Geautomatiseerde verbinding van hybride metaal-thermoplastische composietstructuren
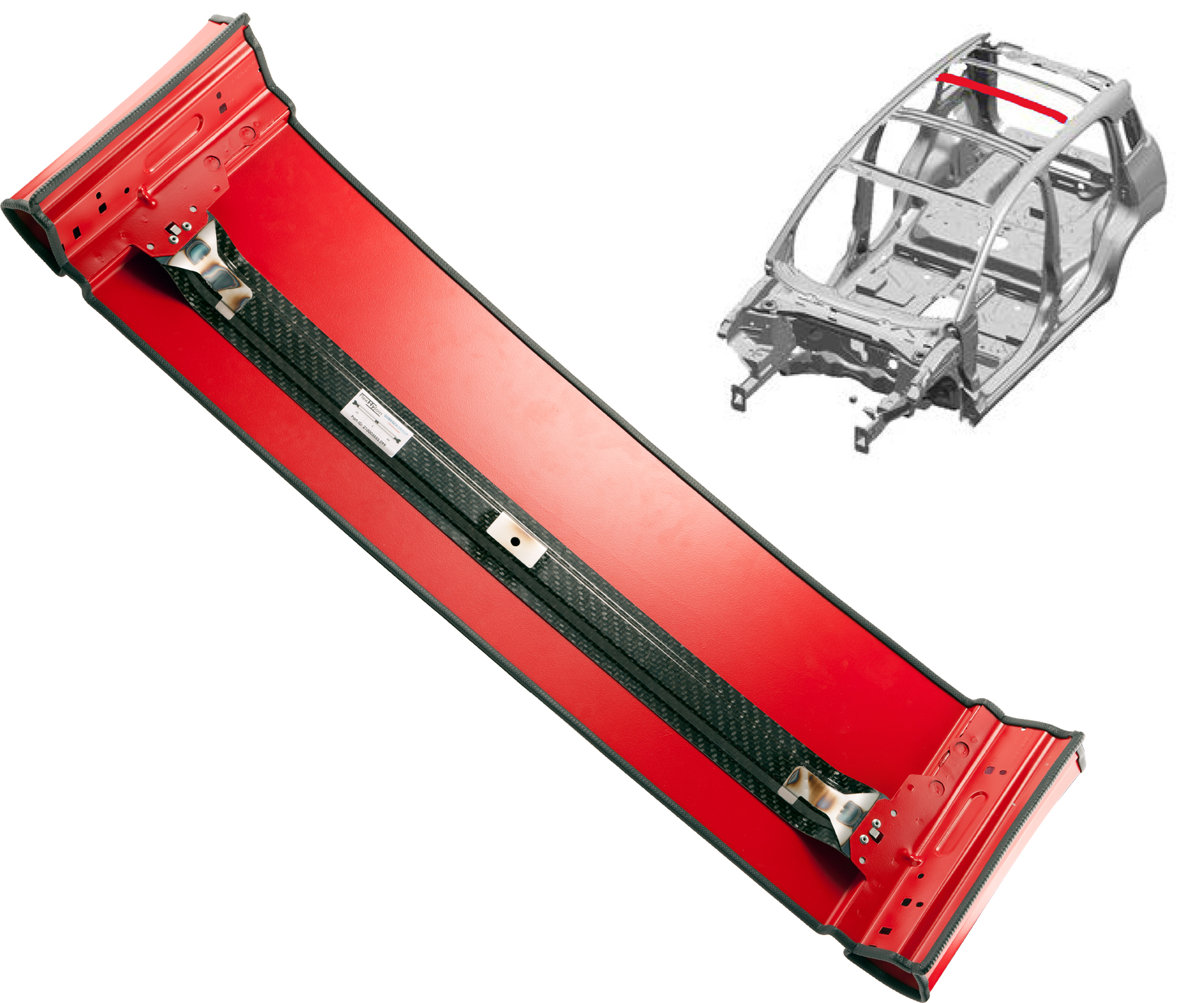
Hybride toetreding op industriële schaal mogelijk maken
FlexHyJoin demonstreert een massaproductieproces voor het produceren van een thermoplastische composiet dakversteviging met gelaste metalen beugels voor montage in een metalen carrosserie-in-wit, zoals dat van de gebruikscase van het project, de Fiat Panda stadsauto. Bron | IVW
Hybride metaal-composietstructuren blijven interessant voor auto- en ruimtevaarttoepassingen, omdat ze een lager gewicht en betere prestaties bieden door "het juiste materiaal op de juiste plaats" te plaatsen. Thermoplastische composieten (TPC's) zijn aantrekkelijk voor dergelijke multi-materiaalstructuren vanwege hun snelle verwerking, inclusief de mogelijkheid om te worden gelast en gethermovormd. Het verbinden van composieten aan metalen was tot nu toe echter voornamelijk afhankelijk van mechanische bevestigingsmiddelen, waarvoor gaten moeten worden geboord die dragende vezels beschadigen. Er is ook lijm gebruikt, maar een aantal thermoplasten is op deze manier moeilijk te lijmen; ook voegen lijmen materiaal en gewicht toe. Bijvoorbeeld de BMW i3 , dat gebruikmaakt van een met koolstofvezel versterkt plastic (CFRP) chassis en kunststof carrosseriepanelen, gebruikt 16 kilogram lijm, wat het gewichtsbesparingspotentieel van composieten gedeeltelijk tegengaat.
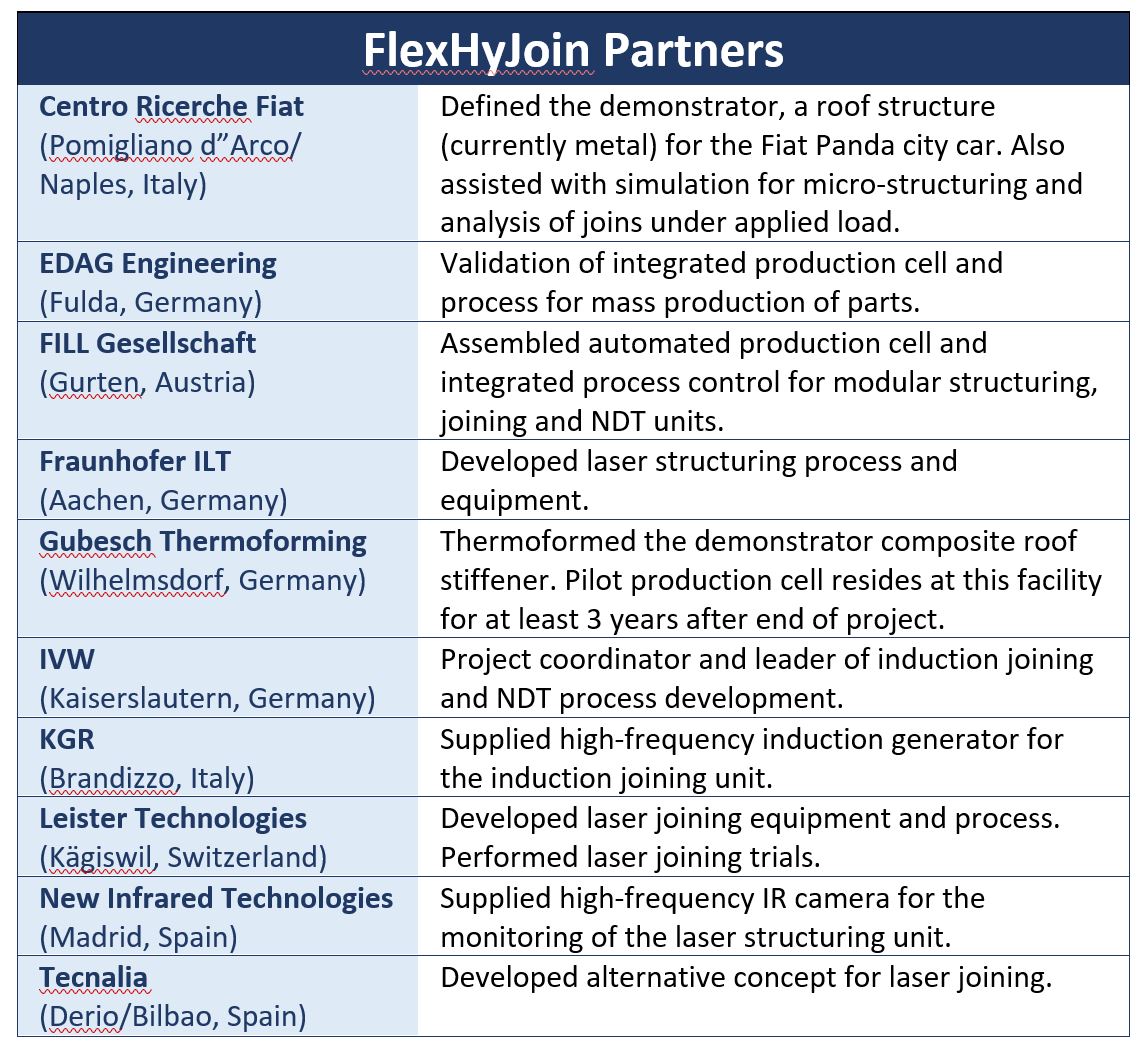
FlexHyJoin is een project dat wordt gefinancierd door het Horizon 2020-onderzoeks- en innovatieprogramma van de Europese Unie, uitgevoerd van oktober 2015 tot december 2018, dat de uitdagingen van het samenvoegen van TPC en metalen onderdelen probeerde aan te pakken. Gecoördineerd door het Institut für Verbundwerkstoffe (IVW) - een non-profit onderzoeksinstelling van de deelstaat Rijnland-Palts en de Technische Universiteit van Kaiserslautern, Duitsland - bracht FlexHyJoin 10 partners uit heel Europa samen om een geautomatiseerd proces te ontwikkelen dat een TPC-autodak mogelijk maakt structuur om te worden geassembleerd tot een metalen body-in-white (BIW). De strategie was om een gewichtsneutrale, zeer sterke verbinding te maken - zonder lijm of bevestigingsmiddelen - door metalen beugels voor te behandelen en deze via inductie en laserverbinding aan de dakverstijver te bevestigen. Dit werd bereikt in een enkele, geautomatiseerde productiecel met geïntegreerde procescontrole en inline niet-destructief testen (NDT).
Hybride demonstrator in 140 seconden
Projectpartner Centro Ricerche Fiat (Pomigliano d'Arco/Napels, Italië) leverde specificaties voor het demonstratieonderdeel - een dakversteviging voor de Fiat Panda stadsauto die momenteel van staal is gemaakt. Voor FlexHyJoin werd het onderdeel thermisch gevormd uit thermoplastisch composiet (Fig. 1) door Gubesch Thermoforming (Wilhelmsdorf, Duitsland) met behulp van 1,5 millimeter dik Tepex Dynalite 102 geweven glasvezel/polyamide 6 (PA6) organoblad geleverd door Bond-Laminates (Brilon, Duitsland). Om deze TPC dakverstijver in de Panda . te plaatsen 's stalen BIW, een set zijbeugels (links en rechts) gemaakt van 0,7 millimeter dik DC04-staal werden met een laser aan de uiteinden bevestigd. Een middenconsole van hetzelfde materiaal werd bevestigd door middel van inductieverbindingen. FlexHyJoin toonde aan dat beide verbindingsmethoden kunnen worden gebruikt voor de productie van industriële hybride constructies.
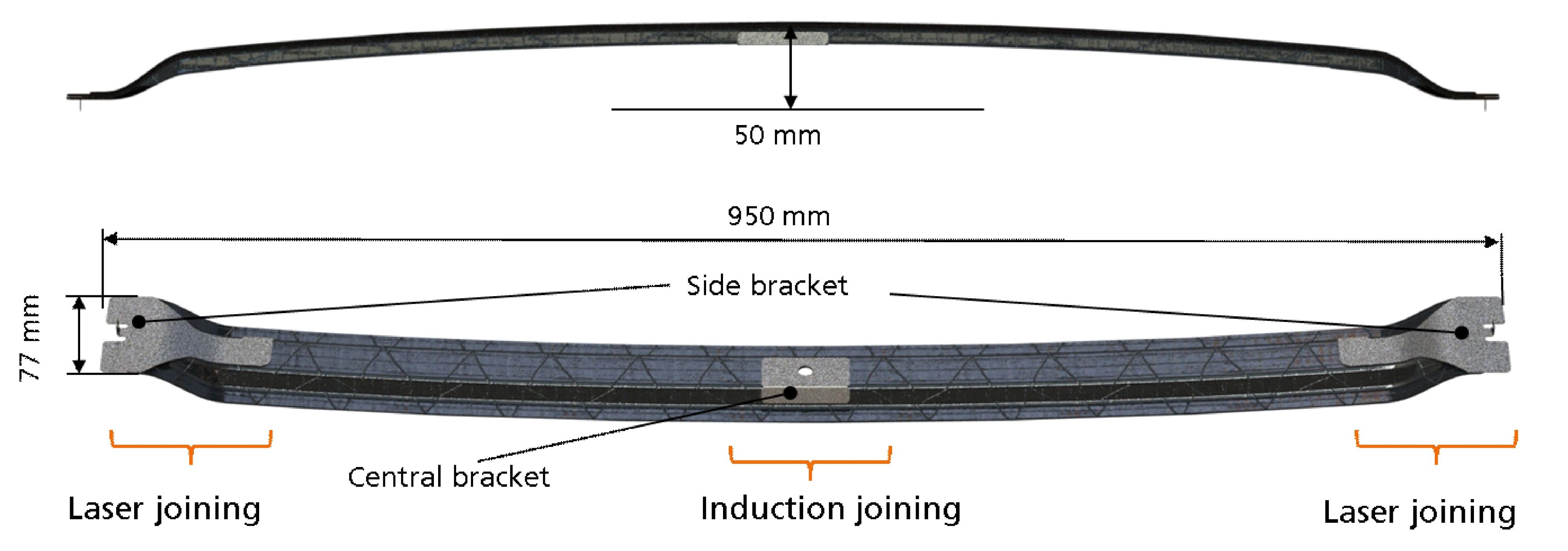
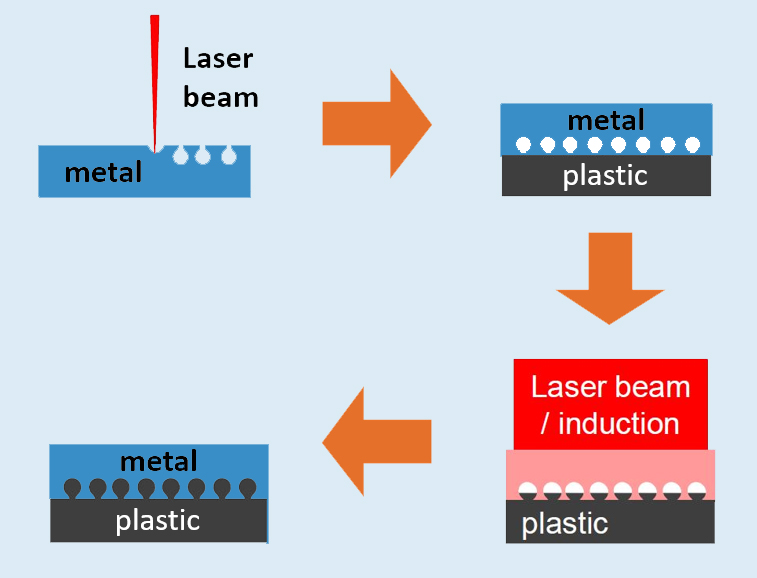
Afb. 1 Oppervlaktestructurering voor hybride verbindingen
FlexHyJoin demonstreert laser- en inductieverbinding van stalen beugels tot een gestanste GF/PA6 dakverstijver (top ). Deze hybride verbindingen zijn afhankelijk van een oppervlaktebehandeling van de metalen beugels om ondersnijdingen te creëren, die tijdens de verbindingsprocesstappen worden gevuld met gesmolten plastic (onder ).
Bron | IVW
Het simpelweg smelten van de PA6-matrix op de stalen beugels zou geen verbinding opleveren met voldoende sterkte om aan de structurele vereisten te voldoen. Er was dus een laserbehandeling van het oppervlak vereist voorafgaand aan het verbinden. "Het oppervlak van de beugels werd met een laser gestructureerd om ondersnijdingen te creëren", legt Johannes Voithofer uit, projectmanager bij Fill Gesellschaft (Gurten, Oostenrijk), die belast was met het monteren en integreren van de geautomatiseerde productiecel. “De behandelde beugels worden op het composietdeel geplaatst. Warmte en druk worden vervolgens toegepast tijdens het verbinden, waardoor de PA6-matrix van het composiet in de lasergeïnduceerde ondersnijdingen stroomt [zie Fig. 1]." Het structureringsproces is ontwikkeld door nog een andere partner, het Fraunhofer Instituut voor Lasertechnologie (ILT, Aken, Duitsland), en resulteert in een metaal-composietverbinding die materiaalhechting en mechanische vergrendeling combineert.
Samengevoegde onderdelen worden vervolgens overgebracht naar een NDO-station waar ze worden gescand op defecten met behulp van een soort thermografie. "Halogeenspots worden gebruikt voor gemoduleerde verwarming van het composietoppervlak", legt Vitalij Popow uit, IVW-onderzoeksmedewerker en hoofd voor de ontwikkeling van de FlexHyJoin NDT en procesbesturing. “Dit leidt tot een oscillerend temperatuurveld binnen de composietstructuur. We analyseren de thermische respons op het oppervlak in de loop van de tijd en identificeren defecten in de verbindingen.” Het volledig geautomatiseerde testen wordt voltooid in de productiecel voor elk gefabriceerd onderdeel. De validatie van het proces werd uitgevoerd op ongeveer 400 gewrichten.
De geautomatiseerde productiecel FlexHyJoin, zoals momenteel geconfigureerd, voert laserstructurering, verbinding en NDT parallel uit met cyclustijden van respectievelijk 81 seconden, 98-108 seconden en 100 seconden, exclusief de tijd voor robotoverdracht van onderdelen tussen stations. Voithofer zegt dat de cyclustijd per voltooid hybride onderdeel ongeveer 140 seconden is.
Afb. 2 Hybride aansluiting op industriële schaal mogelijk maken
De FlexHyJoin pilot-productiecel beschikt over drie modulaire stations voor oppervlaktestructurering, verbinding en NDO. De enkele handlingrobot van de cel brengt componenten over van de laadlade naar elk van deze stations en plaatst afgewerkte hybride onderdelen in een aangrenzende lade. Bron | IVW en vullen
Laserstructurering
Het laserstructureringsproces produceert lijnen met ondersneden geometrieën op het verbindingsoppervlak van de metalen beugels. Voor FlexHyJoin waren de ondersnijdingen 75 micrometer breed en 215 micrometer diep. Deze metingen, evenals het aantal lijnen en het algemene patroon van lijnen kunnen allemaal worden aangepast en, idealiter, worden afgestemd om te voldoen aan de vereisten voor deel- en cyclustijden.
"De positie en het aantal microstructuren op het verbindingsoppervlak kunnen worden aangepast aan de belasting in het onderdeel", legt Stefan Weidmann, IVW-onderzoeksmedewerker en leider van het ontwikkelingsteam voor de FlexHyJoin-inductieverbindingseenheid uit. "De afstand tussen microstructuren kan worden verkleind in sterk belaste gebieden van het verbindingsoppervlak en vergroot in minder belaste gebieden om een efficiënt microstructureringsproces mogelijk te maken."
Het structureren wordt bereikt door het oppervlak van de metalen beugel te ablateren met behulp van een krachtige single-mode fiberlaser geleverd door IPG Photonics (Burbach, Duitsland). Deze YLR-1000-WC laser heeft een maximaal vermogen van 1.000 watt bij een emissiegolflengte van 1.070 nanometer. "We gebruikten de single-mode fiberlaser voor het microstructureringsproces vanwege de hoge focusseerbaarheid, waarbij een puntgrootte van ongeveer 40 micrometer werd behouden", legt Christoph Engelmann uit, teamleider polymeerverwerking bij Fraunhofer ILT.
De laser bevindt zich in een optische kop die op een ABB 1200 robotarm is gemonteerd. "In de optische kop hebben we twee galvanometrische spiegels om de straal af te buigen in een werkveld van 240 millimeter bij 240 millimeter", vertelt Engelmann. “Bovendien is er één beweegbare lens om de z-hoogte (z-shifter) te volgen. We hebben de robot alleen gebruikt om de scankop boven de metalen componenten te positioneren, en dan wordt de straal afgebogen door de spiegels en wordt de z-positie voor elke afzonderlijke lijn van de microstructuur aangepast door de z-shifter. Er is dus geen beweging van de kop tijdens de verwerking. Op deze manier zijn we in staat om 2.5D-onderdelen te behandelen, waarbij we voor elke afzonderlijke lijn in dezelfde z-positie blijven, maar ons tussen lijnen kunnen aanpassen.”
"Om veiligheidsredenen zijn zowel de structurerings- als de verbindingsunits ingesloten", legt Voithofer uit, waarbij hij de zwarte kasten in de pilot-productiecel opmerkt (afb. 2). Zo blijft een geautomatiseerde poort/deur tijdens laserbewerkingen omlaag, openen voor het verwijderen van afgewerkte onderdelen en het inbrengen van nieuwe.
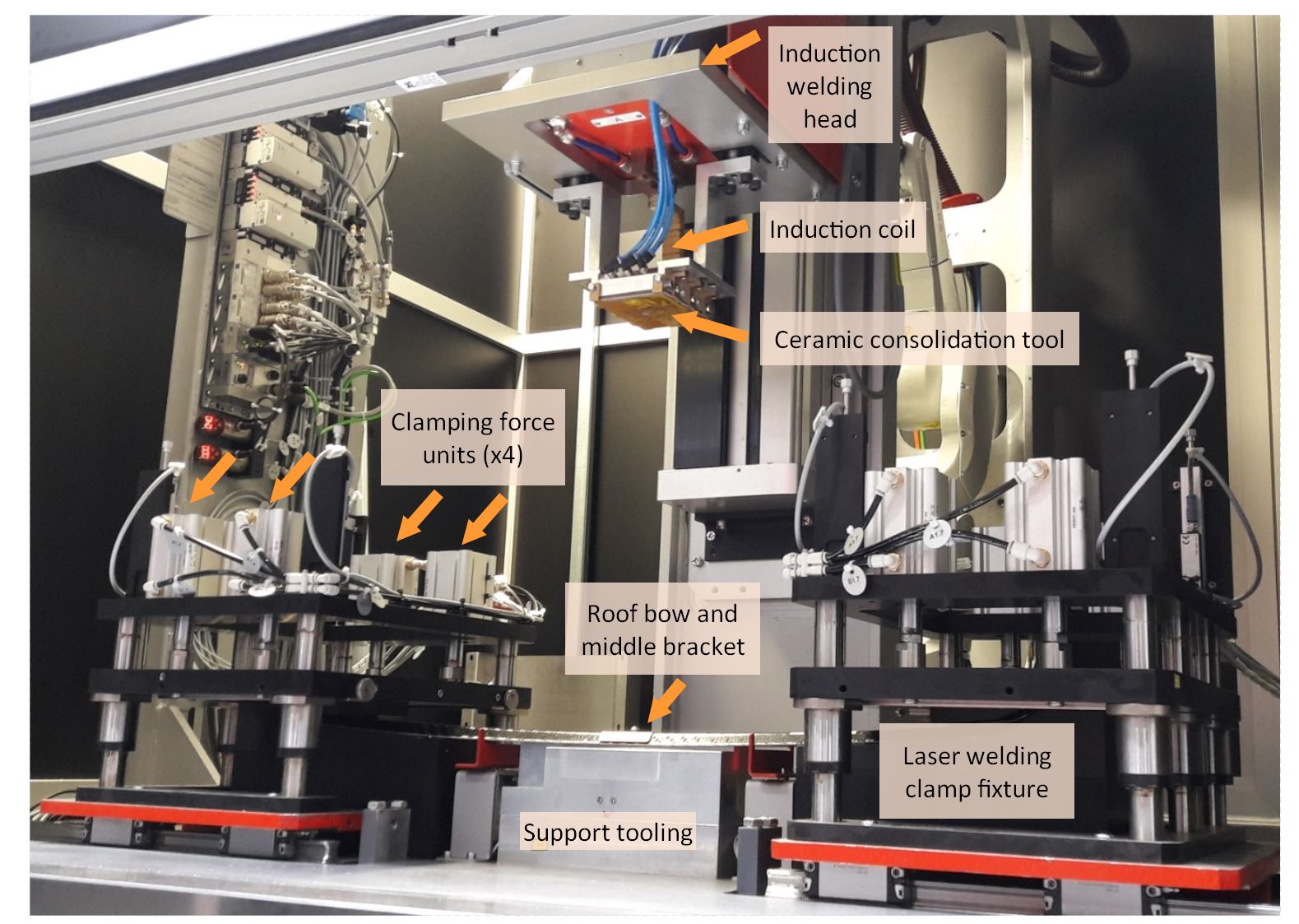
Afb. 3 Inductie- en laserverbindingscel
In de verbindingscel wordt inductieverbinding gebruikt om de middelste beugel te bevestigen, terwijl laserverbinding wordt gebruikt om de zijbeugels aan elk uiteinde van de composiet dakboog te verbinden. Bron | IVW en vullen
Inductie en laserverbinding
Grenzend aan de structurerende cel bevindt zich de verbindingscel, die twee verschillende bewerkingen omvat:inductieverbinding van de middenbeugel en laserverbinding van de linker- en rechterbeugels. "Voor grotere onderdelen met een gemiddelde complexiteit, zoals de middenconsole, is inductieverbinding een geschiktere verbindingsmethode", zegt Weidmann. “Een keramisch consolidatiegereedschap met inductor oefent druk uit op het verbindingsgebied en is doorlaatbaar voor het elektromagnetische veld, wat leidt tot een efficiënte energie-invoer in de metalen beugel voor verwarming. Dit is handig voor platte vormen, maar uitdagender voor complexe vormen, zoals de geometrie van de zijbeugels. Het was dus effectiever om hiervoor laserverbindingen te gebruiken.” Weidmann voegt toe:"Inductielassen is het beste voor grote onderdelen en een gemiddelde complexiteit, terwijl laserlassen meer geschikt is voor onderdelen met een hoge complexiteit."
Een geboord gat in de composiet dakverstijver lijnt het uit op de ondersteuningstooling, gevormd om te passen bij de kromming van de thermisch gevormde verstijver. Een lasergesneden gat in de middenbeugel plaatst het op de dakverstijver terwijl de zijbeugels zijn uitgelijnd door hun vorm die overeenkomt met de uiteinden van de dakverstijver.
"De middelste beugel is verbonden met behulp van discontinue inductie toetreden. "Dit is in wezen een quasi-statische persverbinding", zegt Weidmann, "wat eenvoudig betekent dat het een statisch proces is, waarbij een gebiedsverbinding op één plaats wordt bereikt, maar er is beweging in de z-richting omdat de dikte van het composiet enigszins verandert als gevolg van aan de consolidatiedruk die wordt uitgeoefend tijdens (inductie)verbindingen.”
De inductieverbindingseenheid bevat een KGR (Brandizzo, Italië) hoogfrequente generator om een wisselend elektrisch veld aan de inductiespoel te leveren. De kop wordt bewogen via een elektromotor en spindel (afb. 3), zodat het keramische consolidatiegereedschap op de metalen beugel drukt. De inductiespoel in het consolidatiegereedschap zorgt ervoor dat het metaal opwarmt, waardoor de composietmatrix smelt en de verbinding ontstaat. "Er wordt druk uitgeoefend tijdens het verwarmen en koelen", merkt Weidmann op.
Laserverbinding van de zijbeugels begint gelijktijdig met inductieverbinding. Twee kleminrichtingen, aan weerszijden van het steungereedschap, kunnen 4.000 Newton klemkracht uitoefenen op de zijbeugels. "Het klemmen is nodig om de opening tussen de composiet en metalen componenten te minimaliseren", legt Voithofer uit. "Dit voorkomt holtes in het gewricht." Nadat de klemkracht is toegepast, komt de laserkop in positie. Het is uitgerust met een LineBeam-diodelaser geleverd door Leister Technologies (Kägiswil, Zwitserland). Johannes Eckstaedt van Leister legt uit dat deze laser een maximaal uitgangsvermogen heeft van 600 watt bij een emissiegolflengte van 980 nanometer. De straal wordt gevormd tot een lijn van 27 millimeter bij 1 millimeter door optische lenzen en wordt gefocusseerd op de metalen beugel. De laserkop is op een robotarm gemonteerd waardoor deze langs het gevormde beugeloppervlak kan bewegen. "We hebben verschillende snelheden ingesteld voor elk gebied van de beugels om een homogene verbindingstemperatuur te bereiken, waardoor de thermische spanning wordt verminderd voor de beste verbindingsresultaten", zegt Eckstaedt.
Over het algemeen kan laserverbinding gebruik maken van transmissie- of warmtegeleidingsverbindingen. Voor lasertransmissieverbinding moet het te verbinden composiet transparant zijn voor de geselecteerde golflengte van de laser. De laser gaat dan door het composiet, raakt het metalen oppervlak van de beugel en verwarmt deze. Deze methode werd echter niet gebruikt in de FlexHyJoin-demonstrator omdat het organoplaatlaminaat van de dakverstijver niet lasertransparant was. In plaats daarvan werd de alternatieve methode van warmtegeleidingsverbinding gebruikt. Dit brengt de laser eenvoudig rechtstreeks op het metalen oppervlak aan, dat warmte door het metalen basismateriaal naar de composiet geleidt, waardoor de PA6-matrix smelt bij 220-300ºC en de verbinding ontstaat. "Dankzij de hoge thermische geleidbaarheid van de stalen beugels verspreidt de laserwarmte zich snel, waardoor de zijbeugels efficiënt worden verbonden", zegt Voithofer.
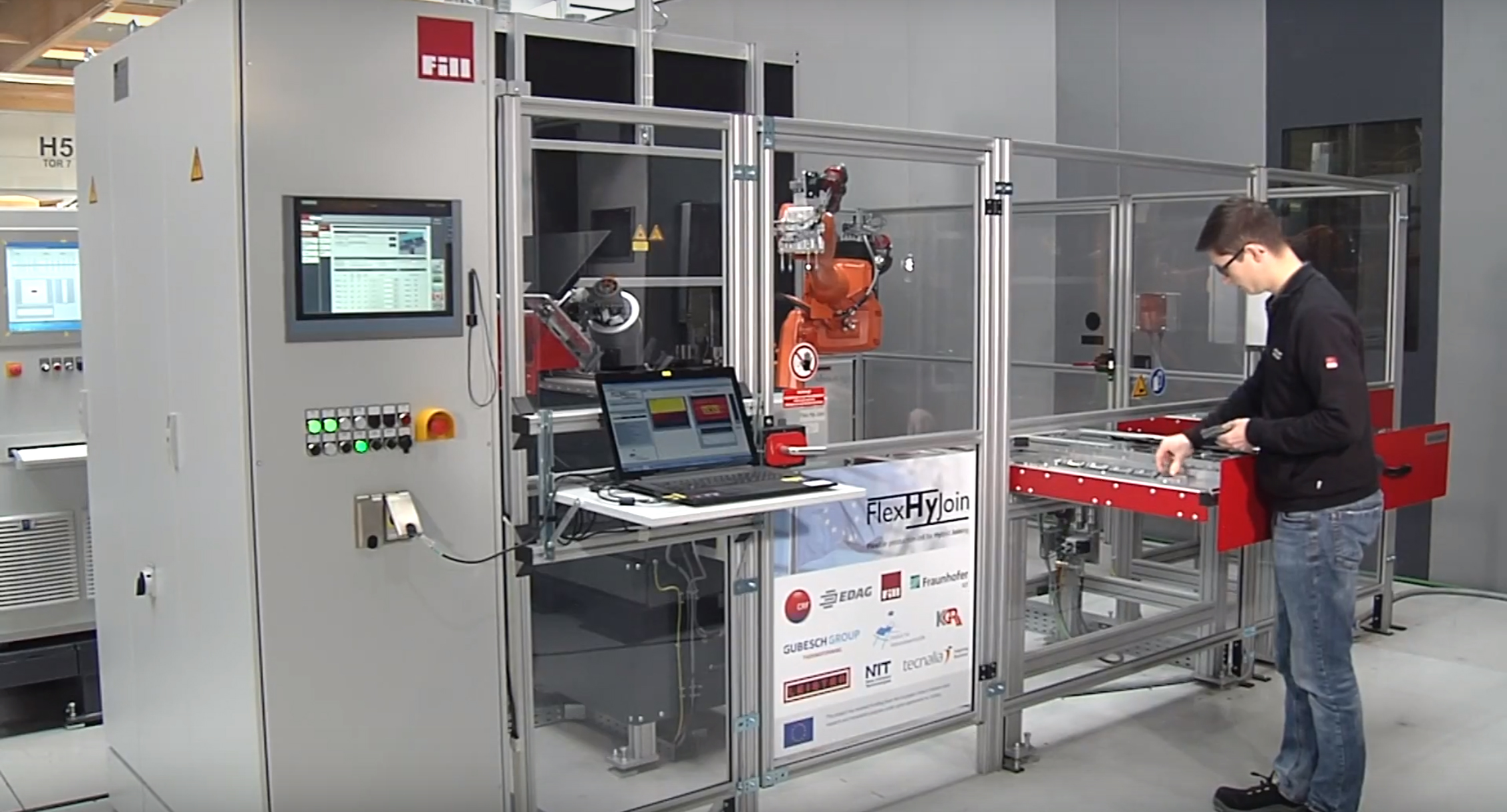
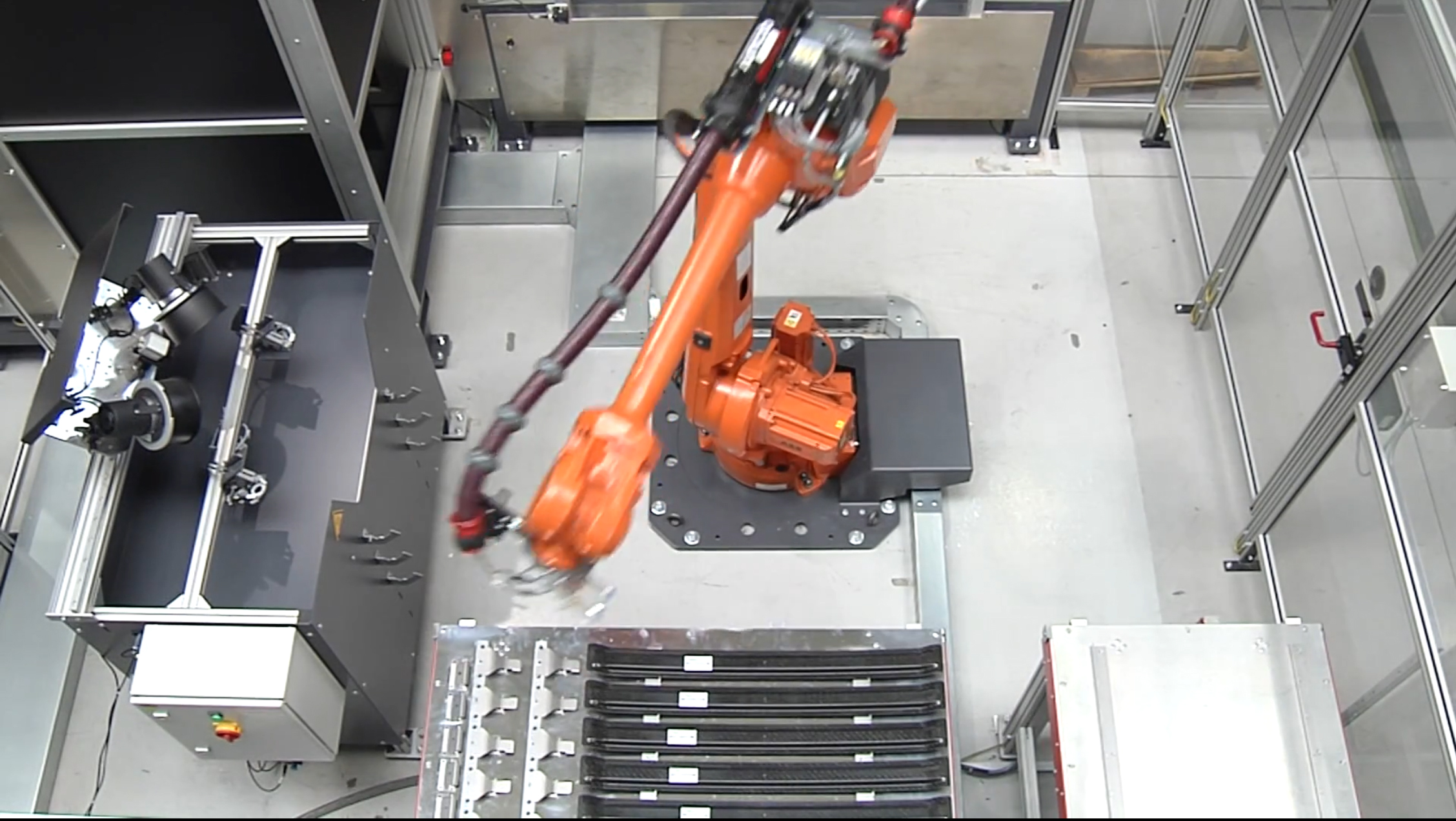
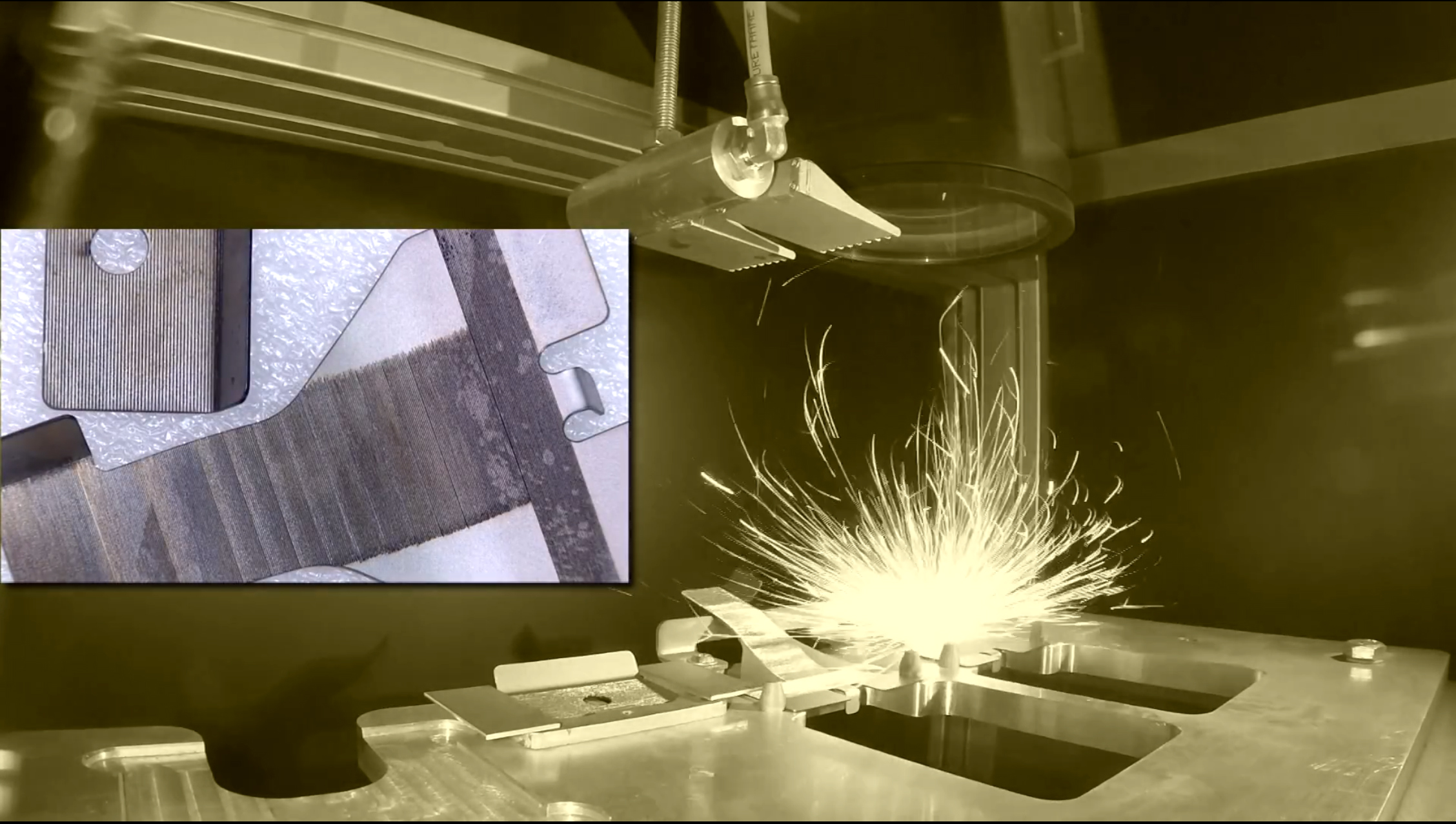
Stap 3. In de structurerende cel creëert een high-power fiberlaser ondersnijdingen in het oppervlak van de beugel die moet worden samengevoegd in de composiet dakverstijver.
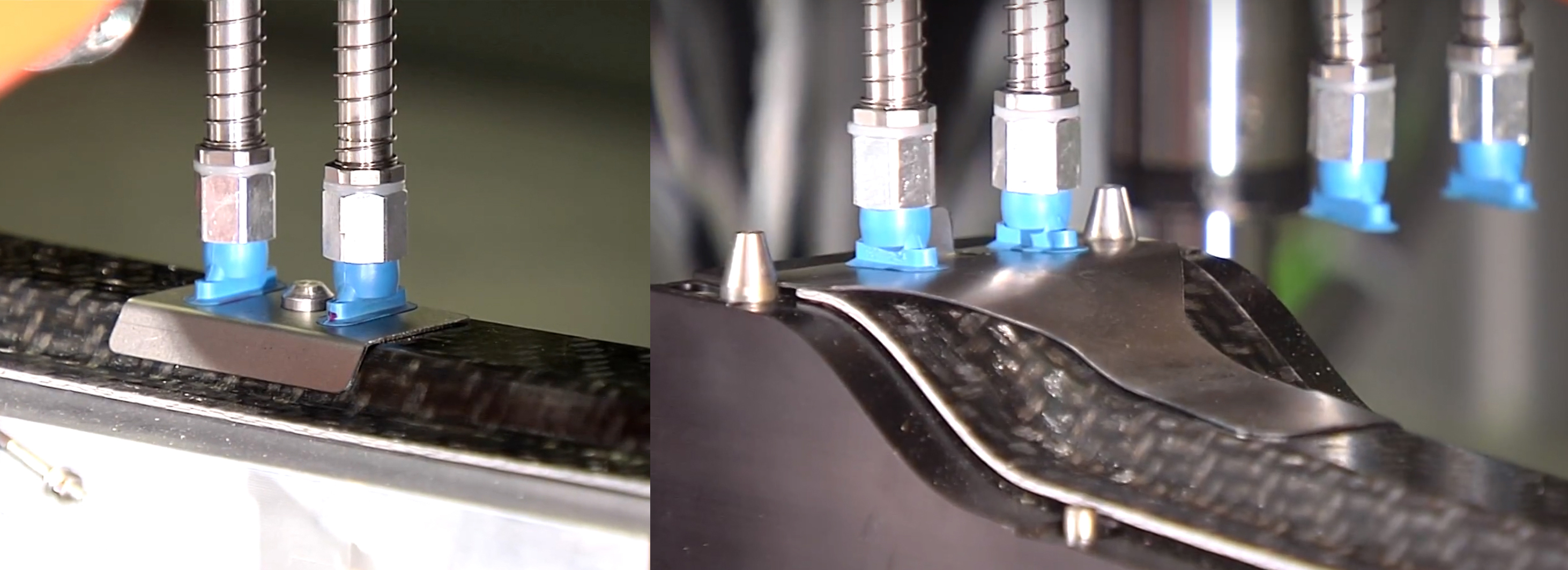
Stap 5. De robot gaat terug naar de structureringscel, pakt de behandelde beugels op en plaatst ze, met de gestructureerde kant naar beneden, op de TPC-dakboog.
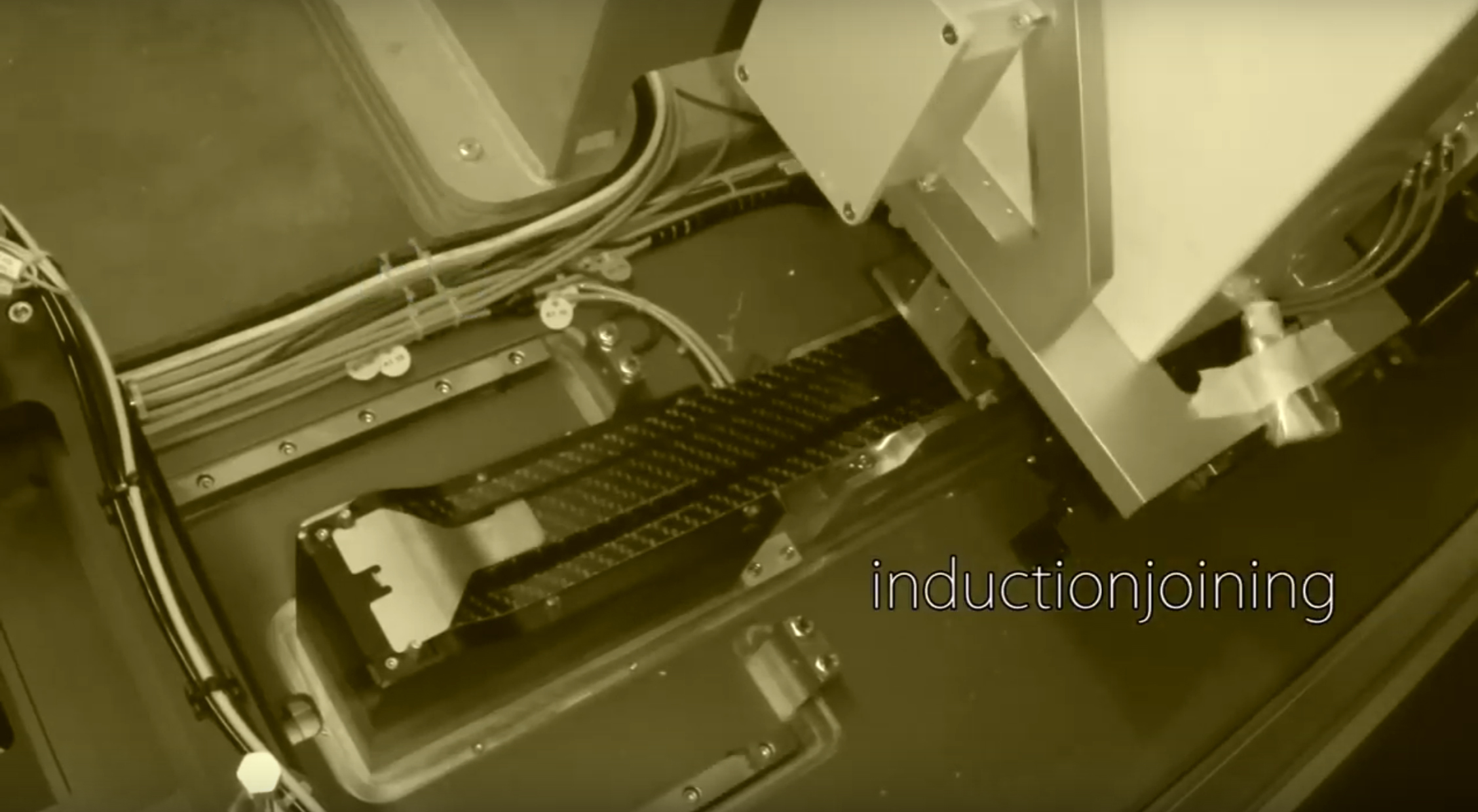
Stap 6. De robot plaatst vervolgens klemunits op de drie beugels. De inductieverbindingseenheid zakt op de middenbeugel. De inductiespoel zorgt ervoor dat de metalen beugel warm wordt, waardoor de PA6-matrix van de onderliggende composiet smelt.
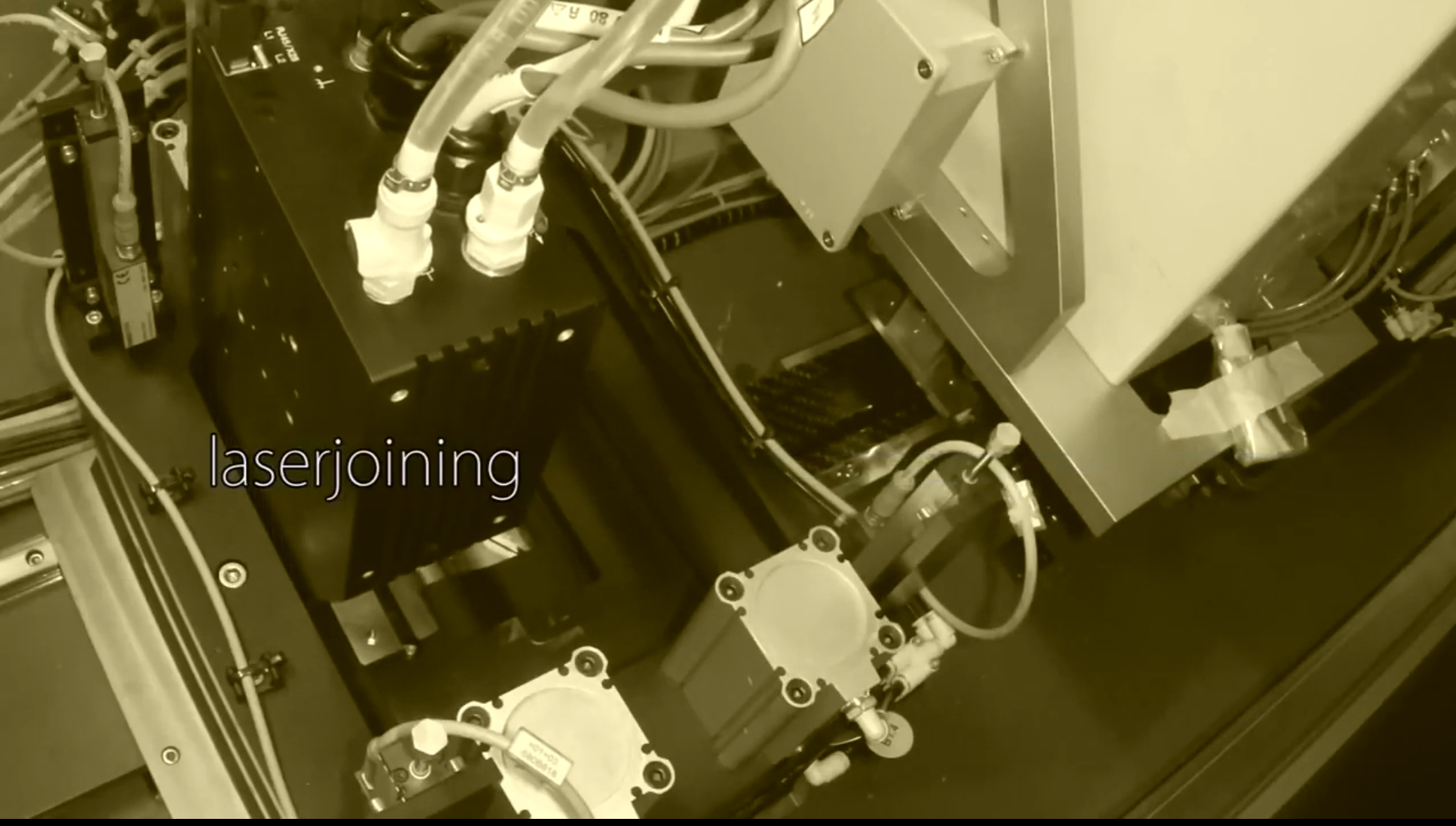
Stap 7. Terwijl de inductieverbinding is voltooid, wordt de laserverbindingseenheid neergelaten om de linker- en vervolgens de rechterbeugel samen te voegen. De laser verwarmt het metaal, waardoor de onderliggende PA6-matrix in de ondersnijdingen smelt, waardoor een zeer sterke verbinding ontstaat.
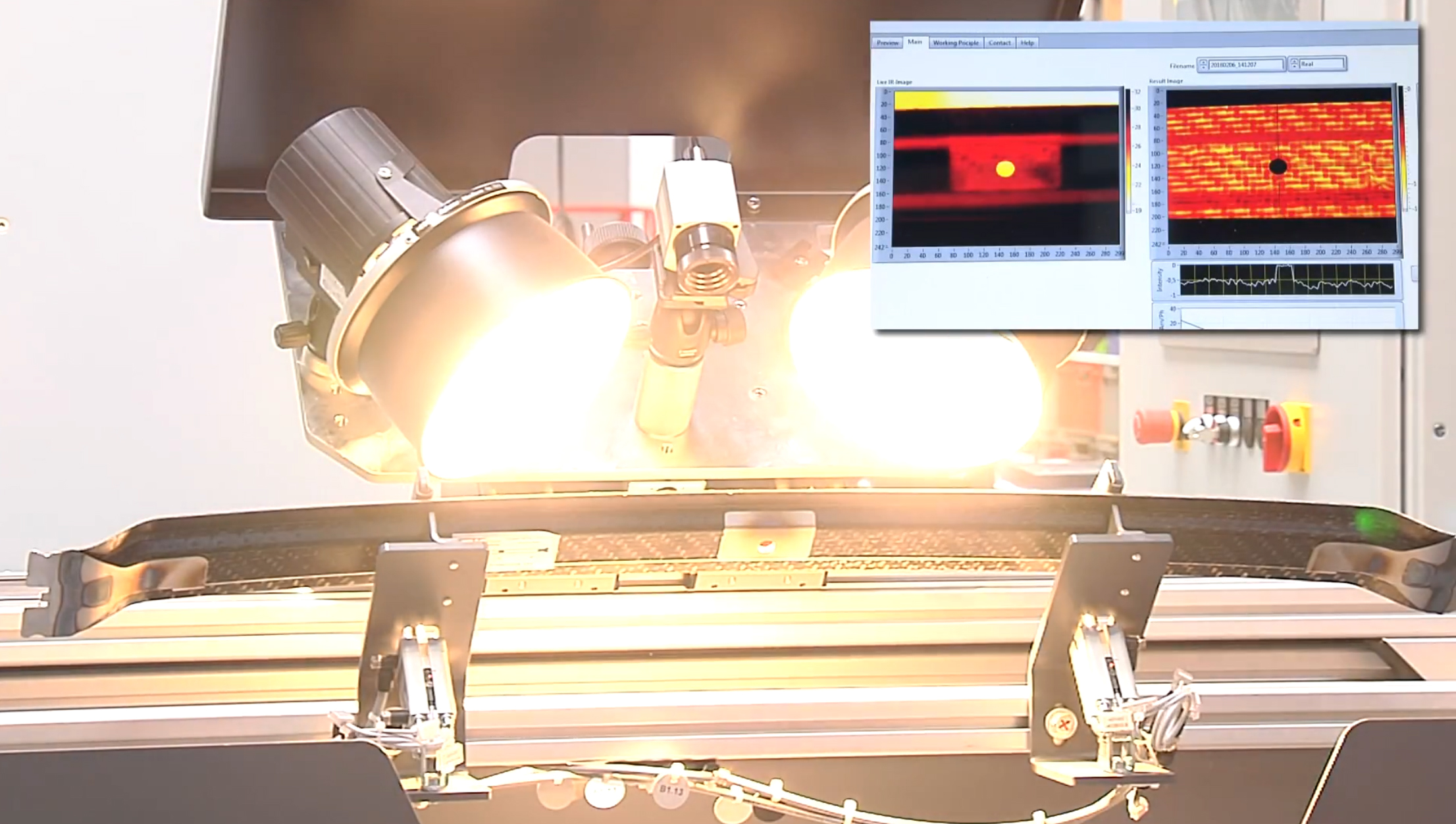
Deelnemen aan procescontrole
De basismethode voor het regelen van beide verbindingsprocessen is het meten van de temperatuur en tijd versus een reeks geoptimaliseerde parameters die door middel van testen zijn gedefinieerd. “Daarom produceerden we samenvoegende testmonsters met verschillende parameters en voerden we mechanische tests uit voor elke parameterset met behulp van speciale testopstellingen. Voor de zijbeugel is een combinatie van een afschuiftest en een afpeltest ontwikkeld, en voor de middenbeugel hebben we een drukbelastingstest gebruikt, vergelijkbaar met een overlappende afschuiftest, maar je duwt in plaats van trekt, om een schuifbelasting te krijgen in het verbindingsgebied”, zegt Popow. De opzet van deze speciale tests is ontworpen in samenwerking met EDAG Engineering GmbH (EDAG, Fulda, Duitsland), die ook de analyse van de testresultaten heeft gedaan. Na deze procedure werd de beste set parameters voor de verbindingsprocessen geïdentificeerd en vervolgens gebruikt in de pilootproductiecel.
"Het inductieverbindingsproces was van tevoren gekalibreerd", zegt Weidmann. “We weten dat we de verbindingstemperatuur na ongeveer 30 seconden bereiken, maar we meten de temperatuur ook ter plaatse om veiligheidsredenen om oververhitting te voorkomen.” Een pyrometer, die op afstand de straling van een oppervlak meet, werd gebruikt om een bekende hotspot in het inductieverbindingsgebied te meten. "Maar het kan geen nauwkeurige metingen van de laserverbinding leveren vanwege het hoge niveau van bestraald licht en warmte ter plaatse", legt hij uit. Contactsensoren kunnen echter worden gebruikt aan de composietzijde van de laserverbindingsgebieden, hoewel ze niet toepasbaar waren voor het inductieverbindingsproces omdat ze doorgaans van metaal zijn gemaakt en door inductie zouden opwarmen en de meting zouden vervormen.
"De verwarmde delen van alle verbindingen worden ook afgedekt door het persgereedschap en de spaninrichtingen", merkt Weidmann op. "Zo hebben we de dikteverandering van het onderdeel als gevolg van druk en hitte voor en na het verbinden gevalideerd als een methode voor kwaliteitsborging." Deze dikteverandering wordt gemeten door een afstandssensor die is geïntegreerd in het positioneringsgereedschap voor de dakverstijver (ook weergegeven in Fig. 3). “Als we de onderdelen tegen elkaar drukken, wordt de afstandssensor verplaatst”, legt hij uit. “Als we warmte en verbindingsdruk toepassen, stroomt het gesmolten matrixpolymeer in de holtes van de laserstructurering en wordt het lichtjes uit de verbindingszone geperst totdat de verbinding afkoelt. Dit leidt tot een verandering in dikte die wordt geregistreerd door de afstandssensor.” Weidmann en het IVW-team hebben deze afstand gecorreleerd aan de kwaliteit van het onderdeel. "Een dikteverandering - met andere woorden een verdichting - van meer dan 0,1 millimeter betekent dat de voegkwaliteit goed is", merkt Weidmann op.
Inline NDT
IVW ontwikkelde een andere methode voor kwaliteitsborging:inline thermografietesten. "Voor kwaliteitsborging was het belangrijkste doel om de eigendommen in het verbindingsgebied te zien", legt Popow uit. "Maar dit was erg moeilijk, dus we voerden thermografie uit aan de composietzijde van de verbindingen nadat het onderdeel was voltooid."
IVW koos voor een actieve thermografietechniek, Lock-In Thermografie genaamd, omdat deze een betere signaal-ruisverhouding biedt dan andere actieve methoden (bijv. Pulsfasethermografie) en ook kan inspecteren op diepere defecten. "Het basisidee is om warmte in de composiet te brengen, die vervolgens in het verbindingsgebied en terug naar het oppervlak wordt geleid", zegt Popow. “Met Lock-in Thermografie wordt het onderdeel geëxciteerd met een gedefinieerde frequentie over meerdere periodes. Vervolgens analyseren we deze reactie in de tijd. Als er gebieden zijn tussen het composietoppervlak en het verbindingsgebied die niet homogeen zijn vanwege een holte of defect, zal dit zichtbaar zijn in de thermische respons.”
De thermische respons wordt vastgelegd als een afbeelding. De punten waaruit deze afbeeldingen bestaan, zijn pixels, een afkorting voor beeldelementen. Elke pixel is ook een meetpunt. Zo wordt het temperatuursignaal voor elke pixel over het hele inspectiegebied geanalyseerd. "Als resultaat krijg je amplitude- en fase-informatie voor elke pixel, en de software reconstrueert dit vervolgens weer tot een afbeelding, die visueel kan worden geïnspecteerd", voegt hij eraan toe. Maar het leverde ook grote sets metingen op voor de 126 geteste onderdelen. "We hebben deze NDO-resultaten gecorreleerd met de resultaten van de mechanische tests die door EDAG zijn uitgevoerd", zegt Popow. Zijn team testte ook het verbindingsgebied na het verwijderen van de haakjes - d.w.z. destructief testen. "We hebben dus drie reeksen testresultaten gecorreleerd en kunnen nu bindingsgebieden met een lage en een hoge sterkte identificeren aan de hand van de visuele analyse van de thermografieresultaten", zegt hij.
Geïntegreerde cel voor massaproductie
Een van de grootste prestaties van FlexHyJoin, zegt Weidmann, is de integratie van alle technologie-eenheden, elk ontwikkeld door een andere projectpartner, in een geautomatiseerde, geoptimaliseerde productielijn. Voithofer, degene die de apparatuur bij Fill integreert, legt uit dat "elke set apparatuur die naar ons werd verzonden, een andere controller gebruikte. Ik moest een master-PLC bedenken om alle verschillende proceseenheden aan te sturen.” Dit omvatte de laserbehuizingen en de handlingrobot van de cel, die werden geleverd door Fill. "Het was ook erg moeilijk om al deze processtappen samen te laten werken, omdat ze verschillende hoeveelheden tijd in beslag nemen", voegt hij eraan toe.
Voithofer begon met het ontwikkelen van een architectuur voor elke proceseenheid en robot, waarbij hij naging hoe deze te positioneren voor de beste flow. "Ons concept was om de drie stations - structureren, verbinden en NDO - modulair te houden, in drie afzonderlijke behuizingen", zegt hij. “Op deze manier konden we losse units eruit halen en ze gebruiken op beurzen of andere demonstratieprojecten, en ze dan teruggeven. De werkcel is dus modulair, maar toch geïntegreerd.”
De decennialange ervaring van Fill in dit soort systeemintegratie voor de productie van seriële composieten heeft geholpen om te bereiken wat Popow ziet als FlexHyJoins grootste prestatie:de overstap van laboratoriumschaal naar industriële schaal. “Wij zijn het eerste consortium dat een dergelijk proces realiseert dat geschikt is voor massaproductie van composieten die aan metaal zijn verbonden”, zegt hij. "Dit proces kan worden gebruikt voor veel auto-onderdelen, zoals stabilisatorstangen, bumpers en deuren", merkt Voithofer op. "Er zijn veel composietonderdelen die aansluiten op metalen onderdelen in een lichtgewicht BIW."
Aanpassing voor meerdere industrieën
Er zijn echter enkele wijzigingen nodig voordat de cel in serieproductie wordt genomen. “We zouden de laserstructurering en verbinding niet langer in aparte behuizingen houden, maar ze combineren tot één”, zegt Voithofer. "Hierdoor zouden de deuren van de behuizing tussen deze processen niet meer hoeven te worden geopend en gesloten, waardoor de cyclustijd wordt verkort." Ook zou hij alle stations lineair op een lopende band met elkaar verbinden. De lijn zou dus continu lopen, waarbij onderdelen worden opgepakt en teruggeplaatst op de transportband voor elk station voordat ze de cel verlaten, klaar voor montage in een BIW. Dit zou de cyclustijd verder verkorten. Bovendien zouden uitgebreide lades die honderden onderdelen kunnen voeden, de lijn in staat stellen om hele ploegendiensten te doorlopen zonder dat herbevoorrading nodig is.
Hoewel deze pilootproductiecel bedoeld was voor de auto-industrie, merkt Popow op dat hij gemakkelijk kan worden aangepast aan de ruimtevaart, sport-/consumptiegoederen en industriële toepassingen. "Dat was eigenlijk een van de belangrijkste richtlijnen", zegt Weidmann, "dat het verschillende geometrieën en onderdelen met elkaar moet kunnen verbinden. De enige verandering zou het inductieverdichtingsgereedschap, de kleminrichtingen voor laserverbindingen en het ondersteunende gereedschap moeten zijn. De belangrijkste delen van de cel moeten hetzelfde blijven.” Hij merkt op dat IVW ook hybride koppeling van titanium en staal aan geweven koolstofvezel/polyfenyleensulfide (PPS) organosheetcomposieten heeft aangetoond en nu polyetheretherketon (PEEK) en polyetherketonketon (PEKK) demonstraties ontwikkelt. "Dit vereist eenvoudigweg het aanpassen van de verbindingsprocessen voor hogere temperaturen en het opnieuw definiëren van optimale procesparameters", zegt Weidmann. "De cel staat open voor een verscheidenheid aan materialen, waaronder aluminium en koper, evenals andere thermoplastische composietmatrixsystemen zoals polypropyleen en polyethyleen."
"De projectpartners hebben goed samengewerkt en zijn verheugd om verder te gaan in de ontwikkeling", merkt hij op. "We denken dat dit soort productie veelbelovend is, en de reacties die we tot nu toe van de industrie hebben ontvangen, laten zien dat er verschillende bedrijven zijn die deze belofte ook zien."
Hars
- Solvay breidt capaciteit thermoplastisch composiet uit
- Synthese en studie van optische kenmerken van Ti0.91O2/CdS hybride bolstructuren
- Oppervlakte-impedantie van meta-oppervlakken/grafeen hybride structuren
- Fraunhofer stelt geautomatiseerde Engel-productiecellen in gebruik voor R&D van thermoplastisch composiet
- Het belang van harskeuze
- DLR Institute of Structures and Design vergroot de maturiteit van thermoplastische composiet rompstructuren
- Gebruiksvriendelijke kits maken reparatie van composietstructuren in het veld mogelijk
- Ontwikkeling van composiet isogrid-structuren met behulp van innovatieve depositietechnologie
- Consortium streeft naar oplossingen voor thermoplastische composietstructuren van koolstofvezel
- Architectonische bekledingscomposiet onthuld
- Composiet + metaal:holle hybride technologie