Ontwerpen voor geautomatiseerde composietproductie van aerostructuren met een klein volume
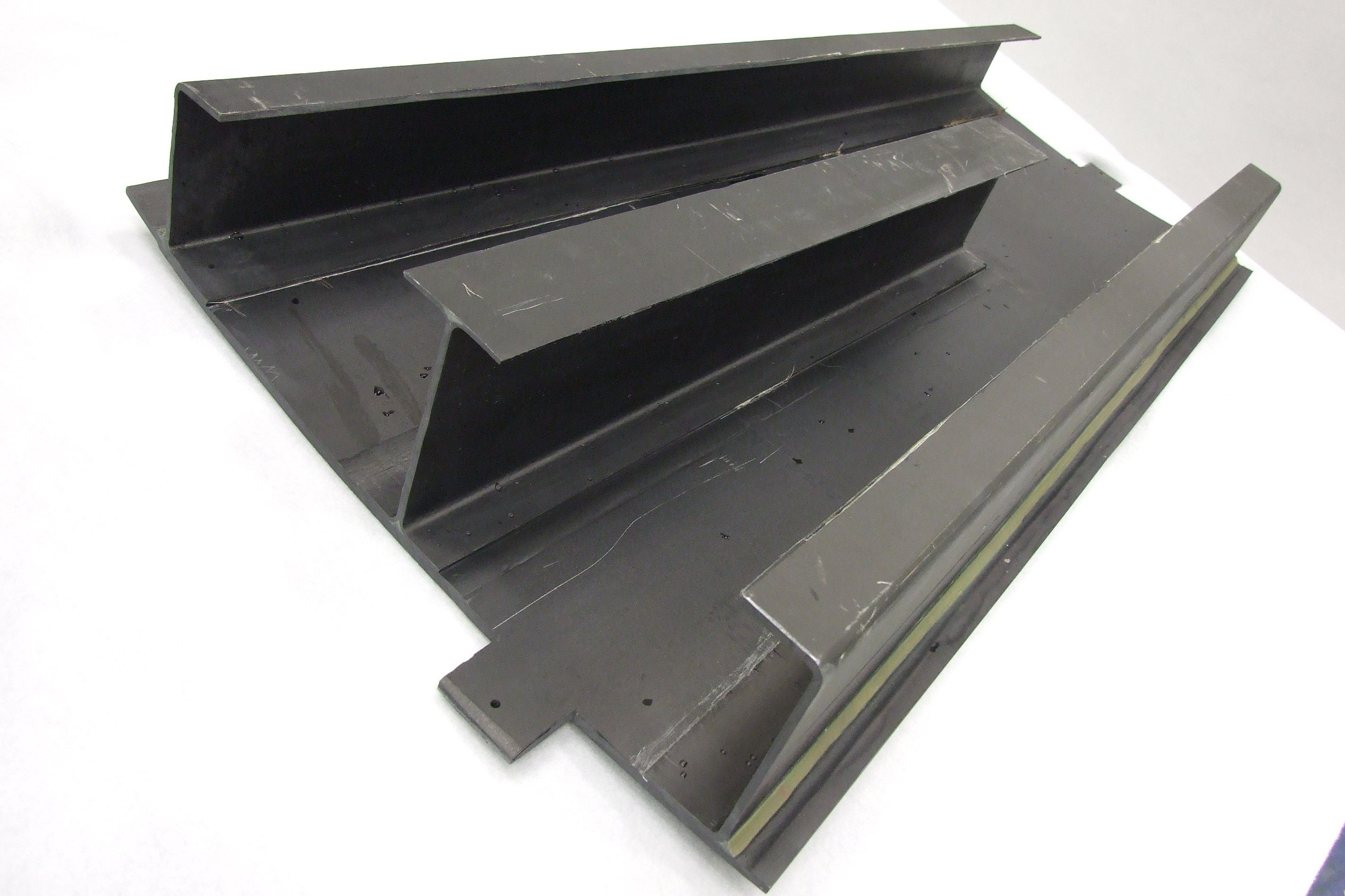
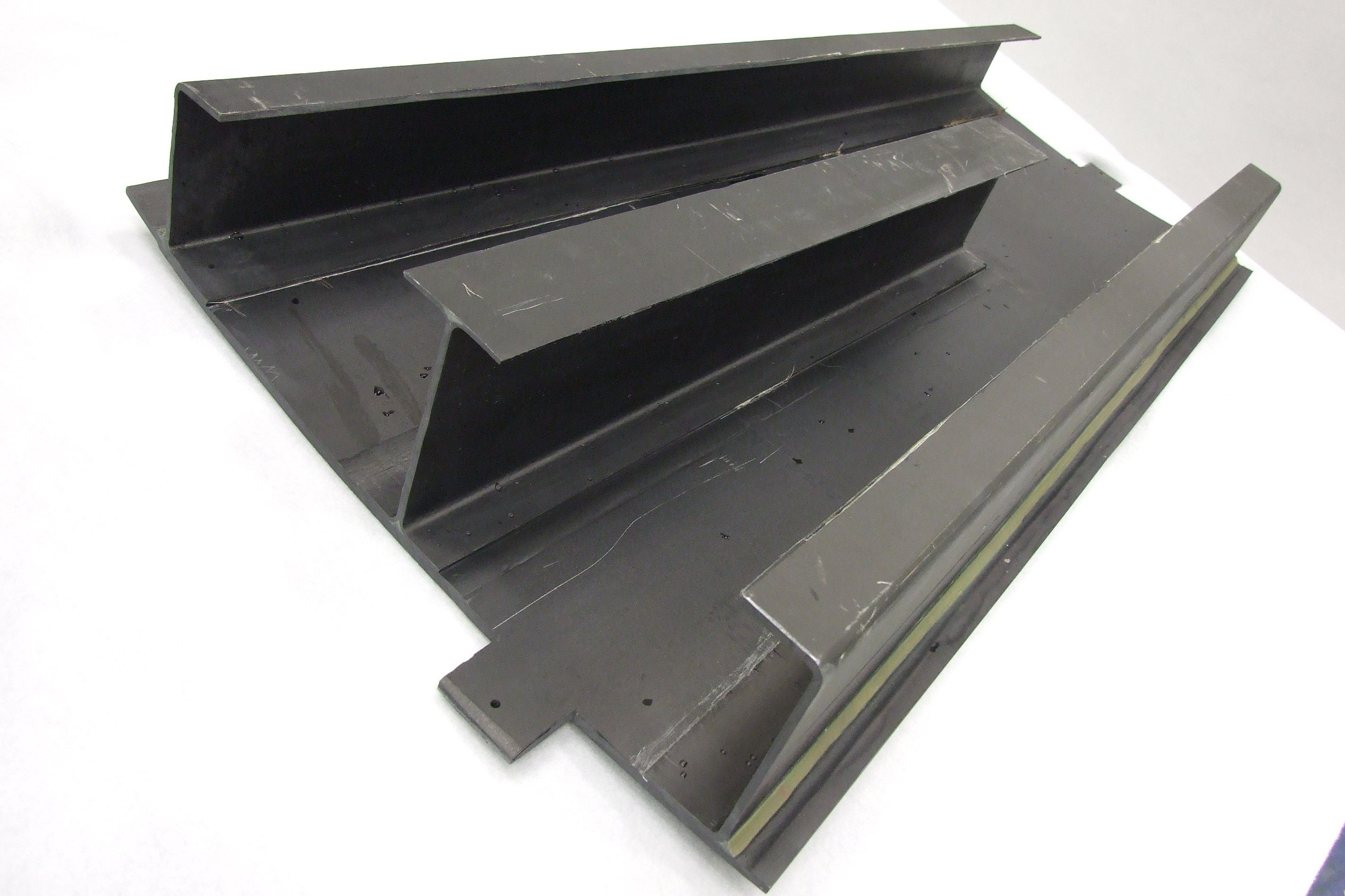
De fabricage van composiet aerostructuren voor commerciële vliegtuigen omvat meer dan 50 jaar en is gestaag gevorderd van kleinere onderdelen tot zeer grote primaire structuren - romp, vleugels, empennage, motoren - ontwikkeld in de vroege jaren 2000 voor de Boeing 787 en de Airbus A350. Het overgrote deel van deze evolutie was afhankelijk van het gebruik van in de autoclaaf uitgeharde koolstofvezel/epoxy prepregs, aanvankelijk met de hand gelegd en vervolgens, uiteindelijk, via geautomatiseerde vezelplaatsing (AFP), geautomatiseerde tape-legging (ATL) en andere machinale processen.
Deze materiaal- en procestechnologieën (M&P) waren geschikt voor de brede 787 en A350 die, vóór de pandemie, een bouwsnelheid hadden van 10-15 per maand. Aangezien Boeing en Airbus echter naar de toekomst kijken en overwegen om composietmaterialen toe te passen in primaire constructies van vliegtuigen met één gangpad die naar verwachting een bouwsnelheid van 60-100 per maand zullen hebben, zullen ontwerp en M&P de voorkeur geven aan high-rate, out-of-of -autoclaaf (OOA), sterk geautomatiseerde processen. Deze processen omvatten onder andere harsoverdrachtsgieten (RTM), persvormen en vloeibare harsinfusie.
Maar zelfs als high-rate fabricage de commerciële lucht- en ruimtevaartsector zal domineren, fabricage van composiet aerostructuren voor low-rate vliegtuigen - inclusief regionale vliegtuigen en zakenjetprogramma's - zullen niet alleen blijven bestaan, maar kunnen en moeten profiteren van dezelfde kosten-, ontwerp- en M&P-innovaties die zullen worden ingezet in hoogwaardige programma's.
Met dit alles in gedachten lanceerde het Europese Clean Sky 2-programma OPTICOMS — Opti mized Com posite S structuren voor kleine vliegtuigen. OPTICOMS is een consortium onder leiding van lucht- en ruimtevaartfabrikant Israel Aerospace Industries (IAI, Lod, Israël) met partners die innovatieve automatiseringstechnologieën, materialen, software, gereedschappen en machines leveren. Het doel van OPTICOMS is het evalueren van een low-rate productie wing box-ontwerp met geautomatiseerde fabricage, geïntegreerde structuren, OOA-behandeling, grote structurele verlijming, innovatieve fabricage- en assemblagetools, structurele gezondheidsmonitoring van bondlines en virtuele testen.
Arnold Nathan, directeur van R&D voor de luchtvaartgroep bij IAI en manager van OPTICOMS, zegt:"Elke keer dat we automatisering proberen te betrekken bij een [discussie] over de fabricage van composieten, horen we onze klanten vaak zeggen:'Automatisering is goed, maar alleen wanneer je een groot productievolume hebt.' OPTICOMS is opgericht om te kijken of je automatisering kunt rechtvaardigen als je niet hebben een grootschalige productie. Kan automatisering van composietproductie concurrerend en kosteneffectief zijn voor kleine volumes?”
Vleugelontwerp
OPTICOMS is ontstaan uit een Clean Sky 2-verzoek van de Italiaanse fabrikant van zakenvliegtuigen Piaggio Aerospace (Genua) voor de ontwikkeling van een volledig samengestelde alternatieve vleugel voor zijn P180 Avanti negen-passagier business twin turboprop. De vleugelkast is 6,8 meter lang, 0,71 meter breed aan de wortel en 0,28 meter breed aan de punt. Piaggio, zegt Nathan, wilde graag een alternatief voor de volledig metalen legacy wingbox evalueren - een alternatief met dezelfde afmetingen, maar met een lager gewicht (20%). Verder zouden de kosten met 20-30% moeten worden verlaagd in vergelijking met de conventionele fabricage van composietvleugelkasten. IAI en zijn partners wonnen het contract en begonnen in 2016 met Piaggio samen te werken.
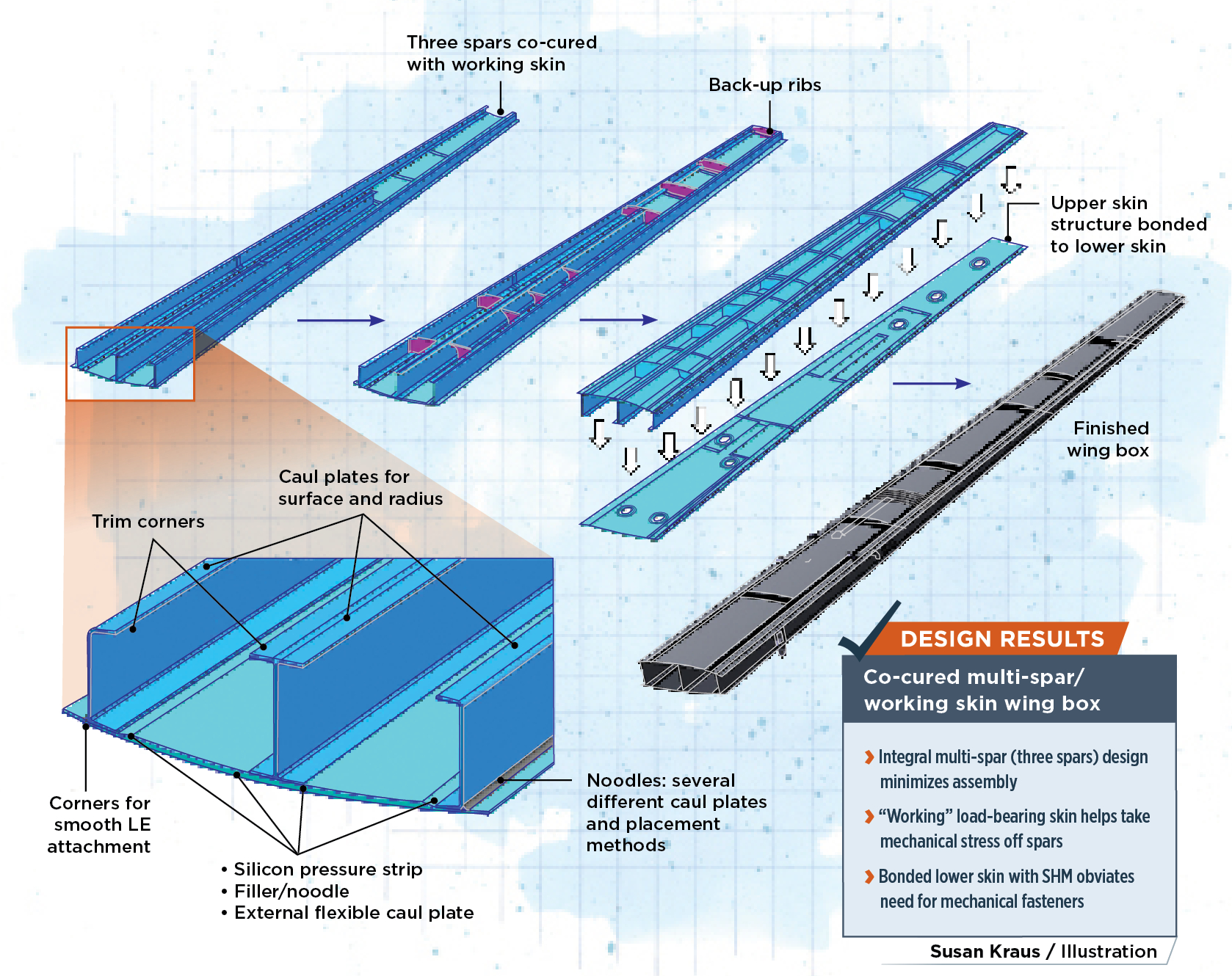
OPTICOMS is een meerdelig programma dat is ontworpen om een reeks zeer gedetailleerde en nauwgezet uitgevoerde handelsstudies uit te voeren om het optimale vleugelontwerp, de materiaalcombinatie en het OOA-fabricageproces te evalueren en te bepalen voor de geautomatiseerde fabricage van een volledig samengestelde vleugelkast met een klein volume.
IAI en OPTICOMS, zegt Nathan, besloten al vroeg dat het zich zou concentreren op en evalueren van het gebruik van drie productieprocessen die door drie partners worden geleverd:Geautomatiseerde robotische pick-and-placement van droge en prepregged stoffen, geleverd door Techni-Modul Engineering (TME, Coudes, Frankrijk); geautomatiseerde vezelplaatsing (AFP) van droge en prepregged tows, geleverd door Coriolis Composites (Queven, Frankrijk); en geautomatiseerde technologie voor het plaatsen van droge materialen (ADMP), geleverd door Danobat (Elgoibar, Spanje). De selectie van deze technologieën en partners zou van cruciaal belang zijn om IAI te begeleiden tijdens haar multi-variant handelsstudies.
Ontwerpresultaten
- Integraal multi-spar (drie rondhouten) ontwerp minimaliseert montage
- Een "werkende" dragende huid helpt de mechanische belasting van de rondhouten weg te nemen
- Gebonden onderhuid met SHM maakt mechanische bevestigingen overbodig
De eerste stap in dit handelsonderzoek was ontwerpevaluatie. Deze inspanning werd bij IAI geleid door Adam Sawday, ingenieur structureel ontwerp voor geavanceerde technologieën. Sawday zegt dat hij en IAI het ontwerp van de vleugel met een schone lei hebben bekeken en meer dan 18 concepten in verschillende architecturen hebben bestudeerd. Ontwerpen vielen al snel in een van de twee categorieën. De eerste maakt gebruik van een "werkende" huid waarin de vleugelkasthuid een dragende structuur wordt. De tweede maakt gebruik van niet-werkende vellen met geladen rondhoutdoppen. Binnen deze categorieën omvatten ontwerpen een traditioneel concept met ribben, liggers en twee liggers, of, als alternatief, het gebruik van drie liggers - multi-spar genoemd - zonder ribben of liggers. Verschillende concepten overwogen ook het gebruik van een sandwichpaneelconstructie die een semi-werkende huid produceert.
"Onze mantra was om de productie-inspanningen te verminderen en de montage-inspanningen te verminderen", zegt Sawday. "En we geloven dat als je een efficiëntere structuur kunt ontwikkelen die meer integraal is, je een goedkopere en lichtere structuur krijgt."
Sawday zegt dat de ontwerpen zijn gemeten aan de hand van een reeks statistieken om te beoordelen of ze in staat zijn om de doelstellingen voor kosten en gewicht van het programma te halen. Deze statistieken omvatten:materiaalkosten, ontwerpcomplexiteit, fabricagekosten van componenten, montagekosten, kosten voor niet-destructief testen (NDT), kosten voor gereedschap en jigging, gewicht, sterkte, technologiegereedheidsniveau (TRL), ecologische overwegingen, risicoprofiel, robuustheid en betrouwbaarheid. Hiervan waren de zwaarste criteria gewicht, fabricage- en montagekosten, ontwerpcomplexiteit, TRL en risicoprofiel.
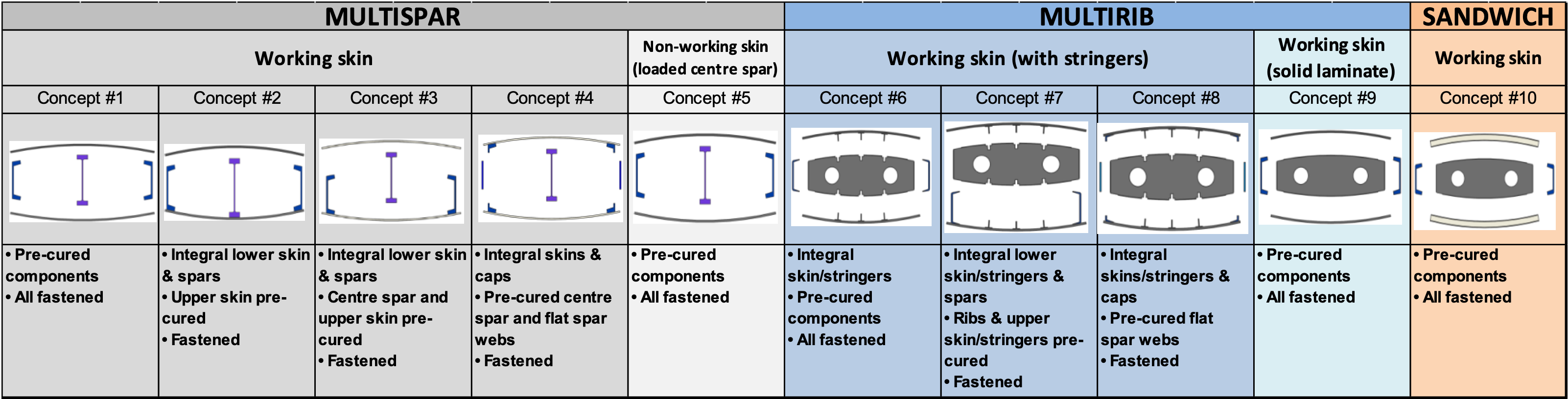
Omlaag selecteren naar definitief ontwerp
Gegevens uit deze evaluatie hielpen IAI om de ontwerpconcepten te selecteren voor 10 finalisten. Vier waren multi-spar/werkende huid, één was multi-spar/niet-werkende huid met geladen rondhouten, vier waren multi-rib/werkende huid met stringers, één was multi-rib/werkende huid zonder stringers en één was sandwich structuur/werkende huid zonder stringers. Elk ontwerp bood verschillende combinaties van pre-curing, co-curing, bonding of mechanische bevestiging.
Om tot het definitieve ontwerp te komen, moest er nog een ronde van handelsonderzoeken volgen waarbij veel van dezelfde criteria werden gebruikt als in het eerste onderzoek. Elk ontwerp kreeg een handelswaarde, gebaseerd op hoe goed het aan de criteria voldeed. "We hadden deze grote ruiltafel en elke ontwerpoptie had een waarde, en dit hielp ons de sterkste optie te zien", zegt Sawday.
Er was vanaf het begin één ontwerp dat consistent goed presteerde in de handelsstudies en waarschijnlijk als beste uit de bus zou komen, merkt Sawday op. En dat deed het. Intern gesynchroniseerd als multi-spar/working skin #2, het heeft een sterk geïntegreerde en co-cured bovenhuid en drie rondhouten. Deze worden vervolgens gehecht aan een lagere huid met toegangspanelen. Selectief geplaatst tussen de rondhouten is een reeks "back-up" ribben, ontworpen om de huid te ondersteunen, die de meeste buigbelastingen draagt.
"De meest gunstige structuren die we hebben ontwikkeld", zegt Sawday, "waren die met multi-spars, waarbij de huid dragend wordt. De rondhouten worden dan eenvoudigere en dunnere constructies, en lang niet zo zwaar als bij traditionele composietvleugelontwerpen. We dachten dat als we deze rondhouten heel eenvoudig konden maken, met een constante dwarsdoorsnede, dat een hoop kopzorg en veel afval zou besparen.”
Sawday zegt dat het gebonden integrale multi-spar/working skin-ontwerp veelbelovend was vanwege de lagere montagekosten, het lage gewicht, het gemak van automatisering en het algehele lage aantal onderdelen. De vraag bleef echter:welke materialen en welke productieprocessen zouden het meest geschikt zijn om dit ontwerp tot leven te brengen?
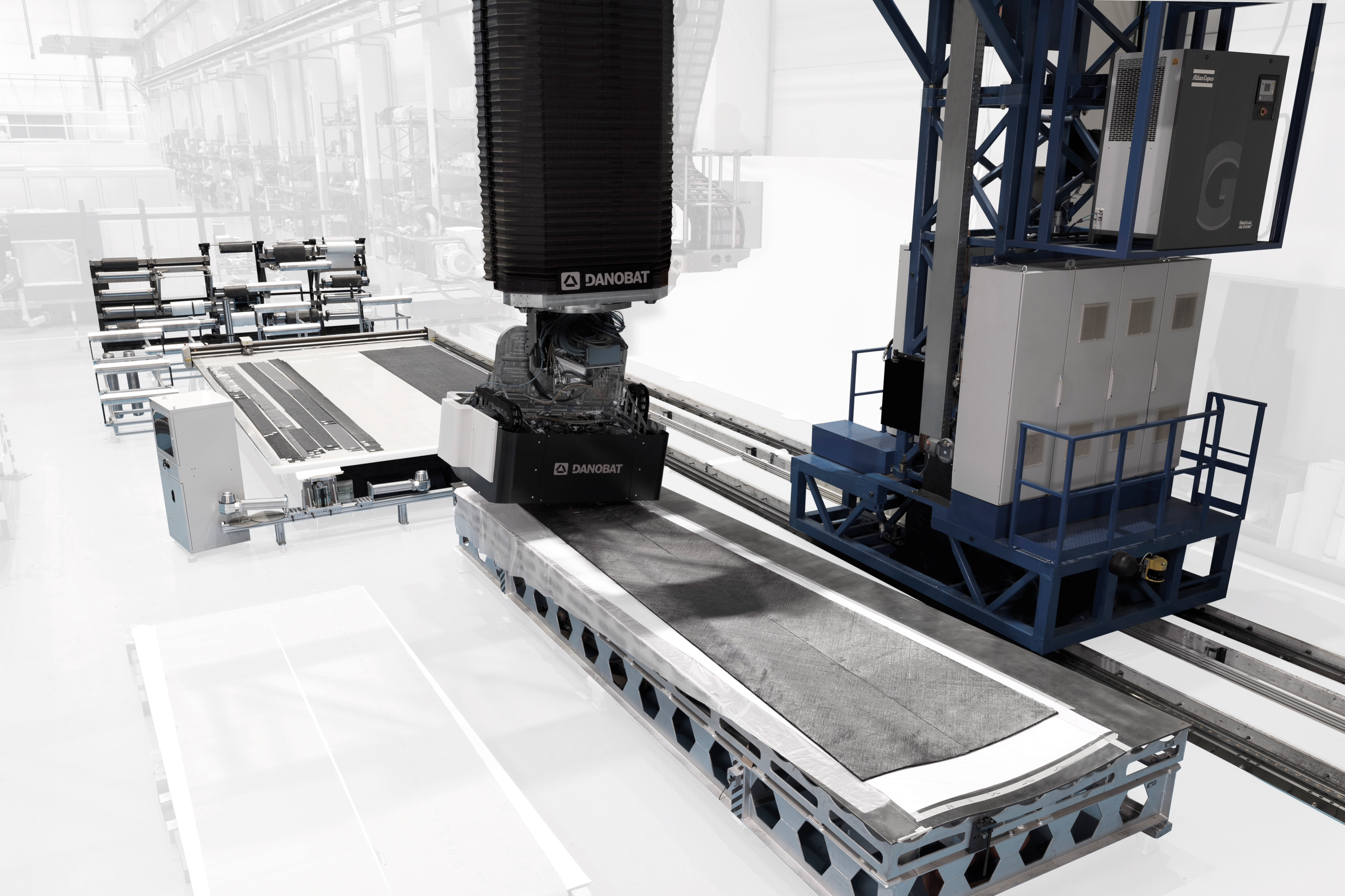
M&P handelsonderzoeken
Als eerste waren er de materialenhandelstudies. Deze werden op IAI uitgevoerd door Yaniv Yurovitch, ingenieur composietmaterialen. Hij zegt dat OPTICOMS is begonnen met het evalueren van prepregs van OOA-koolstofvezel, droge koolstofvezels (tapes en stoffen) en harsen op basis van aanbevelingen van Piaggio, IAI en technologiepartners. Het resultaat was een lijst van 35 gekwalificeerde en nieuwe materialen.
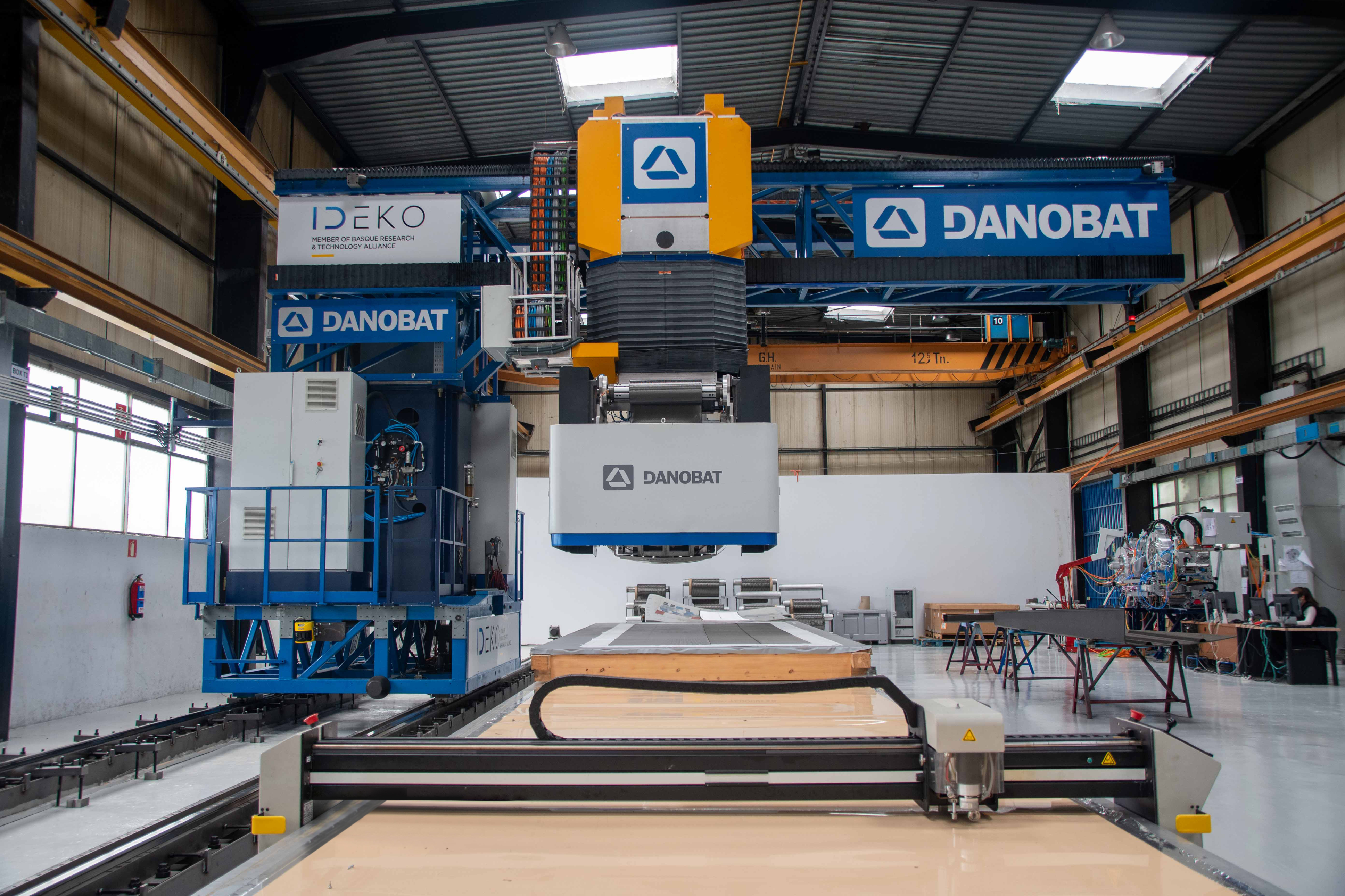
Deze eerste groep materialen werd vervolgens gescreend op basis van de meest cruciale parameters voor het OPTICOMS-project:kosten, glasovergangstemperatuur (Tg ), viscositeit (voor infusie of injectie) en geschiktheid voor geautomatiseerde layup-technologieën. Deze evaluatie bracht de lijst met materialen terug van 35 naar 20 prepregs, droge vezels en harsen.
Van elk van deze 20 materialen werden monsters besteld; Yurovitch maakte vervolgens coupons en voerde mechanische tests uit als onderdeel van de volgende down-select. "Het was een heel groot werkpakket", zegt Yurovitch. "Het stelde ons in staat om meer beslissingen te nemen en de laatste drie materialen te selecteren." Die vezel/hars-combinaties zijn:
- Toray Composites Materials America's (Tacoma, Wash., V.S.) 2510 koolstofvezel/epoxy prepreg.
- Hexcel's (Stamford, Conn., V.S.) HiTape koolstofvezel UD-tapes, voor gebruik met Hexcel's HexFlow RTM6 epoxyhars.
- Kruisvrije koolstofvezelstof (NCF) geleverd door SAERTEX (Saerbeck, Duitsland), te combineren via infusie met PRISM EP2400 geharde epoxy van Solvay Composite Materials (Alpharetta, Ga., VS).
Deze lijst geeft duidelijk de voorkeur aan het gebruik van droge vezels, wat op zijn beurt de voorkeur geeft aan infusie als fabricageproces. Nathan zegt dat dit deels wordt veroorzaakt door de uitdaging om de houdbaarheid van prepreg in een omgeving met een laag volume te beheren. "Als je het hebt over een productie met een laag volume, wil je echt niet veel prepreg bij je hebben en je zorgen maken over het beheer van de houdbaarheid", zegt hij. "Droge vezels hebben dat probleem niet."
Deze drie materialen zijn ook gecombineerd met een of meer van de productieprocessen die voor OPTICOMS zijn geselecteerd:Toray prepreg komt overeen met pick-and-place en AFP, Hexcel's HiTape/RTM6 komt overeen met AFP en pick and place, en de SAERTEX NCF komt overeen met pick-and-place of ADMP.
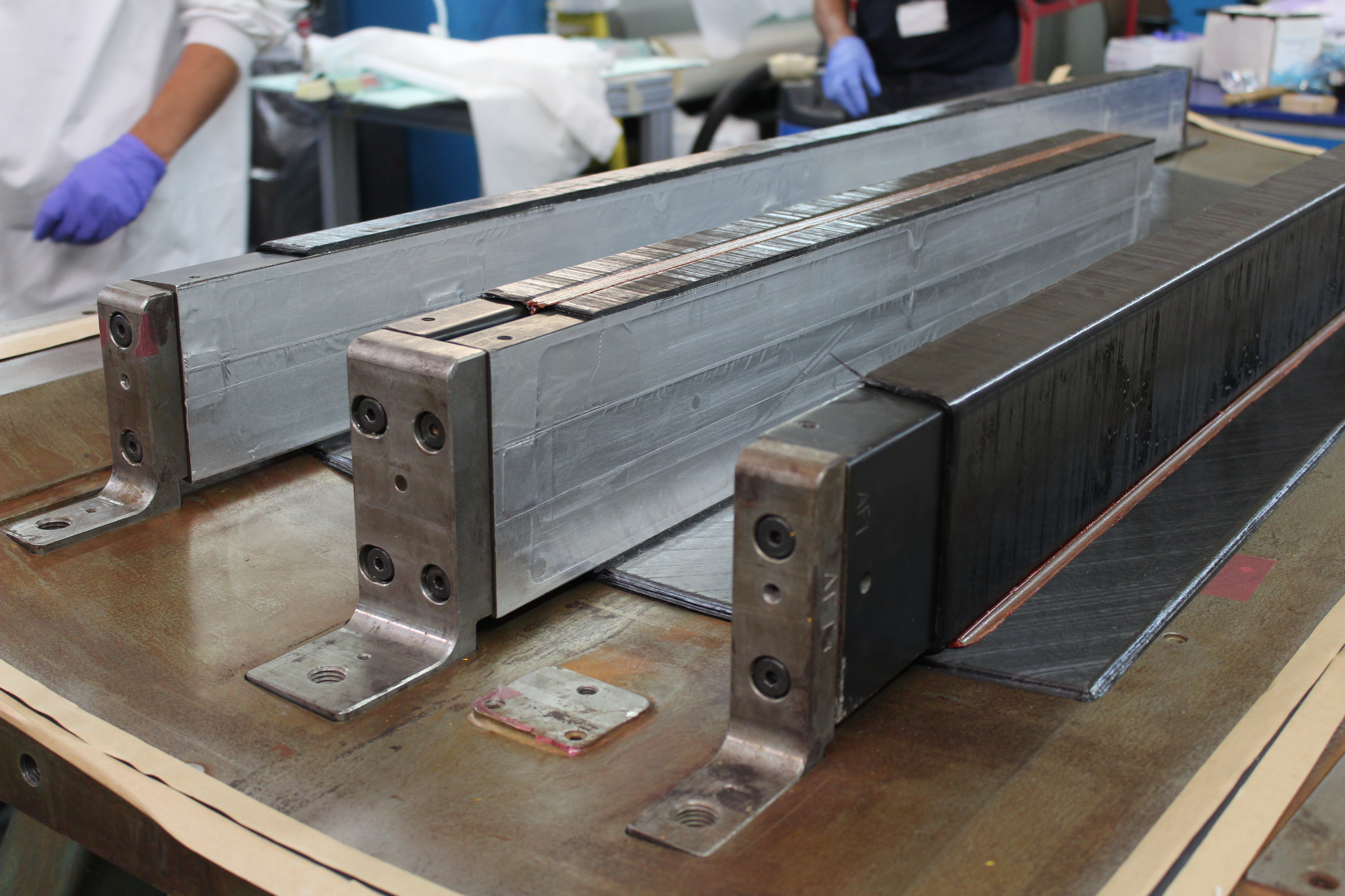
De handelingen rond de geautomatiseerde productieprocessen - die het meest geschikt zijn voor welk type onderdeel - worden nog steeds uitgevoerd door IAI en OPTICOMS. Voorlopige resultaten, zegt Nathan, wijzen echter beslist technologieën in bepaalde richtingen. De ADMP-technologie van Danobat, oorspronkelijk ontwikkeld voor de snelle plaatsing van brede stoffen bij de productie van windturbinebladen, is bijvoorbeeld even efficiënt gebleken in OPTICOMS. De technologie is volwassen geworden tijdens OPTICOMS en de robuustheid en betrouwbaarheid zijn verbeterd, maar het is nog steeds een minder volwassen lay-uptechnologie voor de ruimtevaart in vergelijking met AFP.
Omgekeerd is AFP met het Coriolis-systeem, met zijn uitgebreide ervaring in de ruimtevaart, een volwassen en nauwkeurige technologie, maar heeft deze langere opsteltijden in vergelijking met ADMP en vereist relatief frequente inspectie om te controleren op afwijkingen. Coriolis heeft tijdens het OPTICOMS-project opmerkelijke vooruitgang geboekt met de ontwikkeling van inline, realtime inspectie van de lay-out om deze uitdaging het hoofd te bieden, zegt Nathan. Ten slotte lijkt de pick-and-place-technologie van TME, ontworpen om de overdracht van gesneden weefsels van de snijtafel naar de mal te automatiseren, het meest effectief voor kleinere, discrete onderdelen, zoals de back-up ribben in de multi-spar/working huidontwerp.
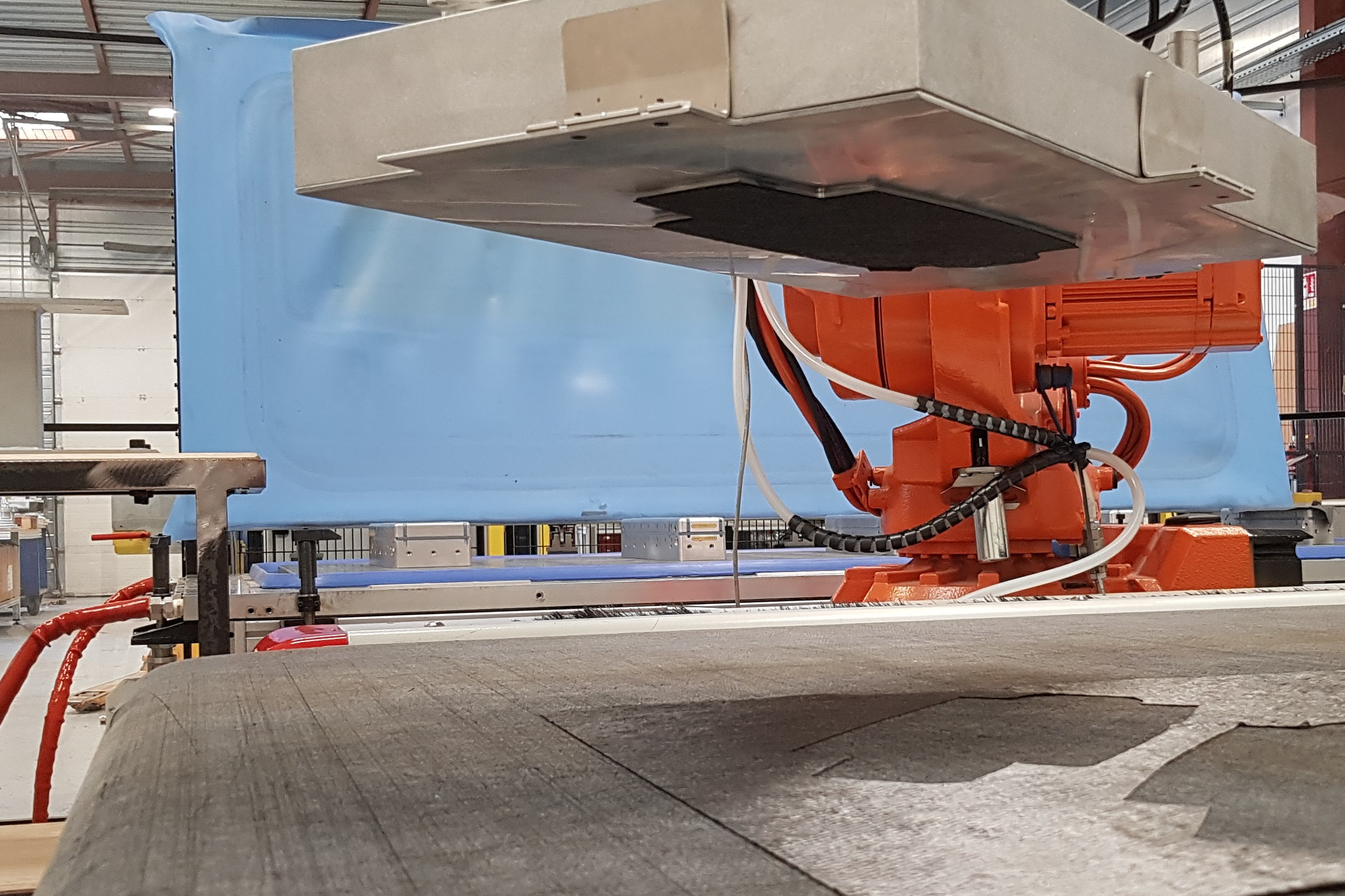
Volgende stappen
OPTICOMS ligt op schema om de doelstellingen op het gebied van automatisering, kostenbesparing en gewichtsbesparing te halen die door het programma zijn uiteengezet, zegt Nathan, hoewel er nog enkele maanden werk moeten worden verzet om de productieprocessen en assemblageoplossingen te evalueren.
"Dit is een belangrijk punt over OPTICOMS", legt hij uit. “We hadden een robuuste down-selectie van het ontwerp. We hadden een down-selectie van het materiaal. We hadden een down-selectie van de processen. Dit alles kost tijd en moeite. Dit is een van de unieke aspecten van het project.”
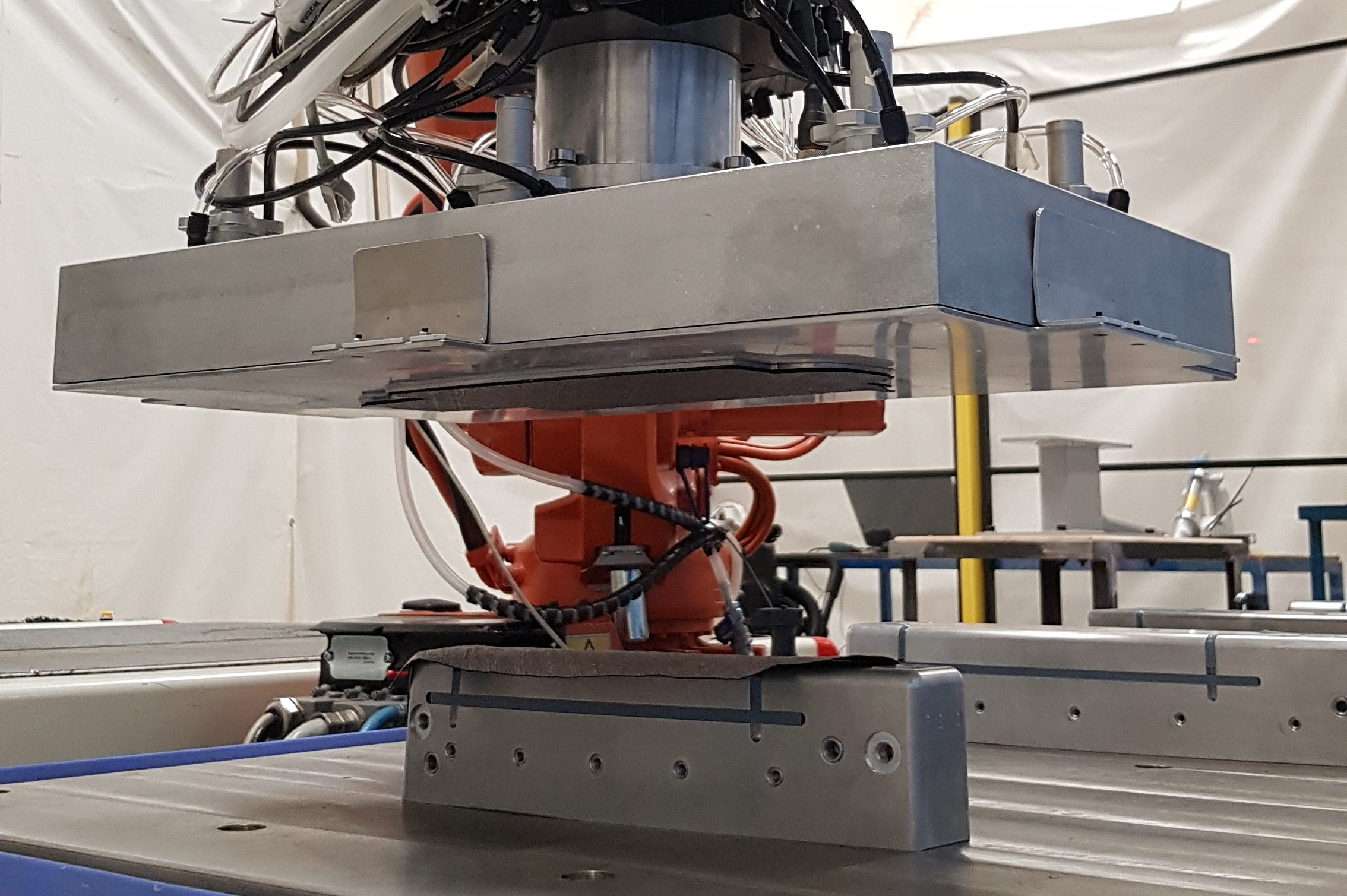
OPTICOMS heeft drie oproepen tot het indienen van voorstellen (CFP) geïnitieerd voor technologieën en hardware om de projectdoelen te ondersteunen, te waarborgen en te verbeteren. De succesvolle voorstellen werden Clean Sky 2-projecten, geassocieerd met en aanvullend op de OPTICOMS 'moeder'-kernpartner - die allemaal samenwerkten aan een gemeenschappelijk doel.
De eerste poging in deze ontwikkeling is FITCoW, dat tot doel heeft een nieuw, integraal koolstofvezelgereedschapssysteem te ontwikkelen voor de co-cure van de werkende huid en drie rondhouten. De lijst met doelen van FITCoW is ambitieus:50% reductie van de kosten van gefabriceerde onderdelen, 30% reductie van de gereedschapskosten (vergeleken met metalen alternatieven), 20% reductie van de productietijd in vergelijking met autoclaaf- en OOA-alternatieven, 40% vermindering van CTE-mismatch in vergelijking met Invar-tooling , 20% reductie in verwarmings- en koeltijd en 40% reductie in inspectietijd dankzij betere dimensionale controlemogelijkheden.
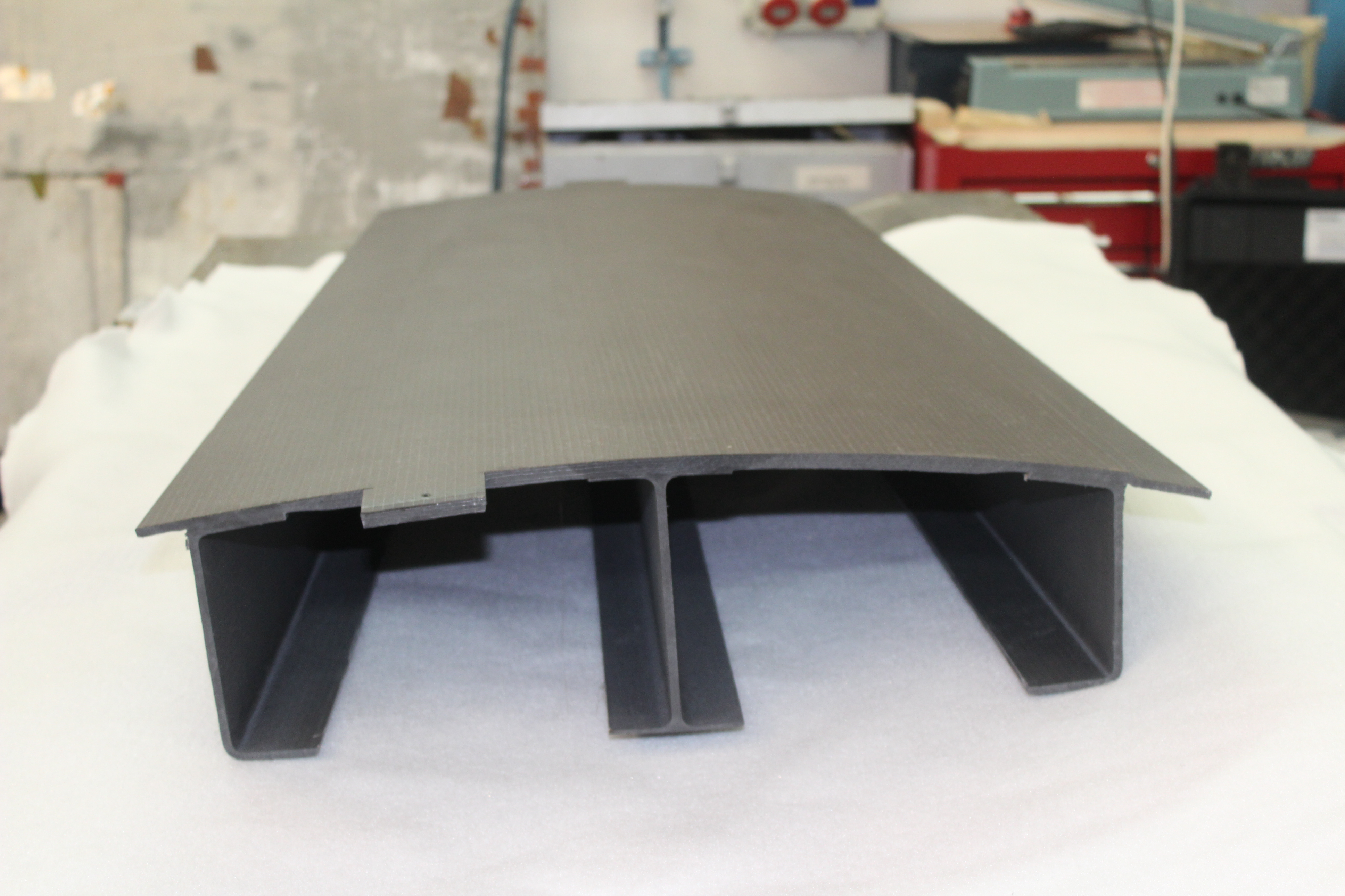
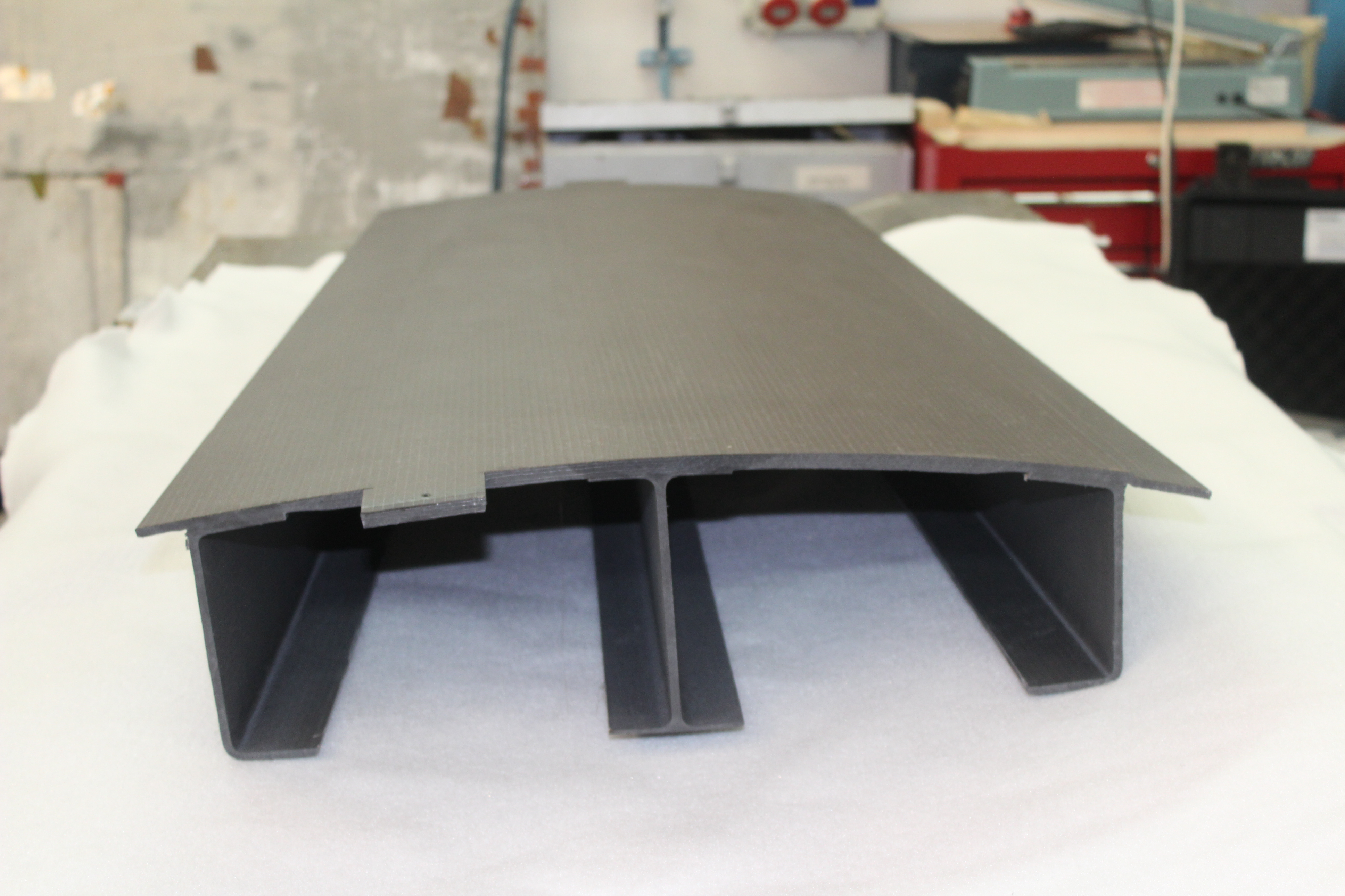
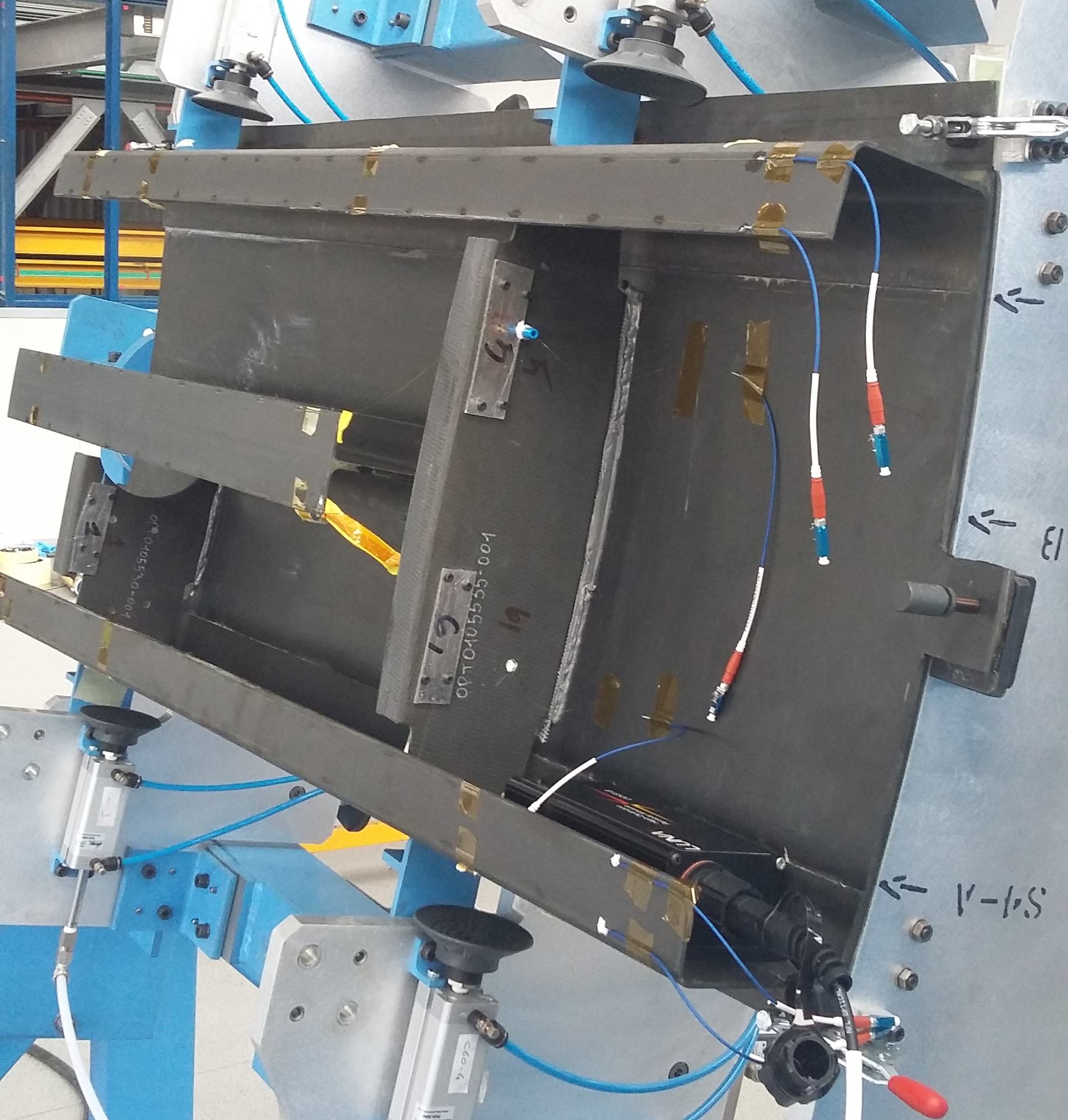
Om de spar/huidstructuur aan de onderhuid te hechten, resulteerde de tweede CFP in een ander OPTICOMS-project genaamd WIBOND, om een hulpmiddel voor het assembleren van lijmen te ontwikkelen dat de lijm plaatst, de juiste druk uitoefent en glasvezelsensoren in de verbindingslijn opneemt voor structurele gezondheid toezicht op de obligatie; CW zal hierover en de andere assemblagetechnologieën rapporteren in een apart artikel dat in 2022 zal verschijnen.
Het derde GVB is gestart om de cruciale uitdaging aan te gaan van restspanningen die een "inspringing" van de ligger/huidstructuur veroorzaken. Deze vervormingen kunnen schadelijke effecten hebben op het assemblageproces van de verlijming. Het ELADINE-project sloot zich aan bij de inspanningen van OPTICOMS om software te ontwikkelen die thermische anisotropie, polymerisatiekrimp, interactie tussen gereedschapsonderdelen, harsstroom en -verdichting en temperatuurgradiënten over de structuur modelleert en voorspelt.
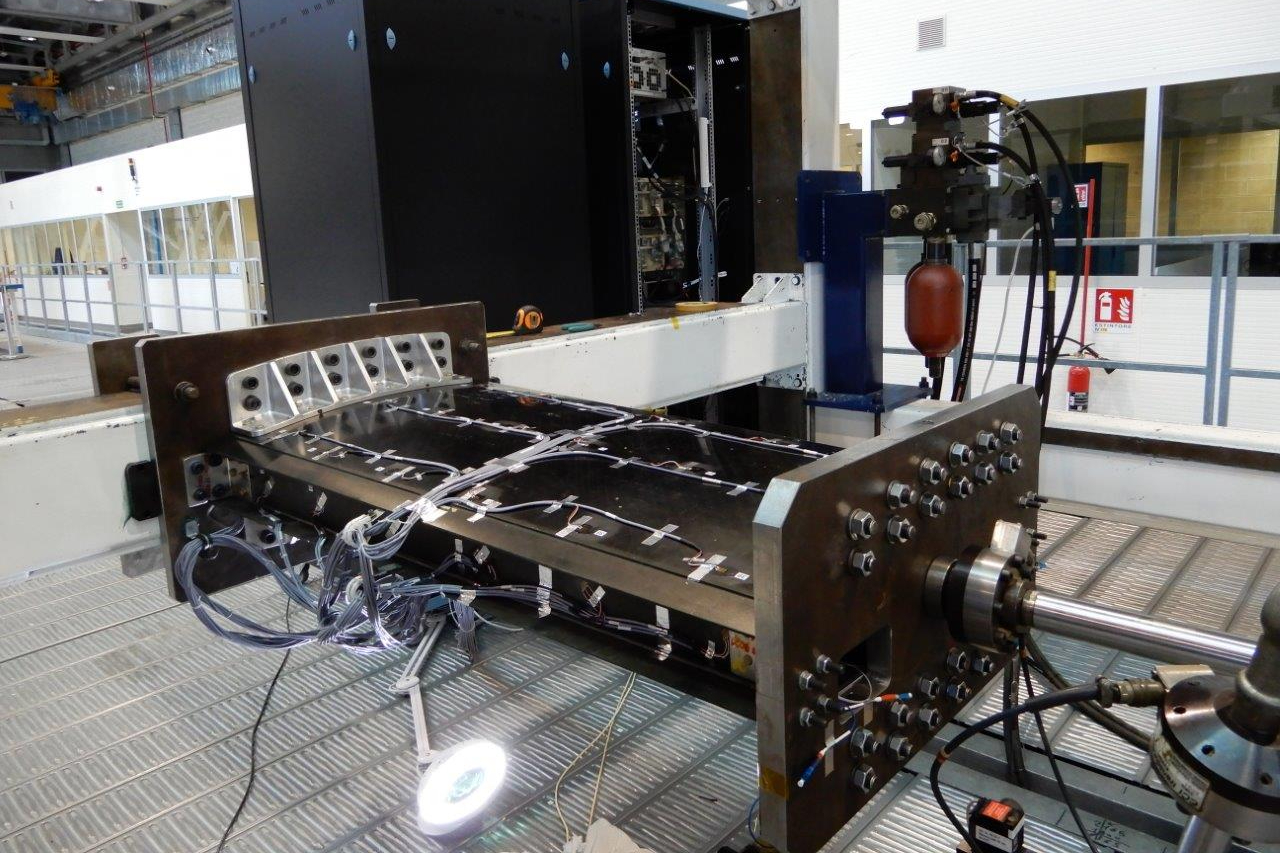
De belangrijkste focus van IAI en OPTICOMS op dit moment is om tegen het tweede kwartaal van 2022 een complete demonstratievleugel van 6,8 meter aan Piaggio te leveren voor statische en vermoeiingstests. Dit wordt gevolgd door een analyse van de algehele prestaties van de vleugel en het vermogen van het ontwerp, de materialen en de processen om aan de projectcriteria te voldoen. Daarna volgt een aanbeveling van Piaggio over mogelijke volgende stappen in de richting van commercialisering.
Buiten Piaggio hoopt IAI echter dat de OPTICOMS-vleugelkast ook in andere vliegtuigen kan worden toegepast. "Hoewel dit project is gebaseerd op een specifiek vliegtuig", zegt Sawday, "hebben we geprobeerd het ontwerp schaalbaar te maken naar verschillende diktes en verschillende maten. We hebben nooit uit het oog verloren dat deze technologie zeer aanpasbaar kan en moet zijn.”
Hars
- Ultralichte TPE-composieten voor schoenen
- Nexam Chemical, de door NCC ontwikkelde oplossing voor de productie van composieten voor hoge temperaturen
- In-house polymeer vergruizer breidt Ensinger's productiecapaciteiten voor composieten uit
- Solvay composieten geselecteerd voor racecatamaran
- Community college voegt flexibiliteit toe voor gevorderde composietstudenten
- 4 veelvoorkomende fouten die u moet vermijden bij het ontwerpen voor productie
- PCB-productie voor 5G
- Inspelen op de grote behoefte aan automatisering van composieten
- Metalen voor high-mix, low-volume productie
- Wat is geautomatiseerde productie?
- Vermijd deze 4 veelvoorkomende fouten bij het ontwerpen voor productie