Aanpassen van ultrasone sensoren voor procesoptimalisatie en controle van composieten
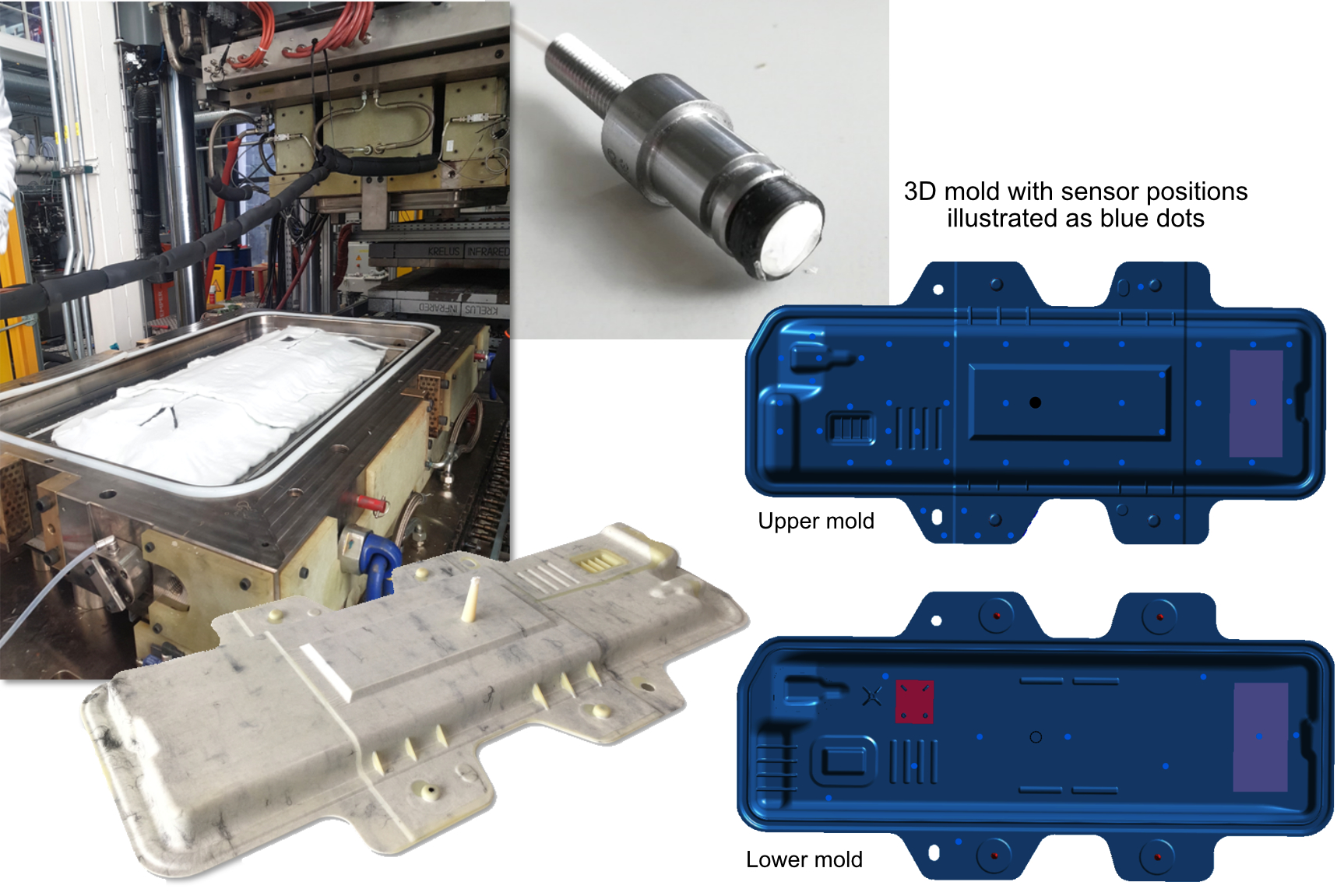
Deze blog is een vervolg op mijn verslag over het CosiMo-project (“composieten voor duurzame mobiliteit”). Dat project werd in 2018 gelanceerd door Faurecia Clean Mobility (Nanterre, Frankrijk) om de "slimme fabricage" van een deksel van een composietbatterijdoos te demonstreren. Het 1.100 millimeter lange en 530 millimeter brede uitdagingsonderdeel was voorzien van niet-geweven glasvezel en unidirectionele koolstofvezelversterkingen, evenals metalen en schuiminzetstukken, een complexe geometrie met verschillende radii en diktes variërend van 2,5 tot 10 millimeter. Het onderdeel werd gegoten met behulp van thermoplastische harstransfervormen (T-RTM), waarbij caprolactammonomeer werd geïnjecteerd en vervolgens in situ gepolymeriseerd tijdens de verwarmde perscyclus om een polyamide 6 (PA6)-composiet te vormen. Het belangrijkste doel van het project was om een volledig geautomatiseerd proces te onderzoeken met behulp van gesloten, sensorgebaseerde procesbesturing.
In deze blog wordt nader ingegaan op het netwerk van 74 sensoren die worden gebruikt in het CosiMo-uitdagingsgedeelte, en met name de ultrasone sensoren die zijn ontwikkeld door de Universiteit van Augsburg (UNA, Augsburg, Duitsland) en hoe gegevens van alle sensoren zijn gebruikt om een digitaal model van het proces (digitale tweeling).
Op basis van het succes van CosiMo en de behoefte aan een ontwikkelingscentrum voor sensor- en AI-gebaseerde productieontwikkeling, heeft UNA het Augsburg AI Production Network gevormd, in samenwerking met CosiMo-projectpartner German Aerospace Center (DLR) Centre of Lightweight Production Technologies ( ZLP, Augsburg) en het Fraunhofer Institute for Foundry, Composites and Processing Technology (Fraunhofer IGCV). "We zijn een nieuwe faciliteit van 5.000 vierkante meter aan het opzetten die we in samenwerking zullen exploiteren", zegt Dr. Markus Sause, UNA-professor en directeur van het Augsburg AI Production Network. "We zullen geautomatiseerde productiecellen hebben, waarvan vele gericht zijn op composiettechnologieën, waarmee we kunnen demonstreren wat AI kan doen."
CosiMo-sensornetwerk
Voor het CosiMo-project werden 74 sensoren geïntegreerd in het stalen RTM-gereedschap geleverd door Christian Karl Siebenwurst GmbH &Co. KG (Dietfurt, Duitsland) voor het vormen van het deksel van de T-RTM-accubak. Dit netwerk werd gebruikt voor het bewaken van procesparameters tijdens harsinjectie, infiltratie (stroomfrontbewaking) en in-situ polymerisatie:
- 1 vacuümsensor
- 4 druk-/temperatuursensoren van Kistler (Winterthur, Zwitserland)
- 4 temperatuursensoren van Kistler
- 8 diëlektrische analyse (DEA)/temperatuursensoren door Netzsch (Selb, Duitsland)
- 57 ultrasone sensoren ontwikkeld door de Universiteit van Augsburg.
In mijn eerste rapport over CosiMo besprak ik hoe dit sensornetwerk was voor R&D, niet voor standaardproductie:
"Voor industriële serieproductie zou niemand zoveel sensoren installeren en dat is niet wat we zouden verwachten", zegt CosiMo productieprojectleider bij DLR ZLP, Jan Faber. "Maar voor dit onderzoeksonderzoek was dit grote sensor netwerk zeer nauwkeurig en hielp ons om volledig inzicht in het proces te hebben en materieel gedrag . We konden de lokale effecten in het proces als reactie zien tot variaties in deeldikte of in de geïntegreerde materialen, zoals de schuimkern.”
Dus, hoe is dit netwerk ontworpen? "De meeste waren de ultrasone sensoren omdat ze de laagste kosten hebben", legt Faber uit. “We gebruikten ze in een raster op een bepaalde afstand van elkaar. Op sommige plaatsen hebben we de ultrasone sensoren eruit gehaald en Kistler temperatuur/druk of Netzsch DEA/temperatuur sensoren geplaatst. En voor deze specifieke sensoren, zowel de DEA als Kistler, probeerden we er een dicht bij de spruw te hebben, waar de hars binnenkwam, en dan een ver weg. Zo konden we de locaties volgen waar de hars arriveert nadat we de maltemperatuur al een tijdje hebben gezien.”
Waarom verschillende soorten sensoren gebruiken? “Een onderzoekstaak was om de signalen te vergelijken en te kijken hoe de verschillende sensoren presteren”, zegt Faber. Dit is belangrijk omdat de verschillende soorten sensoren gebaseerd zijn op verschillende meetprincipes. DEA-sensoren meten bijvoorbeeld de AC-impedantie van de hars, die kan worden opgesplitst in verschillende fracties, die op hun beurt verschillende effecten in het polymeer vertonen. Kistler gebruikt ondertussen piëzoresistieve sensoren die vertrouwen op een op silicium gebaseerde Wheatstone-brug - een type circuit dat wordt gebruikt om dynamische elektrische weerstand te meten - verbonden met een membraan dat het detectie-uiteinde vormt dat in de wand van de vormholte is geïnstalleerd. Het membraan zet uit onder druk, waardoor de elektrische weerstand van de silicium Wheatstone-brug verandert, die op zijn beurt een elektrisch signaal afgeeft. "We hebben ook de nieuwe 4001a-sensor van Kistler gebruikt, die zowel druk als temperatuur meet", merkt Faber op. "Het was erg handig om beide waarden voor geselecteerde lokale punten in de tool te hebben."
UNA ultrasone sensoren
Het merendeel van de sensoren die in het CosiMo-onderdelennetwerk werden gebruikt, waren door UNA ontwikkelde ultrasone sensoren. Sause merkt op dat deze niet alleen de voorkeur genoten vanwege hun lage kosten (<10 euro), maar ook omdat ze een breed scala aan informatie kunnen leveren.
Ultrasone sensoren worden al tientallen jaren gebruikt om afgewerkte composietonderdelen te inspecteren, maar hebben ook een lange geschiedenis in het spuitgieten. Ultrasone sensoren sturen een hoogfrequente geluidsgolf een medium in en meten de reflectie (pulsecho) en/of transmissie ervan. In het CosiMo-project was de nominale frequentie 2.000 kilohertz. Van de 57 ultrasone sensoren die in de mal waren geïnstalleerd - op een afstand van 20 millimeter van het oppervlak van de holte - werkten er 10 in transmissiemodus en de rest in pulse-echo-modus. Ultrasone sensoren meten de snelheid van de golf en nemen de amplitude af (demping); beide zijn gevoelig voor de eigenschappen van het polymeer. Verder kan de golfsnelheid worden berekend als een functie van druk en temperatuur, maar de ultrasone gegevens moeten worden gekalibreerd voor het polymeer dat wordt onderzocht.
“De ultrasone sensor die we hebben ontwikkeld verschilt eigenlijk niet veel van wat er in de handel verkrijgbaar is”, zegt Sause. “Het is gebaseerd op een piëzo-elektrisch materiaal, dat vrij gevoelig is in het omzetten van een elastische beweging in een elektrisch signaal. Maar waar typische sensoren kunnen werken bij temperaturen tot 150 °C, moesten we de hoge temperaturen van thermoplastisch gieten van meer dan 200 °C evenaren, wat een beetje uitdagend was voor de sensorelektronica.”
"We moesten ook het mechanische systeem bedenken om de sensor goed in de mal te integreren", legt hij uit, "waarvoor een veerbelasting met een goede afdichting nodig was om voor een goede koppeling te zorgen. Er was een groot portfolio aan eisen waaraan de sensor moest voldoen; dus we moesten het vrijwel helemaal opnieuw ontwerpen. We hebben ook een goed akoestisch ontwerp van het hele systeem gemaakt.”
Polymerisatie en stroomfrontbewaking
“De akoestiek richt zich op de elastische eigenschappen van de materialen in de mal”, vervolgt Sause. “Kortom, de stijfheid in een vloeistof is niet hetzelfde als wanneer de polymerisatie voltooid is. We monitoren die transitie effectief. We kijken naar de akoestische intensiteit van de golfreflectie op het grensvlak van de mal naar het polymeermateriaal op elke sensorlocatie, en volgen zo de uitharding continu in de tijd.”
De mechanica van deze meting wordt uitgelegd door Sause en Faber, et. al., in de SAMPE Europe 2021-conferentiepaper, "Sensor-based process monitoring of in-situ polymerization in T-RTM manufacturing with caprolactam". De verhouding van de amplitude van de akoestische signaalecho voor en na de impregnering van de voorvorm hangt af van de reflectie-index op het raakvlak van vorm tot onderdeel, R. Dit benadert een constante waarde naarmate de polymerisatie vordert. Idealiter is de verandering in R gelijk aan nul zodra de polymerisatie zijn voltooiing nadert.
Het is ook mogelijk om uit het akoestische transmissiesignaal de reistijd te extraheren die de ultrasone golven nodig hebben om door de geïmpregneerde voorvorm te gaan. Dit is handig omdat de snelheid van het geluid door de voorvorm is gekoppeld aan de mate van polymerisatie. Voor de experimenten die ten tijde van het SAMPE Europe 2021-document werden voltooid, bedroeg de tijd tussen het grondig bevochtigen van de voorvorm op de locatie van de sensor en de voltooiing van de polymerisatie 240 seconden.
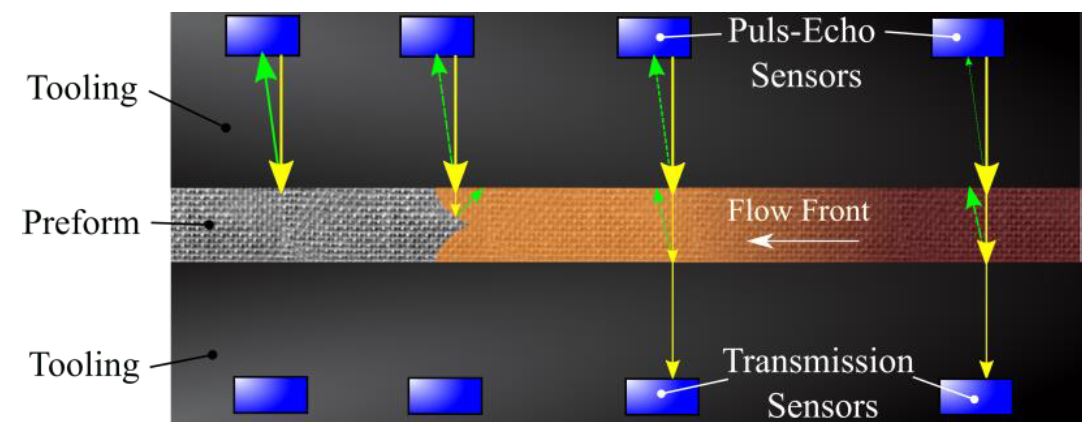
"We kunnen ook de stroom tijdens de injectie volgen", legt Sause uit, "omdat de informatie over het akoestische signaal verandert als het polymeerstroomfront de sensor passeert." Ook geverifieerd in het SAMPE Europe 2021-document, daalde het akoestische signaal abrupt van een aanvankelijke genormaliseerde waarde van 1 tot tussen 0,85-0,9 bij aankomst van het caprolactamstroomfront voor de geselecteerde sensor 15 seconden nadat de injectie begon.
Ontwikkelen van een digitale tweeling van het proces
Sause zegt dat het ontwikkelen van de ultrasone sensor eigenlijk een heel klein onderdeel was van wat UNA deed in het CosiMo-project, "en niet eens het meest fascinerende deel." De echte prestatie, merkt hij op, was de data-analyse en ontwikkeling van een digitaal model van het proces om closed-loop controle mogelijk te maken tijdens de fabricage van onderdelen.
"Wat we proberen te doen, is informatie verstrekken over wat er daadwerkelijk in de mal gebeurt", voegt hij eraan toe. "We hebben routes vastgesteld om het proces min of meer aan te passen aan temperatuur en druk, maar wat we nu doen, is de informatie over het akoestische signaal benutten door actief te pulseren op elke sensorlocatie. En dit stelt ons in staat om verschillende dingen te bepalen, zoals de vorm van het stroomfront, de tijd die het nodig heeft om elk deel van de voorvorm te bereiken en de mate van polymerisatie op elke sensorlocatie."
"Idealiter kun je instellingen maken om closed-loop-besturing mogelijk te maken en tijdens het proces bij te sturen", zegt Sause. “Hieronder vallen parameters als injectiedruk en matrijsdruk en temperatuur. U kunt deze informatie ook gebruiken om uw materialen te optimaliseren.”
De ontwikkeling van de digitale tweeling was een inspanning met meerdere fasen en meerdere partners. Het begon met een van de werkpakketten die aan de DLR ZLP waren toegewezen. "We hebben een simulatie opgezet op basis van een 2D-plaat, waarbij we de vulling en polymerisatie wilden simuleren met behulp van de PAM-RTM-simulatiesoftware van ESI Group (Rungis, Frankrijk)", zegt Faber. “We hebben de permeabiliteitsgegevens van de voorvormen gekregen van projectpartners ITA (Instituut voor Textieltechnologie, RWTH Aken, Duitsland) en SGL Carbon (Wiesbaden, Duitsland) en ook een reactief model van de thermoplastische polymeerreactie van de Universiteit van Augsburg. Vervolgens integreerden we alles in de simulatie en probeerden we te zien hoe dicht we bij de echte sensorgegevens konden komen.”
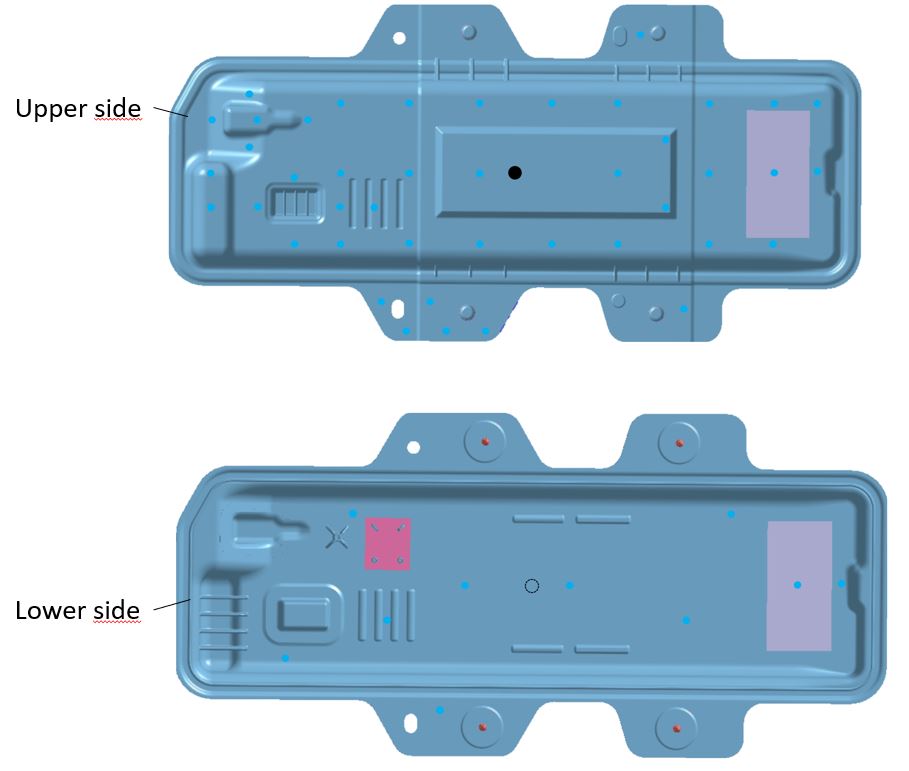
De lichtblauwe stippen in de boven- en ondermal voor het demonstratiedeel van het CosiMo-project leverden op specifieke punten gedurende het proces gegevens op. Dit werd vervolgens gebruikt in de digitale tweelingsimulatie om te interpoleren tussen de sensorlocaties en het proces over het onderdeel te modelleren. Photo Credit:CosiMo-project, DLR ZLP Augsburg, Universiteit van Augsburg
“Op basis van het 2D-plaatmodel ontdekten we dat we qua vulling heel dicht bij elkaar zitten”, vervolgt Faber. "Maar we hadden enkele temperatuureffecten tijdens de polymerisatie die we niet in de simulatie konden beschrijven. Deze polymerisatiereactie is bijvoorbeeld exotherm, en je ziet een lichte stijging bij de temperatuursensoren in de echte data, maar de stijging in de simulatie was veel groter. Dit is dus een gebied waar we nog wat werk hebben verzet.”
Een van de dingen die het team uit de simulatie wilde ontdekken, was de tijd die nodig was om de polymerisatie te voltooien. "Wat we echt wilden, was de minimale tijd die we nodig hadden in de mal", merkt Faber op. Deze informatie was afgeleid van het simulatiemodel en was, zoals bij alle simulaties, gebaseerd op meerdere soorten sensoren en AI-algoritmen. Netzsch leverde bijvoorbeeld de diëlektrische sensoren die worden gebruikt voor diëlektrische analyse, maar hielp ook met delen van de digitale tweeling van het proces. "Ze hebben voorspellende AI-modellen opgezet om de mechanismen binnen de injectie te onderzoeken en om te voorspellen op welk moment de polymerisatie voltooid moet zijn en wat de polymerisatiestatus zou zijn", zegt Faber.
(Let op, Netzsch heeft zijn competenties op het gebied van materiaalkarakterisering, kinetische simulatie en sensortechnologie gecombineerd om nieuwe aanbiedingen op het gebied van AI en cloudoplossingen tot stand te brengen. Dit type geïntegreerde oplossing is met succes gedemonstreerd in CosiMo om realtime evaluatie van de mate van polymerisatie en zal worden gecommercialiseerd onder de merknaam sensXPERT.)
Uit het complete netwerk van sensoren en simulatie bleek dat 96% de maximale polymerisatie was die werd bereikt en dat 4,5 minuten nodig was. "Dus dat is veel sneller dan infusieprocessen, maar veel langzamer dan snelle injectie met bijvoorbeeld thermoharders."
"De sensorgegevens passen in het digitale tweelingmodel", zegt Sause. “Het idee was om tegelijk met het proces een model te laten lopen dat numeriek gestabiliseerd wordt door de sensorinformatie. De blauwe stippen zorgen voor een grof raster van ultrasone sensoren, en toen konden we tussen die punten interpoleren. Zo hebben we op basis van de meetgegevens van onze sensoren een video kunnen maken van hoe het stromingsfront zich in het CosiMo-deel ontwikkelt als functie van de tijd.”
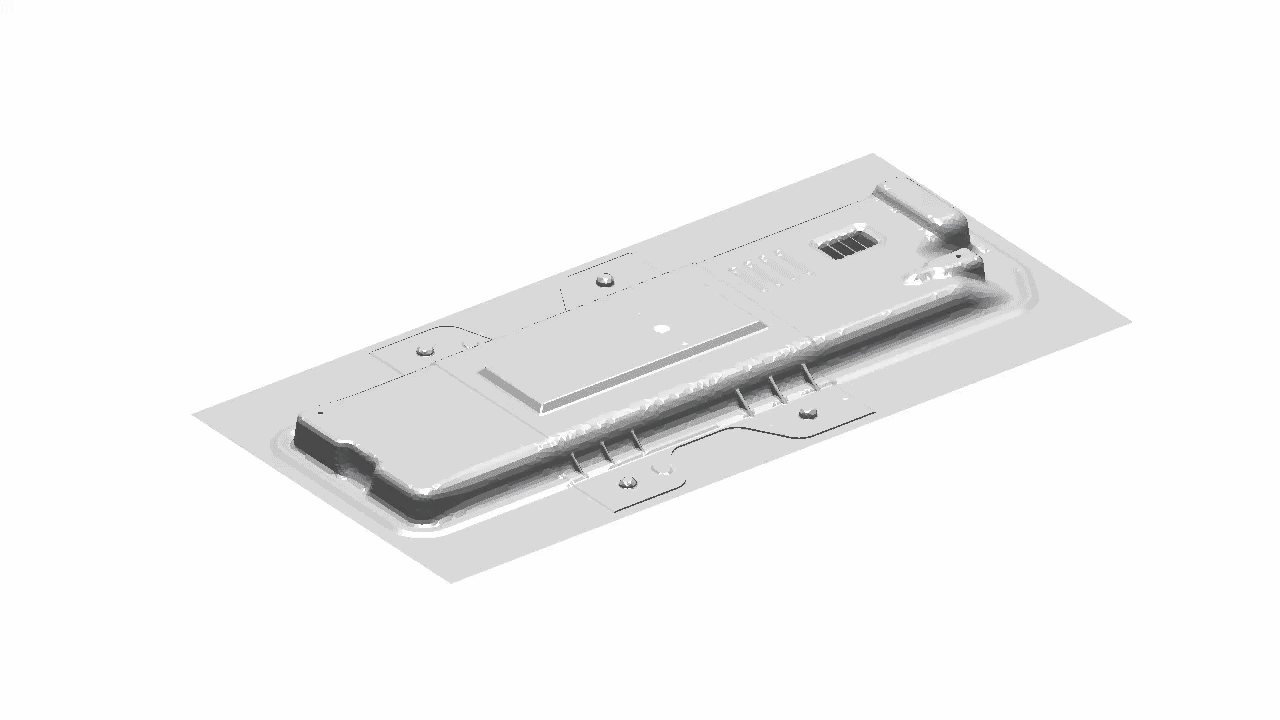
Hoe werden de voorspellingen van de polymerisatiesnelheid gevalideerd? "We hadden verschillende benaderingen", zegt Sause. “Eerst deed een promovendus hier bij UNA een volledige set van modellering voor de reactiekinetiek van het caprolactam-naar-PA6-materiaalsysteem. Dus bestudeerde hij gelijktijdig infraroodspectroscopie samen met reometrische gegevens en gegevens van de diëlektrische analysesensoren om een zeer nauwkeurig materiaalmodel te leveren voor de uitgeharde kinetiek van dat systeem en om dat model te valideren. Dus hebben we hetzelfde model gebruikt om onze sensoren te valideren.”
Architectuur van de digitale tweeling
De architectuur van hoe de digitale tweeling werkt, wordt beschreven door Stieber, et. al. in de technische paper van 2020, "Op weg naar realtime procesbewaking en machine learning voor het vervaardigen van composietstructuren":
Het bestaat uit drie delen:de T-RTM-machinerie, de in-situ sensoren in de matrijsgereedschappen en de digitale tweeling. Deze structuur en in het bijzonder de digitale tweeling zijn ontwikkeld met de volgende doelstellingen O1 – O4 in gedachten:
- O1:Bewaak het fabricageproces van elk composietonderdeel met de in-situ sensoren van de tooling.
- O2:visualiseer elk productieproces in realtime om meer procesinzichten te krijgen.
- O3:ML-modellen trainen op gesimuleerde en echte gegevens om de uitkomst van het productieproces te voorspellen.
- O4:gebruik getrainde ML-modellen om productieuitval te verminderen.
De sensoren voeren vervolgens gegevens door naar de edge-analyse van de digitale tweeling, die vervolgens kan worden gebruikt om toekomstige stromingsfrontdynamiek te voorspellen, het vezelvolume-gehalte van elke textielvoorvorm te bepalen, droge plekken te voorspellen en anomalieën te detecteren die de afgekeurde onderdelen kunnen verminderen.
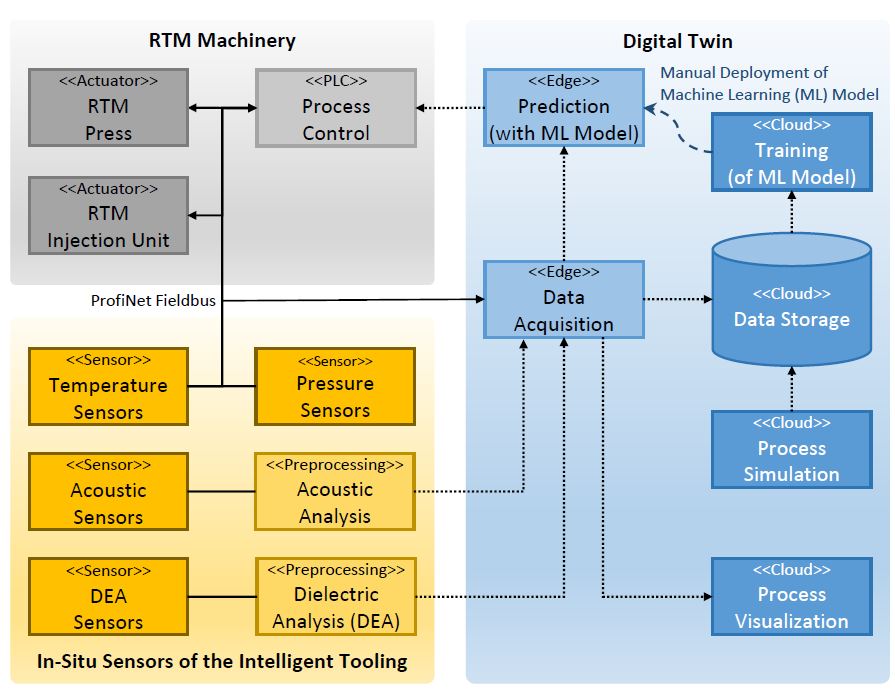
De T-RTM-machine bestaat uit twee kant-en-klare componenten:een Wickert (Landau in der Pfalz, Duitsland) hete pers van 440 kilonewton en een T-RTM-injectie-eenheid van KrausMaffei (München, Duitsland). Zowel deze machines als het hele sensornetwerk zijn verbonden met een PLC (programmed logic controller) die verantwoordelijk is voor de besturing van het algehele productieproces.
Omdat de sensoren realtime voorbewerking nodig hebben om de onbewerkte gegevens om te zetten in informatie op een hoger niveau over het stroomfront of de uitharding van de hars, worden de voorbewerkte gegevens direct aan de rand geregistreerd met behulp van een ibaPDA-gegevensverzamelingseenheid van iba AG ( Fürth, Duitsland). Zo worden de sensorgegevens geregistreerd en samengevoegd met een consistent tijdstempel gekoppeld aan de procesgegevens en onderdeelinformatie met de sensorgegevens per doelstellingen O1 en O2.
Om het productieproces automatisch te optimaliseren, worden de opgeslagen gegevens gebruikt om modellen voor machine learning (ML) te trainen om de doelstelling O3 aan te pakken. Deze modellen zijn bijvoorbeeld verantwoordelijk voor het reconstrueren van het stroomfront van de hars uit het sensornetwerk, voor het voorspellen van de voortgang van het stroomfront en – idealiter – voor het aanpassen van de procesparameters om het resultaat te optimaliseren, hetzij tijdens een procesinstantie of voor daaropvolgende runs . Omdat echte gegevens over het algemeen niet voldoende zijn om betrouwbare modellen te trainen, gebruikte het digitale tweelingteam PAM-RTM gesimuleerde runs om de gemeten gegevens te vergroten. Na een voortraining met behulp van gesimuleerde gegevens, werd de digitale tweeling verfijnd met real-world gegevens. Deze strategie staat bekend als Transfer Learning en is met succes toegepast in toepassingen voor computervisie en natuurlijke taalverwerking. De geavanceerde analyses die mogelijk zijn met ML maken verbeterde voorspellingsmogelijkheden en procesvisualisatie mogelijk, evenals closed-loop-besturing.
Sensorintegratie voor industriële composietproductie
Dus, hoe passen fabrikanten van composietonderdelen deze technologie toe om closed-loop controle te ontwikkelen in hun eigen productieprocessen? Sause zegt dat het zinvol is om verschillende soorten sensoren te gebruiken om de stroom- en uithardings-/polymerisatiemonitoring te valideren en om aanvullende informatie te verstrekken. En dan is het een kwestie van sensorplaatsing definiëren, inclusief welke typen op elke locatie worden geplaatst. "Bijvoorbeeld," merkt hij op, "je hebt niet overal druk- en temperatuursensoren nodig, maar alleen waar je die belangrijke gegevenspunten nodig hebt, zoals harsinvoer, complexe geometriepunten, enz."
Hoeveel sensoren? "Voor CosiMo gebruikten we 74 sensoren, maar voor een deel van een halve meter zou je minder gebruiken, misschien 35-40, afhankelijk van je geometrie en belangrijke aandachtspunten", zegt Sause. “Het hangt ook af van het productieproces. Er zijn bijvoorbeeld processen in de lucht- en ruimtevaart die al tientallen jaren worden gebruikt en goed ingeburgerd zijn. Hiervoor heb je misschien niet heel veel sensoren nodig en het zou mogelijk zijn om ze in het begin zonder veel ontwikkelingswerk te integreren. Maar andere processen zijn meer onbekend en vereisen meer werk vooraf. Voor CosiMo keken we naar het gebruik van T-RTM met in-situ polymerisatie tot PA6, en dit was niet zo goed gedocumenteerd als RTM met bijvoorbeeld epoxy.”
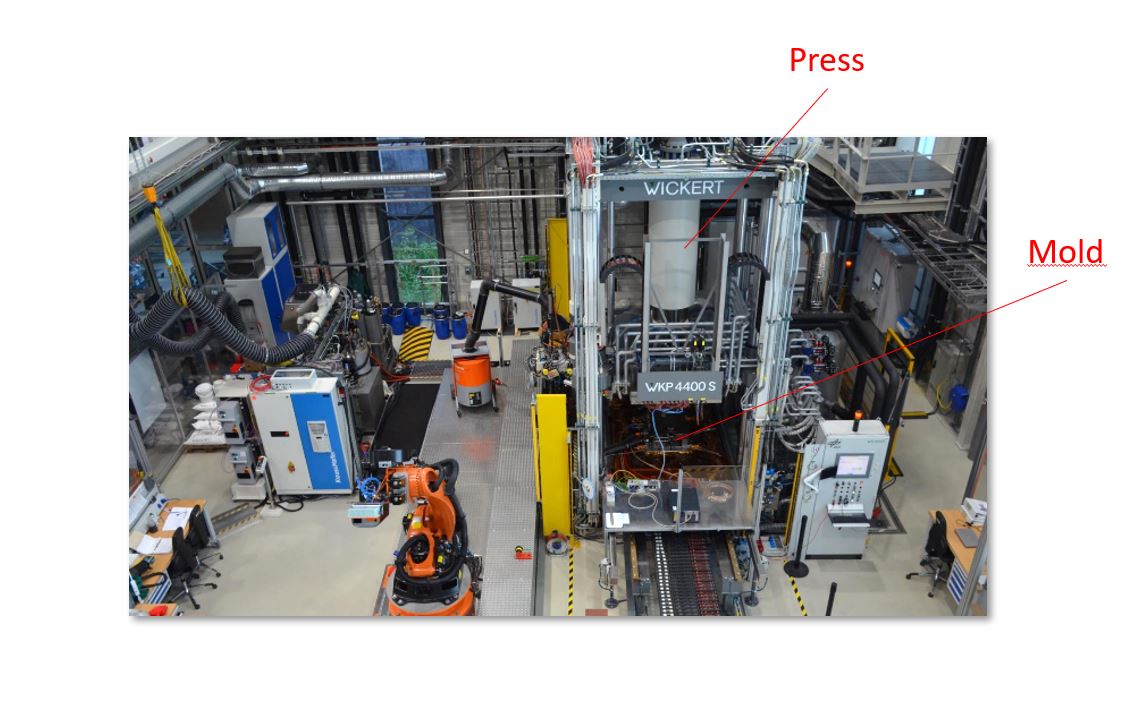
De productieapparatuur in het CosiMo-project bestond uit een Wickert 440 kN-pers en een KraussMaffei-injectiemachine. Fotocredits voor deze serie:CosiMo-project, DLR ZLP Augsburg, Universiteit van Augsburg
Hoe tijdrovend is het bouwen van een digitaal model? En is dat altijd nodig om een closed-loop regeling te bereiken? "Nogmaals, het hangt af van je proces en welk niveau je wilt bereiken", zegt Sause. "Allereerst kun je door de geïntegreerde sensorinformatie te visualiseren wat er in je zwarte doos met verwerking gebeurt en welke parameters je moet gebruiken.
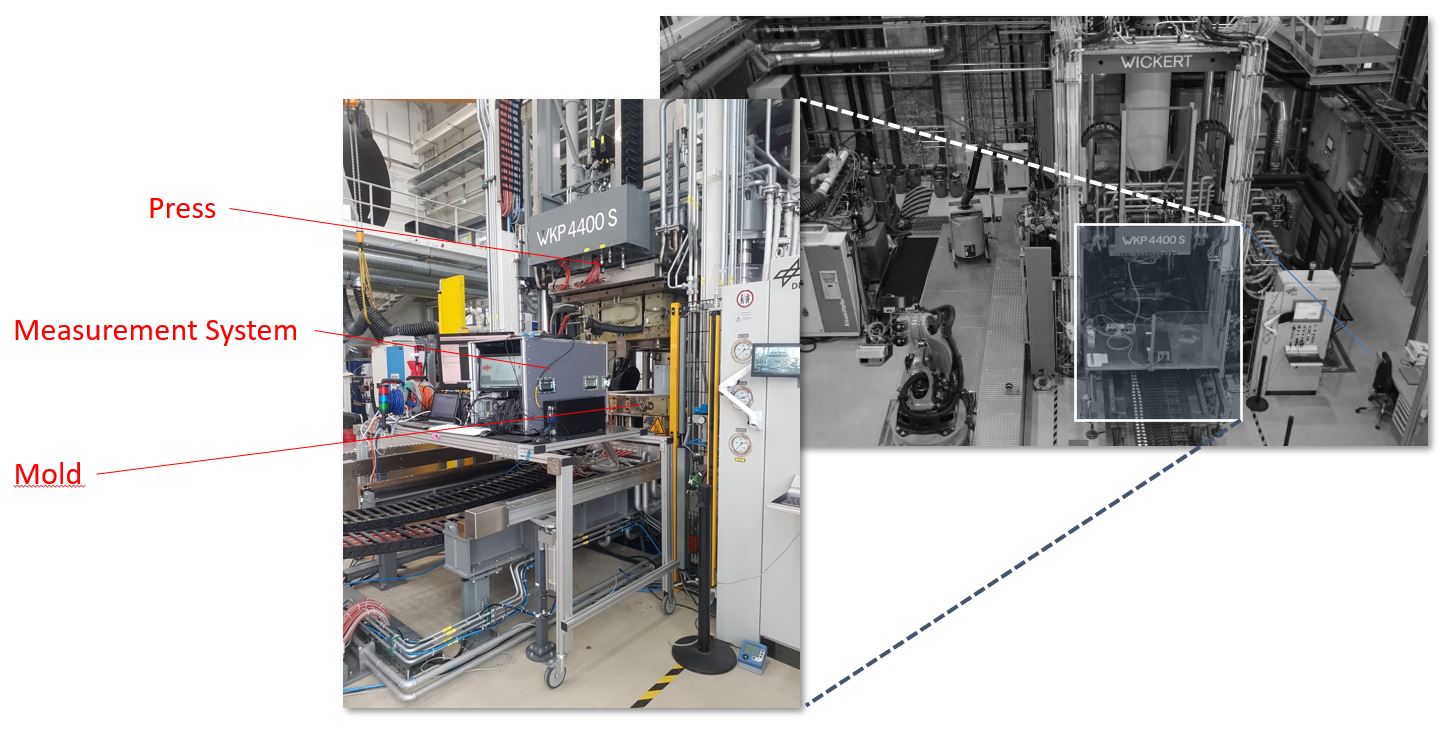
Het in CosiMo ontwikkelde gesloten regelsysteem integreerde ook in-mold sensoren en een data-acquisitiesysteem (meetsysteem hier getoond) van iba AG.
Zodra dat eerste doel is bereikt, zijn er nog een paar stappen nodig om procesbeheersing in een gesloten kringloop te bereiken. Halverwege is misschien de visualisatie en kun je zelf op de stopknop drukken om het proces aan te passen en te voorkomen dat onderdelen worden afgekeurd. Dus ook dat is een begin. En dan kun je de digitale tweeling ontwikkelen, maar die heeft trainingsgegevens nodig. Dus je moet dat op de een of andere manier verstrekken, wat betekent dat je een aantal onderdelen kunt produceren om als invoergegevens te gebruiken. Maar dan moet je ook onderdelen van lage kwaliteit maken. Het is dus een kwestie van uw bereidheid om te investeren in de training van uw machine learning-aanpak."
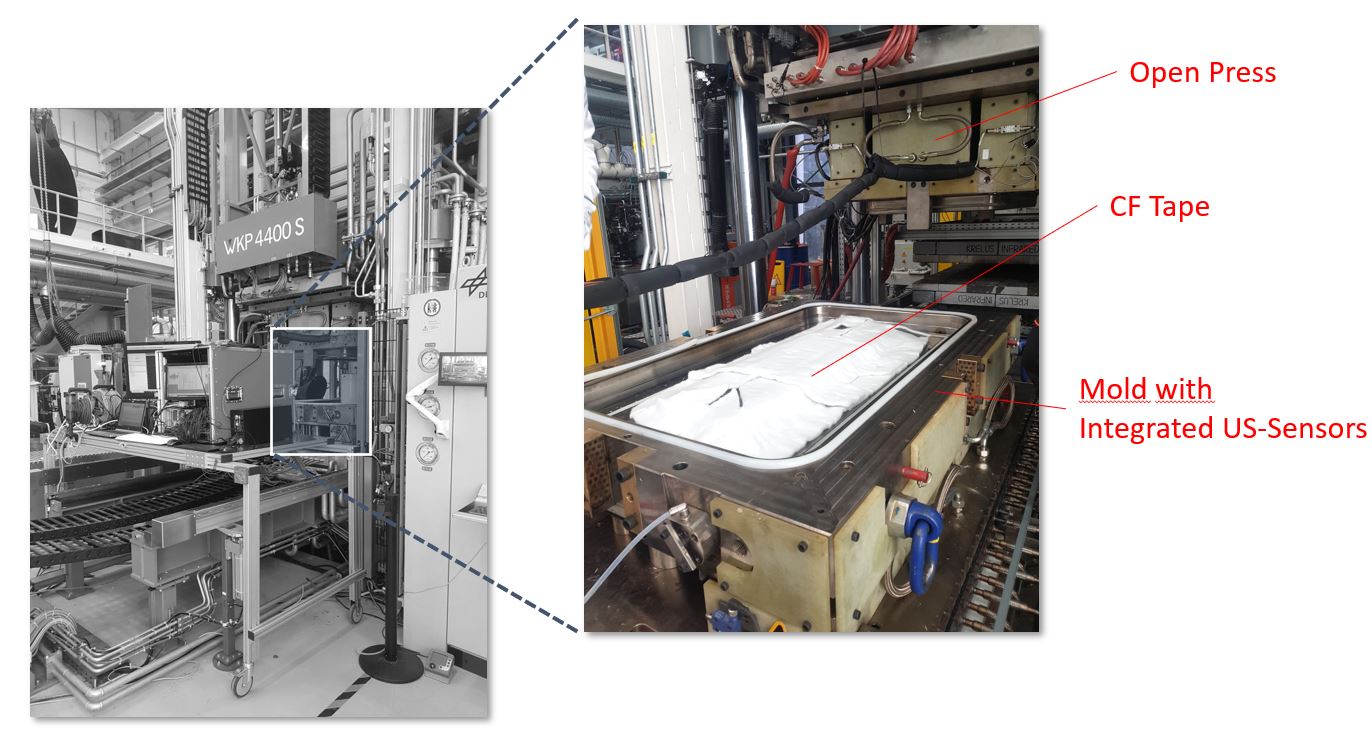
Eenmaal getraind, kan de digitale tweeling procesparameters optimaliseren en procescontrole met gesloten lus bieden.
Sause erkent echter wel dat de transfer learning-aanpak van CosiMo “tot op zekere hoogte overdraagbaar is naar vergelijkbare geometrieën of materiaalsystemen en andere variaties die de situatie niet volledig veranderen. U kunt uw database dus op die manier opbouwen, met de mogelijkheid om efficiëntietrends te identificeren met behulp van de reeds verkregen gegevens. Die kun je dan gebruiken voor andere vragen die je misschien hebt.”
Dus de manier om te beginnen lijkt te zijn:sensoren gaan gebruiken en digitale modellen bouwen die bij de sensoren passen, zodat u uw proces kunt begrijpen? "Absoluut", zegt Sause. “En ik kan je verzekeren dat de meeste machines die tegenwoordig in de productie worden gebruikt, nog steeds erg dom zijn. Veel machines hebben geen sensoren die u de databases kunnen geven om feedback te geven over wat er aan de hand is. Dus ja, integratie van sensorsystemen zou de allereerste stap zijn. Maar je moet een systematische . doen data-acquisitie, en ook een data-opslagarchitectuur bieden, om iets met de data te kunnen doen . Je ziet eigenlijk veel bedrijven die sensoren hebben geïntegreerd, maar dan doen ze niets met de data.”
AI-productienetwerk
Bij het beantwoorden van de bovenstaande vragen kwam Sause steeds terug op verschillende groepen binnen UNA, evenals op spin-offbedrijven die sensorintegratie en digitale tweelingdiensten kunnen bieden. Daartoe werd in januari 2021 het Augsburg AI Production Network gelanceerd door UNA, DLR ZLP en Fraunhofer IGCV. "Het samenwerkingskader komt van projecten die we in het verleden met DLR en Fraunhofer hebben gehad", zegt Sause. “We nemen de blauwdruk in AI-gebaseerde productie-ontwikkeling van CosiMo en breiden deze nu uit naar een zeer brede schaal. Zo was het budget voor ons werk in CosiMo bijvoorbeeld 10 miljoen euro, maar voor het AI Production Network is dat 92 miljoen euro als initiële financiering. Dit geeft ons de mogelijkheid om veel nieuwe onderzoeksprojecten te starten, zoals CosiMo, om AI in de productie te benutten. En we werken niet alleen in composieten, maar we hebben er wel een sterke focus op.”
Het gebruik van ultrasone sensoren om de CNC-bewerking te verbeteren, is een van de projecten die al in 2021 zijn gestart. "Er staat op het punt een project te starten over het recyclen van keramische matrixcomposieten (CMC)", zegt Sause, "en we zullen verschillende projecten hebben met een nauw verband tussen Additive Manufacturing en het hergebruik van specifiek gerecyclede vezelversterkte materialen.”
Wat betreft de rollen die elke organisatie zal spelen, legt Sause uit dat er geen concurrentie is, aangezien elke instelling een toegewezen budget heeft. “We hebben allemaal ons deel en zijn dus vrij om samen te werken zoals we dat in het verleden hebben gedaan. Ook kennen we elkaar vrij goed en onze competenties, sterke en zwakke punten. Het is leuk om samen te werken omdat we weten wat we wel en niet kunnen doen. We zijn benaderd door veel bedrijven die met ons willen samenwerken en we zijn nu aan het overleggen hoe we vanuit onze kant van competenties de ideale match kunnen vinden.”
Wat betreft de productiefaciliteit van 5.000 vierkante meter, "zullen we dat allemaal samen runnen", zegt Sause. “We zijn van plan om begin 2023 open te gaan en machines te installeren. En we zorgen voor geautomatiseerde productie-instellingen die de afzonderlijke cellen aan elkaar koppelen. Veel daarvan zullen gericht zijn op composietproductietechnologieën. En we zullen dat doen om ook aan partners uit de industrie te laten zien en te demonstreren wat AI kan doen in een dergelijke productieomgeving. We willen ook dat partners uit de industrie binnenkomen en ook machines in onze faciliteit plaatsen, zodat we samen projecten kunnen uitvoeren om te zien hoe we nieuwe oplossingen voor hun sites kunnen koppelen en integreren.”
Hars
- Kleppen voor moeilijk afsluiten en regelen
- Sensoren en systemen voor CBM
- Dip-coating procestechniek en prestatie-optimalisatie voor drie-staten elektrochrome apparaten
- OTOMcomposite ontwikkelt software voor de productie van Composites 4.0 met behulp van laserondersteunde tapeplaatsing en -wikkeling
- Herverwerkbare, herstelbare en recyclebare epoxyharsen voor composieten
- Combinatie van AC- en DC-diëlektrische metingen voor het bewaken van de uitharding van composieten
- TPAC en TPRC ontwikkelen recyclingproces voor thermoplastische composieten
- Tips voor de configuratie en bedrading van de behuizing van het bedieningspaneel:
- Wat is ultrasoon bewerken? - Werken en verwerken?
- Aansluitingen voor besturing:communicatie-interfaces voor positie- en bewegingssensoren
- Veldgegevens verzamelen voor procesoptimalisatie