FDM 3D-printen:waar zijn we vandaag?
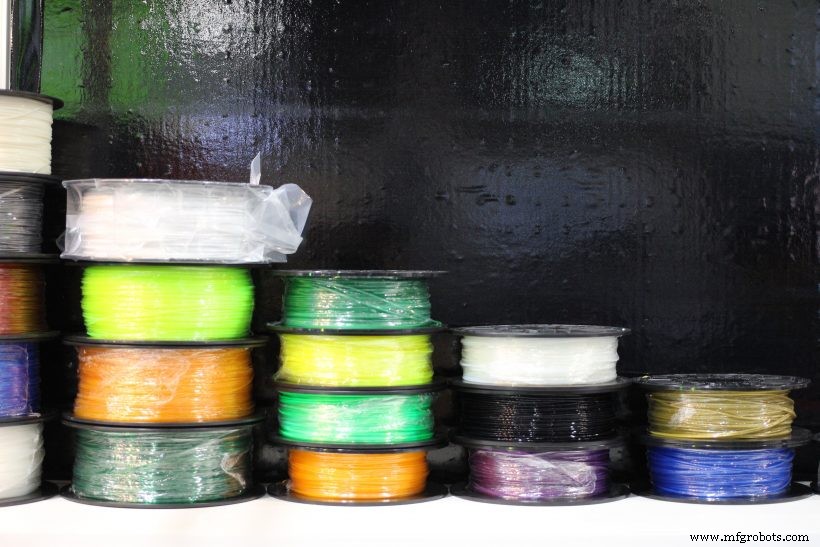
Vooruitgang in op extrusie gebaseerd 3D-printen verandert het traject van Fused Filament Fabrication (FFF)-technologie.
FFF, of FDM (Fused Deposition Modelling), zoals het vaker wordt genoemd, is een van de meest gebruikte 3D-printtechnologieën. Omdat de acceptatie in alle industriële segmenten toenam, was FDM in 2017 de meest inkomstengenererende 3D-printtechnologie en zou het de grootste installed base (SmarTech) hebben.
Dus wat heeft de groei en volwassenheid van de technologie gestimuleerd? En hoe zal 3D-printen op basis van extrusie zich in de toekomst ontwikkelen?
Om deze vragen te beantwoorden, zal dit artikel een kijkje nemen naar enkele van de belangrijkste ontwikkelingen die FDM vormgeven en wat de toekomst biedt voor deze opwindende technologie.
Belangrijke mijlpalen in de ontwikkeling van FDM
- 1989 :Scott en Lisa Crump patenteren een nieuwe additieve productiemethode, het handelsmerk Fused Deposition Modeling (FDM), en richtten hardwarebedrijf Stratasys op.
- 1991 :Stratasys commercialiseert voor het eerst FDM 3D-printen.
- 2005 :markeert het begin van het RepRap-project, dat helpt de kosten van FDM 3D-printen te verlagen.
- 2008 :Stratasys kondigt aan dat het hoogwaardige ULTEM 9085 zal aanbieden voor zijn FDM 900mc- en 400mc-machines - een enorme stap voorwaarts voor FDM-materialen.
- 2009 :De eerste FDM-patenten verlopen, waardoor enthousiastelingen hun eigen DIY FDM 3D-printers kunnen ontwikkelen en commercialiseren. Bedrijven als MakerBot en Lulzbot worden enorm succesvol met hun DIY-printerkits.
- 2011 :Ultimaker, een toonaangevende fabrikant van desktop FDM 3D-printers, wordt opgericht.
- 2013 :Stratasys neemt MakerBot over, een fabrikant van desktop 3D-printers.
- 2013 :Markforged, een hardwarefabrikant die composiet FDM 3D-printtechnologie aanbiedt, wordt opgericht.
- 2014 :Grootschalige FDM 3D-printerfabrikant BigRep wordt opgericht.
- 2015 :Voodoo Manufacturing start zijn 3D-printbedrijf, dat tegen 2019 zal uitgroeien tot een digitale fabriek met meer dan 200 FDM-machines.
- 2017 :Stratasys introduceert zijn Continuous 3D Build Demonstrator - een modulaire 3D-printeenheid voor bewerkingen met een hoge doorvoer.
- 2018 :Essentium commercialiseert zijn High Speed Extrusion-platform, met zijn FlashFuse-technologie die elektrische verwarming gebruikt om onderdelen te 3D-printen.
De oorsprong van FDM
De opkomst van 3D-printen op basis van extrusie gaat terug tot het einde van de jaren tachtig, toen ingenieur en uitvinder Scott Crump een nieuwe methode voor snelle prototyping ontwikkelde.
In 1989 patenteerde Crump de nieuwe technologie en noemde het Fused Depositiemodellering. Datzelfde jaar richtten Scott en Lisa Crump Stratasys samen op en leverden ze twee jaar later hun eerste FDM-machine, de 3D Modeler.
Sindsdien heeft de FDM-technologie enorme aantrekkingskracht gewonnen, de leemte opvullen in goedkopere rapid prototyping-oplossingen.
Tegenwoordig blijft Stratasys een van de grootste hardwarebedrijven binnen de 3D-printindustrie, met 9 modellen van zijn FDM-machines en meerdere Polyjet 3D-printers.
De huidige FDM 3D-printers gebruiken hetzelfde proces van het smelten en extruderen van thermoplastische materialen in een laaggewijze manier, als de eerste FDM-machine dertig jaar geleden.
Dat gezegd hebbende, zou het verkeerd zijn om aan te nemen dat de technologie niet is geëvolueerd. Talloze ontwikkelingen hebben FDM 3D-printen vorm gegeven, waardoor het een van de meest gebruikte additieve technologieën is geworden.
De opkomst van het RepRap-project en goedkope FDM
Het succes van FDM-technologie kan deels worden verklaard door de opkomst van het RepRap-project en het aflopen van verschillende FDM-patenten aan het einde van de jaren 2000.
Het RepRap-project promootte het concept van open-source, zelfreplicerende 3D-printers. Het concept werd voor het eerst overgenomen door de doe-het-zelfgemeenschap. Maar na het verstrijken van de belangrijkste FDM-patenten van Stratasys aan het einde van de jaren 2000, doken er veel bedrijven op die op RepRep gebaseerde FDM 3D-printers wilden commercialiseren.
Dit heeft geleid tot een golf van FDM desktop 3D-printers tegen aanzienlijk lagere kosten - waardoor de technologie een geweldig startpunt is voor bedrijven die nieuw zijn in de technologie.
De jaren 2010:een nieuwe generatie FDM
De opkomst van de RepRap-beweging en het verstrijken van de belangrijkste FDM-patenten hebben de ontwikkeling van de technologie in het afgelopen decennium aanzienlijk versneld. Er zijn een aantal veelbelovende bedrijven ontstaan die FDM 3D-printen verder willen bevorderen.
Baanbrekend continu 3D-printen van koolstofvezel
In 2014 maakte een kleine startup, Markforged, indruk met zijn 3D-printtechnologie Continuous Filament Fabrication (CFF). Het bedrijf is naar verluidt de eerste die continu fiber 3D-printen mogelijk maakt, waardoor nieuwe, industriële kansen voor FDM-technologie ontstaan.
Aangedreven door CFF, gebruiken de compacte en desktop 3D-printers van Markforged twee printkoppen:één om op nylon gebaseerd filament te extruderen en de andere om doorlopende strengen van zeer sterke vezels te leggen, waaronder koolstofvezel, Kevlar en glasvezel .
De versterkende vezels vormen de "ruggengraat" van het geprinte onderdeel, waardoor stijve, sterke en duurzame onderdelen ontstaan.
Bijvoorbeeld, de industriële X7-machine van Markforged, de nieuwste van zes Markforged's polymeer 3D-printers, zou onderdelen sterker en 40% lichter printen dan 6061 aluminium.
Geprijsd op $70.000, heeft de X7 een bouwvolume van 330 x 270 x 200 mm en een laaghoogte van 50 micron. Voor een relatief laag geprijsde machine zijn deze specificaties behoorlijk behoorlijk, om nog maar te zwijgen van het vermogen van de X7 om duurzame gereedschappen te printen, evenals functionele reserve- en eindgebruiksonderdelen.
Door de mogelijkheid te bieden om met versterkte materialen te printen, heeft Markforged een zeer winstgevende markt aangeboord. Alleen al in 2018 heeft het bedrijf naar verluidt meer dan 2500 industriële 3D-printers verzonden. Met zo'n hypergroei lag Markforged op schema om een van de grootste AM-bedrijven in de branche te worden.
De nieuwe maatstaf voor grootformaat FDM-printen?
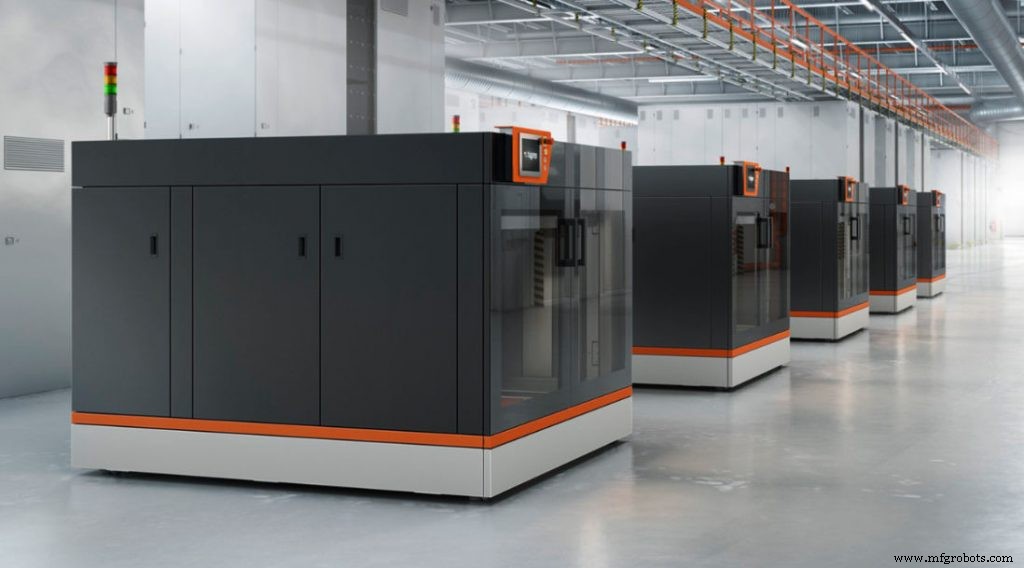
Grootformaat 3D-printen heeft het potentieel om veel uitdagingen op te lossen waarmee fabrikanten worden geconfronteerd bij het maken van prototypes en het produceren van grotere onderdelen.
Dergelijke onderdelen hebben doorgaans een langere doorlooptijd, aangezien montage vereist is. Ze vereisen ook grotere gereedschappen om te produceren, wat vaak tot aanzienlijke kosten leidt.
Een bedrijf dat helpt om deze uitdagingen het hoofd te bieden, is BigRep. BigRep, opgericht in 2014, positioneert zichzelf als de fabrikant van de grootste extrusie 3D-printers op de markt, met printvolumes van meer dan 1m³.
Hoewel het 3D-printen van grote objecten zijn voordelen heeft, is er ook één belangrijke beperking:snelheid. Het afdrukken van grotere onderdelen kan dagen of zelfs weken duren, met een verhoogd risico op afdrukfouten.
BigRep probeert dit probleem op een aantal manieren aan te pakken.
In het verleden introduceerde BigRep grotere nozzles om sneller grotere hoeveelheden plastic te kunnen extruderen en introduceerde het ook bijpassende filamentspoelen met groot gewicht.
In 2017 , begon het bedrijf met de productie van zijn "high speed" filament, waardoor de printtijden tot 50% kunnen worden verkort.
Maar misschien wel een van de meest opwindende ontwikkelingen is BigRep's Metering Extrusion Technology (MXT) ).
Op formnext 2018 introduceerde BigRep twee nieuwe MXT-aangedreven 3D-printers:de BigRep PRO en BigRep EDGE. Het MXT-extrudersysteem is ontwikkeld in samenwerking met Bosch Rexroth en heeft verschillende belangrijke kenmerken die het onderscheiden van standaardextruders.
Het heeft een speciaal reservoir waar het gesmolten materiaal wordt vastgehouden. Een tandwiel, aangedreven door een stappenmotor, haalt een bepaalde hoeveelheid van het materiaal uit dat reservoir en duwt het in het mondstuk.
Deze benadering geeft volledige controle over de snelheid en hoeveelheid materiaal dat wordt gestort. Volgens BigRep maakt het MXT-systeem zijn nieuwe printers vijf keer sneller dan de huidige extrusiemachines en helpt het om een veel grotere precisie te bereiken.
Het huidige MXT-systeem is slechts de eerste versie van het MXT-concept, maar met al zijn voordelen zal het spannend zijn om te zien hoe deze technologie zich in de toekomst zal ontwikkelen.
Doordrenkt met isotrope kracht
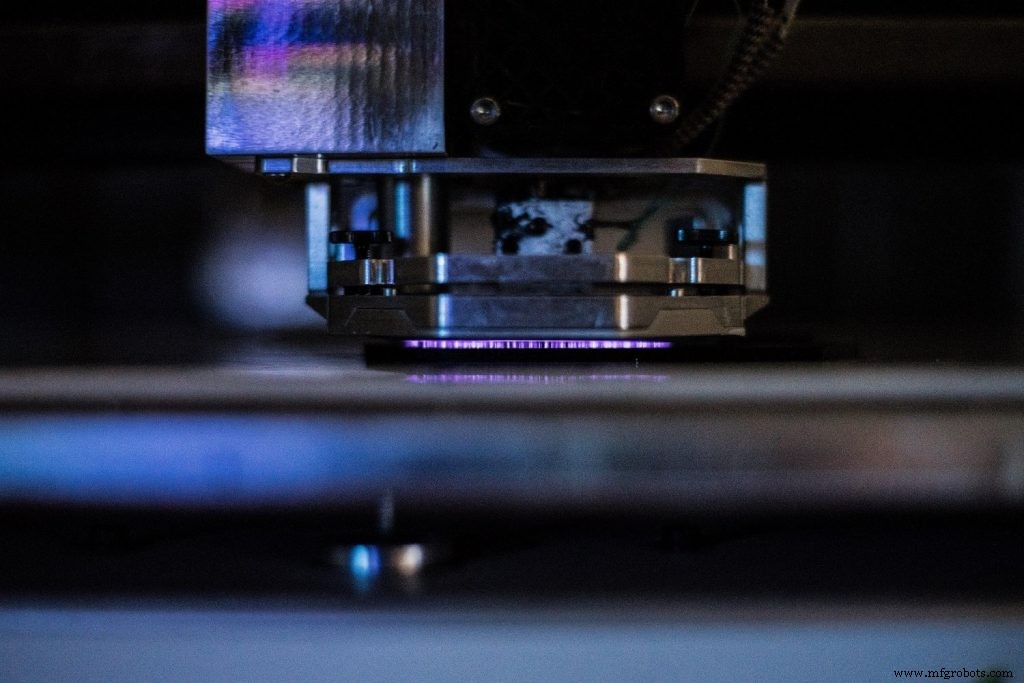
Samen met snelheidsbeperkingen zijn anisotrope onderdelen een ander veelvoorkomend probleem bij FDM 3D-printen, vanwege de laaggewijze aard van het printproces.
Het laag voor laag afzetten van materiaal resulteert in een deelzwakte in de Z-as (de richting waarin de lagen worden afgezet). Dus hoewel een spuitgegoten onderdeel bijna 100% isotroop kan zijn (even sterk in alle richtingen), verliezen FDM-onderdelen doorgaans aan kracht in de Z-as.
Sommige industriële machines pakken dit probleem aan door een behuizing te gebruiken om het hele gebouw te verwarmen. Hoewel deze oplossing helpt om de hechting tussen lagen te verbeteren, is het vaak te veel energie verbruikend.
3D-printbedrijf Essentium heeft een nieuwe, veelbelovende FDM-technologie ontwikkeld om de mechanische sterkte van 3D-geprinte onderdelen te verbeteren.
Bekend als FlashFuse, omvat de technologie de afzetting van een energiegevoelige gloeidraad en de toepassing van een elektrische stroom. Deze stroom verwarmt het onderdeel, waardoor de lagen effectief samen worden gevormd.
Deze aanpak heeft twee voordelen.
Ten eerste bereiken onderdelen die 3D-geprint zijn met behulp van FlashFuse-technologie een sterkte die vergelijkbaar is met die van spuitgegoten onderdelen. Ten tweede voorkomt het vervorming van onderdelen, zoals kromtrekken, omdat de temperatuur stabiel blijft tijdens het printproces.
Deze technologie drijft nu Essentium's High Speed Extrusion (HSE) 180-S 3D-printer aan, die $ 75.000 kost.
Door enkele van de belangrijkste barrières bij FDM 3D-printen te overwinnen, heeft het bedrijf $ 22 miljoen opgehaald in een Serie A-ronde onder leiding van BASF Venture Capital. Met de recente financiering wil Essentium zijn technologie voor productietoepassingen pushen en een nieuwe maatstaf zetten voor FDM 3D-printen.
FDM-materialen van industriële kwaliteit
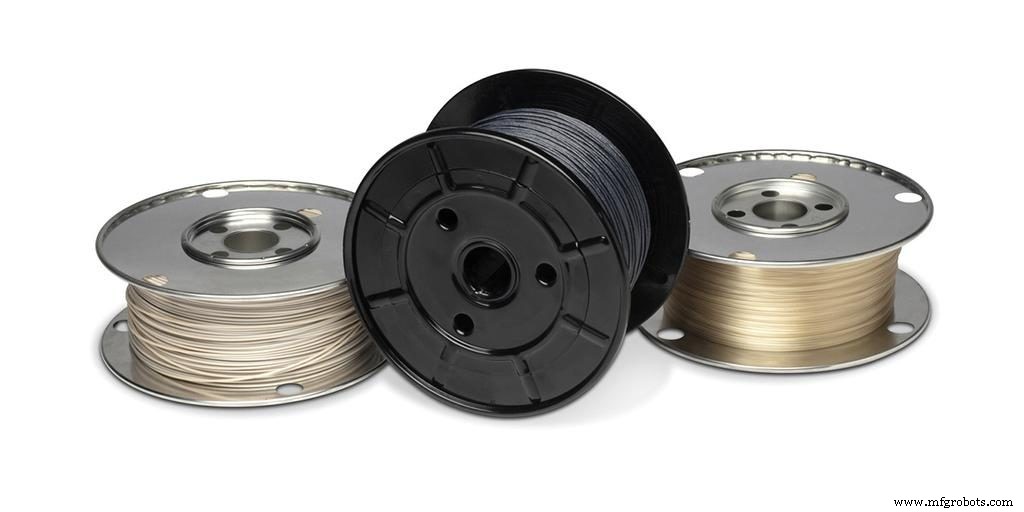
Hoewel de markt voor FDM-materialen nog jong is, is deze in de loop der jaren aanzienlijk geëvolueerd, waardoor de materiaalwetenschap verder gaat dan standaard PLA- en ABS-filamenten.
Vandaag de dag kunnen FDM-gebruikers onder meer composiet-, nylon-, flexibele, biocompatibele en technische materialen kopen.
Bijzonder spannend is de mogelijkheid om te printen met hoogwaardige materialen zoals ULTEM en PEEK.
Deze thermoplasten zijn bijzonder uitdagend om mee te werken vanwege hun hoge smelttemperaturen. Veel huidige FDM-machines zijn echter uitgerust met extruders voor hoge temperaturen, waardoor FDM een van de weinige additieve technologieën is die deze hoogwaardige thermoplasten kunnen verwerken.
Veel van de ontwikkelingen in FDM-materialen zijn mogelijk gemaakt dankzij het toenemende aantal chemische bedrijven dat zich bij de industrie aansluit, met als doel het industriële gebruik van 3D-printen te bevorderen. Deze omvatten BASF, SABIC, Verbatim (Mitsubishi Chemical Group), Evonik en Solvay, om er maar een paar te noemen.
Solvay heeft bijvoorbeeld onlangs PEEK- en PPSU-filamenten op de markt gebracht. Beide materialen hebben uitzonderlijke eigenschappen:PEEK staat bekend om zijn uitstekende sterkte-gewichtsverhouding, terwijl PPSU een hoge hitte-, chemische en slagvastheid bezit.
De beschikbaarheid van dergelijke thermoplasten van productiekwaliteit maakt belangrijke toepassingen mogelijk, zoals vliegtuigonderdelen, autolagers, olie- en gascomponenten en medische apparatuur.
Er zijn nog veel meer FDM-thermoplasten nog te ontwikkelen. Maar de groeiende vraag zal hun ontwikkeling helpen stimuleren, waardoor nieuwe toepassingen voor 3D-printen mogelijk worden.
3D-printboerderijen:de toekomst van FDM?
Er zijn enkele uitdagingen geweest die het gebruik van FDM 3D-printen in productietoepassingen beperken, waaronder zwakke onderdelen en lage afdruksnelheden.
Recente ontwikkelingen in FDM-technologie helpen echter de barrières van snelheid en kracht op te heffen. Maar om FDM echt van de grond te krijgen als productietechnologie, moet het schaalbaarder worden.
Een van de oplossingen kan liggen in zogenaamde FDM 3D-printfarms. Bij dergelijke boerderijen is een netwerk van een tiental of meer 3D-printers nodig om 24-uurs productie mogelijk te maken. Voodoo Manufacturing is een voorbeeld van een bedrijf dat deze aanpak in de praktijk brengt.
Het bedrijf heeft meer dan 200 FDM 3D-printers en gebruikt geavanceerde software om automatisch 3D-printtaken toe te wijzen aan beschikbare machines. Met behulp van zijn 3D-printboerderij kan Voodoo Manufacturing honderden en zelfs duizenden bestellingen uitvoeren tegen spuitgietprijzen.
Ook fabrikanten van 3D-printers bouwen voort op dit concept. In 2017 presenteerde Stratasys zijn Continuous Build 3D Demonstrator, een modulaire unit met meerdere FDM 3D-printercellen, die elk gelijktijdig werken en worden bestuurd door een centrale, cloudgebaseerde architectuur.
Stratasys heeft de commerciële beschikbaarheid van het Continuous Build-platform nog niet aangekondigd. Het bedrijf is echter van mening dat deze aanpak de droom van 3D-printen voor productie kan waarmaken.
In het licht van de verschuiving naar robuustere materialen en nieuwe productiestrategieën, is FDM klaar voor de volgende acceptatiegolf. Sterkere en grotere onderdelen en een sneller en beter schaalbaar 3D-printproces zullen nieuwe markten openen voor op extrusie gebaseerde machines, waardoor FDM-technologie een enorme productiemogelijkheid wordt.
3d printen
- Stressvrije reiniging voor FDM-afdrukken
- Ontwikkelingsnormen voor 3D-printen:waar staan we vandaag? (update 2020)
- Metaal 3D-printen:waar zijn we vandaag?
- Stereolithografie en digitale lichtverwerking:waar zijn we vandaag?
- Hoe desktop 3D-printers 3D-printen transformeren
- Hoe volwassen zijn 3D-printtechnologieën voor metaal?
- 3D-printen in de gezondheidszorg:waar staan we in 2021? (Bijgewerkt)
- Industrie 4.0 fact-check:waar staan we vandaag?
- Nieuwe doorbraken in FDM van Stratasys
- 3D-technologie vergelijking:SLA vs. FDM
- FDM 3D-printen:desktop versus industrieel