Hot draperen
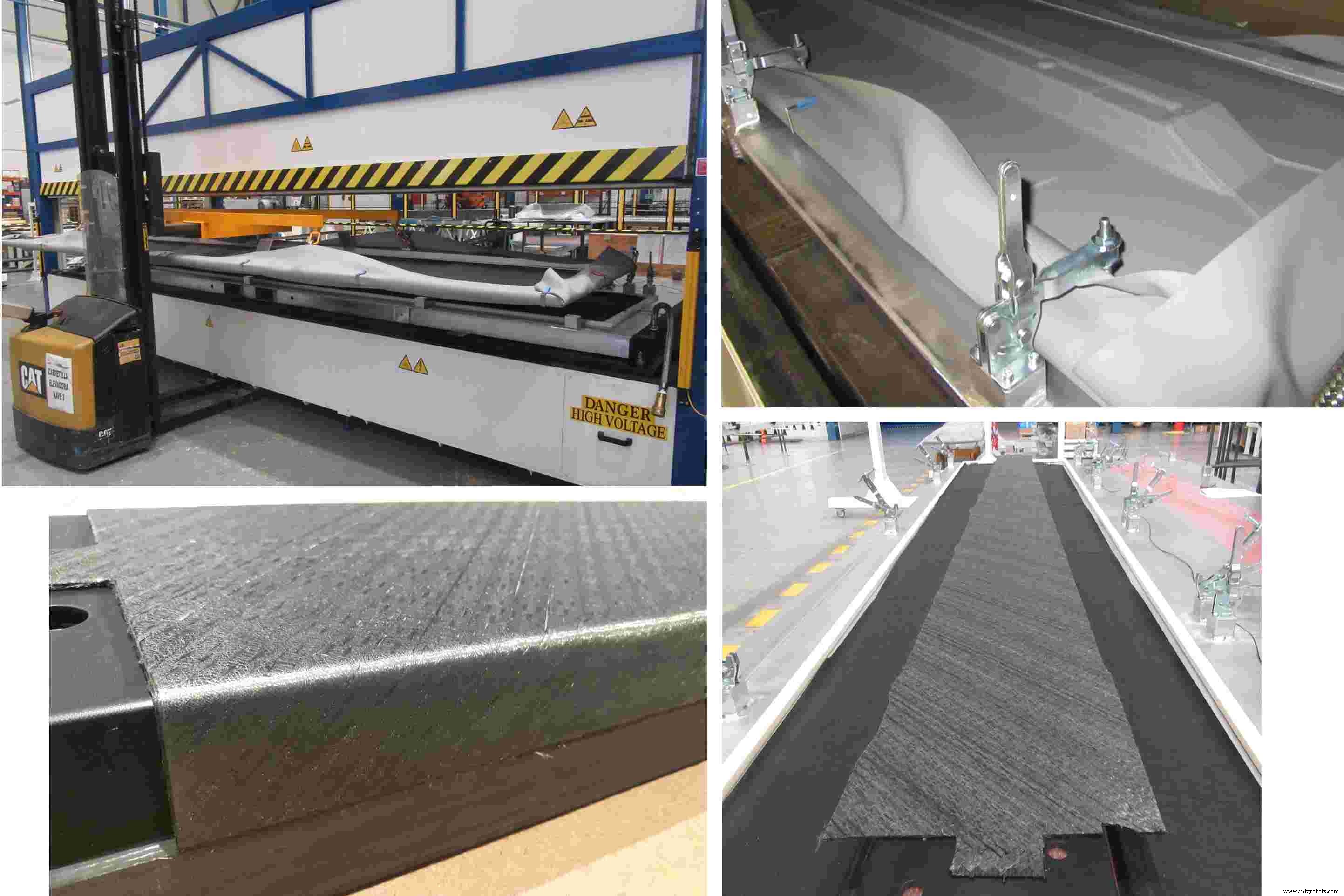
Deze online zijbalk voor het artikel van maart 2021, "Advancing the OOA infused wing box" is bedoeld om samen te brengen wat CW heeft geschreven over het vormen van heet laken in de loop der jaren tot één plek en hopelijk een nuttige bron. Hieronder staan fragmenten uit meerdere artikelen — van 2010 tot 2020 — met foto's om te laten zien hoe hot drape-vorming helpt om de productie van composieten te automatiseren.
2010, GKN Aerospace, A400M rondhouten
Van:"Samengestelde vleugelliggers dragen de enorme turbopropmotoren"
Phil Grainger, technisch directeur en hoofdtechnoloog van GKN Aerospace, legt uit dat het handmatig bouwen van zo'n groot onderdeel, zoals bij de vroege A400M-liggers werd gedaan, traag is, met een neerlegsnelheid van doorgaans 0,75 kg/uur. Tijdens de serieproductie wordt het onderdeel echter plat gelegd, met behulp van een geautomatiseerde tapelaag (ATL) en vervolgens hot drape gevormd in de vorm van de C-sectie. Op dit punt zijn lay-upsnelheden van 25 kg/uur (50 lb/uur) haalbaar. Grainger benadrukt dat dit haalbare gemiddelde tarieven zijn over een dienst, op reële onderdelen.
Om het proces te automatiseren heeft GKN Aerospace geïnvesteerd in een grote ATL met een bed van 20 m/63 ft, vervaardigd door MTorres (Navarra, Spanje). De ATL is in staat om de complexe preforms in hun ontwikkelde vormen te leggen van unidirectionele prepreg, met behulp van een 977-2 koolstofvezel/gehard epoxy uni-tape geleverd door Cytec Engineered Materials Ltd. (nu Solvay, Wrexham, VK). Om de C-sectie te vormen, wordt de voorvorm verplaatst van de tapelaag naar een hete drapeervormer geleverd door apparatuurfabrikant Aeroform Ltd. (Poole, Dorset, V.K.). Om het vacuüm trekken te vergemakkelijken, wordt de lay-up ingeklemd tussen twee membranen gemaakt van Kapton-polyimidefilm, geleverd door DuPont Electronic Technologies (Circleville, Ohio). De ruimte tussen de films wordt geëvacueerd en vervolgens wordt infraroodverwarming van bovenaf toegepast om de temperatuur gedurende een uur tot 60°C/140°F te verhogen. Dit zorgt ervoor dat zelfs het materiaal in het midden van het dikste gedeelte aan het worteluiteinde gelijkmatig wordt opgewarmd tot dezelfde temperatuur. Vervolgens wordt er voorzichtig druk uitgeoefend om het laminaat te vormen, door de twee diafragma's tegen een lichtgewicht gereedschap gedrukt dat nauwkeurig het binnenoppervlak van de ligger weergeeft. Dit C-vormingsproces wordt zeer langzaam bereikt over een periode van 20 minuten. (Na het vormen worden de Kapton-films weggegooid.)
2014, FACC, A321-kleppen
Van:"FACC AG:Aerocomposieten krachtpatser"
In fabriek 3 wordt een grote verscheidenheid aan kleppen, stroomlijnkappen en vluchtbesturingsoppervlakken vervaardigd. Ook hier de efficiëntie van het automatisch leggen van tapes (ATL) en hete draperen worden uitgebuit. De laatste past warmte en druk toe op platte ATL-voorvormen met behulp van een kern en een flexibel vormkussen om driedimensionale vormen te produceren (zie Fig. 7). Een voorbeeld is lopend A321 flapproductie, waarbij gebruik wordt gemaakt van een geavanceerde geautomatiseerde werkcel die op maat is ontworpen door Fill (Gurten, Oostenrijk).
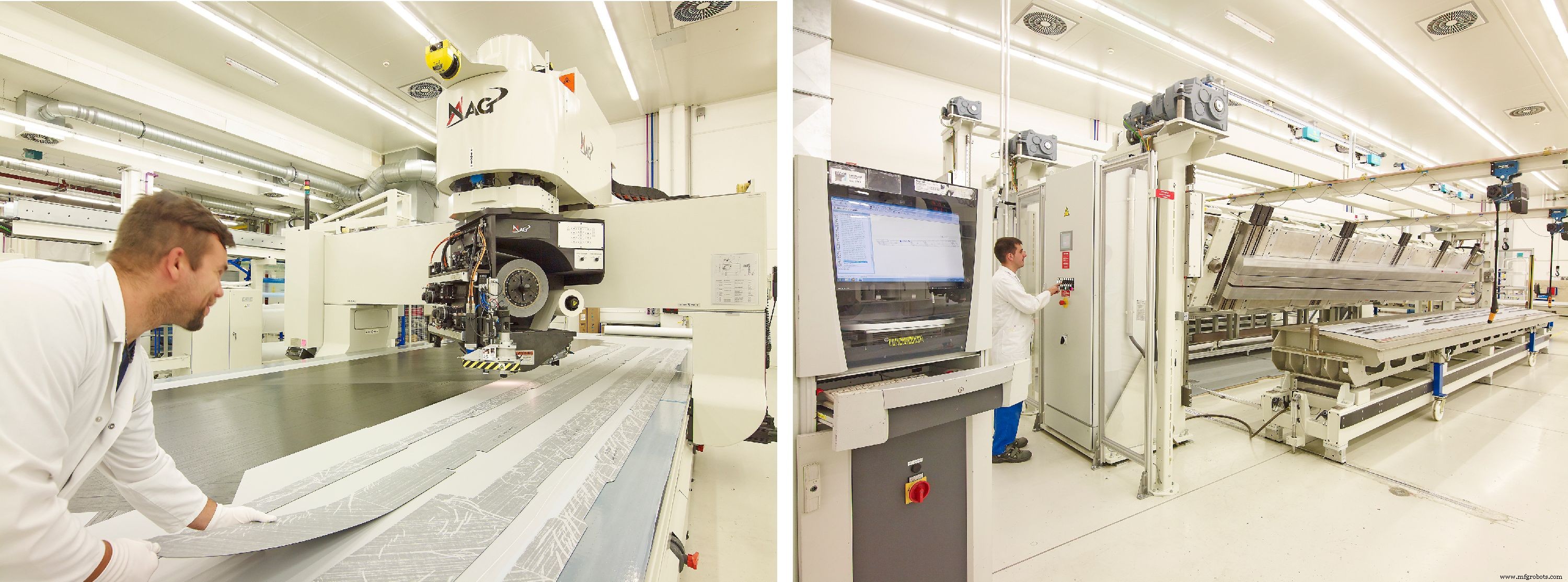
2018, Fill, geautomatiseerde preforming
Uit:"Automated Preforming, Part 7:Fill Gesellschaft"
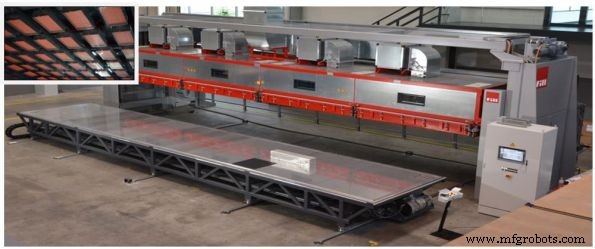
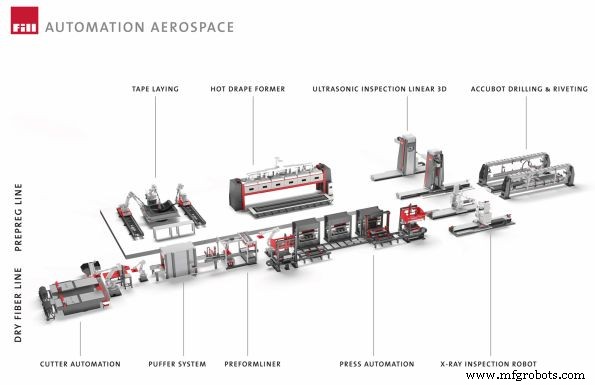
In de recente tourartikelen die Sara Black en ik schreven over hoogwaardige composieten in Israël, merkten we op dat de meeste bedrijven hete draperen gebruikten. . Bij Elbit Cyclone verklaarde onze gids Jonathan Hulaty zelfs:"Ik weet niet hoe je dit soort prepreg-onderdelen met hoge snelheid kunt produceren zonder hot drape-vorming", verwijzend naar balken en rongen voor Boeing 787-assemblages. Warmdoekvormers (HDF) worden ook als onmisbaar beschouwd door FBM en Israel Aerospace Industries.
Fill levert al jaren HDF-systemen, waaronder meerdere units in productie bij FACC. Het zijn in feite vacuümvormende systemen, uitgerust met infrarood- of andere soorten verwarmingselementen en een herbruikbaar siliconenrubbermembraan om prepreg-lay-ups op hun gereedschap te verwarmen en te comprimeren voordat ze worden uitgehard. HDF wordt een belangrijk onderdeel in de hieronder getoonde complete productielijn voor aerocomposieten.
2018, FBM, 787 onderdelen
Uit:"Samenvoeging van ondernemende, metaalgerichte bedrijven claimt de primeur van composieten"
CW wordt eerst naar een cleanroom geleid, waar medewerkers allerlei onderdelen opstapelen. Op een aantal stations, elk uitgerust met een gecomputeriseerd layup-assist computerscherm, ligt de focus deze dag op onderdelen voor de Boeing 787. Gemakkelijk te begrijpen aanraakschermen tonen duidelijk de lay-uphoeken voor elke laag, en hoe ze zijn op elk gereedschap te plaatsen. Een "guillotine"-machine van Century Design (San Diego, CA, VS), met een draaitafel met een diameter van 2 m en een mes in het midden, maakt het snel snijden van schuine lagen uit de carbon/epoxy prepreg mogelijk. Gereedschap voor de deuromlijstingen van de 787 zijn gevormde stalen doornen, meestal langer dan breed, van enkele centimeters lang tot ongeveer 2 m lang, die worden gebruikt om honderden frames, beugels en clips te produceren. Een geautomatiseerde vlakbed snijtafel van Assyst-Bullmer Inc. (Wakefield, VK) wordt door de layup-technici gebruikt om tot 50 gestapelde lagen in één bewerking te snijden.
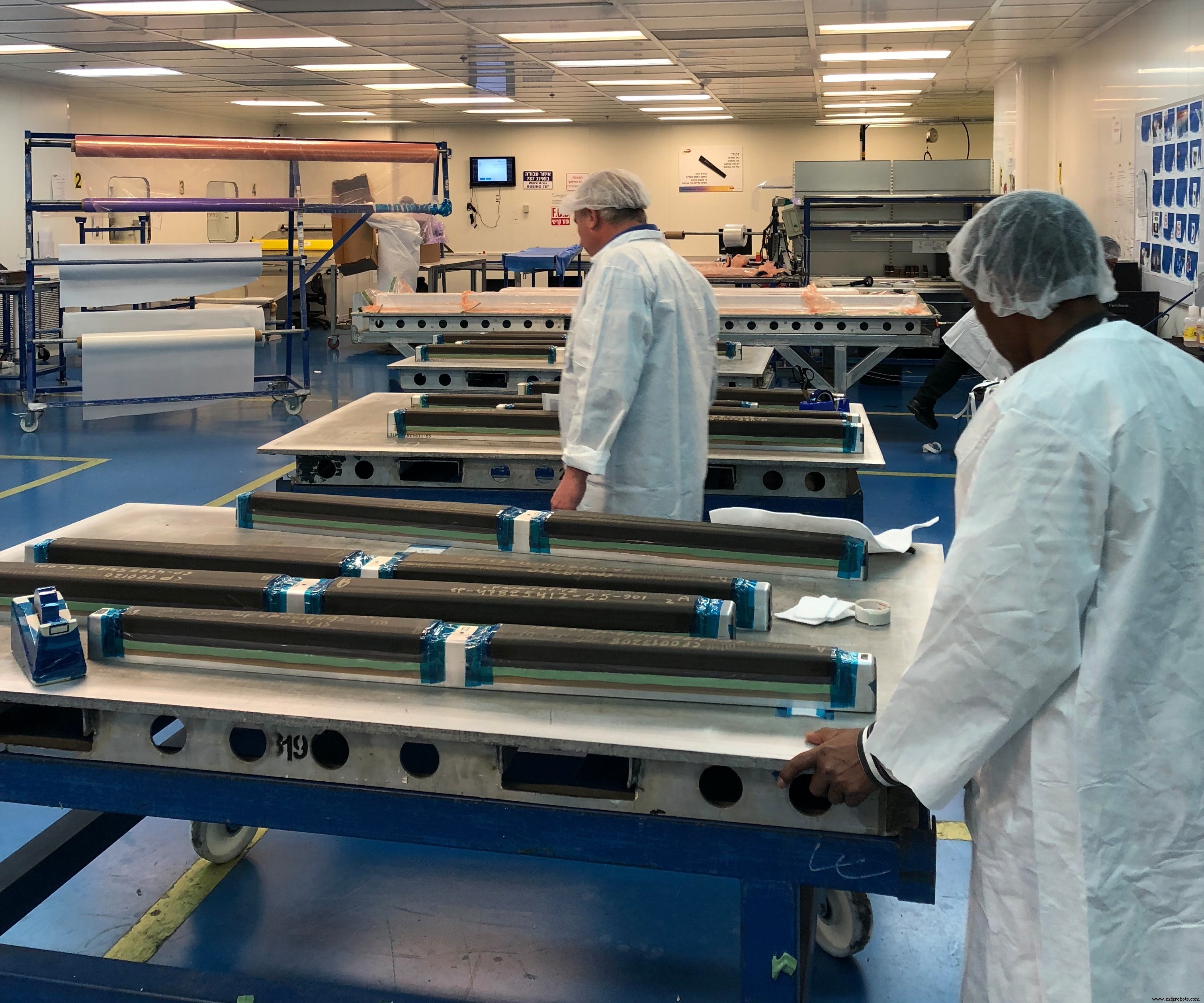
Snijden, afstellen en opleggen van kleine onderdelen in de cleanroom van FBM voor een breed scala aan kleinere geautoclaveerde onderdelen. Fotocredit:CW , Sara Zwart.
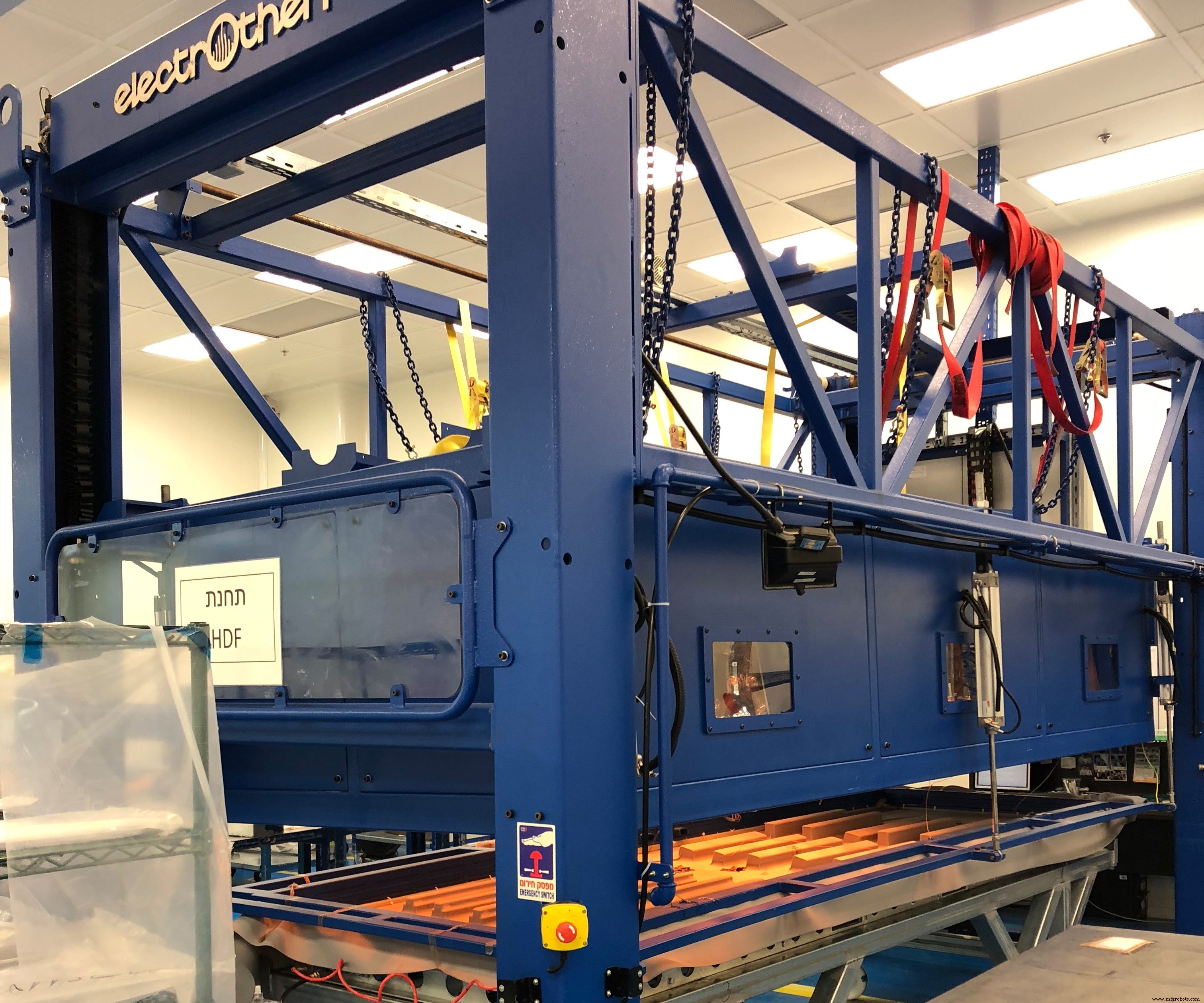
De hot drape-vormmachine van FBM, geleverd door het Israëlische bedrijf Electrotherm Industry, verwijdert tussenliggende debulking-stappen, waardoor maar liefst 50 unidirectionele lagen in één keer worden gevormd, en wordt gecrediteerd voor het versnellen van FBM's lay-upproces voorafgaand aan uitharding. Fotocredits:CW , Sara Zwart.
De cleanroom wordt gedomineerd door een hot drape voormalige (HDF) . Gemaakt door ElectroTherm Industry (Migdal HaEmek, Israël), de statische machine (het bedrijf maakt ook verplaatsbare versies op karren) is een op maat gemaakt vacuümvormsysteem, uitgerust met infrarood verwarmingselementen en een siliconenrubbermembraan om het composiet te verwarmen en te comprimeren layups op de gereedschappen, voorafgaand aan uitharding. De HDF kan maar liefst 50 gestapelde lagen vormen, zegt Poliker, zonder tussenliggende debulking-stappen:"We wilden de complexiteit van het proces elimineren, dus we vormen de lay-ups in één keer." Nadat de prepreg is verwarmd en geconsolideerd in de HDF , wordt een caul over de hele lay-up geplaatst, voorafgaand aan het zakken. Gemaakt met een koolstofvezelcomposiet, vertoont de caul een ruwe oppervlakteafwerking. Poliker zal geen details van het gepatenteerde materiaal onthullen, maar zegt wel dat het de 177 ° C autoclaaf-uithardingstemperaturen aankan:"Het simuleert een gereedschap met een bijpassende matrijs." Hij voegt eraan toe dat de doorngereedschappen indien nodig in-house worden gereviseerd. Zakken en verbruiksartikelen worden geleverd door Airtech International (Huntington Beach, CA, VS).
2018, Elbit Cycloon, 787 onderdelen
Uit:"De composietenwereld in Israël en de VS dienen"
Aan de rechterkant leggen werknemers in de cleanroom voor Boeing 787-onderdelen prepreg voor een reeks onderdelen, van kleine clips en rongen tot complexe J-, I- en C-balken, evenals meerdelige neuslandingsgesteldeuren. Prepreg wordt gesneden met een geautomatiseerde stofsnijder van Assyst Bullmer (Wakefield, VK) en een guillotinemachine om dikke stapels onder elke hoek te snijden. De prepreg vriezer grenst aan de cleanroom. Hulaty merkt op dat soms stapels prepreg worden gesneden, gekit en terug in de vriezer worden geplaatst. Aligned Vision (Chelmsford, MA, VS) laserprojectiesystemen die zich in de cleanroom bevinden, helpen bij het leggen van de hand.
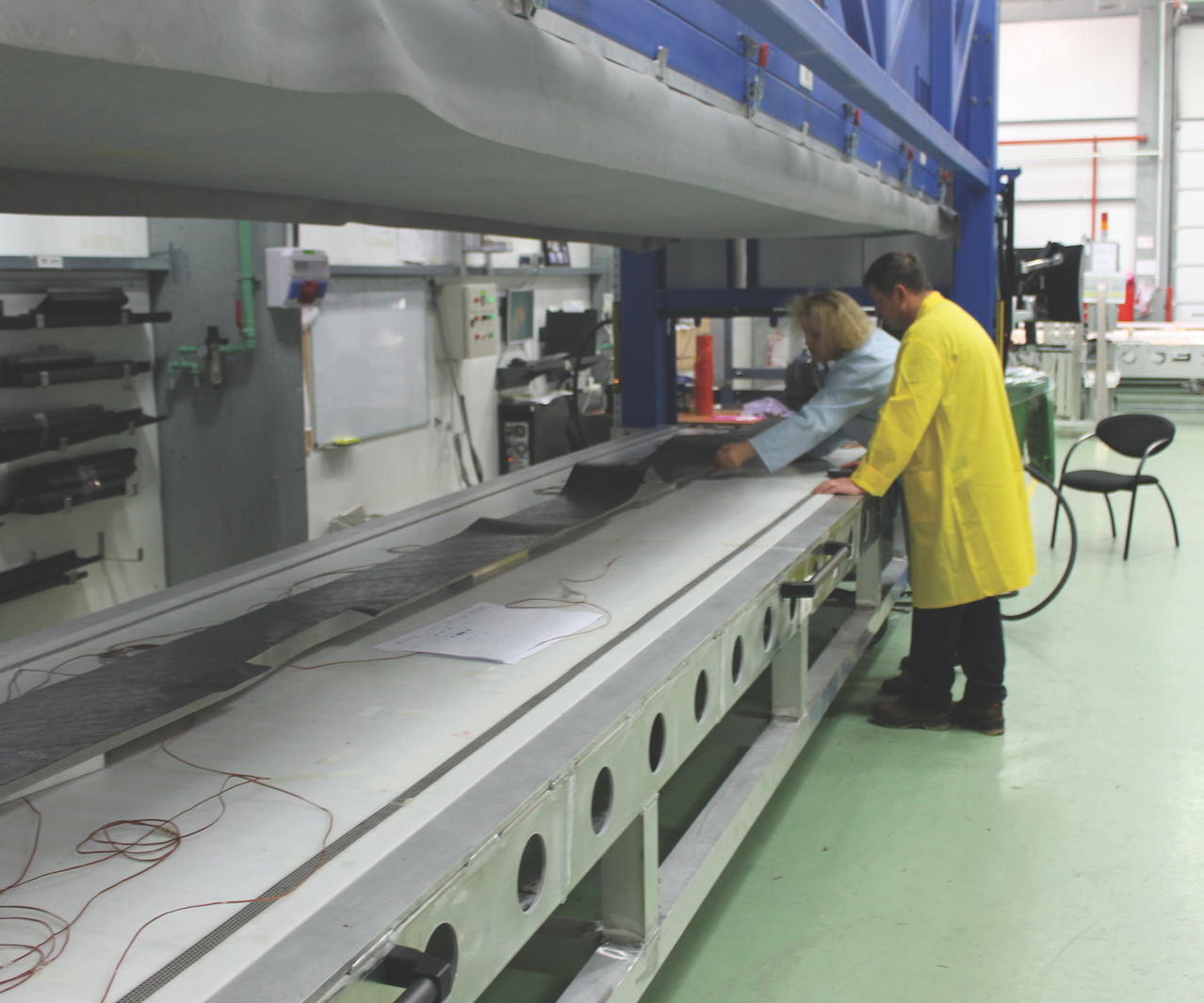
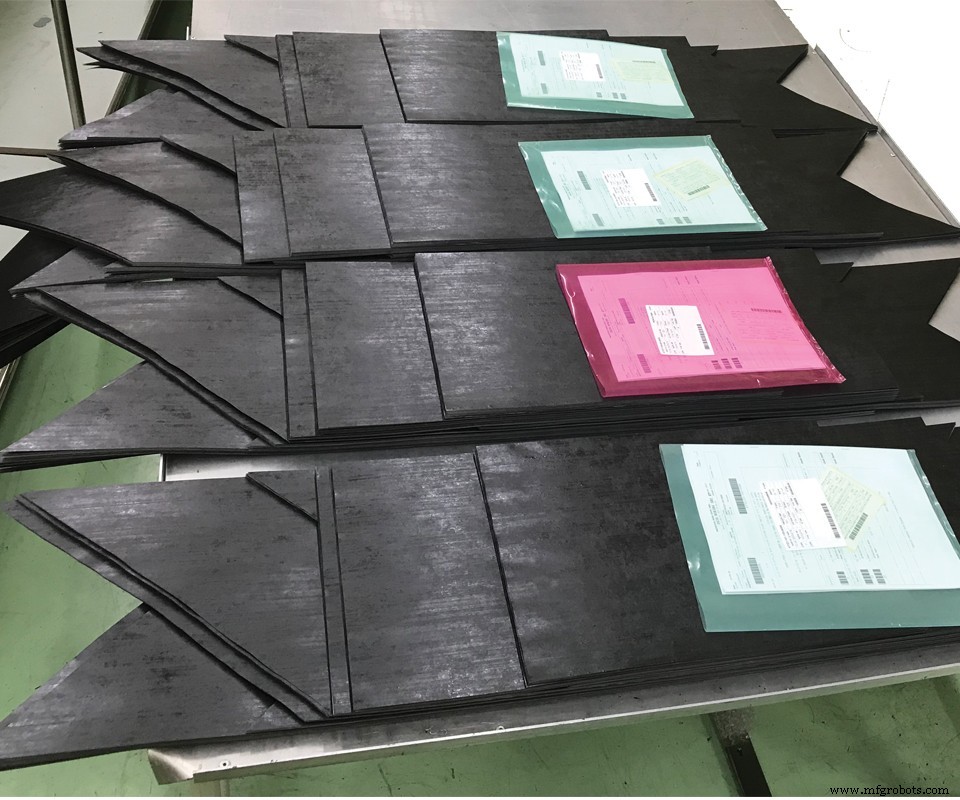
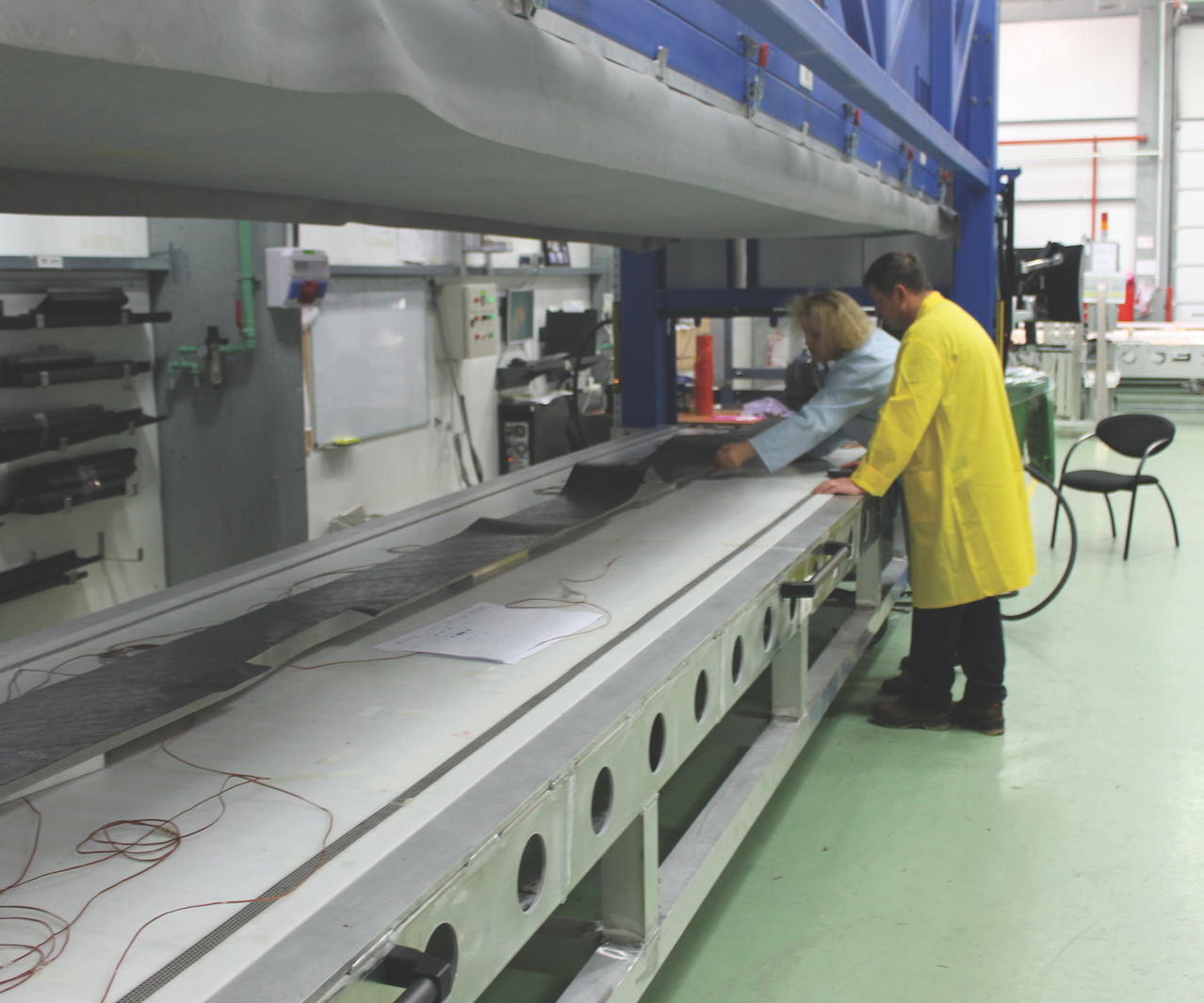
Met koolstofvezel versterkte kunststof (CFRP) vloerbalkdelen worden op mannelijke metalen doornen gelegd. Hulaty beschrijft het gestroomlijnde proces:"We leggen eerst de prepreg-stapels op en brengen ze vervolgens op de doorn aan. Dit bespaart een hoop tijd in plaats van stukje bij beetje op de tool toe te passen. De lay-ups worden vervolgens bedekt met een CFRP-caul van ons eigen ontwerp, wat helpt om 100% herhaalbaarheid in de onderdelen te garanderen."
Een hete lakenvorming machine zit langs de achterwand van de cleanroom, waardoor debulking van vele onderdelen per cyclus mogelijk is. "Ik weet niet hoe je dit soort prepreg-onderdelen met hoge snelheid kunt produceren zonder hot drape-vorming", zegt Hulaty met betrekking tot onderdelen zoals balken en rongen. En toch erkent hij dat deze stap niet het knelpunt is, en ook niet de autoclaaf. "Aan het einde, na uitharding, is het knelpunt om aan het eind te bewerken", stelt hij, en hij legt uit dat het voor lange vloerbalkdelen sneller is om een eenvoudige stapel op te leggen en deze na uitharding te bewerken. "De autoclaaf is niet het probleem, omdat we veel onderdelen kunnen stapelen om in één keer uit te harden", voegt hij eraan toe. "Dus we krijgen eigenlijk een goede productiesnelheid per uithardingscyclus."
2018, IAI, vliegtuigstructuren
Uit:"Israëls aerodefensie hoeksteen klaar voor grotere wereldwijde reikwijdte"
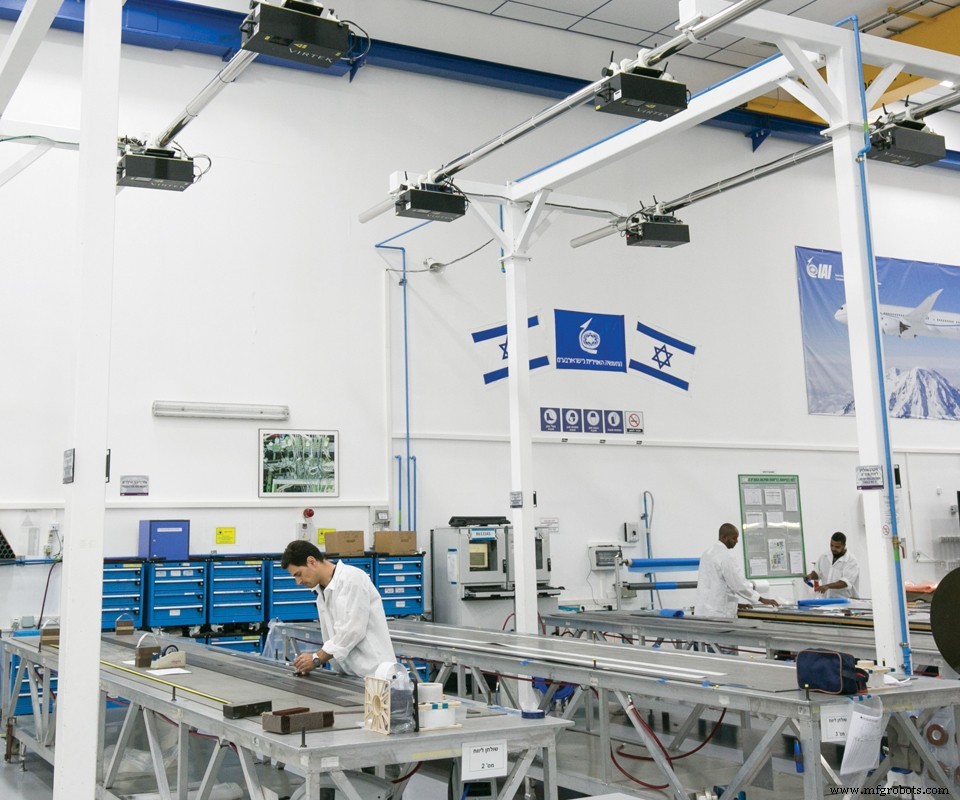
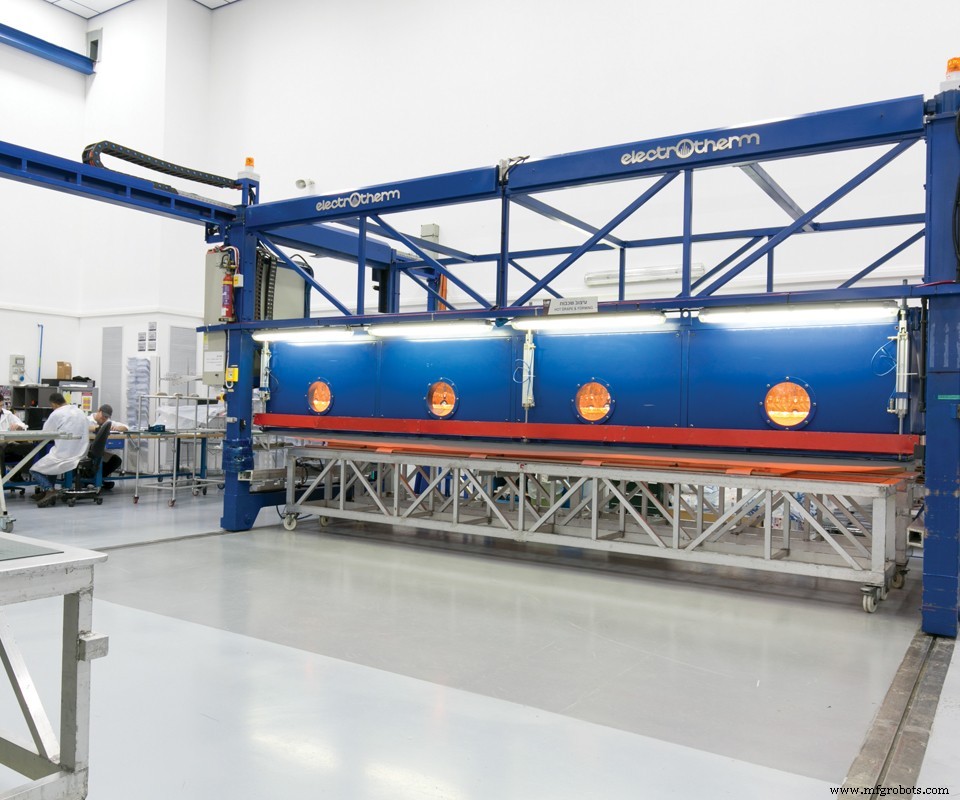
IAI gebruikt een hot drape-vormmachine om dikke prepreg-layups massaal te debulken, waardoor conventionele tussenliggende debulking-stappen overbodig zijn. Photo Credit:Israel Aerospace Industries
De composietactiviteiten van IAI omvatten de fabricage van onderdelen en assemblages voor zakenvliegtuigen en commerciële vliegtuigen, onbemande luchtvaartuigen (UAV's) en militaire vliegtuigen. Geproduceerde onderdelen omvatten verticale en horizontale stabilisatoren, roeren, vleugelconstructies, motorgondels, vloerbalken, deuromlijstingen, structurele schotten, ribben en verstijvers, stuurvlakken, stroomlijnkappen en radomes. Tot de productiemogelijkheden behoren prepreg hand layup en automatische tape layup (ATL), hot drape vorming , autoclaaf en uitharding buiten de autoclaaf (OOA), inclusief vloeibare vormprocessen, zoals harsinfusie en harsoverdrachtvormen (RTM), plus complexe hechting en assemblage. Het bedrijf ontwerpt en bouwt ook zijn eigen gereedschap, is in het bezit van alle belangrijke kwaliteitscertificeringen voor lucht- en ruimtevaart en composieten en biedt kwaliteitsborging via uitgebreide niet-destructieve tests en inspecties.
- De productiecapaciteit van IAI is aanzienlijk, met 10 autoclaven, waarvan er zeven behoren tot de Aero-assemblies Div. en variëren in grootte van 4,5 m lang en 2 m diameter, tot de grootste met 14 m lang en 4,7 m diameter.
- Prepreg-layups worden voorafgaand aan uitharding ontbulderd met behulp van een heet laken machine (6,9 bij 2,7 bij 3,1 m) van Electrotherm Industry (Migdal HaEmek, Israël).
2020, Strata, A350-900 binnenboordflappen
Uit:"Strata levert 100 sets binnenboordkleppen voor A350-900"
Ontworpen om het totale hefvermogen van de vleugel van een vliegtuig te vergroten, is een IBF [inboard flap] gemonteerd op de achterrand van de vleugel om het vleugeloppervlak tijdens het opstijgen en landen te vergroten en de stabiliteit tijdens de vlucht te verbeteren. Strata zegt van plan te zijn het IBF-productieproces volledig te automatiseren, met behulp van hot drapeforming (HDF) en computergestuurde robot-geautomatiseerde tape-layup-machines (ATL), die begin dit jaar de eerste deelkwalificatie (FPQ) en FAI-ontwerp- en kwaliteitsverificaties behaalden.
Als onderdeel van het proces zegt het bedrijf dat de HDF-machine koolstofvezelcomponenten voorvormt voor vliegtuigonderdelen, waardoor een snellere productie van hoogwaardige composietonderdelen mogelijk wordt, en het infraroodstralingsverwarmingssysteem verzacht koolstofvezel snel en gelijkmatig om nauwkeurige onderdelen te leveren die naar verluidt vrij zijn van spanningsrimpels. Verder leggen de twee ATL-machines van Strata unidirectionele prepreg-materialen op een flatbed voordat ze worden overgebracht naar een mal voor verdere verwerking. Volgens Strata maakt het werkbereik van 2,5 meter bij 10 meter geautomatiseerde verwerking van grote composietlay-ups mogelijk, waardoor er geen aparte ultrasone snijmachine nodig is en de verwerkingstijden worden verkort.
2020, Techni-Modul, vleugelrib en stringer
Uit:"Compressie-RTM voor de productie van toekomstige aerostructuren"
“Voor ons ging OPTICOMS ook over automatisering”, zegt Chevallet. Techni-Modul Engineering leverde niet alleen een C-RTM injectiesysteem voor het OPTICOMS project, maar ook een pick-and-place robot en een hot drapeforming (HDF) machine, allemaal geïntegreerd in een volledig geautomatiseerde productiecel. … "We hebben het klassieke handmatige stapelen van lagen geautomatiseerd met behulp van robotpick and place", zegt Chevallet. "De robot pakt de lagen op van een geautomatiseerde snijplotter en brengt deze over naar het verwarmde voorvormgereedschap die op een verdichtingstafel staat [Stappen 1 en 6].” Een peel-ply (blauwe film in stap 6), ontluchter (wit materiaal in stap 6) en scharnierend herbruikbaar vacuümmembraan (lichtblauw links in stap 2 en 6) worden aangebracht, gevolgd door vacuüm en warmte om de lucht voor te vormen en te verwijderen uit de textielstapel (hete draperen, HDF ) terwijl de dunne thermoplastische sluiers smelten om een verdichte voorvorm te creëren.
OPTICOMS vleugelrib en stringer
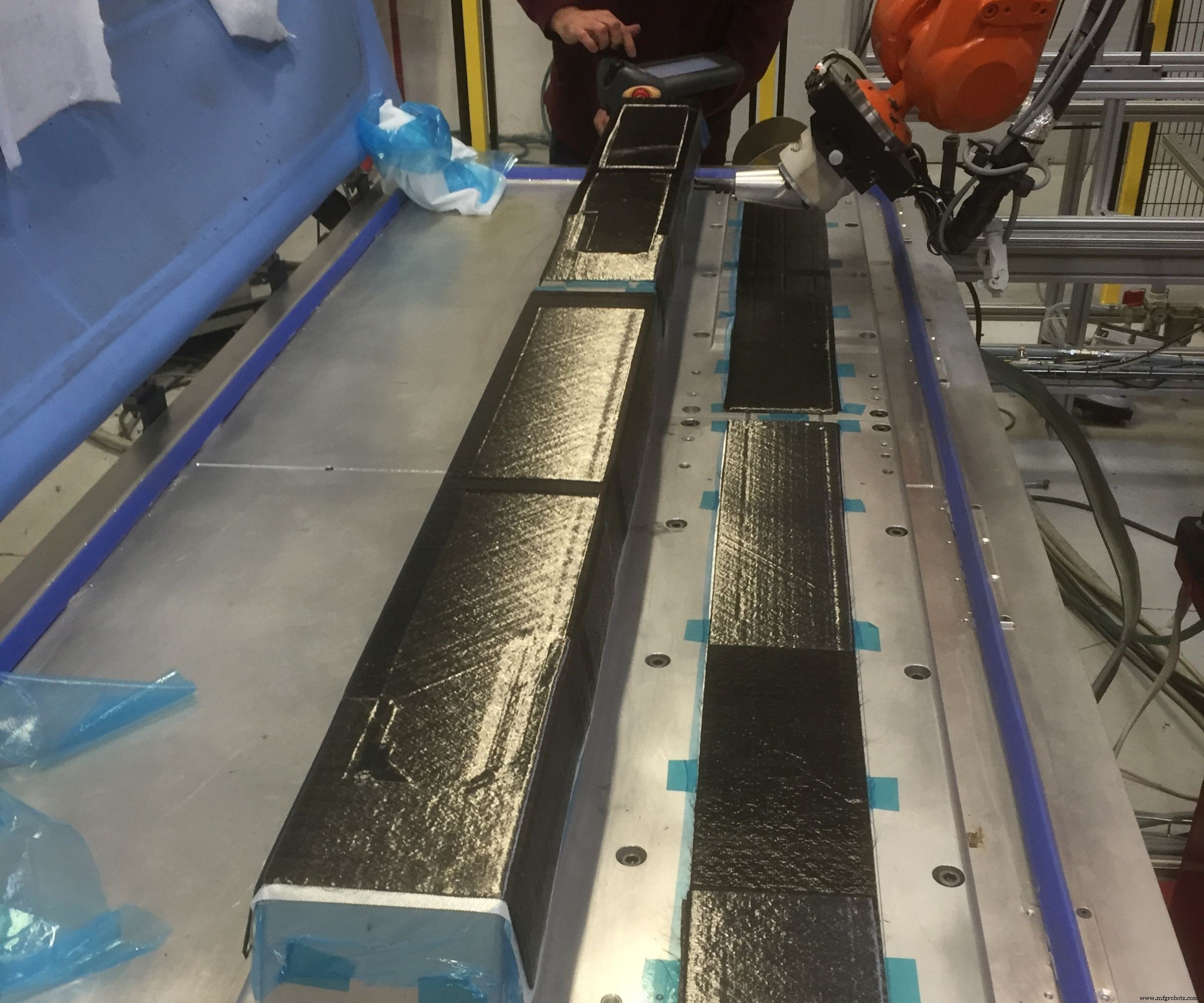
Stap 2. De voorvormgereedschappen bevinden zich op een verdichtingstafel met een scharnierend herbruikbaar vacuümmembraan (blauw, links) dat wordt gebruikt om elke 5-8 lagen een verwarmde debulk te voltooien tijdens het leggen. Fotocredits voor alle afbeeldingen:Tecni-Modul Engineering.
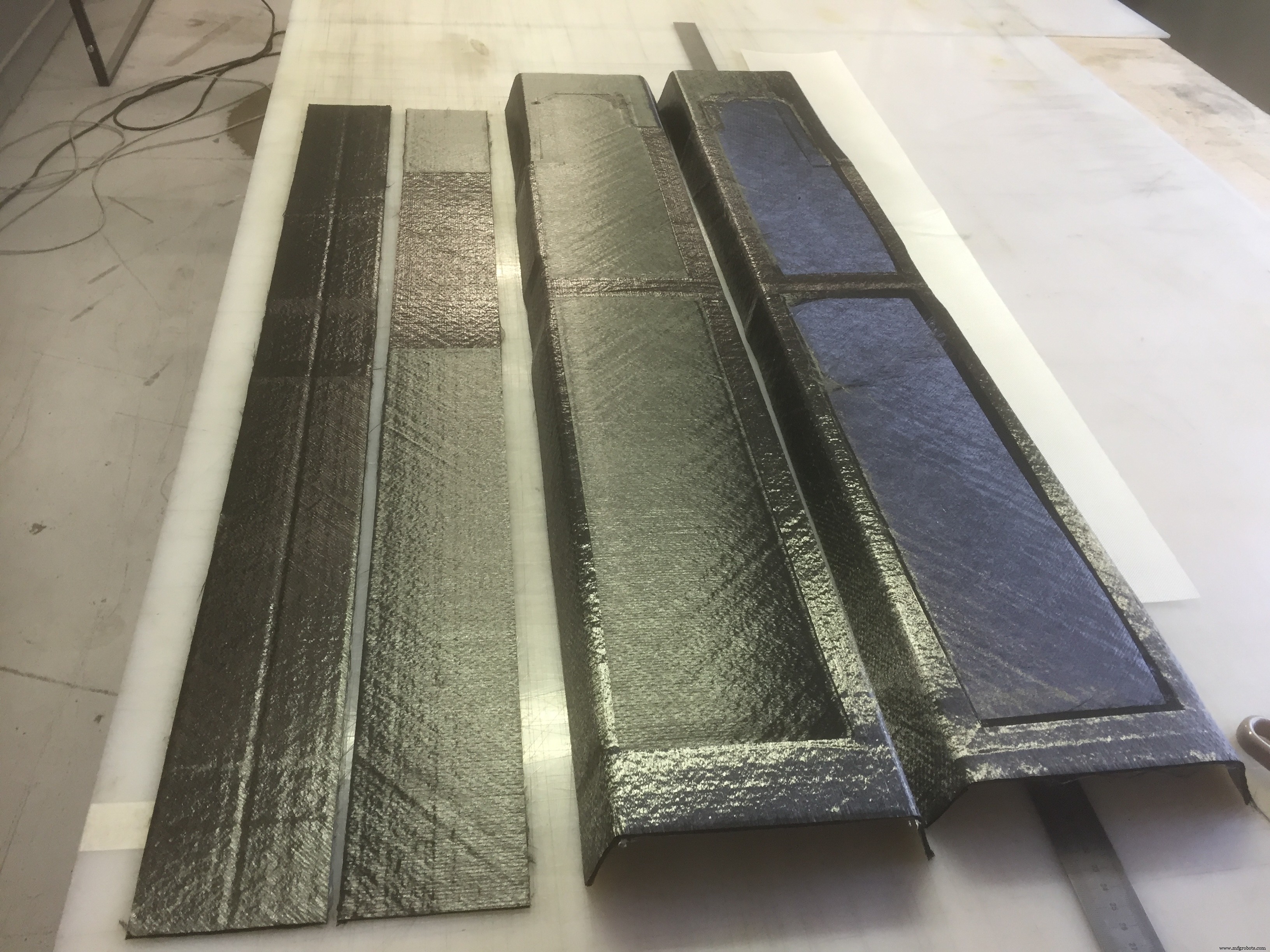
Stap 3. Elke voorvormcyclus van de stringer produceert één voorvorm met C-balk (twee omvatten de I-balk) en één voorvorm met platte flens. Twee sets die nodig zijn voor elke I-beam stringer worden hier getoond.
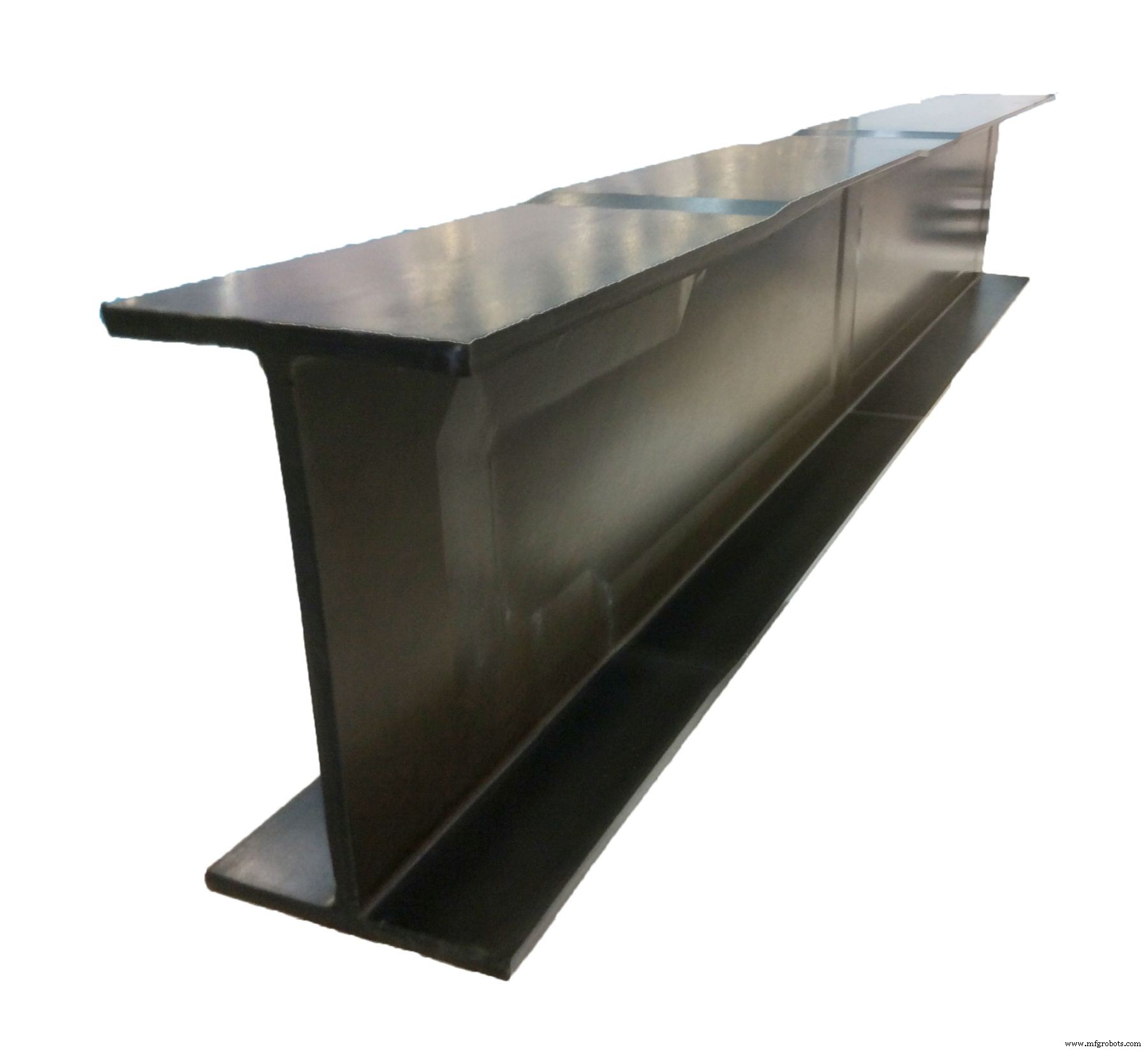
Stap 5. I-beam stringer gemaakt met HDF preforms en RTM voor Clean Sky 2 OPTICOMS project.
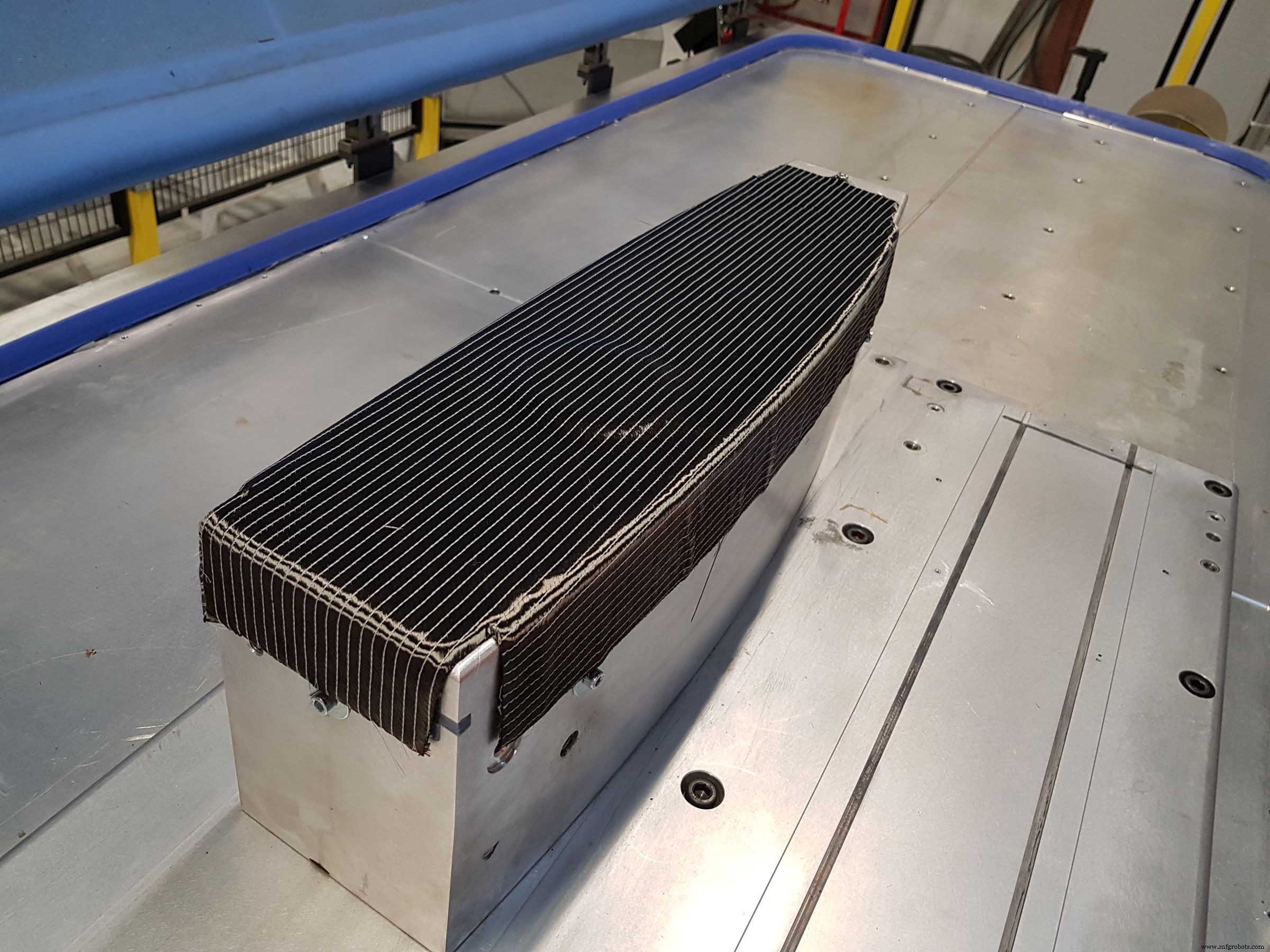
Stap 6. Een robot plaatst snijlagen op het verwarmde voorvormgereedschap. Elke 5-8 lagen wordt een verwarmde debulk voltooid om de preform te verdichten.
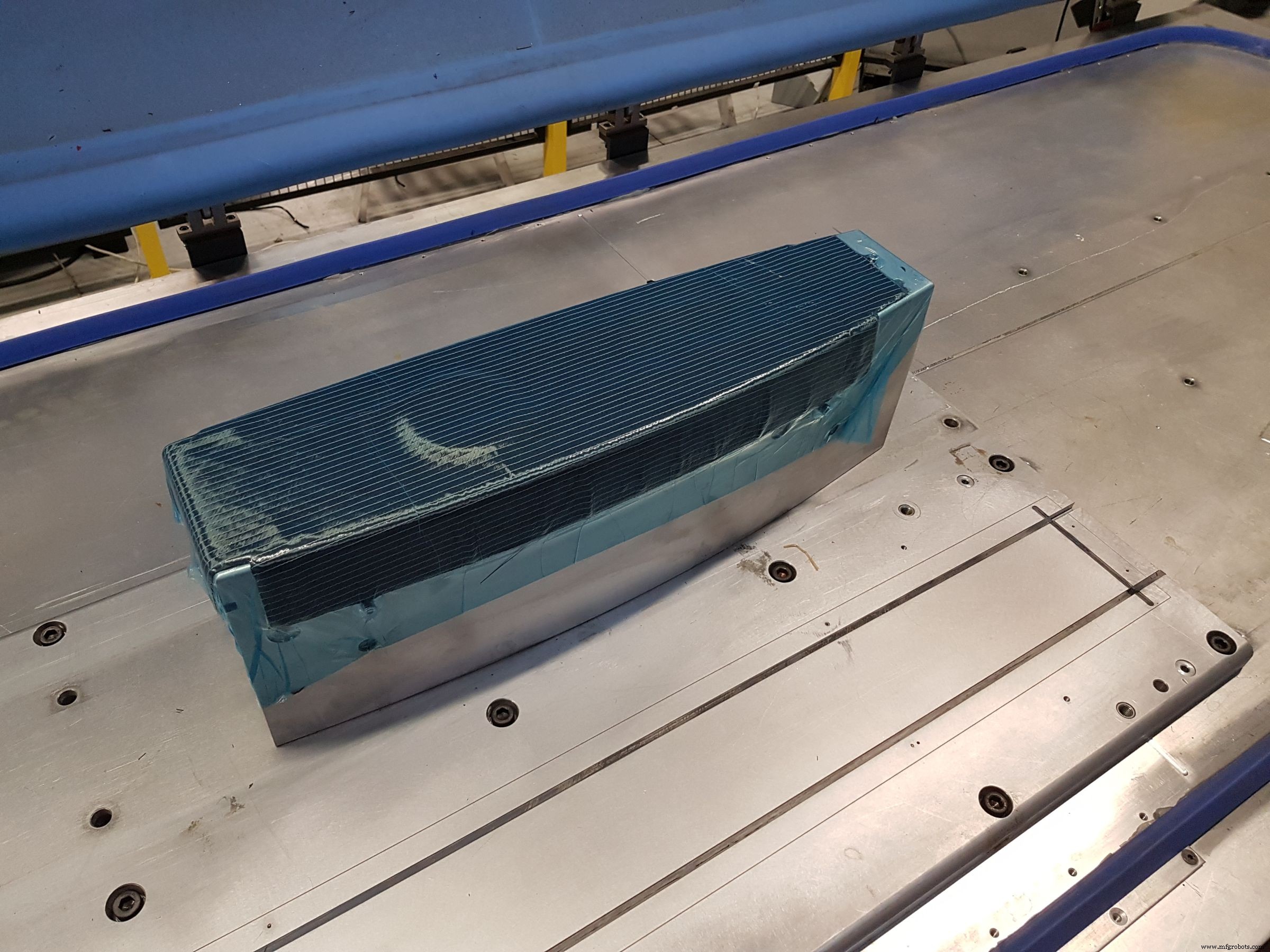
Voor het debulken wordt een blauwe lossingsfilm aangebracht.
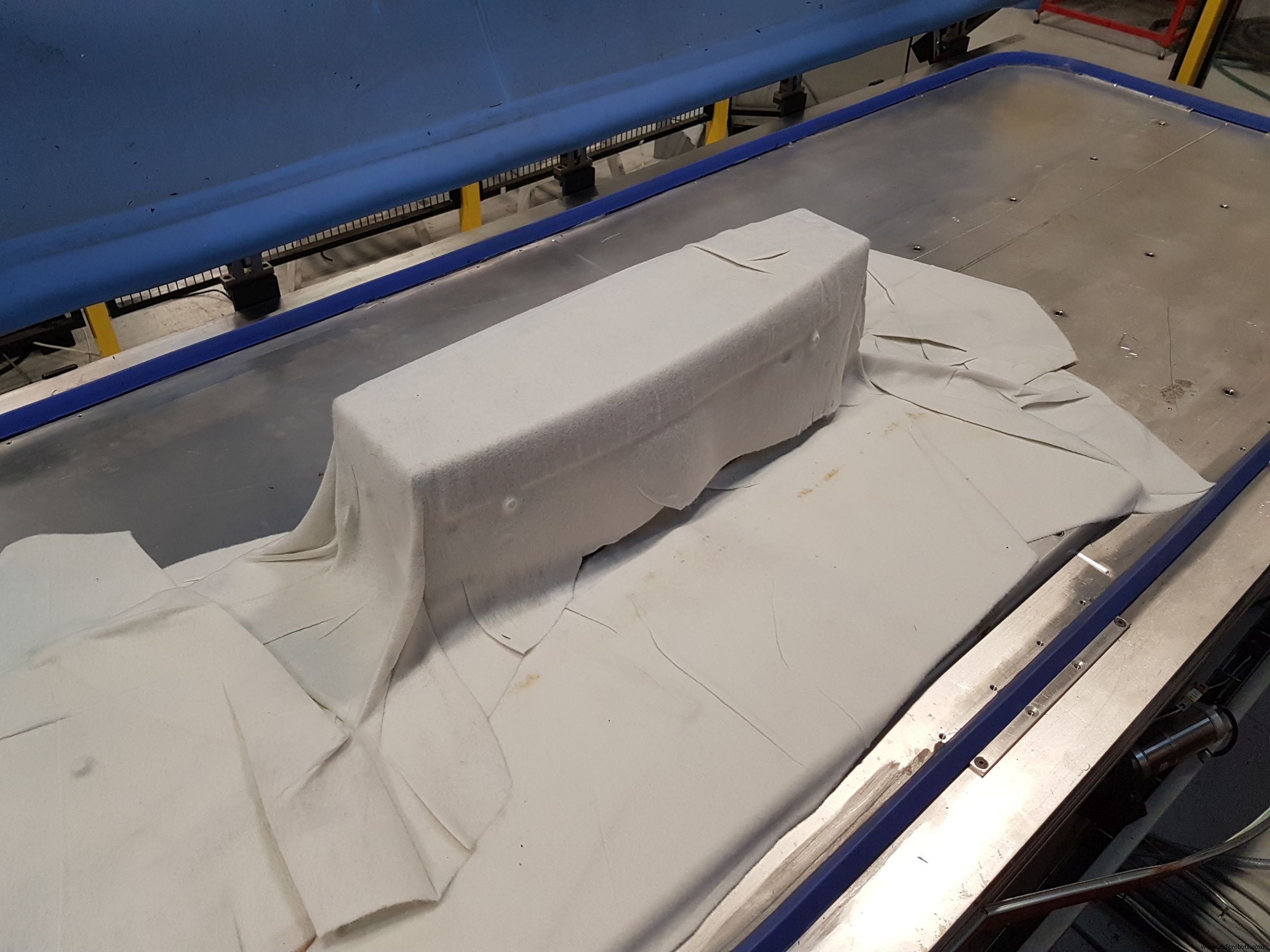
Ademhaling wordt gebruikt om lucht over de voorvorm af te zuigen.
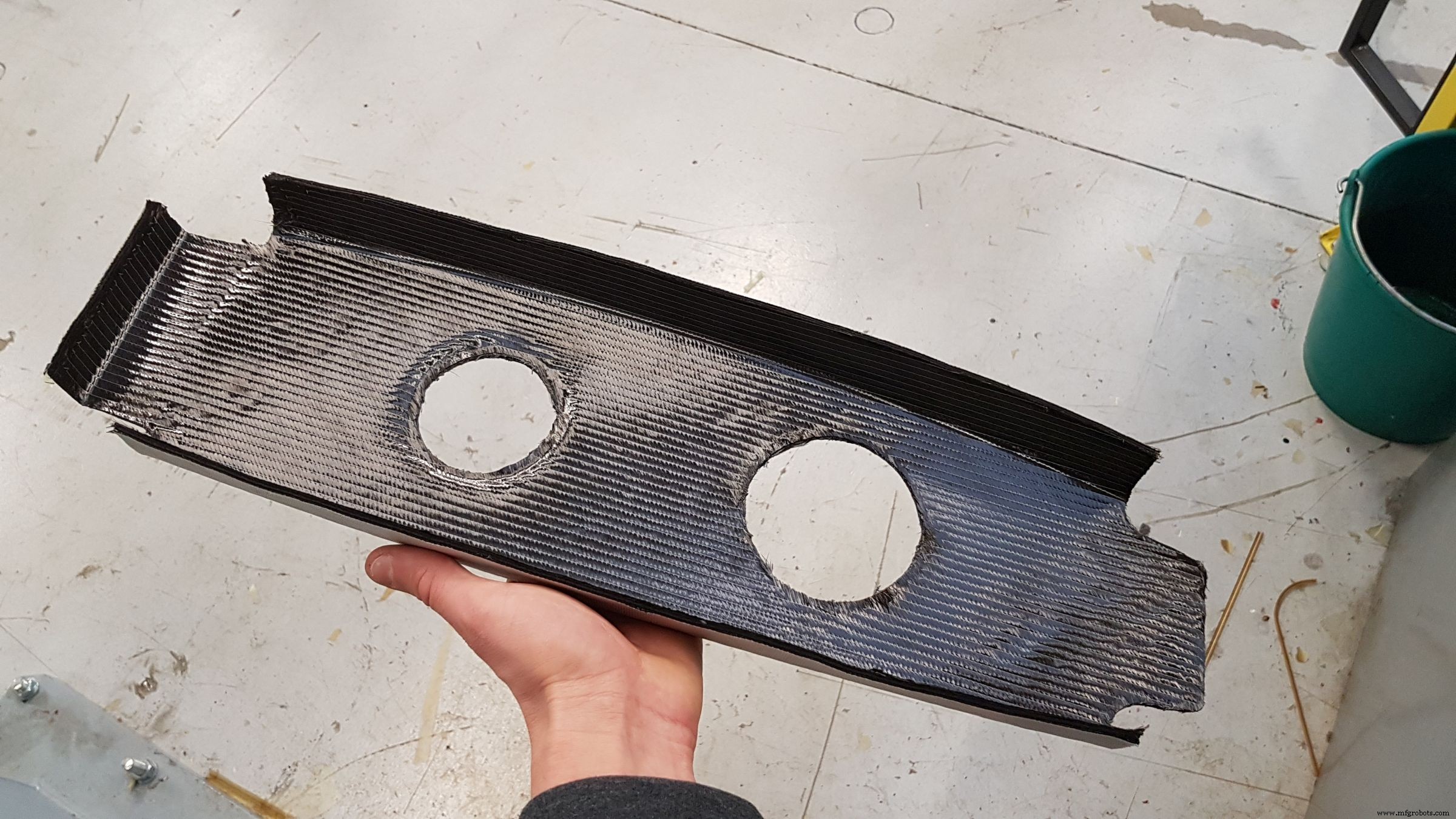
Na de laatste debulk wordt de preform op het gereedschap afgekoeld en worden de uitsnijdingen bijgesneden.
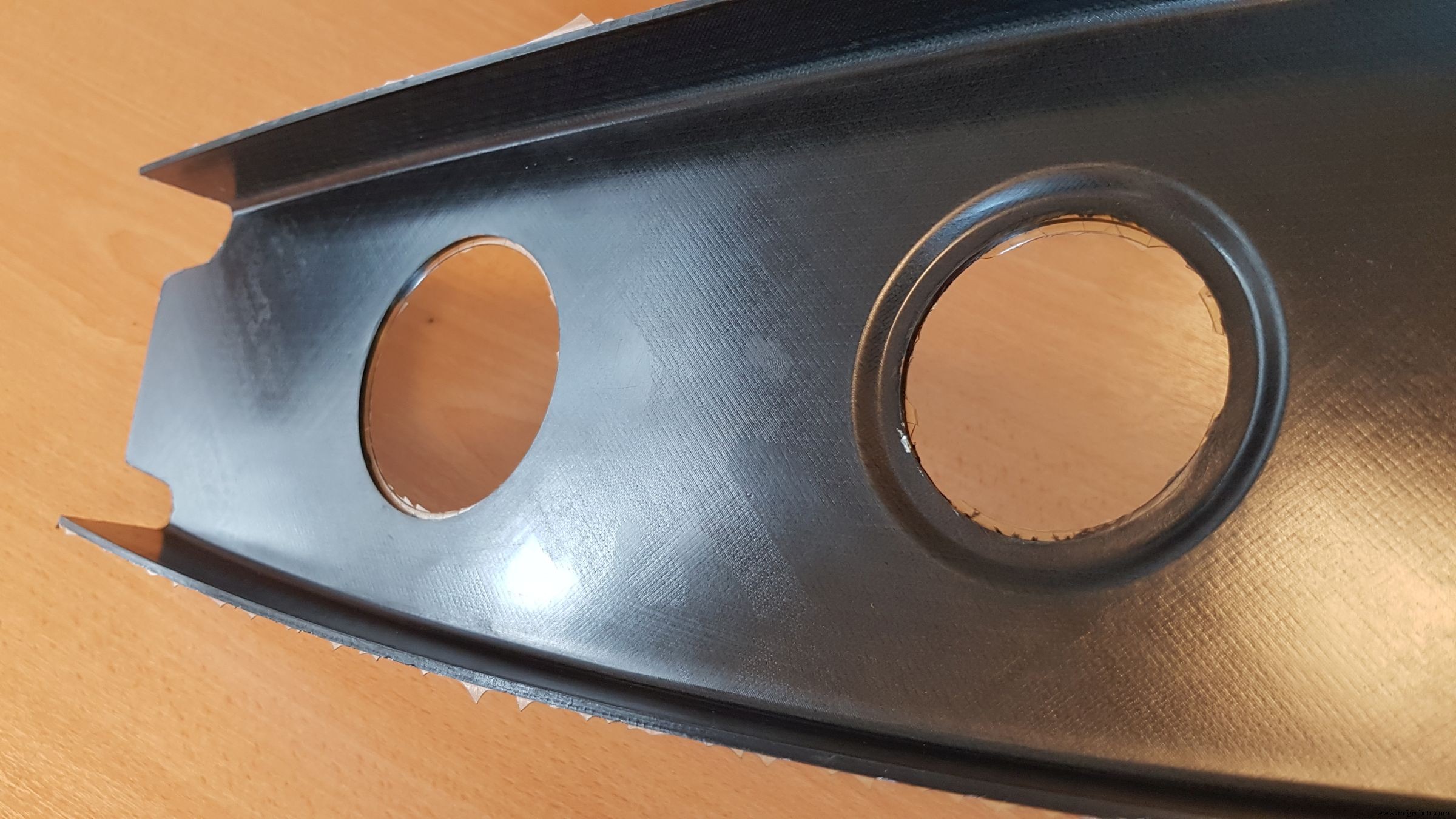
Stap 10. De ribpreform wordt gegoten met RTM en epoxyhars.
Vorige volgende"Hoeveel lagen u in één keer kunt verdichten, hangt af van het materiaal en de vorm van het onderdeel", legt Chevallet uit. “Voor onderdelen met een lage kromming, zoals een wingskin, zou je eventueel elke 50 lagen kunnen verdichten. De OPTICOMS-rib heeft echter hoeken van 90 graden en de test I-beam stringer heeft T-vormen, dus je moet oppassen dat je tijdens het voorvormen geen plooien in de lagen vormt.” Hij voegt eraan toe dat dergelijke complexe vormen wellicht elke 5-8 lagen verdichting vereisen, maar nog steeds deel kunnen uitmaken van een geïndustrialiseerd proces met grote volumes:stapellagen, 2-minuten HDF-verdichting , heropenen en opnieuw stapelen, gevolgd door herhaalde verdichtingscycli met een laatste afkoeling van de preform op het gereedschap voordat deze naar de RTM-mal wordt overgebracht.
vezel