Bevordering van thermoplastische composieten en RTM voor Clean Sky 2 in Spanje

Het EURECAT Centro Tecnológico de Catalunya (EURECAT Technology Center Catalonië, Barcelona, Spanje) is een particuliere, non-profit R&D-organisatie met 11 faciliteiten, 650 medewerkers en 50 miljoen euro aan jaarlijkse inkomsten. "Het is het op een na grootste R&D-centrum in Spanje", legt Angel Lagraña Hernandez uit, programmadirecteur voor de luchtvaart- en ruimtevaartmarkt bij EURECAT. Hij legt uit dat een deel van de inkomsten van EURECAT afkomstig is van de Catalaanse regering en dat van de rest de helft moet komen van particuliere bedrijven — meestal kleine tot middelgrote ondernemingen (kmo's) — terwijl de andere helft publiek kan zijn, zoals de door de Europese Unie gefinancierde Clean Sky 2 programma. "We hebben nu 18 Clean Sky-projecten", merkt Lagraña op, "die we puur op basis van concurrerende inzendingen hebben gekregen in reactie op oproepen tot het indienen van voorstellen."
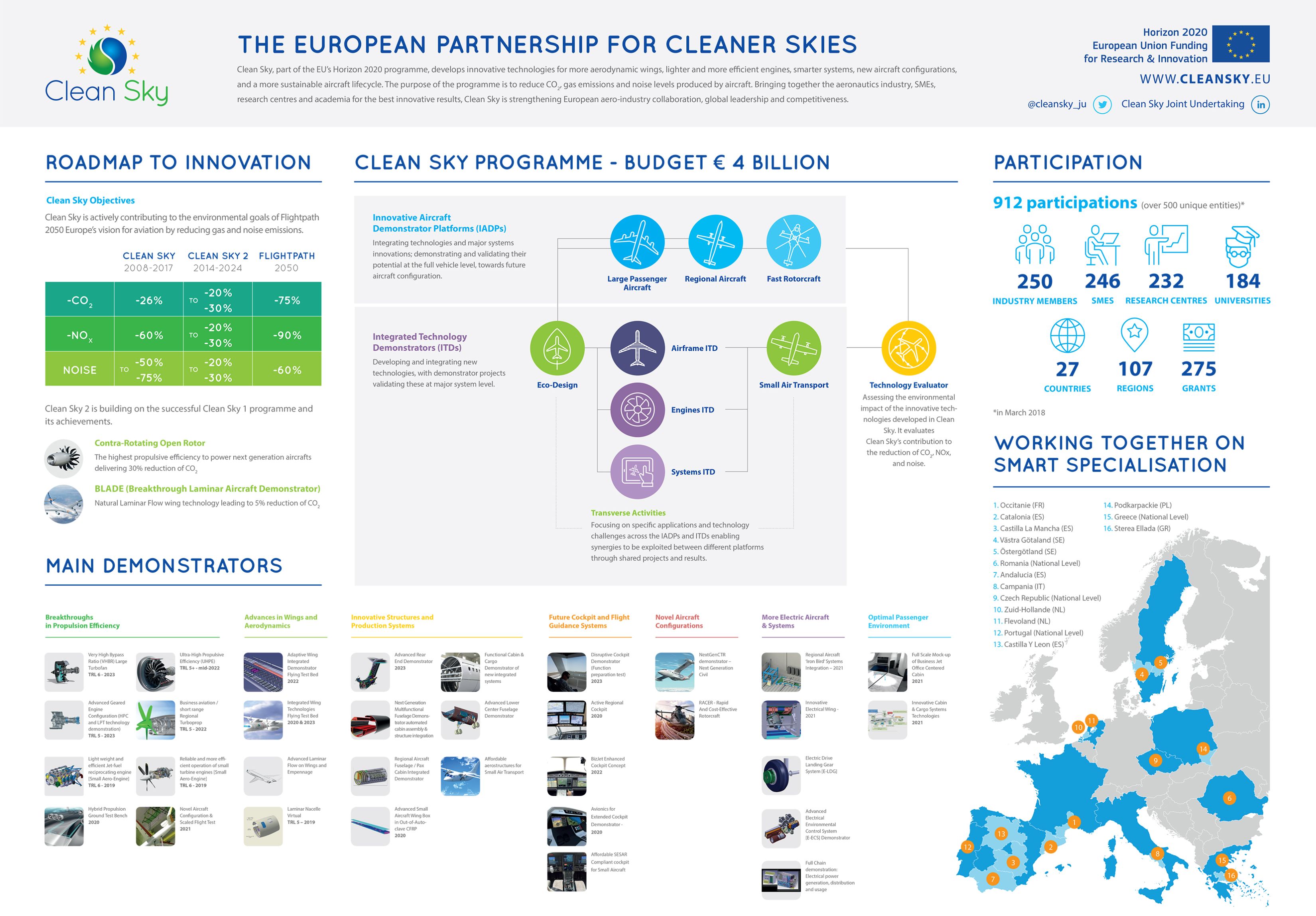
Voorbeelden van hoe composieten een rol spelen in de talrijke doelen en geplande technologiedemonstraties van Clean Sky 2 zijn:
- De multifunctionele demonstrator van de romp van de volgende generatie — gebruikmakend van thermoplasten voor een schonere lucht
- Circulaire economie:composiet romp voor regionale vliegtuigen krijgt vorm
- Gebruikmaken van autosportexpertise voor FastCan van Clean Sky
"EURECAT is zeer transversaal en werkt in de automobiel-, spoorweg- en andere industrieën naast zijn werk in de lucht- en ruimtevaart", zegt Lagraña. "Het heeft ook veel activiteiten op het gebied van IT, zoals data-analyse en blockchain, enz. Composites 4.0 is een van de strategische gebieden." Binnen composieten merkt hij op dat EURECAT voornamelijk werkt in out of autoclave (OOA) technologieën. "We richten ons op thermoplasten en vloeibare compressievormen, inclusief procesbewaking in realtime, inclusief monitoring van de glasovergangstemperatuur (Tg) van de hars tijdens de verwerking." (Blijf het gedeelte over COFRARE lezen, aan het einde van deze blog, voor meer informatie over deze Tg-monitoring.)
EURECAT's meest recente composieten-gerelateerde projecten in Clean Sky 2 omvatten:
- KEELBEMAN om een thermoplastische composiet kielbalk te demonstreren (Dit project heeft financiering ontvangen van de Clean Sky 2 Joint Undertaking in het kader van het Horizon onderzoeks- en innovatieprogramma van de Europese Unie onder GAP n° 785435 KEELBEMAN);
- WINFRAME 4.0 om raamkozijnen van thermoplastisch composiet (TPC) te bouwen voor de Green Regional Aircraft (GRA)-demonstrator in Clean Sky (2008-2017) en uitgebreid tot de Regional Aircraft IADP (Innovative Aircraft Demonstrator Platform) in Clean Sky 2 (2014-2024);
(Dit project heeft financiering ontvangen van de Clean Sky 2 Joint Undertaking in het kader van het Horizon onderzoeks- en innovatieprogramma van de Europese Unie onder GAP nr. 821323 WINFRAME 4.0.) - COFRARE 2020 voor thermohardende rompframes gemaakt met behulp van harstransfergieten (RTM) met TPC-schuifbinders.
(Dit project heeft financiering ontvangen van de Clean Sky 2 Joint Undertaking in het kader van het Horizon onderzoeks- en innovatieprogramma van de Europese Unie onder GAP nr. 821261 COFRARE 2020.)
Thermoplastische composiet kielbalk
Clean Sky 2 - JTI-CS2-2017-CFP06-LPA-02-20. Projectduur:maart 2018 tot december 2019
Het doel van het KEELBEMAN-project is het ontwikkelen van een op fabricage gerichte kielbalkstructuur voor een vliegtuig van het type A320 die hoge vliegtuigproductiesnelheden mogelijk maakt, maar tegen een betaalbare prijs via thermoplastische composieten. Naast EURECAT als projectcoördinator, zijn partners onder meer:
- Airbus (Toulouse, Frankrijk) als topicmanager
- CETMA (European Research Centre for Technologies Design and Materials, Brindisi, Italië)
- De CT Engineering Group (CT Ingenieros, Madrid, Spanje), een firma met talrijke wereldwijde kantoren die een meerjarig contract heeft met Airbus voor de ontwikkeling van vliegtuigen, zoals onderzoek aan de romp, vleugels en achterkant via haar kantoor in Hamburg, Duitsland; onderzoek aan de achterkant (Spanje); onderzoek naar romp- en energiecentrale-gerelateerde constructies (Toulouse, Frankrijk) en vleugelontwikkeling (Bristol, VK)
- Sofitec (Sevilla, Spanje), een specialist in de fabricage en montage van vliegtuigstructuren met expertise en productiecapaciteit in composieten.
De CT Engineering Group leverde volledige modellering van de geometrie van de kielbalk via haar kantoor in Toulouse, terwijl Sofitec niet-destructieve testen (NDT)-inspectie ontwikkelde. "Dit is een hele uitdaging met zo'n gesloten doosstructuur", benadrukt Lagraña.
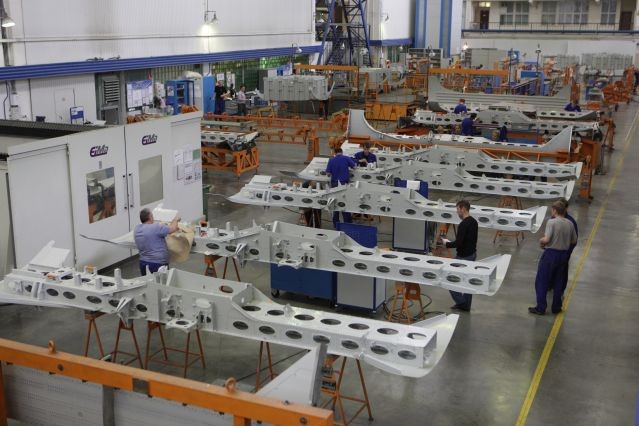
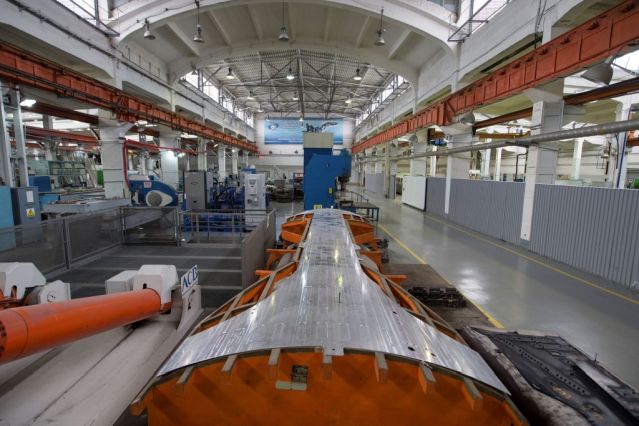
Hier wordt de A320-kielbalkconstructie getoond, gemaakt van metaal door Irkut Corporation (Moskou, Rusland). Naar verluidt sloot Irkut in 2004 een contract met Airbus voor de levering van onderdelen, waaronder een neuslandingsgestel, kielbalk en flaptrack, die gemiddeld in elk derde vliegtuig uit de A320-familie worden geïnstalleerd. BRON | Irkoet
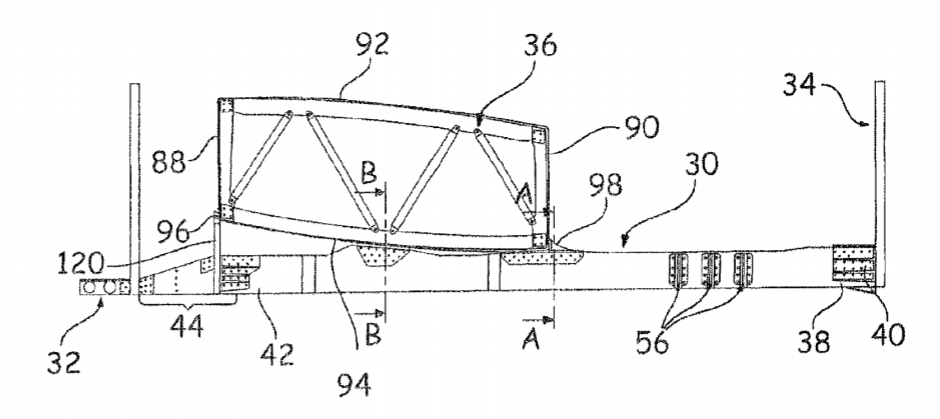
Ontwikkeling van kielbalkconstructies
“Tegenwoordig zijn de meeste kielbalken van vliegtuigen gemaakt van metaal, behalve de Airbus
A350, een monolithische koolstofvezelcomposiet”, zegt Lagraña. "Dit vereist grote aantallen klinknagels en een aanzienlijke hoeveelheid tijd voor montage." Hij legt uit dat de kielbalk een kritieke constructie in de romp is:"Er zijn gevallen geweest waarbij de kielbalk tijdens de landing is gebroken, waardoor de hele romp scheurde en brak.
Volgens een artikel van Steve Wilhelm uit 2011 is de A350-kielbalk 70% composiet, 16,5 meter lang, samen met 10.000 bevestigingsmiddelen, 1,2 ton weegt en de ruggengraat van het vliegtuig vormt. Wilhelm merkt op dat het concurrerende Boeing 787-vliegtuig "niet afhankelijk is van zo'n robuuste kielstructuur, omdat meer van de rompsterkte afkomstig is van composietvaten die end-to-end aan elkaar zijn bevestigd." Het artikel citeert vervolgens Michel Merluzeau, managing partner van luchtvaartadviesbureau G2 Solutions LLC (Kirkland, Wash., VS), die het Airbus-ontwerp omschrijft als "conventioneel" en "minder riskant", maar erop wijst dat de kielbalk "essentieel is voor de structurele integriteit van dat vliegtuig.”
Airbus was in 2001 de pionier van een composiet kielbalk voor de A340. Maar zoals hierboven beschreven, werkt het hoge aantal benodigde klinknagels in tegen de gewichtsbesparing die mogelijk is door composieten te gebruiken. Een belangrijk doel in het KEELBEMAN-project is dus het minimaliseren van bevestigingsmiddelen door thermoplastische composietcomponenten te gebruiken die aan elkaar zijn gelast.
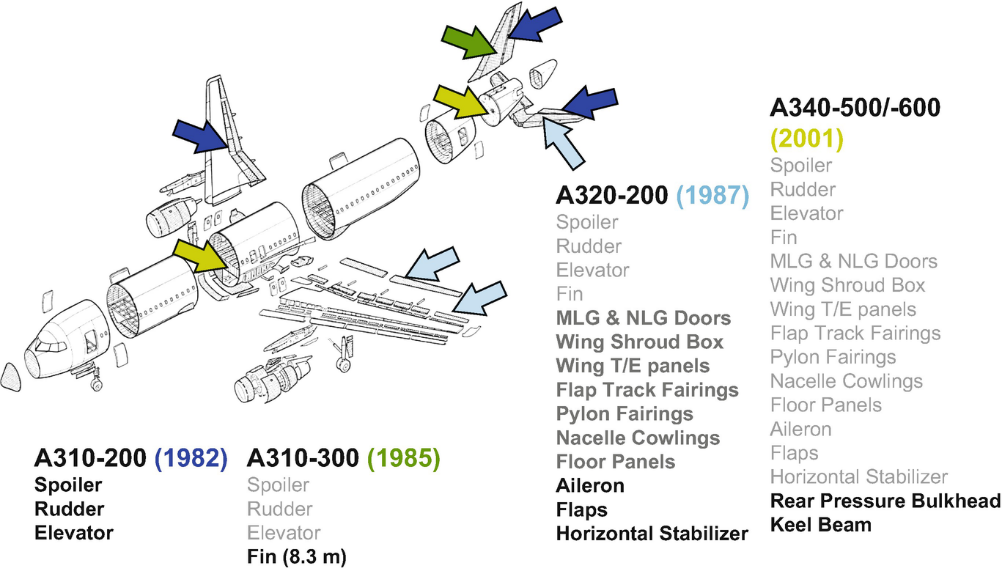
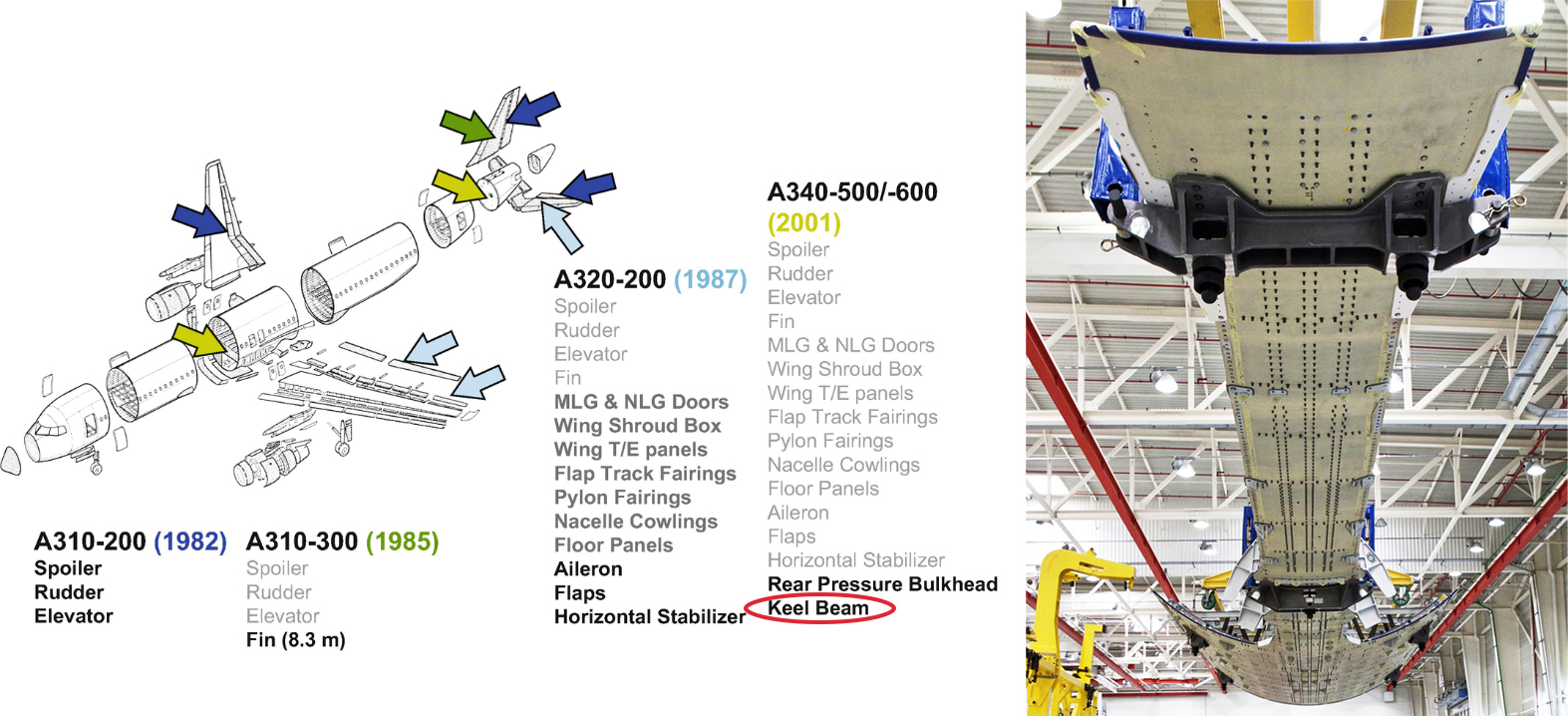
TPC-kielbalk
"De ontwikkeling van een kielbalk van thermoplastisch composiet met behulp van lassen voor montage maakt deel uit van Airbus' ontwikkeling van het vliegtuig van morgen, waaronder programma's als de Wing of Tomorrow en Fuselage of Tomorrow", zegt Lagraña. "Binnen KEELBEMAN hebben we een demonstratiedeel van 250 millimeter bij 500 millimeter bij 1 meter lang geproduceerd van een kielbalk met stringers en hebben we de haalbaarheid aangetoond om deze constructie met zoveel mogelijk automatisering te lassen."
Lagraña merkt op dat de wandplaten en stringers van de demonstrator zijn gemaakt met behulp van koolstofvezel/polyetherketonketon (PEKK) unidirectionele (UD) tape in een continu compressiegietproces (CCM) ontwikkeld door CETMA (zie "Compressie van lucht- en ruimtevaartkwaliteit" en "PEEK vs. PEKK vs. PAEK en continu persen"). "Er zijn ook ribben voor dwarsverstijvers die zijn gemaakt met behulp van traditioneel niet-isotherm persgieten door EURECAT", voegt Lagraña toe.
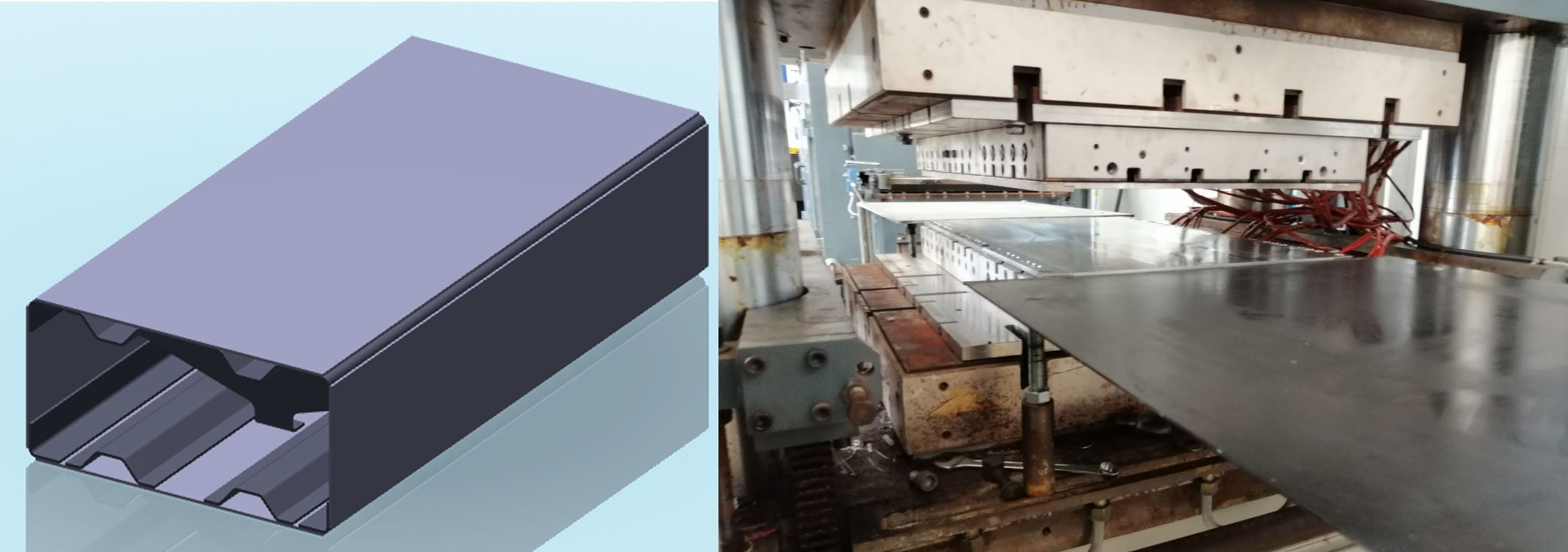
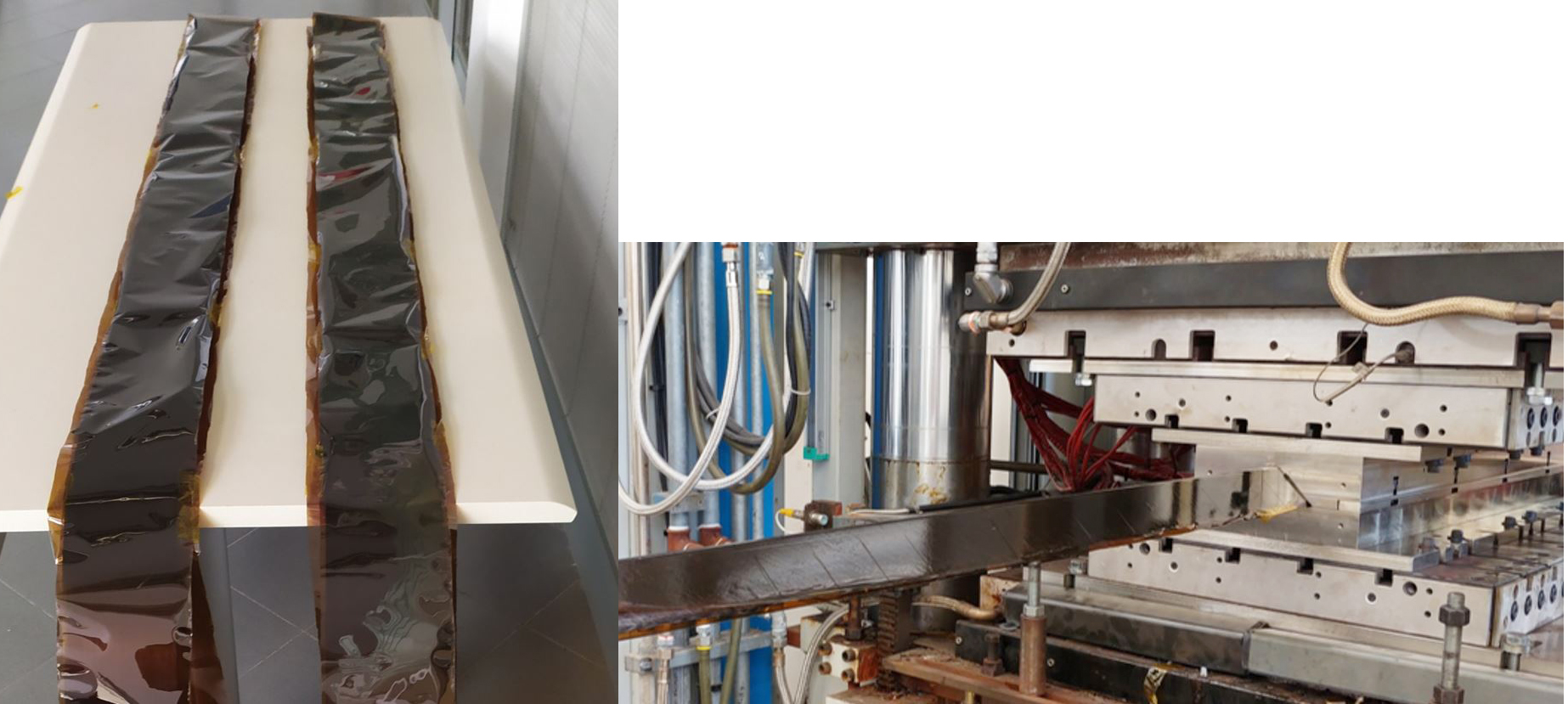
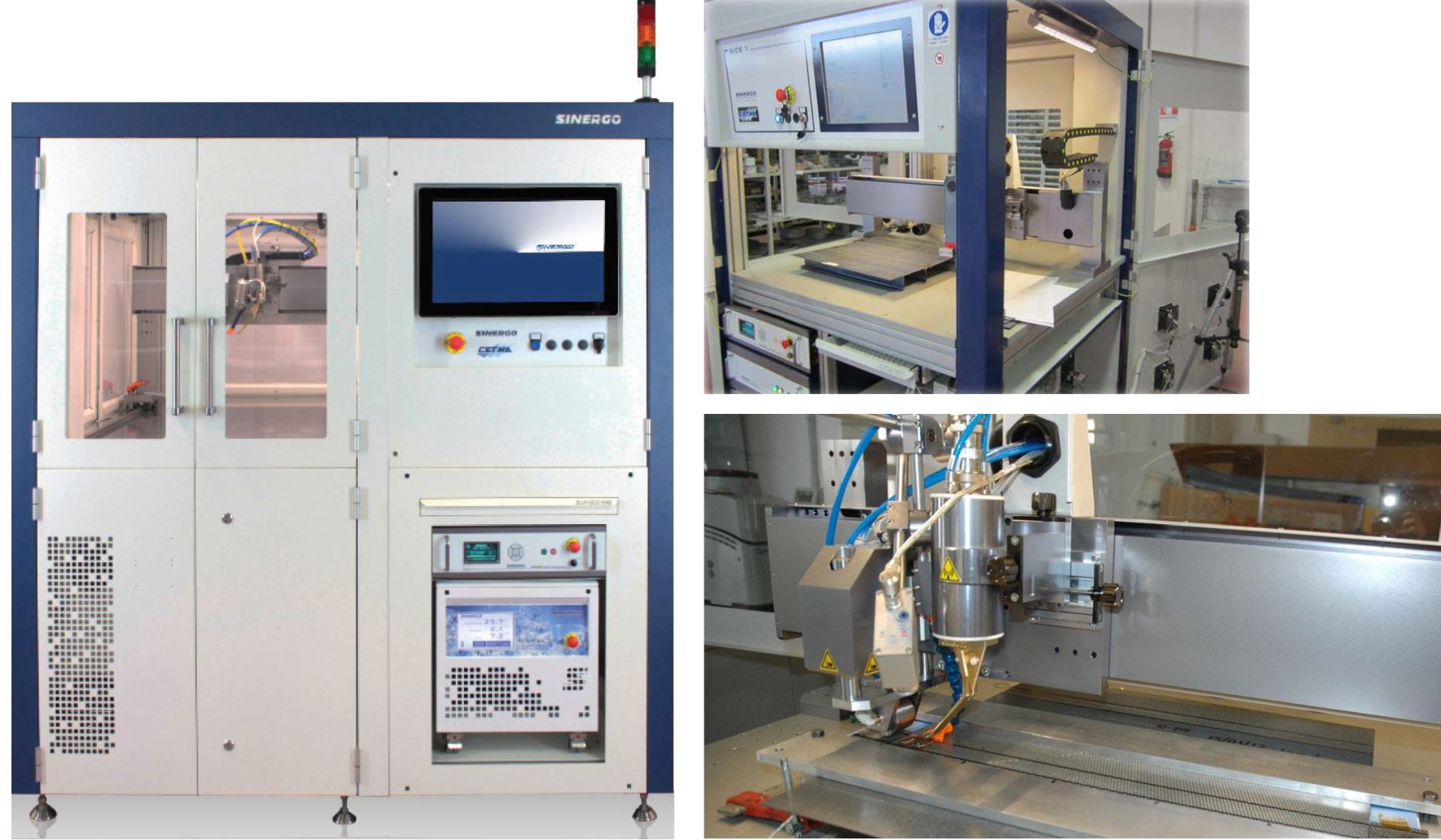
Inductielassen als belangrijke factor
Lagraña merkt op dat CETMA niet alleen een sleutelrol speelde bij de productie van onderdelen voor KEELBEMAN, maar ook bij de assemblage van de demonstrator met behulp van zijn gepatenteerde inductielasmachine en -technologie. Dit lassen werd oorspronkelijk ontwikkeld in het ECO FAIRS-project van het eerste Clean Sky-programma (2011-2014), samen met het hierboven getoonde isotherme en niet-isotherm persgieten van TPC-structuren. In ECO FAIRS gebruikte CETMA al deze technologieën om een prototype demonstrator te produceren op basis van het bestaande bovenpaneel (stringer-verstijfd huidpaneel) van een Agusta Westland helikopterstaart en een gebogen sponson kuip demonstrator. Hoewel deze zijn gemaakt met CETEX (geleverd door TenCate, nu Toray Advanced Composites) T300 3K 5HS koolstofvezeltextiel met dubbelzijdige PPS (polyfenyleensulfide) film, bewees CETMA ook inductielassen met PEEK- en PEI-composieten.
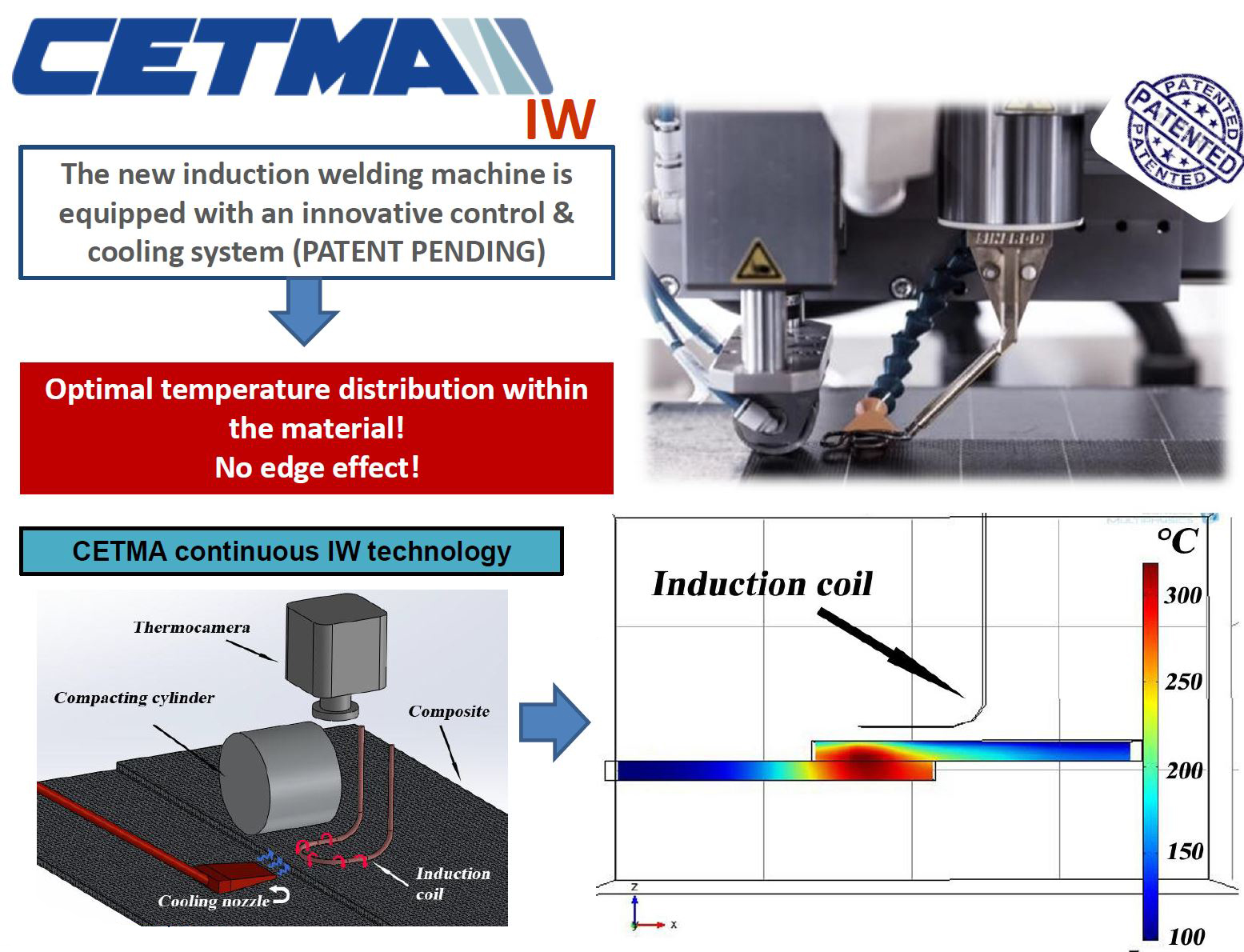
CETMA selecteerde inductielassen (IW) als de meest veelbelovende lastechniek van thermoplastisch composiet en werkte samen met las- en elektronica-engineer SINERGO srl (Valdobbiadene, Treviso, Italië) om een nieuwe inductielasmachine te ontwikkelen. De op een portaal gebaseerde SICE 1 WIDE-machine aangeboden door SINERGO (zie afbeelding hieronder) kan continu lassen van onderdelen van luchtvaartkwaliteit tot 1 meter bij 1 meter. Het bevat een robuust regelsysteem om te zorgen voor optimale temperatuurverdelingen binnen de te lassen materialen. De machine is uitgerust met een gekoelde cilinder om consolidatiedruk uit te oefenen en met een luchtkoelsysteem om waar nodig warmte af te voeren, zoals in de randen, waar de stroom van de geïnduceerde elektrische wervelstromen wordt beperkt, wat resulteert in een hoge stroomdichtheid en oververhitting . Het is ook mogelijk om de CETMA inductielaskop te installeren op een 6-assige robotarm voor het lassen van geometrisch complexe vormen.
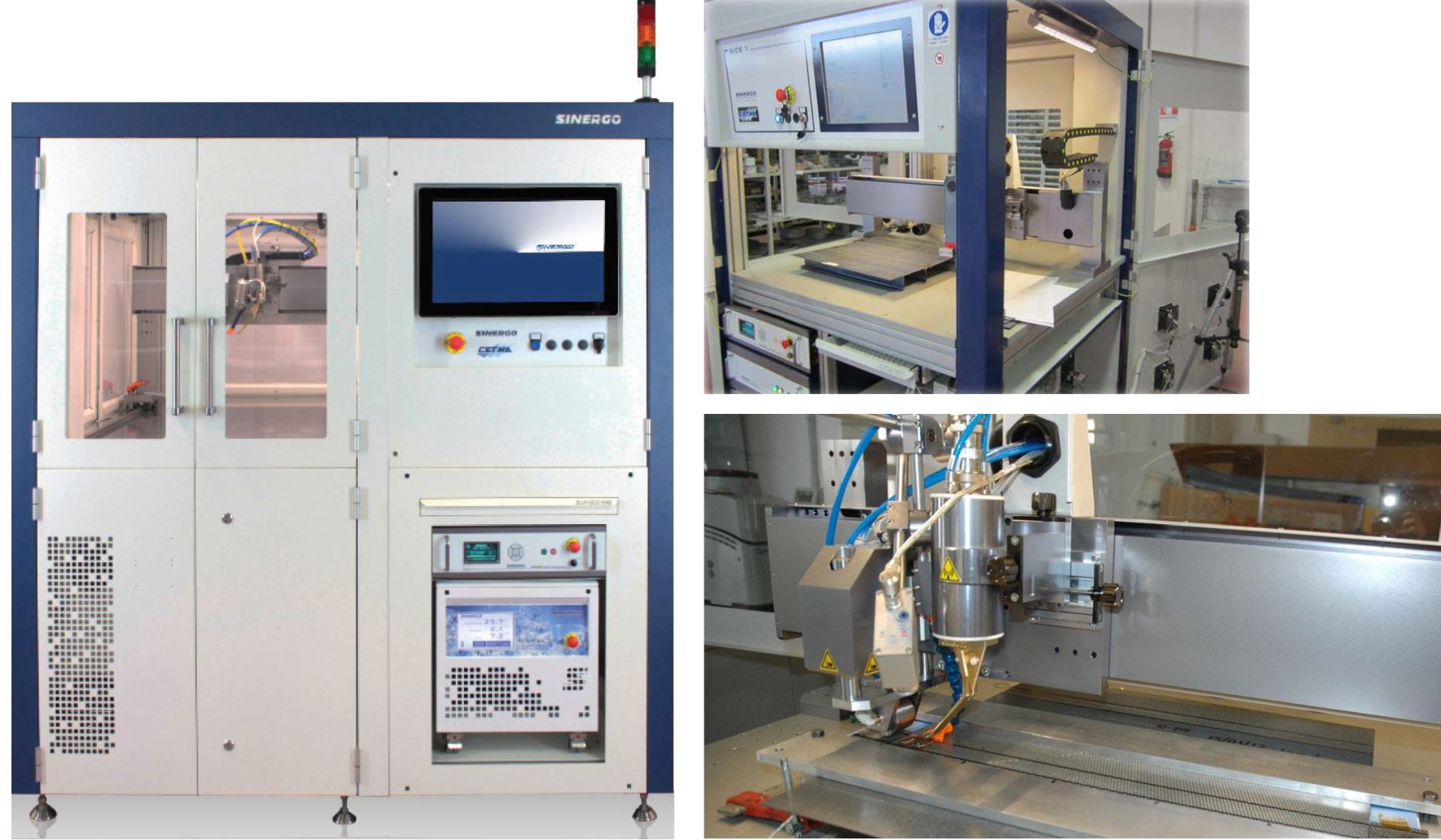
CETMA heeft ook de mogelijkheid ontwikkeld om zijn inductielasproces te optimaliseren door gebruik te maken van simulatietools en numerieke analyses uit te voeren met COMSOL Multiphysics (COMSOL Inc., Burlington, Mass, V.S.) eindige-elementenmodellering (FEM)-software. Het heeft deze modellen geverifieerd door middel van een groot aantal fysieke tests. CETMA bevestigde zijn geoptimaliseerde procesparameters door tests met één ronde op gelaste coupons, waarbij de waarden voor de afschuifsterkte zeer dicht bij het in de literatuur vermelde maximum lagen. Deze waren met name ook veel hoger dan de maximale waarden bij het gebruik van structurele lijmen, zegt CETMA.
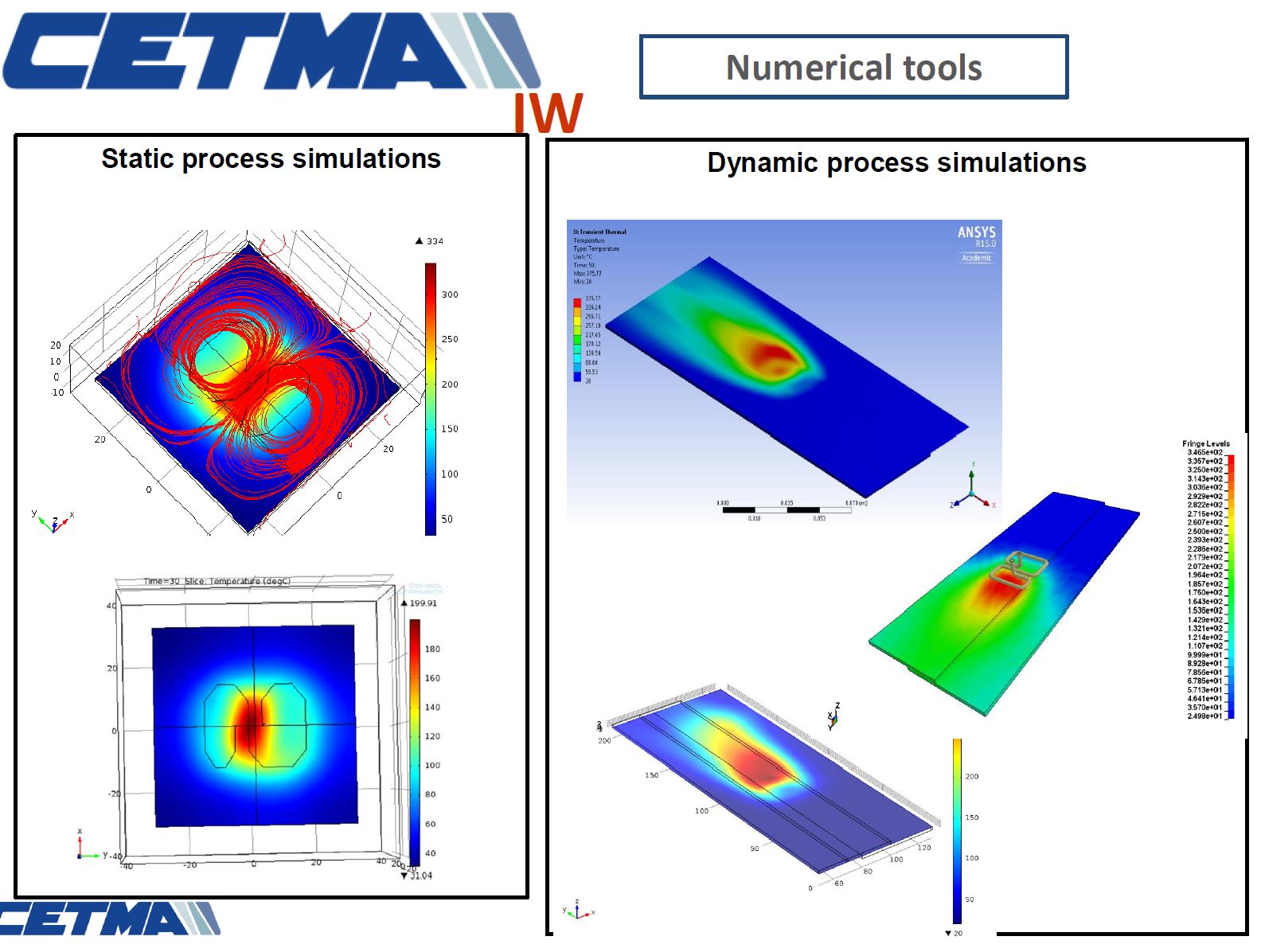
CETMA heeft zijn lasvermogen bewezen voor een breed scala aan materialen, waaronder geweven en UD-koolstofvezel, evenals PEEK, PEI, PEKK, PP, PA6, PA12 en zelfs lassen op CF/epoxy met behulp van een thermoplastische PVB (polyvinylbutyral) hybride laag voor de overgang van het thermohardende substraat naar het thermoplastische vlak voor het lassen. (Veel van de details van deze sectie zijn ontleend aan de presentatie van CETMA-competenties en de CORDIS eindrapport voor ECO BEURZEN.) CETMA heeft in 2014 een Europees patent aangevraagd en de uitvinders Silvio Pappada en Andrea Salomi kregen in 2016 patent EP2801472A1. CETMA heeft talloze artikelen en presentaties over deze technologie gepubliceerd, waaronder:
- "Simulaties van eindige elementen ter ondersteuning van de ontwikkeling van technologieën buiten de autoclaaf", A&D, 11-12 oktober 2012
- "Simulaties van eindige elementen ter ondersteuning van continu inductielassen van PPS-koolstofcomposieten", SEICO 13, 11-13 maart 2013 "Parijs"
- "Ontwikkeling van een nieuwe inductielasmachine voor thermoplastische composieten in de lucht- en ruimtevaartsector", Italiaanse vereniging van lucht- en ruimtevaart XXII conferentie Napoli, 9-12 september 2013
- "Inductielassen in de lucht- en ruimtevaartsector", TPRC, Thermoplastic Composites European Consortium, webvergadering, december 2013.
- “Tests op volledige schaal van thermoplastische componenten voor de lucht- en ruimtevaartsector”, SEICO 14, 10-11 maart 2014 “Parijs”
- “Nieuwe inductielasapparatuur voor de lucht- en ruimtevaartsector”, JEC magazine, nr. 87, maart 2014, pp. 89-91.
KEELBEMAN-status en pad voorwaarts
Airbus bezocht CETMA in december om het laatste laswerk van het demonstratiegedeelte van 1 meter te zien, en het KEELBEMAN-team hield ook een laatste beoordeling van het technologiegereedheidsniveau (TRL). "We behalen goede resultaten en ontwikkelen de technologie van TRL 3 naar TRL 4", zegt Lagraña. De volgende stappen kunnen de verdere ontwikkeling naar TRL 6 en de productie van een kielbalk op ware grootte omvatten die moet worden geïnstalleerd in een van de demonstrators van de Clean Sky 2, zoals de WP 2.3.2 op ware grootte onderste middenromp, maar dit is nog niet besloten.
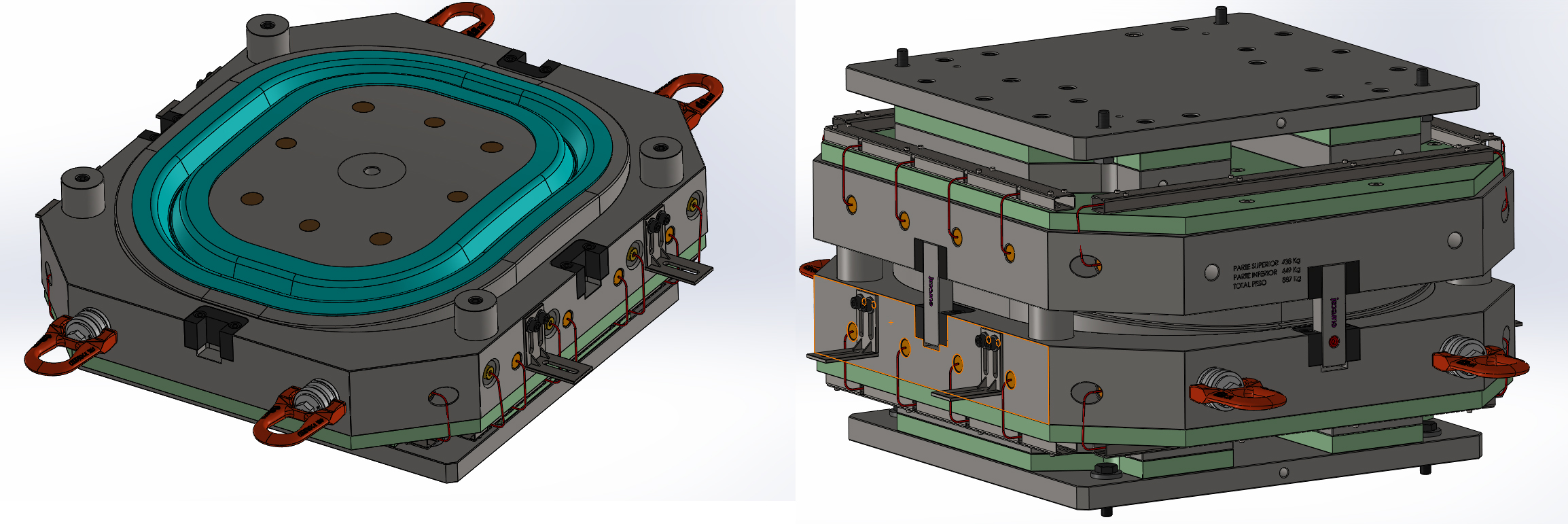
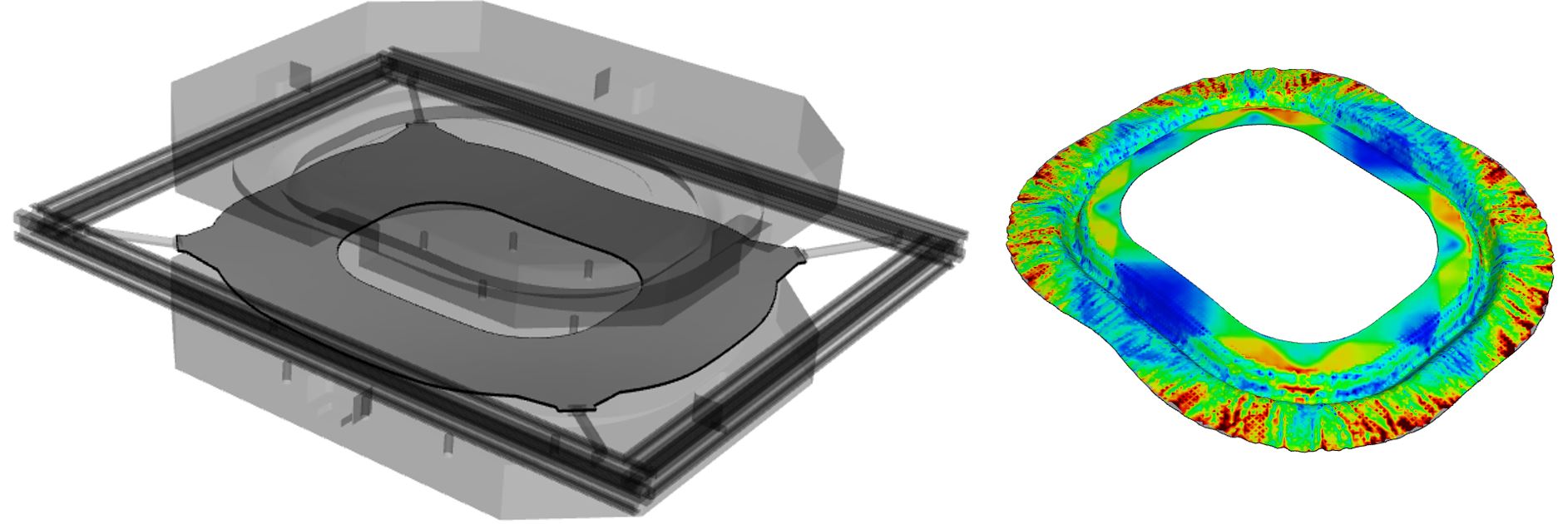
WINFRAME 4.0-project voor TPC-kozijnen
Een ander programma van thermoplastisch composiet (TPC) voor EURECAT is WINFRAME 4.0, met als doel om 24 raamkozijnen te ontwikkelen en te produceren voor een regionaal vliegtuigromp/cabine-geïntegreerde gronddemonstrator (zie uitleg over de ontwikkelingen van Clean Sky 2 voor regionale vliegtuigen en de Full -schaal innovatieve romp en passagierscabinedemonstratie onderstaand). WINFRAME 4.0-partners zijn onder meer:
- Multinationale luchtvaartmaatschappij Leonardo (Rome, Italië) als topicmanager
- EURECAT
- Sofitec.
"De methode die we gebruiken, kan elke 10 minuten een raamkozijn produceren", zegt Lagraña. De productiestappen zijn onder meer:TPC-laminaatblanco's in een oven verhitten, naar een mal vertalen, de mal in een pers sluiten, 10-20 minuten warmte en druk toepassen en het (de) voltooide onderdeel(en) uit de vorm halen. "Deze aanpak zorgt niet alleen voor kortere cycli dan bij vloeibaar gieten, maar ook voor veel goedkopere gereedschappen", voegt hij eraan toe. "Het proces is goed bekend in de auto-industrie, het is persgieten in een sterk geautomatiseerde configuratie die de kwaliteit van het onderdeel verhoogt, maar de gebruikte ruimtevaartmaterialen zijn anders, in dit geval een met koolstofvezel versterkt PPS en koolstofvezel van Toray Advanced Composites (voorheen TenCate). Tegen het einde van dit project hebben we een TRL 6 voor deze technologieën bereikt”, zegt Lagraña.
COFRARE-project:RTM C-frames en thermoplastische breekbinders
Het COFRARE 2020-project is een uitbreiding van het oorspronkelijke COFRARE 2.0-project:
Clean Sky 2 - JTI-CS2-2015-CFP02-AIR-02-16. "Procesontwikkeling voor de fabricage van composietframes met een hoge productiesnelheid en lage kosten"Projectduur:2016 tot 2018.
Het doel van het Clean Sky 2 COFRARE 2.0-project was om een concurrerend en haalbaar fabricageproces te ontwikkelen voor frames van koolstofvezelcomposiet voor gebruik in een op composietpanelen gebaseerde romp voor regionale vliegtuigen. Inclusief partners:
- Gevestigd Tier 1 lucht- en ruimtevaartleverancier en engineering-/industrialisatiebedrijf DEMA in Napels (Design Manufacturing SpA, Somma Vesuviana, Italië)
- EURECAT
- LGAI Technological Center S.A., een divisie van Applus+ Laboratories in Barcelona, Spanje verzorgde testen.
Het doel van het COFRARE 2020-project van de volgende generatie is om composietframes en breekbanden op ware grootte te vervaardigen voor gebruik in de Clean Sky 2 in de romp/cabine geïntegreerde gronddemonstrator. Deze demonstrator is georganiseerd binnen Clean Sky 2's Regional Aircraft IADP (Innovative Aircraft Demonstrator Platform) en gedetailleerd beschreven in paragraaf 5.2.2 van het document van het Joint Technical Programme van maart 2015:
“Regionale vliegtuigen zijn een belangrijk onderdeel van Clean Sky via een speciale ITD (Integrated Technology Demonstrator) - Green Regional Aircraft (GRA) , het leveren van essentiële bouwstenen voor een luchtvervoersysteem dat het milieu respecteert, veilige en naadloze mobiliteit garandeert en industrieel leiderschap in Europa opbouwt. In Clean Sky 2 , … De demonstratiedoelstellingen van de Regional Aircraft IADP zijn veel complexer, uitgebreider en uitdagender dan die van de huidige Clean Sky GRA-project , die genoodzaakt was om binnen budget en tijdsdruk te werken. ..."
Het gezamenlijke technische programma van 2015 schetst de ontwikkeling van regionale vliegtuigen met twee vliegende testbanken en vijf grote geïntegreerde gronddemonstraties. De laatste omvat de Full-scale Innovative Fuselage and Passenger Cabin Demonstrator :"De romp zal een grootschalige demonstratie zijn van technologieën voor composietmateriaal, constructies en fabricage gericht op het bereiken van gewichts- en kostenreductie en het minimaliseren van de milieu-impact door middel van eco-design en optimalisatie van het energieverbruik gedurende de hele levenscyclus (naar een zero-impact).”
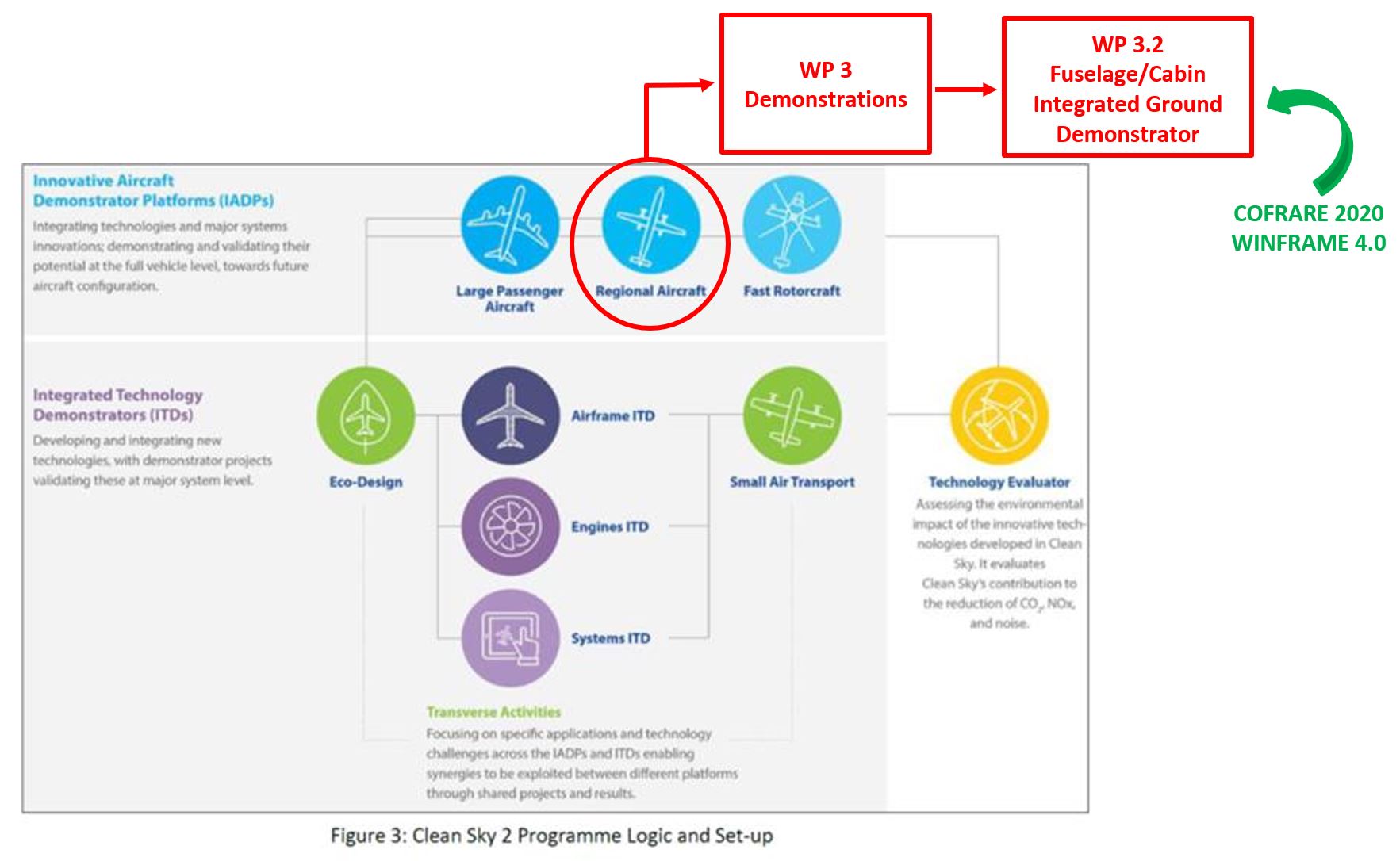
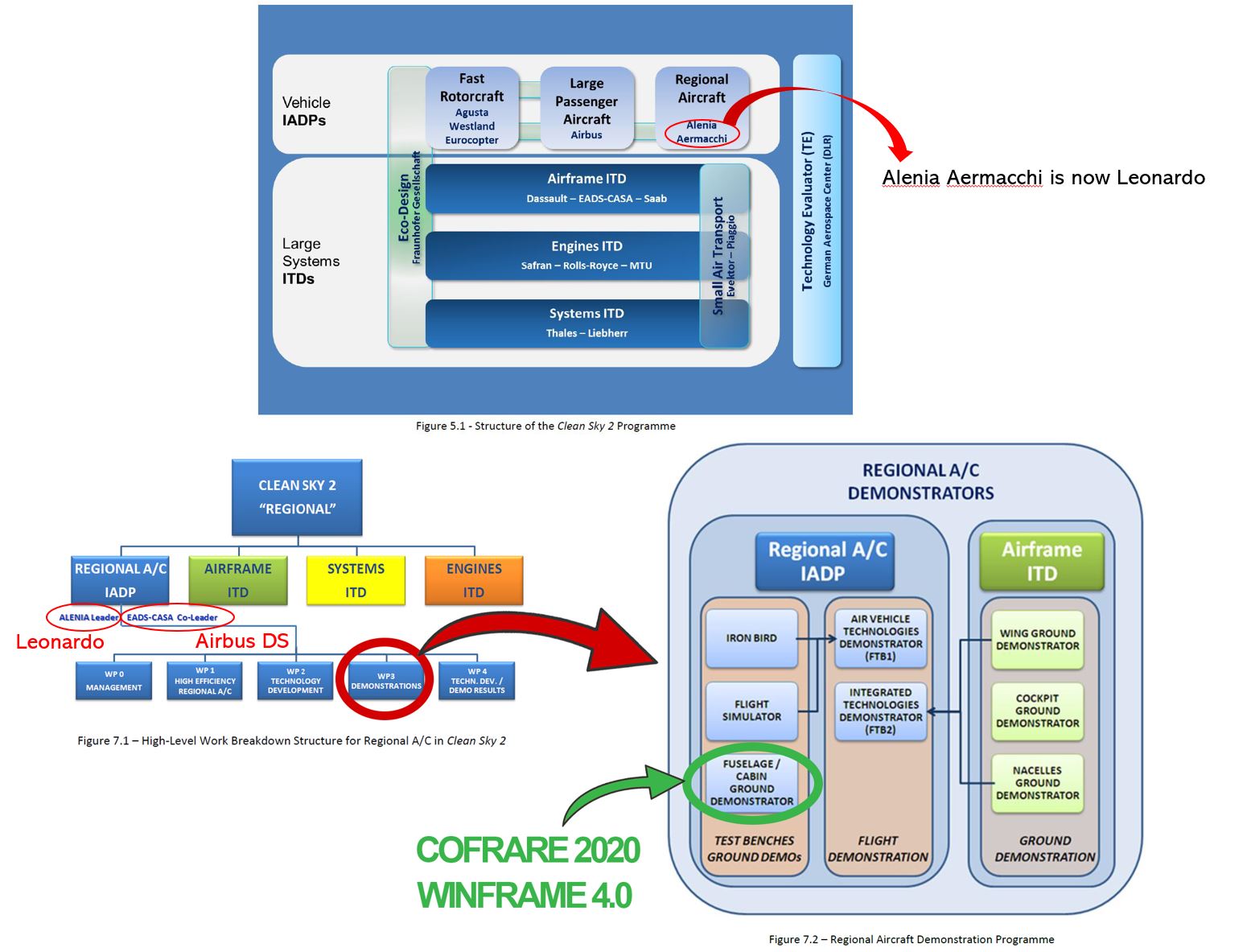
COFRARE 2020-projectpartners zijn onder meer:
- Leonardo als topicmanager
- EURECAT
- DEMA
- Vervaardiging van vliegtuigonderdelen en -assemblages A. Abete (Nola/Marigliano, Italië).
"In COFRARE 2020 maken we rompframes met behulp van RTM (resin transfer molding), dat zal worden geïntegreerd in de rompdemonstrator", legt Lagraña uit. "We gebruiken de Ziplus-technologie van Shikibo (Osaka, Japan) die preforms produceert die zeer geschikt zijn voor injectie met hars." Shikibo Ltd. maakt deel uit van Composite Alliance Corp. (Dallas, Texas, VS) en biedt een verscheidenheid aan technologieën voor het voorvormen van textiel.
Een interessant aspect van dit programma is het gebruik van sensoren van Synthesites (Ukkel, België) voor realtime monitoring van harsaankomst, temperatuur, druk, Tg en uitharding. "De sensoren bevinden zich in specifieke delen van het composietonderdeel en de RTM-tool om de harsinjectiestrategie te optimaliseren", merkt Lagraña op. Injectie wordt bereikt met behulp van een sterk geautomatiseerd systeem geleverd door ISOJET (Corba, Frankrijk), dat ook deel uitmaakt van Composite Alliance Corp. Synthesites-sensoren zijn diëlektrische sensoren, maar in tegenstelling tot de meeste diëlektrische analyse (DEA), die is gebaseerd op wisselstroom (AC) , Synthesieten maken gebruik van gelijkstroom (DC). "Onze sensoren presteren goed met materialen met een hoge weerstand zoals harsen en omdat we een enkele spanning toepassen, hoeven we niet meerdere frequenties te analyseren, maar toch bereiken we een hoge nauwkeurigheid, zelfs aan het einde van de uitharding", legt Synthesites-directeur Dr. Nikos Pantelelis.
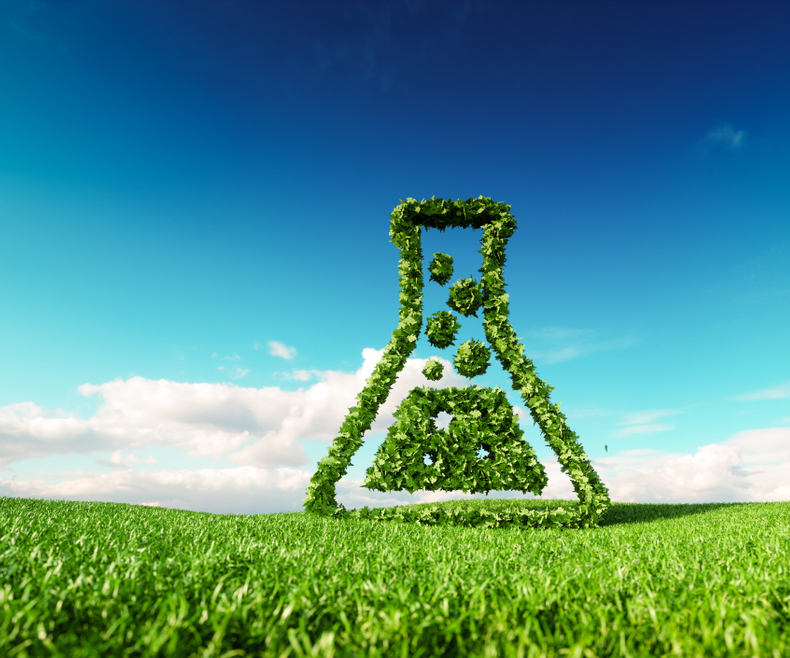
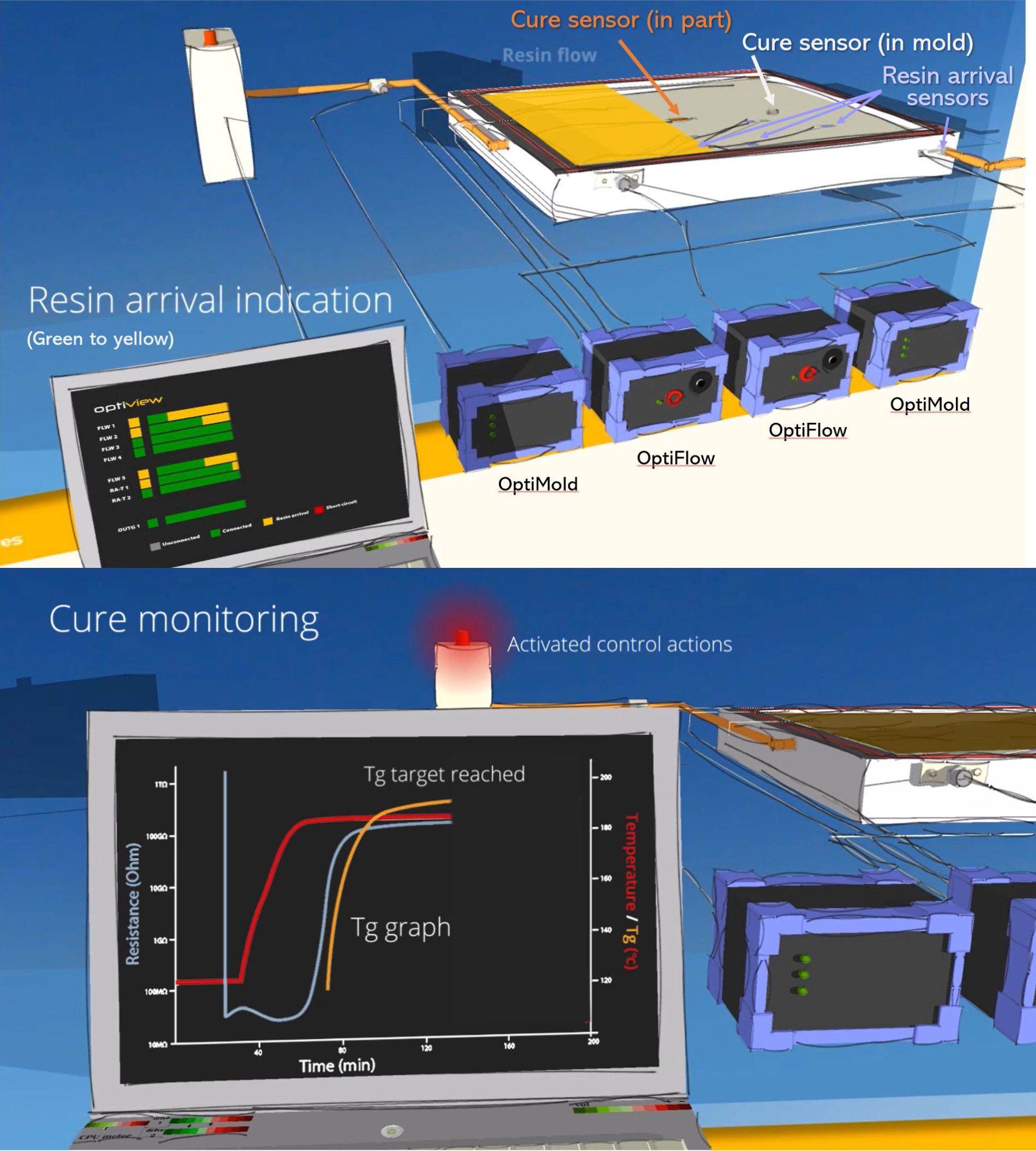
"We ontmoetten Synthesites op een SAMPE-conferentie in 2011", herinnert Lagraña zich. “Ze spraken over sensoren om de uithardingscyclus te verkorten. We onderzoeken hoe we preforms voor de rompframes kunnen automatiseren en zelfs snellere verwerking kunnen gebruiken met HP-RTM (hogedruk-RTM), maar u zit nog steeds op 3-4 uur verwerkingstijd. Met Synthesites hebben we de uithardingscyclus echter met 50 procent verkort door Tg te controleren. We testen nu op eigenschappen. Deze sensoren kunnen onder hoge druk werken, maar in onze RTM-verwerking gebruiken we slechts 8 bar druk.”
De Synthesites DC-diëlektrische sensoren, het OptiFlow vloeibare harsstroombewakingssysteem en het OptiMold-uithardingsbewakingssysteem zijn in productie gedemonstreerd door verschillende fabrikanten van windbladen. Ze worden ook gebruikt door Bombardier Aerospace (Belfast, VK) om de gegoten vleugel van vloeibaar composiet te produceren voor de C-serie, nu Airbus 220. Het Duitse lucht- en ruimtevaartcentrum (DLR, Stade, Duitsland) heeft aangetoond dat de uithardingscyclus tot 50% is verminderd met beide autoclaaf prepreg en RTM, terwijl het National Composites Centre (NCC, Bristol, VK) heeft aangetoond dat zelfs voor zeer reactieve harsen de real-time Tg-berekeningen gemaakt van sensormetingen van harstemperatuur en weerstand net zo nauwkeurig zijn als Tg gemeten van uitgeharde panelen met behulp van differentiële scanningcalorimetrie (DSC).
Frames verbinden met TPC-schuifbinders
Een ander belangrijk onderdeel van COFRARE 2020 is een meer grootschalige productiemethode om de honderden breekbinders en beugels te produceren die nodig zijn om de RTM-romp C-frames aan de composiet romppanelen te verbinden. "We ontwikkelen 255 verschillende geometrieën voor thermoplastische composietbeugels die worden geproduceerd door middel van persgieten", zegt Lagraña. (Let op, GKN Fokker heeft meerdere Clean Sky 2-projecten waar het TPC-beugels zal produceren voor de multifunctionele rompdemonstrator in de IADP voor grote passagiersvliegtuigen; dit werk in COFRARE 2020 is voor kleinere, regionale vliegtuigen.) De basismethode wordt hieronder weergegeven, met behulp van op elkaar afgestemde stalen gereedschappen en een verwarmde pers. "De kosten van dergelijke persgietgereedschappen bedragen slechts 2.000 euro, wat zeer betaalbaar is in vergelijking met RTM-gereedschap", voegt hij eraan toe. “Stempelen levert ook zeer korte cyclustijden op.”
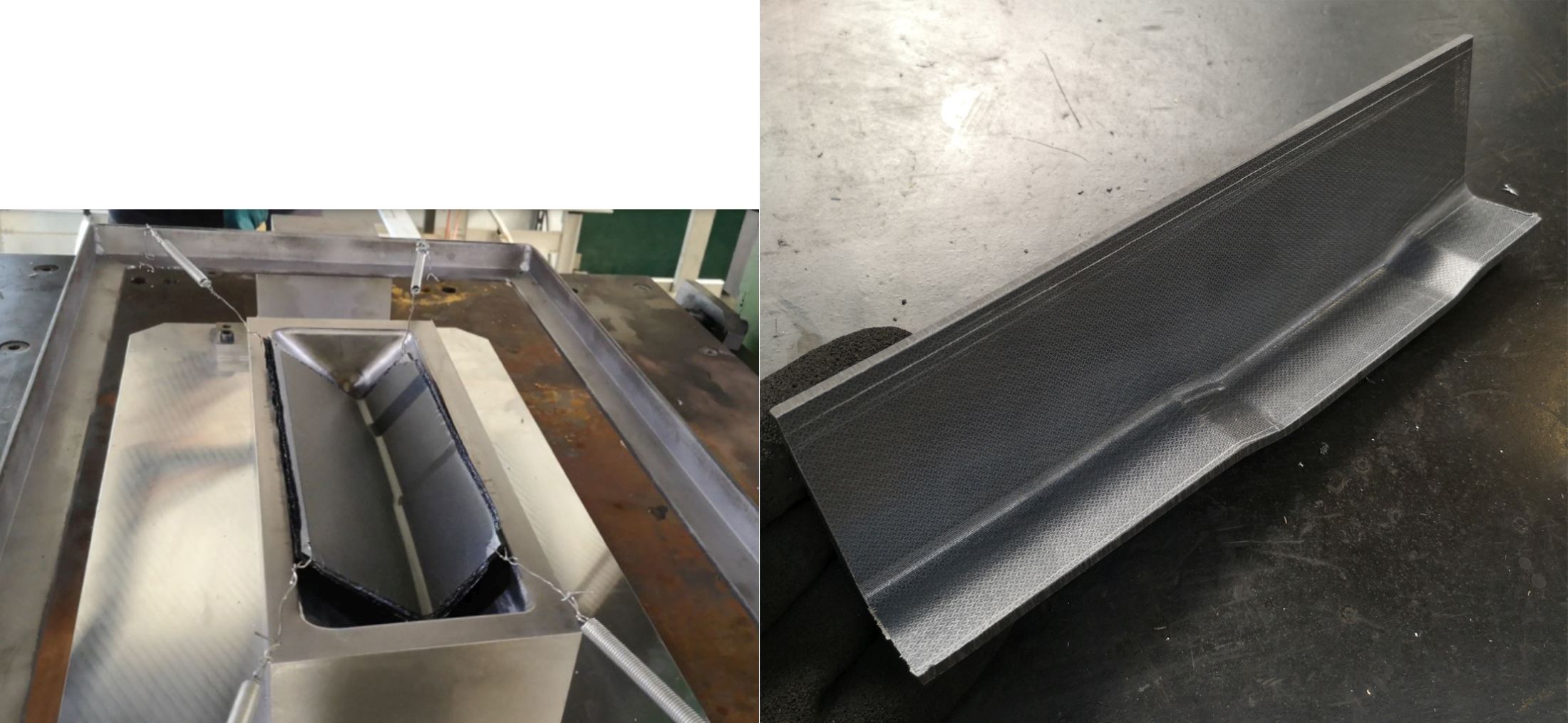
EURECAT investeert om voorop te blijven lopen in de ontwikkeling van composiettechnologie, zegt Lagraña. “Wij geloven dat de druk voor een schoon milieu het gebruik van composieten in al het transport drastisch zal verhogen, en dat betaalbaarheid en prestaties samen zullen gaan. Daarom richten we ons op geautomatiseerde, out-of-autoclave-technologieën om onze klanten aan te bieden.”
Blijf op de hoogte van mijn aanstaande blog over de projecten Clean Sky 2 STUNNING en MECATESTERS, waarin de ontwikkeling van gelaste TPC-beugels voor de Multifunctional Fuselage Demonstrator en een volledige karakterisering van PAEK voor dit project worden besproken. Ik zal ook meer in detail bloggen over Synthesites en meer over CETMA's ontwikkelingen op het gebied van composieten. 2020 wordt een zeer interessant jaar voor composieten!
Hars
- Thermoplastische honingraatsandwich voor overmolding tot dunnere lichtgewicht composieten
- Aanpassen van ultrasone sensoren voor procesoptimalisatie en controle van composieten
- Herverwerkbare, herstelbare en recyclebare epoxyharsen voor composieten
- Combinatie van AC- en DC-diëlektrische metingen voor het bewaken van de uitharding van composieten
- Solvay, Leonardo lanceren gezamenlijk onderzoekslab voor thermoplastische composieten
- Meerlaagse thermoplastische tapes, AFP en harsinfusie voor meer democratische composieten
- Thermoplastische deur een primeur voor autocomposieten
- LANXESS breidt productiecapaciteit voor continue vezelversterkte thermoplastische composieten uit
- TPAC en TPRC ontwikkelen recyclingproces voor thermoplastische composieten
- Thermoplastische composieten lassen
- Consortium thermoplastische composieten streeft naar productie in hoog volume voor Automotive en Aerospace