Applicatie Spotlight:3D-printen voor medische implantaten
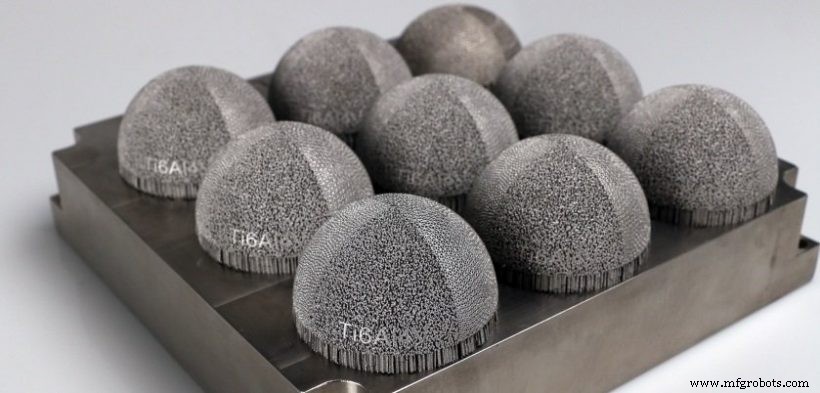
[Image credit:Health Canada]
Het creëren van beter passende, duurzamere en beter presterende botimplantaten is een voortdurende zoektocht van zowel orthopedisten als chirurgen. 3D-printen draagt enorm bij aan de vooruitgang op dit gebied.
De technologie stelt implantaatfabrikanten in staat implantaten te maken met verbeterde functionaliteit en meer gepersonaliseerd voor de specifieke behoeften van de patiënt. Bovendien opent 3D-printen de deur naar gepersonaliseerde implantaten die op het zorgpunt kunnen worden gemaakt.
Deze week gaan we verder met onze 3D Printing Application Spotlight-serie door te kijken naar het gebruik van 3D-printen voor medische implantaten, evenals de voordelen en huidige toepassingen van de technologie.
Bekijk de andere toepassingen die in deze serie worden behandeld:
3D-printen voor warmtewisselaars
3D-printen voor lagers
3D-printen voor fietsproductie
3D-printen voor productie van digitale tandheelkunde en heldere uitlijners
3D-geprinte raketten en de toekomst van de fabricage van ruimtevaartuigen
3D-printen voor de productie van schoenen
3D-printen voor elektronische componenten
3D-printen in de spoorindustrie
3D-geprinte brillen
3D-printen voor productie van eindonderdelen
3D-printen voor beugels
3D-printen voor turbineonderdelen
Hoe 3D-printen zorgt voor beter presterende hydraulische componenten
Hoe 3D-printen innovatie in de kernenergie-industrie ondersteunt
De medische 3D-printmarkt in 2019
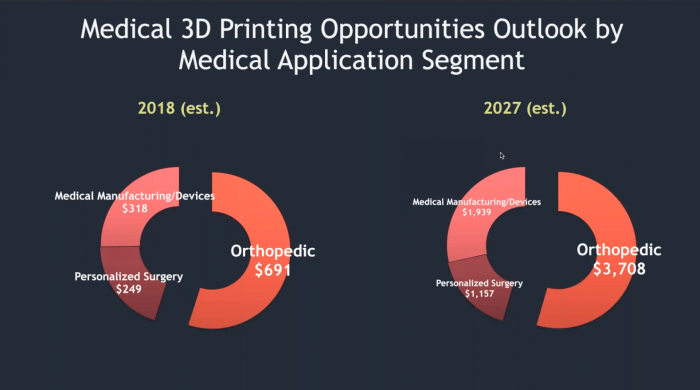
Orthopedische implantaten - medische hulpmiddelen die operatief worden gebruikt om een ontbrekend gewricht of bot te vervangen - zijn slechts één kans die 3D-printen biedt aan de medische industrie.
De markt voor 3D-printen voor orthopedie werd in 2018 gewaardeerd op $ 691 miljoen en door SmarTech Analysis wordt voorspeld dat deze in 2027 zal uitgroeien tot een markt van $ 3,7 miljard.
Hoewel de productie van implantaten een redelijk nieuwe toepassing voor 3D-printen — het werd voor het eerst gebruikt rond 2007 — het heeft een snelle groei doorgemaakt in het afgelopen decennium.
In 2010 ontving een early adopter van Arcam's Electron Beam Melting (EBM) metaal 3D-printtechnologie de eerste FDA-goedkeuringen voor 3D-geprinte implantaten. Zeven jaar later produceerden meer dan 300 3D-printers over de hele wereld orthopedische producten.
Tegenwoordig wordt de technologie gebruikt om heup- en kniegewrichtvervangingen, schedelreconstructie-implantaten en ruggengraatimplantaten te maken. Vanaf 2019 worden naar schatting meer dan 600.000 implantaten geproduceerd met behulp van 3D-printen. In 2027 zal dit aantal de 4 miljoen overschrijden.
Met zo'n enorme groeimogelijkheid is het geen verrassing dat alle grote fabrikanten van medische hulpmiddelen steeds meer de 3D-printtechnologie omarmen.
Stryker, een van de grootste medische technologiebedrijven ter wereld, heeft onlangs zijn eigen 3D-geprinte implantaten gelanceerd, waaronder de 3D-geprinte Tritanium TL Curved Posterior Lumbale Cage. Dit holle ruggengraatimplantaat kreeg in maart 2018 goedkeuring van de FDA.
Naast Stryker investeren andere opmerkelijke fabrikanten van orthopedische hulpmiddelen zoals DePuy Synthes, een dochteronderneming van Johnson &Johnson, en Medtronic zwaar in 3D-printen. De laatste lanceerde in mei 2018 een 3D-printplatform, TiONIC Technology, met als doel complexere ontwerpen en geïntegreerde oppervlaktetechnologieën voor spinale chirurgische implantaten mogelijk te maken.
Naast gevestigde fabrikanten van medische apparatuur zijn er de afgelopen tien jaar ook medische startups ontstaan, die eigen benaderingen hebben ontwikkeld voor 3D-geprinte orthopedische implantaten.
Onder hen bevinden zich bedrijven als Osseus Fusion Systems, Nexxt Spine, 4WEB Medical en SI-BONE. Sommige producten van deze bedrijven hebben al FDA-goedkeuring gekregen en zijn gebruikt om patiënten met succes te behandelen.
Het is duidelijk dat er het afgelopen decennium een opwaarts traject is geweest voor 3D-geprinte implantaten. Maar wat maakt deze technologie precies zo nuttig voor medische implantaten?
De voordelen van 3D-geprinte implantaten
Ontwerpflexibiliteit
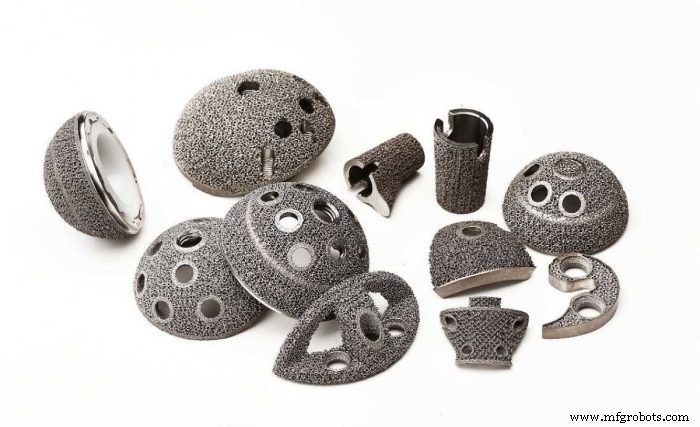
Met 3D-printen kunnen complexe ontwerpen worden gemaakt die anders moeilijk te realiseren zouden zijn met traditionele technologieën. Implantaatfabrikanten kunnen dit voordeel gebruiken om implantaten te produceren met ingewikkelde ontwerpkenmerken zoals trabeculaire structuren.
Trabeculair bot is een van de twee soorten botweefsel die in het menselijk lichaam worden aangetroffen. Het heeft een sponsachtige, poreuze structuur die moeilijk na te bootsen kan zijn in een implantaat. Van oudsher gebruiken implantaatfabrikanten een speciale coating om een trabeculaire structuur op het implantaat te creëren. Dit brengt echter een risico met zich mee van delaminatie en falen van het implantaat.
Met 3D-printen daarentegen kunnen implantaten met een trabeculaire structuur direct worden geproduceerd, waardoor het coatingproces wordt omzeild. Wat nog belangrijker is, is dat de trabeculaire, poreuze structuur die in een 3D-geprint implantaat is geïntegreerd, een sterker implantaat creëert met een verminderd risico op delaminatie.
Een dergelijke ontwerpflexibiliteit wordt geboden door 3D-printtechnologieën voor metaal, zoals Selective Laser Melting of Electron Straal smelten. Deze technologieën passen een krachtige energiebron zoals een laser (SLM) of een elektronenstraal (EBM) toe op een dunne laag van een biocompatibel poeder zoals titanium.
Door dit proces over honderden lagen te herhalen, is het mogelijk om een complex implantaat te creëren dat zich veel efficiënter aanpast aan de menselijke botstructuur dan traditioneel gemaakte implantaten.
Een ander belangrijk voordeel van poreuze 3D-geprinte implantaten is de verbeterde osseo-integratie.
Osseo-integratie is een proces waarbij een implantaat een permanent onderdeel van het lichaam wordt. Door de poreuze trabeculaire structuur kan een bot in de poriën groeien, waardoor de binding tussen het implantaat en het bestaande bot verder wordt versterkt.
Verminderde spanningsafscherming
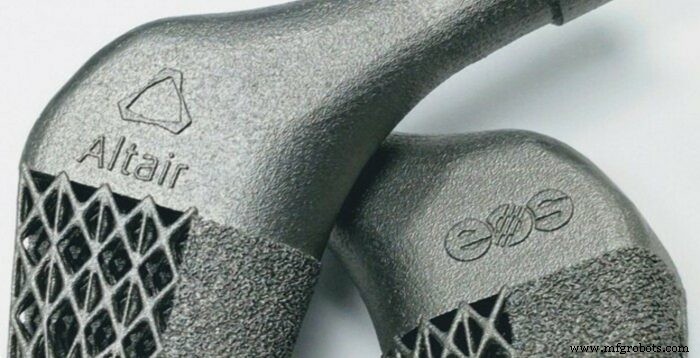
Bovendien kunnen fabrikanten van medische hulpmiddelen implantaten ontwerpen die de botstijfheid en dichtheid van een patiënt nabootsen. Naast het verbeteren van de osseo-integratie, kunnen 3D-geprinte implantaten de afscherming tegen stress verminderen en de fysieke functie verder verbeteren.
Stressafscherming verwijst naar het fenomeen waarbij metalen implantaten typische spanningen van het bot van een patiënt verwijderen. Het resultaat is de vermindering van de botdichtheid, waardoor het bot zwakker wordt. Spanningsafscherming kan leiden tot breuken en dislocaties. Om deze reden is het ontwerpen van een implantaat zo dicht mogelijk bij het botweefsel van de patiënt van cruciaal belang om de bescherming tegen spanningen te verminderen en deze ongewenste effecten te elimineren.
In een recent voorbeeld hiervan combineerde IT-bedrijf Altair software voor 3D-printen en topologie-optimalisatie om een verbeterd heupstamimplantaat te creëren.
Door parameters zoals grootte, gewicht en de verwachte belasting van het implantaat in te voeren, werd topologie-optimalisatiesoftware gebruikt om een nieuw ontwerp voor een heupimplantaat te maken. Het geoptimaliseerde ontwerp verdeelt stress en spanning op een efficiëntere manier dan een generiek implantaat.
Bovendien hielp topologie-optimalisatiesoftware om te bepalen waar het materiaal kon worden vervangen door roosterstructuren om het implantaat lichter te maken.
Tijdens het testen bood het geoptimaliseerde implantaat een vermindering van de spanningsafscherming van 50,7%. Tegelijkertijd nam zijn uithoudingsvermogen toe tot ongeveer 10 miljoen cycli. Dit betekent dat het heupimplantaat bestand is tegen joggen van Los Angeles naar New York en terug — twee keer.
3D-printen van patiëntspecifieke implantaten
In meer complexe gevallen kunnen kant-en-klare implantaten vaak niet de nodige flexibiliteit bieden. 3D-printen kan in dergelijke gevallen helpen, omdat het de mogelijkheid biedt om medische apparaten, waaronder implantaten, aan te passen en te personaliseren.
Om een patiëntspecifiek implantaat te produceren, gebruiken fabrikanten de gegevens die zijn verkregen uit een patiëntscan, zoals een computertomografie (CT) of magnetische resonantiebeeldvorming (MRI) scan. De gegevens van de patiënt worden vervolgens geïmporteerd in CAD, voorbereid voor productie, 3D-geprint en afgewerkt.
Het gebruik van een op maat gemaakt, 3D-geprint implantaat biedt het potentieel voor kortere chirurgische tijd en verbeterde implantaatpasvorm.
Momenteel kan 3D-printen worden gebruikt om schedel- en kaakimplantaten op maat te maken, waarbij esthetische vereisten net zo belangrijk zijn als functionaliteit.
Bijvoorbeeld, een 10-jarige Chinese jongen kreeg in 2018 een 3D-geprint kaakimplantaat. Hij had een tumor in zijn kaak die niet verwijderd had kunnen worden zonder significante gezichtsmisvormingen te veroorzaken.
Het chirurgisch team concludeerde dat een conventionele gezichtsreconstructie te gevaarlijk was voor zo'n jonge patiënt. Op zoek naar een betere oplossing, schakelden ze over op 3D-printen, waarbij ze digitale modellen van de kaak van de jongen gebruikten om een perfect aangepast titaniumimplantaat op maat te ontwerpen.
Volgens de chirurgen was het kaakimplantaat gemakkelijk te plaatsen omdat het was gebaseerd op de anatomie van de patiënt. Drie maanden na de ingreep bleek de implantatie succesvol, de kaak werd goed uitgelijnd en er groeide een grote hoeveelheid weefsel.
3 voorbeelden van 3D-geprinte implantaten
Een 3D-geprint heupimplantaat maakt extreem bergbeklimmen mogelijk
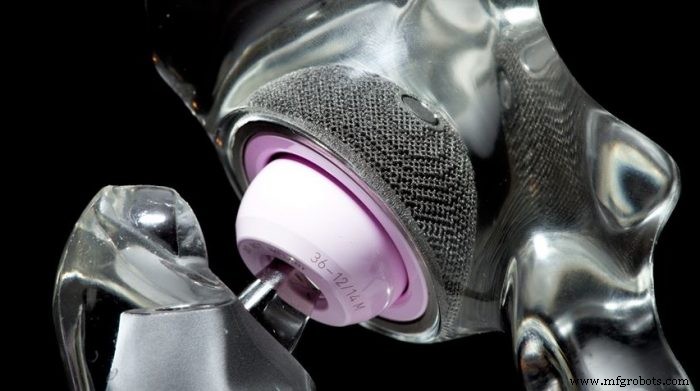
Romano Benet en zijn vrouw, Nives Meroi, beklimmen al jaren de gevaarlijkste bergen ter wereld. In 2017 was het bergsportteam het eerste paar dat alle 14 van 's werelds hoogste toppen beklom. Het bereiken van deze prestatie zou echter waarschijnlijk onmogelijk zijn gebleken zonder de hulp van 3D-printen.
Benet leed aan bilaterale avasculaire necrose, wat in wezen leidt tot het instorten van het bot.
Toen de diagnose voor het eerst werd gesteld, waren Benet en zijn vrouw drie toppen te kort om het wereldcircuit van alle 14 bergen te voltooien. Om hun reis voort te zetten, had de bergbeklimmer een stabiel implantaat nodig waarmee hij snel zou herstellen.
Om deze reden besloot de chirurg van Benet voor een 3D-geprint implantaat te gaan.
Het implantaat, bekend onder de merknaam Delta Trabecular Titanium (TT) cup, werd geproduceerd door het Italiaanse bedrijf voor medische hulpmiddelen, Lima Corporate, met behulp van de EBM 3D-printer van Arcam.
Door Lima's Trabecular Titanium-technologie en 3D-printen te combineren, was het mogelijk implantaten te maken die de poreuze structuur van natuurlijk bot nabootsten.
Dankzij deze trabeculaire structuur is een 3D-geprint implantaat bestand tegen mechanische spanningen tijdens zware inspanningen. De chirurg van Benet, die een handvol keren TT-cups bij andere patiënten had geïmplanteerd, geloofde dat 3D-geprinte implantaten niet alleen een grote stabiliteit en sterkte bieden, maar ook het potentieel hebben om langer mee te gaan dan de levensduur van conventionele implantaten.
Toen Benet zijn eerste, niet-3D-geprinte implantaat ontving, had hij vele maanden van inactiviteit geleden voordat hij weer begon te klimmen. Met een 3D-geprint implantaat kon de bergbeklimmer zijn activiteit na twee en een halve maand hervatten.
Uiteindelijk deed het 3D-geprinte implantaat zijn werk:het stelde Benet in staat snel te herstellen en succesvol af te ronden zijn zoektocht naar het bereiken van de laatste drie grote hoogtepieken.
Osseus Fusion Systems:op weg naar gepersonaliseerde metalen implantaten

Osseus Fusion Systems, opgericht in 2012, is een in de VS gevestigd bedrijf met een focus op de ontwikkeling van geavanceerde medische producten voor letsels aan de wervelkolom.
Om de kwaliteit en functionaliteit van zijn producten te verbeteren, heeft Osseus een eigen 3D-printtechnologie ontwikkeld, PL3XUS genaamd.
De technologie is gebaseerd op 3D-printen met poederbedfusie, met name Selective Laser Melting (SLM), en kan 80% poreuze titaniumimplantaten creëren, geoptimaliseerd voor botfusie en biologische fixatie (het proces waarbij een levend bot permanent hecht aan het implantaatoppervlak).
In augustus 2018 behaalde Osseus FDA 510(k)-goedkeuring voor Aries, zijn familie van additief vervaardigde lumbale interbody fusie-apparaten. De Aries-familie van implantaten is ontworpen om chirurgen te helpen rugpijn te verlichten en de hersteltijd van de wervelkolom te verkorten.
Eerder dit jaar is het Ram-product van Osseus voor het eerst in de praktijk gebracht door Joseph Spine, een centrum voor wervelkolom- en scoliosechirurgie. PL3XUS-technologie maakte het mogelijk om het implantaat te ontwerpen met een architectuur die vergelijkbaar is met het bot van een patiënt, waardoor de ingroei van het bot wordt vergemakkelijkt.
In de komende jaren is Osseus van plan om gepersonaliseerde apparaten te lanceren op basis van CT-scans, röntgenfoto's en MRI's van de patiënt.
Met deze volgende stap wil het bedrijf ziekenhuizen in staat stellen superieure patiëntenzorg te bieden en, uiteindelijk, de operatieresultaten voor patiënten verder te verbeteren.
3D-printen van implantaten met hoogwaardige thermoplasten
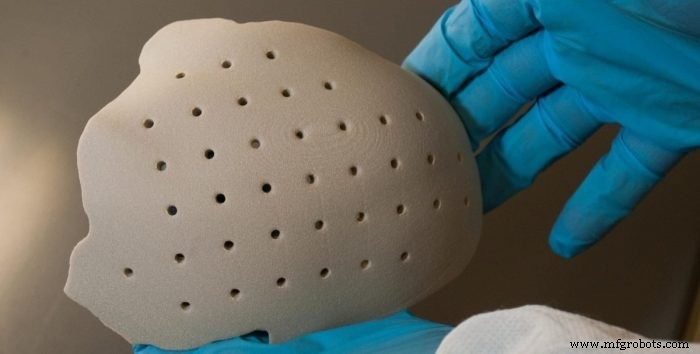
Naast titanium en andere biocompatibele metalen kan 3D-printen worden gekoppeld aan polymeren zoals PEEK en PEKK om implantaten te produceren. Deze thermoplasten staan bekend om hun hoge sterkte en biocompatibiliteit, en bieden ook enkele voordelen ten opzichte van metalen implantaten, zoals lagere kosten en radiolucentie.
In 2013 werd Oxford Performance Materials (OPM) het eerste bedrijf dat FDA-goedkeuring kreeg voor een patiëntspecifiek 3D-geprint PEKK-schedelimplantaat. Tegen 2017 had OPM meer dan 1400 schedelimplantaten verzonden en FDA-goedkeuringen ontvangen voor twee andere apparaten:maxillofaciale en spinale implantaten.
Het bedrijf maakt gebruik van Selective Laser Sintering-technologie, die het eigen OsteoFab®-platform van OPM voor de ontwikkeling en productie van implantaten aandrijft. Met dit platform kon bijvoorbeeld een patiëntspecifiek schedelimplantaat worden ontworpen, vervaardigd, getest en verzonden door OPM in slechts 3 werkdagen. In minder dan een week hebben chirurgen de operatie met succes uitgevoerd, zonder enige snij- of booraanpassingen aan te brengen om het implantaat opnieuw vorm te geven.
3D-printen voor medische implantaten:impact maken
Biocompatibiliteit, draagvermogen en duurzaamheid zijn de fundamentele vereisten voor orthopedische implantaten. 3D-printen voldoet volledig aan deze eisen en verbetert tegelijkertijd de functionaliteit en pasvorm van implantaten.
Dit kan voornamelijk worden toegeschreven aan het vermogen van de technologie om complexe vormen zoals poreuze structuren te creëren, die het lichaam van een patiënt helpen zich aan te passen aan een implantaat sneller en met minder complicaties.
In de toekomst zal 3D-printen voor implantaten blijven evolueren. Een bijzonder spannend gebied van lopend onderzoek is de combinatie van 3D-geprinte implantaten en sensoren. Door sensorgestuurde implantaten te ontwikkelen, kunnen zorgverleners de patiëntresultaten aanzienlijk verbeteren.
Ingebouwde sensoren kunnen gegevens verzamelen zoals temperatuur rond het implantaat, beweging en belasting die op het implantaat wordt uitgeoefend. Dit stelt chirurgen in staat om vroegtijdig op mogelijke problemen te reageren en de behandeling af te stemmen op de behoeften van individuele patiënten.
Renishaw, een Britse fabrikant van metalen 3D-printers, en Western University hebben het Additive Design in Surgical Solutions (ADEISS) Centre al opgezet op de campus van de universiteit. Het centrum brengt academici en clinici samen om te werken aan de ontwikkeling van nieuwe 3D-geprinte medische apparaten zoals hierboven beschreven.
Het is duidelijk dat de 3D-printtechnologie een sterke voet aan de grond krijgt binnen het orthopedische segment.
De technologie zal echter moeten rijpen om het potentieel voor op maat gemaakte implantaten die op het punt van zorg worden geproduceerd, echt te ontsluiten.
Toegegeven, slechts een klein percentage van de implantaten wordt momenteel op maat gemaakt met 3D-printen. Hoewel de technologie een enorm potentieel heeft, moeten vragen rond standaardisatie en regelgeving nog steeds worden aangepakt.
Dat gezegd hebbende, het maken van op maat gemaakte medische implantaten is waar de technologie de grootste impact zou kunnen hebben en meer mensen in staat zou stellen te profiteren van gepersonaliseerde gezondheidszorg. We zijn van mening dat deze richting de komende jaren aanzienlijk zal aantrekken.
In ons volgende artikel zullen we bekijken hoe 3D-printen de productie van raketten kan verbeteren. Blijf op de hoogte!
3d printen
- Micro tantaal poeders voor medische toepassing
- Applicatie Spotlight:3D-printen voor digitale tandheelkunde &Clear Aligner-productie
- Applicatie Spotlight:3D-printen voor fietsproductie
- Applicatie Spotlight:3D-printen voor lagers
- Applicatie Spotlight:3D-printen voor warmtewisselaars
- Applicatie Spotlight:3D-printen in de spoorwegindustrie
- Applicatie Spotlight:5 elektronische componenten die kunnen profiteren van 3D-printen
- Applicatie Spotlight:3D-printen voor schoenen
- Applicatie Spotlight:3D-geprinte raketten en de toekomst van de fabricage van ruimtevaartuigen
- Applicatie Spotlight:3D-geprinte brillen
- 10 sterkste materialen voor 3D-printen