Onderzoek naar het effect van het beïnvloeden van richting op het schurende nanometrische snijproces met moleculaire dynamiek
Abstract
Abrasive flow-polijsten speelt een belangrijke rol bij moderne ultraprecieze bewerkingen. Ultrafijne deeltjes gesuspendeerd in het medium van schurende stroom verwijderen het materiaal op nanoschaal. In dit artikel worden driedimensionale moleculaire dynamica (MD)-simulaties uitgevoerd om het effect van de invloed van de richting op het abrasieve snijproces tijdens het polijsten van de abrasieve stroom te onderzoeken. De moleculaire dynamica-simulatiesoftware Lammps werd gebruikt om het snijden van eenkristalkoper met SiC-slijpkorrels onder verschillende snijhoeken te simuleren (0 o –45 o ). Bij een constante wrijvingscoëfficiënt vonden we een directe relatie tussen snijhoek en snijkracht, wat uiteindelijk het aantal dislocaties tijdens abrasieve stroombewerking verhoogt. Onze theoretische studie laat zien dat een kleine snijhoek gunstig is voor het verbeteren van de oppervlaktekwaliteit en het verminderen van interne defecten in het werkstuk. Er is echter geen duidelijke relatie tussen snijhoek en wrijvingscoëfficiënt.
Achtergrond
Bij moderne ultraprecisiebewerkingen spelen materiaalverwijderingstechnologieën een belangrijke rol bij de productie van micro-elektronica, micromechanische en optische elementen. De vraag naar geminiaturiseerde apparaten met een hoge maatnauwkeurigheid en een hoogwaardig oppervlak, waardoor ultraprecisieprocessen de belangrijkste keuze zijn op het genoemde gebied [1]. Bovendien zijn de veranderingen van oppervlaktecomponenten en ondergrondstructuur op de nanometer-lengteschaal. Polijsttechnologie met schurende deeltjesstroom speelt een belangrijke rol in veel gebieden van precisiebewerking en is net als andere niet-traditionele afwerkingstechnologieën die de oppervlaktekwaliteit verbeteren. Deze technologie heeft veel onderzoekers aangetrokken vanwege zijn belangrijke rol. E. Uhlmann en andere onderzoekers hebben de computersimulatie van het polijsten van keramisch oppervlak met schuurkorrels gerapporteerd voor de ontworpen experimenten om de slijpvloeistofstroom van verschillende verwerkingsfactoren op het effect van snijmaterialen te verifiëren [2]. Sehijpal Singh en andere onderzoekers gebruiken de schurende polijsttechnologie voor het snijden van koper- en aluminiummaterialen. Uit scanning-elektronenmicroscopische analyse vonden ze een diep groefoppervlak van hun werkstuk [3]. G. Venkatesh en andere onderzoekers hebben ultrasoon geassisteerde schuurkorrelpolijsttechnologie gerapporteerd voor de conische versnelling op het complexe oppervlak van het afwerkingsproces. Bij deze techniek is de slijpkorrelsnelheid hoger dan de conventionele slijpkorrelstroom om met het oppervlak van het werkstuk in botsing te komen, wat de verwerkingsefficiëntie kan verbeteren. Op basis van hun experimentele en theoretische methoden ontdekten ze dat deze technologie een van de beste keuzes is voor het afwerken van tandwielbladen [4, 5]. K. Kamal et al. bestudeerde de reologische eigenschappen van de abrasieve vloeistof in de vloeibare abrasieve viscositeit, afschuifsnelheid en kruiptijd [6]. De meeste onderzoeken naar het polijsten van schurende stroming zijn echter gebaseerd op macroniveau en er is zeer zelden aandacht besteed aan microniveau. In het schurende stroompolijstproces zullen de gesuspendeerde deeltjes in het medium langs de media stromen, met een bepaalde snelheid met de impact van het microsnijwerkstukoppervlak (Fig. 1).
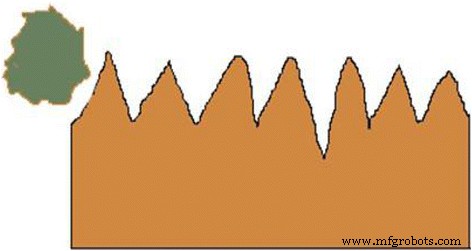
Schets van schurend snijdend werkstuk. Alle cijfers gaan over het effect van het beïnvloeden van de richting op het abrasieve nanometrische snijproces met moleculaire dynamica. Figuur 1 is de schets van een schurend snijwerkstuk. In het schurende stroompolijstproces zullen de gesuspendeerde deeltjes in het medium met een bepaalde snelheid langs de media stromen met de impact van het microsnijwerkstukoppervlak
Omdat de vorm van de slijpkorrels niet regelmatig is, met bepaalde randen en hoeken die op het oppervlak van het werkstuk werken, vergelijkbaar met het gereedschap. Maar het snijproces is op atomaire schaal, wat duidelijk verschilt van het materiaalverwijderingsproces. Bij het snijden op nanoschaal is een paar nanometer of minder van het materiaaloppervlak betrokken, maar het is erg moeilijk om dit proces met experimenten waar te nemen. Daarom is MD-simulatie als theoretische onderzoeksmethode zeer nuttig bij het bestuderen van het nanometrische snijproces. Moleculaire dynamica als een computersimulatietechniek, die een op tijd gebaseerde statistische mechanicamethode gebruikt om de onderlinge relatie van atomen te bestuderen voor voorspelling en analyse van omstandigheden. Dit is ook een krachtig hulpmiddel voor het simuleren en begrijpen van materiaalverwijderingsprocessen. In de literatuur bestaan talrijke studies over MD als een instrument om precisiebewerking te onderzoeken. Oluwajobi en Chen hebben uitgebreid werk verricht aan MD-simulatie van machinale bewerking op nanoschaal van koper [7]. In hun studies onderzochten ze verschillende parameters voor nanobewerking, zoals minimale snijdiepte, geometrie en interatomair potentieel [8]. Bovendien zijn de resultaten van MD-simulaties in het verleden ook succesvol geweest om een aantal problemen aan te pakken met betrekking tot het nanometrische snijproces van brosse materialen zoals silicium [9]. Komanduri et al. voerde een MD-simulatie uit voor nanometrisch snijden van eenkristal van puur silicium zonder defecten, met behulp van de Tersoff-potentiaal. Ze bestudeerden de effecten van de hellingshoek, de snedebreedte, de snedediepte en de vrijloophoek op materiaalverwijdering en oppervlaktegeneratie [10]. Goel et al. onderzocht de atomistische aspecten van de ductiele respons van SiC tijdens het nanometrische snijproces. Ze ontdekten de aanwezigheid van een sp3-sp2 orde-stoornis overgang die uiteindelijk resulteerde in de grafitisering van diamant [11]. Cai et al. gebruikte MD om het nanoschaal ductiele modus snijden van silicium te bestuderen. Hun rapporteerde de snijkant van het gereedschap en de effecten ervan op de schuifspanning in het werkstukmateriaal [12]. Arafin et al. heeft het effect besproken van de snijkantstraal bij het snijden van siliciumwafels op nanoschaal in ductiele modus [13]. Verschillende andere onderzoekers hebben ook de verschillende omstandigheden in nanobewerking van silicium benadrukt met behulp van MD-simulaties. Hun onderzoeken bestaan uit snijkrachten, snedediepte, temperatuur, schuifspanning en andere parameters. Er is echter een gebrek aan adequate experimentele validaties op dit gebied. Qihong Fang et al. bestudeerde het interactiemechanisme van dislocaties in verschillende heterogene materialen met verschillende schalen, en de dislocatie en de relatie tussen materiaaltaaiheid en breukschade. Ze gebruiken moleculair dynamische simulaties om de nano-indentatie op drie verschillende kristalstructuren te bestuderen, waaronder het monokristallijne, polykristallijne en nanotwinned polykristallijne koper. Met de toename van de krassnelheid, nemen de kraskracht en de temperatuur van het werkstuk continu toe als gevolg van ernstige plastische vervorming en een groot spaanvolume, wat resulteert in dislocatieslip, GB-slip en twinning/detwinning [14, 15].
Methoden/experimenteel
In het schurende stroompolijstexperiment werd het werkstuk gewoonlijk gesneden met SiC-schuurmiddel. Nadat het model van SiC-slijpkorrels was vastgesteld, werd de moleculaire dynamica-simulatie van het werkstuk uitgevoerd door de software Lammps. Het model van twee SiC schurend snijdend monokristallijn koper met verschillende hoeken werd geconstrueerd. Een simulatiemodel van een SiC-schuurkorrels die crash-cutting eenkristalkoper wordt getoond in Fig. 2.
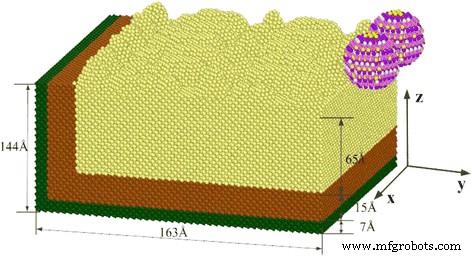
Simulatiemodel van SiC schurend snijdend eenkristal koper. Figuur 2 gaat over het simulatiemodel van SiC schurend snijdend eenkristalkoper; we hebben twee SiC-schuurmiddelen gebouwd voor het snijden van monokristalkoper. In het schurende stroompolijstexperiment werd het werkstuk gewoonlijk gesneden met SiC-schuurmiddel. Na de constructie van het SiC-schuurmodel, werd de moleculaire dynamische simulatie van het werkstuk uitgevoerd. Het model van twee SiC schurend snijdend monokristallijn koper met verschillende hoeken werd geconstrueerd
De grootte van het model wordt getoond in Fig. 2 terwijl het aantal gesimuleerde atomen 159.020 was. De straal van het slijpmiddel is 15 , het totale aantal C-atomen en Si-atomen in de slijpkorrels is 1406. En het aantal koolstof- en siliciumatomen was respectievelijk 681 en 725. Het relaxatiestapnummer is ingesteld op 10.000 stappen voor het gesimuleerde evenwichtsensemble, botsingssimulatiestappen op 100.000 snijstappen, elke stap van de simulatie was 0,001 ps, snijsimulatie, de SiC-schuurdeeltjes in de snijrichtingsnelheid van 80 m/s. AFM-analysewaardekorrels botsen met het microbewerkingswerkstuk tijdens het polijsten, SiC-slijpkorrels om de moleculaire botsingsdynamiek onder verschillende hoeken te onderzoeken. Tijdens het snijden van schurende stroom neemt de snijkracht toe naarmate de snijsnelheid toeneemt, en de grootte van de snijkracht heeft direct invloed op het snijeffect. Daarom heeft de keuze van een redelijke snijsnelheid een belangrijke invloed op de snijkwaliteit. Om een hoogwaardige snede te bereiken, hebben we gekozen voor de snijsnelheid van 80 m/s, omdat deze de snijkracht produceert die de interactie tussen de werkstukatomen snel kan vernietigen [16].
In moleculaire dynamische simulaties bij lage snijsnelheid zoals 10 m/s, atomaire verplaatsingskaarten en het patroon hoe de snijkracht van siliciumcarbide schurende deeltjes en snijhoeken variëren met de simulatiestapgrootte, zoals getoond in Fig. 3 en 4. Omdat de snijsnelheid te klein is, is ook de snijkracht onvoldoende, waardoor de vervorming en dislocatie van het rooster veel minder is. Over het geheel genomen is de snij-efficiëntie laag en is de snijkwaliteit relatief slecht. Daarentegen, wanneer de snijsnelheid bij microscopische experimenten tot 80 m/s is, kunnen chemische bindingen tussen koperatomen snel en effectief worden verbroken om het doel van onmiddellijk snijden van hoge kwaliteit te bereiken. Daarom is na een uitgebreide analyse een snijsnelheid van 80 m/s redelijk voor de simulatie.
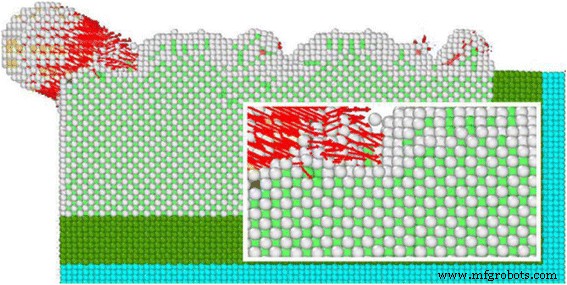
Atomaire verplaatsing met lage snelheid
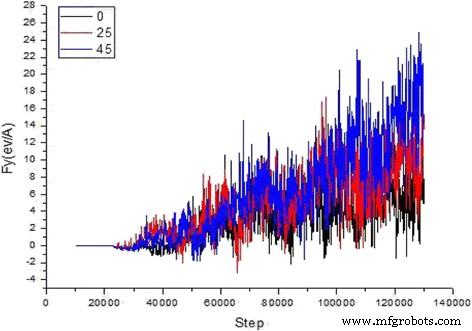
De relatie tussen de snijkracht, de snijhoek en de simulatiestap
Om de haalbaarheid en geloofwaardigheid te simuleren, kiezen we een redelijke empirische potentiaalfunctie om de interatomaire potentialen van atomen te beschouwen. Volgens de verschillende objecten kunnen we de potentiële functie verdelen in een paarpotentiële functie en een veellichamenpotentiële functie. De twee modellen tussen monokristallijn koper en slijpkorrels beschrijven de interatomaire potentialen van atomen daartussen door middel van Morse-potentiaal [17], de EAM-potentiaal wordt gebruikt om de interatomaire potentialen van atomen tussen koperatomen te beschrijven [18,19,20], en de interactie tussen SiC-deeltjes wordt beschreven met behulp van de Tersoff-potentiaal [21].
Tijdens het polijstproces is de botsingsrichting van de slijpkorrels in het medium willekeurig; hun banen lopen niet precies langs het oppervlak van het werkstuk. Tijdens het microsnijproces staat de snijrichting van de slijpkorrels niet altijd loodrecht op het werkstukmateriaal. De snijhoek verwijst naar de mate van de hoek tussen de snijrichting van de slijpkorrel en het horizontale vlak. Het is positief wanneer deeltjes het werkstukoppervlak naderen. De schets van de snijhoek wordt getoond in Fig. 5.
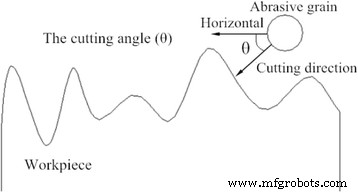
De schets van de snijhoek. Figuur 5 is de schets van de verschillende snijhoeken wanneer de slijpkorrels worden gesneden. Schuurkorrel uit verschillende richtingen die het werkstukmateriaal snijden, het materiaal zal de prestaties hebben en de verwerkingskwaliteit zal anders zijn
In deze studie wordt MD-simulatie gebruikt om multi-schuurmiddelen met verschillende inslagrichtingen van het gesneden monokristallijne koper te simuleren. Zoals getoond in Fig. 5, ligt de snijhoek tussen 0° en 45° terwijl het oppervlak van het koperen werkstuk ruw is.
Resultaten en discussie
Analyse van botsing tussen SiC-slijpmachines
De impact van siliciumcarbide schuurmiddel op het snijden van monokristallijn kopermateriaal wordt bereikt door de roosterstructuur van eenkristal van kopermateriaal te vernietigen. Tijdens de afbraak werden interacties tussen koperatomen, de schuifspanning opgelegd door C, Si-atomen of SiC-schuurdeeltjes op de Cu-atomen van werkstukmateriaal geïdentificeerd als de snijkracht, wat een belangrijke fysieke parameter is voor het feit dat de snijkracht weerspiegelt diepgaand het verwijderingsproces van enig kristalkoper werkstukmateriaal. Zoals eerder besproken, is er een groot verschil tussen micro- en macro-snijkracht. Over het algemeen is macro-snijkracht de som van snij- en slijpkracht, terwijl bij microsnijden de snijkracht wordt gegenereerd door de interacties tussen de slijpkorrels en de atomen van het werkstuk.
In Fig. 6 hebben we de veranderingen van de schuifspanning van slijpkorrels in verschillende richtingen, het effect van de schuifspanning in verschillende richtingen en de verdeling van snijkrachten over verschillende snijhoeken getoond.
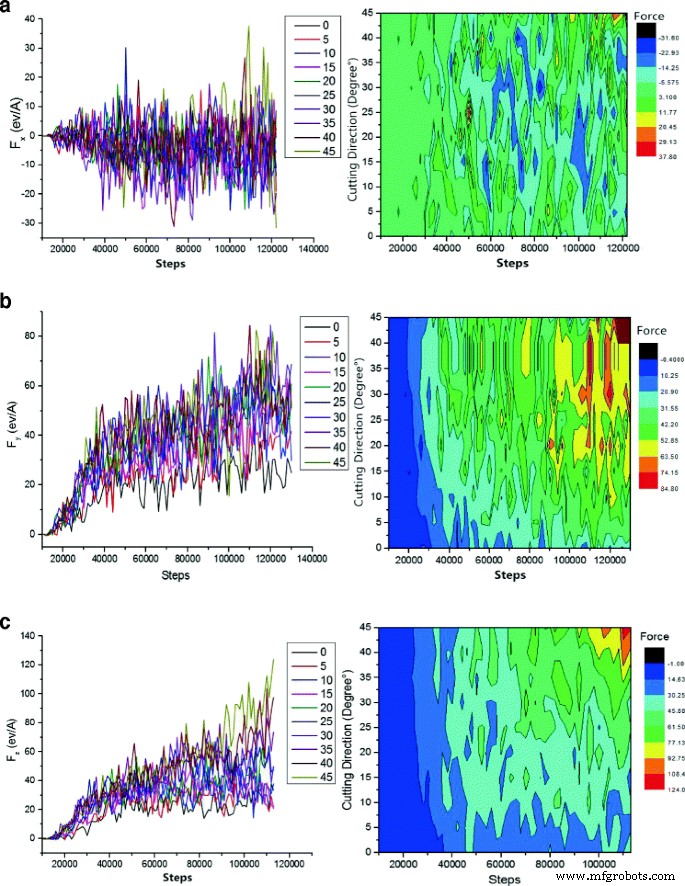
Hoe snijhoek en simulatiestapgrootte de snijkracht beïnvloeden. Figuur 6 toont SiC schurende snijkracht en het snijhoek- en simulatiestapdiagram, met toenemende snijdiepte neemt het aantal kristalstructuur van vernietiging toe, de maximale waarde van de fluctuatie van snijkracht wordt ook groter. een [100] richting van de snijkracht. b [010] richting van de snijkracht. c [001] richting van de snijkracht
De siliciumcarbide-slijpkorrels sneden en sloegen in op monokristallijn kopermateriaal in verschillende hoeken, zoals [010] en [100]. De snijkrachten in de richtingen [001] en [010] waren afschuifkrachten. Bij verdere simulatie nam de snijdiepte geleidelijk toe, wat de snijkrachten in de richtingen [001] en [010] voortdurend heeft verhoogd. Tot een bepaalde grens fluctueerden deze krachten echter, zoals blijkt uit figuur 6. Wanneer schurende deeltjes naar de materialen van het werkstuk bewogen, heeft dit de interactie (van aantrekking naar afstoting) tussen de buitenste koperatomen en de atomen totaal veranderd. van SiC (Si en C). Aanvankelijk waren bij het slijpen van het werkstukmateriaal de snijkrachten onvoldoende door de aanwezigheid van afstotende krachten van koperatomen. Voor het afwerkingsproces moeten de snijkrachten voldoende hoog zijn zodat de slijpkorrels gemakkelijk de chemische bindingen in koperatomen kunnen verbreken om vrij te kunnen bewegen. Bovendien heeft de toename van de snijdiepte een directe relatie met de atomaire interacties. Toen de atomen zich begonnen op te stapelen, nam de snijkracht consequent toe totdat de schurende deeltjes het werkstuk binnendringen, wat een constante snijkracht vereiste. In deze relatief stabiele fase werd de snijkrachtfluctuatie onderworpen aan de mate van roostervervorming, roosterreconstructie, amorfe faseverandering en generatie van chips. Terwijl de slijpkorrels in de snijrichting marcheerden, werd een externe kracht uitgeoefend op het koperatoom in het FCC-rooster, wat resulteerde in verplaatsingen van de koperatomen. Deze verplaatsing laat het FCC-rooster instorten en transformeert het in een nieuwe roosterstructuren met dislocatie. Een soortgelijke situatie wordt ook waargenomen bij de snijkracht. Er is geen positieve lineaire correlatie tussen de snijkracht in de richting van [010] en de botsingshoek van deeltjes. Bij de botsing met 0°, 5°, 10° en verder was de kracht in [010] richting kleiner en minder fluctuerend dan die in andere snijrichtingen. Snijden onder een kleinere hoek, verwijder in principe bramen, aangezien de braam kan worden gedefinieerd in een hoogtebereik van 3,5 ~ 15 . Bij vergelijking van deze richtingen met elkaar, als de snijdiepte relatief kleiner is, zal de schade en vervorming van de kristalstructuur matig zijn. Daarom werd in het hele snijproces de afschuifkracht langs de [010]-richting kleiner gehouden, zoals weergegeven in de curvegrafiek van Fig. 6b. In de latere simulatiefase bereikte de snijkracht het minimum van 0°. Er is ook gevonden dat de snijkracht een directe relatie heeft met de hoek zoals getoond in figuur 6c, wat kan worden toegeschreven aan het feit dat wanneer de deeltjessnelheid 80 m/s bereikt, een grotere snijhoek wordt bereikt. Aan de andere kant, bij dezelfde simulatiestap, hoe groter de componentsnelheid in de [001] richting, hoe groter de hoek, hoe dieper de deeltjes werden gesneden en hoe meer atomaire roosters werden vernietigd. Er was echter een positieve correlatie tussen de snijhoek en de snijkracht. Wanneer korrels in de richting [100] bewogen, waren wrijvingen tussen C-, Si- en Cu-atomen de bron van snijkracht. De snijkracht vertoonde dus geen geleidelijk stijgende trend. Bij verdere simulatie nam de snijkracht echter toe en fluctueerde, wat nauw verband hield met de vervorming en reconstructie van het rooster en het genereren van amorfe structurele faseovergang. Voordat de schurende deeltjes zouden kunnen vernietigen, wordt de interactie tussen de atomen van het werkstuk bereikt om materiaal te verwijderen, wat uiteindelijk de snijkracht consequent heeft verhoogd. Bij het verhogen van de abrasieve snijkracht, voorbij de kritische waarde (atoombindingskracht), wordt het atoomrooster beschadigd en dissociëren de bindingen, wat resulteert in een amorfe structuur. Bij het bereiken hiervan daalde de snijkracht tot een relatief lage waarde. De snijkrachtfluctuaties verschenen continu tijdens het hele proces van abrasieve stroombewerking, wat te wijten is aan de toename van de snijdiepte, en er vond meer vernietiging van de kristalstructuur plaats. Er wordt dus geconcludeerd dat in dit stadium de maximale waarde van de fluctuatie van de snijkracht groter was. Zoals weergegeven in Fig. 6b, nam het rode gebied een groter gebied in beslag tijdens de latere simulatiefase, wat aangeeft dat de snijkracht aanzienlijk was verhoogd. Onder dezelfde simulatietijd was de snijkracht kleiner wanneer de snijhoek minder dan 15° was, wat betekent dat een klein deel van het kristalrooster werd vernietigd.
Energieanalyse voor het SiC Abrasive Impact Cutting-proces
De totale energie van de thermodynamica is de som van de totale potentiële energie en de totale kinetische energie in een systeem, die het effect laat zien van het werk dat door slijpkorrels op het werkstuk wordt gedaan. De invloed van de snijhoek op siliciumcarbide-slijpmiddel op de energieverandering van het systeem wordt getoond in Fig. 7. Tijdens het snijden van eenkristal koperen werkstukmaterialen met siliciumcarbide-slijpkorrels, werkt het werk dat wordt gedaan door slijpkorrels op werkstukmateriaal. op twee manieren; een deel wordt omgezet in kinetische energie die de warmte van eenkristalkoperatomen verhoogt contact met siliciumcarbidedeeltjes werkt polijsten, het andere deel wordt omgezet in potentiële energie die veranderingen in de interne structuur van het eenkristalkoperen werkstuk mogelijk maakt, de roostervervorming en de roosterenergie die vrijkomt.
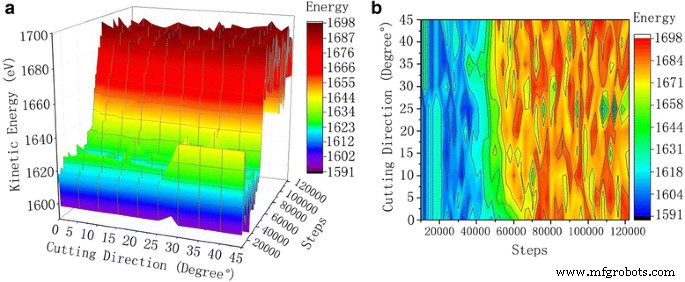
Kinetische energiecurve van de werkstukatomen. Figuur 7 is de kinetische energiecurve van de verschillende snijhoeken tijdens het snijproces. Met de toename van het aantal simulatiestappen fluctueert de kinetische energie van de atomen in een laag bereik, en vervolgens naar een hoger bereik binnen de fluctuaties. een 3D-curve. b Contour
Tijdens het snijden van slijpkorrels van een eenkristal koperen werkstuk, is de kinetische energie van het systeem nauw gerelateerd aan het werk dat door SiC-schuurmiddelen aan het werkstukmateriaal wordt gedaan. Door op elk moment de snelheid van deeltjes in het systeem te berekenen, kan de totale kinetische energie van het systeem worden berekend:
$$ K=\sum \limits_{i=1}^N\frac{1}{2}{m}_i\left({v}_{\mathrm{ix}}}^2+{v}_{\ mathrm{iy}}^2+{v}_{\mathrm{iz}}^2\right) $$ (1)In de formule, \( {v}_{\mathrm{ix}}^2 \), \( {v}_{\mathrm{iy}}^2 \), en \( {v}_{\mathrm {iz}}^2 \) vertegenwoordigen de snelheidscomponent x , j , z richting atomen, respectievelijk.
De kinetische curve in Fig. 7 bracht ons tot de conclusie dat bij toenemende simulatiestappen de kinetische energie van de atomen aanvankelijk fluctueert in een laag bereik en vervolgens in een hoger bereik. Met de beweging van slijpkorrels wordt een afstotende interactie over lange afstand gevonden tussen de buitenste koperatomen en Si, C-atomen (SiC). De koperatomen in het werkstuk beginnen kinetische energie te krijgen en te bewegen. Wanneer de siliciumcarbidedeeltjes in contact komen met het eenkristal van koper, neemt de atomaire temperatuur van het contactgebied toe, waardoor de atomaire thermische beweging toeneemt. Wanneer het snijden stabiel is, wordt de kinetische energie van de koperatomen in het materiaal overgebracht en getransformeerd in een dynamisch evenwichtspatroon, en fluctueert de kinetische energie van de atomen in een hoog bereik.
Analyse van de kinetische energie bracht ons tot de conclusie dat tijdens het snijproces, wanneer de deeltjes contact beginnen te maken met het werkstuk, de atomen in het geëxtrudeerde gebied roostervervorming ondergaan, atomaire coördinaten veranderen en verplaatsing verandert met kinetische energie. Met de schurende deeltjes die in eenkristalkoper terechtkomen, verschijnt de piekwaarde van de kinetische energie van het eenkristalkoperen werkstuk wanneer het werkstuk het werkstuk volledig binnengaat. Omdat de kinetische energie en potentiële energie van schurende deeltjes slechts onderling worden getransformeerd. De energie van het hele systeem zal echter niet veranderen, behalve de bewegende deeltjes die het werkstuk binnenkomen. Bovendien dwingt de beweging van siliciumcarbidedeeltjes de werkstukatomen om gelijktijdig met hen te bewegen. De warmte die wordt gegenereerd tijdens de atomaire wrijving wordt vrijgegeven door de kinetische energie en de spanningsenergie die vrijkomt als gevolg van dislocatiebeweging.
De conversie tussen warmte en kinetische energie wordt berekend met de volgende formule:
$$ \frac{1}{2}{\sum}_i{m}_i{v}_i^2=\frac{3}{2}{nk}_B{T}_i $$ (2)In formule, n is het aantal atomen; vi staat voor de momentane snelheid; k B is de Boltzmann-constante, en T ik is de temperatuur van de atomen.
De snijkracht verhoogt de atoomtemperatuur van het gebied waar het schuurmiddel in contact komt met het werkstukmateriaal. Bij beschouwing van de thermische beweging van het atoom en de kinetische energie van de atomen, neemt de kinetische energie van de koperatomen gedeeltelijk toe. Het gesimuleerde systeem is ingesteld op het canonieke ensemble; de totale systeemtemperatuur schommelt binnen een bepaald bereik. De warmte die wordt geproduceerd tijdens het snijden van schurende deeltjes wordt snel overgebracht naar de atoomlaag met constante temperatuur, zodat de algehele kinetische energie van het systeem zeer weinig verandert.
Zoals blijkt uit de potentiële energiecurve van figuur 8, neigt bij verhoging van het aantal simulatiestappen ook de potentiële energie onder het monokristal van koperatomen in het werkstuk toe te nemen. Wanneer siliciumcarbide schuurmiddel contact maakt met het eenkristal van het koperen werkstuk van begin tot volledig stabiel snijden, vervormt het werkstukmateriaal geleidelijk en verdringen de koperatomen, wat leidt tot de vervorming van het kristalrooster in het kristal. Dit resulteert ook in een elastisch spanningsveld, waarbij de rekenergie toeneemt. Wanneer de spanningsenergie niet voldoende is om de materiële atomen te herschikken, treedt de dislocatie van atomen op die de totale energie van het systeem verhoogt. In tegenstelling tot de potentiaalcurven van 0° tot 45°, zien we een consistentie in thermische beweging van atomen bij constante temperatuur. Er is geen significant verband tussen de atomaire kinetische energie en de snijhoek van SiC-slijpkorrels. De kinetische energie van de atomen hangt nauw samen met de thermische beweging van atomen. De verandering van potentiële energie en totale energie is echter duidelijk gerelateerd aan de snijhoek van SiC-slijpdeeltjes. De grootte van de atomaire potentiële energie neemt toe met toenemende snijhoek. Wanneer de snijhoek tussen 0° en 20° ligt, wordt een duidelijke verandering in potentiële energie waargenomen. Wanneer de snijhoek echter tussen 25° en 45° ligt, blijft de potentiële energie als zodanig en zijn de algemene potentiële energiecurven van 0° tot 20° snijhoek. Zoals getoond in Fig. 9 is de totale energietrend vergelijkbaar met die van de potentiële energiecurve. De totale energiewaarden van alle snijhoeken liggen zeer dicht bij elkaar. Dit komt doordat de totale energie gelijk is aan de potentiële energie en kinetische energie van het systeem, terwijl de kinetische energie tijdens het snijproces niet mee verandert met de snijhoek. De verandering in kinetische energie van het werkstuk is erg laag met verschillende snijhoeken. Daarom is de veranderingscurve van de potentiële energie vergelijkbaar met de curve van de totale energie. Als we de atomaire verplaatsingsdiagrammen van Fig. 9 vergelijken, blijkt dat onder dezelfde snijconditie de snijdiepte in een eenkristal koperen werkstuk groter is wanneer de snijhoek tussen 25° en 45° ligt, wat kan worden toegeschreven aan de grotere verplaatsing van koperatomen. Langs de [001] richting van SiC-deeltjes worden meer atomaire beschadiging in het rooster en dislocaties gegenereerd. De rekenergie die gedurende deze tijd wordt geproduceerd, is hoger, wat resulteert in een hoge potentiële energieveranderingscurve en een totale energieveranderingscurve van de werkstukatomen.
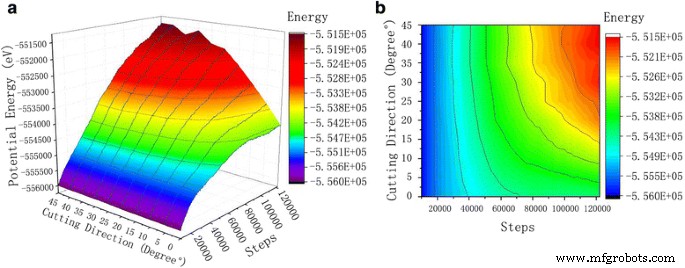
Potentiële energiecurve van het werkstuk. Figuur 8 is een grafiek van potentiële energievariaties bij verschillende snijhoeken tijdens het snijproces. Met de toename van het aantal stappen voor simulatie, neigt de potentiaal tussen de monokristallijne koperatomen van het werkstuk toe te nemen. een 3D-curve. b Contour
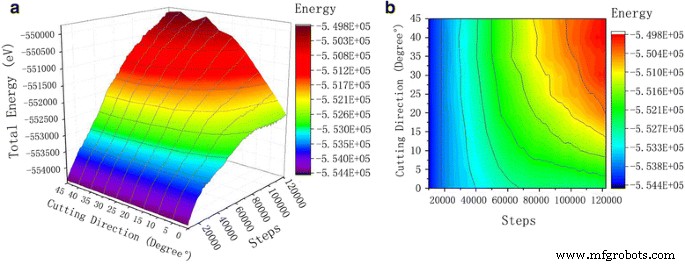
Totale energiecurve. Figuur 9 toont de totale energiecurve. Tijdens het SiC-snijden van het eenkristalkoperen werkstuk manifesteert het effect van de slijpkorrels op het werkstuk zich in twee vormen:een deel daarvan wordt omgezet in kinetische energie, de atoomwarmte wordt verhoogd en de lokale kinetische energie wordt groter bij het polijsten het gezamenlijke gebied van het eenkristalkoperwerkstuk en de SIC-deeltjes; het andere deel wordt omgezet in potentiële energie, de interne structuur van het monokristallijne koperen werkstuk wordt veranderd, het rooster wordt vervormd en de roosterenergie komt vrij en verandert in potentiële energie. een 3D-curve. b Contour
Analyse van atoomverplaatsing in SiC schurende deeltjes botsen snijproces
Bij het snijproces van werkstukmateriaal onder verschillende hoeken, bewegen de slijpkorrels in de snijrichting, waardoor de koperatomen in het werkstuk gedwongen worden te bewegen. Uit de analyse van de bewegingsrichting van het werkstuk, het effect van de slijpkorrels op het werkstukmateriaal, hoe de spaanvorm en de materiaalafname volledig worden opgehelderd. Volgens de bindingshoekanalysemethode, voorgesteld door Ackland-Jones, wordt verschillende atomaire roosterstructuur gemarkeerd door gediversifieerde kleuren, voor observatiedoeleinden en analyse. Het ZOY-vlak is geselecteerd om het snijproces van een afzonderlijk SiC-deeltje te observeren, en het atomaire verplaatsingsdiagram van het snijgebied wordt vergroot, zoals te zien is in figuur 10.
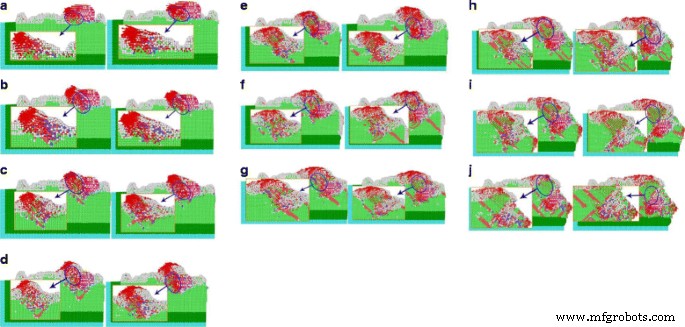
Verschillende snijhoeken veroorzaken atomaire verplaatsingen. Figuur 10 beschrijft atomaire verplaatsingen van verschillende snijhoeken. Wanneer de eenkristal SiC-slijpdeeltjes botsen met het werkstuk dat koper in verschillende richtingen snijdt, terwijl SiC-slijpkorrels worden gesneden, neemt de snijdiepte toe, aangezien de snelheid van de snijrichting 80 m/s is, de [001] richting De bewegingssnelheid is v z = 0.8 ∗ sin θ , met toenemende snijdiepte van de snijhoek, verhoogt [001] in dezelfde snijhoek simulatiestappen, is de snijdiepte tegelijkertijd groot. een 0° verplaatsing. b 5° verplaatsingen. c 10° verplaatsing. d 15° verplaatsing. e 20° verplaatsing. v 25° verplaatsing. g 30° verplaatsing. u 35° verplaatsing. ik 40° verplaatsing. j 45° verplaatsing. (atomaire kleur: HCP-structuur,
BCC-structuur,
FCC-configuratie als een witte amorfe structuur)
Wanneer de éénkristal SiC-schuurdeeltjes botsen met het werkstuk dat koper in verschillende richtingen snijdt, neemt de snijdiepte tijdens het proces toe. De snelheid van de snijrichting is 80 m/s, waarbij de componentsnelheid in de [001] richting v is z = 0.8 ∗ sin θ . At the same simulation step, cutting depth increases with increasing the cutting angle. As shown in Fig. 10, there is an atomic position shift in both of the surface and interior of the workpiece material, contacting with the abrasive grains, where atoms of different lattice types are arranged and doped with each other. Due to the movement of these abrasive particles, the copper atoms accumulated at the tip of the abrasive grains, which results no cracks during abrasive particles cutting. It can be seen that the material removal mode of the abrasive particles is plastic deformation. At the same time, due to abrasive cutting, the atoms displacement in single crystal copper increases from 15° to 45°.
The number of the workpiece atoms along the abrasive grain motion direction also increases, and the atomic displacement is perpendicular to the direction of abrasive cutting. This part of the atomic displacement is due to that of the abrasive particles, change the cutting action to the extrusion upon the workpiece atoms. At cutting angle, the abrasive particles is between 0° and 10°, while the cutting depth is smaller than those of the 15° to 45°. Abrasive particles are performing mainly the cutting function, the extrusion of the workpiece atoms is marginal, and the number of atoms is small whose displacement direction is perpendicular to the direction of the abrasive grain motion. With the repeated cutting on the workpiece surface by numerous abrasive particles, the abrasive particles having large cutting angle produce deep pits on the workpiece material during the whole cutting process, while ones following smaller cutting angles will continue cutting along the cutting mark produced by the former. Under the combined action, the workpiece material is cut to a certain depth (micro-cutting) followed by whole abrasive flow polishing.
Dislocation Collision Analysis for SiC Abrasive Cutting
Dislocation is a special arrangement of atoms in crystal along certain crystal surface and crystal direction, or a boundary between the slip zone and the non-slip zone on the slip surface. Dislocation can be divided into edge dislocation, spiral dislocation, and mixed dislocation, among which mixed dislocation is most common. In the process of abrasive particle cutting, the single crystal copper workpiece is plastically deformed, the atoms move, and the crystal lattice breaks and reconstructs, which results in a large number of dislocations. The analysis for dislocation and bond angles at different incidence angles is shown in Fig. 10. In the simulation model of abrasive flow simulation, two abrasive particles are used for cutting the workpiece material. For ease of analysis, the generation and change of different dislocation lines in single crystal copper material, during cutting process and the different lattice structures in the cutting part are analyzed in the view of one single SiC particle on the YOZ surface, as shown in Fig. 11.
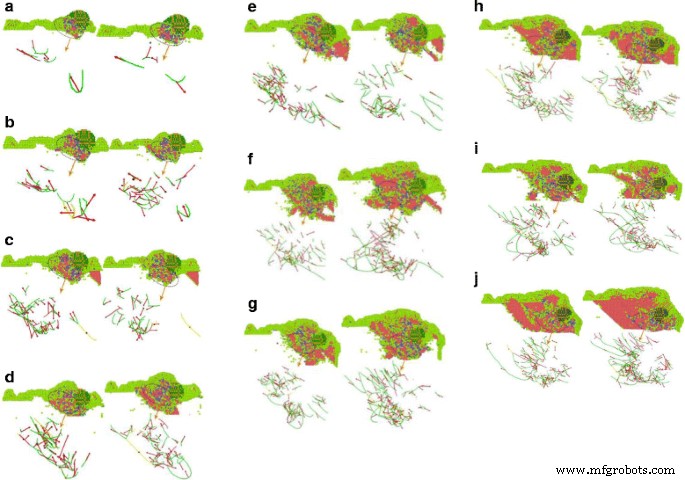
Different angles-bond angle dislocation line charts. Figure 11 represents the cutting dislocation line and the bond angle. As the repeated cuttings on the workpiece surface are done by the numerous abrasive particles during the polishing process, in the entire cutting process, the abrasive particles with larger cutting angle produce bigger pits, while the following abrasive particles with smaller cutting angles continue to polish along the cutting trace. Therefore, certain depth is done on the workpiece material and the whole micro-cutting of abrasive flow polishing is achieved. een Dislocation lines with 0° cutting angles. b Dislocation lines with 5° cutting angles. c Dislocation lines with 10° cutting angles. d Dislocation lines with 15° cutting angles. e Dislocation lines with 20° cutting angles. v Dislocation lines with 25° cutting angles. g Dislocation lines with 30° cutting angles. u Dislocation lines with 35° cutting angles. ik Dislocation lines with 40° cutting angles. j Dislocation lines with 45° cutting angles. (Note:the upper part of the key angle analysis, the figure in the atomic color: HCP
BCC
Amorphous structure
Abrasive grain; the lower part of the dislocation line diagram, the figure dislocation line color:
Stair-rod,
Shockley,
Hirth,
Perect,
Frank,
Burgers vectors)
Key angle analysis diagram of each cutting angle is shown in Fig. 11, where the sample from the interior workpiece simulation at time 60 and 70 ps, the atoms are colored individually according to different arrangement of atoms through BAD technology. To facilitate the analysis of the lattice changes in the cutting part, atoms of the FCC structure in the workpiece material are removed. By DXA techniques, different types of dislocations are marked in diverse colors:red arrow indicates the Burgers vector (Burgers vectors), green for Shockley partial dislocations (Shockley), light blue for the Frank partial dislocations (Frank), pink pole position for the pressure error (Stair-rod), and blue for the whole dislocation (Perfect).
As can be observed from the analysis of the bond angle portion in Fig. 11, a large number of dislocations and lattice deformations occurred under the impact of external cutting forces. The bond angle analysis shows that the internal HCP structure of the workpiece appears more clearly with increasing of cutting angle. On further simulations, the structure of HCP increases gradually. The silicon carbide particles continuously cut and squeeze the workpiece material at 80 m/s speed, resulting in a phase transition from the FCC structure to the HCP structure. During this phase transition, the atomic strain of the workpiece continues to increase. However, when the stress state of atoms of the workpiece has exceeded the threshold of thermodynamic phase transition, it turns to metastable state. As the strain increases, the HCP phase begins to nucleate and grow spontaneously, and the FCC lattice of copper undergoes absolute destabilization, which induces a sudden change in mechanical quantities. As the kinetic energy of the atom is directly related to the atomic temperature (formula 1), there is a saltatory augment in the kinetic energy change curve, as can be seen from Fig. 7. This is due to high strain energy, accumulated in the single crystal copper workpiece before the nucleation of HCP. The HCP structure increases the system temperature through metastable nucleation and partial stress release. Due to the abrasive cutting and extrusion, bonds of copper atoms in workpiece material break down which results in disorder. The original regular lattice structure is broken, where the partial copper atoms gradually change into disorder and form an amorphous structure. It can be seen from the bond angle analysis diagram that (Fig. 11) atoms with relatively disordered displacement tend to form amorphous structures at 60 and 70 ps, which is because of silicon carbide abrasive particles. At the same time, many atoms with the same displacement direction are transformed into HCP structures. Meanwhile, the particles shear downward and the atomic structure is rearranged due to the displacement of atoms in the original amorphous structure, results an amorphous structure of HCP. Atoms that have already been transformed into HCP structures, even before the next cut stage, change back into amorphous structure. As the cutting depth increases, the number of amorphous atoms near the abrasive particles also increases.
When the FCC crystal structure undergoes cutting by abrasive particles, a shear stress generates in atoms, which results in the displacement of atoms in the lattice and the arrangement of various lattice structures. In moving the atoms of workpiece, the rigid displacements of the atoms produce dislocations, also called as dislocation lines (Fig. 11). Dislocation line can be termed as the boundary between the slip zone and the non-slip zone, on the slip surface. According to the relation between the dislocation and the PATS vector, dislocation is parallel to the PATS vector, called the screw dislocations. The vertical ones are edge dislocations, and the mixed dislocations are neither parallel nor vertical. In Fig. 11, most of the dislocation lines are neither parallel nor vertical to PATS vectors, which are typical mixed dislocations. In the cutting process of abrasive particles, the dislocation line changes, moves and grows around the abrasive particles. The closer the particle, the greater the density of the dislocation line. Dislocation lines are also very dense, when the arrangement of atoms is complicated. The abrasive particles marked as orange, produce a large amount of HCP, BCC, and amorphous structures around them, which interlace and blend with each other to form dislocations that increases the internal energy of the crystals. When atoms arrange their self just like shown in Fig. 12b, possess maximum potential energy. While for the arrangement, shown in Fig. 12a–b, the atoms situate at the lowest potential energy position. The number of dislocation lines is directly related to the magnitude of strain energy of the crystal. The total strain energy of the unit length dislocation can be measured with the given formula:
$$ W=\alpha {Gb}^2 $$ (3)
Schematic view of dislocation changes. Dislocation is a special arrangement of atoms in crystals. It is the crystal in the atomic arrangement along a certain crystal face and crystal orientation occurred in a certain wrong line, and it is the boundary of the slip surface within the area where the slip has occurred and the area with no slip has occurred. In Fig. 12a –c , the relative displacement of the rigidity of the upper atom and the underlying atom produce dislocations, the upper atom belongs to the sliding region, and the lower atoms belong to the non-slip region, they are in the slip surface of the intersection line which is called dislocation line, that is, dislocation. Figure 12 is the process of dislocation generation and development
Where, α is the geometric factor (type dislocations, dislocation density) parameter related to, and generally 0.5 ~ 1.0; G is the shear modulus, and b is the slippage distance.
When the workpiece material is being cut, particles break the atomic arrangement and the lattice reconstructs, which constitutes, macroscopically, the plastic deformation of the workpiece material. In the process of plastic deformation, the dislocation was supposed to escape from the crystal and decrease the dislocation density. However, this dislocation density increases due to dislocation propagation. There are many ways of dislocation multiplication and the main one is the Frank–Reed dislocation source theory, of which the growth mechanism is shown in Fig. 11. As illustrated in Fig. 11, the density of the dislocation line increases markedly from 60 to 70 ps when the cutting simulation proceeds, change both the number and shape of dislocation lines in accordance with Frank–Reed dislocation source theory. At simulation time of 60 ps, there are many long Shockley dislocations. But after another 10 ps simulating, the long Shockley dislocation line becomes less and shorter. The original straight dislocation lines turn into bent, which is especially evident near the abrasive grains. From formula 3, the strain energy of the dislocation is proportional to b 2 . From the viewpoint of energy, the dislocations with the smallest b in the crystal should be most stable with low energy; however, dislocations with larger b will break down into ones. In addition, the energy of the dislocation is valued by the unit length of the dislocation line. Given the shortest line between two points is the straight, the strain energy of straight dislocation is lower than that of the bent one, means straight dislocations are more stable. Frank–Reed dislocation source theory argued that the long dislocation line becomes shorter and breaks down into smaller dislocations, thus decreasing the strain energy of the crystal.
Analysis for Friction Coefficient Between Workpiece Surface and Abrasive Particles
To quantitatively disclose mechanical properties and surface effect of SiC abrasive cutting single crystal copper material, the tangential force ([010] direction) and normal force ([001]direction) on the cutting surface are further analyzed. The friction coefficient can be defined as the ratio of the tangential force to the normal force, with the formula below:
$$ f=\frac{F_y}{F_z} $$ (4)Figure 13 shows the variation of friction coefficient along different cutting angles during abrasive cutting. The change of friction coefficient can be divided into two periods. Period I, when the cutting distance is less than half of the size of the abrasive particle, the friction coefficient fluctuates violently in certain range due to surface effect of the material; while in period II, all the friction coefficients fluctuate in very small range, and the friction coefficients remains steady state at different angles. However, at cutting angle of 5°, there is a small amount of abnormal fluctuation at the end of simulation. Moreover, in period I, abrasive particles contact the workpiece atoms to the abrasive grains enter into the workpiece of half abrasive diameter (shown in Fig. 13b), the cutting movement distance reaches 7.5 Å. In Fig. 6, the cutting force change curve shows that the tangential force and normal force are in an oscillating phase during period I. Since the friction coefficient can be characterized as the adhesion among atoms in the contact surface and is related to the two atoms contacting with each other, regardless of the cutting mode, which can interpret the phenomenon that change of cutting angle does not cause significant change of friction coefficient, as shown in Fig. 13a.
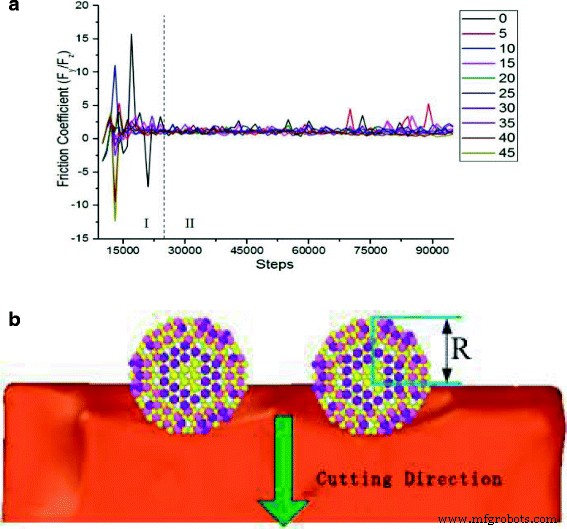
Friction coefficients of different cutting angles. Figure 13 is the changes of the frictional coefficients during SIC particles cutting single crystal copper from different angles. The change in cutting angle did not cause significant changes in friction coefficient. It described two kinds of coefficient of friction in contact with the relevant atoms in the cutting process, regardless of the cutting mode. een Friction coefficient variation curve with cutting angle. b Instantaneous structure when SiC abrasive grains move 7.5 Å
Conclusies
The micro cutting simulation of single crystal copper by SiC abrasive particles is achieved during abrasive flow polishing. Comprehensive analysis of the SiC abrasive cutting reveals that when SiC abrasive particles cut at angle from 0° to 15°, cutting forces in along Y and Z direction are relatively small and tend to stay steady. A larger cutting angle results more dislocations, which brings about larger grooves damaging of the workpiece material. In the process of cutting, it is necessary to avoid more dislocations, which has an immediate adverse effect on the performance of all aspects of crystal material. Therefore, a cutting angle of 0° is better than other angles. Considering the amount of dislocation produced, or the change of cutting force and energy in the cutting process; cutting with small or medium angles is not only beneficial for improving surface quality but reduce the internal defects.
Nanomaterialen
- Oppervlakte-effect op olietransport in Nanochannel:een onderzoek naar moleculaire dynamiek
- Moleculaire dynamische modellering en simulatie van diamantslijpen van cerium
- Toxiciteit van PEG-gecoate CoFe2O4-nanodeeltjes met behandelingseffect van curcumine
- Onderzoek naar wrijvingsgedrag op nanoschaal van grafeen op gouden substraten met behulp van moleculaire dynamiek
- Temperatuur- en drukafhankelijkheid van de elastische eigenschappen van enkelvoudige tantaalkristallen onder <100> trekbelasting:een onderzoek naar moleculaire dynamiek
- Synthese en in vitro onderzoek van een dual-mode probe gericht op integrine αvβ3
- Thermische geleidbaarheid van twee soorten 2D-koolstofallotropen:een onderzoek naar moleculaire dynamiek
- Vergelijkende studie van negatieve capaciteitsveldeffecttransistoren met verschillende MOS-capaciteiten
- Schurende waterstraalbewerking en -snijden
- Voordelen van het lasersnijproces
- Voor- en nadelen van schurend snijden