Thermoplastische primaire aerostructuren zetten weer een stap voorwaarts
Voordelige eigenschappen van thermoplastische composieten, zoals taaiheid, relatief hoge out-of-plane sterkte en duurzaamheid/recyclebaarheid, hebben het ontwerp van vliegtuigen aangetrokken. ingenieurs al tientallen jaren aan het idee van primaire structuren van thermoplastisch composiet. Maar vliegtuigen productie ingenieurs waren onzeker over het vinden van een kosteneffectieve manier om ze van CAD-simulatie naar de productievloer te brengen. Ze laten zich echter niet afschrikken:de inspanningen om de noodzakelijke productietechnologieën te ontwikkelen zijn over de hele wereld voortgezet — misschien nergens zo hardnekkig als in Nederland.
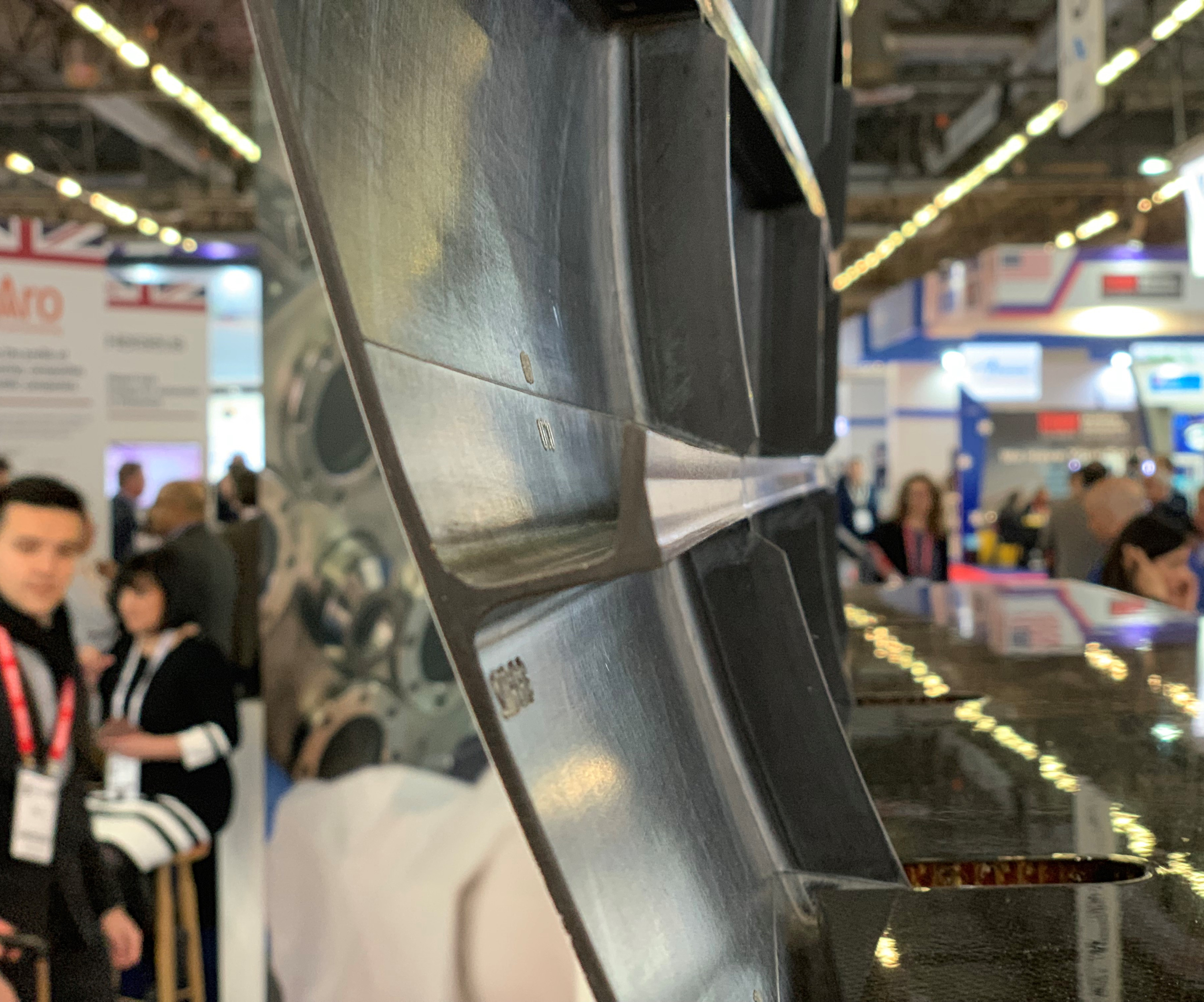
Integrale L-stringers. De GKN Fokker koolstofvezel/PEKK-romp, ontworpen en gebouwd voor Gulfstream, bevat gebogen longitudinale L-stringers met een enigszins stompe hoek om het losmaken van het gereedschap mogelijk te maken. CW foto | Jeff Sloan
In 2009 vormden negen Nederlandse industriële bedrijven en onderzoeksinstituten samen met Airbus (Toulouse, Frankrijk), het Thermoplastic Affordable Primary Aircraft Structure (TAPAS) Consortium. Het initiatief breidde zich in 2014 uit tot 12 partners en ging verder als TAPAS2. Gericht op door Airbus ontwikkelde toepassingen onder TAPAS2, heeft GKN Fokker (Hoogeveen, Nederland) onlangs een rompdemonstrator ontwikkeld met behulp van wat zij een "butt-jointed orthogrid-technologie" noemt die een kosteneffectieve productie van een thermoplastisch composiet rompontwerp mogelijk maakt.
De volledige uitbetaling van een primaire vliegtuigstructuur van thermoplastisch composiet - hoewel nog jaren weg - is nu misschien in zicht, aangezien Gulfstream Aerospace (Savannah, Ga., VS) een samenwerking aangaat met GKN Fokker om zijn TAPAS2-romptechnologie te verbeteren, en de weg wijst naar mogelijke toepassing de materialen en het proces tot een volledige romp. Het verhaal achter het nieuw ontwikkelde romppaneel (dat eerder dit jaar op JEC World werd getoond) is er een van vorderingen in ontwerp- en fabricagemethoden, en verder, in een meer grondig geïntegreerde ontwerp-fabricage-engineeringbenadering.
"Traditioneel", legt GKN Fokker-hoofdingenieur Andries Buitenhuis uit, "of ze nu stoffen of unidirectionele tapes gebruikten, ontwerpers bleven meestal bij conventionele lagen van 0-, 90- en 45-graden oriëntaties. Ze zouden werken vanuit hun ply layup-tafels, onafhankelijk van andere disciplines.” De nieuwe aanpak is een geïntegreerd, gedigitaliseerd ontwerp-productiesoftwareplatform (ontwikkeld door TAPAS) waarin ingenieurs uit verschillende disciplines allemaal naar hetzelfde digitale model kijken en de mogelijkheid hebben om complexere onderdeelontwerpen te conceptualiseren. “Dit opent een hele nieuwe wereld van ongekende optimalisatiemogelijkheden”, vervolgt Buitenhuis. "Bij complexe vormen kunnen vezelrichtingen overal zijn. We kunnen onconventionele laminaten bouwen en een frisse blik werpen op toelaatbare ontwerpen, fabricagehiaten en overlappingen, radiussen…. En je kunt de sterkte van de constructie lokaal optimaliseren.” Deze uitgebreide ontwerpopties maken vollediger gebruik van de vezelbesturingscapaciteit van AFP-machines (geautomatiseerde vezelplaatsing) en de vooruitgang in andere productiemogelijkheden die hieronder worden besproken.
De ontwerpvrijheid die dit geïntegreerde digitale systeem biedt, is onmisbaar gebleken voor het ontwerp en de fabricage van business jet-panelen. In de TAPAS2-rompontwerpen heeft het koolstofvezel/polyetherketonketon (PEKK)-paneel (gemaakt met Solvay's APC PEKK-FC) een gelaste, bevestigingsvrije frame-op-huidverbinding, die een essentiële bijdrage levert aan de kosteneffectiviteit van het ontwerp. "We voorspellen dat we kostenpariteit bereiken met aluminium rompschalen", legt Arnt Offringa uit, hoofd thermoplastische composiettechnologie bij GKN Fokker, "en dit komt omdat aluminium schalen zijn geklonken." De eliminatie van mechanische bevestigingsmiddelen zal naar verwachting leiden tot een kostenbesparing van 20% en een gewichtsvermindering van 10% in de primaire constructies van vliegtuigen in vergelijking met conventionele composietoplossingen. Natuurlijk komen veel van de kosten- en gewichtsbesparingen voort uit het wegvallen van de bevestigingsmiddelen zelf, evenals de arbeidskosten voor het installeren ervan. Ook van groot belang is het elimineren van gaten in de composietcomponenten om plaats te bieden aan de bevestigingsmiddelen - gaten die extra versteviging en dus extra gewicht vereisen.
GKN Fokker bereikte technology readiness level (TRL) 3 (proof of concept) met Airbus voor een onder druk staande romp, wat de kostengelijkheid aantoont met aluminium romppanelen, onder TAPAS2 in december 2017. Gaandeweg breidde het GKN Fokker-team zijn visie voor deze thermoplast uit. romptechnologie van commerciële vliegtuigen tot toepassingen voor zakenvliegtuigen.
De interesse van Gulfstream
GKN Fokker's historie van succesvol werk voor Gulfstream aan thermoplastische composietcomponenten, maakte een samenwerking met de business jet-fabrikant een logische volgende stap. "Het is algemeen bekend dat Gulfstream al jaren met thermoplastische composietonderdelen vliegt", zegt Mark Chapman, manager van Gulfstream's Advanced Structures and Materials Initiative (ASMI). Hij voegt eraan toe dat het romppaneelproject "een natuurlijke voortzetting is van wat we hebben gedaan, beginnend met eenvoudigere onderdelen en op weg naar primaire structurele onderdelen." GKN Fokker is een samenwerking aangegaan met Gulfstream bij de ontwikkeling van talrijke secundaire componenten van thermoplastisch composiet, waaronder staartliften en roeren, evenals vloerpanelen op de G650.
In 2015 presenteerden Offringa en Buitenhuis TAPAS2-projectontwikkelingen aan Gulfstream, en Chapman en zijn team erkenden het potentieel om de voordelen van TAPAS2-resultaten te behalen. "We zagen de potentiële voordelen van gewichtsvermindering, betere slagvastheid en taaiheid en verbeterde prestaties", herinnert Chapman zich. Ontwerp zonder bevestigingsmiddelen is ook aantrekkelijk. "Lastechnologie zou ons in staat stellen om de romp efficiënter te monteren" dan een mechanisch bevestigde assemblage, zegt Chapman.
De samenwerking met GKN Fokker ondersteunt Gulfstream's onderzoek en ontwikkeling van complexere rompvormen die economisch niet haalbaar zijn om te produceren met metalen constructies. "Je kunt tot nu toe alleen metaal rekken", merkt Chapman op. "De verbindingen en ondersteunende structuur die nodig zijn voor complexe vormen zijn niet erg efficiënt." Offringa is het daarmee eens:"Dergelijke complexe geometrieën zijn moeilijk te vervaardigen met conventionele technologieën."
Ontwerp en fabricage samenbrengen
Om een maakbaar ontwerp zonder bevestigingsmiddelen te bereiken, richt de aanpak van GKN Fokker zich op het weerstaan van de twee belangrijkste krachten waaraan de rompverbindingen onderhevig zijn:cabinedruk en schokken zoals het vallen van gereedschap. Cabinedruk plaatst radiale kracht op de romp, waardoor er hoge belastingen ontstaan in de frame-huidverbinding. In conventionele ontwerpen bevatten rompframes "muisgaten" waardoor de langsliggers passeren. Onder druk van de cabine dienen deze muisgaten als discontinuïteiten die onderhevig zijn aan hoge afpelkrachten - een grote zorg voor een ontwerp zonder bevestigingsmiddelen, gezien de lage out-of-plane sterkte van composieten in vergelijking met metalen. Schokken veroorzaken ook hoge belastingen in de verbinding tussen frame en huid, omdat het frame niet buigt onder impact.
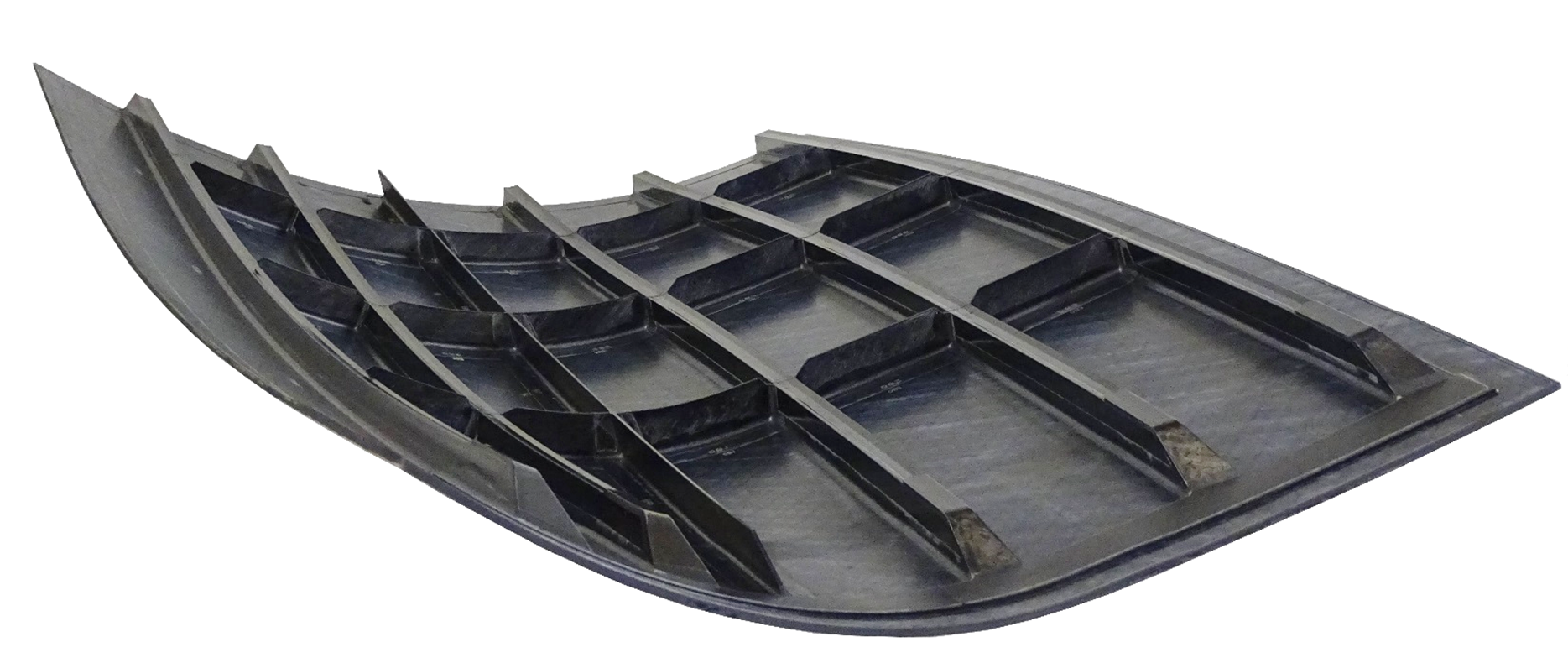
Dubbele kromming. Het thermoplastische composiet romppaneel herbergt de complexe geometrie van een Gulfstream business jet achter op de romp met vezelgestuurde AFP-lay-out van de huid en co-consolidatie van de orthogrid. Let op de omtreksmesstringers, die later aan het frame worden gelast. Bron | GKN Fokker
Het GKN Fokker/Gulfstream-team wist dat het onhaalbaar was om de uitdagingen aan te gaan die worden veroorzaakt door een complexe kromming, hetzij met metaal, hetzij met conventionele benaderingen voor ontwerp en fabricage van composieten. Buitenhuis merkt met name op:"Een complex rompontwerp zou niet mogelijk zijn zonder fiber steering." Dit vermogen van AFP-machines heeft de ontwerpers bevrijd om de vezeloriëntatie lokaal te optimaliseren op basis van de complexe vorm van de schaal, en om af te wijken van de standaard 0/45/90 vezeloriëntatie-opties. "Vezelbesturing voor vorm- en gewichtsoptimalisatie is een van de belangrijkste verbeteringen van dit project", meent Chapman.
GKN Fokker maakte de huid van het romppaneel op een ultrasone AFP-machine die het bedrijf ontwikkelde voor snelle plaatsing van thermoplastische tape. De tape is unidirectioneel, wat ook de laminaatprestaties verbetert in vergelijking met stoffen tapes.
Het nieuwe concept dat onder TAPAS en TAPAS2 is ontwikkeld en dat nu wordt toegepast in het Gulfstream-paneel, dat met succes omgaat met de hoge belastingen die worden veroorzaakt door cabinedruk en botskrachten, evenals andere prestatie-eisen, wordt beschreven als een "stompgewricht orthogonaal verstijfd". huid met gelaste frames.” Bij het uitpakken van deze beschrijving worden drie belangrijke ontwerpkenmerken en de fabricage-ontwikkelingen die nodig zijn om ze te implementeren naar voren gebracht:(1) de orthogrid, (2) de stompe verbinding en (3) lastechnologie.
Orthogrid
Aan de sterkte-eisen van het paneel wordt gedeeltelijk voldaan door volledig onderling verbonden orthogonale rasterverstijvingen. Deze orthogrid elimineert de piekbelastingen die gepaard gaan met de muizengaten, waardoor het ontwerp van punten waarop de afpelkrachten worden vergroot, wordt verwijderd. De orthogrid bestaat uit doorlopende langsliggers en frames die uit twee afzonderlijke componenten bestaan:onderbroken maar verbonden omtrekslangen en frames die daarop zijn gelast.
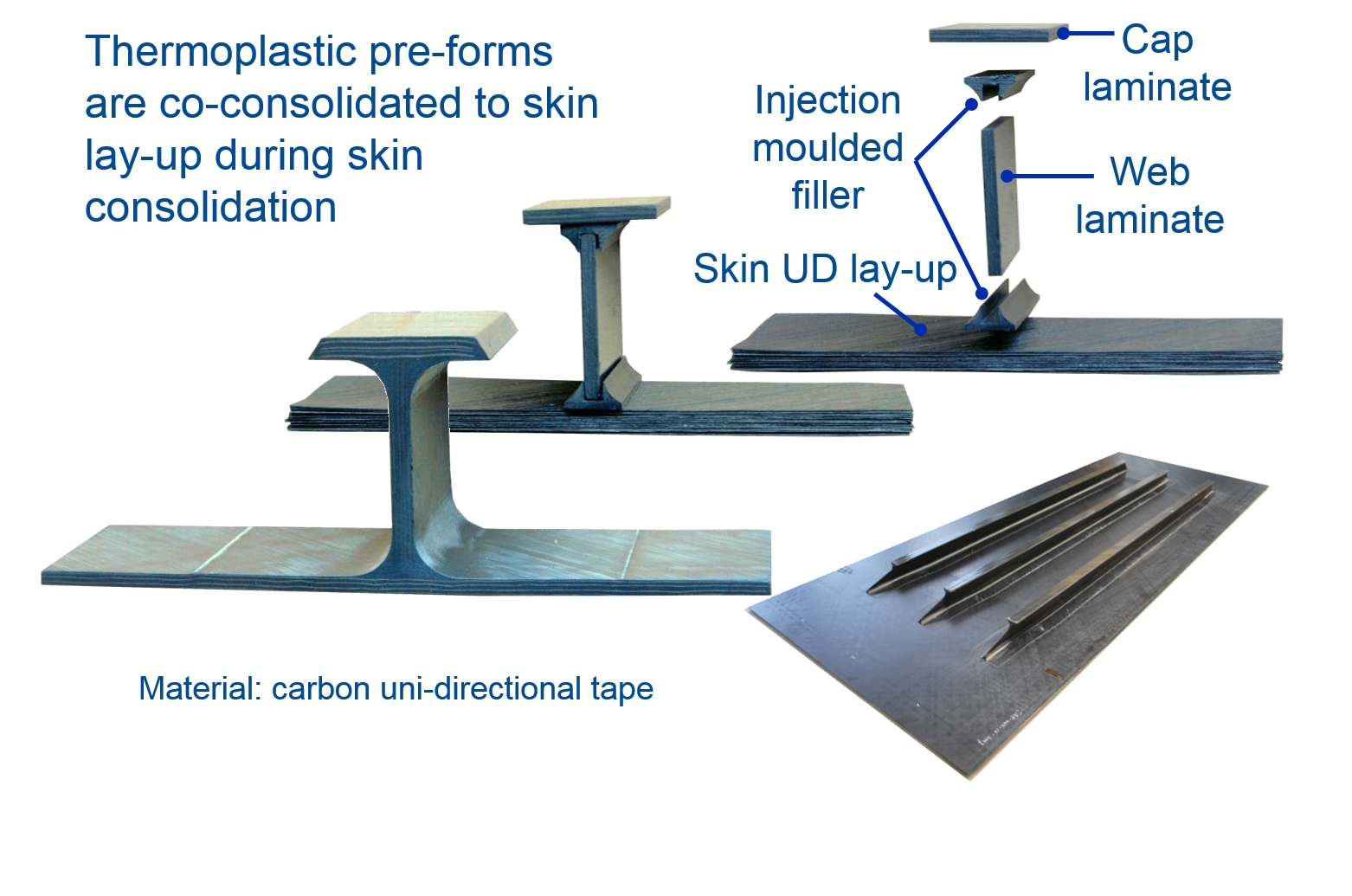
Voordelige stootvoeg. GKN Fokker innoveerde en patenteerde een stompe verbinding die orthogrid en orthogrid-op-huid verbinding mogelijk maakt met behulp van kosteneffectieve kortvezelige spuitgegoten elementen en doorlopende vezel platte laminaten voor het stringerweb en de dop (hier een T-stringer; het Gulfstream-paneel bevat L-stringers met dezelfde techniek). Bron | GKN Fokker
Dit vertegenwoordigt dus een nieuwe generatie in het ontwerp van rompverstijvers die is geëvolueerd gedurende jaren van orthogrid-ontwikkeling. Aanvankelijk gebruikte GKN Fokker T-stringers waarbij de doppen van zowel langs- als omtrekselementen doorlopend waren en elkaar op de hoeken overlapten. Bij het verbinden met het frame moest echter de omtreksdop worden verwijderd. Zo werden T-stringers L-stringers en frames werden rondlopende bladstringers met frames die vervolgens eraan werden gelast.
Een andere wijziging is vereist omdat de gebogen langsliggers die zowel in de lengte als in de omtrek worden gebruikt, het vrijgeven van het gereedschap veel uitdagender maken. Zo zijn de L-stringers ontworpen met een kap-naar-webhoek van meer dan 90 graden, zodat gereedschapsstukken altijd zijwaarts uit het stringerraster kunnen schuiven.
Kontgewrichten
GKN Fokker ontwikkelde niet alleen het orthogrid-ontwerp, maar ook een nieuwe productiebenadering voor het grid en het grid-to-skin verbindingsmechanisme. "Het kan onbetaalbaar zijn om het raster te fabriceren", merkt Offringa op, "maar ons raster is opgebouwd uit platte laminaten en eenvoudige spuitgegoten 'vulstoffen'."
Meer specifiek heeft GKN Fokker haar gepatenteerde stootvoegtechnologie toegepast op het Gulfstream-paneel (ook op de voorgaande TAPAS-panelen). Het lijf en de dop van de T- of L-stringercomponenten, evenals de blade-stringercomponenten, zijn vervaardigd uit voorvormen die met een waterstraal zijn gesneden uit een plat koolstofvezel/PEKK-laminaat. De verbindingselementen (skin to web en web to cap) zijn spuitgegoten, pi-vormige vulstof gemaakt van een kortvezelig koolstof/PEKK-materiaal. Zowel het hars- als het koolstofvezeltype komen overeen met die in de roosterelementen.
Huid en orthogrid worden samen geconsolideerd in een Invar Invar Inner Mold Line (IML) tool. Het gereedschap is voorzien van groeven waarin de orthogrid-componenten en gereedschapsblokken worden geladen. De AFP-gevormde huid wordt vervolgens op de IML geplaatst en het hele samenstel wordt in zakken gedaan en in de autoclaaf geconsolideerd.
Lassen
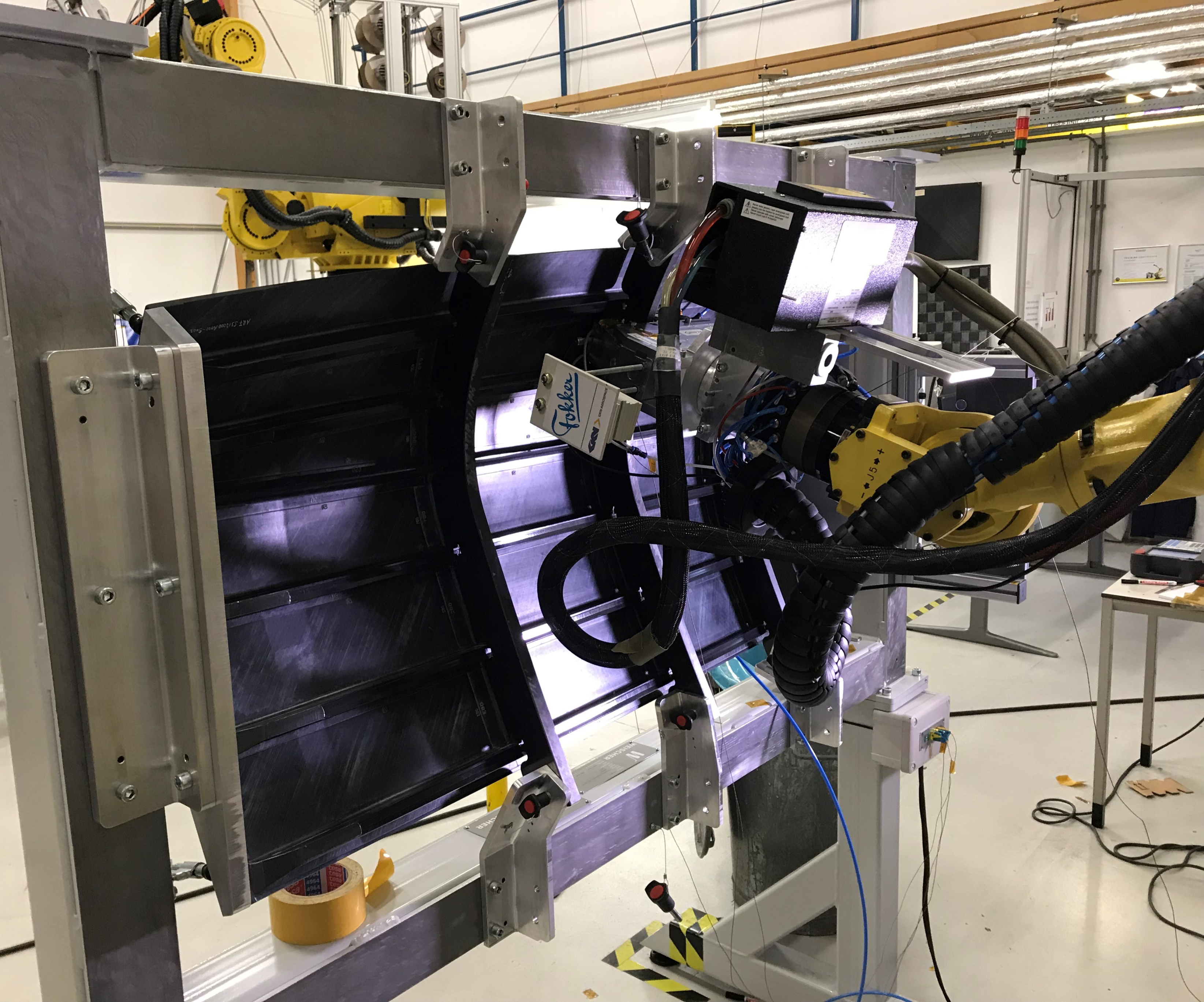
Geautomatiseerd lassen. Om bij te dragen aan de economische haalbaarheid van het thermoplastische composiet romppaneel, heeft GKN Fokker een robotlastechniek ontwikkeld en toegepast. Bron | GKN Fokker
De combinatie van het orthogrid- en stootvoegontwerp maakt een bevestigingsloze verbinding van het orthogrid en frame mogelijk door middel van lassen. Tijdens de TAPAS2-fase zijn verschillende lastechnologieën ontwikkeld door TAPAS-teamleden, waaronder inductie-, geleidings- en ultrasone lastechnologieën. Het Gulfstream-paneel maakte gebruik van geleidingslassen om het frameweb te verbinden met de omtreksbalk van het blad. Deze taak wordt uitgevoerd met de laskop gemonteerd op een robot - een andere ontwikkeling die bijdraagt aan een kosteneffectieve produceerbaarheid.
Een stap van meerdere
GKN Fokker begon in 2017 de samenwerking met Gulfstream en creëerde ontwerpconcepten voor het romppaneel. Ontwerp en fabricage van verschillende gebogen panelen volgden in 2018 en 2019, waarbij de mijlpaal van de eerste paneeldemonstrator dit jaar werd getoond op JEC World.
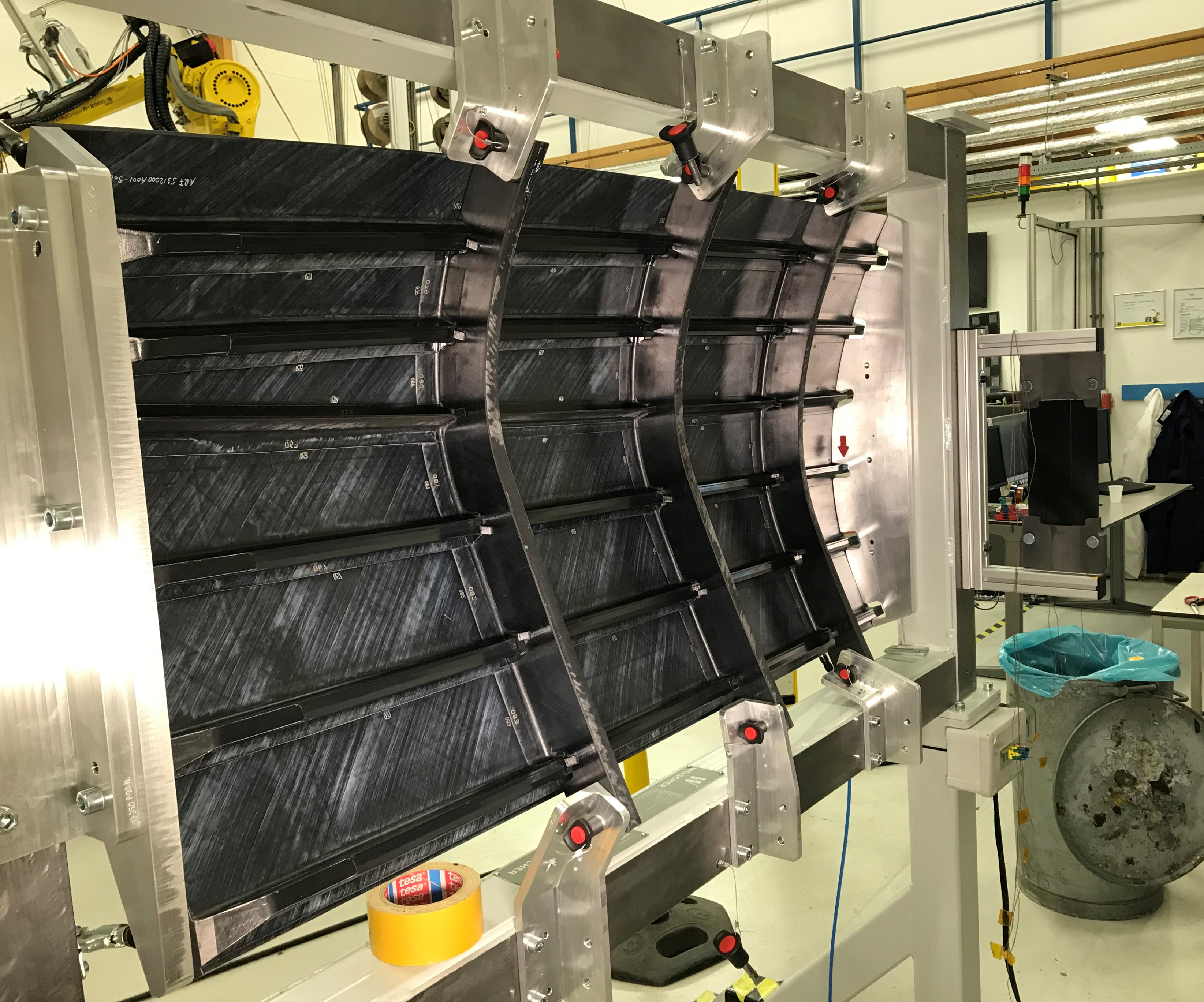
Voltooid onderdeel. Met frame-elementen die aan de omtrekslangen van het blad zijn gelast, is het Gulfstream-romppaneel klaar voor testen, beoordeling en voortdurende ontwikkeling terwijl de bedrijven werken aan de productie van thermoplastische composietrompen. Bron | GKN Fokker
GKN Fokker gaat door met het bouwen van panelen en verwacht later dit jaar TRL4 (component validatie) te behalen. "We bespreken momenteel de weg voorwaarts naar volledige volwassenheid", meldt Offringa. Chapman wijst erop dat het ontwerp van het paneel niet op een bepaald platform is gericht, en meldt dat het testen van panelen het begrip van Gulfstream van materiaaleigenschappen en prestaties zal helpen verdiepen. Met betrekking tot de bredere businesscase voor primaire structuren van thermoplastisch composiet, waaronder de prestaties, productiekosten, gebruikskosten en duurzaamheid van de jet, merkt Chapman op:"We zullen deze beter begrijpen naarmate we verder komen op de onderzoeks- en ontwikkelingsweg. Voorlopig ligt onze focus op het kosteneffectief maken van deze complexe vormen.”
Hars
- Covestro verhoogt investeringen in thermoplastische composieten
- Grafeenversterkte thermoplastische masterbatches gelanceerd
- Solvay breidt capaciteit thermoplastisch composiet uit
- Tariefbesprekingen krijgen een andere wending
- Thermoplastische composieten bij Oribi Composites:CW Trending, aflevering 4
- DLR Institute of Structures and Design vergroot de maturiteit van thermoplastische composiet rompstructuren
- Suprem breidt thermoplastische mogelijkheden uit
- Thermoplastische tapes blijven potentieel tonen voor composiet aerostructuren
- Thermoplastische composieten lassen
- Ontwerpers moeten profiteren van trends in de gegoten industrie
- Ontwerptips voor spuitgieten