Interview met expert:onderzoek naar de daglichtpolymeerprinttechnologie van Photocentric met algemeen directeur Paul Holt
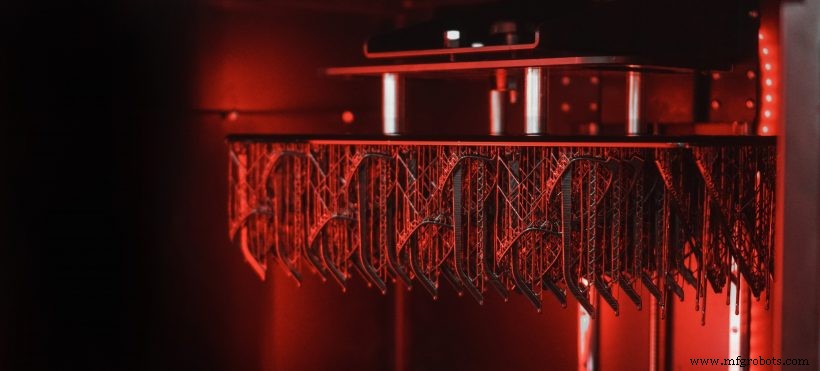
Photocentric is een in het VK gevestigde fabrikant van 3D-printers en materialen. Het bedrijf, opgericht in 2002, staat bekend om zijn unieke en innovatieve benadering van 3D-printen, dat het Daylight Polymer Printing noemt.
In tegenstelling tot vergelijkbare op hars gebaseerde technologieën zoals stereolithografie (SLA) of Digital Light Processing (DLP), gebruikt de Daylight Polymer Printing-technologie van Photocentric geen UV-laser of projector om 3D-geprinte onderdelen te produceren.
In plaats daarvan gebruikt de technologie licht van LCD-schermen om 3D-geprinte onderdelen te maken door vloeibare fotopolymeerhars laag voor laag uit te harden. Deze Daylight-harsen, ook vervaardigd door Photocentric, stollen wanneer ze worden blootgesteld aan licht van de LCD-schermen van de printers.
Met name de 3D-printers van Photocentric gebruiken LCD-schermen van mobiele telefoons, televisies en tablets, waardoor ze betaalbaarder zijn dan SLA/DLP-technologieën, maar met dezelfde kwaliteit.
Voor meer informatie over de unieke technologie van Photocentric en voorbeelden ervan in gebruik, spreken we met Paul Holt, de algemeen directeur van Photocentric.
Kun je me iets vertellen over Photocentric en je missie als bedrijf?
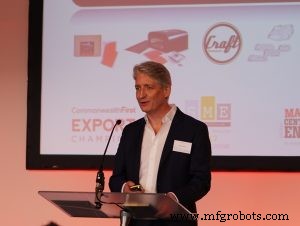
Photocentric is oorspronkelijk opgericht om een gepatenteerd pakket fotopolymeren te vervaardigen. Sindsdien is ons bedrijf uitgegroeid tot een groot aantal markten en passen we onze innovaties op het gebied van fotopolymeer toe op een breed scala van industrieën, waaronder 3D-printen.
Innoverende fotopolymeertechnologie vormt de kern van ons bedrijf . In 2005 hebben we het concept uitgevonden om lcd-schermen te gebruiken voor 3D-printen. In 2014 ontwikkelden we ons eerste LCD-prototype. We hebben zojuist onze zevende lcd-printer uitgebracht, met plannen voor meer in de pijplijn.
De gebruikers van onze technologie zijn onder meer sieradenontwerpers die de productie willen versnellen of unieke geometrische stukken willen maken met 3D-printen, tandtechnici die een nauwkeurige printer met hoge capaciteit nodig hebben voor patiëntspecifieke modellen en fabrikanten, ingenieurs en uitvinders die hun ontwerpconcepten willen omzetten in tastbare prototypen of functionele onderdelen voor eindgebruik.
Uiteindelijk is het onze missie om de wereldwijde productie te veranderen - niet alleen 3D-printen. We doen dit door 3D-printen betaalbaar, grootschalig en functioneel te maken en door massaproductie op maat wereldwijd mogelijk te maken.
Hoe werkt uw Daylight Polymer Printing-technologie en wat onderscheidt deze van andere op hars gebaseerde machines die op de markt verkrijgbaar zijn?
Daylight Polymer Printing maakt gebruik van onze in-house geformuleerde Daylight vloeibare fotopolymeerhars. De hars wordt laag voor laag uitgehard wanneer deze wordt blootgesteld aan onze 3D-printers met een hoge resolutie op LCD-schermen.
Een onderdeel wordt gemaakt zodra elke laag hars is uitgehard door het licht dat door het LCD-scherm wordt uitgestraald.
Een van de belangrijkste onderscheidende factoren van onze technologie is de kwaliteit van onze machines. Elke fase van onze producten doorloopt een grondige kwaliteitscontroleprocedure om ervoor te zorgen dat onze klanten de beste ervaring en het beste beschikbare product krijgen.
Bovendien is onze aanpak ontworpen om de kosten van 3D-printen te verlagen en de bredere toepassing van de technologie. Alledaagse schermen, zoals telefoon- of tv-schermen, zijn de kern geworden van onze 3D-printers. Deze LCD-schermen zijn betrouwbare en goedkope digitale beeldapparatuur.
Dat, in combinatie met onze fotopolymeerhars, betekent dat we een betaalbaar 3D-printpakket kunnen aanbieden. Veel 3D-printbedrijven doen de engineering en besteden vervolgens de chemie uit - we doen alles in eigen huis.
We bieden ook de grootste op LCD-scherm gebaseerde printer op de markt, met onze Liquid Crystal Magna-machine , zodat we op grote schaal een hoge mate van nauwkeurigheid kunnen bereiken.
Welke sectoren kunnen het meeste profiteren van uw technologie?
We kunnen 3D-printoplossingen bieden aan industrieën zoals tandheelkunde en sieraden, waar kleine en nauwkeurige toepassingen typisch zijn, en ook oplossingen bieden voor industrieën waar grootschalige componenten en prototypes nodig zijn.
We zijn met name van mening dat er een enorm potentieel is op het gebied van tandheelkunde voor Photocentric. Na een bezoek aan de IDS 2019-show dit jaar, zagen we in deze sector een enorme vraag naar LCD-printen.
Daarom is een groot deel van ons onderzoek en onze ontwikkeling gewijd aan het produceren van tandheelkundige specifieke producten, zoals Liquid Crystal Dental - onze geoptimaliseerde tandheelkundige printer voor aan de stoel of in het laboratorium, die later dit jaar op de markt komt.
Aan de andere kant is onze technologie ook geschikt voor toepassingen met grote componenten binnen de automobiel- en entertainmentindustrie. De reikwijdte is enorm, vooral gezien de veelzijdigheid van onze ontwikkelingen op het gebied van LCD-printers.
Kunt u een of twee succesvolle toepassingen delen over hoe uw technologie is gebruikt?
Een unieke klant is Quimbaya Orfebreria, een Argentijnse goudsmid die ambachtelijke speciale stukken voor zijn klanten produceert.
Toen de vraag groter begon te worden dan het aanbod en ze te maken kregen met ontwerpbeperkingen, besloot Quimbaya de traditionele methoden terzijde te schuiven en 3D-printen te introduceren in hun werkstroom. Ze kozen ervoor om onze LC Precision 1.5 desktopprinter met hoge resolutie te gebruiken.
Door 3D-printen te gebruiken, konden ze hun productietijd met 80% verminderen. Hun productie steeg ook met 400% en ze zijn nu in staat om meer ingewikkelde en complexe ontwerpen voor hun klanten te produceren.
Dichter bij huis in het VK is een ander voorbeeld het Robert Jones en Agnes Hunt Orthopedic Hospital in Oswestry, een gespecialiseerd orthopedisch ziekenhuis met een lange traditie van innovatie in de behandeling van hun patiënten.
Met behulp van modellen die zijn afgedrukt op de LC Pro, de voorloper van LC Magna, kon een chirurg helpen bij het plannen van een complexe femurosteotomie bij een juveniele patiënt met een heupafwijking. De noodzakelijke sneden werden van tevoren gepland, samen met het voorvormen van het implantaat dat nodig was voor een succesvolle correctie. Deze 3D-prints hebben de NHS uiteindelijk meer dan £ 1000 bespaard en een uur tijd in het theater bespaard.
Wat zijn enkele van de uitdagingen die moeten worden overwonnen om de adoptie van additive manufacturing te versnellen?
De grootste uitdaging is het ontbreken van materiaaleigenschappen.
Toen we voor het eerst begonnen met 3D-printen, ontdekten we dat drie belangrijke problemen de bredere acceptatie van 3D-printen in de weg stonden:1) de extreem hoge kosten, 2) het gebrek aan schaalbaarheid van de productie en 3) het gebrek aan van functionele eigenschappen.
LCD-schermen hebben zeker het eerste probleem veranderd, met duizenden goedkopere mobiele schermen die afdrukken met een extreem hoge resolutie bieden. Grootformaat LCD-schermen beginnen het probleem van schaal te beantwoorden, maar het probleem rond materiaaleigenschappen moet nog goed worden aangepakt.
We werken momenteel samen met BASF om het breedste assortiment harsen te ontwikkelen met duurzame eigenschappen die functioneel in de industrie kunnen worden gebruikt.
Hoe ziet u technologieën voor additieve productie en de industrie evolueren?
Voor ons zijn LCD-schermen echt storend en zullen het spel voor SLA-afdrukken veranderen.
Via LCD-schermen kunnen we op maat gemaakte massaproductie van onderdelen mogelijk maken, hetzij door middel van enkele grote schermen die grote onderdelen kunnen produceren in een fractie van de tijd die technologieën met behulp van lasers of projectoren nodig hebben, of een reeks kleinere , schermen met een hogere resolutie die veel kleinere onderdelen produceren.
Ik zie ook dat alle machines automatisch worden, waardoor handmatige tussenkomst overbodig wordt. Ik verwacht dat functionele 3D-geprinte plastic onderdelen binnen 2 jaar in productielijnen zullen worden gebruikt, omdat de voordelen van het ontbreken van gereedschap, aangepaste ontwerpen en vrijheid van geometrie industrieel worden benut.
De andere verandering die ik zie bij het transformeren van de productie van keramische en metalen onderdelen, is de creatie van het groene lichaam via 3D-printen met daaropvolgend sinteren om solide en levensvatbare keramiek en metalen te leveren. Dit proces is zowel minder energie-intensief als goedkoper, waardoor een bredere productie van deze materialen op maat mogelijk wordt.
Photocentric heeft onlangs zijn nieuwe Liquid Crystal Magna 3D-printer aangekondigd. Kunt u ons enkele specificaties en voordelen van deze machine doornemen?
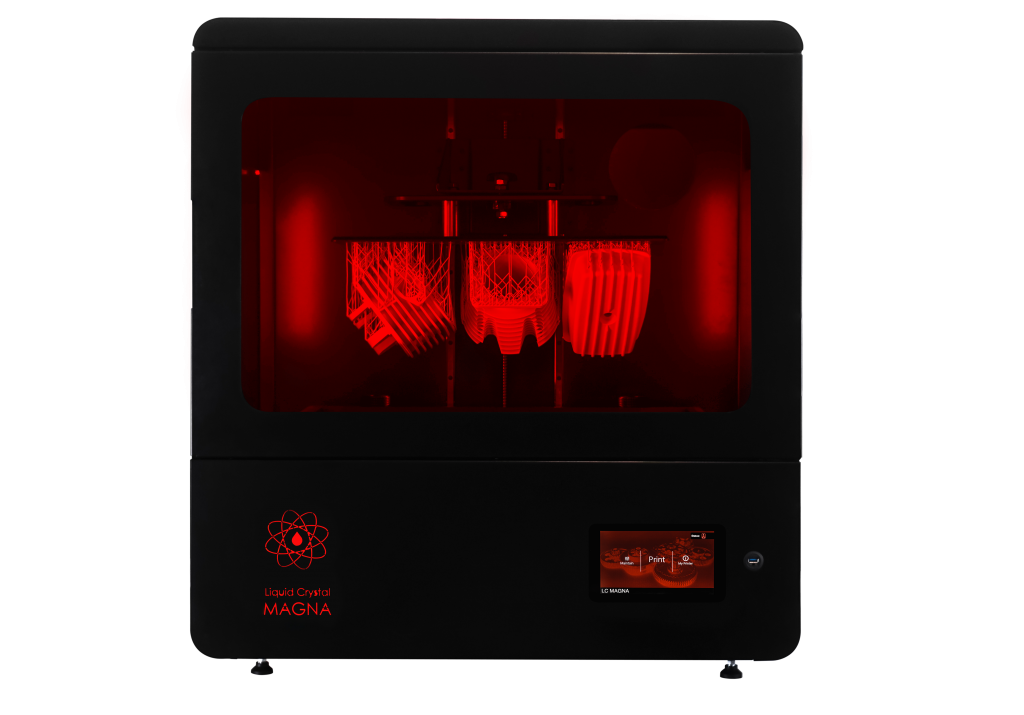
De visie achter onze LC Magna-machine is om massaproductie op maat en prototyping van grote componenten mogelijk te maken tegen een kosteneffectieve prijs. LC Magna kan honderden op maat gemaakte onderdelen maken tegen aanzienlijk lage kosten.
LC Magna heeft een groot bouwvolume en biedt zeer nauwkeurige afdrukken, waardoor het ideaal is voor massaproductie op maat. Het bouwvolume is 510 mm x 280 mm x 350 mm - waardoor het de grootste op een LCD-scherm gebaseerde 3D-printer is die momenteel beschikbaar is.
LC Magna heeft ook een 23,4” 4K Ultra HD-scherm, gekoppeld aan een op maat gemaakte achtergrondverlichting. Deze twee elementen werken samen om een extreem hoge afdruknauwkeurigheid en detail te garanderen. Dankzij de helderheid van de achtergrondverlichting kan de printer lagen van 100 micron in 3-8 seconden belichten.
De machine is voornamelijk bedoeld voor tandtechnici, productontwerpers, ingenieurs en fabrikanten, die in staat zijn om verhogen hun doorvoer, versnellen assemblageproducties en verkorten doorlooptijden.
Een brilfabrikant kan bijvoorbeeld nu 36 optische monturen in massa produceren binnen 12 uur - dat is minder dan 20 minuten voor elke set. Een tandtechnicus die een groot aantal patiëntspecifieke modellen nodig heeft, kan nu 46 platte bogen printen in iets meer dan 1 uur - deze kosten minder dan £ 1,06 per boog bij gebruik met onze in-house Daylight tandheelkundige modelhars.
Wat houden de komende 12 maanden in voor Photocentric?
Wij zijn van mening dat de 3D-printindustrie veel kansen biedt - het heeft invloed op elk aspect van de productie. Gezien de grote verscheidenheid aan onontgonnen mogelijkheden op dit gebied, zijn we nauw betrokken bij een reeks spannende projecten.
We werken bijvoorbeeld aan een reeks nieuwe 3D-printers om kunststoffen, keramiek te produceren en metalen.
We breiden ons team ook uit, met name op de R&D-afdeling, om dieper te graven in 3D-printen van metaal en keramiek. Dit zal een dramatische impact hebben op onze benadering van het vervaardigen van materialen.
Ga voor meer informatie over Photocentric naar:https://photocentricgroup.com/
3d printen
- Interview met een expert:professor Neil Hopkinson, directeur 3D Printing bij Xaar
- Interview met een expert:Philip Cotton, oprichter van 3Dfilemarket.com
- Interview met een expert:Spencer Wright van pencerw.com en nTopology
- Interview met een expert:Dr. Alvaro Goyanes van FabRx
- ACEO® onthult nieuwe technologie voor 3D-printen met siliconen
- Interview met een expert:Dr. Bastian Rapp van NeptunLab
- Expertinterview:Felix Ewald, CEO van DyeMansion
- Interview met een expert:Ibraheem Khadar van Markforged
- Expertinterview:Nanoe CEO Guillaume de Calan over de toekomst van keramisch 3D-printen
- Expert Interview:Ultimaker President John Kawola over de toekomst van 3D-printen
- Hoe Ford Motor Company 3D-printen voor de auto-industrie innoveert:interview met experts van Harold Sears