Vooruitgang met de Multifunctional Fuselage Demonstrator (MFFD)
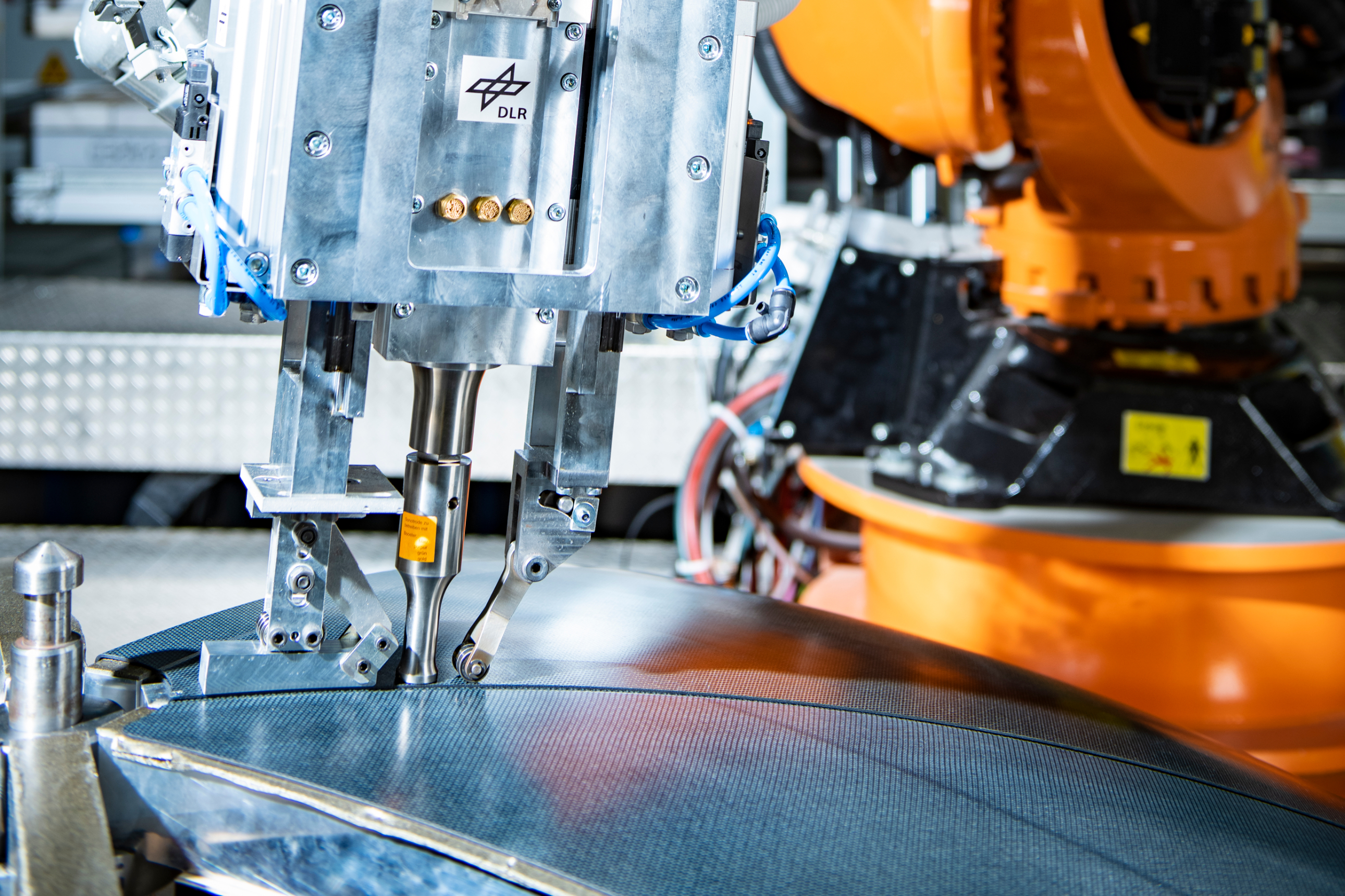
Lagere brandstofemissies en energieverbruik, en de mogelijkheid om commerciële vliegtuigen met één gangpad te produceren met een snelheid van ten minste 60 per maand, vormen de drijvende kracht achter de technologische ontwikkeling van het Europese partnerschap Clean Sky 2 voor de volgende generatie vliegtuigen die in 2035 en daarna de lucht in gaan . Lichtgewicht composieten en snellere, milieubewustere productieprocessen maken deze doelen werkelijkheid, vooral voor het project Multifunctional Fuselage Demonstrator (MFFD).
Het belangrijkste resultaat voor dit project, dat wordt geleid door Airbus (Hamburg, Duitsland) met partners uit de academische wereld en de luchtvaartindustrie, is een 8 meter lange, thermoplastische composiet, enkelbeukige rompdemonstrator voor commerciële vliegtuigen, te produceren door 2022. De MFFD is een van de drie volledige rompsecties die worden geproduceerd binnen Clean Sky 2's Large Passenger Aircraft (LPA) Innovative Aircraft Demonstrator Platform (IADP).
Begonnen in 2014, omvatten de doelstellingen van het MFFD-project:
- Maak productiesnelheden van 60-100 vliegtuigen per maand mogelijk
- Verminder het gewicht van de romp met 1000 kilogram
- Verlaag de terugkerende kosten met 20%.
Om deze doelen te bereiken, worden tientallen individuele projecten en werkpakketten voltooid, waarbij twee hoofdconstructies worden geproduceerd:een bovenste rompschaal en een onderste rompschaal, die aan elkaar worden gelast om de uiteindelijke demonstrator te vormen. In feite is stofvrij verbinden (zonder bevestigingsmiddelen of gaten) via lassen een belangrijk onderdeel van het programma. Beide helften worden vervaardigd uit Toray Cetex TC1225 low-melt polyaryletherketon (PAEK) koolstofvezel thermoplastische prepreg van Toray Advanced Composites (Morgan Hill, Californië, VS). Volgens Dr.-Ing. Lars Larsen, hoofd verbindings- en assemblagetechnologieën bij het Duitse lucht- en ruimtevaartcentrum (DLR; Augsburg, Duitsland), zullen beide helften het gebruik van verschillende productietechnieken testen.
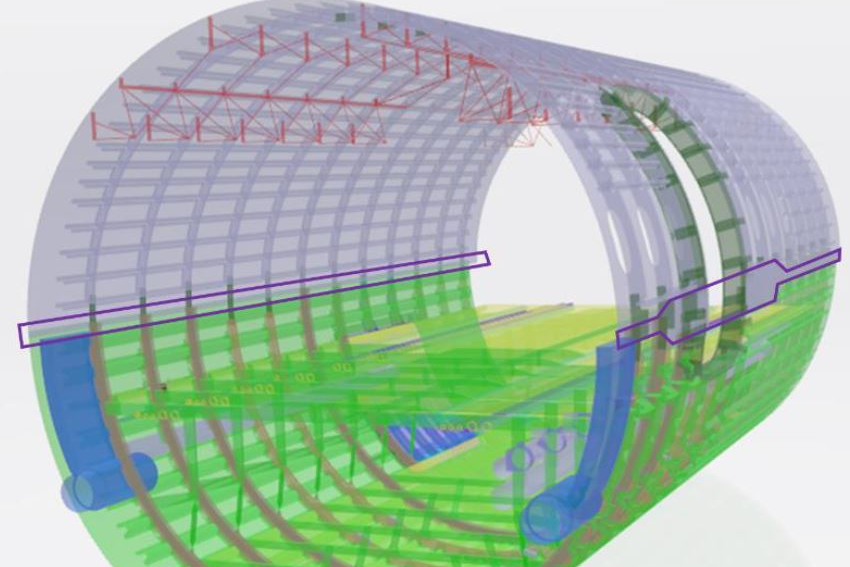
Het onderste deel van de romp van de MFFD wordt geproduceerd door middel van project STUNNING (SmarT multifunctionele en INtegrated thermoplastische fuselaGe), dat zelf vele projecten eronder heeft (zoals MECATESTERS, gericht op inductielassen). Het onderste deel omvat de onderste rompschaal met gelaste stringers en frames, de cabine- en laadvloerstructuur en relevante interieur- en systeemelementen.
STUNNING wordt geleid door GKN Fokker (Papendrecht, Nederland) met belangrijke partners Diehl Aviation (Laupheim, Duitsland), Netherlands Aerospace Centre (NLR; Amsterdam, Nederland) en de Technische Universiteit Delft (TU Delft; Delft, Nederland). Het project heeft tot doel geautomatiseerde assemblageprocessen, thermoplastische fabricage- en lastechnologieën, geïntegreerde ontwerp- en fabricageontwikkeling en geavanceerde elektrische systeemarchitecturen verder te ontwikkelen.
"Onze impact op de industrie is tweeledig:het niveau van automatisering dat we toepassen op de assemblage van de demonstrator en het ontwikkelen van duurzame manieren om onderdelen te produceren", zegt Dr. Bas Veldman, programmamanager bij GKN Fokker.
Volgens een artikel dat Veldman in februari 2020 publiceerde, is modulaire montage van de onderste romp essentieel om het doel van snelle productietijden te bereiken. Om de hoofdhuid van de romp te vervaardigen, worden grote preforms van koolstofvezel/thermoplastische prepreg gelegd door een ultrasone of laserverwarmde automatische tape-legmachine (ATL), maar niet in-situ geconsolideerd. Details worden gelegd door een geautomatiseerde vezelplaatsing (AFP) machine. Robots plaatsen de preforms vervolgens in een vrouwelijke consolidatievorm en na het inpakken wordt de huid geconsolideerd in een autoclaaf. Volgens Veldman worden ook processen buiten de autoclaaf onderzocht. De stringers en frames worden aan de huid gelast.
"Oorspronkelijk was het plan om alle onderdelen dit jaar te laten produceren", zegt Veldman, maar vanwege de vertragingen door het coronavirus:"Het gaat nu ook over naar volgend jaar. Maar we hebben wel een flink aantal onderdelen die nu zijn voltooid”, waaronder veel van de kleinere, geperste onderdelen zoals clips, stutten en beugels die zullen worden gebruikt voor het bevestigen van vliegtuigstoelen en andere componenten. Met de nadruk op duurzame productie, voegt Veldman eraan toe dat sommige clips zijn vervaardigd van hergebruikte restanten van andere onderdelen van de demonstrator, via een Clean Sky 2-project genaamd ECO-CLIP.
Begin 2020 omvat het consortium dat de 8 meter lange bovenschaal produceert Airbus, Premium Aerotec (Augsburg, Duitsland), dat de industriële en structurele ontwerpleider is; DLR, verantwoordelijk voor de huidopmaak en de ontwikkeling van lastechnologie; en Aernnova (Vitoria-Gasteiz, Spanje), die de stringers produceert.
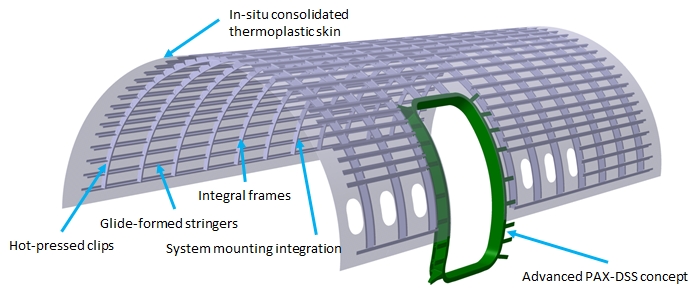
Om de lucht- en ruimtevaartindustrie over te laten stappen op duurdere thermoplastische materialen, zegt Larsen:"We moeten laten zien dat we kosten kunnen besparen tijdens de productie." Het bovenste helftconsortium ontwikkelt nieuwe geavanceerde vezelplaatsingstechnologie (AFP) met met name in-situ consolidatie voor de koolstofvezel/PAEK-huidlay-up, evenals de industrialisatie van continu ultrasoon lassen en weerstandslassen voor integratie van de stringers, frames en andere componenten, waardoor de veiligheid wordt verbeterd en de kosten worden verlaagd. DLR bouwt eerst een 1 meter lange pre-demonstrator-testomhulling om de technologieën te valideren voordat de volledige demonstrator wordt gebouwd, en is van plan om de huid voor de pre-demonstratorschil eind 2020 te laten vervaardigen. de stringers staat gepland voor begin 2021.
De volledige versies van beide helften zullen naar verwachting eind 2021 klaar zijn. Zodra ze klaar zijn, zullen ze worden gelast in de laatste demonstrator van het Fraunhofer Institute for Manufacturing Technology and Advanced Materials IFAM (Stade, Duitsland).
Hars
- Verder gaan dan de basis:machine learning en AM
- De voordelen van composiet vliegtuigontwerp in vliegtuigen van alle formaten
- Waarom automatisering de enige weg vooruit is voor productie
- 5 robottoepassingen in de lucht- en ruimtevaartindustrie
- Het productielandschap:terugkijken en vooruitkijken
- Drie voordelen van het verplaatsen van uitgavenbeheer naar de cloud
- Vervaardiging van de bovenste helft van de Multifunctional Fuselage Demonstrator (MFFD)
- De eerste composiet rompsectie voor de eerste composiet commerciële jet
- De composietenwereld in Israël en de VS dienen
- Wat is de doorlaatspanning van de diode?
- Stikstofproductie in de lucht- en ruimtevaartindustrie