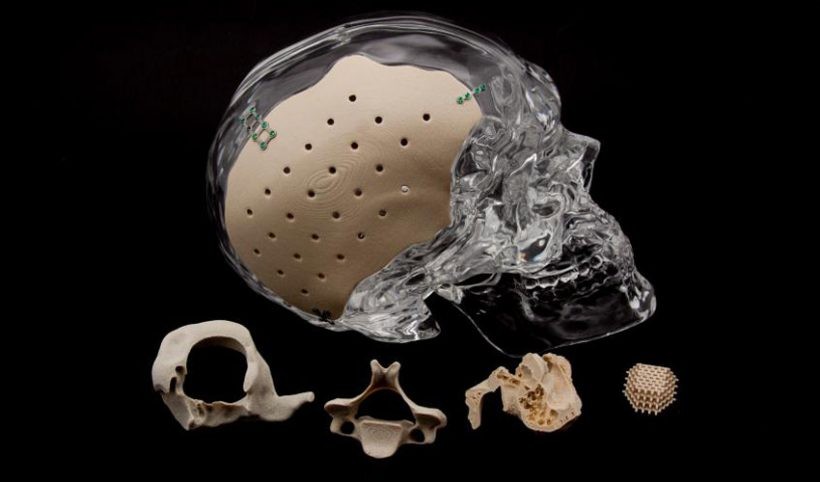
Hoewel polymeren voor algemeen gebruik, zoals ABS en nylon, momenteel de markt voor 3D-printmaterialen domineren, is er een groeiende vraag naar sterke, functionele materialen die bestand zijn tegen ruwe omgevingen en hoge temperaturen.
Deze materialen, bekend als hoogwaardige polymeren, worden steeds meer gevraagd door gebruikers van 3D-printen in sectoren zoals de ruimtevaart en de medische sector.
De belangrijkste hoogwaardige polymeren die momenteel beschikbaar zijn voor 3D-printen, behoren tot de polyaryletherketon (PAEK)-familie van thermoplasten, die stabiliteit bij hoge temperaturen en een grote mechanische sterkte bieden.
Slechts enkele bedrijven op de markt ontwikkelen momenteel dergelijke materialen, waaronder Oxford Performance Materials (OPM).
Gebaseerd in Connecticut, is OPM in het bijzonder gericht op het PEKK-materiaal van de PAEK-familie en heeft het gepatenteerde technologie en apparaten ontwikkeld rond dat thermoplast.
Om meer te weten te komen over OPM en zijn aanbod, hebben we gesproken met de CEO van het bedrijf, Scott DeFelice. Met Scott hebben we de belangrijkste toepassingen voor 3D-geprinte PEKK besproken, evenals trends en uitdagingen die de markt voor 3D-printmaterialen vormgeven.
Kun je me iets vertellen over Oxford Performance Materials en je missie als bedrijf?
Oxford Performance Materials is opgericht in 2000. We zijn een bedrijf in hoogwaardige thermoplastische materialen. We hebben al onze tijd besteed aan een bepaald polymeer genaamd Poly Ether Ketone Ketone of PEKK. En sinds 2000 ontwikkelen we technologieën rond dit materiaal.
PEKK is de top van de thermoplastische voedselketen in de thermoplastische wereld. Het is een super high-performance polymeer vanwege zijn uitstekende thermische, chemische en mechanische eigenschappen en biocompatibiliteit.
Tegenwoordig hebben we een breed portfolio van intellectueel eigendom en patenten die voortkomen uit hoe men PEKK maakt op een synthetische niveau tot hoe men het verwerkt, poeders voorbereidt voor 3D-printen, tot hoe men print met het materiaal.
Op het gebied van 3D-printen zijn onze activiteiten ongeveer 10 jaar geleden begonnen met de ontwikkeling van een selectieve lasersmelt proces naar 3D-printen met PEKK. Rond 2006 lanceerden we onze eerste commerciële 3D-geprinte apparaten voor de medische sector. En dat was het begin van de ontwikkeling van 3D-printen.
In 2008 heeft de FDA ons eerste apparaat goedgekeurd, een schedelimplantaat, dat patiëntspecifiek is en wereldwijd wordt gedistribueerd door Zimmer Biomet. We hebben een doorlopende productie en maken elke dag schedel- en gezichtsimplantaten.
Van daaruit zijn we meer dan drie jaar geleden overgestapt op spinale implantaten, en die producten worden verkocht in samenwerking met een bedrijf genaamd RTI Surgical. We hebben tot nu toe meer dan 70.000 spinale implantaten verzonden.
Onlangs hebben we nog een FDA-goedkeuring ontvangen voor een sportmedische toepassing voor hechtdraadankers, die worden gebruikt om zacht weefsel chirurgisch aan het bot te bevestigen.
Parallel hieraan hebben we onze technologie ontwikkeld en gevalideerd voor gebruik in ruimte- en defensietoepassingen en hebben we certificering ontvangen van onder meer Boeing en Northrop Grumman. Sindsdien hebben we dat bedrijf verkocht aan een van onze strategische partners, Hexcel, die een aanzienlijke schaalgrootte heeft om het te ondersteunen.
OPM komt naar de 3D-printindustrie, niet vanuit het oogpunt van mensen die bijvoorbeeld aan het prototypen waren en vervolgens overgingen naar productieonderdelen. We benaderen het vanuit het oogpunt van een bedrijf in geavanceerde materialen dat ontdekte dat hun materiaal om interessante technische redenen zeer goed zou zijn voor additieve productie. We zijn nu verticaal geïntegreerd in die bedrijven en blijven ons materialen- en technologieplatform exploiteren.
Hoe zie je dat de ruimte voor 3D-printmateriaal zich in de loop der jaren heeft ontwikkeld, en waar zie je dat traject gaan in termen van materiaalkosten en materiaalontwikkeling?
3D-printen is een proces, en wat dat proces uniek en mogelijk maakt, is het materiaal dat ermee wordt gebruikt. Ik zeg altijd tegen mensen dat je een appel kunt printen, maar dan moet je hem opeten. U moet dus printen met materialen die de functionaliteit hebben voor de eindmarkten en het beoogde eindgebruik.
We hebben gezien hoe bijvoorbeeld metaal AM in de loop der jaren erg populair is geworden omdat het functionele eigenschappen heeft die nuttig zijn in specifieke eindmarkten.
Ik denk dat deze trend doorzet. Materialen - polymeren, metalen en andere - zullen blijven evolueren om meer functionaliteit mogelijk te maken in de eindgebruiksmarkten, ongeacht wat die markten zijn.
Het interessante aan kosten is dat er altijd een discussie is geweest over 'O, de materialen zijn te duur'. Ik beargumenteer dat naarmate je je in de beter presterende eindmarkten begeeft en materialen capabeler worden, de materiaalkosten zelf eigenlijk minder belangrijk worden.
We verkopen bijvoorbeeld orthopedische implantaten en wanneer we een schedelimplantaat in het ziekenhuis verkopen, kan dat implantaat voor $ 10.000 worden verkocht. Maar als we kijken naar de kosten van wat we doen, zijn de materiaalkosten eigenlijk een vrij klein onderdeel van de kosten. De rest is allemaal de kwaliteit en de regelgeving, de productiesystemen die men moet hebben om te verkopen op een sterk gereguleerde markt, of het nu een biomedische markt is of ruimte- en defensie- of halfgeleiders.
Dus, naarmate de industrie steeds verder evolueert van de productie van prototypes naar producten voor eindgebruik, zijn de prestaties van het materiaal van cruciaal belang en wordt de component van de materiaalkosten minder een drijfveer.
/>
Kun je, naast de medische sector, uitbreiden naar andere industrieën die kunnen profiteren van de materialen die je ontwikkelt voor 3D-printen?
We zijn begonnen op de voor de hand liggende plaatsen, biomedisch en ruimtevaart, omdat we een lange traditie hebben in onze dienstverlening aan die markten. Maar nu steken we ons hoofd omhoog en kijken we om ons heen naar andere gebieden.
De eindmarkten zijn zeer specifiek voor de prestaties van onze materialen. Ons PEKK-materiaal houdt bijvoorbeeld van zure en basische omgevingen, dus dat is waar we naartoe gaan als het gaat om het milieu. Dus een gebied dat we vrij nauwkeurig volgen, is bijvoorbeeld het vastleggen van koolstof.
Het afvangen van koolstof is een technologie die tegenwoordig werkt, maar de kapitaalkosten van die fabrieken zijn te duur.
Dus we hebben naar dat gebied gekeken en er zijn veel mogelijkheden voor onze materialen en 3D-printen in die ruimte. Binnenkort kondigen we een samenwerking aan met een van de toonaangevende overheidslaboratoria van de VS op dat gebied.
We houden ook van de farmaceutische proces- en bioprocesgebieden waar u een materiaal wilt met de juiste eigenschappen van ons polymeer om de procesefficiëntie te verbeteren en de kapitaalkosten te verlagen.
Het is duidelijk dat met de huidige COVID-19-situatie sommige van deze processen moeten worden geschaald en dat je veel complexe structuren en de juiste hoogzuivere chemie nodig hebt om in die ruimte te oefenen. We volgen dat ook vrij nauwkeurig.
De Polyketonen-klasse van polymeren doet een aantal zeer interessante taken.
We hebben vele miljoenen dollars uitgegeven om inzicht te krijgen in de prestaties van onze 3D-geprinte onderdelen. Daarom vliegen onze onderdelen in bemande ruimtevaartuigen, daarom hebben we duizenden onderdelen in het menselijk lichaam. Het is omdat we het uitputtende werk hebben gedaan om te karakteriseren wat we printen tot het comfort van mensen die heel serieus nemen wat deze structuren in de praktijk doen.
Hoe ziet dat proces van het ontwikkelen en testen van materiaal voor 3D-printen eruit?
Er zijn over het algemeen twee delen. Wanneer we materiaal en een proces ontwikkelen, ondergaan we een interne beoordeling, die over het algemeen gaat van analytische methoden die we in de loop der jaren hebben ontwikkeld tot vrij conventionele mechanische, thermische, elektrische screeningtests die op ontwikkelingsniveau worden uitgevoerd.
Zodra je de baseline hebt en zegt 'Ja, dit is een reproduceerbaar product en we begrijpen het', kom je bij de eerste base.
Om thuis te komen, moet je in elke branche gaan, of je nu aan het printen, gieten of bewerken bent of wat je procestechnologie ook is. Elke branche kent manieren om prestaties te begrijpen, of dat nu een ASTM-norm, een ISO-norm of een bedrijfsspecifieke norm is, of een overheidsnorm.
We hebben een goed voorbeeld in de luchtvaartindustrie. Nadat we al dat werk hadden gedaan en ervoor hadden gezorgd dat we een stabiel en herhaalbaar proces hadden, moesten we iets doen dat een MIL 17-standaard was die resulteert in een statistische beoordeling van prestaties met een zeer hoge voorspelbaarheid, en dat wordt de B-Basis genoemd.
Maar dat programma alleen al liep meerdere jaren en vergde miljoenen dollars. Dat deden we in samenwerking met NASA en Northrop Grumman, en dus was het een vrij uitputtende branchespecifieke beoordeling.
In de biomedische sector, als we het geval van onze spinale implantaten nemen, onderging het eerst een uitgebreide reeks ISO 10993-tests die de biocompatibiliteit en zuiverheid echt beoordelen. Zodra u dat vakje aanvinkt in 'Oké, het materiaal zoals afgedrukt is puur en biocompatibel, niet giftig', dan willen we het nu gebruiken in een ruggengraatimplantaat.
Er is een hele andere reeks mechanische tests als onderdeel van de ASTM F2077-standaard die specifiek zijn voor spinale implantaten. Als je daar doorheen bent, kun je met die gegevens een aanvraag indienen bij de FDA.
Dus je moet eerst je eigen interne testen doen om je comfortabel te voelen, omdat deze andere testregimes erg duur zijn. En dat wil je niet doen, tenzij je er een groot vertrouwen in hebt dat je die tests zult doorstaan.
Dat geldt voor elke eindmarkt, vooral in onze materiaalklasse. Voor technische materialen zijn de normen lager omdat het risico dat gepaard gaat met de acceptatie door het eindgebruik lager is.
Het is bekend dat polymeren in bepaalde toepassingen worden gebruikt om metalen te vervangen. Kunt u voorbeelden geven van hoe hoogwaardige polymeren metalen materialen hebben kunnen vervangen?
Als we 30 jaar geleden teruggaan, hebben we een gestage vooruitgang gezien van polymere materialen die metaal vervangen. Als je in de jaren 70 een auto zou kopen, wogen auto's twee keer zoveel als een auto vandaag weegt en bijna alles zou van metaal zijn, of als je een stofzuiger zou kopen, zou hij van metaal zijn gemaakt.
Als je die dingen nu koopt, vormen ze een fractie van het gewicht en zijn ze grotendeels van plastic. Dus deze trend van polymeren die metalen vervangen voor verschillende functies is zeer goed ingeburgerd.
3D-printen is gewoon een ander proces waarbij je metalen kunt vervangen en de redenen voor het vervangen van metalen zijn kosten, gewicht en corrosie.
We zijn voortdurend op zoek naar mogelijkheden voor metaalvervanging om de kosten voor mensen te verlagen, het gewicht te verminderen en de efficiëntie van apparaten te verbeteren. Goede voorbeelden daarvan zijn ruggengraatkooien, fusie-apparaten die je ruggengraat samensmelten als je chronische pijn hebt.
Deze apparaten waren van oudsher gemaakt van machinaal bewerkt titanium en nu printen we ze met PEKK.
Een ander voorbeeld is dat schedelimplantaten worden gemaakt van 3D-geprint titanium. Vandaag maken we ze van 3D-geprint PEKK.
Als we kijken naar een aantal zaken in het afvangen van koolstof, is dat precies waar we nu naar kijken:het vervangen van zeer duur machinaal bewerkt roestvrij staal of titanium door 3D-geprint PEKK.
Dus dit idee om over te schakelen van metalen naar polymeren is al geruime tijd een megatrend in de industrie. Het is de afgelopen jaren steeds sneller gegaan en 3D-printen maakt nu deel uit van dat grotere verhaal, inclusief gebieden zoals olie &gas en transport, waar we ontwikkelingsprojecten in een vroeg stadium hebben met industriële partners.
Over trends gesproken, zie je trends op het gebied van 3D-printmaterialen?
Aan de metaalkant zien we mensen die metal AM naar meer bekende en voorspelbare morfologieën proberen te drijven.
Ik wil niet te technisch worden, maar 3D-printen van metaal is niet het morele equivalent van ruw, of gesmeed of gegoten metaal. Het is een ander beest.
Toen de industrie voor het eerst erg populair werd, was daar veel verwarring over. Na verloop van tijd hebben mensen zich gerealiseerd dat het een ander dier is. En nu werken ze aan de materiaal- en procestechnologieën die metaal AM op de een of andere manier conventioneler maken. Ik denk dat het metal AM aanzienlijk zal bevorderen.
Aan de polymeerzijde is er nu de algemene tendens om eindmarkten te bedienen met polymeer AM. De twee dominante materialen hiervoor zijn Nylon 11 en Nylon 12. Dit zijn technische materialen en bevinden zich in het midden van de polymeerpiramide.
Ze hebben echter een beperkt eindgebruik. Ze zijn niet bijzonder thermisch of mechanisch robuust.
Nu beginnen mensen erachter te komen hoe ze de piramide kunnen beklimmen. We beginnen bedrijven zoals BASF Nylon 6 te zien introduceren, die iets meer prestaties kopen.
Ik denk dat we die trend zullen blijven zien van meer materialen die verschijnen tussen waar OPM staat met PEKK en andere materialen in het midden van de prestatiepiramide.
Als keerzijde, wat zijn enkele van de uitdagingen waar de sector 3D-printmaterialen nog steeds voor staat?
Dit is een fundamentele vraag.
Toen we vele jaren geleden begonnen te kijken naar 3D-printen, was een van de dingen waar we naar keken:heeft ons polymeer de basiseigenschappen om 3D te printen? En die vraag komt neer op de erkenning dat 3D-printen een consolidatieproces zonder druk is.
Als je een polymeer kneedt, stamp je het in een mal en knijp je alles samen en krijg je deze consolidatie. Dit resulteert in voorspelbare prestaties en goede mechanische eigenschappen.
3D-printen heeft die deugd niet. Met 3D-printen heb je deze lagedrukconsolidatie of nuldrukconsolidatie zoals een FDM-proces waarbij je een filament hebt dat wordt gesmolten en op elkaar wordt gelegd. In dat proces krijg je tot 10 procent holtes, en in mijn wereld zijn holtes slecht, omdat ze betekenen dat een onderdeel niet robuust is. Het is geweldig voor een prototype, maar je wilt er niet aan blijven hangen.
Dan heb je deze poederbedprocessen zoals OPM's, waarbij lasers de ene laag poeder op de andere smelten, maar er is geen druk. Waar u op vertrouwt om herhaalbare prestaties te krijgen in dit soort omgevingen, is een polymeer dat graag aan zichzelf blijft plakken.
Als een polymeer niet goed hecht, krijg je slechte prestaties in de Z-richting.
PEKK is daarin echt uniek omdat het de affiniteit heeft om aan zichzelf vast te houden. Dat is vrij ongebruikelijk in de polymeerwereld.
Om je vraag te beantwoorden:wat de zaken heeft tegengehouden, is de ontwikkeling van een fundamenteel nieuwe chemie.
Als je vandaag naar een van de grote chemische bedrijven gaat en zegt:'Kun je een polymeer ontwikkelen dat speciaal is bedoeld om aan zichzelf te kleven?' Ze zullen je raar aankijken omdat je in het bereik van miljarden dollars en een aantal jaren om nieuwe polymeren te ontwikkelen. Het is een groot probleem.
Als je een adviseur van een polymeerbedrijf vraagt hoeveel echt nieuwe chemicaliën er de afgelopen 20 jaar zijn ontwikkeld, leg je het waarschijnlijk op één hand, omdat die investeringen zo substantieel zijn. En het Amerikaanse bedrijfsleven heeft gewoon niet zo vaak trek in dat soort dingen. Het is dus een grote uitdaging en ik zie dat eerlijk gezegd niet veel gebeuren.
Denk je dat dat de komende maanden en jaren zal veranderen of evolueren?
Nieuwe materiaalplatforms gebaseerd op nieuwe nieuwe chemie? Ik denk niet dat dat gaat gebeuren. Dat is erg afgelegen.
Procestechnologieën zullen vooruitgaan en mensen zullen die bestaande materiaalsets aanpassen met andere unieke vulstoffen en compatibilisatoren en maatbepalingen om dingen te verbeteren. Dus ik denk dat daar de dingen waarschijnlijk interessanter zullen worden.
Wat brengt het komende jaar voor OPM?
We hebben het geluk dat we in een deel van deze branche zitten, waar we op dit moment niet afhankelijk zijn van R&D-contracten of durfkapitaal.
We zitten in het deel van de "noodeconomie".
Hoewel we hebben gezien dat we door deze eerste fase van de COVID-pandemie de beschikbaarheid van ziekenhuizen zijn gedaald voor service en weg van electieve chirurgie, beginnen we nu al te zien dat het bedrijf terug begint te komen .
Het is voor elk bedrijf pijnlijk geweest, maar met de kerntechnologie die we hebben, kunnen we blijven groeien. We introduceren nu net ons hechtdraadankerproduct, een nieuwe, goedkopere productlijn, en zelfs gezien COVID zullen we kansen hebben om dat op de markt te brengen.
We hebben ook onze verantwoordelijkheid nieuwe markten. We houden van de koolstofafvangmarkt, andere industriële gebieden en de markt voor biofarmaceutische processen.
Ik denk dat COVID-19 in sommige opzichten meer kapitaal aanjaagt en meer efficiëntie eist voor de markten waarvoor we van nature geschikt zijn , gezien de prestaties van onze materialen.
Enige laatste gedachten?
Het enige wat ik zou willen zeggen is dat deze specifieke tijd substantiële kansen biedt.
Ik denk dat we als bedrijf in 3D-printen hebben geprobeerd technologieën te pushen die echt waarde toevoegen . In uitdagende en krappe tijden, zoals nu, beginnen mensen te zoeken naar manieren om de kosten te verlagen en nieuwe markten te penetreren. CEO's gaan naar hun CTO en zeggen:'Hé, wat heb je voor mij? We hebben iets nieuws nodig'.
Dus als je echt iets inhoudelijks hebt, niet zomaar een andere manier om een prototype te maken, als je iets hebt dat de boog van technologie op een inhoudelijke manier buigt, ga je om nu goed naar te luisteren.
We hebben gezien dat in ons bedrijf waar we in het verleden op sommige deuren hebben geklopt, mensen er niet klaar voor waren om het te horen. En we beginnen nu die callbacks te krijgen die zeggen:'Hé, vertel ons over dat ding waar we wat geld kunnen besparen of iets efficiënter kunnen doen'.
Dus ik zou lezers willen aanmoedigen om niet moedeloos te worden als ze echte technologie hebben. Het verandert het spel echt. Dit is een interessante tijd.
3d printen
- Scalmalloy:het nieuwste hoogwaardige materiaal voor 3D-metaalprinten
- ULTEM &PEEK:de ultieme gids voor hoogwaardige 3D-afdrukmaterialen
- Expertinterview:Nanoe CEO Guillaume de Calan over de toekomst van keramisch 3D-printen
- Expert Interview:Ultimaker President John Kawola over de toekomst van 3D-printen
- Expertinterview:Armin Wiedenegger, voestalpine High Performance Metals GmbH
- Hoe Ford Motor Company 3D-printen voor de auto-industrie innoveert:interview met experts van Harold Sears
- Interview met expert:Simon Fried, medeoprichter van Nano Dimension over de opkomst van 3D-printen voor elektronica
- Interview met expert:CEO van PostProcess Technologies over het oplossen van het knelpunt in de nabewerking voor additieve productie
- Interview met experts:Brian Alexander van Solvay over de ontwikkeling van hoogwaardige polymeren voor 3D-printen
- Expert Interview:Jabil's Rush LaSelle over de toekomst van additieve productie
- De evolutie van medische materialen