HP-RTM voor serieproductie van kosteneffectieve CFRP-luchtstructuren
Toen harstransfergieten (RTM) ongeveer tien jaar geleden begon over te stappen op hogedruk-RTM (HP-RTM), werd het vooral geprezen voor autotoepassingen, waardoor de cyclustijden van composietonderdelen werden teruggebracht van uren tot minder dan 2 minuten. Er is minder gezegd over het toepassen van deze technologie op lucht- en ruimtevaartonderdelen. De vliegtuigindustrie heeft een lange geschiedenis met conventionele RTM, waaronder het gebruik ervan om duizenden ventilatorbladen van koolstofvezelversterkte kunststof (CFRP) en omhulsels voor commerciële vliegtuigmotoren te produceren. Airbus heeft zelfs een prototype gemaakt van een 7 meter lange, uit één stuk samengestelde multispar-flap voor de Airbus A320 met behulp van RTM. Maar is het mogelijk om deze ervaring met urenlange processen in enkele minuten om te zetten in volledig geautomatiseerd gieten van composiet vliegtuigonderdelen? Verschillende hoofdrolspelers zeggen dat het mogelijk is.
Traditionele RTM, hier voor de duidelijkheid LP-RTM genoemd, gebruikt doorgaans injectiedrukken van 10-20 bar. HP-RTM daarentegen gebruikt injectiedrukken van 30-120 bar.
"We begonnen tien jaar geleden te werken met RTM-verwerking in de ruimtevaart via een door de EU gefinancierd project om rompframes te vervaardigen", zegt Bernhard Rittenschober, hoofd onderzoek en ontwikkeling bij Alpex Technologies (Mils, Oostenrijk), een leverancier van innovatieve gereedschapssystemen voor serieel composiet productie van onderdelen. "Destijds was de voorspelling dat veel onderdelen voor de [Airbus] A350 met RTM zouden worden gemaakt, maar dat is niet uitgekomen." Alpex bleef echter aan de technologie werken en begon als leverancier aan zowel de auto- als de lucht- en ruimtevaartindustrie te kijken hoe de processen die in deze twee industrieën worden gebruikt, konden worden samengevoegd. "Het idee was om de [Hexcel] RTM6 epoxyhars te gebruiken die gekwalificeerd is in de lucht- en ruimtevaart, maar met best practices voor autogereedschap en een geautomatiseerd injectiesysteem voor een kortere cyclustijd", legt Rittenschober uit.
Het resultaat was een onderzoeksprogramma van 2013-2015 genaamd TAKE OFF, gefinancierd door de Oostenrijkse overheid, waaraan Alpex heeft deelgenomen met partners Airbus Helicopters (faciliteit in Donauworth, Duitsland), apparatuurleverancier KraussMaffei (München, Duitsland), testspecialist Aerospace en Advanced Composites (AAC, Wiener Neustadt, Oostenrijk) en harsleverancier Hexcel (Stamford, Conn., VS). Het programma toonde aan dat HP-RTM resulteerde in een kostenbesparing van 30 procent voor een A350-deurkozijn en een aanzienlijke technologische ontwikkeling, waaronder het gebruik van een tweecomponenten (2K) harssysteem, intelligente bewaking van injectie en uitharding via in-mold sensoren en de mogelijkheid om de deelcyclustijd verder te verminderen. Alpex is doorontwikkeld en ziet mogelijkheden voor deze HP-RTM-technologie om de huidige problemen met de productie van CFRP te helpen oplossen.
Het Composites Technology Center (CTC), een dochteronderneming van Airbus Operations GmbH, ondersteunt deze visie en ontwikkelt ook al tien jaar geautomatiseerde RTM, eerst met LP-RTM en vervolgens ongeveer vijf jaar geleden overgestapt op HP-RTM. (CompositesWorld merkte CTC's KraussMaffei HP-RTM-machine en ontwikkelingswerk op tijdens een rondleiding door zijn faciliteit in 2016.) "HP-RTM lost het knelpunt van injectie en uitharding op vanwege de hoge snelheidsmenging, waardoor zeer reactieve harsen kunnen worden gebruikt", legt Jan Schiller uit, CTC projectleider voor productiesystemen en lead contact voor RTM-technologieën. "We hebben een proces ontwikkeld dat enigszins complexe geometrieonderdelen van 1-2 meter produceert die voldoen aan de ruimtevaartvereisten (bijvoorbeeld 60 procent vezelvolume en minder dan 2 procent lege ruimte) in een cyclustijd van 20 minuten." Hij voegt eraan toe dat na bezoeken en discussies met Airbus-leveranciers vorig jaar een aantal onderdelen werden geïdentificeerd voor de overgang naar HP-RTM, waardoor een hogere productiesnelheid voor het A320-vliegtuig mogelijk werd. "We ontwikkelen hier nu specifieke bewerkingen voor en werken dit jaar eraan om ze in serieproductie te krijgen."
HP-RTM A350 deurkozijn
De ontwikkeling van Alpex werd voltooid via het Oostenrijkse TAKE OFF-programma via een project genaamd SPARTA. "Airbus Helicopters kozen de rol", herinnert Rittenschober zich. “Dit deurframe is wat je ziet als je een A350 binnenloopt met de deur open. Het is ongeveer 2 meter hoog, 200-250 millimeter breed en 8-10 millimeter dik, met een complexe vorm en ontwerpkenmerken om te voldoen aan de verschillende vereisten van de geassembleerde deur, die de primaire structuur is.” De A350-deur bestaat uit 14 onderdelen die zijn gemaakt door Airbus Helicopters in Donauworth, Duitsland, met behulp van LP-RTM. Het gekozen frame voor SPARTA is een van de meer uitdagende onderdelen van de deur. "Het is een goed demonstratieonderdeel omdat we HP-RTM rechtstreeks kunnen vergelijken met de standaard LP-RTM voor de ruimtevaart", voegt Rittenschober toe.
Alpex ontwierp en bouwde de LP-RTM-tooling die momenteel wordt gebruikt voor de productie van A350-deurkozijnen bij Airbus Helicopters. Voor het ontwerp en de bouw van de HP-RTM-tooling, het zou een meer autogerichte mentaliteit toepassen. "Ons doel was om automatisering van het autotype in de productie van composietonderdelen voor de luchtvaart mogelijk te maken", zegt Rittenschober. “Dat is nodig als Airbus een toekomstige A320 gaat bouwen met meer composiet onderdelen en met een snelheid van 60 tot 100 vliegtuigen per maand.”
Hij vervolgt:"We kwamen van het produceren van matrijzen voor BMW, dat actief probeerde zijn onderdelen en processen te vereenvoudigen om de cyclustijd te verkorten, terwijl Airbus voortkwam uit de eerdere complexiteit van de ruimtevaart. Toen we begonnen, vroeg Airbus Helicopters bijvoorbeeld hoeveel onderdelen deze mal zal hebben.” Let op:de huidige LP-RTM-deurproductie omvatte complexe meerdelige gereedschappen. "We hebben uitgelegd dat de HP-RTM-tool slechts één bovenste en één onderste mal heeft", zegt Rittenschober.
Alpex begon dus met een eenvoudig matrijsontwerp en voegde vervolgens functies toe om de verwerking robuuster en flexibeler te maken, bijvoorbeeld afdichtingssystemen die worden gebruikt voor grootschalige autoproductie. "Bovendien hebben we alle sensoren in de mal geïntegreerd", merkt hij op.
Voorvormen en proces
De preforms die momenteel worden gebruikt voor het A350-deurkozijn, maken gebruik van geweven materiaal en vereisen meerdere debulking-stappen, wat resulteert in een productiecyclus van drie dagen. "We hebben ervoor gekozen om in plaats daarvan krimpvrije stof (NCF) te gebruiken", zegt Rittenschober. “Dit verlaagt de prijs en de cyclustijd aanzienlijk. We hebben uiteindelijk ook sommige onderdelen gedemonstreerd met de Hexcel-gekwalificeerde geweven preforms, maar we zien een omslag in de composietenindustrie buiten de lucht- en ruimtevaart, met ontwikkeling door SGL en anderen weg van geweven stoffen en naar tapes en goedkopere vormen zoals NCF's.
Gevraagd naar injectiepunten en eventuele problemen met het wassen van vezels, legt Rittenschober uit dat de HP-RTM-tool slechts één injectiepunt heeft, maar dat er geen vezels worden gewassen omdat de voorvorm is vastgeklemd, zodat deze in de mal wordt gefixeerd en zeer stabiel is.
Een ander belangrijk punt is dat Alpex ervoor heeft gekozen om een tweecomponenten (2K) harssysteem te gebruiken in plaats van de ééncomponent RTM6 die momenteel door Airbus Helicopters wordt gebruikt. Rittenschober beweert dat het 2K-systeem reactiever kan zijn, wat beter past bij HP-RTM, en kosten kan besparen omdat het niet voorgemengd is en er geen transport van gevaarlijke stoffen nodig is. Wel is een hogere temperatuur van 180°C nodig. “Dit was voor ons het meest uitdagende onderdeel”, zegt Rittenschober, “omdat we meer gewend waren aan verwerking bij 120°C.”
KraussMaffei installeerde in zijn lichtgewicht technologiecentrum in München, Duitsland, de afgewerkte gereedschappen in zijn RimStar Compact HP-RTM-systeem met geautomatiseerde hogedrukmix (tot 80 bar/1100 psi), meter en injectie. Het maakte toen 20 demonstratieonderdelen. Rittenschober beschrijft het basislijnproces:injecteren bij 80 °C, opvoeren tot 120 °C, één uur vasthouden, opvoeren tot 180 ° en 90 minuten vasthouden, uitlopen (2 °C/min) en uit de vorm halen. "De injectie duurt slechts 20 seconden", zegt hij, "maar de totale vormcyclus duurt ongeveer vier uur."
Cyclustijd en kosten
De nog steeds langdurige uithardingscyclus voor het SPARTA-deurkozijn wordt aangedreven door de Hexcel RTM6-harsformulering en -verwerking die Airbus-gekwalificeerd is. "We waren in staat om uithardingscycli van 30 minuten bij 180 °C te bereiken met een extra naharding onder vacuüm daarna om thermische spanning te verwijderen en mechanische eigenschappen te garanderen", merkt Rittenschober op, eraan toevoegend dat de eigenschappen redelijk goed waren en vergelijkbaar met de LP -RTM-gedeelte.
"We hebben laten zien dat je het proces kunt gebruiken en de productie kunt automatiseren voor grotere onderdelenvolumes", zegt Rittenschober. "Je kunt in de mal injecteren en uitharden en vervolgens uit de pers uitharden." Hij geeft toe dat hiervoor extra gereedschapssets nodig zijn, maar slechts één pers- en injectie-eenheid. "Met dit systeem kun je de onderdeelkosten met € 700 verlagen, waardoor je de apparatuur gemakkelijk kunt betalen met een productiesnelheid van 500 tot 1.000 onderdelen / jaar, wat niet eens een heel hoog volume is."
CTC-procesontwikkeling en demonstrators
Afgezien van gereedschap en proces, omvatte het HP-RTM-deurproject ook innovatief gebruik van vezelformaat. "We begonnen met geweven textiel dat al door Airbus was gekwalificeerd en waren zeer succesvol", herinnert Schiller zich. “Vervolgens gingen we verder met NCF en meer innovatief textiel.” De laatste omvatte de plaatsing van droge vezels en het doorbladeren van gespreide sleeplagen voor verhoogde taaiheid, maar de laatste gaf problemen met een strakke pakking van vezels en lagen, wat een slechte permeabiliteit veroorzaakte en de infiltratie van hars belemmerde. "Er zijn ook ontwikkelingen om dit aan te pakken, zoals NCF met speciale vezels om de doorlaatbaarheid te verbeteren", voegt hij eraan toe.
Met betrekking tot de drukken voor HP-RTM benadrukt Schiller dat de beslissing om het proces te gebruiken meer werd gedreven door mengtechnologie uit de polyurethaanindustrie dan door hoge procesdrukken. "We gebruiken HP-RTM alleen om een goede menging van zeer reactieve harsen te krijgen", legt hij uit. “Er kan wat hogere druk in de matrijs zijn, maar dit is een secundair effect van snelle injectie. Voor auto-onderdelen met een cyclustijd van 2 minuten moeten ze veel sneller dan wij de droge voorvorm met hars infiltreren. Onze uithardingstijd van 15 minuten zorgt voor meer tijd voor harsinfiltratie, wat ook de druk in de mal verlaagt.”
Het tonnage van de pers is ondertussen afhankelijk van de grootte van het onderdeel. "Het maken van onderdelen tot 2 meter groot werkt goed (ongeveer 1.500 ton), maar voor onderdelen van 4-6 meter moet de businesscase worden berekend omdat de investering in de pers erg hoog wordt", zegt Schiller. CTC toonde een CFRP-rib van 1,5 meter bij 0,5 meter die elke mogelijke primaire lucht- en ruimtevaartstructuur voorstelt bij JEC World in 2018. Het zal eind 2019 ook een pers met een hoger tonnage ontvangen.
2K-harsen en op sensoren gebaseerde QA
Schiller merkt op dat alle eerdere RTM-vliegtuigconstructies alleen 1K-systemen hebben gebruikt die zijn gemengd door de leverancier, die vervolgens het mengsel certificeert en de verantwoordelijkheid draagt om ervoor te zorgen dat de hars voldoet aan de kwalificatie-eisen. "Nu overwegen we 2K-systemen, maar de uitdaging is om de mengkwaliteit te waarborgen", legt hij uit. Voorgemengde 1K-systemen vereisen koude verzending en opslag om reactie tot onderdeelverwerking te voorkomen. De voordelen van 2K-systemen omvatten dus de eliminatie van deze kosten en een hogere reactiviteit voor een snellere verwerking. Een probleem is echter dat de kwaliteitsborging (QA) wordt overgedragen van de harsleverancier naar de fabrikant van de onderdelen. “Deze QA vereist detectie van de mengverhouding en de gemengde harskwaliteit. Beide zijn nodig voor Airbus-kwalificatie van een nieuw materiaal. Dit betekent dus metingen van de twee componenten net voor het mengen en van de hars na het mengen. Tegenwoordig hebben we alleen sensoren voor de mixkop, die laten zien hoeveel hars en hoeveel verharder er in de mix wordt gedoseerd. Dit is niet genoeg voor kwalificatie.”
Alpex werkt ondertussen aan de ontwikkeling van een inline kwaliteitssysteem om de verificatie van 100% goed gemengde hars te bieden die Airbus vereist. "Vanaf het begin van deze ontwikkeling hebben we met Netzsch in-mold-sensoren gewerkt", merkt Rittenschober op. “Nu Netzsch samenwerkt met Kistler (Winterthur, Zwitserland), is er nieuwe technologie beschikbaar. We kunnen temperatuur, druk en de uitharding van de hars volgen met één enkele sensor, die we in de mal plaatsen.”
"Alpex zegt in-mold-sensoren te gebruiken, en de leveranciers van mix-/injectieapparatuur zeggen dat de sensoren in hun moeten zitten. systemen”, zegt Schiller. "Beiden hebben gelijk." Maar ook in dat laatste stelt hij vast dat er verbetering nodig is. "In automotive HP-RTM wordt de harsmengverhouding gemeten over het volledige proces, dus het is een gemiddelde", legt Schiller uit. “Ik heb deze meting echter op elk afzonderlijk punt tijdens het proces nodig, zodat ik weet dat de mengverhouding altijd klopt, zelfs voor de laatste halve seconde tijdens het injecteren. We hebben een betere tijdresolutie nodig in de meetsystemen.” Schiller suggereert dat sensoren waarschijnlijk nodig zijn vóór de mixkop, in de mixkop en in de mal. “We werken aan deze QA-ontwikkeling parallel aan de evaluatie van 2K-harsen in ruimtevaarttoepassingen, en samen met de machineleveranciers hebben we sensorsystemen geïdentificeerd die voldoende resolutie beloven. Ze zullen dit jaar worden gevalideerd.”
Alpex test ook een nieuwe hybride multifunctionele piëzo-elektrische sensor die is ontwikkeld door Aerospace &Advanced Composites (AAC, Wiener Neustadt, Oostenrijk). Geplaatst op de RTM-matrijs, het fungeert als een druksensor om het harsstroomfront in de mal te bewaken. Zodra de voorvorm door de hars is geïmpregneerd en het uitharden begint, wordt de verandering in het impedantiespectrum door de sensor gebruikt om de mate van uitharding te bepalen. Zodra de uitharding is voltooid, worden de piëzo-elektrische sensoren samen uitgehard op het oppervlak van het onderdeel dat wordt gebruikt voor structurele gezondheidsmonitoring, hetzij in passieve modus als akoestische emissiesensoren of in actieve modus met behulp van geleide ultrasone golven. Ze zijn aangetoond voor het bewaken van impact en schade aan afgewerkte onderdelen.
Merk op dat deze procesgegevens kunnen worden geanalyseerd door Industrie 4.0 intelligente productiesystemen om routes te identificeren voor verdere verbeteringen in kwaliteit en efficiëntie. Deze procesgegevens kunnen ook worden gelogd voor de digitale tweeling van elk onderdeel.
Toekomstig potentieel
Rittenschober zegt dat de enige echte hindernis voor de HP-RTM-technologie certificering is:"We demonstreren met Airbus Helicopters dat dit proces kan werken, maar iemand moet het certificeren." Schiller is het ermee eens dat het altijd een horde is om te bepalen wie de eerste zal zijn, maar hij heeft het afgelopen jaar ook voor veel onderdelen businesscases berekend. “Voor 200 onderdelen per jaar is het niet logisch. Voor onderdelen op bijvoorbeeld de A320 wordt het echter aantrekkelijk. Elke maand zien we een hoger streefpercentage voor het A320-programma. Veel van deze onderdelen zijn ontworpen in de jaren 80 en worden handmatig geproduceerd, dus ze zouden gemakkelijk veel efficiënter kunnen worden gemaakt met HP-RTM.”
Met CTC-aangetoonde deelcyclustijden van 20 minuten, zou HP-RTM ook aantrekkelijk kunnen zijn voor de markt voor elektrische verticale start- en landingsvliegtuigen (eVTOL), waar productievolumes van 5.000 vliegtuigen per jaar door de fabrikant van luchttaxi's als een bovengrens zijn voorgesteld UBER.
Alpex zal doorgaan met het ontwikkelen van een reeks RTM-verbeteringen, zegt Rittenschober. "Wij geloven dat HP-RTM echt potentieel heeft om een aantal van de problemen op te lossen met een meer kosteneffectieve, geïndustrialiseerde productie van CFRP-aerostructuren." Schiller is het daarmee eens en merkt op dat er voor veel van de beoogde A320-toepassingen talloze CFRP-onderdelen per scheepsset zijn. “Zo begint het voordeel van een efficiënter proces zich op te stapelen. Als we de eerste toepassing in productie kunnen krijgen, zullen er andere komen.”
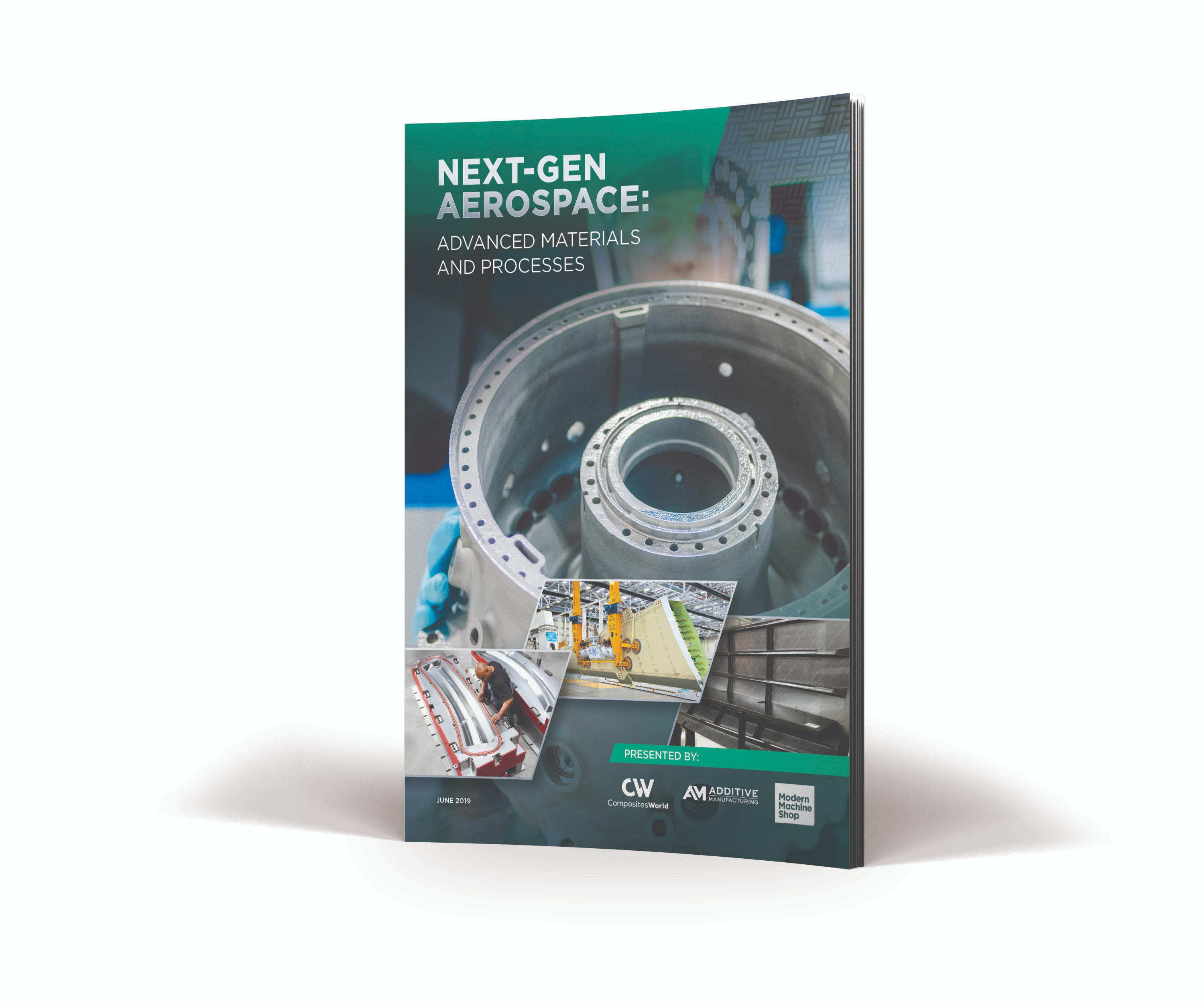
De volgende generatie van
Lucht- en ruimtevaartindustrie
Aangezien de commerciële luchtvaartindustrie naar verwachting in de komende 20 jaar zal verdubbelen, zijn nieuwe technologieën en ongekende productiesnelheden nodig om aan de vraag naar passagiers- en vrachtvliegtuigen te voldoen.
Leer meer over de materialen en processen die de volgende generatie vliegtuigen zullen vormen in een verzameling verhalen van CompositesWorld, Modern Machine Shop en Additieve productie , beschikbaar om gratis te lezen of te downloaden . Download het hier.
Hars
- Aditieven:kosteneffectieve kleurstoffen voor draad- en kabeltoepassingen
- Reinigingsmiddelen voor de productie van dunwandige polyolefineverpakkingen
- Fraunhofer stelt geautomatiseerde Engel-productiecellen in gebruik voor R&D van thermoplastisch composiet
- Ontwerpen voor geautomatiseerde composietproductie van aerostructuren met een klein volume
- Thermoplastische tapes blijven potentieel tonen voor composiet aerostructuren
- AFP combineren met 3D-printen voor flexibele productie van onderdelen
- Karl Mayer lanceert productielijn voor thermoplastische UD-tapes
- Fusing waterjet, laser voor efficiëntie in CFRP/CMC-bewerkingen
- Broetje-Automation vergroot AFP-portfolio voor seriële composietproductie
- INEOS Styrolution gaat productielocatie bouwen voor StyLight thermoplastisch composiet
- Traceerbaarheidspraktijken voor castingproductie