Interview met expert:Oerlikon's hoofdingenieur voor AM, Matthew Donovan, over 3D-printen voor ruimtevaart
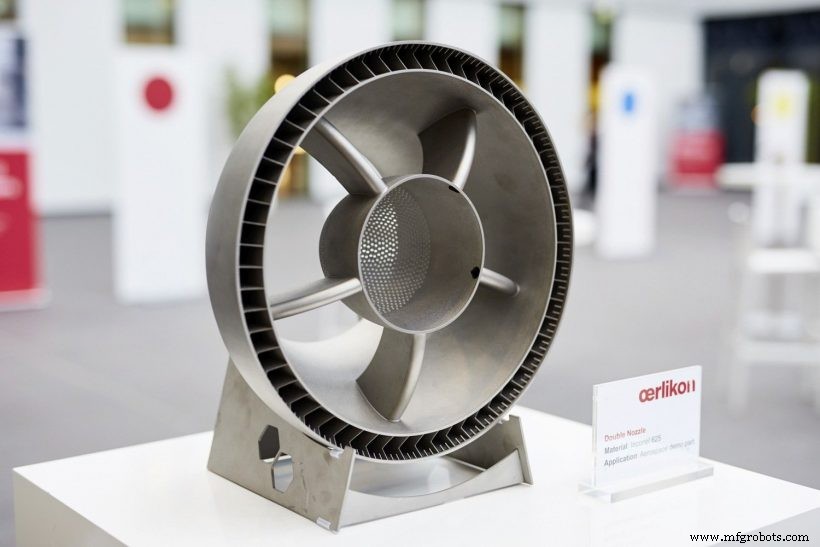
Oerlikon, een wereldwijde technologie- en engineeringgroep, bedient enkele van de meest veiligheidskritieke industrieën, waaronder ruimtevaart en defensie . Additieve productie is in toenemende mate een belangrijk onderdeel van zijn aanbod geworden, waarbij het bedrijf eerder dit jaar een Innovation Hub &Advanced Component Production-faciliteit ter waarde van $ 55 miljoen in de VS heeft opgericht.
In het expertinterview van deze week zitten we met Matthew Donovan, hoofdingenieur voor additieve productie bij Oerlikon, om te bespreken hoe het bedrijf een end-to-end AM-productiefaciliteit blijft ontwikkelen, opwindende AM-trends om kijk uit voor en waarom normen van cruciaal belang zijn voor de toekomst van de industrie.
Kun je me iets over Oerlikon vertellen?
Oerlikon is een wereldwijd bedrijf en een productieleider in zowel de Surface Solutions- als de Manmade Fibers-segmenten. Oerlikon AM, onderdeel van het Surface Solutions-segment, biedt oplossingen voor additieve productie, van metaalpoeders tot prototyping en serieproductie.
Hoe kwam je voor het eerst in aanraking met additive manufacturing?
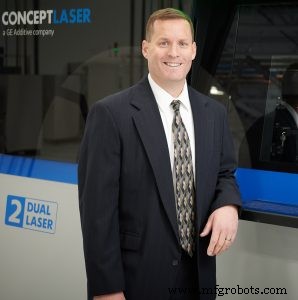
Mijn achtergrond ligt in de ruimtevaart. Voordat ik naar Oerlikon kwam, heb ik de afgelopen 20 jaar voornamelijk gewerkt aan gasturbinemotoren, componenten voor hete secties en componenten voor verbrandingssecties.
Ik heb een achtergrond in brandstoftoevoersystemen, voornamelijk voor ruimtevaartgasturbinemotoren, maar ook voor industriële gasturbines en brandstofcelreformers. Ik heb ook gewerkt aan verschillende R&D-inspanningen met NASA en andere bedrijven. Ik heb dus ervaring met het werken met zeer sterke materialen bij hoge temperaturen voor zeer veeleisende omgevingen.
Ik begon als productie-ingenieur en leerde de ins en outs van het vervaardigen en bouwen van onderdelen en besteedde tijd als kwaliteitsingenieur die veldonderzoeken deed voor diezelfde componenten.
In 2006 begon ik te werken in geavanceerde productie. Ik begon uitdagende geometrieën en componenten tegen te komen die we niet echt konden maken met conventionele productie.
Op dat moment werkte ik met Morris Technologies aan metalen 3D-geprinte componenten. We zijn begonnen met het ontwikkelen van componenten voor brandstofinjectoren met behulp van additive manufacturing.
In de loop der jaren heb ik een aantal componenten ontwikkeld met behulp van additive manufacturing. Ik werkte voor United Technologies en assisteerde de hele onderneming bij het ontwikkelen en implementeren van AM-technologieën, voornamelijk met een focus op hardware voor vluchtcertificering.
Terwijl we bezig waren deze componenten te implementeren, ontdekte ik een van de grootste hiaten dat er een compleet gebrek was aan normen voor het maken van onderdelen en hoe men ze certificeert.
Veel van de kosten in verband met ruimtevaart zijn niet noodzakelijk de componenten zelf, maar de certificering. We moeten volledige traceerbaarheid bieden voor elk onderdeel dat we maken. Het was een hele uitdaging om de normen te ontwikkelen voor hoe we dat doen en dat te implementeren voor additieven.
Ik begon rond 2009 te werken aan AM-normen met ASTM F42. Ik heb geholpen bij het opstellen van enkele normen en heb vervolgens in een paar commissies gezeten. Ik was co-auteur van de ontwerpgids voor metaalpoederbedfusie door laser, ISO ASTM 52911, met ISO/TC 261 en ASTM F42.
Door dat werk met United Technologies, door met veel zeer getalenteerde mensen te werken en toegang te hebben tot een aantal geweldige bronnen, hebben we verschillende innovaties kunnen bedenken en een aantal echt toonaangevende producten voor AM kunnen ontwikkelen. metalen poederbed.
Wat houdt je rol bij Oerlikon in?
Ik ben in 2017 bij Oerlikon begonnen en mijn rol is nu Principal Engineer voor AM. Mijn rol was sterk gericht op de implementatie en ontwikkeling van productieklare AM-metaaltechnologieën.
We zijn begonnen als een start-up divisie van de Surface Solutions Group. We hebben een nieuwe faciliteit gebouwd in Huntersville, North Carolina, waar we iets minder dan een jaar geleden naar verhuisden.
Het is een faciliteit van 120.000 vierkante meter die momenteel 18 metalen poederbedsystemen exploiteert. Ter plaatse hebben we HIP (Hot Isostatic Pressing) en vacuümovenmogelijkheden, evenals mogelijkheden voor nabewerking, poederbehandeling en inspectie.
Het doel was om van deze faciliteit een echte end-to-end AM-productieworkflow te maken, met controle over elk aspect van de toeleveringsketen, zodat we traceerbaarheid voor onze klanten kunnen bieden.
Mijn rol daarin was voornamelijk in machinecertificering. Ik werk nauw samen met de machine-OEM's bij de installatie en kwalificatie van onze machines en zorg ervoor dat ze gecertificeerd worden voor hun capaciteit en cross-capability voor componenten van verschillende machines.
We zijn dan in staat om de machinecapaciteiten, de tolerantie en de precisie van een individuele machine te begrijpen om geometrische tolerantie van een AM-component en de verschillen tussen onze machines te produceren en deze vervolgens af te stemmen zodat we kunnen leveren hetzelfde product op meerdere machines.
Standaardisering is een heel belangrijk gespreksonderwerp geweest, vooral voor industrieën zoals de lucht- en ruimtevaart. Hoe hebben de zaken zich ontwikkeld in de tijd dat u bij de branche betrokken bent geweest en wat is de huidige status van AM-standaardisatie?
Er zijn een aantal zeer goede ontwikkelingen geweest.
We hebben normen nodig, vooral in de ruimtevaart, maar ook op andere veiligheidskritieke gebieden zoals medisch, nucleair en energie. Het belangrijkste van standaarden is dat iedereen dezelfde taal kan spreken en begrijpen waartoe een product in staat is.
Bij het ontbreken van standaarden was iedereen effectief onderdelen aan het bouwen en hun werk op vaak vergelijkbare manieren uit, maar niet op dezelfde manier. Ze spraken niet dezelfde taal. Het is heel gewoon dat mensen naar verschillende termen verwijzen om hetzelfde proces aan te duiden, of naar dezelfde term verwijzen en radicaal verschillende processen bedoelen.
Door standaarden te ontwikkelen, kunt u over de hele linie in dezelfde taal praten en begrijpen wat u bedoelt als u verwijst naar bijvoorbeeld een kwalificatie-opbouw, een kwalificatieniveau voor grondstoffen of machines.
Als u in de lucht- en ruimtevaart geen norm heeft waarmee u een onderdeel kunt certificeren tegen of typisch, meerdere normen om het onderdeel dat u maakt, de mechanische eigenschappen, prestaties en toleranties te identificeren en om in staat zijn om het terug te traceren naar het oorspronkelijke lot waar het vandaan kwam, helemaal terug naar de chemische samenstelling van de elementen die erin gingen, dan kun je het niet op een ruimtevaartplatform zetten.
We kunnen ongelooflijk complexe geometrieën maken en onderdelen maken met AM die fysiek gewoon niet op een andere manier mogelijk zijn. We kunnen veel gewicht, tijd, materiaal en kosten besparen door onderdelen via AM te maken.
De ontwerp- en fabricagevrijheid die AM ons biedt, is duidelijk. Maar het nadeel is dat het geweldig is als je het onderdeel kunt maken, maar als je niet kunt bewijzen dat het een goed onderdeel is, doet het niemand goed.
Normen zijn wat ons over die grens brengt om onderdelen te kunnen produceren en verkopen en deze te kunnen gebruiken in de productie voor de lucht- en ruimtevaart.
Lucht- en ruimtevaartnormen zijn dus een van de belangrijkste puzzelstukjes voordat je onderdelen kunt maken.
Er zijn verschillende ontwikkelingsorganisaties die al heel lang heel hard werken op dit gebied. Ik werk nu ongeveer 10 jaar als vrijwilliger aan ASTM-normen en ik heb de voordelen gezien van wat we doen.
Zoals ik al zei, heb ik bijgedragen aan de originele titaniumstandaard voor poederbedfusie. Die eerste kostte me (en verschillende andere mensen), iets meer dan twee jaar om die eerste gevalideerd te krijgen. Vervolgens hebben we in ongeveer de helft van die tijd extra kunnen omdraaien.
Het begint nu echt te versnellen. ASTM lanceerde onlangs zijn Center of Excellence, gevestigd in Auburn, Alabama, in samenwerking met Auburn University.
De bedoeling hierachter was om gerichte onderzoeks- en ontwikkelingsfinanciering en inspanningen via samenwerkingspartners toe te passen om snel tot meer standaarden te komen. Er is veel samenwerking geweest tussen de industrie en de overheidsinstanties om de hiaten en normen te identificeren die we in de industrie waarnemen, en dat is wat we nodig hebben om vooruit te komen.
Je hebt misschien wel eens gehoord van de ANSI-roadmap. Het is een zeer goed document waaraan sommigen van ons in de industrie hebben bijgedragen, om te identificeren wat onze belangrijkste lacunes zijn die we moeten opvullen om echte productie voor additieve productie te bereiken.
In de nieuwste versie van die routekaart waren er volgens mij 91 hiaten, voornamelijk op standaardgebieden, en sommige daarvan hebben een zeer hoge prioriteit. Het ASTM Center of Excellence is een voertuig dat wordt gebruikt om R&D toe te passen om die hiaten in de normen te dichten.
Op een ander gebied heeft SAE International zijn Aerospace Materials Specification (AMS). De eersten voor additieve poederbedfusie waren AMS 7000, 7001, 7002 en 7003 voor nikkellegering 625, die onlangs werd uitgebracht.
Dat zijn uitstekende oeuvres die veel resultaten zullen opleveren. Velen van ons gebruiken deze normen al om productieonderdelen te ontwikkelen.
Wat waren enkele van de uitdagingen bij de interne integratie van de technologie, gezien uw ervaring met het adopteren van AM, en hoe heeft u dat proces doorlopen?
Oerlikon AM heeft zich ten doel gesteld om AM-oplossingen te bieden die voldoen aan de eisen van de meest veeleisende industrieën, zoals de lucht- en ruimtevaart en de medische sector.
Over onze verschillende faciliteiten beschikken we over de juiste kwaliteitssystemen, zoals AS9100 voor ruimtevaart en ISO 13485 voor medisch. Maar wat betreft het integreren van alle systemen die nodig zijn om daar te komen, dat was een uitdaging, hoewel er enkele oplossingen zijn die stukjes van de puzzel bieden.
Ik zou zeggen dat er niet één oplossing is die elk aspect van wat we nodig hebben, van begin tot eind dekt. Maar er zijn veel goede tools die delen van die hele end-to-end supply chain bestrijken.
Dus een van onze uitdagingen is om de oplossingen te identificeren die verschillende aspecten van onze supply chain bestrijken, aan boord die de aspecten dekken die we nodig hebben en integreer ze.
Sommige oplossingen gaan bijvoorbeeld heel goed om met financiën en inventaris, maar ze doen het niet erg goed voor productieworkflows. Anderen gaan goed om met productieworkflows en productieplanning, maar niet met bijvoorbeeld schattingen van de bouwtijd, materiaalbeoordeling of problemen met geometrische componenten, zoals blauwdrukken en 3D-modellen.
Er zijn er dus veel van verschillende aspecten, en onze uitdaging is om al die verschillende onderdelen te integreren om een naadloze end-to-end oplossing te hebben. Het is momenteel een vrij handmatig proces, maar we werken eraan om het naarmate we verder gaan veel meer geautomatiseerd te maken.
Kun je succesverhalen delen over hoe je AM in productie hebt gebruikt?
Hoewel ik niet specifiek naar die klanten kan verwijzen zonder hun toestemming te krijgen, hebben we verschillende componenten die actief in productie zijn. Sommige die ik zo uit mijn hoofd kan bedenken, zijn ruimtevaart- en defensiegerelateerde componenten.
Dus een is een vluchtcomponent die deel uitmaakt van een missiesysteem op een militaire helikopter. We zijn nu twee jaar in productie voor dat onderdeel en hebben tot nu toe met succes meer dan 200 eenheden geleverd.
We maken ook een ander onderdeel dat wordt gebruikt voor een grondsensor, waarbij je een geïntegreerd systeem hebt van 80 verschillende afzonderlijke componenten in één monolithisch stuk. Die is ook al bijna twee jaar in productie.
We hebben een aantal andere productiecomponenten die we maken — voor olie en gas en onderzeese exploratiegebieden, die in actieve productie zijn voor onderzeese robotica — voor een andere van onze klanten maken we onderdelen voor, die actief worden gebruikt in zowel olie en gas, boren en exploratie, als onderzeese robotica.
Hoe ziet u additive manufacturing de komende vijf jaar evolueren, zowel wat betreft de technologie als de industrie in het algemeen?
In de komende vijf jaar zie ik de technologie evolueren met meer multi-lasersystemen, waardoor onderdelen sneller kunnen worden geproduceerd, waardoor de kosten van componenten dalen. Dit zal de implementatie van AM-onderdelen verder stimuleren.
De kosten van onderdelen zijn een belangrijke factor, en lasertijd is uw belangrijkste drijfveer voor de kosten van een AM-component. Dus als je meer lasers in een onderdeel kunt persen en de componenten kunt certificeren met behulp van die multi-lasersystemen, kun je hetzelfde onderdeel sneller en dus goedkoper bouwen.
De andere evolutie is dat we betere in-process monitoringsystemen zullen hebben. Er zijn momenteel een paar verschillende beschikbaar door verschillende fabrikanten, maar mijn indruk is dat hoewel veel van hen goede systemen zijn, ze nog niet op het niveau zijn dat gebruikers, zoals ik, nodig zouden hebben om ze te kunnen implementeren tegen een echt productietempo.
Ik hoop dat we binnenkort echte in-process monitoring hebben, zodat we kunnen volgen wat er tijdens het proces in de machine gebeurt en problemen met een onderdeel kunnen identificeren voordat het de machine.
Het ideale scenario zou zijn om intelligente software te hebben die problemen kan identificeren en mogelijk correcties kan aanbrengen met technische ondersteuning ter plekke. Het zou natuurlijk nog beter zijn om echt robuuste machines te hebben die geen problemen hebben en gewoon 24/7 draaien.
Zijn er trends waar je enthousiast over bent?
Ik ben enthousiast over verschillende ontwikkelingen, waarbij in-process monitoringsystemen, zoals ik al zei, er één zijn.
Er worden ook enkele nieuwe materialen ontwikkeld en gelanceerd. We ontwikkelen een aantal verschillende materialen waarmee bepaalde van onze klanten een aantal zeer revolutionaire componenten kunnen maken.
Het andere waar ik enthousiast over ben, is dat er veel meer diversificatie is bij fabrikanten over de hele wereld. In het begin werden de meeste AM-machines in een handvol landen in Europa geproduceerd. Nu zijn er nieuwe fabrikanten en verschillende landen die verschillende en nieuwe benaderingen toepassen op het bouwen van machines.
Ze verlagen de kosten van de machines en leren van het gebruik in de hele branche om ze intuïtiever te maken voor de operators.
Mijn ervaring de eerste jaren met deze machines was dat ze erg kieskeurig zijn en veel aandacht en “oppassen” vergen. En eerlijk gezegd was veel van het machineontwerp niet erg productievriendelijk.
Ik zie dat er nu veel gebruiksvriendelijkheid in de machines wordt ingebouwd, aangezien machinefabrikanten feedback krijgen van hun gebruikers.
Maar ook de toegenomen concurrentie van verschillende fabrikanten over de hele wereld helpt, denk ik, om innovatie in de systemen te stimuleren, de kosten te verlagen en de bruikbaarheid van de machinesystemen te vergroten.
Wat volgt er voor Oerlikon, vooral voor de faciliteit die u helpt te overzien en te runnen?
Ons kortetermijndoel voor deze faciliteit is om alle apparatuur die we hebben gekocht, geïnstalleerd en gecertificeerd te krijgen. Dus we hebben momenteel 18 metalen poederbedsystemen online en operationeel, en we doen productiehardware op veel van die systemen.
Onze volgende stap daarvoor is het completeren van materiaaleigenschappen voor al onze materiaalsystemen voor al onze machines en de datasets daarvoor. Maar dat is erg tijdrovend en kostbaar.
Gelukkig hebben we hier veel zeer getalenteerde mensen met veel materiaal, metallurgie en technische ervaring, en ik ben erg trots om lid te zijn van dat team.
Het andere doel is om alle andere apparatuur op te zetten om die echte end-to-end productiefaciliteit te bereiken.
We hebben onlangs onze HIP-oven en vacuümoven online gebracht en we werken eraan om deze gecertificeerd te krijgen.
We hebben ook wat CNC-apparatuur ingebracht en we hebben ook een aanzienlijk aantal extra ovens en CNC-apparatuur voor nabewerking. Het doel is dus om al deze apparatuur geïnstalleerd, gecertificeerd en operationeel geïntegreerd te krijgen om een compleet, samenhangend productiesysteem te creëren.
Ga voor meer informatie over Oerlikon naar: https://www.oerlikon.com/en/
3d printen
- Interview met een expert:professor Neil Hopkinson, directeur 3D Printing bij Xaar
- Interview met een expert:Philip Cotton, oprichter van 3Dfilemarket.com
- Interview met een expert:Spencer Wright van pencerw.com en nTopology
- Interview met een expert:Dr. Alvaro Goyanes van FabRx
- Expertinterview:Nanoe CEO Guillaume de Calan over de toekomst van keramisch 3D-printen
- Expert Interview:Ultimaker President John Kawola over de toekomst van 3D-printen
- Hoe Ford Motor Company 3D-printen voor de auto-industrie innoveert:interview met experts van Harold Sears
- Interview met expert:Simon Fried, medeoprichter van Nano Dimension over de opkomst van 3D-printen voor elektronica
- Interview met experts:Brian Alexander van Solvay over de ontwikkeling van hoogwaardige polymeren voor 3D-printen
- Interview met experts:een blik op de ultrasnelle, industriële SLA 3D-printers van Nexa3D
- Interview met expert:AMendate over zijn geautomatiseerde topologie-optimalisatiesoftware voor 3D-printen