Automated Preforming, Part 7:Fill Gesellschaft
Dit is het laatste deel van een zevendelige serie over voorvormen. Klik op de onderstaande links voor meer informatie over deze serie:
BRON:Vullen Gesellschaft
Geschiedenis van automatisering
De eerste machines van Fill werden ontwikkeld om de productie van ski's voor Fischer te automatiseren. Tegenwoordig is er 25 procent van de arbeiders nodig om 80 procent van het oorspronkelijke jaarlijkse productievolume te produceren. Merk ook op dat ski's een hybride ontwerp zijn, bestaande uit lagen glas en/of koolstofvezelcomposiet, houten kernen, stalen randen en meerdere soorten plastic.
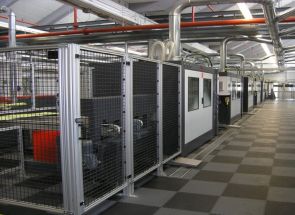
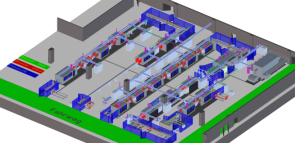
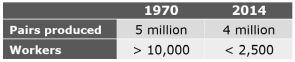
Vulling heeft geleverd meerdere generaties geautomatiseerde apparatuur voor het produceren van composietski's.
BRON:Fill Gesellschaft 2017 CAMX-presentatie.
BMW
Toen BMW de i3-, i8- en nieuwe modellen uit de 7-serie ontwikkelde, die allemaal gebruik maken van met koolstofvezel versterkte kunststof (CFRP) composieten, leverde Fill een reeks automatiseringsoplossingen.
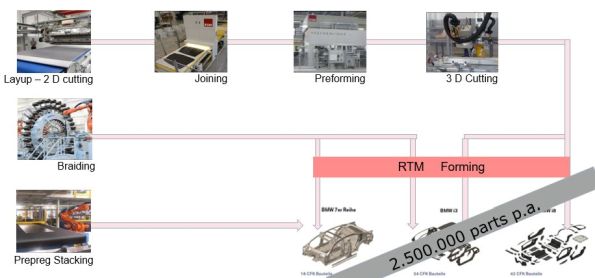
BRON:Vullen Gesellschaft 2017 CAMX presentatie
Samengestelde monocoques
Fill ontwikkelde ook een unieke productielijn voor Mubea CarboTech die CFRP-monocoques kan produceren voor twee verschillende automodellen:de Volkswagen VW XL1 en de Porsche 918 Spyder. Deze geautomatiseerde lijn omvatte meerdelige aangedreven vormgereedschappen, HP-RTM (high-press resin transfer molding) pers, naharding en bewerkingsmogelijkheden.
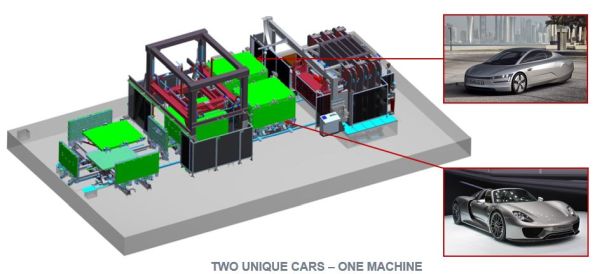
Vul de meegeleverde composiet monocoque productielijn voor Mubea CarboTech.
BRON:Fill Gesellschaft 2017 CAMX presentatie
Layup automatiseren
Voor geautomatiseerde layup heeft Fill systemen ontwikkeld voor een reeks verschillende materialen, waaronder droge stof tot 3 m breed (voor productie in grotere volumes bij BMW). Het SpeedLayer 800 automatische liggerkap-legsysteem voor windturbinebladen past unidirectionele koolstofvezel prepreg toe tot 800 mm breed met een gerapporteerde snelheid van 1,5 m/s en een nauwkeurigheid van ±1,5 mm. Het kan prepreg-rollen van 600 kg aan en integreert procesvalidatie- en kwaliteitsborgingsfuncties.
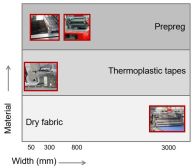
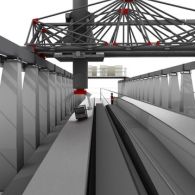
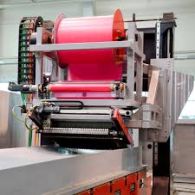
Fill is ontwikkeld een reeks geautomatiseerde layup-systemen (links) inclusief SpeedLayer 800 voor windblade spar-doppen met UD carbon prepreg tot 800 mm breed (rechts).
BRON:Fill Gesellschaft 2017 CAMX presentatie
Het Low-Cost Flexible Integrated Composite Process (LOWFLIP)-project was een 3-jarig (oktober 2013-okt 2016) door de EU gefinancierd initiatief met onder meer Fill en negen andere partners, gericht op het automatiseren van prepreg lay-up voor uit autoclaaf (OOA) uitgehard transport structuren. Het bestond uit drie demonstranten:
- 2,5 × 2,9 m voorwand voor een vrachtwagentrailer
- 1,2 m lange autodwarsbalk
- 1,0 × 1,2 m verstijfd vliegtuigstaartconuspaneel
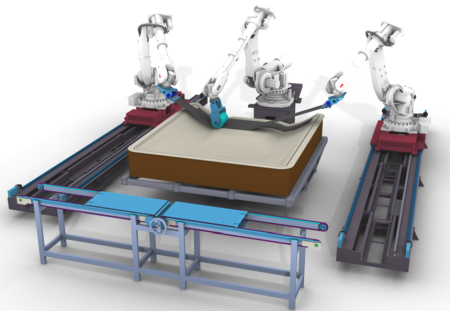
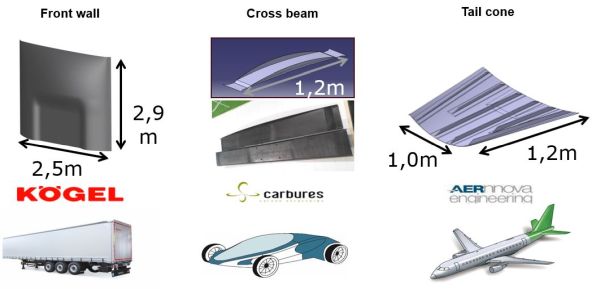
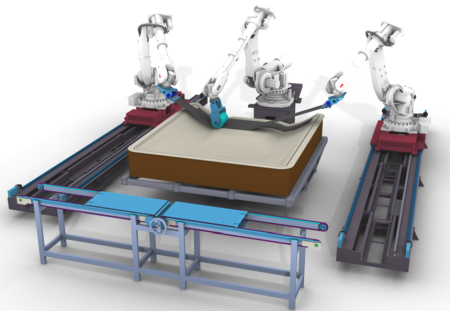
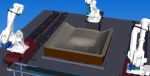
Animatie
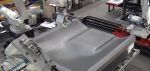
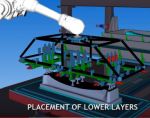
Fill werkte samen met negen partners in LOWFLIP om een geautomatiseerde layup-cel te ontwikkelen voor de productie van grote composiet transportstructuren zonder autoclaaf.
BRON:Fill Gesellschaft 2017 CAMX presentatie
"We gebruikten elektrische weerstandsverwarming om de mal tot 120 °C te verwarmen", herinnert Wilhelm Rupertsberger, hoofd van Fill's Competence Center for Composites and Plastics, zich. "Het materiaal stond altijd onder spanning tijdens geautomatiseerde lay-up," voegt hij eraan toe, "en we bereikten kreukvrij draperen rechtstreeks op de mal. We hebben een menselijk proces gebouwd, maar dan met robots om de herhaalbaarheid te verbeteren.”
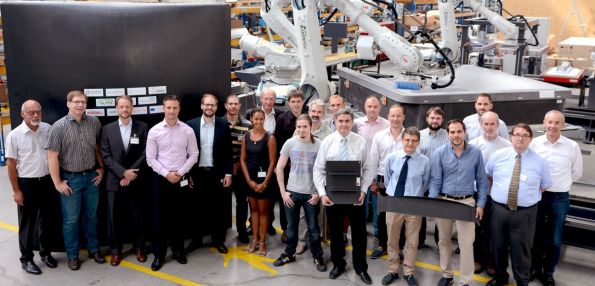
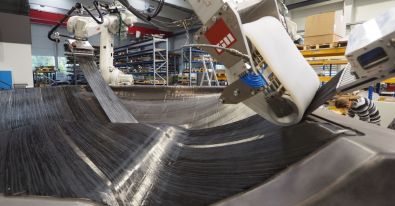
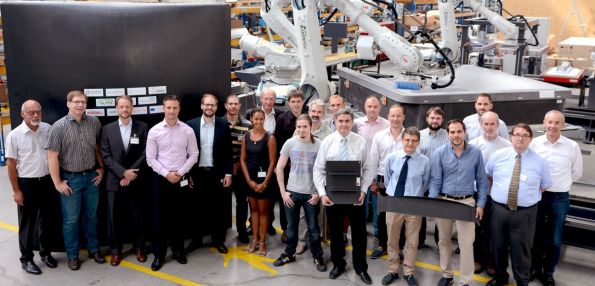
Je kunt de muur van de vrachtwagentrailer links zien, evenals de demonstrators van de autodwarsbalk en het vliegtuigstaartkegelpaneel op de LOWFLIP-teamfoto hierboven .
BRON:Fill Gesellschaft 2017 CAMX presentatie
Meerlaags tot meerlaags systeem
Het Multi-Layup-systeem van Fill is ontwikkeld voor de productie van carrosserie-in-witte (BIW) onderdelen voor auto's, zoals achterwanden en onderste bumperverstevigingen met behulp van thermoplastische tapes. Het was de bedoeling dat deze onderdelen omgevormde ribben en andere kenmerken zouden bevatten, dus de lay-upcyclus voor de voorvorm zou moeten overeenkomen met de daaropvolgende spuitgietcyclus.
Mijn JEC 2017-blogpost na de show bevatte een video van het Multi-Layup-systeem, dat tapes van meerdere rollen invoerde, waarbij alle benodigde tapes per laag tegelijk werden geplaatst, in plaats van serieel, één voor één. Op deze manier bereikte het een cyclustijd van 10-15 seconden per laag.
Fill heeft het systeem nu verder aangepast en hernoemd tot Multilayer. Hij voert, snijdt en plaatst tot 16 banden met een breedte tot 50 mm (elk 0,01-0,04 mm dik) op een draaitafel. Het tapelegbed kan onderdelen produceren tot 1,6 × 1,6 m. Tapes worden aangebracht met een snelheid van ≈500 m 2 /uur—elke 12-15 seconden wordt een volledige laag aangebracht gedurende een cyclustijd van ongeveer 1 minuut per voltooide voorvorm. Lagen worden niet volledig geconsolideerd, maar verbonden via thermische binding. Omdat elke spoel geen tape meer heeft, wordt deze automatisch verwisseld zonder de machine te stoppen.
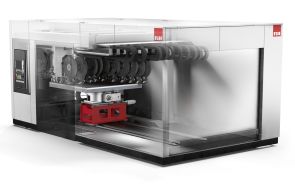
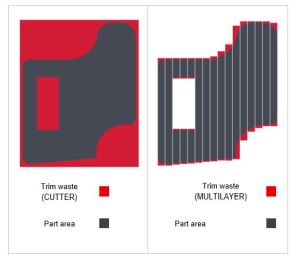
Vullen van meerlaagse geautomatiseerde Het preforming-systeem zorgt voor een aanzienlijke vermindering van snijafval door tapes alleen te plaatsen waar dat nodig is en ze zo nodig te oriënteren om op maat gemaakte laminaten te verkrijgen.
BRON:Fill Gesellschaft 2017 CAMX presentatie
Afgewerkte preforms worden vervolgens geconsolideerd in een pers. "We hebben Multilayer geïntegreerd met een geautomatiseerde consolidatiepers en Engel-spuitgietcel die samen een cyclustijd van 1 minuut leveren", zegt Rupertsberger. Fill ontving eerder dit jaar een bestelling voor het eerste meerlagensysteem van de Swinburne University of Technology (Melbourne, Australië) en zal de apparatuur voor het eerst live demonstreren op JEC World 2019 (12-14 maart, Parijs, Frankrijk).
RTM-persen en adaptieve injectie
Fill heeft meerdere RTM-persen geleverd, waaronder HP-RTM-persen aan SGL Composites.
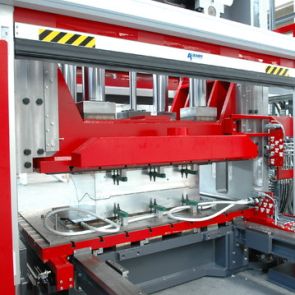
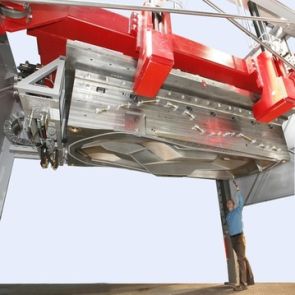
Vulling heeft geleverd een breed scala aan persen voor composietproductie, van HP-RTM-persen tot SGL Composites (rechts).
BRON:Vul Gesellschaft
Met Airbus Operations (Stade, Duitsland) en het Institute of Plastics Processing (IKV) van de RWTH Aachen University heeft Fill een innovatieve adaptieve injectie-eenheid voor RTM ontwikkeld, in eerste instantie voor aerocomposietconstructies. Voordat onderdelen die met RTM zijn gemaakt in een vliegtuig kunnen vliegen, moeten ze een tijdrovend en kostbaar kwaliteitsborgingsproces (QA) doorlopen. Om dit proces te verkorten, zijn RTM-vormgereedschappen uitgerust met sensoren, waardoor de QA tijdens de productie inline kan worden ingezet. IKV, Airbus en Fill hebben deze sensoren nu geïntegreerd in het injectiesysteem, waardoor het niet meer nodig is om elk vormgereedschap uit te rusten. Door wegwerppatronen te gebruiken op dezelfde manier waarop zuigerinjectiesystemen worden gebruikt in typische RTM-systemen, is de adaptieve injectie-eenheid uitgerust met een sensorbox waarmee de volgende gegevens ter plaatse kunnen worden gemeten en geregistreerd:
- Temperatuur
- Druk
- Harsviscositeit
- Crosslink-dichtheid van het harssysteem
- Glasovergangstemperatuur (Tg).
Naast het waarborgen van de kwaliteit van de gegoten onderdelen, kunnen deze gegevens ook worden gebruikt om het injectieproces te beheren en te controleren. Dit adaptieve injectiesysteem van Industry 4.0 wordt ontwikkeld voor aerocomposieten en wordt ook uitgebreid naar andere industrieën, zoals de auto-industrie.
Warmdoekvorming
In de recente tourartikelen die Sara Black en ik schreven over hoogwaardige composieten in Israël, merkten we op dat de meeste bedrijven hot drape-forming gebruikten. Bij Elbit Cyclone verklaarde onze gids Jonathan Hulaty zelfs:"Ik weet niet hoe je dit soort prepreg-onderdelen met hoge snelheid kunt produceren zonder hot drape-vorming", verwijzend naar balken en rongen voor Boeing 787-assemblages. Hot drape vormers (HDF) worden ook als onmisbaar gezien door FBM en Israel Aerospace Industries. Fill levert al jaren HDF-systemen, waaronder meerdere units in productie bij FACC. Het zijn in feite vacuümvormende systemen, uitgerust met infrarood- of andere soorten verwarmingselementen en een herbruikbaar siliconenrubbermembraan om prepreg-lay-ups op hun gereedschap te verwarmen en te comprimeren voordat ze worden uitgehard. HDF wordt een belangrijk onderdeel in de hieronder getoonde complete productielijn voor aerocomposieten.
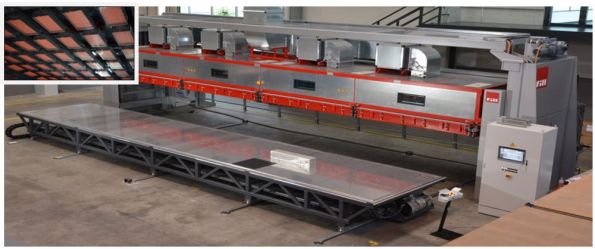
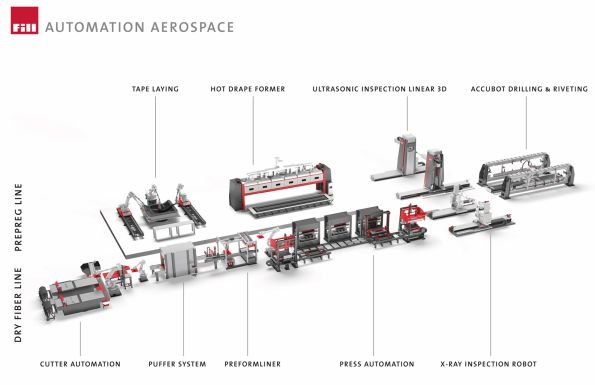
Warmdoekvorming is een belangrijke factor geworden voor de productie van grote volumes van prepreg composiet aerostructuren en wordt door Fill geautomatiseerd als onderdeel van zijn volledige procesketenoplossingen. BRON: Fill Gesellschaft
Industrie 4.0-productiecellen voor CFRP
Eind 2013 begon Fill in samenwerking met de Tier-leverancier met de ontwikkeling van een productiesysteem voor het vervaardigen van CFRP-stringers, die worden gebruikt voor het verstijven van Airbus A320-landingsklepschalen. Na installatie heeft dit systeem met succes het aantal stations verminderd, de productiestroom verbeterd en ook de gebruiksvriendelijkheid verbeterd. Het omvat:
- Automatische opslag van vormgereedschap
- HDF-zender
- Druk-draai-hefstation waar laminaten worden verwerkt tot stringers.
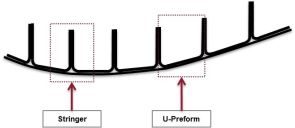
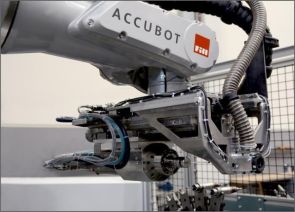
Fill is ontwikkeld drie generaties geautomatiseerde productiecellen (rechts) voor landingsgestel flapstringers gemaakt van prepreg (links).
BRON: Fill Gesellschaft
Een systeem van de tweede generatie om hetzelfde type onderdelen te produceren, werd in 2017 in gebruik genomen. Waar het eerste systeem zich richtte op het optimaliseren van individuele stations, was dit latere systeem gericht op het minimaliseren van handmatige taken en het integreren van alle gereedschapslogistiek. Drie belangrijke ontwikkelingsgebieden zorgen ervoor dat dit systeem van de tweede generatie een hoge reproduceerbaarheid en een aanzienlijk verhoogde productiviteit kan bereiken:
- Het handmatig ophalen en opslaan van vormgereedschappen wordt vervangen door een volautomatische gereedschapsretour, waardoor de logistieke procestijden worden verkort. Dit heeft ook de benodigde ruimte met meer dan 50 procent verminderd.
- Verdere automatisering van subprocessen heeft de onproductieve tijd verminderd.
- Industrie 4.0 digitalisering van alle opnames en rapportages. Door Fill ontwikkelde software maakt het mogelijk om het proces te allen tijde te visualiseren en de geschiedenis van elk onderdeel in de hele procesketen vast te leggen. Sensoren detecteren de beschikbaarheid van gereedschappen en materialen om knelpunten te voorkomen en het nabestellen te verbeteren.
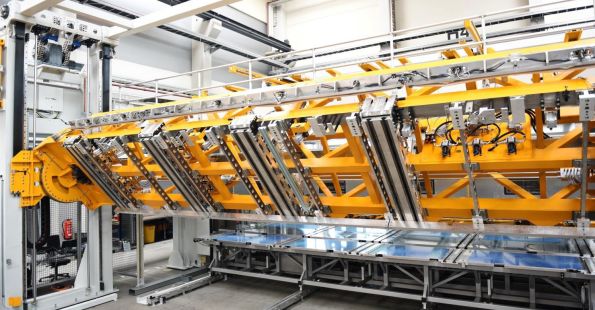
Druk-draaien -hefstation gebruikt in geautomatiseerde productiecellen voor A320 en A350 landingsgestel flapstringers.
BRON: Fill Gesellschaft
Fill werkt nu aan een derde generatie productiesysteem voor landingskleppen bedoeld voor de Airbus A350-900. Het omvat ook een gereedschapsopslag, een membraanvormend (HDF)-station, een pers-draai-hefstation en een automatische gereedschapsretour, maar is verbeterd met een transportsysteem voor autoclaafgereedschap, ter vervanging van eerdere handmatige transportvrachtwagens en elektrische tractoren door automatisch geleide voertuigen (AGV's). ). Fill werkt al aan toekomstige systemen en bekijkt hoe de samenwerking tussen mens en machine verder kan worden verbeterd.
Accubot
Zelfs voordat de composietenindustrie hun verwachte toekomstige behoefte aan een multi-operatieve werkcel begon te verwoorden, ontwikkelde Fill al de eerste prototypes, wat het Accubot noemt. Het idee was om een nauwkeurige robot te ontwikkelen met een lasertracker voor zowel ruimtelijke compensatie als directe externe meetsystemen. Deze robot zou in staat zijn om functies uit te schakelen met eindeffectors, waardoor hij niet alleen een cel voor niet-destructief onderzoek (NDT) wordt, maar ook een bewerkingscel. Accubot-toepassingen omvatten:
- Boren
- Blijvend
- NDT – Echografie met een squirter
- NDT – Röntgenfoto
- NDT – Computertomografie
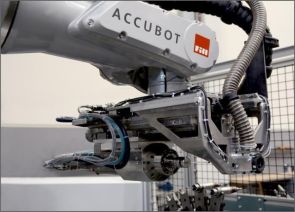
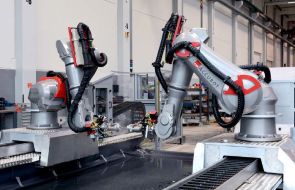
Accubot voor boren (links) en NDT met ultrasone scan met hoge snelheid (rechts).
BRON:Fill Gesellschaft.
FlexHyJoin
Fill is lid van het door de EU gefinancierde project Flexible Production Cell for Hybrid Joining (FlexHyJoin). Dit 3-jarige programma is gericht op het ontwikkelen van een volledig geautomatiseerd proefproces voor het verbinden van metalen beugels/fittingen met thermoplastische composieten in automobieltoepassingen door laserverbindings- en inductieverbindingstechnologieën te combineren. Fill ontwierp en bouwde de geautomatiseerde cel inclusief software en integratie van de verschillende technologieën.
Het onderzoek en de ontwikkeling van Fill gaan door. Het begrijpt dat innovatieve en intelligente productiesystemen nodig zijn om de fabricage van composietonderdelen zuiniger en geschikter te maken voor grotere volumes. En het zet zich in om deze systemen te ontwikkelen volgens de schaal en specifieke behoeften van zijn klanten.
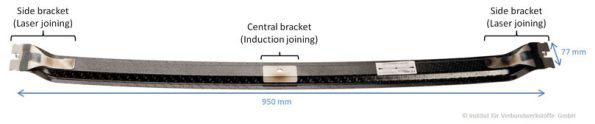
BRON:FlexHyJoin.
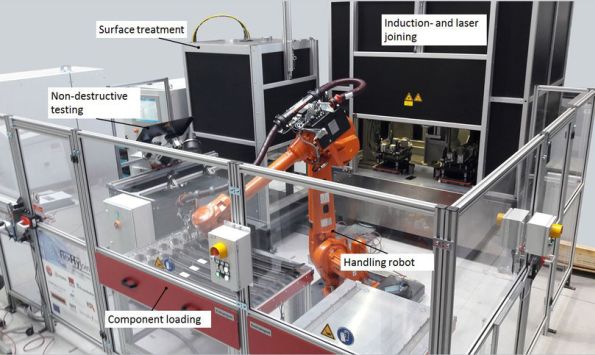
Hars
- Vuldam
- C# Preprocessor-richtlijnen
- Python strftime()
- Python strptime()
- Je sterkste onderdelen met 3D-printen van koolstofvezel – Isotropische vulling, deel 1
- High Strength 3D Printing – Isotropic Fill Part 2
- Inleiding tot harmonischen:deel 1
- Duurzaamheid in productie - deel 3
- Draaien is optioneel
- In-line, geautomatiseerde CT-scangegevensinspectie van elektronische connectoren
- Cilindriciteit in GD&T