Tepex versterkt demonstrator hoofdsteun kinderzitje
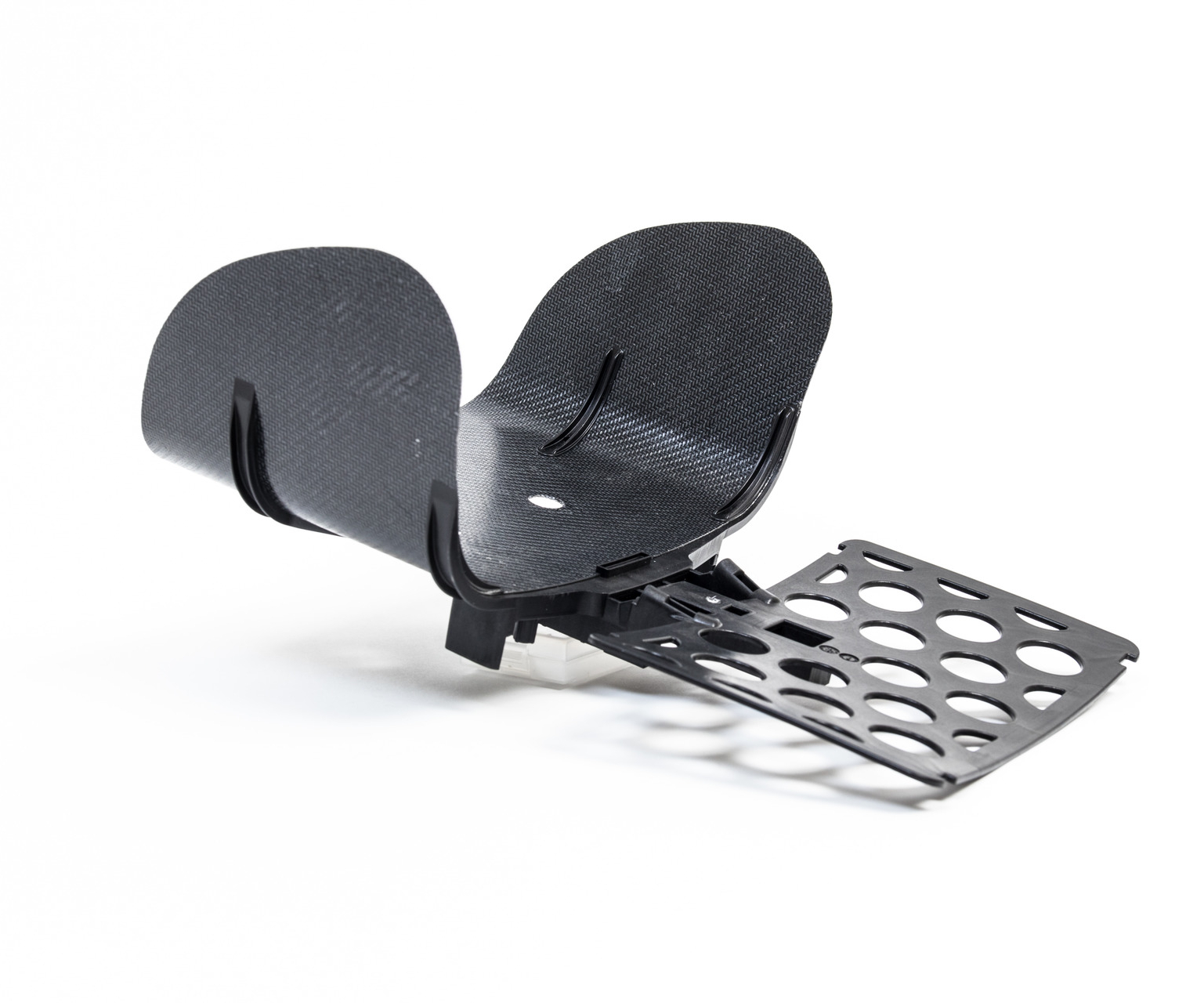
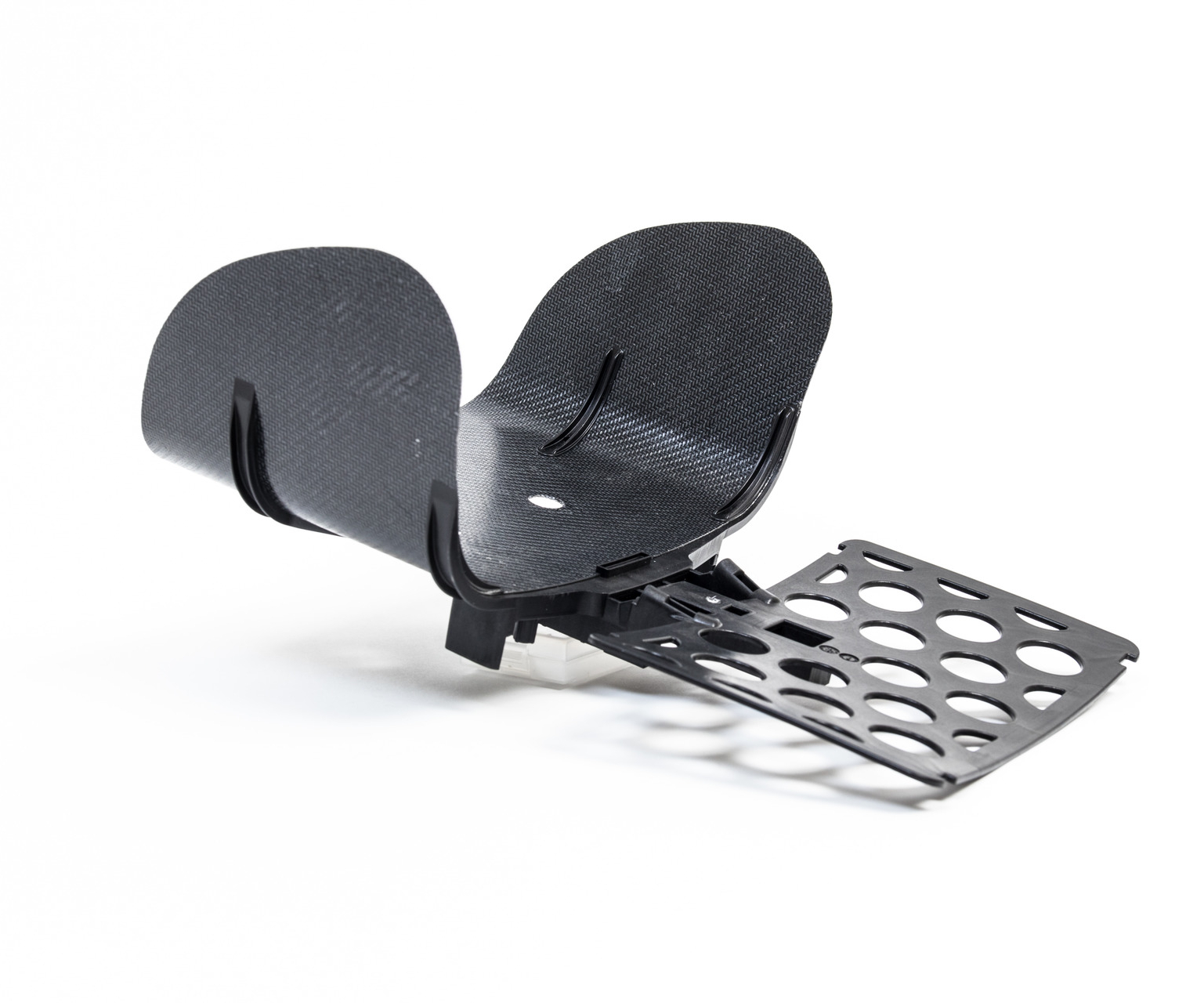
Tepex continu-vezelversterkte thermoplastische composietmaterialen van LANXESS (Pittsburgh, Pa., V.S.) hebben potentieel aangetoond voor een verscheidenheid aan automobieltoepassingen - die CW heeft recentelijk onder meer ondersteuning geboden voor een hybride metaal-composiet A-stijl voor auto's, een achterbankschaal voor auto's en een demonstratiemodel voor de armsteun in de middenconsole. Een recente case study van het bedrijf voegt lichtgewicht constructie van structurele veiligheidscomponenten toe aan de lijst.
LANXESS ontwikkelde onlangs een hoofdsteun voor kinderzitjes als technologiedemonstratie om de kansen van materialen op deze markt te illustreren. Het onderdeel wordt geproduceerd in een deeltjesschuim composiet spuitgietproces (PCIM).
"Het inzetstuk van Tepex kan het gewicht van de hoofdsteun tot 30% verminderen in vergelijking met de commercieel geproduceerde componentvariant - en ook met vergelijkbare goede crashprestaties. Het vereenvoudigt ook het productieproces”, zegt Dr. Klaus Vonberg, van de Tepex Automotive Group bij LANXESS. Tepex wordt ontwikkeld en geproduceerd door LANXESS-dochter Bond-Laminates GmbH (Brilon, Duitsland).

De demonstrator is het resultaat van een transnationaal onderzoeksproject gefinancierd door het Duitse federale ministerie van Economische Zaken en Energie als onderdeel van het Centraal Innovatieprogramma voor Kleine en Middelgrote Ondernemingen (MKB) (Duits acroniem:ZIM). Deelnemen aan dit programma zijn de afdeling lichtgewicht constructies en polymeertechnologie (SLK) van de Chemnitz University of Technology, Polycomb GmbH (Auengrund, Duitsland) en de fabrikant van kinderzitjes Avinaut (Szarlejka, Polen).
Voor de hoofdsteun ontwikkelden de projectpartners een alternatief productieproces op basis van PCIM. Om de hoofdsteun op individuele plaatsen te versterken en het gewicht te verminderen, gebruikten ze een op maat gemaakt inzetstuk gemaakt van Tepex dynalite 104-FG290(4)/47%. Dit is een op polypropyleen gebaseerd composietmateriaal dat is versterkt met twee lagen doorlopende glasvezelrovings. Het inzetstuk wordt gevormd in een enkel proces met behulp van een spuitgietgereedschap met draaiplaat en aan de achterkant geïnjecteerd met een korte glasvezelversterkte polypropyleenverbinding om de ondersteunende structuur voor de hoofdsteun en rugleuning te integreren. Het geprefabriceerde inzetstuk wordt vervolgens teruggeschuimd in een tweede gereedschap met behulp van deeltjesschuim op basis van geëxpandeerd polypropyleen (EPP).
De referentie-hoofdsteun daarentegen wordt volgens LANXESS momenteel in serie geproduceerd met meerdere afzonderlijke componenten. De draagstructuur bestaat uit lang glasvezelversterkt polypropyleen. Het wordt geassembleerd met een afzonderlijk geschuimd EPP-onderdeel met behulp van vier polypropyleen draagpennen.
“Het nieuwe, sterk geïntegreerde productieproces is niet alleen energiezuiniger dan de vorige procedure, het resulteert ook direct in het afgewerkte onderdeel. Dit vermindert het totale aantal onderdelen van zes naar één, wat ook de productiekosten verlaagt in termen van logistiek en de benodigde machine-uitgaven”, zegt Norbert Schramm, wetenschappelijk assistent aan de Chemnitz University of Technology en hoofd van het ZIM-project daar.
De gewichtsbesparing met de huidige versie van de hoofdsteuncomponent met glasvezel is ongeveer 26%, hoewel projectdeelnemers opmerken dat er potentieel is voor meer. Volgens Schramm:"Als een wapening op basis van koolstofvezels wordt gebruikt in het composiet halffabrikaat en in het spuitgietmateriaal, is het resultaat een assemblage die bijna 30% lichter is."
Voor het project koos de SLK de materialen, analyseerde de composietadhesie, ontwierp de structuur en voerde topologie-optimalisatie uit. Polycomb leidde de ontwikkeling en ontwerpimplementatie van de demonstrator, productie van prototypes en optimalisatie van het systeemconcept. Avinaut analyseerde de krachtoverbrengingsgebieden, ontwikkelde het ontwerp en onderzocht onder meer het crashgedrag van de hoofdsteun en de gehele stoel in realistische botsproeven. LANXESS hielp de projectpartners bij het kiezen van materialen en hielp ook bij taken zoals de ontwikkeling van het hybride gietproces.
LANXESS ziet potentieel voor Tepex en het nieuwe proces in de productie van autostoeltjes, rugleuningen en armleuningen, evenals zitschalen voor nieuwe, zeer complexe zitconcepten in autonome auto's of voor comfortstoelen voor shuttle-, VIP- en gezinsbussen en elektrische voertuigen.
Hars
- Fietszitje
- Eenwieler
- Kinderzitje
- Koolstofvezel toiletbrilhoes
- Quarter Midget Build:3D-geprinte hoofdsteun
- Lanxess voegt twee nieuwe productielijnen toe voor composietmateriaal Tepex
- Lichtgewicht composiet rugleuning, ontwikkeld door Covestro en de Chinese autofabrikant GAC
- Eerste volledig kunststof rempedaal voor batterij-elektrische sportwagen
- Continu-vezelversterkte thermoplastische composiet volledig gemaakt van natuurlijke hulpbronnen
- LANXESS thermoplastische composieten gebruikt in Audi A8 achterbankschaal
- JEC World 2019:Cevotec motorgondeldemonstratie