Soorten vormprocessen - Volledig overzicht [met afbeeldingen]
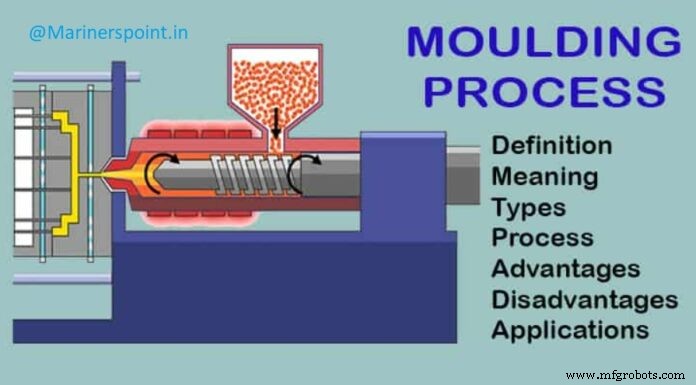
In dit artikel zullen we het hebben over het vormproces, soorten vormprocessen die zijn geclassificeerd op basis van verschillende termen zoals droog zandvormen, groen zandvormen, bankvormen enz.
Vormproces algemeen gebruikt kunnen worden ingedeeld volgens verschillende vormen. Ze kunnen grofweg worden geclassificeerd als:
- Handgieten , en
- Machine gieten .
In stuk- en kleine productie-gieterijpraktijken worden zandvormen met de hand gemaakt; vormmachines worden gebruikt in grote partijen en massaproductie.
Soorten vormprocessen
Vormprocessen worden vaak geclassificeerd volgens:
(A) Het soort materiaal waarvan de mal is gemaakt of
(1) Groene zandvormen,
(2) Droge zandvormen,
(3) Huidgedroogde mallen,
(4) Leemvormen.
(B) De methoden die zijn gebruikt bij het maken van de mal.
(1) Bankafgietsel,
(2) Vloerafwerking,
(3) Putafgietsel,
(4) Sweep molding, en
(5) Plaatvormen.
Vormproces op basis van gebruikt zand
1. Groen zand lijstwerk
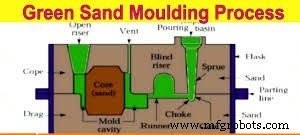
Groen zandafgietsel is een veelzijdige, snelle en goedkope methode om mallen te maken voor hoogwaardige ferro- en non-ferro gietstukken. Groen zand bestaat uit kwartszand, water, bentoniet en andere additieven, zoals steenkoolstof voor ijzertoepassingen.
Groenzandvormen worden gemaakt met natuurlijk vormzand of met mengsels van kwartszand, hechtklei en water. Deze materialen worden grondig gemengd in verhoudingen die de gewenste eigenschappen geven voor de klasse van het werk dat wordt gedaan.
2. Droge zandvorm
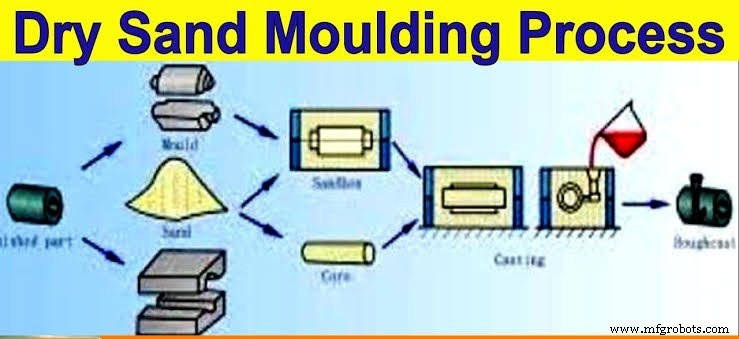
Het vormproces dat betrokken is bij het maken van droog zand mallen zijn vergelijkbaar met die welke worden gebruikt bij het vormen van groen zand, behalve dat een ander zandmengsel wordt gebruikt en dat alle delen van de mal in een oven worden gedroogd voordat ze weer in elkaar worden gezet voor het gieten.
De groene zandvorm is afhankelijk van het vocht en het natuurlijke kleibindmiddel in het zand om zijn vorm te behouden. Maar het zand dat voor droge zandvormen wordt gebruikt, is afhankelijk van toegevoegd bindmateriaal zoals meel, hars, melasse of klei. De materialen worden grondig gemengd en getemperd met een dun kleiwater. De hoeveelheid bindmiddel wordt bepaald door de grootte van de casting gemaakt.
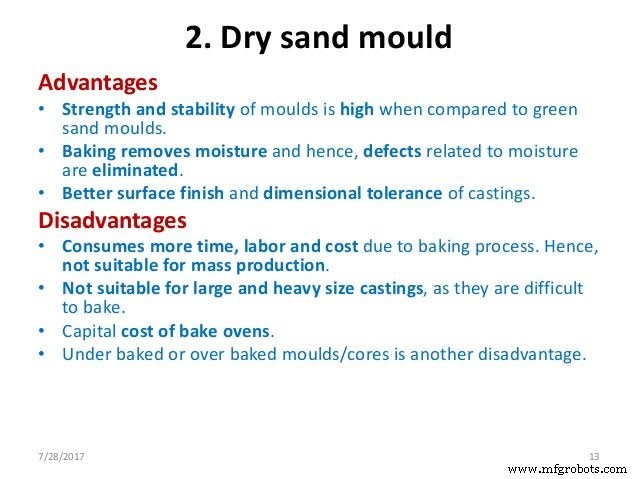
3. Huidgedroogd Vormen
Huidgedroogd Vormingsproces is een proces waarbij het vocht van de oppervlaktelaag van het aangestampte zand tot een diepte van ongeveer 25 mm of meer wordt gedroogd met behulp van gastoortsen of verwarmingstoestellen. Het heeft tot op zekere hoogte de voordelen van zowel groen zand als droog zandvormen. Omdat de droogtijd korter is dan bij droog zand, is de methode goedkoper. Het drogen van de huid is bijzonder geschikt voor zeer grote mallen of voor werken die nauwkeurige details vereisen.
4. Leemvorm
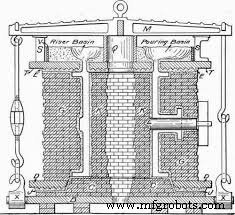
Leem is klei en zand vermengd met water om een dun plastic mengsel te vormen waaruit mallen worden gemaakt. Leemzand bevat ook vuurklei of ganisters. De leem moet voldoende hechtend zijn zodat deze zich aan de verticale vlakken kan hechten. Voor leemvormen zijn altijd speciale voorzieningen nodig om voor voldoende ventilatie te zorgen. Het doel is om de poriën in de verder compacte, hechte massa op kunstmatige wijze te openen. Dus verschillende soorten organisch materiaal zoals gehakseld stro, en vooral paardenmest , wordt vermengd met het zand. Een typisch leemzandmengsel wordt hieronder gegeven:
Dit wordt als gips aangebracht op de ruwe structuur van de mal, meestal gemaakt van metselwerk en de exacte vorm wordt gegeven door een roterende beweging rond een centrale as, zoals weergegeven in de afbeelding. Gietijzeren platen en staven worden gebruikt om het metselwerk te versterken dat het vormmateriaal vasthoudt. Leemvormen kunnen ook worden gemaakt door gebruik te maken van een skeletpatroon van hout. De oppervlakken van leem worden zwart gemaakt en gedroogd voordat ze worden geassembleerd.
Leemvormen worden voornamelijk gebruikt bij het maken van grote gietstukken waarvoor het te duur zou zijn om volledige patronen en gewone kolvenuitrusting te gebruiken. Objecten zoals grote cilinders, ketels met ronde bodem, chemicaliënpannen, grote tandwielen en andere machineonderdelen worden in leemvormen geproduceerd.
Soorten vormprocessen op basis van de gebruikte methoden
1. Bank- en vloerafwerking
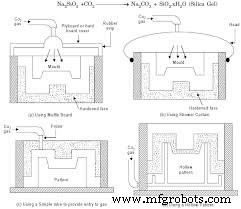
Bankprofiel is voornamelijk van toepassing op mallen die klein genoeg zijn om op een werkbank te worden gemaakt van een hoogte die geschikt is voor de maler.
Zeer zware gietstukken of gietstukken met een aanzienlijke diepte of oppervlakte kunnen in het zand van de gieterijvloer worden gegoten op vrijwel dezelfde manier als gieten met groen zand of droog zand. In dergelijke gevallen fungeert de vloer zelf als de sleep, en deze kan worden afgedekt met een kap of de mal kan worden opengegoten.
2. Putgieten
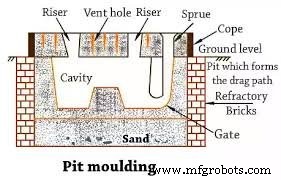
Pitgieten Proces :Mallen voor grote klussen worden over het algemeen voorbereid in een gegraven put in de gieterijvloer, wat het gemakkelijker maakt om het patroon op te tillen en de mal gemakkelijk te gieten. Aangezien een put die als een belemmering fungeert niet kan worden omgerold, kan het zand onder het patroon worden geramd door ingebed. Het patroon kan op de juiste plaats worden opgehangen als het zand eronder wordt geramd. In andere gevallen, als het onderoppervlak van een patroon vlak is, kan het patroon op een vlak, vlak oppervlak worden geplaatst dat ervoor is geramd.
Op de bodem van de put wordt een bed van cokes gelegd, bedekt met stro en vervolgens een laag zand, die wordt geramd en geëgaliseerd. Het cokesbed is verbonden met de atmosfeer door verticale ontluchtingspijpen in de hoeken van de put om een uitlaat te bieden voor de gegenereerde gassen. Als de vloer licht vochtig is, zijn de binnenoppervlakken van de put bekleed met teerpapier, bakstenen of houten planken. Over het algemeen is één doos nodig om het vormproces te voltooien. Lopers, gietbakken, feeders, worden erin gesneden.
3. Sweep Moulding
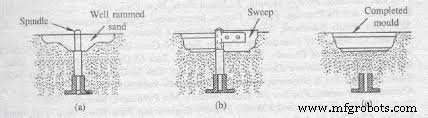
Veeglijsten worden gebruikt voor het vormen van onderdelen waarvan de vorm die van een omwentelingsoppervlak is. In het voortraject worden een basis 1 en spindel 2 goed in de gieterijvloer geplaatst. Het zand wordt opgevuld en geramd totdat de uitgraving ongeveer de vorm en grootte van het benodigde gietstuk heeft. Dit wordt geïllustreerd in figuur a.
Vervolgens wordt een sweephouder 5 in het spindelland geplaatst, de sweep 6 wordt met bouten en moeren bevestigd. Het oppervlak van de mal wordt geproduceerd door het profiel van de zwaai terwijl deze rond de spil wordt gedraaid, zoals weergegeven in figuur (b). Na het vegen wordt de spil verwijderd en wordt de mal in het midden gepatcht. De poort wordt vervolgens gesneden en de mal is klaar om te gieten. Dit wordt getoond in Fig. (c).
4. Plaatgieten
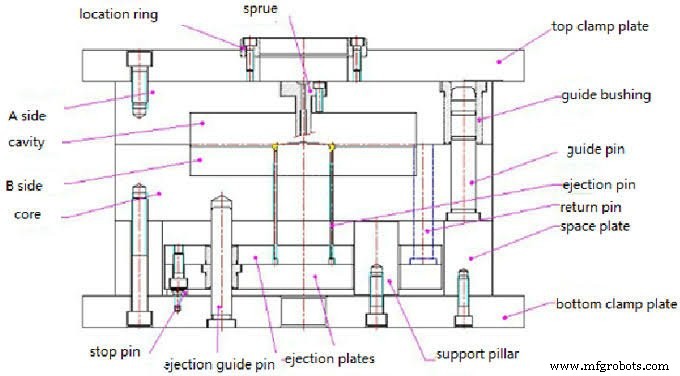
Plaatvormen Proces :Bij dit gemonteerde scheidingsproces wordt het patroon in tweeën verdeeld over de scheiding en in tweeën op platen met evenwijdige zijden van dezelfde vorm als de afbeelding. Het gebruik van platen geeft de volgende voordelen :
- De patronen kunnen gemakkelijk worden verwerkt en snel.
- De taak van het maken van de verbinding tussen de twee delen van de mal wordt verlicht, omdat de plaat zijn eigen verbinding biedt wanneer de kolf wordt geramd.
- Het patroon kan snel getekend worden , aangezien de plaat de zijkant van de doos overlapt en de pinnen die de doos op zijn plaats houden, fungeren als geleiders tijdens het tekenen.
Enkele speciale vormprocessen
In de afgelopen jaren zijn speciale vormprocessen zijn ontwikkeld om tijd en kosten te besparen, matrijzen en kernen van betere kwaliteit te produceren en de productiviteit te verhogen met minder inspanning en vaardigheid. Over het algemeen vereisen deze processen niet in alle gevallen het drogen of bakken van vormen of kernen, en vindt snelle uitharding plaats vanwege chemische reacties daarin. Het gebruik van de volgende speciale vormprocessen is de afgelopen jaren aanzienlijk toegenomen.
1. Kooldioxideafgietsel
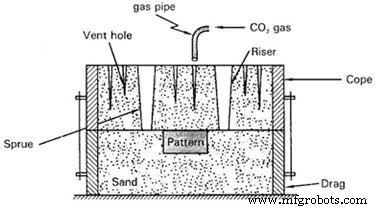
Kooldioxide-afgietsel Proces: Het proces is in feite een uithardingsproces voor mallen en kernen. Het principe van werken van het CO2-proces is gebaseerd op het feit dat als CO2-gas is doorgegeven een zandmix met natriumsilicaat (waterglas), wordt het zand onmiddellijk extreem sterk gebonden omdat het natriumsilicaat een stijve gel wordt. Deze gel is verantwoordelijk voor het geven van de nodige stevigheid aan de mal.
2. Ferro-silicium gieten
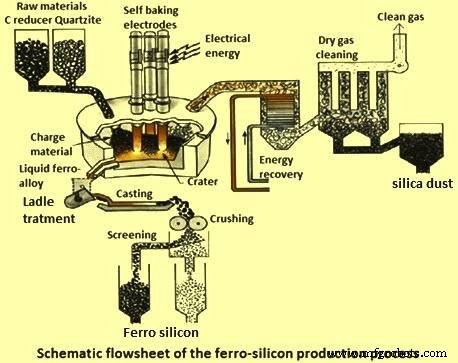
Ferro-silicium gieten :Dit vormproces is gebaseerd op het principe dat als natriumsilicaat en ferrosiliciumpoeder zijn gemengd in de verhouding van 2,25 :1 op gewichtsbasis vindt schuimvorming plaats en stijgt de temperatuur door exotherme reactie daartussen. Bij kamertemperatuur verloopt deze reactie langzaam, maar zodra de temperatuur wordt verhoogd, versnelt de reactie. Ten slotte vormt het kwartszand een harde sponsachtige massa. Het bakken van de vorm of kern is niet nodig zoals bij het CO2-proces.
Normaal gesproken, voor ijzerhoudend gieten schoon, droog zand van 65 mesh , terwijl voor non-ferro gieten , zand van 100 mesh is geschikt. De mallen moeten worden gecoat met een geschikte wasbeurt voordat ze worden gesloten.
3. Dicalciumsilicaatafgietsel
Dicalciumsilicaatafgietsel :Dit vormproces is gebaseerd op het principe dat als ongeveer 2 tot 3 procent dicalciumsilicaat , waarvan bekend is dat het een zeer effectieve verharder is, en 5 procent natriumsilicaat zijn gemengd met zand samen met geschikte schuimchemicaliën neemt de vloeibaarheid van de zandmassa toe. Als gevolg hiervan kan het zandmengsel gemakkelijk in de mal vloeien en is het niet nodig om te stampen zoals vereist bij een conventioneel vormproces. Ten slotte vormt het zand een harde massa met voldoende inklapbaarheid
Het belangrijkste voordeel van dit vormproces is de grote besparing op arbeidsinput en vormapparatuur omdat er geen droging of backing nodig is. Anderzijds worden er hoogwaardige, foutloze gietstukken geproduceerd. Dit vindt brede toepassing in middelzware en zware gietstukken, zowel in grijs gietijzer als in stalen gietstukken.
4. Cement-zand gieten
Cement-zand gieten :Portlandcement kan gebruikt worden als bindmiddel om zandkorrels aan elkaar te binden. Het blijkt dat een goede combinatie van sterkte, permeabiliteit en vloeibaarheid wordt bereikt door cement samen met natriumsilicaat te gebruiken. Vloeibare cementslurry kan ook worden geproduceerd met schuimende chemicaliën in het zandmengsel. Het aanstampen van zand wordt zo aanzienlijk verminderd. Een goede hechting kan echter in zand worden ontwikkeld door toevoeging van ongeveer 2 procent 2 cement, 4-5 procent natriumsilicaat en 1 procent pek of melasse.
Deze mallen produceren een glad en nauwkeurig oppervlak, maar het grootste nadeel van cementgebonden zandvormen is dat ze moeilijk uit de kolf te kloppen zijn.
5. Schelpvormen
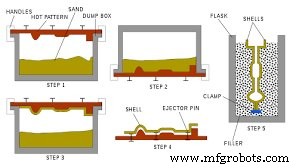
Schelpvorm :Naar de naam van de uitvinder, is het vormstuk ook bekend als Croning-proces of C-proces . Dit is een variant van de kunsthars gebonden zandtechniek voor het gieten van staal, ijzer of non-ferro legeringen.
De mal wordt gevormd uit een mengsel van fijn zand (100-150 mesh) en een thermohardend harsbindmiddel dat tegen een verwarmd metalen patroon wordt geplaatst, bij voorkeur gemaakt van grijs gietijzer. Wanneer het mengsel op deze manier wordt verwarmd, hardt de hars uit, waardoor de zandkorrels aan elkaar gaan kleven en een stevige schaal vormen die precies overeenkomt met de afmetingen en vorm van het patroon en de helft van een mal vormt.
Nadat de schaal is uitgehard en van het patroon is gestript, worden alle benodigde kernen geplaatst, worden de twee helften van de mal aan elkaar vastgemaakt, in een kolf geplaatst en wordt back-upmateriaal toegevoegd; dan is de mal klaar om te gieten.
6. Hot en Cold Box Molding
Het hotbox-proces , speciaal aangepast voor het maken van kernen, gebruikt in principe dezelfde materialen als die gebruikt worden bij het vormen van schelpen, maar hier wordt de hars aangebracht voor het coaten van de zandkorrels. Het hars-zandmengsel wordt vervolgens over het metalen patroon of de kerndoos geblazen, verwarmd tot ongeveer 200° tot 300°C en toegestaan om een vaste massa te vormen in plaats van schilvorming toe te staan.
Er zijn nu speciale hot-box-machines beschikbaar waarbij het zandmengsel over het verwarmde patroon wordt geblazen, het geblazen zand wordt uitgehard en de mal of kern vervolgens van de patroon- of kerndoos wordt verwijderd.
Er wordt een grotere nauwkeurigheid van afmetingen en hogere productiesnelheden bereikt dan in het geval van schaalgieten. Dit is een vorm- en kernproductieproces dat hoofdzakelijk bedoeld is voor de gemechaniseerde productie van kleine gietstukken die in grote hoeveelheden nodig zijn.
Het cold-box-proces bestaat uit het mengen van fijn droog zand ofwel polyisocyanaathars bindmiddel en alkyd fenolhars , het mengsel in een afgesloten kerndoos blazen en een luchtkatalysator-triethylaminedamp door de kerndoos injecteren. De hydroxylgroep van de vloeibare fenolhars combineert met de isocyanaatgroep om een stijve urethaanhars te vormen. De twee bindmiddelcomponenten worden gewoonlijk gebruikt in een verhouding van 1:1 waarbij 1 tot 2 gewichtsprocent van het harsmengsel aan het zand wordt toegevoegd. a
Het proces heeft het voordeel dat er geen verwarming van het patroon nodig is, en de uitharding vindt plaats in slechts 20-30 seconden. Het is dus een eenvoudig kernproductieproces met hoge productie en uitermate geschikt voor kleine gietstukken die in grote hoeveelheden nodig zijn.
7. Invest Molding
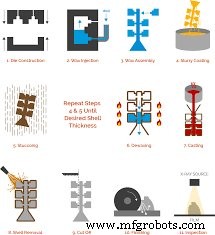
Invest Molding :Dit proces van het maken van gietstukken wordt vaak aangeduid als "verloren wasproces ” en “precisie gietproces ”. Gieten kan in dit proces met zeer nauwe toleranties worden gemaakt en vereist geen latere bewerking.
Het bestaat voornamelijk uit twee fasen die in de figuur zijn weergegeven. Eerst wordt een masterpatroon gemaakt van hout of metaal waar een mal omheen wordt gevormd. Het bestaat niet uit vormzand maar uit gelatine of een legering met een laag smeltpunt die over het moederpatroon wordt gegoten. Deze master mal bestaat uit de gebruikelijke twee secties en kan worden geopend. Het wordt gebruikt voor het maken van het "verloren patroon ".
8. Gips gieten
Gips gieten :Bij deze methode wordt de mal voorbereid in gips of gips van Parijs. In de praktijk wordt het gips van parijs gemengd met talk, asbest, vezels, silicameel en een gecontroleerde hoeveelheid water om een slurry te vormen. Deze gipsbrij wordt over het in een kolf opgesloten metalen patroon gegoten.
De mal wordt getrild en de suspensie laat men uitharden. Het patroon wordt verwijderd na ongeveer 30 minuten wanneer de instelling voltooid is en de mal wordt gedroogd en ondersteund door het langzaam te verwarmen tot ongeveer 200°C in een transportoven. Inserts en kernen worden geplaatst, omgaan en slepen op elkaar afgestemd door geleidepennen. Gesmolten metaal wordt vervolgens in de mal gegoten. Ten slotte wordt het gietstuk in de mal afgekoeld, uitgeschud en wordt de mal vernietigd. Gietstukken worden vervolgens ontdaan van poorten, sprues en flits.
9. Keramisch Afgietsel
In keramisch gieten proces wordt een dikke slurry, bestaande uit speciaal ontwikkelde keramische aggregaten en een vloeibaar chemisch bindmiddel (siliciumester op alcoholbasis) gepureerd over het herbruikbare gespleten en gepoorte metalen patroon dat gewoonlijk op een luciferplaat wordt gemonteerd. De slurry vult vanzelf alle holtes en uitsparingen en er is geen stampen of trillen van de mal nodig. Het patroon wordt teruggetrokken nadat het in ongeveer 3 tot 5 minuten is uitgehard. De keramische massa wordt vervolgens uit de kolf verwijderd, behandeld met een verharder om chemische stabilisatie te bevorderen en in een oven tot ongeveer 980°C verwarmd om het vloeibare bindmiddel te verwijderen. De mal is dan klaar om gesmolten metaal te gieten.
10. Zuiggieten
Zuiggieten Proces: Bij deze methode wordt een vacuüm gecreëerd door lucht aan de matrijsruimte te onttrekken. Vervolgens wordt vormzand aangezogen en wordt de spouw opgevuld. Het zand kan daarna in het patroon worden geramd. De processen worden gebruikt voor het gieten van ijzer, staal en aluminium.
We hebben geprobeerd alle belangrijke punten met betrekking tot het vormproces en zijn typen en classificaties te behandelen. Ik hoop dat je genoten hebt van dit artikel. Geef uw feedback in de onderstaande opmerking.
Industriële technologie
- MTBF:een compleet overzicht
- 5 verschillende soorten datacenters [met voorbeelden]
- Vormzand:soorten en bestanddelen | Gieten | Metallurgie
- Eigenschappen van vormzand | Materialen | Gieten | Metallurgie
- Wat is vormzand? - Soorten en eigenschappen
- Soorten zand gebruikt in het vormproces
- Zuiger – Volledig overzicht
- Soorten meters - Volledig overzicht [met afbeeldingen]
- Freesmachinedefinitie, proces en typen
- Betekenis en typen productieproces
- Soorten zandgietapparatuur