barrières voor het lichter maken van schepen met composieten
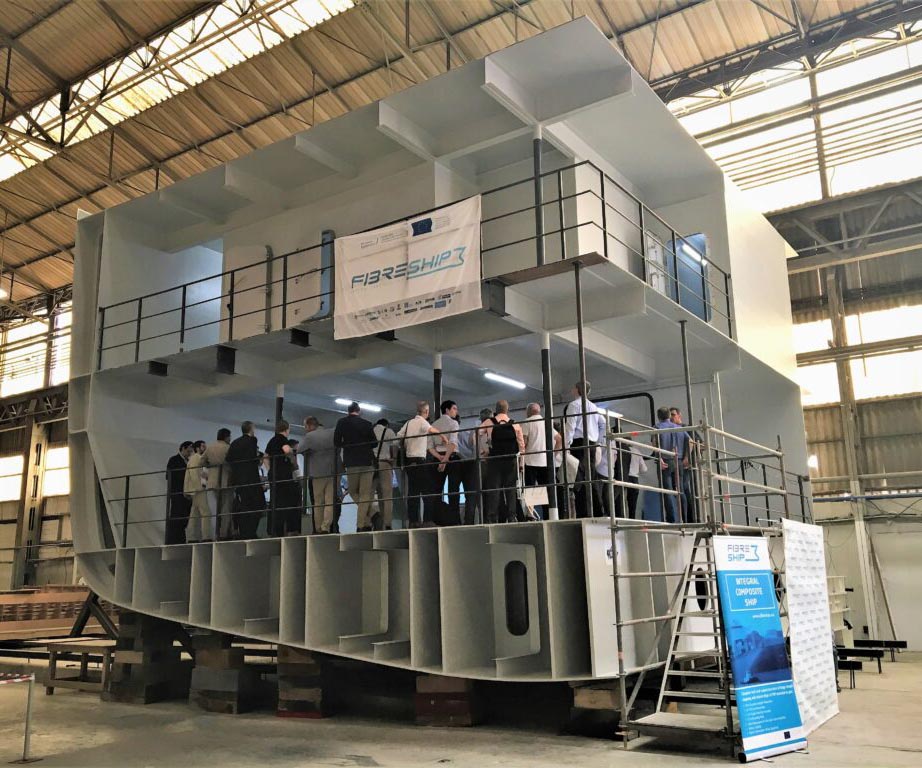
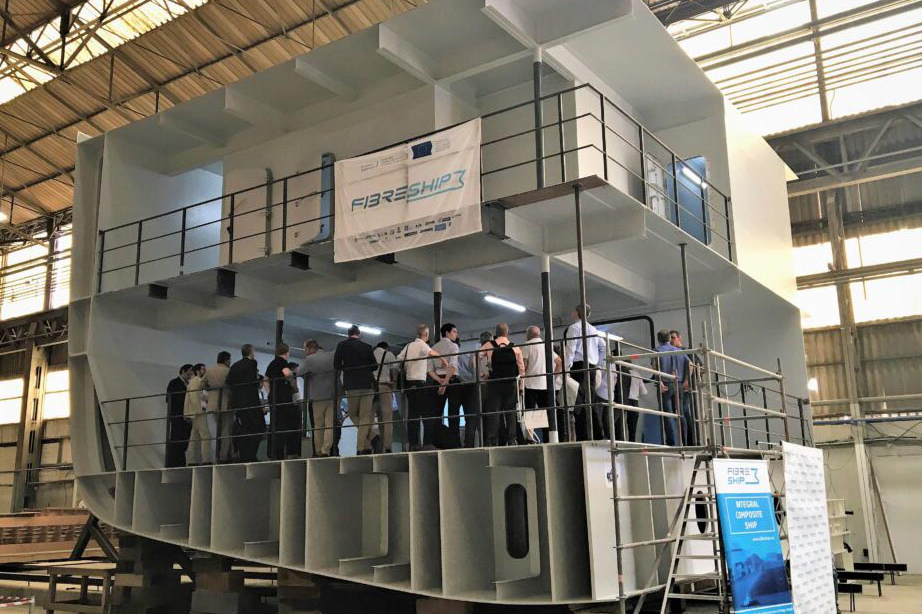
Glas- en koolstofvezelversterkte polymeercomposieten (GFRP en CFRP) worden al tientallen jaren gebruikt om zeeschepen te bouwen, waaronder talloze mijnenjagers van 40 tot 60 meter en zelfs grotere schepen, waaronder de 72 meter lange Visby Class Corvette van de Zweedse marine en het 75 meter lange zeiljacht Mirabella V . Het 141 meter lange motorjacht Swift 141 (omgedoopt tot Yas ) is een Nederlands stalen fregat herbouwd met GFRP/CFRP in onderdekzolen en driedeks bovenbouw (zie "Van fregat tot luxe gigayacht"), inclusief een composiet-naar-staal dekverbinding.
En toch worden composieten zelden gebruikt in de scheepsbouw. Dit is voornamelijk te wijten aan de SOLAS-voorschriften (Safety Of Life At Sea) die zijn uitgevaardigd door de Internationale Maritieme Organisatie (IMO, Londen, V.K.), die voorschreef dat commerciële schepen tot de MSC/Circ in staal moesten worden gebouwd. 1002 is uitgegeven in 2002 en staat alternatieve ontwerpen toe.
“De verordening schrijft voor dat er een risicoanalyse moet worden uitgevoerd, waaruit blijkt dat het alternatieve ontwerp en de alternatieve constructie gelijkwaardig zijn aan staal”, legt Stéphane Paboeuf uit, hoofd van de sectie Composites Materials van het classificatiebureau Bureau Veritas (BV, Nantes, Frankrijk). "Dit proces is lang, duur en de uiteindelijke beslissing kan nog steeds negatief zijn." Dus hoewel composieten veel voordelen bieden voor de scheepsbouw, hebben de uitdagingen op het gebied van brandveiligheid en regelgeving barrières opgeworpen voor het gebruik.
Ondertussen zoeken scheepseigenaren, exploitanten en bouwers naar oplossingen voor meer duurzaamheid, waaronder een lager gewicht om het brandstofverbruik, de uitstoot van broeikasgassen en de diepgang van de schepen te verminderen - de laatste voor ondiepe binnenwateren. De inherente corrosieweerstand van composieten om onderhoud te beperken is ook aantrekkelijk.
In 2017 heeft IMO MSC.1/Circ. uitgegeven, een nieuwe reeks richtlijnen voor het gebruik van composietmaterialen van composiet in commerciële schepen. Nu de IMO-evaluatie van deze richtlijnen in 2021 nadert, vindt er een verbazingwekkende hoeveelheid activiteit plaats. Twee Europese consortia, FIBRESHIP en RAMSSES, ondersteund door het 378 leden tellende Europese netwerk voor lichtgewicht toepassingen op zee (E-LASS), leiden deze golf van demonstratieprojecten, waaronder composiet dekken, roeren, rompen, modulaire cabines en bovenbouw, patch reparaties aan staal en composiet-naar-staal lasverbindingen. Samen willen ze de barrières voor lichtgewicht composiet scheepsbouw overwinnen door niet alleen de brand- en structurele prestaties van grote constructies en hele schepen aan te tonen, maar ook door nieuwe routes te ontwikkelen voor certificering en productiemethoden, nieuwe verbindingstechnologieën en ontwerptools. Ze delen ook informatie via doorlopende workshops, kennisopslagplaatsen en materialen/ontwerpdatabases. Er gaat misschien een nieuwe markt open voor mariene composieten, maar welke oplossingen zijn daarvoor nodig?
FIBRESHIP en RAMSSES
FIBRESHIP en RAMSSES zijn gestart in juni 2017, gefinancierd door het Horizon 2020-programma van de Europese Unie. FIBRESHIP heeft 18 leden en loopt tot mei 2020, terwijl RAMSSES 36 leden heeft en eindigt in mei 2021. Beide omvatten bedrijven uit de hele supply chain van R&D-centra, universiteiten, leveranciers van materialen en technologie, fabrikanten van onderdelen, scheepsarchitecten en ingenieursbureaus, scheepswerven, scheepseigenaren en classificatiebureaus. Deze laatste zijn verantwoordelijk voor het ontwikkelen van specifieke regels voor individuele scheepsbouw op basis van de algemene richtlijnen van de IMO. Ze zijn geautoriseerd door vlaggenstaten (elk schip draagt de vlag van een land) om de scheepsconstructie te controleren en ervoor te zorgen dat deze regels worden nageleefd. "Het is belangrijk dat alle belanghebbenden en eindgebruikers worden betrokken", zegt Alfonso Jurado, hoofd R&D bij Tecnicas y Servicios de Ingeniería (TSI, Madrid, Spanje) en projectcoördinator van FIBRESHIP.
"Het belangrijkste doel van FIBRESHIP is het ontwikkelen van ontwerp- en productiecapaciteit voor grote zeeschepen (meer dan 50 meter lang) met minder gewicht", vervolgt Jurado. “Dit is ook de belangrijkste drijfveer voor mijn bedrijf.” TSI ontwerpt de composietstructuur van een 85 meter lengte over alles (LOA) visserijonderzoeksvaartuig (FRV), dat als demonstratieschip zal dienen en tot nu toe een reductie van bijna 70% in structureel gewicht bereikt ten opzichte van het stalen referentievaartuig. "Dit is verbazingwekkend en biedt de echte mogelijkheid om de scheepvaartsector te helpen", zegt hij. Een sectie van 20 ton van deze FRV, met afmetingen van 11 bij 11 bij 8,6 meter (zie openingsafbeelding), werd gebouwd door scheepswerf partner iXblue in La Ciotat, Frankrijk, en tentoongesteld in de tweede openbare werkplaats van FIBRESHIP in juni 2019 (zie nieuwsbericht met video van de demonstrator die wordt gefabriceerd).
Jurado legt uit dat de FRV de eerste is van drie algemene composiet scheepskoffers die FIBRESHIP aan het ontwikkelen is. De volgende twee zijn LOA-containerschepen van 260 meter lang en ROPAX van 204 meter lang, waarbij de laatste het laadvermogen van een roll-on/roll-off-schip combineert met de passagiersfaciliteiten van een veerboot. "De FRV werd gekozen als demonstratiemodel omdat het kleiner is met een meer conventionele maritieme structuur en dus het meest haalbaar is om in de nabije toekomst te bouwen", zegt hij. “Ook reders hebben oprechte interesse getoond in zo’n schip.” Ondertussen heeft RAMSSES 13 demonstranten in uitvoering, waarvan 10 composieten, en is het ook bezig met een volledig composiet vaartuig.
Jurado merkt op dat de bedrijven die aan deze projecten deelnemen het potentieel zien voor dergelijke nieuwe ontwerpen en nieuwe lichtgewicht producten om een concurrentievoordeel te bieden voor zowel hun bedrijven als de scheepvaartindustrie van elk land. Maar vooruitgang zal niet alleen worden verzekerd door grote demonstranten. "We moeten ook steun krijgen van de regelgevende instanties", voegt hij eraan toe. “Een eerste stap is om de IMO erbij te betrekken en de huidige SOLAS-regelgeving aan te passen aan de nieuwe eisen en eisen van de scheepvaartindustrie. Zonder dit kunnen we niet verder, omdat verzekeringsmaatschappijen de vezelversterkte composietschepen niet zullen verzekeren als ze bijvoorbeeld niet voldoen aan de minimumeisen en de certificering van veiligheid.”
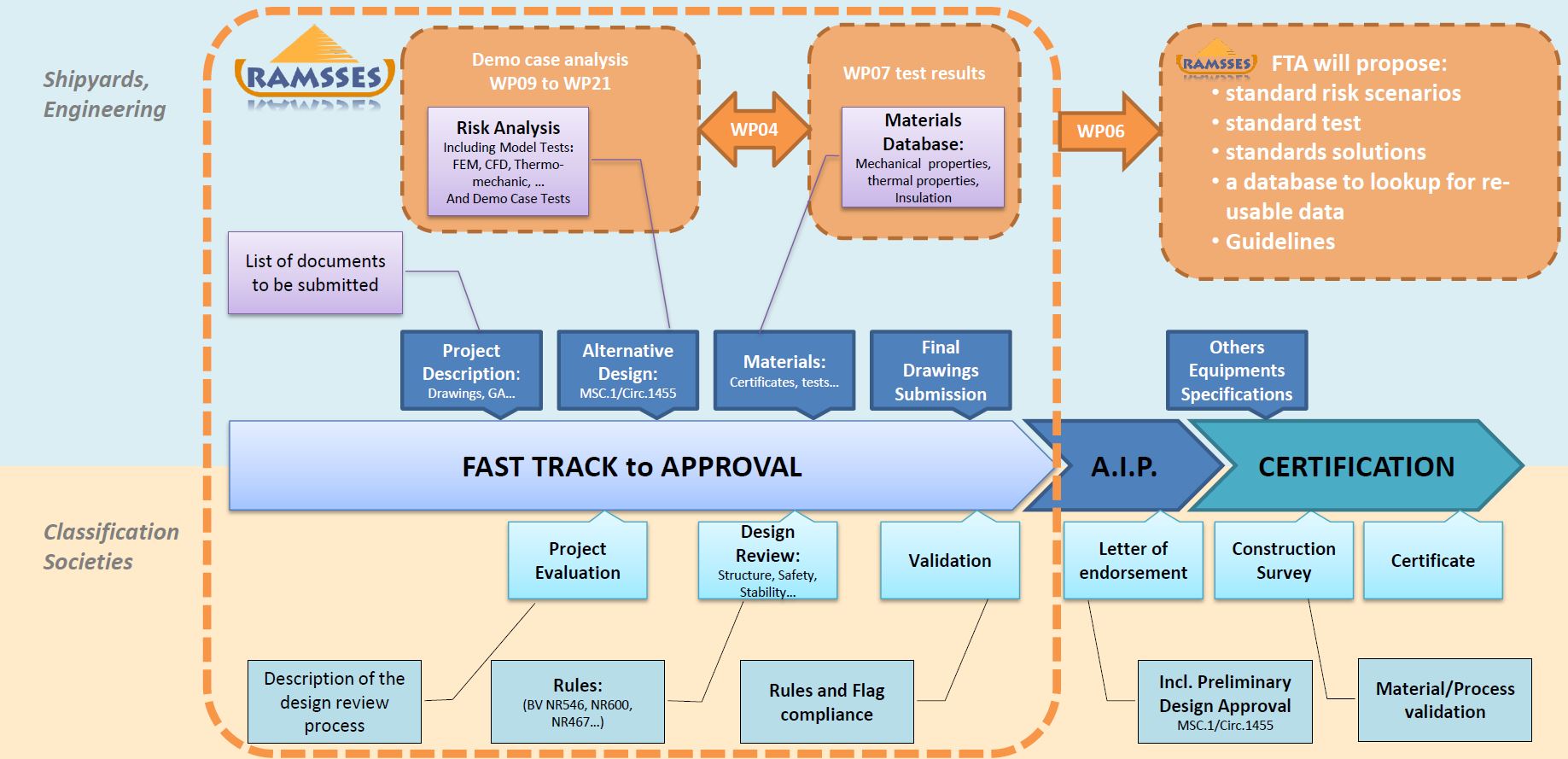
Voorgestelde Fast Track to Approval (FTA)-aanpak voor certificering van composieten in commerciële schepen die wordt ontwikkeld binnen het RAMSSES-project, zoals gepresenteerd tijdens het E-LASS Seminar van juni 2019 (Vigo, Spanje). Bron | RAMSSES en Stephane Paboeuf, Bureau Veritas
"FIBRESHIP streeft naar een langetermijnaanpak door nieuwe regels te ontwikkelen, terwijl RAMSSES een kortetermijnaanpak ontwikkelt door gebruik te maken van bestaande regels en methoden", legt Paboeuf van BV uit, de enige partner van classificatiebureaus in RAMSSES, en een van de drie in FIBRESHIP naast Lloyd's Register (Londen, VK) en RINA (Genua, Italië). "In RAMSSES ontwikkelen we een Fast Track to Approval (FTA)-procedure op basis van hergebruik van projectgegevens om tests te standaardiseren en richtlijnen te geven voor ontwerp en goedkeuring." Deze procedure moet eenvoudig en goed leesbaar zijn voor scheepswerven, scheepsarchitecten en leveranciers. Versnelling versus het huidige proces zal komen door ondersteuning die wordt ontwikkeld in RAMSSES-demonstratieprojecten, waaronder:
- een database met vooraf goedgekeurde oplossingen en materiaaltestresultaten om herhaald testen te voorkomen,
- brandrisicoscenario's voor een reeks vergelijkbare toepassingen om het aantal en de omvang van risicobeoordelingen te beperken, en
- tools voor analyse en modellering, inclusief numerieke of statistische modellen die in de toekomst fysieke tests kunnen vervangen.
"In FIBRESHIP werken we samen met Lloyd's Register en RINA om een reeks prescriptieve regels te ontwikkelen die specifiek zijn voor grote schepen gebouwd met composieten", vervolgt Paboeuf. "Voor structurele prestaties definiëren we nieuwe veiligheidscoëfficiënten voor lokale en globale belastingen." RAMSSES en FIBRESHIP stellen ook voor om de huidige brandklassen zoals A60, B30 en B15 te vervangen door een nieuwe conventie REIxx, waarbij R staat voor brandwerendheid (draagvermogen bij brand), E voor integriteit (voorkomen van rook en vlamverspreiding ) en I definieert brandisolatie. "Het doel is om de structurele brandklassen beter af te stemmen op de gebruikte composietmaterialen", legt Paboeuf uit.
Daarnaast houden de twee projecten zich ook bezig met risicobeoordelingen als gevolg van vlamverspreiding, rookproductie en brandrisico in de ruimte van herkomst, maar ook op het wereldwijde veiligheidsniveau van schepen. "Voor brandprestaties ontwikkelen we een lokale gelijkwaardigheidsaanpak, die brandveiligheid op lokaal niveau behandelt op basis van de brandclassificaties van de schotten en andere structurele scheidingen in elke ruimte van het schip", zegt Paboeuf. “De tweede benadering, globale equivalentie, houdt zich bezig met brand op scheepsniveau, waarbij rekening wordt gehouden met alle systemen (actieve en passieve brandbeveiliging, detectie, evacuatie, enz.) die van invloed zijn op de brandveiligheid van het schip als geheel, niet alleen verdeelde ruimte.”
"Bredere acceptatie van composieten in de scheepsbouw zal stap voor stap plaatsvinden", zegt hij. “Het zal beginnen met kleine onderdelen zoals dekken en bovenbouw, of uitrusting zoals aslijnen en schroeven, voordat het verder gaat met de bouw van hele schepen, die in eerste instantie voornamelijk schepen voor speciale doeleinden zullen zijn, zoals onderzoeks- en seismische testvaartuigen en hogesnelheidsvaartuigen. patrouillevaartuig.”

Afb. 1 RAMSSES 80 meter lang composiet vaartuig
Damen Shipyard (DSNS) ontwikkelt een volledig composiet offshore patrouillevaartuig in het RAMSSES-project. De 6 bij 6 bij 3 meter grote rompsectiedemonstrator zal in 2020 worden gebouwd met behulp van harsinfusie in samenwerking met InfraCore Company (ICC) en Airborne International (AIR). Bron | Damen Shipyard en RAMSSES
Alle composiet vaartuigdemonstraties
Naast de 85 meter lange FRV die door FIBRESHIP wordt gedemonstreerd, wordt binnen RAMSSES een 80 meter lang offshore patrouillevaartuig ontwikkeld om het eerste volledig samengestelde SOLAS-schip te worden. Onder leiding van Damen Shipyard Group (Gorinchem, Nederland) draagt dit werk de resultaten van het Bluenose-project dat in 2014 is gestart voort. Binnen RAMSSES werkpakket 17 leidt Damen de demonstratie van een 6-bij-6-bij-3-meter full- composiet rompgedeelte van dit schip gemaakt met behulp van vacuüminfusie, legt Matthias Krause uit, R&D-ingenieur bij het Center of Maritime Technologies (CMT, Hamburg, Duitsland) en co-coördinator van het RAMSSES-project samen met CETENA (Genua, Italië). “Evonik heeft een nieuwe hars ontwikkeld voor dit deel van de demonstratieromp en er is gereedschap van 6 meter hoog gefabriceerd. Damen werkt ook samen met Airborne International (Den Haag, Nederland), een leverancier van de vliegtuigindustrie die ook grote geïnfuseerde constructies heeft gebouwd.” Evonik (Essen, Duitsland) heeft zijn rol uitgelegd om de slagvastheid en het vermoeidheidsgedrag van de met glasvezel/vinylester doordrenkte romp te verbeteren.
Een andere partner in deze demonstrator is InfraCore Co. (Rotterdam, Nederland), dat nieuwe toepassingen ontwikkelt voor de InfraCore-technologie die wordt gebruikt door zusterbedrijf FiberCore Europe (Rotterdam) in meer dan 1.000 composietbruggen en sluisdeuren wereldwijd. “Oorspronkelijk waren we bij Damen betrokken bij dit project om een helikopterdek van 12 tot 14 ton te bouwen”, legt InfraCore operations manager Laurent Morel uit. “We werken nu met hen samen om de dekken, schotten en rompconstructie te bouwen. We zullen zowel horizontale als verticale infusie gebruiken om het rompgedeelte in één keer te produceren. Tot nu toe hebben we tot een hoogte van 9,8 meter geïnfuseerd.” Eenmaal voltooid, zal deze demonstrator worden getest op structurele en brandprestaties, waarbij de resultaten en geleerde lessen worden ingevoerd in de nieuwe FTA-modules van RAMSSES.
Lichtgewicht decks
Composieten zijn al gedemonstreerd in de eerste roll-on/roll-off auto-carrier die gebruik maakt van een composiet vrachtdek, ontworpen en gebouwd door Uljanik Group (Pula, Kroatië) als onderdeel van RAMSSES werkpakket 14 (zie “Laag gewicht op de hoge zeeën"), evenals een lichtgewicht zonnedek voor een 110 meter lang riviercruiseschip (zie "Samengesteld dek vermindert de diepgang van rivierschepen") en een composiet tussendek voor een 200 meter lang stukgoedschip. "Een tussendek is een verwijderbaar dek dat u kunt installeren om het laadruim te verdelen om verschillende soorten lading te vergemakkelijken", legt Arnt Frode Brevik uit, manager bij Compocean (Sandvika, Noorwegen), een leverancier van composietoplossingen die voortkwamen uit de olie- en gasindustrie. industrie.
"We werken al enkele jaren samen met Oshima Shipbuilding (Nagasaki, Japan) en DNV GL om een lichtgewicht tussendek te ontwikkelen met als doel het gewicht met 50% te verminderen ten opzichte van staal", zegt Brevik. Dit resulteerde in een GVK-prototype van 9 bij 2 meter dat werd getest op impact en maximale belastingen en vervolgens werd tentoongesteld op NOR-Shipping 2017.
Compocean heeft deze ontwikkeling nu uitgebreid tot een nieuw project met Oshima, DNV GL en scheepseigenaar Masterbulk Pte Ltd. (Singapore) om een volledig prototype composiet tussendek van 27 bij 12 meter te bouwen, dat volgend jaar zal worden geïnstalleerd en getest tot eind 2021.
"Oshima probeerde artikelen te optimaliseren om de brandstof- en handlingkosten te verlagen", zegt Brevik. "Hoewel er niet veel tussendekken per schip zijn, is het een gemakkelijk onderdeel om mee te beginnen bij het introduceren van nieuwe materialen, omdat het geen deel uitmaakt van de primaire structuur van het schip." Het ontwerp is gebaseerd op een met polyesterhars doordrenkte glasvezelplaat met daaronder hoedverstevigers. “We gebruiken een mix van ±45-graden, 0-graden en 0-graden/90-graden lay-up voor alle onderdelen, maar in verschillende verhoudingen. De dekstructuur moet ook veel sjorpunten integreren om de lading vast te zetten.” De plaat wordt met een structurele lijm aan de hoedverstevigers verlijmd, terwijl bouten worden gebruikt in combinatie met het sjorsysteem. Een geboute stalen eindbeugel verbindt het composiet met de stalen scheepsconstructie. "In de toekomst zullen we ook een ontwerp nastreven met puur lijmverbindingen", voegt Brevik toe.

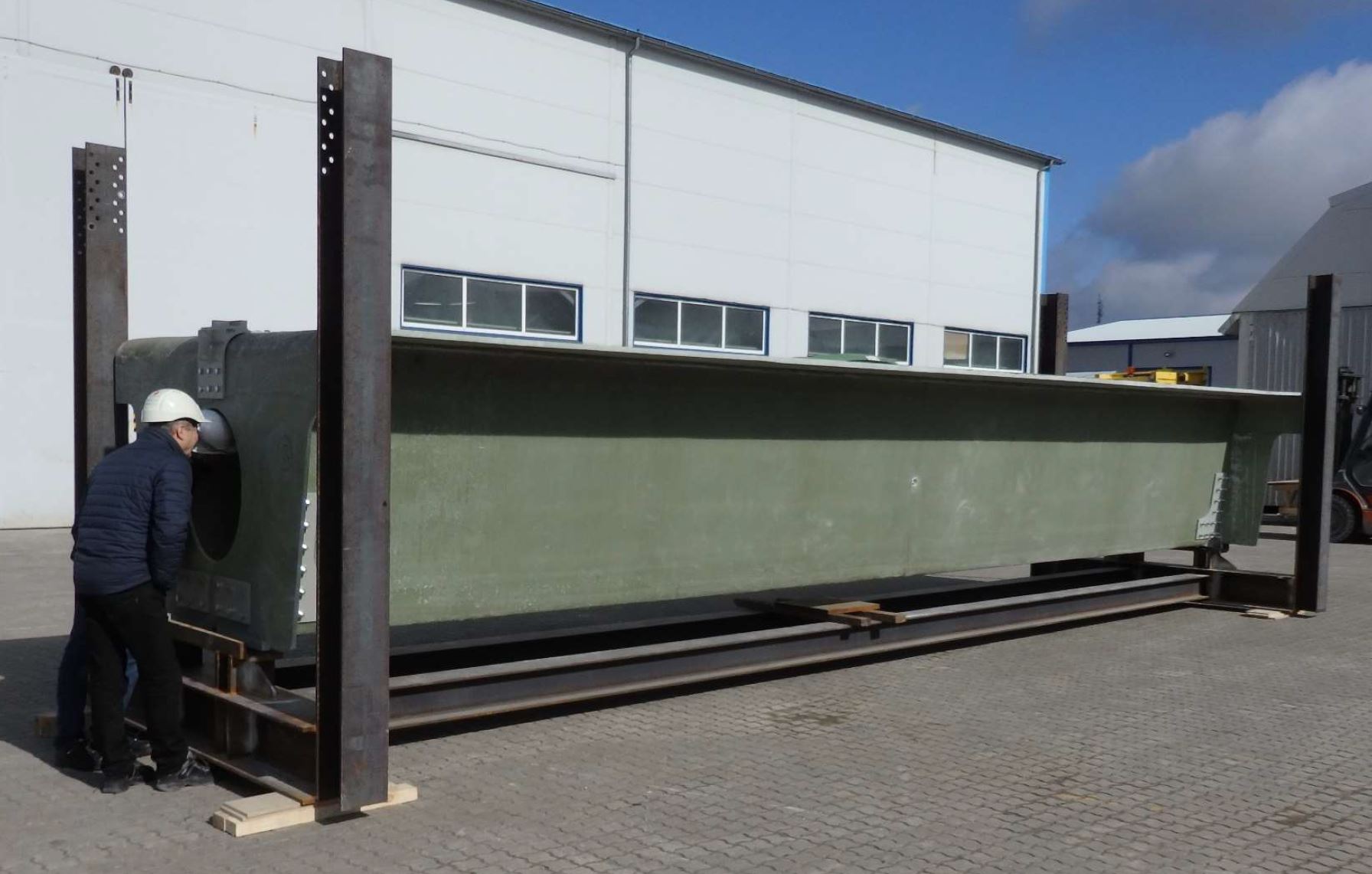
Afb. 2 Composiet tussendek
Het nieuwe 65k open-hatch algemene vrachtschipontwerp van Oshima Shipbuilding maakt gebruik van Compocean's prototype composiet tussendek, dat 50% gewicht bespaart ten opzichte van staal en zal bestaan uit meerdere geïnfuseerde FRP-hoedverstijvingen (inzet) gebonden aan een FRP-bovenplaat met boutverbindingen van het composiet tot de stalen scheepsconstructie. Bron | Compocean en DNV GL
Na de definitieve goedkeuring van DNV GL voor het volledige ontwerp van het tussendek, heeft Compocean de mallen geproduceerd en is begonnen met het testen van de fabricage. “Het composietdek op ware grootte zal worden gebouwd door een partner in Maleisië, die het per binnenschip naar het schip zal vervoeren”, zegt Brevik. De volgende stap is om te streven naar veel meer gewichtsreductie, bijvoorbeeld composiet luiken bovenop laadopeningen (platte platen bovenop groene “dozen” in scheepsweergave hierboven). "Er zijn zeven grote luiken op dit type bagagedrager", merkt hij op. "Om deze goedgekeurd te krijgen door DNV GL zal een aantal nieuwe uitdagingen met zich meebrengen, maar succes met het tussendek zal helpen."
Lichtgewicht bovenbouw, modulaire cabines
RAMSSES heeft zes werkpakketten gericht op composiet bovenbouw en componenten die boven het hoofddek worden gebruikt, de meeste met demonstrators en testresultaten die in 2020 worden gepresenteerd. Werkpakket 16, geleid door Naval Group (Parijs, Frankrijk), demonstreert een lichtgewicht composiet bovenbouwmodule verbonden met een stalen dek. De op de wal gebaseerde demonstrator vertegenwoordigt een standaardblok voor een offshore patrouillevaartuig. "Scheepsbouw in metalen materialen is gebaseerd op constructie in blokken om tijd en kosten te verminderen", legt Jurado uit. "Het bouwen van dergelijke blokken met composieten brengt problemen met zich mee met de noodzaak van grote mallen, verbindingstechnieken en veiligheidsvereisten voor verbindingen. Fibreship heeft dit bestudeerd en enkele aanbevelingen ontwikkeld voor het verbinden van op composiet gebaseerde blokken, inclusief de montagevolgorde.” In RAMSSES heeft Naval Group drie soorten sandwichconstructies onderzocht, waaronder GF/polyester/balsa-kern, FR epoxy/PET-schuimkern en GF/polyester/3D vezelversterkte schuimkern. Het ontwikkelt ook een structureel gezondheidsmonitoringsysteem (SHM) in de voeg- en composietpanelen.
Werkpakket 18, onder leiding van Chantiers de l'Atlantique (Saint Nazaire, Frankrijk) ontwikkelt een modulaire oplossing voor passagierscabines. "Deze hebben meestal geen vloer omdat ze op de stalen dekken van het schip zijn gelast", zegt Krause. "Het idee is om ze te maken van composieten, vooraf uitgerust met alle hulpsystemen zoals verwarming en lucht, elektriciteit, enz. Door een composietvloer op te nemen, kunnen deze in een stalen frame (zoals een lade) worden geplaatst in plaats van te lassen op een solide stalen dek, waardoor veel gewicht wordt bespaard.” Hoewel het project composieten beoordeelt om de productie- en montagetijd voor wanden, plafonds en badkamerunits te verminderen, omdat het vervangen van het stalen dek naar schatting 125 kilogram per vierkante meter zou besparen, zijn composietvloeren een belangrijk aandachtspunt. Hutchinson (Parijs, Frankrijk) heeft voorgesteld om zijn ZALTEX mineraalvezelversterkte composietschuim te gebruiken, dat bestand is tegen temperaturen van -190°C tot 1.000°C.
Werkpakket 13, onder leiding van cruiseschipbouwer Meyer Werft (Papenburg, Duitsland), is ook gericht op efficiënte processen voor assemblage, maar dan op schotten. . Het doel is om twee demonstrators te bouwen - een onshore en een offshore (proef op zee) - waar composietwanden worden verbonden met stalen frameconstructies en vervolgens worden onderworpen aan 80 mechanische tests. Projectpartner InfraCore heeft analyses uitgevoerd om eisen te definiëren voor warmte- en geluidsisolatie, eigenfrequentie (trillingen), vervorming en maximale breedte en hoogte voor composietwanden. “We zijn gevraagd om multifunctionele binnen- en buitenwanden te ontwikkelen”, legt Morel van InfraCore uit. “Om tijd, kosten en gewicht te besparen, moeten we isolatie en een goede binnenafwerking integreren met het lichtgewicht structurele paneel. Er zijn tot 6800 vierkante meter van deze muren op elk cruiseschip. We hebben een opening om deze medio 2020 aan boord van een cruiseschip te plaatsen, wat mogelijk de eerste SOLAS-goedgekeurde composietwanden op een cruiseschip wereldwijd zijn.”
In werkpakket 10 ontwikkelt Podcomp (Öjebyn, Zweden) een alternatief binnen-/buitenpaneel met behulp van biobased composieten die brandvertragend en scherp geprijsd moeten zijn. Drie sandwichconcepten op basis van GF/polyfurfurylalcohol (PFA) prepreg van Composites Evolution (Chesterfield, U.K.) en verschillende kernmaterialen werden onderzocht. Slechts één concept doorstond de kegelcalorimeter en andere brandtesten uitgevoerd door RISE Research Institutes of Sweden (Borås). Het wordt nu geoptimaliseerd voor gewicht en kosten.
Na het proberen van aluminium en wrijvingsroerlassen, gaat Baltic Workboats (Nasva, Estland) nu verder met composieten om voorgemonteerde, verstevigde panelen te ontwikkelen voor het dekhuis/de bovenbouw van aluminium werkboten (werkpakket 15). Paneelontwerp, verbinding met andere panelen en met de rest van de dekhuisstructuur, structurele analyseprocedures en isolatieoplossing zullen worden gedemonstreerd, evenals installatietechnieken aan boord.
Een andere oplossing voor lichtgewicht bovenbouw wordt ontwikkeld door BaltiCo (Hohen Luckow, Duitsland), een producent van scheepsuitrusting die een nieuwe start-up heeft om complete boten te bouwen met behulp van in een robot geplaatste koolstofvezel die rond de spantstructuur is gedrapeerd. "Je bouwt het skelet van de structuur die je wilt produceren, plaatst GFRP-kruisstructuur of ribben ongeveer elke halve meter, en dan windt een robot koolstofvezel eromheen", legt Krause uit. Het doel is een ultralicht modulair systeem dat gebruikmaakt van een sterk geautomatiseerd proces. De demonstratie omvat de productie en montage van twee zelfdragende romp- en dekmodules in een niet-SOLAS lichtgewicht catamaran op zonne-energie.
Gelaste FRP-stalen verbindingen
"Wij geloven dat de toekomst van de scheepsbouw ligt in het combineren van FRP-composieten, staal en andere materialen tot hybride constructies", zegt Dr. Lars Molter, een 10-jarige veteraan bij CMT. “We hebben gekeken naar verlijming, maar er is geen gestandaardiseerd voegontwerp dat je op alle schepen kunt gebruiken en er zijn geen algemene regels voor het aanbrengen van lijmverlijming in SOLAS-schepen. Ook moet je de omgeving en het bindingsproces beheersen.” Hij merkt op dat dit moeilijk is te midden van het lassen en snijden dat typisch de scheepswerfbouw domineert. "We hebben DNV GL gevraagd wat zij zouden goedkeuren voor verbindingen van ongelijksoortige materialen", zegt Molter. "Ze zeiden dat de primaire structuur doorgaans een mechanische bevestiging vereist; pure verlijming zou niet gemakkelijk worden gecertificeerd zonder overtollige bevestigingsmiddelen.”
Molter en CMT reageerden met het door Duitsland gefinancierde FAUSST-project (Fiber and Steel Standard Joint), dat een hybride gebreide stof ontwikkelde die overgaat van 100% glasvezels naar 100% staalvezels. Deze laatste wordt gelast aan een stalen verbindingsstuk (bijv. vlakke plaat, rechthoekig profiel, enz.), die vervolgens gemakkelijk in de staalconstructie van een schip kan worden gelast (Fig. 3). Het glasvezeluiteinde wordt met behulp van harsinfusie met de composietstructuur verbonden. "Dit verbindingsontwerp biedt 100% NDT-inspectie omdat je UT (echografie) of röntgenfoto's op de las kunt gebruiken", zegt Molter. FAUSST voerde mechanische, milieu- en vermoeiingstests uit op dit type verbinding en kreeg ook in principe goedkeuring van de classificatiebureaus, maar er was nog veel werk te doen om de technologie om te zetten in een commercieel product. Zo verliet Molter CMT en richtte in 2018 HYCONNECT GmbH (Hamburg, Duitsland) op.
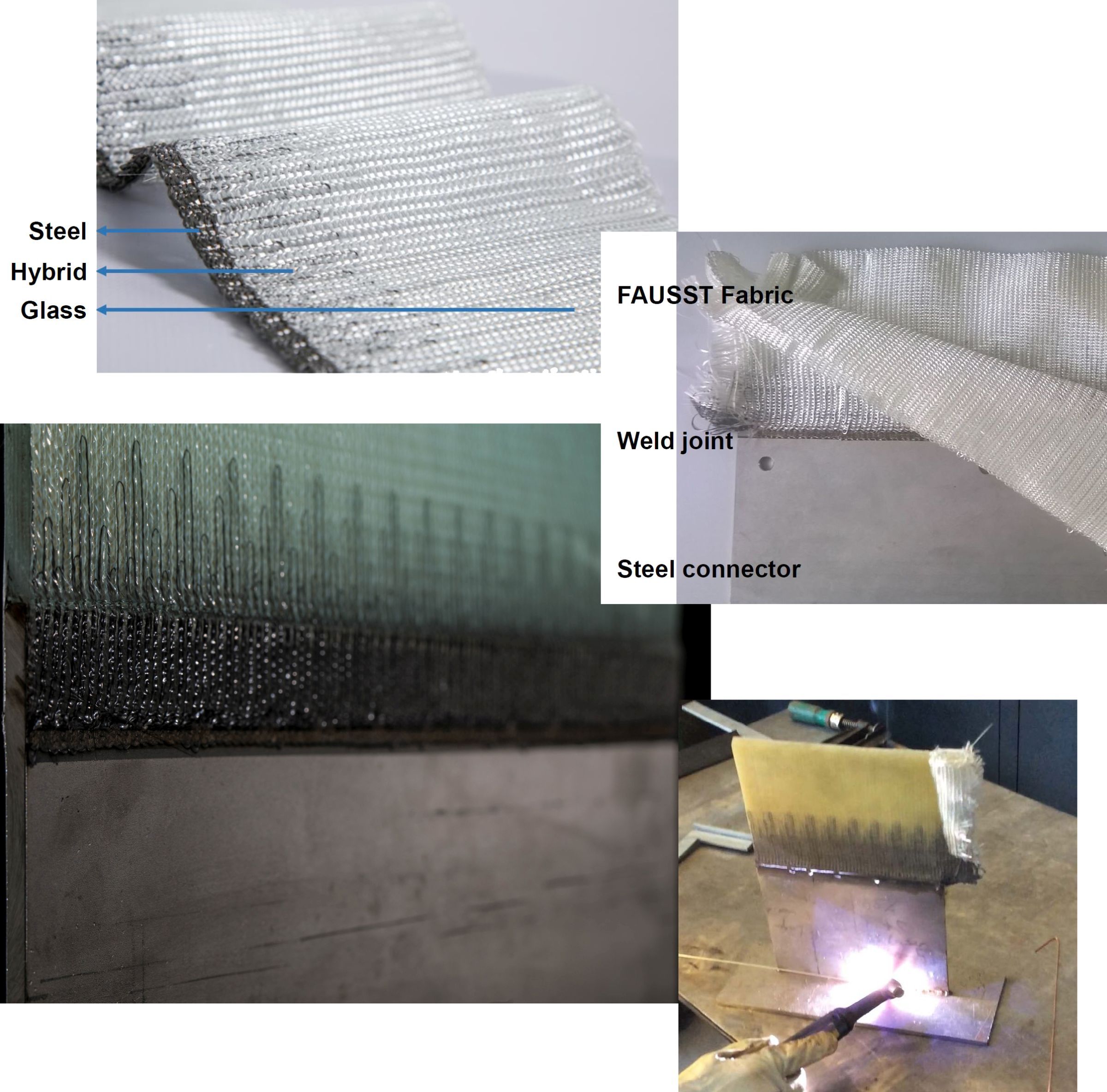
Afb. 3 HYCONNECT gelaste staal-FRP verbinding
FAUSST hybride staal-glasvezelweefsel (linksboven) is gelast aan een stalen plaat of andere connector (rechtsboven) en kan vervolgens worden geïntegreerd in een composietstructuur via harsinfusie (linksonder) . Dergelijke hybride composietconstructies worden vervolgens eenvoudig in stalen scheepsframes gelast (rechtsonder) .
Bron | HYCONNECT
“We hebben een ontmoeting gehad met scheepswerven, DNV GL en BV en ontwikkelen een product dat gecertificeerd kan worden”, zegt Molter. “Met dit verbindingssysteem bestel je eenvoudig je composietdelen en dan kun je ze in je schip lassen. Dat is onze visie. We ontwerpen de verbinding van composiet naar staal en leveren vervolgens een product dat is gelast aan een stalen verbindingsstuk (plaat, profiel, enz.).”
Hij legt uit dat het ontwerp van de verbinding en de stof in een stapsgewijs systeem zullen worden gecertificeerd:"Door meer lagen FAUSST-stof aan te brengen, is er een lineaire toename van het draagvermogen." Het basisproduct kan bijvoorbeeld bestaan uit vier lagen FAUSST waaraan een platte staaf van 1 meter is gelast, geschikt voor een bepaalde trek- en buigbelasting. Dan zijn er links (bijv. twee tot drie lagen in totaal voor een lagere belasting) en rechts (bijv. zes lagen in totaal voor een hogere belasting) enkele producten beschikbaar. “We are still finalizing these details, but the goal is a standardized and easy-to-use system,” notes Molter.
HYCONNECT has adapted the fabric technology to handle the difference in stiffness and coefficient of thermal expansion (CTE) between steel and composites; the use of knitted fibers for mechanical interlocking with unidirectional fibers for carrying load through the joint; and the technique required for high-quality press welding of the steel fibers to the steel connector (see "Connecting composites to steel”). “This solution is based on continuous testing,” says Molter. “Because FAUSST consists of standardized ready-made sub-products, it can be supplied quickly, within days.” Prototypes are currently being produced for selected customers, and HYCONNECT will begin full production in 2020.
Composite rudders
Ship rudders are also being developed as FRP-steel hybrids. As part of RAMSSES work package 12, Becker Marine Systems (BMS, Hamburg, Germany) is demonstrating a lightweight composite flap for a steel rudder designed for large container ships. Such rudders typically weigh more than 200 tons, says Jörg Mehldau, head of R&D at BMS. “By adding a hinged aft flap, you can significantly reduce the rudder area.” BMS pioneered this flap rudder, which dramatically reduces ship turning radius and improves course-keeping and maneuverability, enabling berthing without tugboat assistance. A composite flap not only reduces weight but also enables more functional shapes as well as more hydrodynamically- and load-optimized designs.
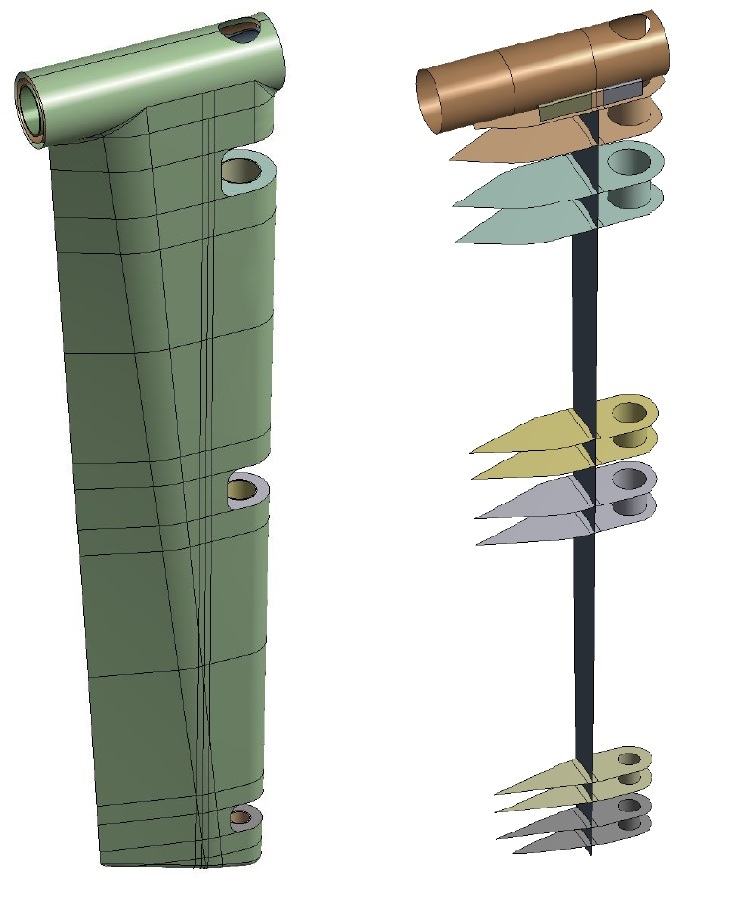
Afb. 4 Composite rudder flap
Becker Marine Systems is working with InfraCore to develop a lightweight, resin-infused rudder flap for the largest container ships. Measuring 11.8 meters long and 0.9 meter wide with a 2.9 meter chord, the full-scale flap must withstand 100 tons/m
2
of load. A 2-meter high demo will be tested 2Q 2020. Source| Becker Marine Systems
“The composite flap we are developing was inspired by the aviation industry,” notes Mehldau. For RAMSSES, the full-scale test case is aimed at one of the largest container ships (≈400 meters long), a flap measuring 11.8 longmeters and 0.9 meters wide with a chord of 2.9 meters (see Fig. 4). “We calculated the forces on this rudder and flap using formulas based on DNV GL rules for this ship’s type, weight and maximum speed,” says Mehldau. BMS then conducted preliminary design and engineering analysis, as well as trade studies for manufacturability and cost. “We first favored filament winding but it was too expensive,” he notes. “For each new ship hull, the rudder is a single design.” Thus, resin infusion was chosen, as was an alternative design from InfraCore. “It was the best for production flexibility, cost and structural performance combined,” Mehldau explains.
“To me, this was a natural fit for InfraCore because the composite lock gates we have built are very similar,” says Morel. He notes container ship rudders must withstand loads of roughly 100 tons per square meter with a surface area of 150 square meters. This matches well with InfraCore’s infusion-based technology used in bridge decks spanning up to 142 meters. Instead of bonding a high-density structural core to faceskins, InfraCore uses a low-density foam core only as a permanent formwork for multiple Z-shaped, two-flanged web structures. These are overlapped, faced with multiaxial fabrics and co-infused to form a robust construction. InfraCore will build a 1:6 scale demonstrator, using glass fiber and polyester resin materials already certified by DNV GL to keep costs low.
Morel notes that the reduced-weight InfraCore composite flap is cost-competitive, “because steel ship rudders are quite complicated to manufacture.” Mehldau agrees, “together with less maintenance and operational cost advantages, we see a successful business case.” The 2-meter -high demonstrator will be finished by 2Q 2020, followed by testing.
“We will test this using a lab test bench and air cushions, which can apply up to 8 bar of pressure equal to at least 80 Mpa of load,” says Mehldau. “We will measure strains and deflections to verify our simulations and perform a break load test.” A lab-scale demonstrator will also be tested via sea trials on a research ship in the Elbe River by CETENA (Genoa, Italy) which serves as project coordinator for RAMSSES along with CMT.
Forward momentum
“The outlook for composites in ships is good because many of the marine sector stakeholders have shown interest in FIBRESHIP, RAMSSES and other projects,” says Jurado. “The largest challenges are the need for new regulations, fire safety aspects, bonding techniques and reduction of shipbuilding costs.” For the latter, he cites automated manufacturing in shipyards as a key issue as well as mold construction and composite materials sourcing and storage. “Composites are already growing in ships,” says Krause at CMT, “but we started this work 20 years ago, so it is a slow process. However, we now have this critical mass and the industry is more connected via E-LASS.”
Jörg Bünker, head of R&D, application service for SAERTEX LEO FR products at SAERTEX (Saerbeck, Germany), agrees:“The drivers to reduce weight are strengthening. Within the next five to seven years, more composite materials will be sold into ships. This is the right time for more projects because IMO needs to see this interest and effort from the industry. Suppliers must show new solutions and shipyards must show where composites can be used, but no one can do it alone.”
Hars
- Verzenden in een fles
- montage-armaturen voor 3D-printen met Markforged Composites
- Recycling:continu-vezelversterkte thermoplastische composieten met gerecycled polycarbonaat
- Hoe mobiele technologie reisbelemmeringen wegneemt
- TxV Aero Composites voldoet aan de AS9100-normen
- Mikrosam automatiseert thermoplastische composieten met gereedschaploos plaatsingssysteem voor meerdere robots
- Hexcel werkt samen met Lavoisier Composites, Arkema
- Continuous Fiber Manufacturing (CFM) met moi-composieten
- Lightweighting Summit:gericht op composieten, mogelijkheden voor automatische aandrijflijn
- Ashland werkt samen met Velox voor distributie van composieten in Frankrijk
- 3D-print composieten met continue vezels