Injectievormen voor hoogwaardige, verenigde thermoplastische structuren
Verenigde composiet tandwiel-aandrijfas. Herone gebruikt gevlochten thermoplastische composiet prepreg-tapes als voorvormen voor een proces dat het laminaat van de aandrijfas consolideert en functionele elementen zoals tandwielen omhult, waardoor eenheidsstructuren worden geproduceerd die het gewicht, het aantal onderdelen, de montagetijd en de kosten verminderen. Bron voor alle afbeeldingen | reiger
De huidige prognoses vragen om een verdubbeling van de vloot van commerciële vliegtuigen in de komende 20 jaar. Om hieraan tegemoet te komen, variëren de productiesnelheden in 2019 voor composiet-intensieve widebody-straalvliegtuigen van 10 tot 14 per maand per OEM, terwijl de narrowboden al zijn gestegen tot 60 per maand per OEM. Airbus werkt specifiek samen met leveranciers om traditionele maar tijdrovende, met de hand opgemaakte prepreg-onderdelen op de A320 om te zetten in onderdelen die zijn gemaakt via snellere cyclustijdprocessen van 20 minuten, zoals hogedrukharsoverdrachtgieten (HP-RTM), waardoor onderdelen leveranciers voldoen aan een verdere push richting 100 vliegtuigen per maand. Ondertussen voorspelt de opkomende markt voor stedelijke luchtmobiliteit en vervoer een behoefte aan 3.000 elektrische verticale start- en landingsvliegtuigen (EVTOL) per jaar (250 per maand).
"De industrie heeft geautomatiseerde productietechnologieën nodig met kortere cyclustijden die ook de integratie van functies mogelijk maken, die worden aangeboden door thermoplastische composieten", zegt Daniel Barfuss, mede-oprichter en managing partner van herone (Dresden, Duitsland), een composiettechnologie en onderdelenproductie bedrijf dat hoogwaardige thermoplastische matrixmaterialen gebruikt, van polyfenyleensulfide (PPS) tot polyetheretherketon (PEEK), polyetherketonketon (PEKK) en polyaryletherketon (PAEK). "Ons belangrijkste doel is om de hoge prestaties van thermoplastische composieten (TPC's) te combineren met lagere kosten, om op maat gemaakte onderdelen mogelijk te maken voor een grotere verscheidenheid aan seriële productietoepassingen en nieuwe toepassingen", voegt Dr. Christian Garthaus toe, de tweede medeoprichter en directeur van Herone. partner.
Om dit te bereiken heeft het bedrijf een nieuwe aanpak ontwikkeld, te beginnen met volledig geïmpregneerde, continue vezeltapes, deze tapes te vlechten om een holle preform "organoTube" te vormen en de organoTubes te consolideren tot profielen met variabele doorsneden en vormen. In een volgende processtap gebruikt het de lasbaarheid en thermovormbaarheid van TPC's om functionele elementen zoals composiet tandwielen op aandrijfassen, eindfittingen op pijpen of belastingoverdrachtselementen in trek-compressiesteunen te integreren. Barfuss voegt eraan toe dat er de mogelijkheid is om een hybride vormproces te gebruiken - ontwikkeld door ketonmatrixleverancier Victrex (Cleveleys, Lancashire, VK) en onderdelenleverancier Tri-Mack (Bristol, RI, VS) - dat PAEK-tape met een lagere smelttemperatuur gebruikt voor de profielen en PEEK voor het overmolding, waardoor een versmolten, enkelvoudig materiaal over de verbinding mogelijk is (zie "Overmolding breidt het assortiment van PEEK in composieten uit"). "Onze aanpassing maakt ook geometrische vormvergrendeling mogelijk", voegt hij eraan toe, "waardoor geïntegreerde structuren ontstaan die zelfs hogere belastingen kunnen weerstaan."
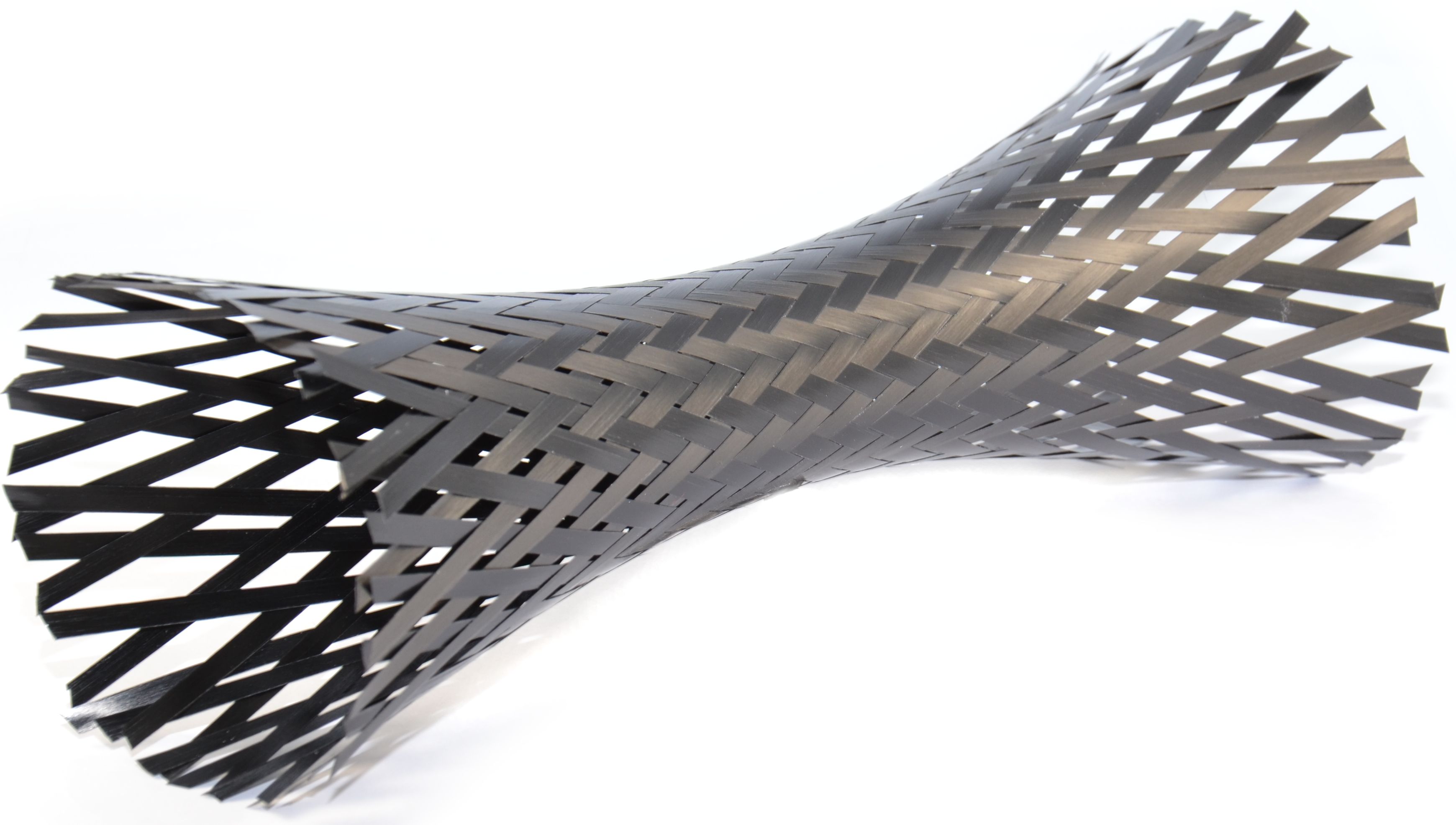
Gevlochten vormproces op basis van organoTube
Het herone-proces begint met volledig geïmpregneerde, met koolstofvezel versterkte thermoplastische tapes die tot organotubes worden gevlochten en geconsolideerd. "We zijn 10 jaar geleden met deze organoTubes begonnen om composiet hydraulische leidingen voor de luchtvaart te ontwikkelen", zegt Garthaus. Hij legt uit dat omdat geen twee hydraulische leidingen voor vliegtuigen dezelfde geometrie hebben, er voor elk een mal nodig zou zijn, gebruikmakend van bestaande technologie. “We hadden een buis nodig die nabewerkt kon worden om de individuele buisgeometrie te bereiken. Het idee was dus om doorlopende composietprofielen te maken en deze vervolgens CNC te buigen tot de gewenste geometrieën.”
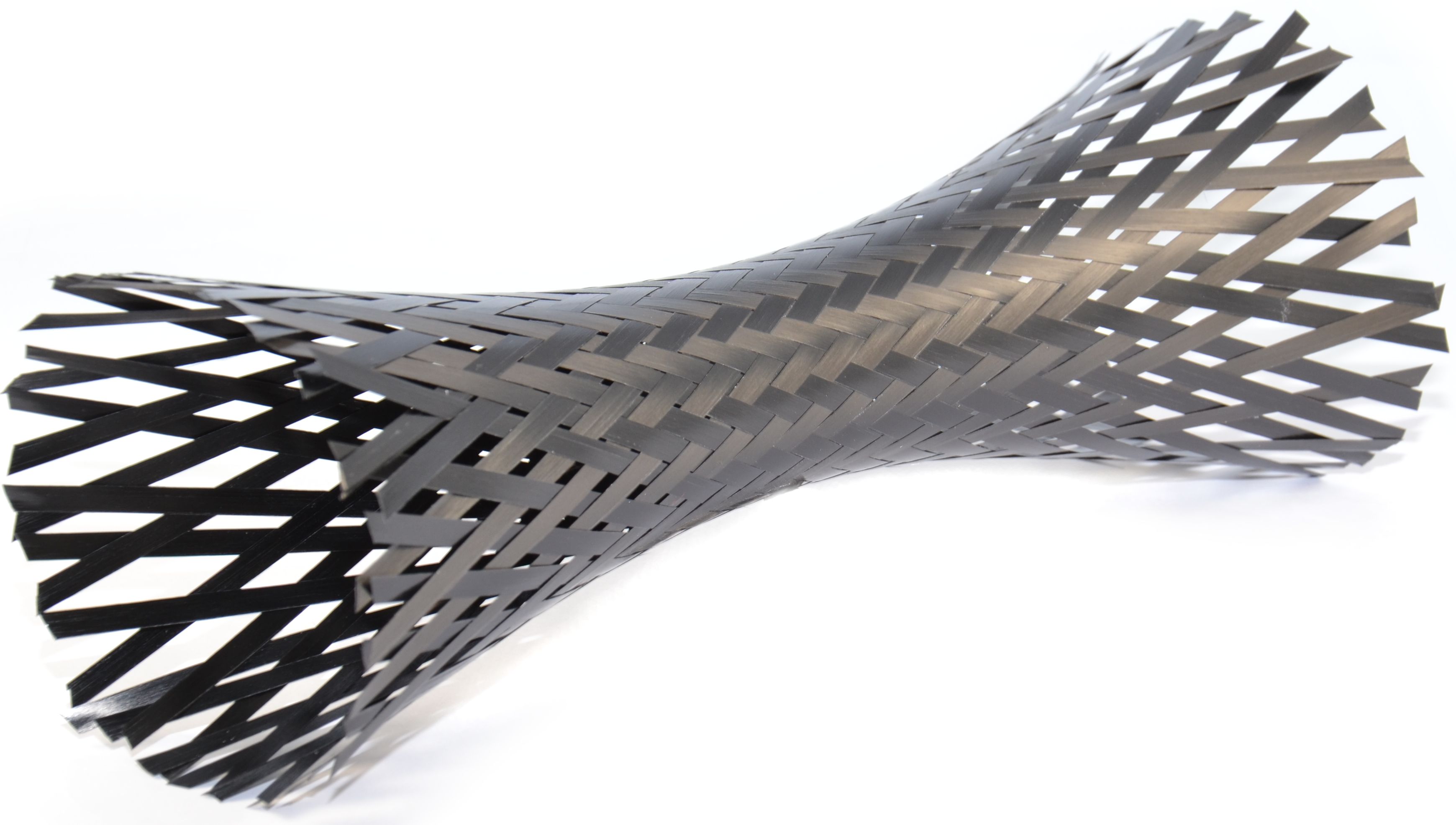
Afb. 2 Gevlochten prepreg-tapes bieden netvormige voorvormen, organoTubes genaamd, voor het herone's injectievormingsproces en maken de productie van verschillende vormen mogelijk.
Dit klinkt vergelijkbaar met wat Sigma Precision Components (Hinckley, U.K.) doet (zie "Aeromotoren herstellen met composietbuizen") met zijn koolstofvezel/PEEK-motorbekleding. "Ze kijken naar vergelijkbare onderdelen, maar gebruiken een andere consolidatiemethode", legt Garthaus uit. "Met onze aanpak zien we mogelijkheden voor betere prestaties, zoals een porositeit van minder dan 2% voor ruimtevaartconstructies."
Garthaus' Ph.D. scriptiewerk bij de ILK onderzocht het gebruik van continue thermoplastische composiet (TPC) pultrusie om gevlochten buizen te produceren, wat resulteerde in een gepatenteerd continu productieproces voor TPC-buizen en profielen. Voor nu heeft herone er echter voor gekozen om samen te werken met luchtvaartleveranciers en klanten met behulp van een discontinue vormproces. "Dit geeft ons de vrijheid om alle verschillende vormen te maken, inclusief gebogen profielen en profielen met verschillende doorsneden, evenals het aanbrengen van lokale patches en ply drop-offs", legt hij uit. “We werken eraan om het proces voor het integreren van lokale patches te automatiseren en deze vervolgens te coconsolideren met het samengestelde profiel. Kortom, alles wat u kunt doen met platte laminaten en schalen, kunnen wij doen voor buizen en profielen.”
Het maken van deze holle TPC-profielen was eigenlijk een van de moeilijkste uitdagingen, zegt Garthaus. “Je kunt niet stempelen of blazen met een siliconenblaas; dus moesten we een nieuw proces ontwikkelen.” Maar dit proces maakt zeer hoogwaardige en op maat gemaakte buis- en schachtonderdelen mogelijk, merkt hij op. Het maakte het ook mogelijk om het hybride gieten te gebruiken dat Victrex heeft ontwikkeld, waarbij PAEK met een lagere smelttemperatuur wordt overgoten met PEEK, waardoor de organoplaat en het spuitgieten in één stap worden geconsolideerd.
Een ander opmerkelijk aspect van het gebruik van preforms van gevlochten organoTube-tape is dat ze heel weinig afval produceren. "Met vlechten hebben we minder dan 2% afval, en omdat het TPC-tape is, kunnen we deze kleine hoeveelheid afval terug in de overmolding gebruiken om de materiaalbenuttingsgraad tot 100% te krijgen", benadrukt Garthaus.
Ontwikkelen van een bedrijf en een demonstratiemodel voor tandwielassen
Barfuss en Garthaus begonnen hun ontwikkelingswerk als onderzoekers aan het Institute of Lightweight Engineering and Polymer Technology (ILK) aan de TU Dresden. "Dit is een van de grootste Europese instituten voor composieten en hybride lichtgewichtontwerpen", merkt Barfuss op. Hij en Garthaus werkten daar bijna 10 jaar aan een aantal ontwikkelingen, waaronder continue TPC-pultrusie en verschillende soorten verbindingen. Dat werk werd uiteindelijk gedestilleerd tot wat nu de heldhaftige TPC-procestechnologie is.
"Vervolgens hebben we ons aangemeld voor het Duitse EXIST-programma, dat gericht is op het overdragen van dergelijke technologie naar de industrie en dat jaarlijks 40-60 projecten financiert in een breed scala van onderzoeksgebieden", zegt Barfuss. "We hebben financiering ontvangen voor kapitaalgoederen, vier werknemers en investeringen voor de volgende stap van opschaling." Ze vormden herone in mei 2018 na een expositie op JEC World.
Tegen JEC World 2019 had herone een reeks demonstratie-onderdelen geproduceerd, waaronder een lichtgewicht, hoog koppel, geïntegreerde tandwielaandrijfas of tandwielas. "We gebruiken een organoTube van koolstofvezel/PAEK-tape gevlochten onder de hoeken die nodig zijn voor het onderdeel en consolideren dat tot een buis", legt Barfuss uit. "Vervolgens verwarmen we de buis voor op 200 ° C en overgieten deze met een tandwiel dat is gemaakt door korte koolstofvezelversterkte PEEK te injecteren bij 380 ° C." De overmolding is gemodelleerd met Moldflow Insight van Autodesk (San Rafael, Californië, VS). De vultijd van de mal werd geoptimaliseerd tot 40,5 seconden en werd bereikt met een ALLROUNDER-spuitgietmachine van Arburg (Lossburg, Duitsland).
Dit overgieten vermindert niet alleen de montagekosten, fabricagestappen en logistiek, maar verbetert ook de prestaties. Het verschil van 40°C tussen de smelttemperatuur van de PAEK-as en die van het omgevormde PEEK-tandwiel maakt een samenhangende smeltverbinding tussen de twee op moleculair niveau mogelijk. Een tweede type verbindingsmechanisme, vormsluitend, wordt bereikt door de injectiedruk te gebruiken om de as gelijktijdig te thermovormen tijdens het overgieten om een vormsluitende contour te creëren. Dit is in figuur 1 hieronder te zien als “injectievormend”. Het creëert een gegolfde of sinusoïdale omtrek waar het tandwiel is verbonden versus een gladde cirkelvormige dwarsdoorsnede, wat resulteert in een geometrisch vergrendelende vorm. Dit verhoogt de sterkte van de geïntegreerde tandwielas verder, zoals aangetoond tijdens testen (zie grafiek rechtsonder). Afb. 1. Ontwikkeld in samenwerking met Victrex en ILK, gebruikt herone injectiedruk tijdens het overgieten om een vormsluitende contour te creëren in de geïntegreerde tandwielas (boven). Dit injectievormingsproces zorgt ervoor dat de geïntegreerde tandwielas met vormvergrendeling (groene curve in grafiek) een hoger koppel kan behouden dan een overgegoten tandwielaandrijfas zonder vormvergrendeling (zwarte curve in grafiek).
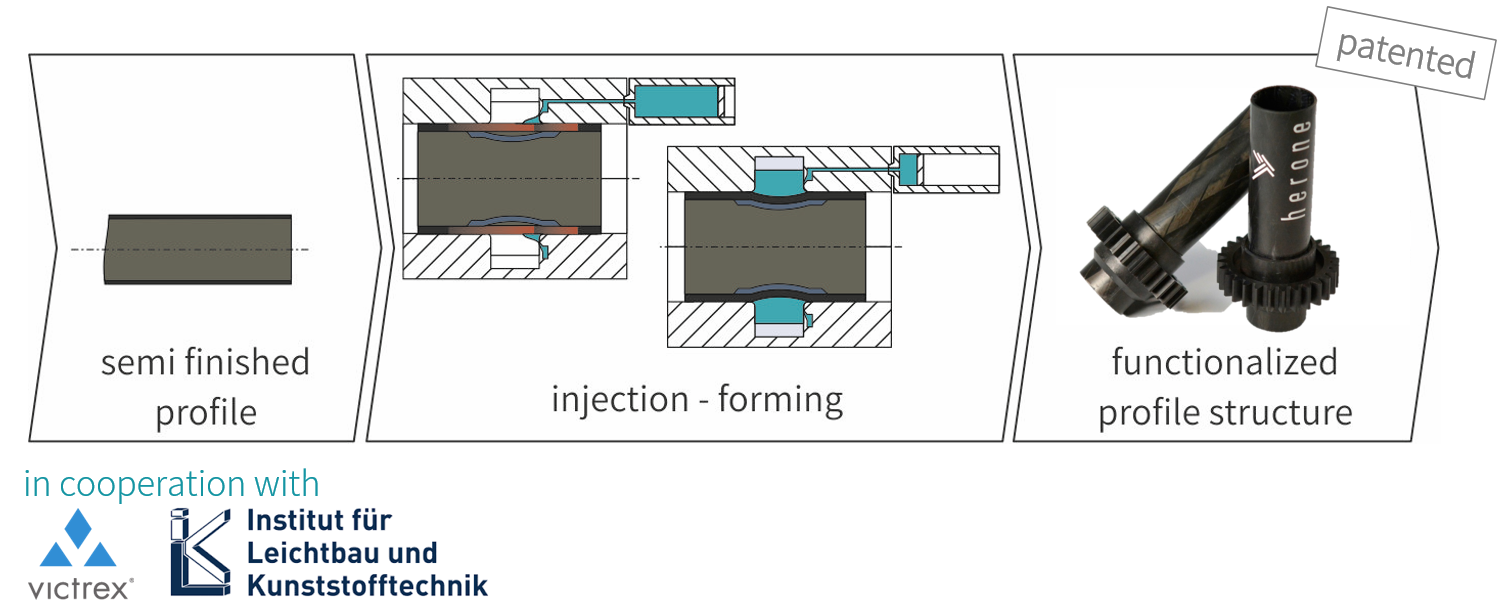
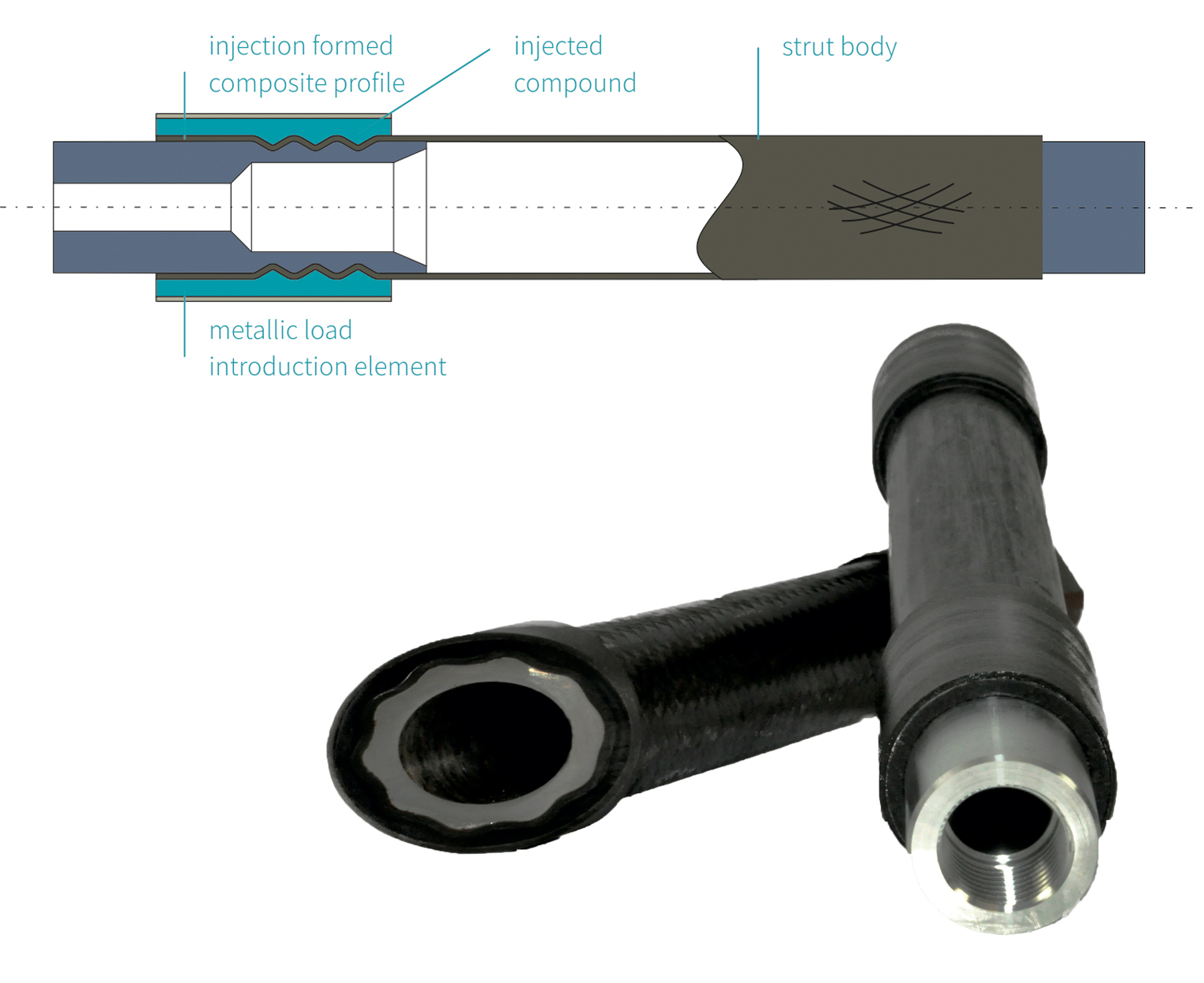
"Het belangrijkste voordeel dat we bieden, is het verminderen van het aantal onderdelen", merkt hij op. “Dit vereenvoudigt de vermoeidheid, wat een grote uitdaging is voor veerpoottoepassingen in vliegtuigen. Vormsluitend wordt al toegepast bij thermohardende composieten met een kunststof of metalen inzetstuk, maar er is geen samenhangende hechting, waardoor je een lichte beweging tussen de onderdelen kunt krijgen. Onze aanpak biedt echter een verenigde structuur zonder een dergelijke beweging.”
Garthaus noemt schadetolerantie als een andere uitdaging voor deze onderdelen. "Je moet de stutten raken en dan vermoeidheidstests doen", legt hij uit. "Omdat we hoogwaardige thermoplastische matrixmaterialen gebruiken, kunnen we tot 40% hogere schadetolerantie bereiken dan thermoharders, en ook worden eventuele microscheurtjes door impact minder met vermoeidheidsbelasting."
Hoewel demonstratiesteunen een metalen inzetstuk laten zien, ontwikkelt herone momenteel een volledig thermoplastische oplossing, waardoor een samenhangende verbinding tussen het composiet veerpootlichaam en het belastinginvoerelement mogelijk wordt. "Als we kunnen, geven we er de voorkeur aan om volledig composiet te blijven en de eigenschappen aan te passen door het type vezelversterking te veranderen, waaronder koolstof, glas, continue en korte vezels", zegt Garthaus. “Op deze manier minimaliseren we complexiteit en interfaceproblemen. We hebben bijvoorbeeld veel minder problemen met het combineren van thermoharders en thermoplasten.” Bovendien is de hechting tussen PAEK en PEEK getest door Tri-Mack, waarbij uit de resultaten blijkt dat deze 85% van de sterkte van een unidirectioneel CF/PAEK-basislaminaat heeft en twee keer zo sterk is als lijmverbindingen die gebruik maken van de industriestandaard epoxyfilmlijm.
Nieuwe fabriek, nieuwe onderdelen, nieuwe markten
Barfuss zegt dat herone nu negen medewerkers heeft en overgaat van een leverancier van technologieontwikkeling naar een leverancier van luchtvaartonderdelen. De volgende grote stap is de ontwikkeling van een nieuwe fabriek in Dresden. "Tegen het einde van 2020 zullen we een proeffabriek hebben die onderdelen uit de eerste serie produceert", zegt hij. "We werken al samen met luchtvaart-OEM's en belangrijke Tier 1-leveranciers, en demonstreren ontwerpen voor veel verschillende soorten toepassingen."
Het bedrijf werkt ook samen met eVTOL-leveranciers en een verscheidenheid aan medewerkers in de VS. Terwijl Herone luchtvaarttoepassingen volwassener maakt, doet het ook productie-ervaring op met toepassingen voor sportartikelen, waaronder vleermuizen en fietsonderdelen. "Onze technologie kan een breed scala aan complexe onderdelen produceren met voordelen op het gebied van prestaties, cyclustijd en kosten", zegt Garthaus. “Onze cyclustijd met PEEK is 20 minuten, tegenover 240 minuten met autoclaaf-uitgeharde prepreg. We zien een breed scala aan kansen, maar voorlopig ligt onze focus op het in productie krijgen van onze eerste toepassingen en het aantonen van de waarde van dergelijke onderdelen aan de markt.”
Herone zal ook presenteren op Carbon Fiber 2019. Lees meer over het evenement op carbonfiberevent.com.
Hars
- Thermoplastisch biomateriaal 'Fine-Tuned' voor medische toepassingen
- Fraunhofer stelt geautomatiseerde Engel-productiecellen in gebruik voor R&D van thermoplastisch composiet
- Composites Evolution toont hoogwaardige prepregs, nieuwe thermoplastische UD-tapes
- Thermoplastische tapes blijven potentieel tonen voor composiet aerostructuren
- UBQ Materials heeft ISO-certificeringen toegekend voor van afval afgeleid thermoplast
- Consortium streeft naar oplossingen voor thermoplastische composietstructuren van koolstofvezel
- Karl Mayer lanceert productielijn voor thermoplastische UD-tapes
- INEOS Styrolution gaat productielocatie bouwen voor StyLight thermoplastisch composiet
- Herone-productietechnologie wint JEC Innovation Award
- AeroLas onderzoekt nieuwe spintechnologie voor thermoplastisch hybride garen
- Thermoplastische deur een primeur voor autocomposieten