Interview met expert:Aconity3D Managing Director Yves Hagedorn over het helpen van bedrijven bij het innoveren met additieve productie
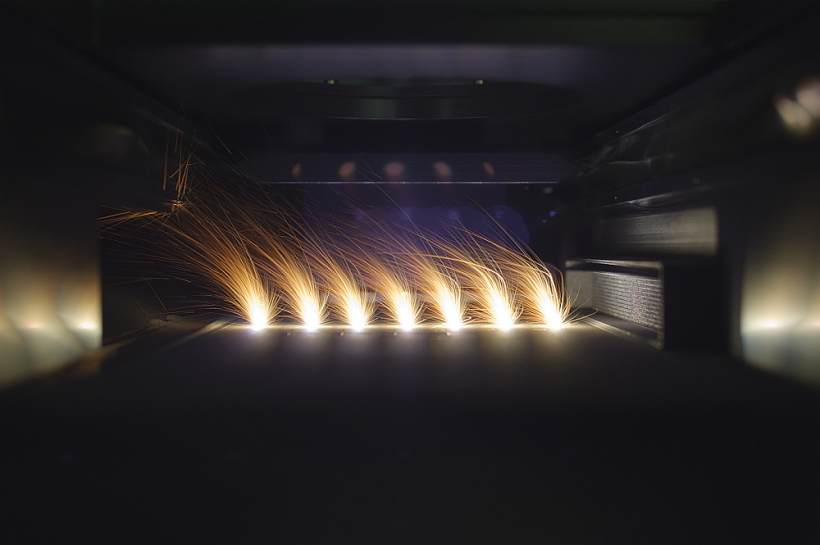
Het adopteren van 3D-metaalprinten kan een uitdaging zijn vanwege de noodzaak om applicaties te ontwikkelen en materialen en processen te kwalificeren. Om deze uitdagingen het hoofd te bieden, biedt het Duitse bedrijf Aconity3D flexibele metalen 3D-printsystemen voor laboratoria waarmee klanten kunnen experimenteren met procesparameters en nieuwe toepassingen voor de technologie kunnen onderzoeken.
In het expertinterview van deze week bespreekt Yves Hagedorn, Managing Director bij Aconity3D, de voordelen van hardwaresystemen met open architectuur en waarom ontwerpsoftware een van de belangrijkste uitdagingen is bij 3D-metaalprinten.
Kun je me iets vertellen over Aconity3D?
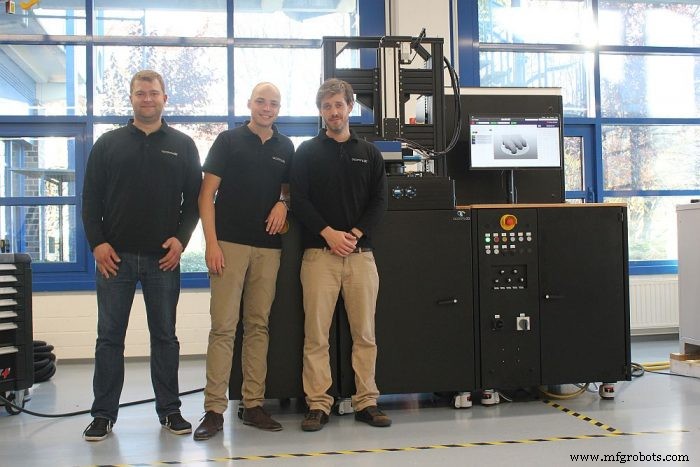
Bij Aconity3D bieden we alles wat nodig is voor de productie van metalen additieven.
We bieden speciale machinecomponenten en verschillende modules, die kunnen worden gecombineerd om apparatuur te creëren die is ontworpen voor gespecialiseerde toepassingen. Dat komt omdat we geloven dat er niet één systeem is dat geschikt is voor alle mogelijke toepassingen in de hele markt.
Onze klantreis begint met advies. Een klant kan ons bijvoorbeeld benaderen om te kijken of het mogelijk is om magnesium te 3D-printen. In dit geval zouden we wat onderzoek doen in onze tweede business unit, namelijk materiaaldistributie, en voor onze klant uitzoeken waar het specifieke materiaal in kwestie te krijgen is.
Bij onze derde business unit zouden we wat testen doen om er zeker van te zijn dat het materiaal geschikt is om te worden verwerkt met additive manufacturing. En als dat allemaal werkt en een klant tevreden is, zouden we optreden als een werkplaats en die specifieke toepassing voor de klant vervaardigen.
Op de lange termijn kan de klant besluiten onze apparatuur te kopen die voor die specifieke toepassing is ontworpen.
Onze aanpak stelt onze klanten in staat om efficiënt onderzoek te doen in termen van uitbreiding van de reikwijdte van de toepasselijke materialen.
Als klanten bepaalde materialen voor speciale toepassingen hebben die nog niet gekwalificeerd zijn, kunnen ze met onze apparatuur veel onderzoek doen naar kwalificatie. Ze kunnen verschillende parameters gebruiken, zijn volledig softwarevrij en kunnen ook wijzigingen aan de hardware uitvoeren, afhankelijk van de parameters die ze nodig hebben.
Uiteindelijk willen we een one-stop-shop zijn voor klanten. Het verkopen van apparatuur is echter onze hoofdactiviteit.
Wat was de motivatie achter de oprichting van het bedrijf?
Wel, als u de reikwijdte van additive manufacturing wilt uitbreiden, hetzij in termen van toepasbare materialen of door verhoging van de productiviteit of maatnauwkeurigheid, hebt u volledige toegang tot de hardware en tot alle mogelijke parameters in het proces nodig.
We zagen dat er geen systeem op de markt was waarmee je dit kunt doen. En toen kwamen we op het idee om klanten de mogelijkheid te bieden hun proces te finetunen. Toen werd Aconity3D geboren.
We realiseerden ons al snel dat we een echte troef hebben en dat we daadwerkelijk kunnen voldoen aan een echte klantbehoefte om toegang te hebben tot zowel de hardware als de software.
Zijn er specifieke sectoren die het meest profiteren van de technologie en diensten die Aconity3D biedt?
Er is geen specifieke industrie, aangezien de industriële toepassingen voor additieven zo veelzijdig zijn als de mogelijkheden.
Laten we de medische industrie nemen, waar een enorm toepassingsgebied is. U kunt bijvoorbeeld titaniumimplantaten hebben of zelfs magnesium, dat biologisch absorbeerbaar is. Er zijn ook toepassingen in de medische sensorindustrie.
Hetzelfde geldt voor de ruimtevaart. De lucht- en ruimtevaartindustrie heeft er belang bij het toepassingsgebied van toepasbare legeringen voor bijvoorbeeld plateren of legeringen voor hoge temperaturen uit te breiden.
Automotive is ook een ander interessant voorbeeld omdat de industrie erg kostenbewust is. Dit betekent dat autobedrijven alleen willen betalen voor wat ze krijgen.
Onze waardepropositie is onze hoge flexibiliteit, waardoor we alles weg kunnen laten wat niet nodig is voor die specifieke toepassing. Hierdoor kunnen we concurreren met traditionele productietechnologieën.
Welke toepassingen zijn het meest geschikt voor de technologie als het gaat om 3D-printen van metaal en hoe kunnen bedrijven beginnen met het identificeren van de juiste soorten toepassingen?
Het is goed om additieve fabricage te overwegen als u componenten van kleine afmetingen en complexe structuren heeft. Een andere reden om additieven te gebruiken kan zijn om nieuwe materialen te combineren waar dat voorheen onmogelijk was - neem als voorbeeld koper en chroom.
De belangrijkste hindernis hier is dat voor bijna alle toepassingen het produceren van een onderdeel is duurder met additive manufacturing in vergelijking met frezen of andere traditionele productietechnologieën.
Een uitzondering vormen tandheelkundige restauraties:hiervoor is additive manufacturing goedkoper dan frezen. Daarom was het een van de eerste industriële toepassingen voor lasersmelten op basis van poeder. Een andere uitzondering zijn brilmonturen, wat ook een geweldige toepassing is voor additieven.
Maar voor alle anderen is er vaak een conflict tussen de businesscase en de levenscycluskosten van het product. Dat is de grootste hindernis, omdat veel klanten gewoon geen idee hebben van de levenscycluskosten van hun product.
Om het anders te zeggen, je kunt nu een functionele integratie hebben. Zo kun je bijvoorbeeld koelkanalen in een behuizing integreren, maar daar is echt moeilijk een prijskaartje aan te hangen. De grootste uitdaging is dus om de onderdelen te screenen en een geldige businesscase te vinden voor uw additieftoepassing en productie.
Wat zijn de belangrijkste uitdagingen van 3D-printen met metaal en hoe heb je ze aangepakt?
Naar mijn mening ligt een van de belangrijkste uitdagingen in het ontwerp van onderdelen en de bijbehorende softwareoplossingen voor gegevensvoorbereiding. Als het gaat om additive manufacturing is standaardisatie nog steeds een uitdaging en ik denk dat dit deels komt doordat de software niet echt gestandaardiseerd is. Neem bijvoorbeeld de vele verschillende dataformaten voor elke individuele systeemaanbieder. Ook op het gebied van het ontwerp van onderdelen zijn er beperkte tot geen richtlijnen als gevolg van de enorme flexibiliteit van additieve productie. Dit is ook de reden waarom raamwerken voor tandheelkundige restauratie de eerste echte industriële toepassing waren:een volledig geautomatiseerd onderdeelontwerp en gegevensvoorbereidingsraamwerk - een voorwaarde voor serieproductie van onderdelen van een enkele partijgrootte.
Voor de eerste keer sinds de jaren 70 bevinden we ons nu in een situatie waarin we complexere onderdelen kunnen bouwen dan we daadwerkelijk kunnen ontwerpen of simuleren.
Dus ontwerp en gegevensvoorbereiding zijn nog steeds een knelpunt in deze branche, terwijl de nadruk wordt gelegd op hardwaresystemen met een hogere productiviteit, waarbij intelligente softwareoplossingen van deze vergelijking worden uitgesloten. Onderdelen voorbereiden zodat ze geschikt zijn voor additive manufacturing is een belangrijke vaardigheid en kost ook behoorlijk wat tijd.
Ik heb voorbeelden gezien waarbij het ontwerp van een onderdeel en de voorbereiding van de gegevens meer dan twee weken duurden, terwijl het printen van het onderdeel slechts twee dagen duurde. Dit is gewoon inefficiënt om een onderdeel voor die tijd te ontwerpen. En daar komt naar mijn mening het probleem om de hoek kijken.
Kunt u een van de succesverhalen van uw klanten delen?
Ja absoluut. We hebben klanten gehad die nu magnesiumonderdelen voor medische toepassingen produceren. We hebben anderen die FDA-goedkeuring hebben gekregen voor hun titanium implantaten.
In de auto-industrie hadden we een specifiek verzoek voor een systeem met hoge productiviteit. Dus zorgden we voor een vier-lasersysteem met volledige overlap op een plaat met een diameter van 400 millimeter. Ik denk dat wij de enigen in de markt zijn die dit hebben kunnen doen, en het heeft een aanzienlijke impact op de productiviteit.
Verdere klanten benutten de mogelijkheid van voorverwarmen bij hoge temperatuur om het toepassingsgebied van de toepasbare materialen uit te breiden naar hooggelegeerde gereedschapsstaalsoorten, titaniumaluminiden en bepaalde op nikkel gebaseerde superlegeringen.
Hoe ziet u de AM-industrie de komende jaren evolueren?
De industrie is zeker volwassen geworden in de 12 jaar dat ik betrokken ben geweest bij additieven. Toen ik begon, was er een hype. Nu is de hype enigszins afgenomen.
De evolutie van de technologie heeft ertoe bijgedragen dat veel toepassingen voor additive manufacturing zijn ontsloten, maar al deze toepassingen vereisen nog steeds een hoog niveau van expertise.
Tegenwoordig kun je bepaalde desktop 3D-printers kopen voor minder dan 1000 euro, wat veel mensen doet geloven dat je industriële gereedschapsmachines kunt kopen, zoals die dure poedergebaseerde lasersmeltsystemen, op play drukken en je heeft u direct uw businesscase.
Natuurlijk is dat niet het geval bij industriële additive manufacturing. Er ligt een grote uitdaging in het opleiden en ontwikkelen van expertise. En ik denk dat dat is waar de hele industrie zich zal moeten blijven ontwikkelen.
Het hebben van meer expertise binnen de industrie en vooral het hebben van meer gestandaardiseerde processen en betrouwbare producten zal essentieel zijn voor de industriële adoptie van additive manufacturing.
Zijn er ontwikkelingen in de AM-industrie waar u enthousiast over bent?
Ja absoluut. We hebben een sterke focus op niet alleen in-process monitoring, wat betekent dat we verschillende sensoren gebruiken om zoveel mogelijk informatie uit uw proces te halen, maar ook op het gebruik van die informatie om in-process controle te doen.
Ik denk dat dat de heilige graal voor AM is, want met in-process controle kun je vrijwel onmiddellijk reageren op tekortkomingen in je proces.
Hierdoor worden de systemen een stuk slimmer.
Kun je iets meer vertellen over bewaking en controle tijdens het proces, en wat Aconity3D op dat gebied doet?
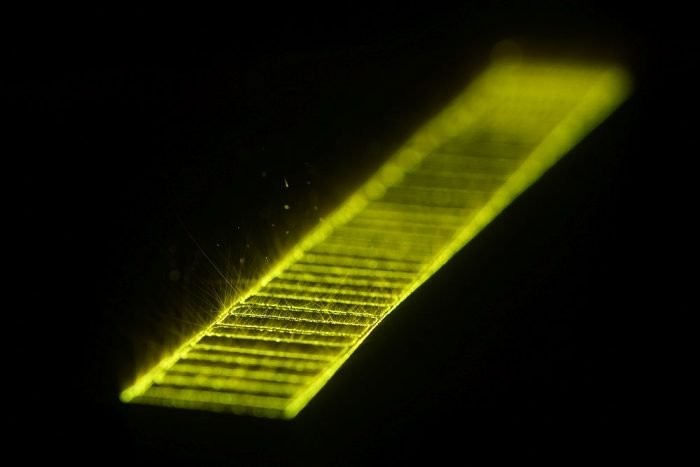
Ons bedrijf is een spin-off van het Fraunhofer Institute for Laser Technology, waar het poederbed lasersmelten is ontstaan.
Met die achtergrond konden we verschillende optische sensoren implementeren die bij de verwerkingslaser passen. En daarmee haal je direct veel informatie uit de interactiezone, melt pool en laser.
Dit leidt echter tot andere uitdagingen in verband met Big Data. Wat doe je met die enorme hoeveelheid vastgelegde data? Hoe zorg je ervoor dat je de gegevens overslaat die je eigenlijk niet nodig hebt? En hoe maak je onderscheid tussen nuttige en nutteloze data?
Ik denk dat de industrie zich daar momenteel bevindt. En dat is wat we ook doen. We gebruiken een hogesnelheidscamera om in het proces te kijken en ervan te leren, en we hebben ook verschillende sensoren die een gesloten procescontrole mogelijk maken.
Dus als je dat systeem hebt, kun je kan detecteren of uw smeltbad te heet of te groot is, en u kunt dat regelen door middel van laservermogen, en zo reageren op dat signaal van het proces.
Dat fascineert me echt. En ik denk dat er hier nog veel potentieel is.
Aconity3D heeft onlangs een samenwerking aangekondigd met Aerosint. Wat betekent deze samenwerking voor de toekomst voor uw bedrijf?
Sinds ik in de branche ben, zijn mensen geïnteresseerd in metalen onderdelen van meerdere materialen. En het was altijd de vraag wat er eerst moest komen, de toepassing of de technische ontwikkeling.
Een tijdlang gebeurde er eigenlijk niets in die richting. En toen ontmoetten we Aerosint, een Belgisch bedrijf dat een poederdepositieapparaat heeft ontwikkeld dat in staat is om twee verschillende materialen in de X- en Y-dimensies op een poederbed te leggen. Dit is eigenlijk wat er ontbrak in additieve productie van meerdere materialen.
Nu komen we in de vergelijking met de mogelijkheid om te reageren op het gewijzigde poederpatroon of materiaalpatroon op onze bouwplaat door de vereiste procesparameters voor elk afzonderlijk materiaal te wijzigen.
Dit betekent dat beide partners, Aconity3D en Aerosint, een sterke basis hebben om die multi-materiële AM-droom waar te maken.
Welke nieuwe toepassingen kunnen worden geopend met de mogelijkheid van 3D-printen van metaal met meerdere materialen?
Een branche die hier echt van kan profiteren, is de sieradenindustrie.
Het creëren van gegradeerde materialen, van koper tot chroom, kan een andere mogelijkheid zijn. Die kunnen worden gebruikt voor gereedschappen in de vorm- of smeedindustrie. Bij 3D-printen met meerdere materialen kunt u bijvoorbeeld koper gebruiken om koelstructuren te maken en chroom of staal om het buitenoppervlak van het onderdeel te creëren.
Als u hellingen heeft, kunt u mogelijk ook uw mechanische eigenschappen beoordelen. Dit kan nuttig zijn in de medische wereld voor het verminderen van stress-shielding. Dit effect treedt op wanneer metalen implantaten te dicht zijn, waardoor een bot zijn kracht verliest. Stressafscherming kan ook worden verminderd door de mechanische eigenschappen van het implantaat te veranderen met behulp van 3D-printen met meerdere materialen.
Echter, voordat er nieuwe toepassingen worden ontwikkeld, denk ik dat er een technologische push moet komen om de mogelijkheden te laten zien die vergelijkbaar zijn met de huidige mogelijkheden van additive manufacturing.
Wat brengt de toekomst voor Aconity3D?
We zullen doorgaan met het uitbreiden van de reikwijdte van toepasbare materialen die ons, net als multi-materialen, in staat zullen stellen nieuwe toepassingen aan te bieden voor onze industriële partners. We willen diep in gespecialiseerde serietoepassingen duiken.
We begrijpen dat het met nichetoepassingen erg moeilijk kan zijn om nieuwe materialen te kwalificeren, vooral als het maar voor één klant is. Ons brood is echter om ervoor te zorgen dat onze klanten tevreden zijn en de toepassingen kunnen benutten die ze voor ogen hebben.
Uiteindelijk willen we innovatie voor onze klanten mogelijk maken.
Ga voor meer informatie over Aconity3D naar: aconity3d.com
3d printen
- Hoe kunnen luchtvaartbedrijven additieve productie naar een hoger niveau tillen met MES?
- Waarom zouden bedrijven gedistribueerde productie van additieven moeten omarmen?
- Interview met experts:Pat Warner, specialist in additieve productie van Renault Formula One Team
- Interview met een expert:professor Neil Hopkinson, directeur 3D Printing bij Xaar
- Interview met een expert:Dr. Alvaro Goyanes van FabRx
- Interview met een expert:Dr. Bastian Rapp van NeptunLab
- Expertinterview:Felix Ewald, CEO van DyeMansion
- Interview met een expert:Ibraheem Khadar van Markforged
- Verbeteren van additieve productie met reverse engineering
- Expertinterview:James Hinebaugh van Expanse Microtechnologies
- Interview met expert:CEO van PostProcess Technologies over het oplossen van het knelpunt in de nabewerking voor additieve productie