Magnetisch 3D-printen, de volgende generatie op maat gemaakte composieten
Fortify (Boston, Massachusetts, VS) werd in 2016 opgericht op basis van onderzoek naar composiet 3D-printen door Josh Martin (CEO van Fortify) en Randall Erb, directeur van het DAPS Lab aan de Northeastern University in Boston. (Erb is ook mede-oprichter van zowel Boston Materials als Fortify.) Hun doel was om een snelle productie van composieten met geoptimaliseerde microstructuren mogelijk te maken. De gepatenteerde Fluxprint-technologie die ze hebben ontwikkeld, maakt gebruik van magnetische velden en digitale lichtverwerking (DLP) - maar met sterk gevulde harssystemen - om aangepaste microstructuren te produceren in 3D-geprinte composietonderdelen met hoge resolutie.
Fluxprint versus DLP
Zowel DLP als stereolithografie (SLA) worden momenteel gezien als de 3D-printtechnologieën die de hoogste complexiteit en precisie bieden. Beide zijn afhankelijk van het gebruik van licht - meestal ultraviolet (UV) - om een lichtgevoelige hars uit te harden die gewoonlijk epoxy- of acryl- en methacrylmonomeren omvat. Het licht wordt digitaal gericht om op de hars in de tank van het systeem te schijnen om de vormen of patronen voor elke laag te creëren. Het fabricageplatform wordt na elke laag verplaatst, waardoor de volgende laag kan worden afgedrukt en verder kan gaan naar een afgewerkt, stevig onderdeel.
DLP-projectoren en SLA dateren uit het begin van 3D-printen in de jaren tachtig. DLP-printers zijn meestal groter omdat ze de eigenlijke lichtprojector bevatten. De meeste SLA- en DLP-machines gebruiken thermohardende polymeren, maar EnvisionTEC maakt een printer die ook thermoplasten kan gebruiken. Beiden hebben traditioneel zuivere polymeren gebruikt zonder versterking.
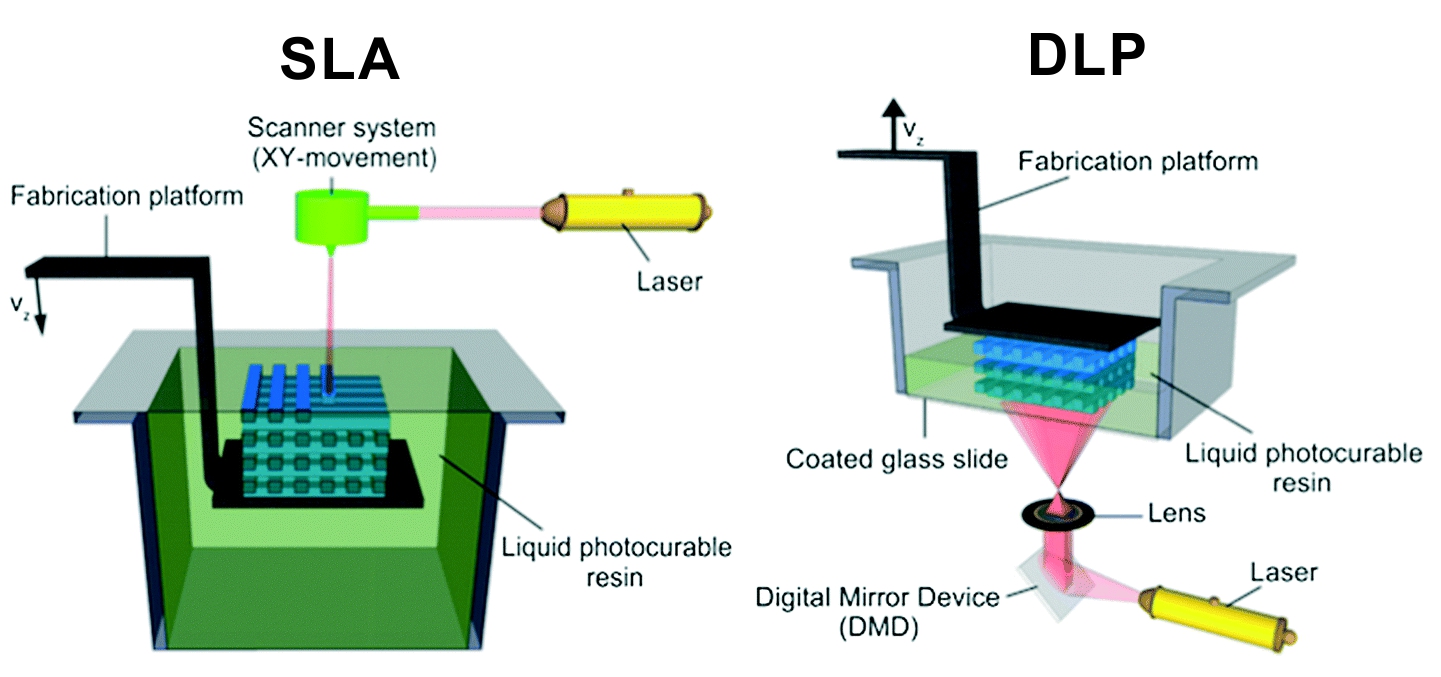
"DLP-platforms zijn in staat om voldoende productiesnelheden en kwaliteit te leveren", zegt Josh Martin, CEO van Fortify, "maar de mechanische eigenschappen zijn altijd een uitdaging geweest. Onze kernthese is dat een stapsgewijze verandering in prestatie niet alleen bereikt kan worden door polymeerchemie. Het benutten van de unieke eigenschappen van composieten in de additievenindustrie met hoge resolutie zal echter een game changer zijn.”
Hij legt uit dat Fortify gespecialiseerd is in UV-uitharding van hooggevulde technische harsen met behulp van unieke additieven en het controleren van de oriëntatie van deze eigenschapverhogende additieven in de print. Vulstoffen omvatten glas-, koolstof- en keramische vezels, evenals deeltjes. Technische harsen zijn onder meer op acrylaat en methacrylaat gebaseerd (PMMA) of op epoxy gebaseerd, op kationen gebaseerd - die volgens Martin meer conventioneel zijn voor de coatingsindustrie. Topharsfabrikanten over de hele wereld (BASF, DSM, Dupont en anderen) investeren zwaar om de eigenschappen van hun additieve materialen te verbeteren. Fortify kan de beste van deze ontwikkelingen selecteren om hun versterkende technologie toe te voegen.
Controle van de vezeloriëntatie wordt bereikt door gebruik te maken van een magnetisch veld. Terwijl Fortify 3D een onderdeel afdrukt met behulp van zijn Fluxprint-technologie, worden vezels voxel-voor-voxel magnetisch uitgelijnd om te voldoen aan de belastingsvereisten van het onderdeel. (Zie het proces in actie in de video hierboven.) Voor niet-magnetische versterkende materialen, zoals keramische en glasdeeltjes en vezels, worden gepatenteerde magnetische labelingstechnieken gebruikt om de vulstoffen te coaten op een manier die ze magnetisch responsief en compatibel maakt met de hars.
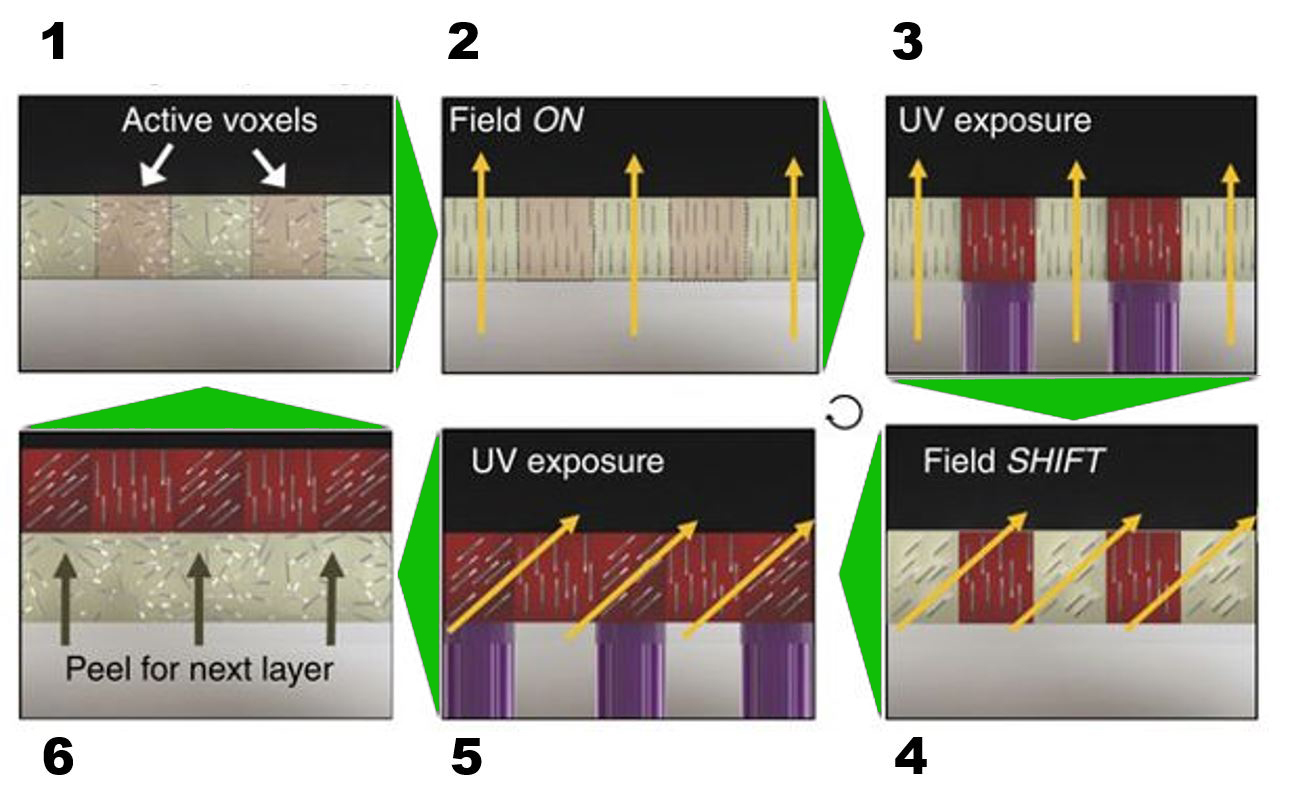
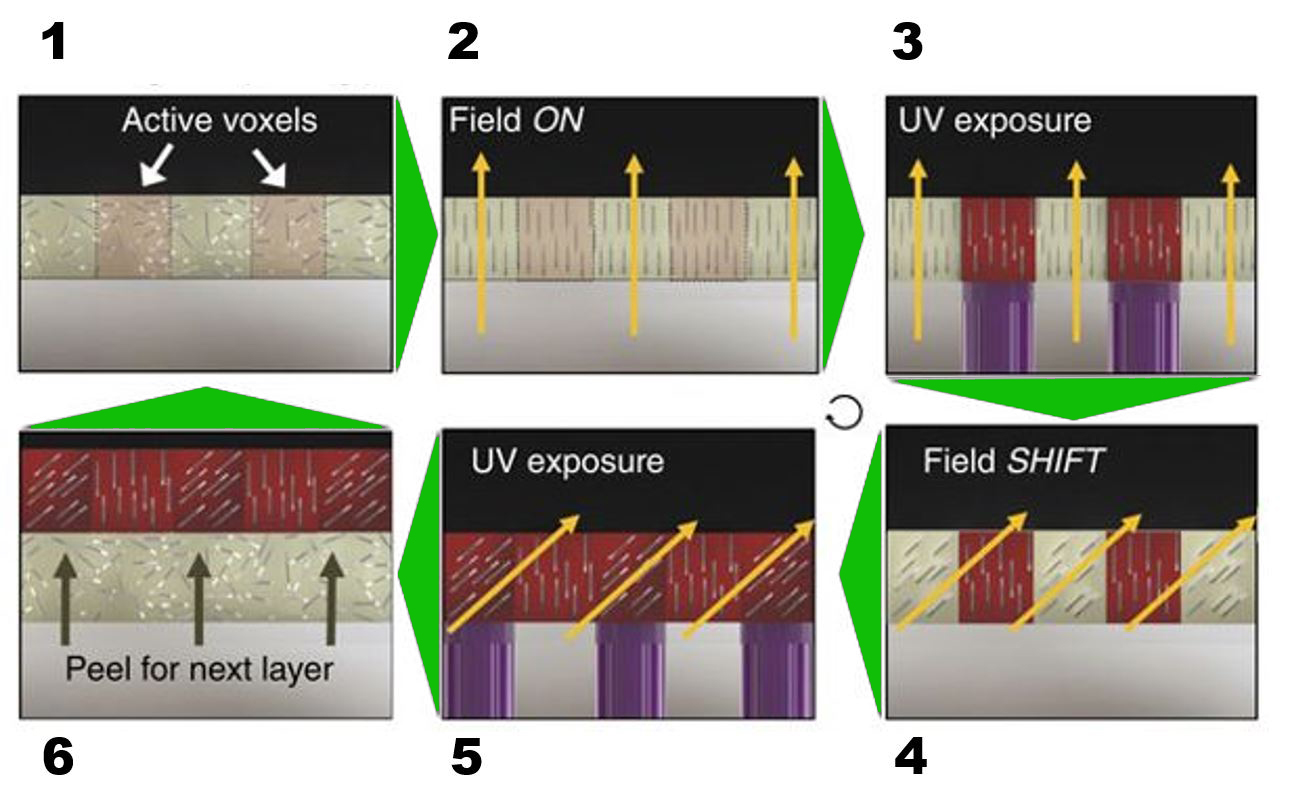
Het Fluxprint-proces wordt weergegeven in de afbeelding hierboven en als volgt beschreven:
- Een laag voedermiddel wordt aan het bouwgebied geleverd met willekeurig uitgelijnde wapening.
- Magnetisch veld wordt toegepast om de wapening uit te lijnen.
- Actieve voxels worden blootgesteld aan UV-licht, waardoor de oriëntatie van de versterking in die voxels wordt gefixeerd (nu in rood weergegeven).
- Het magnetische veld wordt verschoven om een nieuwe oriëntatie van de wapening in te stellen.
- Herhaal de UV-belichtingsstap om de oriëntatie voor de volgende set voxels te corrigeren (herhaal indien nodig).
- Bouwplaat wordt aangepast om de niet-uitgeharde matrix van toevoermateriaal binnen te brengen voor de volgende afdruklaag.
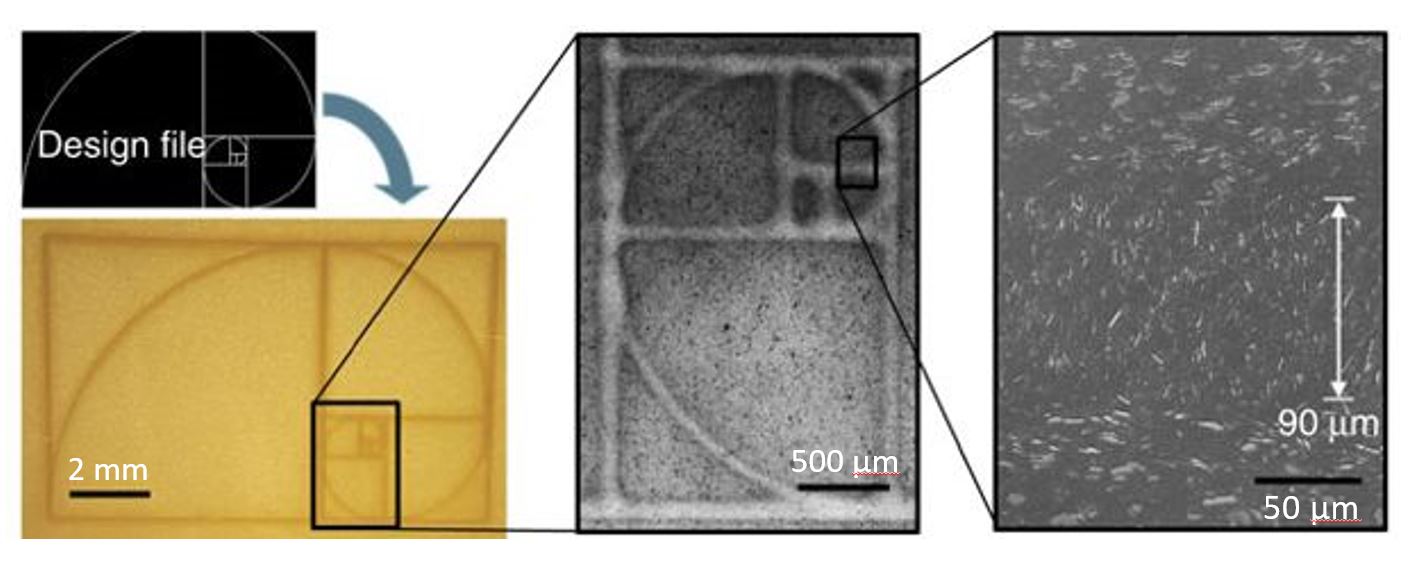
De Fluxprint-technologie maakt controle op voxelniveau mogelijk over de vezeloriëntatie tijdens het printproces. Bron | "Ontwerpen van bio-geïnspireerde composietversterkingsarchitecturen via 3D magnetisch printen" door Joshua J. Martin, Brad E. Fiore en Randall M. Erb, Nature Communications volume6, artikelnummer:8641 (2015).
Waarom voxel-by-voxel?
"Elke geometrie heeft unieke spannings- en spanningstoestanden", legt Martin uit. “De meeste composieten worden met de hand vervaardigd om dit te verklaren. We digitaliseren het proces. Als je bijvoorbeeld een UAV-frame goed kunt verstevigen, kun je minder materiaal gebruiken. Elke toepassing die de zwaartekracht tegengaat, heeft hier fundamenteel baat bij.”
Voxel-by-voxel afdrukken is ook inherent hoge resolutie. "Dit is het composietproductieproces met de hoogste resolutie tot nu toe", zegt Martin, en hij merkt op dat fused deposition modeling (FDM) - waarbij niet-versterkte of gefreesde vezelversterkte kunststof filament wordt gesmolten en op een printbed wordt afgezet - een resolutie heeft van honderden micrometer, terwijl die van Fluxprint binnen tientallen micrometers ligt. "Dus dat is een verbetering van de orde van grootte, die het gebied betreedt dat verder gaat dan wat met het blote oog wordt waargenomen. Dit soort resolutie is erg belangrijk voor een breed scala aan eindgebruiksonderdelen.”
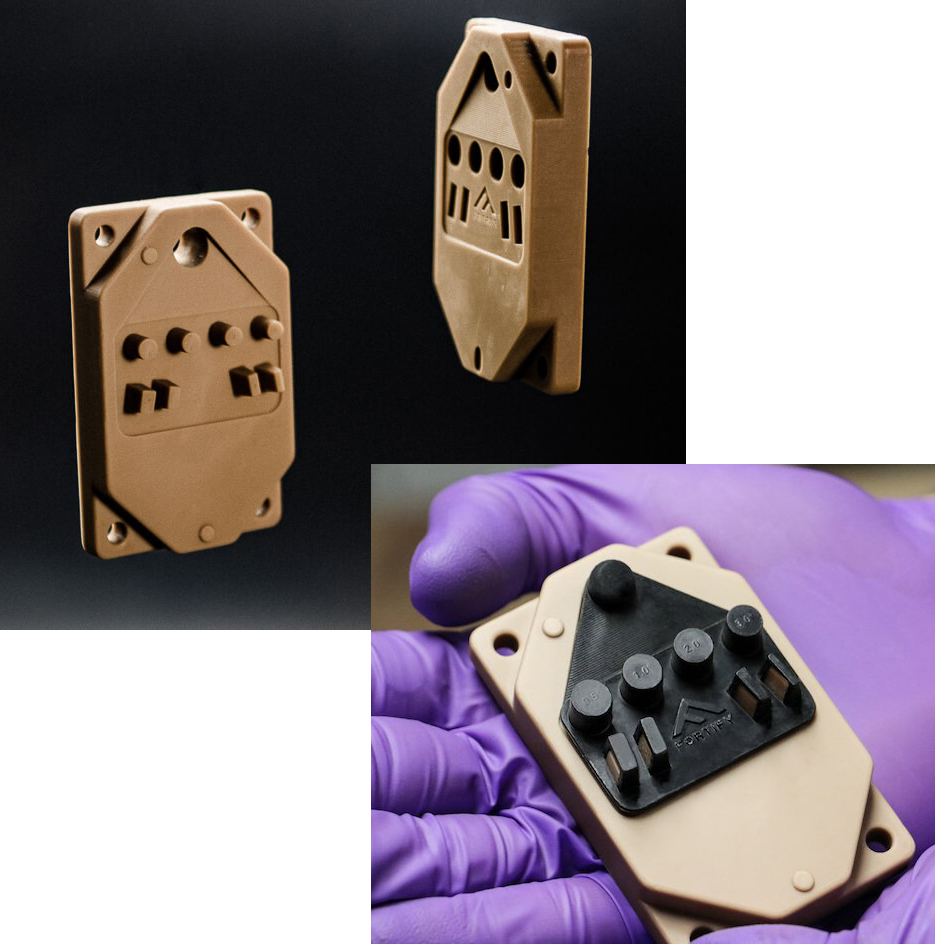
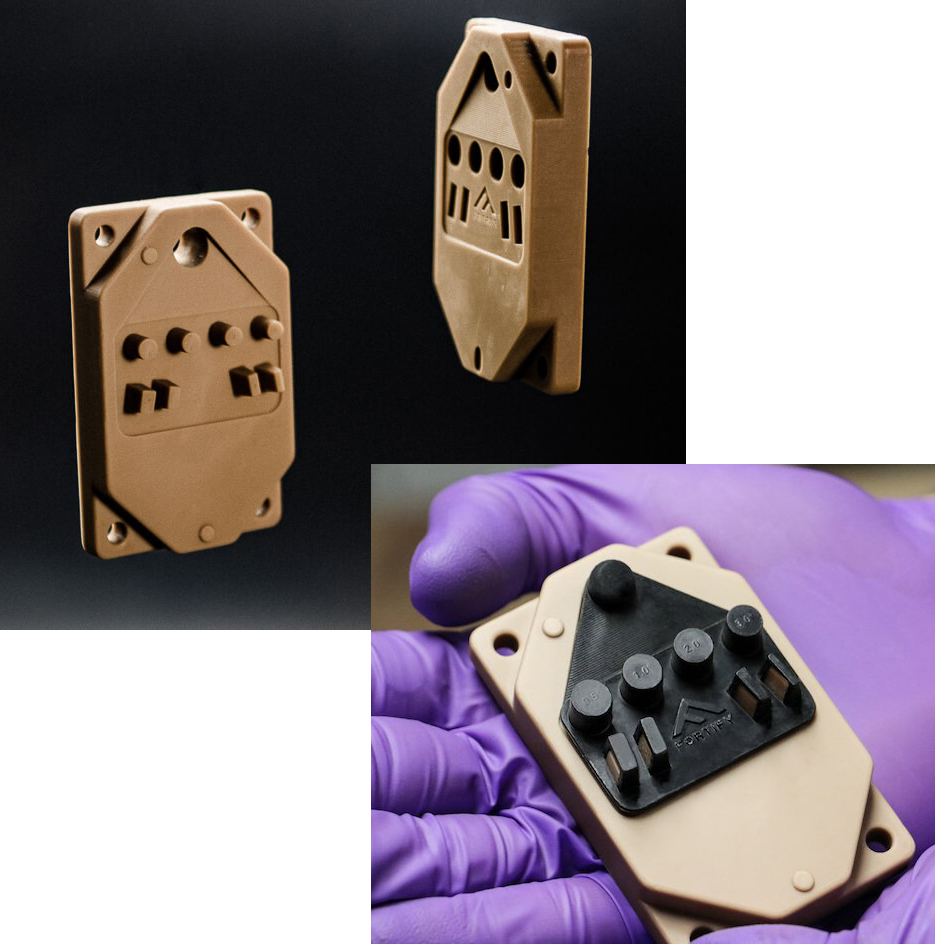
Fortify's Fluxprint magnetische 3D-printtechnologie kan vezels oriënteren om "peg"-projecties op spuitgietgereedschappen te versterken. Bron | Versterken.
"We bieden spuitgietgereedschappen die aanzienlijk goedkoper zijn dan traditioneel bewerkt metaal, in een fractie van de tijd kunnen worden geleverd en functies bieden die conventionele bewerkingspraktijken niet zouden kunnen bereiken", vervolgt Martin. “Eén klant herhaalde 12 verschillende ontwerpen per jaar, vervaardigd uit aluminium. We hebben hun time-to-market aanzienlijk gecomprimeerd en hebben in enkele maanden meer dan een dozijn ontwerpen geproduceerd. Ze kunnen nu in een kwestie van weken van ontwerp naar onderdelen in het schap gaan.” Een ander voordeel is de mogelijkheid om projecties, ook wel 'pinnen' genoemd, te versterken. Deze extrusies met een hoge aspectverhouding trekken vaak uit. Versteviging voorkomt dat, terwijl de toleranties beperkt blijven.
Lees meer over de voordelen van Fortify op het gebied van spuitgieten in het zustermagazine Additive Manufacturing van CW.
Open materialen, nieuwe ontwikkelingen
Fortify streeft een open materialenbenadering na. "We willen het vermogen van onze klanten om te groeien en te onderzoeken op het gebied van additieven niet beperken", legt Karlo Delos Reyes, VP Applications van Fortify, uit. "We garanderen onze klanten flexibiliteit en de best beschikbare materialen door open innovatie te omarmen."
"We werken samen met grote fabrikanten van polymeren en stemmen de oppervlaktechemie van additieven af", zegt Martin. Hij merkt op dat elke vulstof zijn eigen voor- en nadelen heeft met betrekking tot slijtvastheid, prestatie bij temperatuur, enz. “Voor vezels varieert de lengte van enkele µm tot enkele mm, afhankelijk van de toepassing. Waar we oppervlakteresolutie nodig hebben, gebruiken we een hoger percentage additieven met een kleinere lengte. Waar we ons een ruwer oppervlak kunnen veroorloven, maar willen optimaliseren voor bijvoorbeeld treksterkte, gebruiken we langere vezeladditieven.”
Een van de strategieën van Fortify is om samen te werken met marktleiders en leveranciers om expertise te benutten en kruisbestuiving van ideeën mogelijk te maken. Fortify heeft onlangs een samenwerking aangekondigd met DSM Additive Manufacturing (Hoek van Holland, Nederland en Elgin, Illinois, VS) om hoogwaardige composietmaterialen te ontwikkelen die zullen worden gebruikt in de printsystemen van Fortify om uitgebreide mechanische en temperatuurprestaties te bereiken. "Ze zullen ons harspalet uitbreiden", zegt Martin, "en we zijn verheugd om met hen samen te werken om geavanceerde harsen te ontwikkelen."
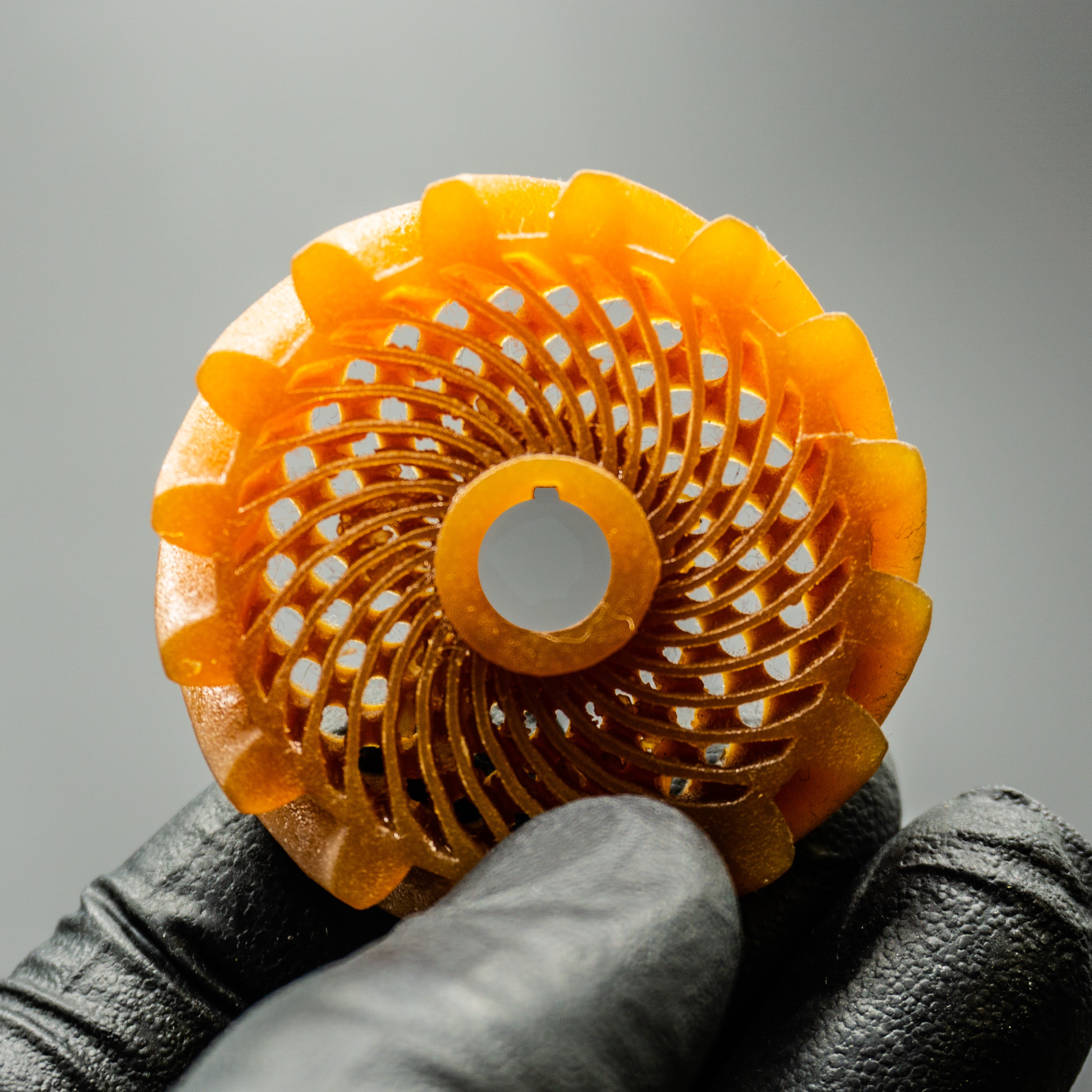
Glasvezelversterkt composiet onderdeel gemaakt met Fluxprint. BRON | Versterken.
Z-richting wapening en toepassingen
Fluxprint print nog steeds in lagen. Dus, is het mogelijk om versterking in de z-richting te bereiken? "Als je vezels van 2 millimeter lang print, kun je die niet in de z-richting plaatsen", zegt Martin. "Maar je zou korter kunnen worden vezels in z-oriëntatie. We kijken naar meerdere lengteschalen en we zien dat zich in de toekomst ontwikkelen voor een geoptimaliseerde belastingoverdracht.”
Fortify produceert al onderdelen voor UAV's, waaronder propellers, en ziet veel meer van dergelijke toepassingen in de lucht- en ruimtevaart. "We hebben een klein bouwgebied, dus we richten ons op toepassingen waar we gemakkelijk kleinere onderdelenvolumes kunnen halen", zegt Martin. "Dit is een volwassen ecosysteem, maar we bieden een nieuw prestatieniveau in mechanische eigenschappen bij hoge temperaturen en toleranties." Hij haalt aan dat hij in staat is om de warmteafbuigingstemperatuur van een onderdeel te verbeteren en legt uit dat er tientallen onderdelen onder de motorkap in auto's zijn die sterkte en stijfheid moeten bieden bij blootstelling aan temperaturen van 160°C. "Zulke onderdelen met complexe geometrieën lenen zich goed voor 3D-printen met onze technologie. Vergeleken met de huidige methode om onderdelen uit PEI (polyetherimide) te vormen en te bewerken, bieden we hogere prestaties, een kortere doorlooptijd en een hoog potentieel voor lagere kosten .”
Tooling is ook een huidige markt, inclusief matrijzen, mallen en armaturen voor spuitgieten. "Nogmaals, onze onderdelen zijn stijver, sterker en hebben een hogere temperatuurbestendigheid, waardoor de maatnauwkeurigheid behouden blijft", zegt Martin. “Maar hun echte waarde ligt in niet die een aanzienlijke nabewerking vereisen, zoals wat nodig is bij het gebruik van EDM-machines, en toch komen ze overeen met de kwaliteit van opspanningen die met deze traditionele methoden zijn gemaakt, waaronder CNC-frezen.”
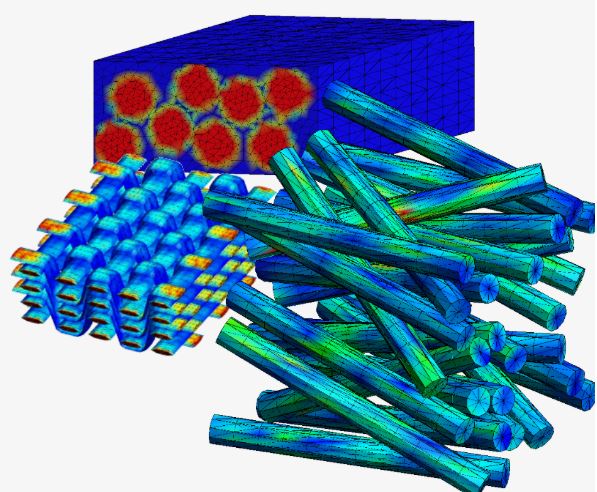
Bron | MultiMechanics
De volgende generatie multischaal, multifunctionele composieten bevorderen
Fortify werkt samen met MultiMechanics (Omaha, Neb., V.S.), een ontwikkelaar van multiscale modellerings- en simulatiesoftware voor geavanceerde materialen. Deze samenwerking is om een aantal redenen interessant. Ten eerste zal Fortify het vlaggenschipproduct van MultiMechanics, MultiMech, gebruiken om de prestaties van onderdelen te voorspellen en optimaliseren hun ontwerp en vezeloriëntatie voordat ze worden afgedrukt. MultiMech zal dus optreden om de feedback te geven voor closed-loop iteratief ontwerp , waardoor gebruikers sneller Fluxprinted composietonderdelen kunnen aanpassen en optimaliseren. Fortify en MultiMechanics zijn ook van plan om MultiMech te integreren in INFORM van Fortify generatieve ontwerp- en printcontrolesoftware. Dus, van ontwerp tot virtueel testen tot printen - alle functies worden bestuurd binnen een enkele, digitale stroom.
Voor het tweede punt is het belangrijk om te begrijpen wat MultiMechanics te bieden heeft via zijn MultiMech-software:
- Multischaal eindige-elementenanalyse , inclusief modellering van een praktisch onbeperkt aantal schalen (bijv. nano, micro, ply, laminaat, onderdeel).
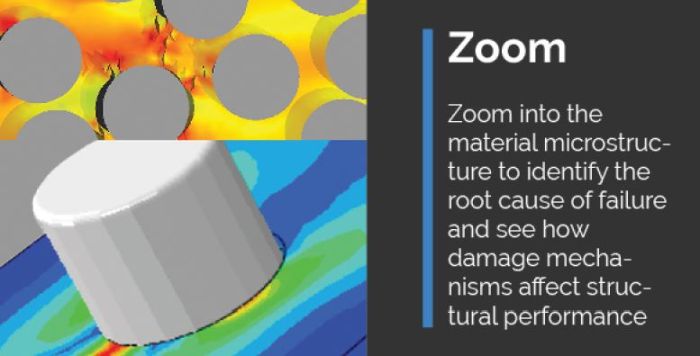
- Automatisch genereren van complexe 3D-microstructuren met eindige elementen en modellering van bijna elke materiële microstructuur, inclusief continue en gehakte vezels, deeltjes, holtes, schuim, stoffen, enz.
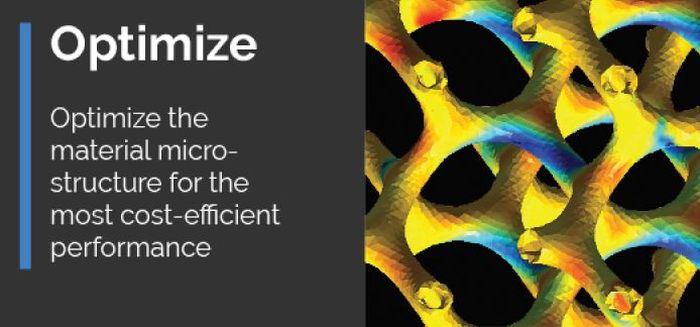
- Model effecten van bestanddelen op microschaal, inclusief interacties , volumefracties, distributie en oriëntatie, plus import p door roces veroorzaakte variatie uit programma's (bijv. Moldex3D, Moldflow).
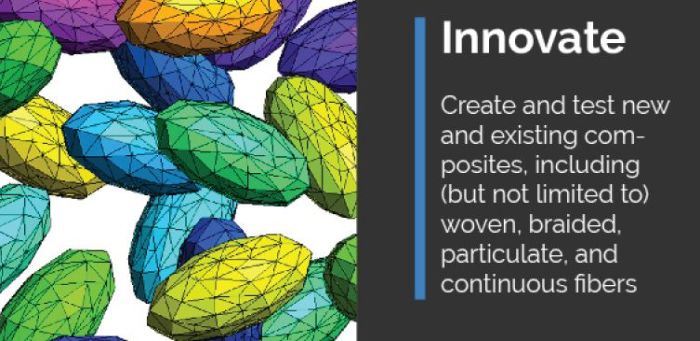
- Analyseren hoe variatie in fabricage van invloed is op de prestaties van onderdelen en voer da . uit magie modelleren inclusief overgang op meerdere schalen van microscheuren naar macroscheuren.
Dit gaat terug op waarom Martin en Erb Fortify in de eerste plaats begonnen. In hun artikel uit 2015, "Ontwerpen van bio-geïnspireerde composietversterkingsarchitecturen via 3D magnetisch printen", stellen ze:
Martin en Erb bespreken natuurlijke composieten die gebruik maken van discontinue vezels en versterkende deeltjes die zijn georganiseerd in meerschalige, complexe architecturen om superieure eigenschappen te bereiken ten opzichte van hun bestanddelen. Een voorbeeld gegeven door Qunfeng Cheng in een 2017 Materials Today artikel is parelmoer in abalone schelpen. Bestaande uit 95 vol% anorganische aragoniet en 5 vol% organische eiwitmatrix, is de breuktaaiheid van parelmoer 3.000 keer hoger dan die van aragoniet. Cheng merkt op dat dit een 'versterkingseffect' in mechanische eigenschappen vertoont dat ver buiten de regel van mengsels in traditionele composieten gaat .
In de Geavanceerde materialen van 2018 artikel, "Additive Manufacturing as a Method to Design and Optimize Bioinspired Structures", beweren de auteurs Audrey Velasco-Hogan, Jun Xu en Marc A. Meyers dat de hiërarchische structuur van materialen zoals parelmoer, been, bamboe en schelpen van schaaldieren maakt hun indrukwekkende combinatie mogelijk van sterkte, modulus, lichtgewicht, taaiheid en weerstand tegen vermoeiing. Hun samenstellende deeltjes/filamenten en matrix zijn op elk niveau anders georganiseerd (bijv. nano-, micro-, meso-, macro-), variërend van de eigenschappen op elk niveau (d.w.z. een multischaalcomposiet). In combinatie met efficiënte interfaces tussen de niveaus werkt deze hiërarchische structuur synergetisch om de verspreiding van scheuren te verminderen en de taaiheid te verbeteren met behoud van hardheid - iets dat na ongeveer een eeuw proberen nog niet is bereikt in keramiek.
Toekomst van composieten en INFORM
Dit is de toekomst van composieten:het ontwerpen van hiërarchische composieten met unieke eigenschappen op maat gemaakt voor precieze toepassingen. En het wordt al snel gevorderd. Het Duitse Aerospace Center (DLR) Institute of Structures and Design in Stuttgart is bijvoorbeeld ook een samenwerking aangegaan met MultiMechanics begrijpen hoe temperatuurverandering de microstructuur en het materiaalgedrag van keramische matrixcomposieten (CMC's) beïnvloedt . Deze analyse wordt als cruciaal beschouwd voor de toekomstige productie van CMC-componenten van DLR, waaronder straalbuizen voor raketten en thermische beveiligingssystemen voor terugkeervoertuigen. "Ons werk bij MultiMechanics van de afgelopen tien jaar is gewijd aan het nauwkeurig het verbinden van microstructureel gedrag van geavanceerde materialen tot de algemene prestatie van het onderdeel en de fabricage ”, zegt Dr. Flavio Souza, president en CTO van MultiMechanics. "MultiMech stelt ons in staat microstructurele scheuren te modelleren en te bepalen hoe deze het algehele composietdeel zouden beïnvloeden", zegt Neraj Jain, groepsleider in de afdeling Keramische Composieten en Structuren bij DLR. "De efficiënte integratie van MultiMech met onze andere FEA-tools zoals Abaqus en ANSYS verhoogt onze productiviteit en brengt ons dichter bij ons doel om de CMC-materialen virtueel te optimaliseren .”
Zodra deze composieten virtueel zijn geoptimaliseerd, worden ze afgedrukt, met MultiMech ingebed in de INFORM-software van Fortify, die al is gericht op organische, voor belasting geoptimaliseerde architecturen via de generatieve ontwerpruggengraat . (Merk op dat de business unit Composite Materials van Solvay ook heeft geïnvesteerd in zowel MultiMechanics als 3D-printtechnologie.)
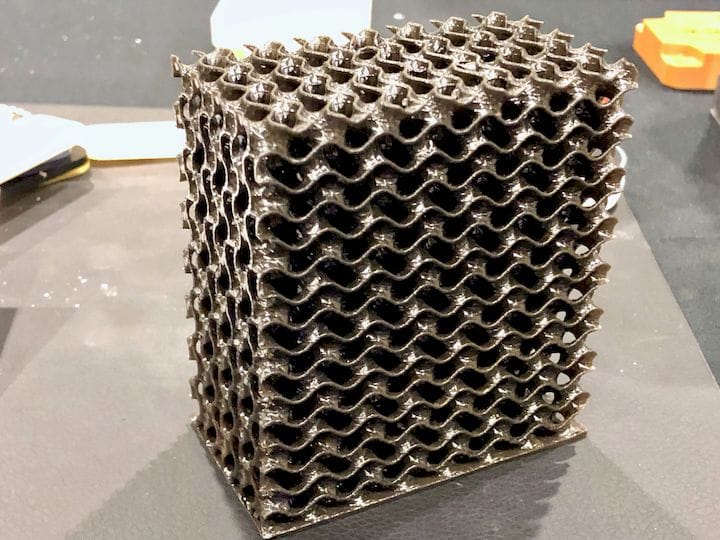
Vezelversterkt rooster, ontwerp geleverd door nTopology. Bron | Versterken.
“INFORM gebruikt geavanceerde algoritmen om de vezeloriëntatie voor elk onderdeel te optimaliseren”, legt Martin uit. "Waar traditioneel de 3D-printworkflow begint met STL om het ontwerp te snijden, de onze begint met FEA (een model met spanning en rek) en beslist vervolgens in welke voxels dat gemodelleerde ontwerp moet worden gescheiden en hoe de vezels moeten worden georiënteerd. We doorlopen iteraties, brengen de vezels op één lijn met spannings-/rekveldvectoren en simuleren vervolgens hoe die afdruk zich zal gedragen en gebruiken die gegevens om het ontwerp te verfijnen en optimaliseren, om een microstructureel generatief ontwerp te bereiken. .”
Alleen het begin
Merk op dat deze toekomstige composieten een reeks materialen bevatten. Het Naval Research Laboratory (NRL, Arlington, Va., V.S.) ontwikkelt CMC's met behulp van een keramische matrix met een secundaire keramische versterking via nanodeeltjes en/of filamenten. Deze CMC's kunnen ook continue vezelversterking gebruiken. Met andere woorden, op elk niveau kunnen verschillende componenten en architecturen worden gebruikt voor de verbeterde taaiheid en op maat gemaakte elektrische en thermische eigenschappen die vereist zijn (lees bijvoorbeeld in hypersonics meer in mijn juli 2019-artikel over nanocomposieten).
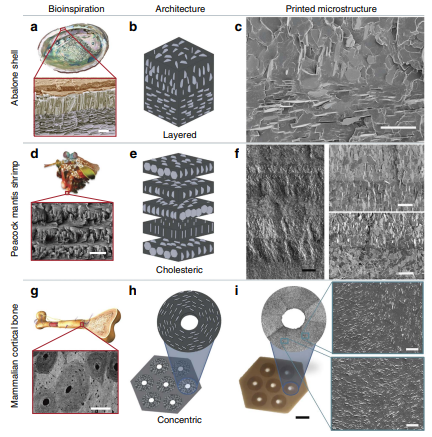
BRON | Afbeelding 3, "Ontwerpen van bio-geïnspireerde composietversterkingsarchitecturen via 3D magnetisch printen" door Joshua J. Martin, Brad E. Fiore en Randall M. Erb, Nature Communications, deel 6 (2015).
Hiërarchische composieten worden ook gedrukt en getest met behulp van versterkte epoxy-inkten en thermoplastische polymeermatrices. Dit is misschien wel het grootste voordeel voor Fortify als startup. Het bereidt zich niet alleen voor op de composieten van de toekomst, het ontwerpt en produceert ze nu al. En hoewel wat het al heeft bereikt indrukwekkend is, is het nog maar het begin.
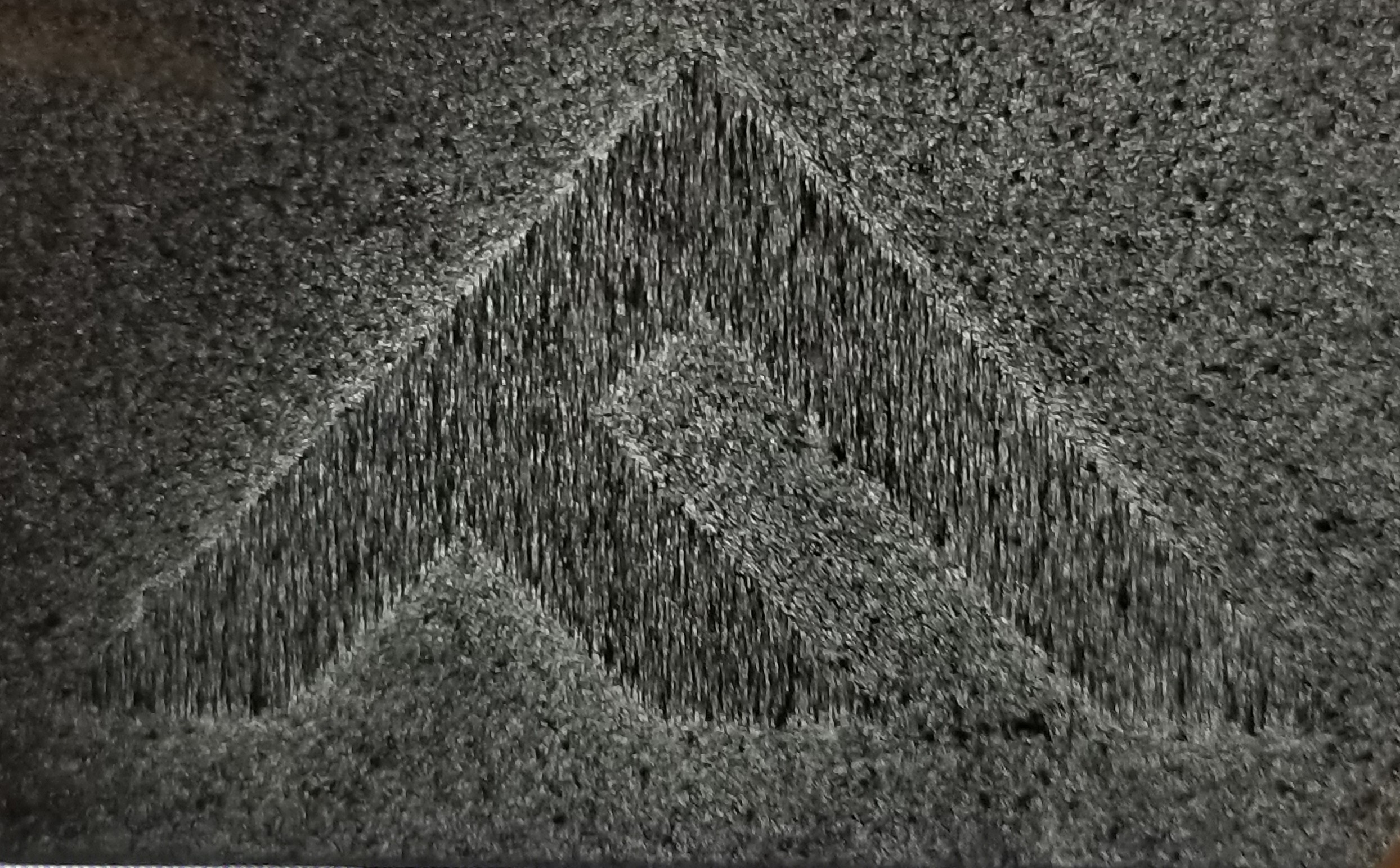
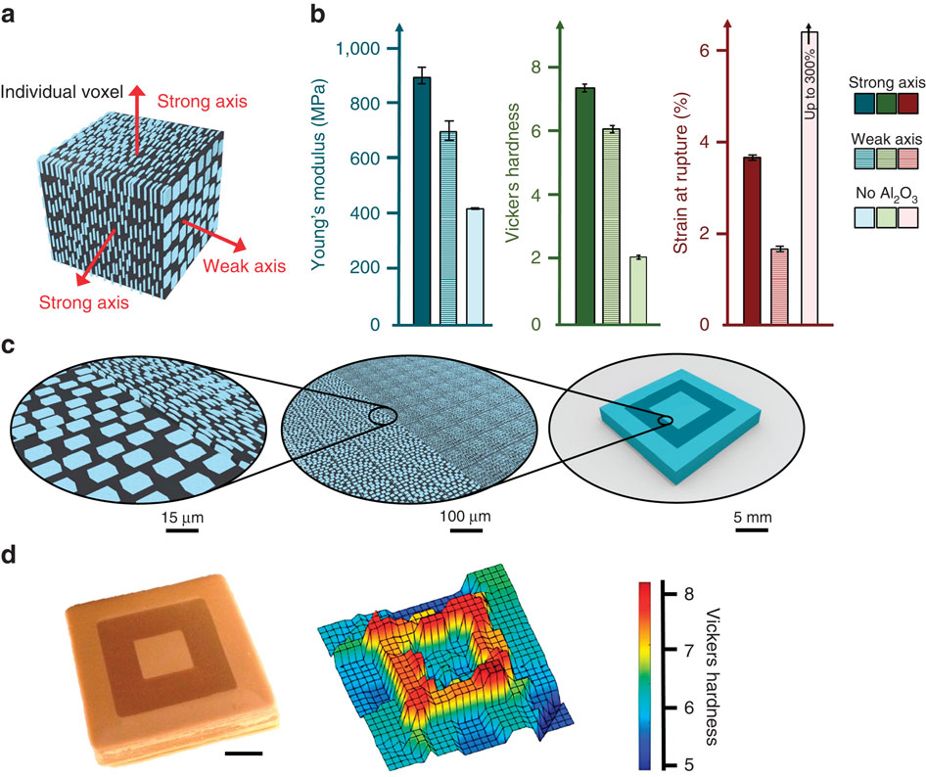
Hars
- De 3 basisstappen van 3D-printen
- Kan 3D-printen met meerdere materialen de volgende stap zijn voor AM?
- Het ABC van 3D-printen
- De evolutie van 3D-printen
- Community Colleges:opleiding van de volgende generatie fabrikanten
- Productiedag 2017:de volgende generatie werknemers opleiden
- De evolutie van additieve composieten
- 3D-print composieten met continue vezels
- Materiaal voor de volgende generatie slimme sensoren
- Ultradunne Terahertz-bron effent de weg naar de volgende generatie communicatietechnologie
- COVID-19:vraag naar de volgende generatie slimme fabrieken