Samengesteld dek vermindert de diepgang van rivierschepen
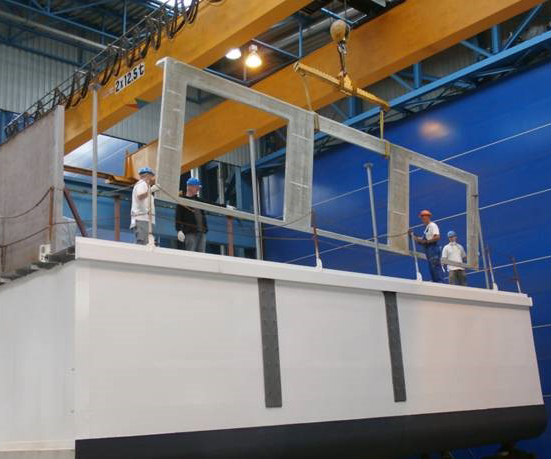
SAERTEX werkte samen met scheepsbouwer Neptun Werft om een composiet bovenbouw te bouwen om het gewicht van 45% te verminderen ten opzichte van staal in een riviercruiser. BRON | SAERTEX
Deze blog is een zijbalk bij mijn hoofdartikel van december 2019, "De belemmeringen voor het lichter maken van schepen met composieten".
Leverancier van composietmaterialen SAERTEX (Saerbeck, Duitsland) begon in 2014 samen te werken met Neptun Werft (Rostock, Duitsland), met als doel het gewicht te verminderen in een 110 meter lang, 11,4 meter breed riviercruiseschip om het vaarseizoen van het schip te verlengen. "De rivier is in bepaalde maanden weinig diep", legt Jörg Bünker uit, hoofd van R&D, applicatieservice voor SAERTEX LEO brandwerende (FR) producten. “Om de diepgang van het schip met 1 centimeter te verminderen, moeten ze 11 ton gewicht besparen. We hebben met hen samengewerkt om staal te vervangen door composieten in alles boven de waterlijn. Ons doel was om 45 procent af te vallen en dat hebben we bereikt.”
Naast het leveren van LEO-materialen — niet-krimpende weefselversterkingen (NCF) plus FR-schuimkernen en met aluminiumtrihydroxide gevulde of opschuimende coatings (zie "Brandbestendig zonder het gewicht") — werkte SAERTEX ook samen met de scheepswerf om het ontwerp te ontwikkelen en demonstratieonderdelen te maken . "We kozen voor LEO met een glasvezelversterkt, quasi-isotroop laminaat voor de gelaatshuiden en een FR-gemodificeerde versie van SAERfoam, die glasvezelcomposietverbindingen heeft tussen de gelaatshuiden door middel van een polyisocyanuraatschuimkern", zegt Bünker. “Deze verbindingen in het SAERfoam zorgen voor een goede constructieve weerstand tijdens de brand en ook voor goede resteigenschappen. Door LEO-composieten te gebruiken, hoefde de bouwer geen extra isolatie te gebruiken voor temperatuur en geluid zoals bij staal. Dit levert een enorme gewichtsbesparing op.”
Het duurde twee jaar om het ontwerp en de bouwgoedkeuring te krijgen van de Centrale Commissie voor de Rijnvaart (CCR, Straatsburg, Frankrijk), die werkt met binnenwateren in heel Europa. “Die lange periode kwam mede doordat de autoriteiten maar twee keer per jaar bijeenkomen”, legt Bünker uit. “Na ons eerste voorstel kregen we de opdracht om gegevens te verzamelen en enkele brandtesten uit te voeren, die we tijdens de volgende vergadering presenteerden. Verbindingen waren ook een probleem. We moesten wat brandonderbrekingen aanbrengen in de voegen tussen panelen en de brandprestaties van zowel composiet-composiet- als composiet-stalen verbindingen bewijzen.”
Het bouwen van de mock-up stelde meer uitdagingen. “Een composietfabriek inbouwen is geen probleem. Maar bouwen in de werfomgeving is moeilijker. Dit was echter cruciaal om de autoriteiten te overtuigen. Ze moesten zien hoe het werd gebouwd en eroverheen lopen als het klaar was.” Hij wijst erop dat de verkregen goedkeuring op maat was gemaakt, op basis van het specifieke ontwerp en de tests voor dit schip. Na goedkeuring waren de composieten snel gebouwd. De uiteindelijke structuur - een zonnedek genoemd - gebruikte meer dan 1.000 vierkante meter met hars doordrenkte composietpanelen, verbonden door middel van tabs en bonding.
Bünker zegt dat de werf nu meer wil doen. "Ze hebben veel kennis opgedaan en het heeft hun geest geopend voor wat er mogelijk is." De twee bedrijven hebben verschillende andere projecten in uitvoering. SAERTEX is ook een leverancier voor het Duitse nationale AERONAUT-project, dat tot doel heeft de windweerstand te verminderen/de luchtstroom rond de bovenbouw van schepen te optimaliseren om het brandstofverbruik en de uitstoot van broeikasgassen te verminderen. “Hiervoor werken we aan het toevoegen van een voorruit/spoiler aan het dekhuis van een ander binnenvaartschip”, legt hij uit. “De onderdelen zijn kleiner dan het zonnedek, maar de regelgeving vereist dat hetzelfde werk wordt gedaan om de gelijkwaardigheid met staal voor dit nieuwe ontwerp aan te tonen. Dit is een van de redenen dat we ook het werk in FIBRESHIP en RAMSSES ondersteunen, die streven naar een composietspecifiek en snel goedkeuringsproces dat kan worden gebruikt om een veel snellere kwalificatie te verkrijgen.”
Hars
- Solvay breidt capaciteit thermoplastisch composiet uit
- Het belang van harskeuze
- Arevo introduceert aangepaste, 3D-geprinte composiet scooter
- Ontwerpinnovaties verbeteren de efficiëntie van composiet medische tafel
- Grote composiet hoezen beschermen veel water
- Alveus commercialiseert Compa Repairs composiet scheepsreparatieservice
- Re:Build Manufacturing neemt Composite Resources over
- Samengestelde wapening voor toekomstige infrastructuur
- Architectonische bekledingscomposiet onthuld
- Betere composietfietsen maken in Arkansas
- Composiet + metaal:holle hybride technologie