De verbonden bediening
Het internet en cloud-based computing veranderen de manier waarop fabrikanten CNC-bewerkingsmachines gebruiken. Is jouw winkel er klaar voor?
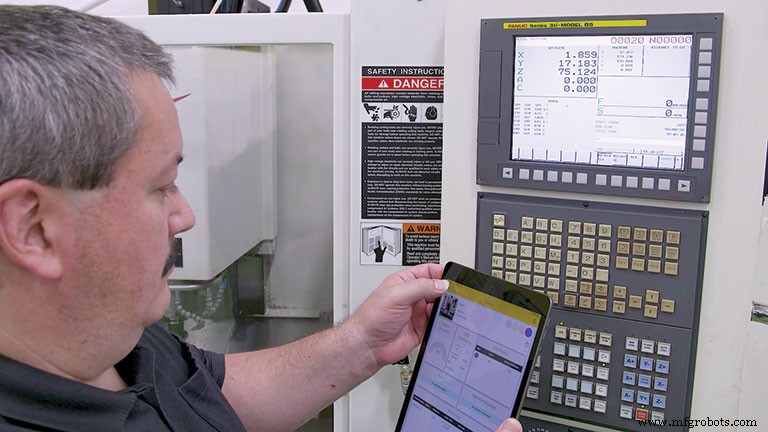
Ethernet-poorten verschenen meer dan 20 jaar geleden voor het eerst op CNC-draaibanken en bewerkingscentra. De MTConnect-communicatiestandaard voor bewerkingsmachines maakte zijn officiële Amerikaanse debuut op de IMTS in Chicago in 2010. Fabrikanten begonnen kort daarna te praten over cloud computing en het Industrial Internet of Things (IIoT), termen die mainstream zouden worden toen de Duitse econoom Klaus Schwab in 2015 een paper publiceerde waarin stond dat de wereld een vierde industriële revolutie was ingegaan.
Welkom in 2021. Het zou nu duidelijk moeten zijn voor eigenaren van machinewerkplaatsen, CNC-programmeurs en productie-ingenieurs dat de verspanende industrie de afgelopen twee decennia aanzienlijk is veranderd. CNC-bewerkingsmachines zijn veel slimmer dan ze ooit waren en kunnen aanzienlijke hoeveelheden gegevens genereren over alles wat er achter het glas gebeurt. Productiesoftware is ook slimmer geworden en biedt interoperabiliteit en cloudgebaseerde mogelijkheden waar alleen rond de eeuwwisseling van werd gedroomd.
Of al deze technische tovenarij een goede zaak is of niet, staat ter discussie. Sommigen zullen misschien beweren dat het leven op de werkvloer al uitdagend genoeg is - wie heeft Big Data en slimme machines nodig als er nauwelijks genoeg uren in de dag zijn om onderdelen de deur uit te krijgen? Anderen zien Industrie 4.0 en alles wat het met zich meebrengt als het duidelijke pad voorwaarts voor fabrikanten, en iedereen die het niet omarmt, zal binnenkort failliet gaan.
FOCAS verkrijgen
De waarheid ligt ergens tussenin. Paul Webster, directeur van F.A. Engineering bij FANUC America Corp., met hoofdkantoor in Rochester Hills, Michigan, merkte op dat CNC-bewerkingsmachines al sinds Y2K netwerk- en internetgereed zijn. Winkels die ervoor kiezen om deze mogelijkheid te negeren, sjokken nog steeds prima door, bedankt, en zullen dat nog jaren blijven doen. En toch zullen maar weinigen beweren dat de connectiviteit van bewerkingsmachines en de grotere zichtbaarheid van de bewerkingsprocessen die daardoor mogelijk worden gemaakt, nooit een slechte zaak is, en het verschil kan maken tussen een winstgevende klus en een klus die u net zo snel zou vergeten.
"We hebben onze FOCAS API (application programming interface) begin jaren 90 geïntroduceerd, evenals glasvezel- en vervolgens Ethernet-poorten, dus het aansluiten van een CNC is al geruime tijd eenvoudig", zei hij. "Het moeilijkste is altijd geweest om erachter te komen welke gegevens je nodig hebt en wat je ermee gaat doen als je ze eenmaal hebt."
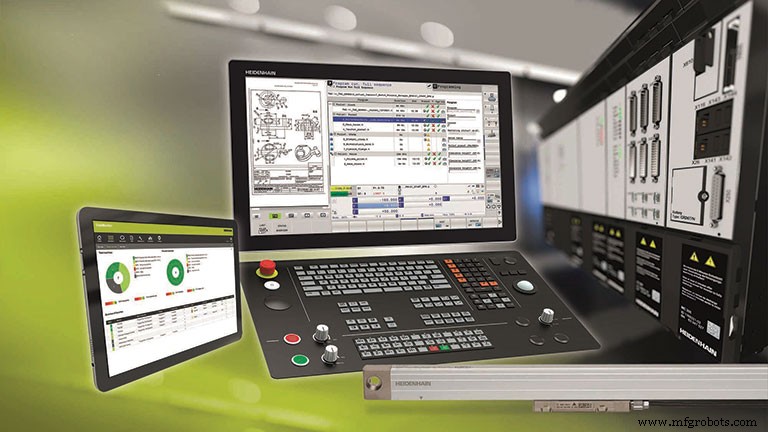
Deze gegevens omvatten alarmgeschiedenissen, voedingssnelheid en spiloverride-instellingen, servomotor- en spiltemperaturen, stroomverbruik, macrovariabelen en nog veel meer, die allemaal continu en automatisch uit de bewerkingsmachine kunnen worden gehaald. Voeg daarbij verschillende door de operator geleverde inputs - taaknummer, productiestatus, verbruik van snijgereedschap en zelfs informatie over de kwaliteit van onderdelen - en het verkrijgen van een compleet beeld van de activiteiten op de werkvloer wordt niet moeilijker dan een blik op het dashboard van de monitoringsoftware die deze gegevens verzamelt .
In het geval van FANUC is dit MT-LINKi, een merkonafhankelijk analyseplatform dat in staat is om meer dan 1.000 CNC-bewerkingsmachines tegelijk te bewaken, evenals FASData, een productiebewakingsprogramma. Andere besturingsbouwers bieden vergelijkbare oplossingen, net als veel machinebouwers, leveranciers van snijgereedschappen en externe softwareontwikkelaars. Ze bieden allemaal de middelen om, wat weliswaar een berg gegevens is, te verzamelen en deze op een voor mensen begrijpelijke manier te presenteren, zodat ze kunnen reageren op trends en potentiële problemen lang voordat ze een negatieve invloed kunnen hebben op de productieniveaus.
Het cloud-raadsel
De vraag wordt dan waar is de beste plaats om deze gegevens op te slaan en de software te huisvesten die wordt gebruikt om ze te analyseren? Moeten beide zich in de cloud op een externe hostingfaciliteit bevinden en worden beheerd door toegewijde hardware- en softwarespecialisten? Of is een "on-premise" installatie meer geschikt, waarbij gebruik wordt gemaakt van het interne IT-talent dat de winkel in huis heeft?
Webster en de anderen die voor dit artikel zijn geïnterviewd, waren het er grotendeels over eens dat, hoewel de eerste vaak de veiligere en kosteneffectievere benadering is, veel winkels schichtig blijven over onderdeelprogramma's en productiegegevens die hun fabriek verlaten. Hetzelfde geldt voor Gisbert Ledvon, directeur bedrijfsontwikkeling voor werktuigmachines bij het in Schaumburg, Illinois gevestigde Heidenhain Corp. Hij merkte op dat klanten de StateMonitor-software van het bedrijf kunnen installeren waar ze maar willen, maar installatie ter plaatse waar mogelijk promoot.
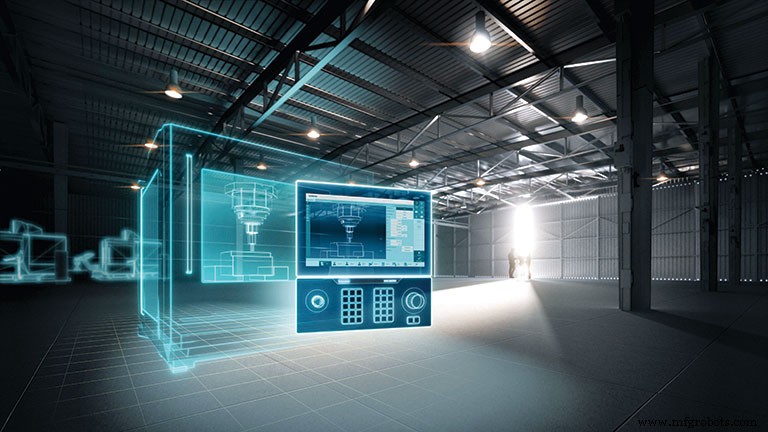
"Onze filosofie is dat klanten hun intellectuele eigendom moeten beschermen, en voor ons betekent dit dat ze hun werktuigmachines en softwaresystemen moeten aansluiten op een goed beveiligd bedrijfsnetwerk", zei hij. “Er zijn veel gevallen geweest waarin winkels zijn gehackt en gedwongen om losgeld te betalen. Toegegeven, deze aanvallen worden meestal uitgevoerd via e-mail en niet via de besturing van de machine, maar het is niettemin een punt van zorg. Daarom is de NTMA (National Tooling and Machining Association) begonnen met het aanbieden van seminars die fabrikanten laten zien hoe ze zich kunnen beschermen tegen dit soort cybercriminaliteit.”
Desondanks geeft Ledvon toe dat de cloud een technologietrend is die alleen maar aan kracht zal winnen. Wat nodig is om eventuele bijbehorende risico's te beperken, zijn goede IT-huishoudingspraktijken. Installeer een robuuste firewall tussen het winkelnetwerk en de buitenwereld. Vermijd directe CNC-naar-cloud-verbindingen door externe bestanden, softwareprogramma's en patches te downloaden naar een beveiligde interne server en deze vervolgens te controleren met antivirussoftware voordat ze worden gedistribueerd. Train alle computergebruikers hoe ze wachtwoorden kunnen beheren, kwaadaardige e-mails en websites kunnen herkennen en bedrijfsinformatie kunnen beschermen. De lijst gaat maar door.
"Aangezien de besturing het zenuwcentrum is van elke bewerkingsmachine, denk ik niet dat het gemak van toegang tot de cloud het risico van blootstelling aan internet waard is", zegt Ledvon. “Niets van dit alles weerhoudt fabrikanten er echter van om een Industrie 4.0-strategie te implementeren. Ze moeten in ieder geval hun werktuigmachines in een netwerk plaatsen en beginnen met het verzamelen van gegevens voor analyse. Hierdoor krijgen ze de informatie die ze nodig hebben om machines sneller in te stellen, cyclustijden te verkorten, de standtijd van het gereedschap te maximaliseren en alle andere voordelen te benutten die de huidige CNC-besturingen en softwaresystemen bieden.”
Native Talent
Een ander onderdeel van Industrie 4.0 is de digitale tweeling, die in dit geval verwijst naar een virtuele maar zeer nauwkeurige en uitgebreide weergave van een CNC-bewerkingsmachine. Volgens Vivek Furtado, hoofd digitaliseringsmachines voor Siemens Industry Inc., Elk Grove Village, Illinois, stroomlijnen digitale tweelingen het ontwerp en de inzet van CNC-machines, waardoor fabrikanten uiteindelijk efficiënter worden.
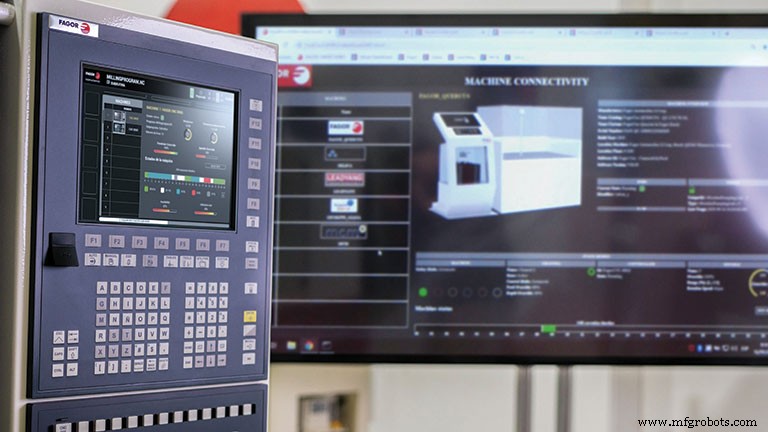
"Onze SINUMERIK One-controller staat bekend als een digital native, omdat hij van de grond af is gebouwd om de digital twin en andere ondersteunende technologieën te ondersteunen", zei hij. “Het geeft fabrikanten van CNC-bewerkingsmachines de mogelijkheid om een virtuele versie van een draaibank of bewerkingscentrum te creëren die alle kinematica en bedieningskenmerken bevat. Dit vermindert de engineeringtijd en ontwikkelingskosten aanzienlijk en zorgt ervoor dat het product voldoet aan de behoeften van de eindgebruikers.”
Digitale twin-compatibele controllers hebben andere doelen. Ze versnellen de opleiding van nieuwe medewerkers en verkleinen de kans dat een dure werktuigmachine crasht. Ze stellen schatters in staat om nauwkeuriger opdrachten te citeren, ingenieurs om geoptimaliseerde productieprocessen te ontwikkelen en CNC-programmeurs om de G-code en de selectie van snijgereedschappen te valideren voordat het werk naar de werkvloer wordt gestuurd. Eenmaal daar maken ze de bediening van de bewerkingsmachine gemakkelijker met verbeterde graphics en grotere bruikbaarheid.
Iedereen met een high-end CAM-systeem of PLM-software zou kunnen zeggen dat ze dit grotendeels kunnen bereiken zonder een geavanceerde CNC-besturing. En hoewel het onbetwistbaar is dat de mogelijkheden van deze en andere softwareplatforms de afgelopen jaren enorm zijn toegenomen, bieden bewerkingsmachines die deelnemen aan de digitale draad machinewerkplaatsen een belangrijk hulpmiddel, een hulpmiddel dat de gegevensuitwisseling verbetert en de cirkel rond interoperabiliteit sluit.
Aanpassen en overwinnen
Afgezien van digitale twinning, suggereerde Furtado dat CNC-controllers veel intelligenter en gebruiksvriendelijker worden, met functies en functies die elke smartphonegebruiker zal herkennen. "De meesten van ons herinneren zich dat we ooit onze telefoons gebruikten om mensen te bellen", zei hij. “Vandaag de dag laten ze je je gezondheid monitoren, informatie zoeken, producten bestellen, enzovoort. Nieuwere generaties controllers bieden vergelijkbare functionaliteit. Ze zijn in staat om informatie te verwerken en gegevens voor te bereiden op een manier die het mogelijk maakt deze effectiever te gebruiken door hun menselijke operators of door andere systemen.”
Deze intelligentie strekt zich ook uit tot het bewerkingsproces. Siemens, FANUC en externe leveranciers van oplossingen, zoals Caron Engineering, bieden adaptieve besturingsmogelijkheden die de spindel- en asbelastingen, machinetrillingen en soortgelijke factoren die van invloed zijn op de levensduur van het snijgereedschap en de kwaliteit van de onderdelen continu bewaken. Deze slimme systemen passen vervolgens de bewerkingsparameters in realtime aan, waardoor de materiaalverwijdering wordt geoptimaliseerd en potentiële problemen worden geëlimineerd.
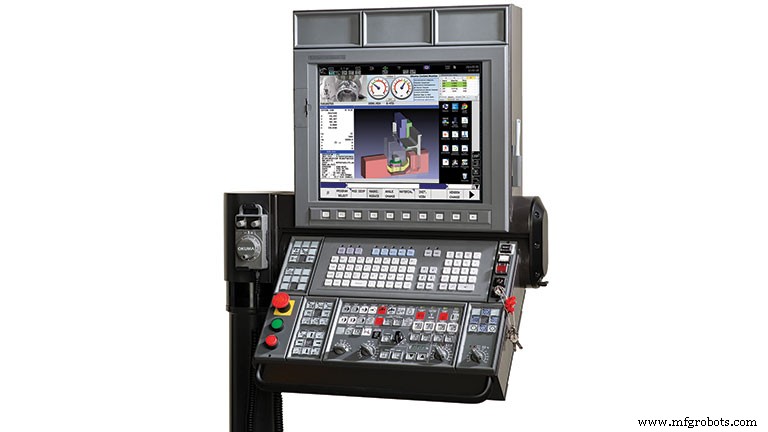
Fagor Automation Corp., Elk Grove Village, Illinois, is een andere leverancier van regelsystemen met het oog op de Industry 4.0-prijs. Harsh Bibra, algemeen directeur voor Noord-Amerika bij Fagor, legde uit dat de ARFS-regeling (Adaptive Real-time Feed and Speed) dit alles en meer doet, maar merkte op dat dit type sensorgebaseerde technologie ook kan worden gebruikt voor voorspellend onderhoud.
"We bieden ook ons i4.0 Connectivity Pack aan", zei hij. "Hierdoor kunnen gebruikers natuurlijk bewerkingsgegevens verzamelen, maar ook dingen doen zoals het verzenden van op de toestand gebaseerde waarschuwingen, het afstemmen van de bewerkingsmachine en het bijwerken van de firmware, het wijzigen van parameterinstellingen, enzovoort, allemaal vanaf een mobiel apparaat of een externe computer."
Het grootste knelpunt
Bibra ziet grote veranderingen in het verschiet. Afgezien van het toegenomen gebruik van IIoT-compatibele sensoren en versnellingsmeters in werktuigmachines, samen met intelligentere controllers, zullen de fabrieken zelf slimmer worden. Kunstmatige intelligentie (AI) die veel verder gaat dan de zojuist genoemde adaptieve mogelijkheden, zal de overhand krijgen en deuren openen naar de geautomatiseerde besluitvorming die nodig is voor wijdverbreide light-out-productie.
Dit alles zal letterlijk aan snelheid winnen gezien de ontwikkeling en daaropvolgende uitrol van 5G-cellulaire netwerken, suggereerde Bibra. Deze zullen niet alleen de internetbandbreedte vergroten en de latentie verminderen, maar mogelijk ook de eerder genoemde hackvrees wegnemen. "Controles van de toekomst zullen worden uitgerust met 5G en de gegevens die ze genereren, kunnen vervolgens draadloos worden verzonden met snelheden tot 10 gigabit per seconde (Gbit/s) naar zogenaamde edge-apparaten", zei hij. "We verwachten dat deze technologie binnen een paar jaar de manier waarop fabrikanten informatie van de werkvloer verzamelen fundamenteel zal veranderen."
Het nadeel van Industrie 4.0 is het gebrek aan geschoolde werknemers die geavanceerde technologie kunnen begrijpen en ermee kunnen werken. Bibra zei dat omscholing nodig zal zijn naarmate fabrikanten meer technisch onderlegd worden. Bezorgdheid over stammenkennis en het verlies van ervaring als gevolg van personeelsverloop en pensionering zou echter oude geschiedenis moeten worden.
De winkel bezoeken
Jim Kosmala, vice-president engineering en technologie bij Okuma America Corp., Charlotte, N.C., schrijft een groot deel van de huidige toegenomen connectiviteit toe aan het gebruik van pc-gebaseerde bedieningselementen. “Veel mensen vergeten dat Okuma niet alleen een machinebouwer is, maar ook zijn eigen servosystemen en besturingen maakt. Deze draaien op Microsoft Windows en gebruiken een Intel-chip, die beide gemakkelijke connectiviteit bieden.”
Pc-gebaseerde bedieningselementen maken het ook gemakkelijk om verschillende softwareprogramma's op de besturing te installeren - aan het begin van de COVID-pandemie konden Okuma-klanten bijvoorbeeld samenwerken met anderen door Microsoft Teams te gebruiken, schermen te delen of anderen indien nodig afstandsbediening te geven. "Dat is het hele idee achter onze App Store," zei Kosmala. “Gebruikers kunnen alles wat ze nodig hebben rechtstreeks downloaden en installeren op de OSP-besturing, waardoor er geen aparte pc nodig is. Het vertegenwoordigt geheel nieuwe mogelijkheden voor samenwerking en connectiviteit.”
Een van deze apps is Okuma's Connect Plan, waarmee gebruikers CNC-bewerkingsmachines kunnen monitoren en operationele gegevens kunnen verzamelen. Het werkt met vrijwel elk merk of vintage machinegereedschap, evenals met robots en andere vormen van automatisering. Volgens Kosmala gebruikt Connect Plan echter een AI-algoritme om naar de beschikbare informatie te kijken en trends te identificeren die een mens zou kunnen missen.
Denk aan de manager van een draaiafdeling, die na wekenlang kijken naar rapporten en dashboards voor gegevensverzameling merkt dat een bepaalde draaibank elke ochtend altijd 10 minuten te laat opstart dankzij de koffiegewoonte van de operator, of dat de spiltemperatuur op de molen die het dichtst bij de verzendafdeling zakt elke keer dat ze de laaddeur openen. Kosmala legde uit dat AI deze trends veel sneller oppikt dan een mens, waardoor supervisors de mogelijkheid hebben om potentiële probleemgebieden eerder aan te pakken. Bovendien wordt deze informatie opgeslagen in een database, dus als de leidinggevende het bedrijf verlaat, gaat er geen kennis verloren.
"Deming vertelde ons dat je zonder data gewoon iemand bent met een mening", zei Kosmala. “Het IIoT en Industry 4.0 gaan over het verzamelen van die data en het gebruiken ervan, om er uiteindelijk kennis van te maken. Dat is de eerste stap voor iedereen op deze reis. We hebben nu virtuele conferenties en de mogelijkheid om de machinestatus of productieniveaus overal te controleren, en toegang tot externe tools die automatisering vereenvoudigen. Als je dat kunt doen zonder de plant in te hoeven, des te beter. Het draait allemaal om het verhogen van de efficiëntie en de uptime van de machine, die beide gemakkelijker kunnen worden bereikt met moderne CNC-controllers.”
Automatisering Besturingssysteem
- Wat moet ik doen met de gegevens?!
- Het IoT democratiseren
- De toekomst van datacenters
- De basisprincipes van elektrische bedieningspanelen
- Machine learning in het veld
- Industriële integratie van het internet der dingen
- De cloud in IoT
- On the Edge of Glory:een nieuw tijdperk van internetmachines mogelijk maken
- Decoder maakt verbonden bewaking van de gegevens van elke machine mogelijk
- De vele voordelen van Smart IIoT Connected Factories
- Voordelen van een aangesloten machinewerkplaats