Wat zijn de soorten 3D-printers en wat kunnen ze doen?
3D-printen is een optimale productiemethode voor het produceren van prototypes en zelfs bepaalde onderdelen voor eindgebruik. Het is vaak de meest kostenefficiënte optie en levert enorme waarde op, afhankelijk van de specifieke technologie die u kiest.
Er zijn veel verschillende categorieën 3D-printers en daarbinnen veel verschillende soorten commerciële en industriële printers. Dit artikel behandelt de belangrijkste soorten 3D-printers en wat ze kunnen produceren.
Inzicht in het complexe landschap van 3D-printen zal u helpen wanneer het tijd is om de door u ontworpen onderdelen te vervaardigen en u veel tijd en geld besparen. Dus laten we beginnen.
Wat zijn de verschillende soorten 3D-printers?
In 2015 is de ISO/ASTM 52900 in het leven geroepen om te standaardiseren hoe 3D-printers en 3D-printtechnologie worden geclassificeerd. Er zijn in totaal zeven procescategorieën vastgesteld.
-
Vt-polymerisatie: vloeibaar fotopolymeer (hars) uitgehard door licht
-
Materiaal extrusie: gesmolten thermoplast (filament) afgezet via een verwarmd mondstuk
-
Kruisbedfusie (PBF): poederdeeltjes versmolten door een energierijke bron
-
Materiaalstralen: druppels vloeibaar lichtgevoelig smeltmiddel afgezet op een poederbed en uitgehard door licht
-
Binderstralen: druppels vloeibaar bindmiddel afgezet op een bed van granulaat, die later aan elkaar worden gesinterd
-
Directe energiedepositie: gesmolten metaal dat tegelijkertijd wordt afgezet en samengesmolten
-
Lamineren van vellen: individuele vellen materiaal in vorm gesneden en aan elkaar gelamineerd.
Elke technologische paraplu omvat veel verschillende soorten technologieën en printers. De processen die we bij Hubs aanbieden zijn Stereolithography (SLA), Fused Deposition Modeling (FDM), Selective Laser Sintering (SLS) en HP's Multi Jet Fusion (MJF).
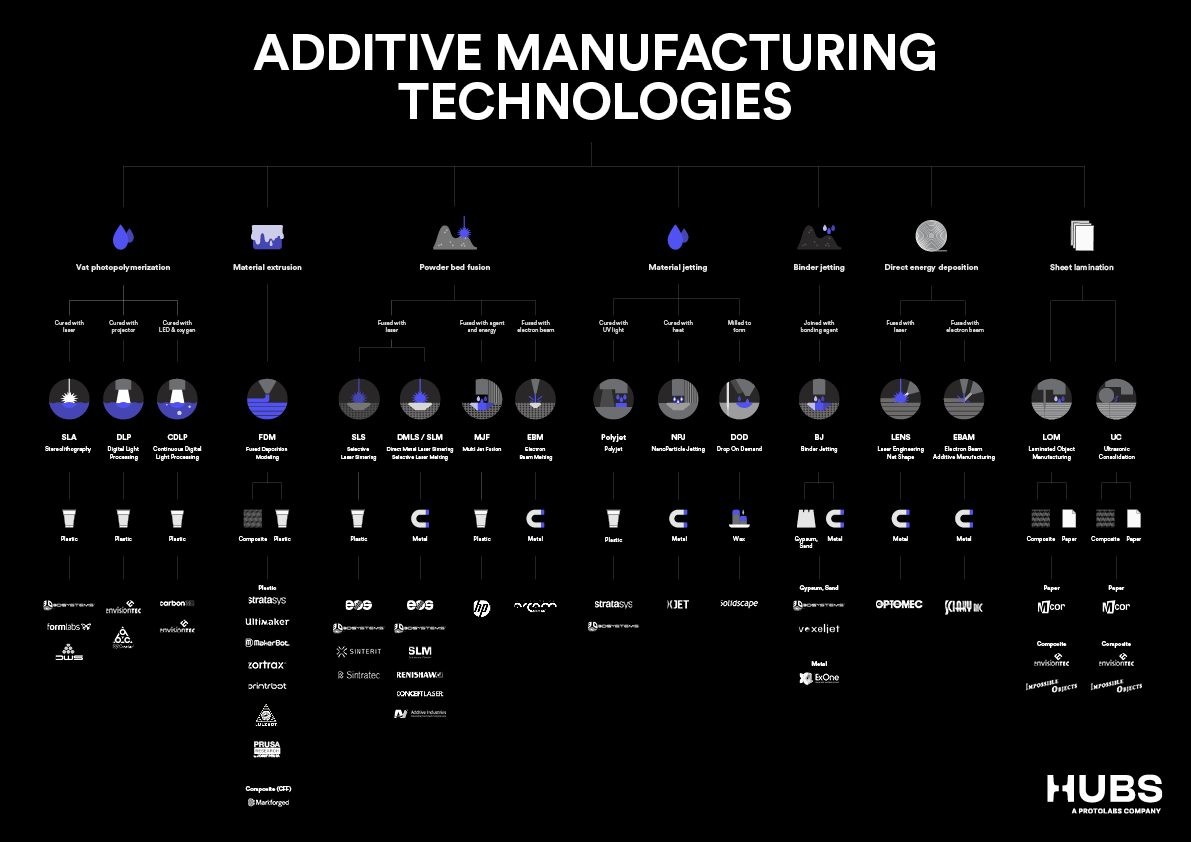
Wat is btw-fotopolymerisatie en hoe werkt het?
Vat-fotopolymerisatie produceert onderdelen door vloeibare fotopolymeerharsen selectief uit te harden met een UV-lichtbron. Een bouwplatform wordt ondergedompeld in een tank die is gevuld met hars. Het licht wordt selectief met spiegels over het harsoppervlak gericht.
Zodra een laag is uitgehard, wordt het platform in een kleine stap omhoog of omlaag gebracht om nieuwe vloeistof te laten stromen. De volgende laag wordt dan uitgehard en sluit aan op de eerder uitgeharde. Nadat de laatste laag is uitgehard, wordt de afdruk van de hars verwijderd. In dit stadium is het volledig gevormd, maar kan het worden versterkt door verder uit te harden in een UV-oven.
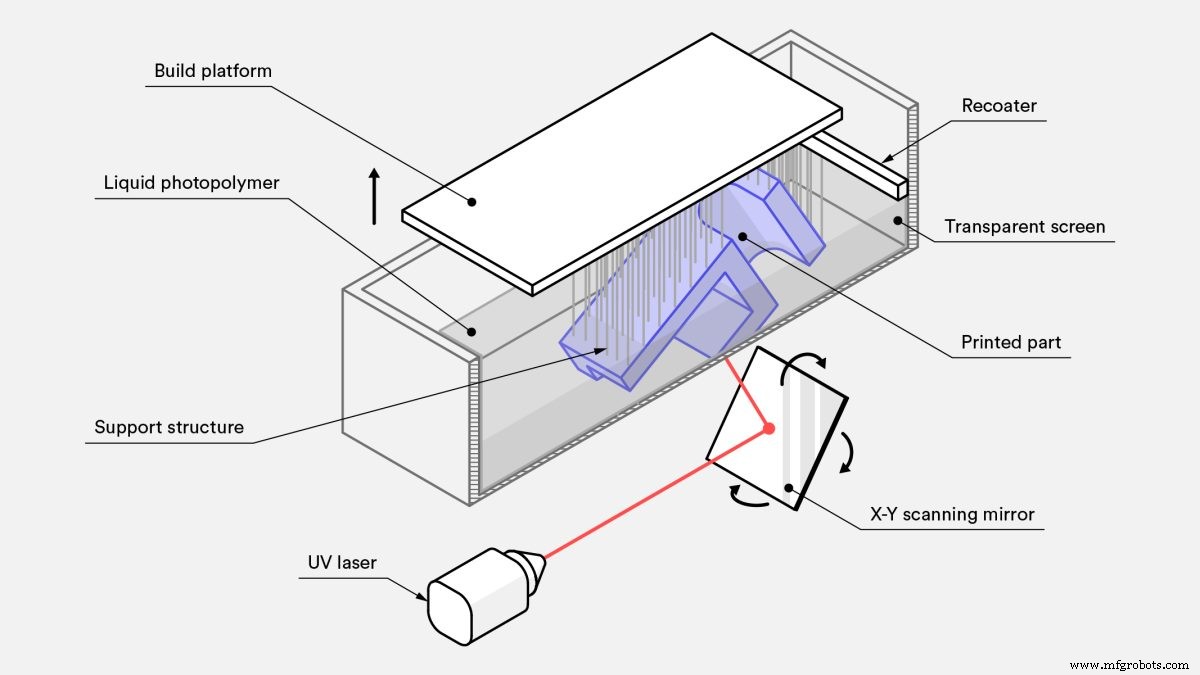
Soorten btw-fotopolymerisatie 3D-printers
Vat-fotopolymerisatie heeft een paar verschillende printtechnologieën. De drie meest voorkomende zijn SLA, directe lichtverwerking ( DLP ) en continue productie van vloeistofinterfaces (CLIP). Ze lijken erg op hoe een lichtbron het licht op de hars richt. Over het algemeen is SLA de meest voorkomende en meest gebruikte onder printers in de familie van fotopolymerisatie voor vat.
Laten we de verschillende soorten 3D-printers voor fotopolymerisatie opsplitsen:
-
SLA gebruikt een eenpuntslaser om een dunne lijn langs het oppervlak van de hars te trekken en de vorm van de uit te harden dwarsdoorsnedelaag in te vullen. Het is zeer nauwkeurig, maar kan tijdrovend zijn.
-
DLP gebruikt een digitale lichtprojector om een enkel beeld van een hele laag in één keer te flitsen. Dit maakt het sneller dan SLA. Omdat de projector echter een digitaal scherm is, bestaat het beeld van elke laag uit vierkante pixels, wat resulteert in een iets lagere resolutie.
-
CLIP is hetzelfde als DLP, behalve dat het bouwplatform in een continue beweging beweegt. Dit zorgt voor nog snellere bouwtijden en vloeiendere contouren langs de z-as.
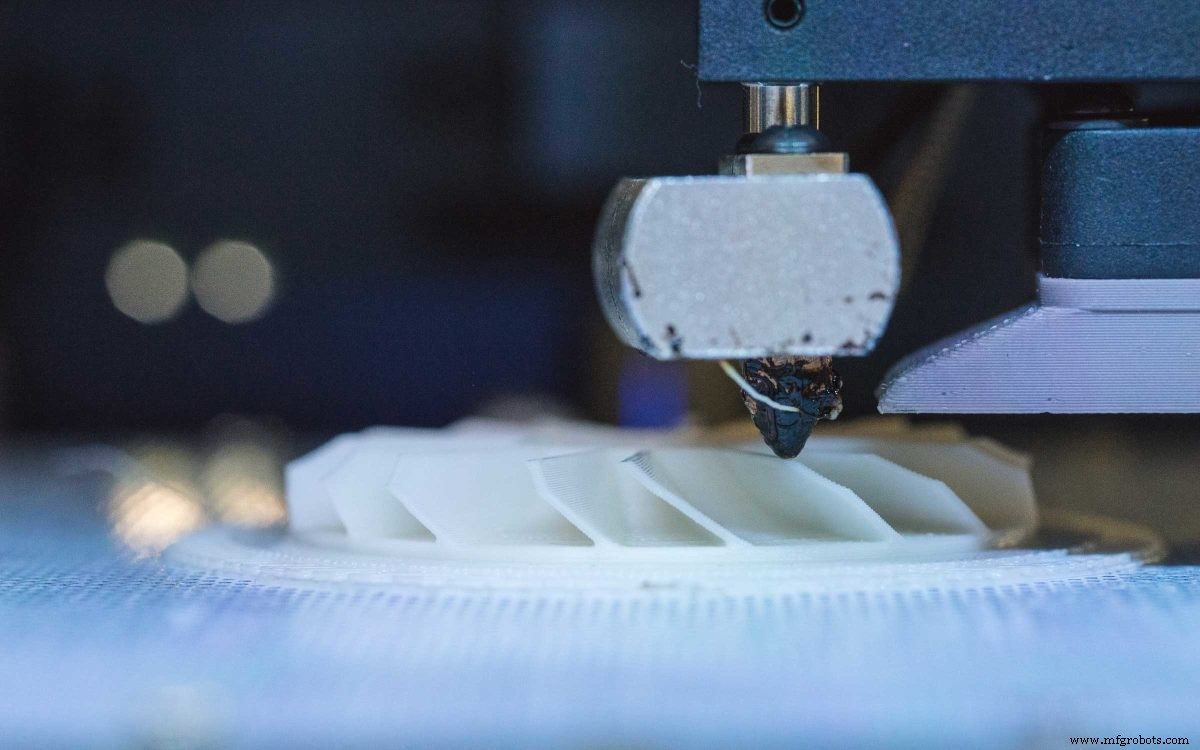
Materialen voor btw-fotopolymerisatie
Alle btw-fotopolymerisatieprinters gebruiken fotopolymeerharsen, waarvan de meeste eigendom zijn. Er zijn veel verschillende soorten beschikbaar, waaronder standaardharsen voor algemene prototyping. Andere veel voorkomende typen zijn onder meer robuust ABS -achtige harsen, flexibele rubberachtige harsen, transparante gietbare harsen zonder asgehalte na burnout, keramisch gevulde harsen voor zeer stijve prints en biocompatibele harsen voor medische hulpmiddelen.
Sommige harsen, waaronder transparante, vereisen extra nabewerking om de beste visuele resultaten te bereiken of, in het geval van heldere harsen, optische helderheid. Als u kiest voor SLA voor uw aangepaste onderdelen, bekijk dan onze vergelijking van verschillende SLA 3D-printmaterialen .
Geometrische eigenschappen van btw-fotopolymerisatie
De bouwvolumes variëren sterk tussen desktop-SLA- en industriële SLA-printers, maar zijn doorgaans kleiner dan die van FDM of PBF. Ze printen maximaal ongeveer 300 mm in één afmeting. Vat-fotopolymerisatiemachines kunnen zeer complexe onderdelen printen, hoewel niet zo complex als die van PBF vanwege de behoefte aan ondersteunende structuren.
Wat het mist in bouwvolume en complexiteit, compenseert vatfotopolymerisatie in de printresolutie, aangezien deze machines ongelooflijk fijne details kunnen printen.
Mechanische eigenschappen van fotopolymerisatie in het vat
Vat-fotopolymerisatieprinters produceren onderdelen met zeer nauwe toleranties en kunnen consistente herhaalbaarheid mogelijk maken. Als onderdelen na het printen volledig zijn uitgehard, kunnen ze ook volledig isotroop zijn. Maar waar deze technologie echt uitblinkt, is de oppervlakteafwerking. Vat-fotopolymerisatie kan extreem gladde contouren printen, vergelijkbaar met wat spuitgieten kan bereiken.
Een ander groot voordeel ten opzichte van andere technologieën is dat volledig uitgeharde onderdelen waterdicht en luchtdicht kunnen worden gemaakt. Het uithardingsproces is echter onomkeerbaar, dus verwarmde onderdelen verbranden in plaats van smelten.
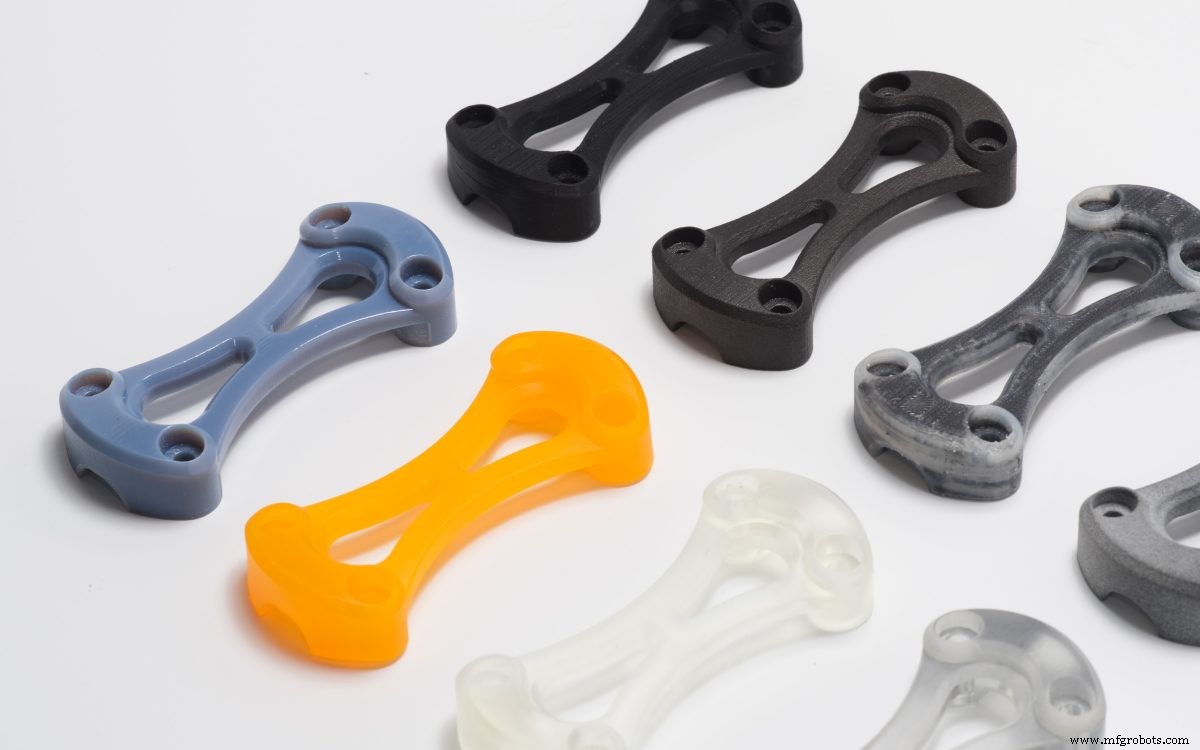
Zijn btw-fotopolymerisatieprinters snel en kostenefficiënt?
Vat-polymerisatie is de oudste vorm van 3D-printen, met de vroegste SLA-printers uit de jaren 70. Concurrentie tussen printerfabrikanten blijft de prijzen drukken, maar het blijft duur en kost ongeveer hetzelfde als plastic poederbedfusie (PBF). Deze machines zijn goedkoper dan die voor SLS, maar het materiaal is duurder.
Veel factoren zijn van invloed op de afdruktijden, maar vatpolymerisatie wordt over het algemeen als een van de snelste technologieën beschouwd.
Commerciële toepassingen:wat kunt u produceren met btw-fotopolymerisatie?
Het brede scala aan beschikbare materialen geeft fotopolymerisatieprocessen in het vat een even uitgebreid scala aan toepassingen, van prototyping tot onderdelen voor eindgebruik.
Hoge resolutie en nauwe toleranties maken de technologie ideaal voor sieraden , low-run spuitgieten en vele tandheelkundige en medische toepassingen . Het kunnen printen van waterdichte onderdelen maakt btw-fotopolymerisatie populair in de automobiel-, lucht- en ruimtevaartindustrie en de gezondheidszorg. Ook maken de gladde oppervlakteafwerkingen het optimaal voor het prototypen van spuitgegoten onderdelen.
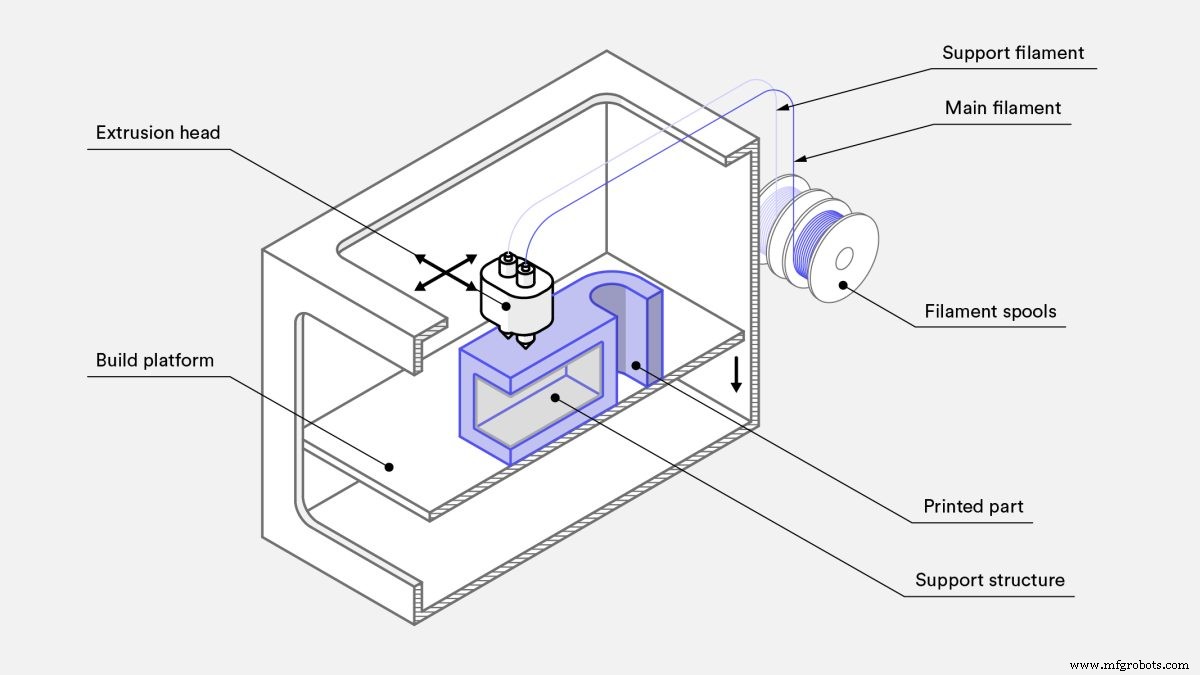
Wat is materiaalextrusie en hoe werkt het?
Materiaalextrusie produceert onderdelen door lagen gesmolten thermoplastisch filament op elkaar te printen. Een spoel filament wordt door een verwarmd extrusiemondstuk gevoerd en gesmolten. Printers zetten continu gesmolten filament af op precieze locaties, waar het afkoelt en stolt. Stel je een geautomatiseerd lijmpistool voor dat methodisch over een plat bouwoppervlak beweegt.
De printernozzle kan langs drie assen bewegen ten opzichte van het bouwplatform. Het volgt de vorm van een enkele dwarsdoorsnede van de afdruk langs de x- en y-as, en legt dwarsdoorsneden op elkaar langs de z-as om de volledige afdruk op te bouwen.
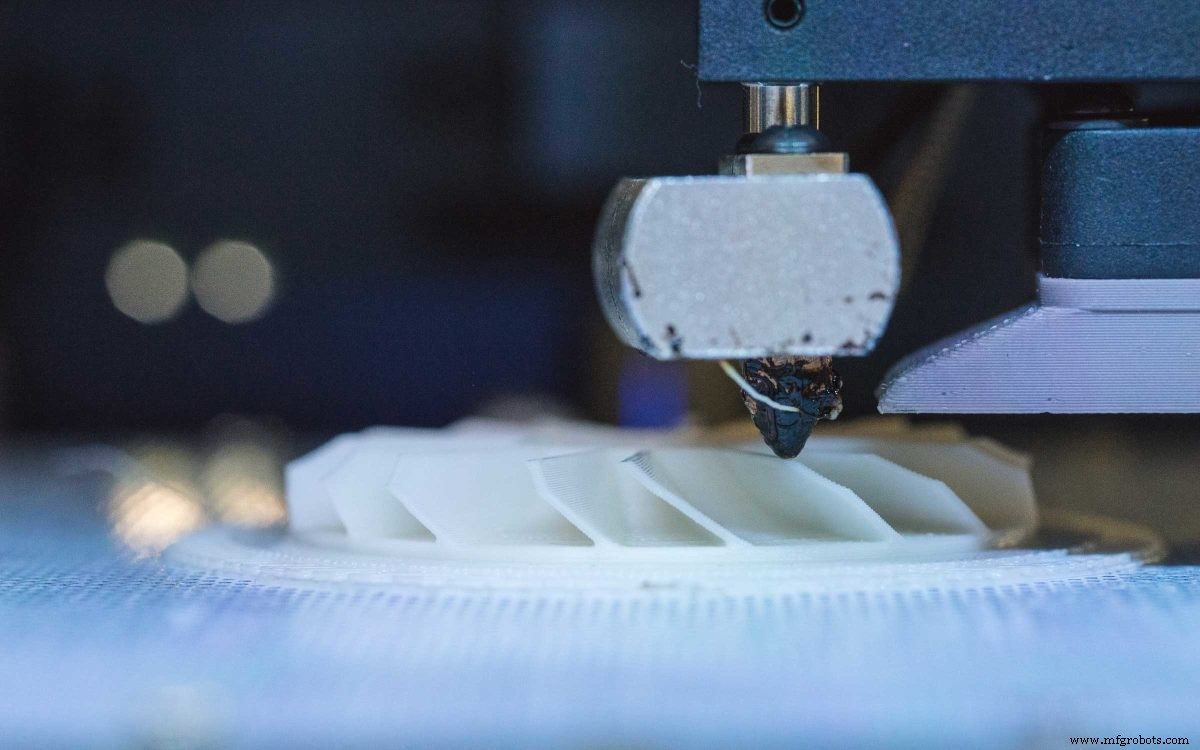
Soorten materiaal extrusieprinters
Fused deposition modeling (FDM) en fused filament fabricage (FFF) zijn de twee soorten materiaalextrusiedruktechnologieën. Materiaalextrusie is relatief eenvoudig en is verreweg de meest kostenefficiënte en algemeen beschikbare printtechnologie op de markt.
De twee belangrijkste soorten FDM zijn prototyping (desktop) en industrieel. We maken onderscheid tussen de twee omdat, hoewel de technologieën vrijwel identiek zijn, de schaal van elk enorm verschillend is.
Materialen voor materiaalextrusie
Omdat FDM zo veel gebruikt wordt, zijn er duizenden verschillende filamenten op de markt verschenen. Veruit de meest voorkomende zijn ABS en PLA, maar Nylon, PC, PETG, TPU en PEI zijn ook beschikbaar. Bepaalde filamenten zijn ook versterkt met vezels, zoals koolstof, Kevlar, glasvezel, hout en metaal.
Voor meer informatie over het kiezen van de juiste filamenten voor uw taak, hebben we een gids geschreven waarin verschillende FDM 3D-printmaterialen worden vergeleken .
Geometrische eigenschappen van materiaalextrusie en FDM
Er zijn duizenden merken FDM-printers, in alle soorten en maten. De grootste hebben platformen van zo'n 1.500 mm in alle afmetingen, terwijl de kleinste makkelijk op je bureau naast je espressomachine passen.
Omdat onderdelen van onder naar boven worden gebouwd, vereisen bepaalde kenmerken, zoals overhangen, ondersteuningen die samen met het eigenlijke onderdeel worden gebouwd. Daarom is FDM niet altijd de ideale oplossing voor het printen van complexere componenten.
De resolutie is een functie van het filament, waarbij de dunste filamenten ongeveer 0,15 mm dik zijn. Het feit dat filament rond is, betekent dat scherpe hoeken niet kunnen worden geprint en muren nooit vlak zijn, tenzij ze na het printen zijn verwerkt.
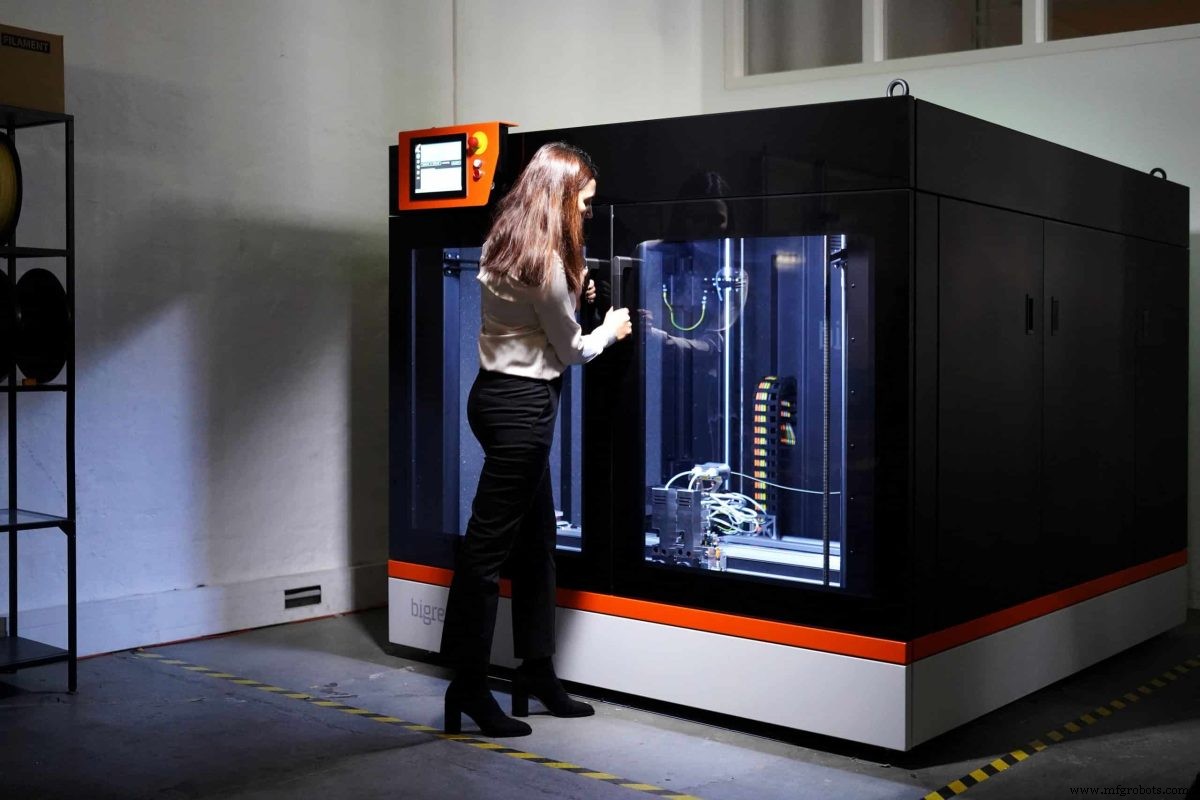
Mechanische eigenschappen van materiaalextrusie en FDM
FDM-printers worden over het algemeen niet gebruikt voor het produceren van functionele onderdelen voor eindgebruik, hoewel er hier en daar een paar uitzonderingen zijn. Het zijn niet de meest nauwkeurige 3D-printers, omdat de onderdelen die ze printen zwak zijn langs de z-as. Onderdelen hebben ook zeer duidelijke lagen op elk oppervlak.
Zijn materiaalextrusie en FDM snel en kostenefficiënt?
FDM-printers staan erom bekend dat ze qua kosten lager zijn, met desktopmachines die tussen $ 500 en $ 5.000 kosten. Industriële machines daarentegen kunnen veel duurder zijn en ver buiten het financiële bereik van zelfs de meest toegewijde hobbyisten.
Machines voor het extruderen van materialen zijn goedkoop in het bezit en gemakkelijk te gebruiken, maar outsourcing is even populair omdat de alomtegenwoordigheid van de technologie eendaagse doorlooptijden gemeengoed maakt.
Standaard FDM-materialen zijn overal verkrijgbaar en concurrentie houdt de prijzen laag. De afdruktijden zijn snel voor afzonderlijke onderdelen, maar in tegenstelling tot fotopolymerisatie in het vat of PBF zijn er geen schaalvoordelen. Dat maakt FDM relatief traag voor grote oplagen en waarschijnlijk niet de beste waarde voor een groot aantal onderdelen.
Commerciële toepassingen:wat kunt u produceren met materiaalextrusie en FDM?
Hoewel FDM-onderdelen niet zo duurzaam of cosmetisch zijn als onderdelen die met andere technieken zijn gemaakt, zijn ze zeer kosteneffectief. Deze kenmerken maken FDM de meest gebruikte technologie voor vele stadia van prototyping, vooral vroeg in de proof of concept-fase.
FDM's verscheidenheid aan beschikbare materialen, snelheid en kosteneffectiviteit maken het ook zeer aantrekkelijk voor bepaalde soorten productieonderdelen, zolang de resolutie en oppervlakteafwerking geen kritische factoren zijn. Industriële FDM-printers kunnen eenvoudig functionele prototypen en onderdelen voor eindgebruik produceren van robuuste materialen, zoals grepen, mallen en armaturen . Het produceren van deze laatste componenten met FDM-machines heeft qua prijs de voorkeur boven traditionele fabricage.
Wat is poederbedfusie (PBF) en hoe werkt het?
Poederbedfusieprinters produceren onderdelen door selectief poedervormige deeltjes te smelten of te sinteren om een heel object te vormen. Het poedermateriaal wordt tot net onder het smeltpunt verhit en in een zeer fijne laag over het bouwplatform uitgespreid. Een laser- of elektronenstraal wordt vervolgens over het oppervlak van het poeder gericht, waarbij deeltjes samensmelten om een enkele dwarsdoorsnede van de afdruk te vormen.
Na elke laag wordt het bouwplatform neergelaten en herhaalt het proces zich. Elke nieuwe laag is versmolten met de vorige totdat alle lagen zijn samengesmolten tot één object.
Omdat lagen op elkaar worden gebouwd, fungeren de niet-versmolten deeltjes als een ondersteuningsstructuur voor de afdruk, waardoor de meeste afzonderlijke ondersteuningsstructuren niet meer nodig zijn. Zodra de afdruk is voltooid, wordt het overtollige ondersteunende poeder verwijderd en gerecycled.
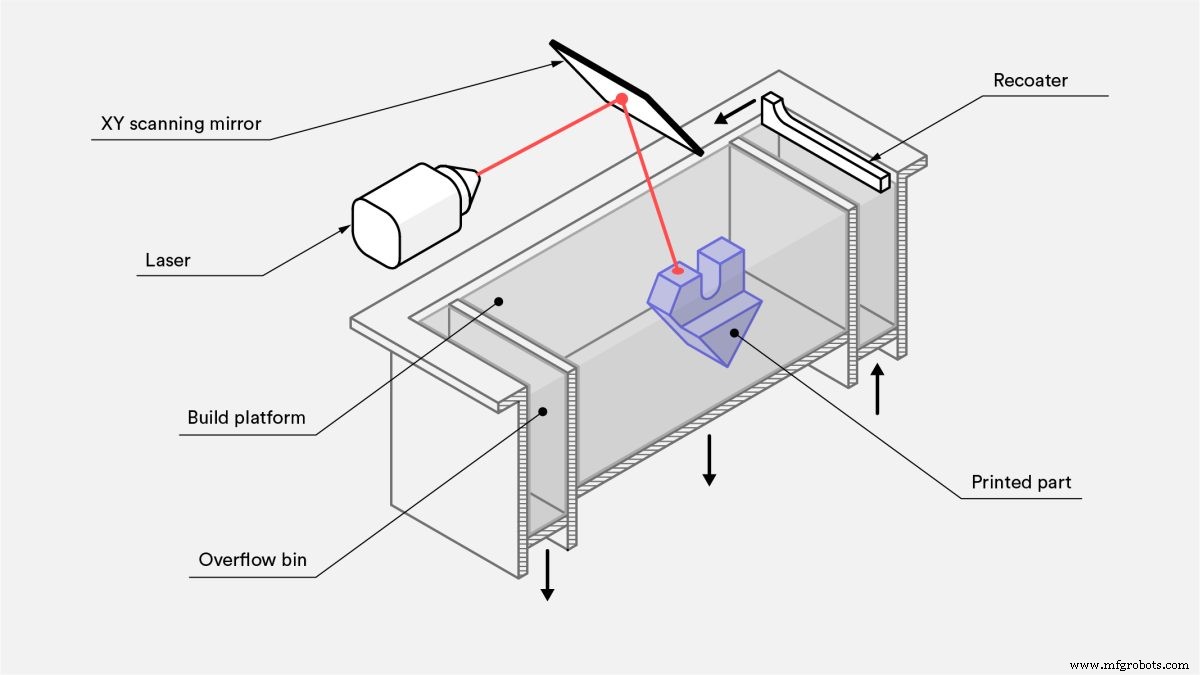
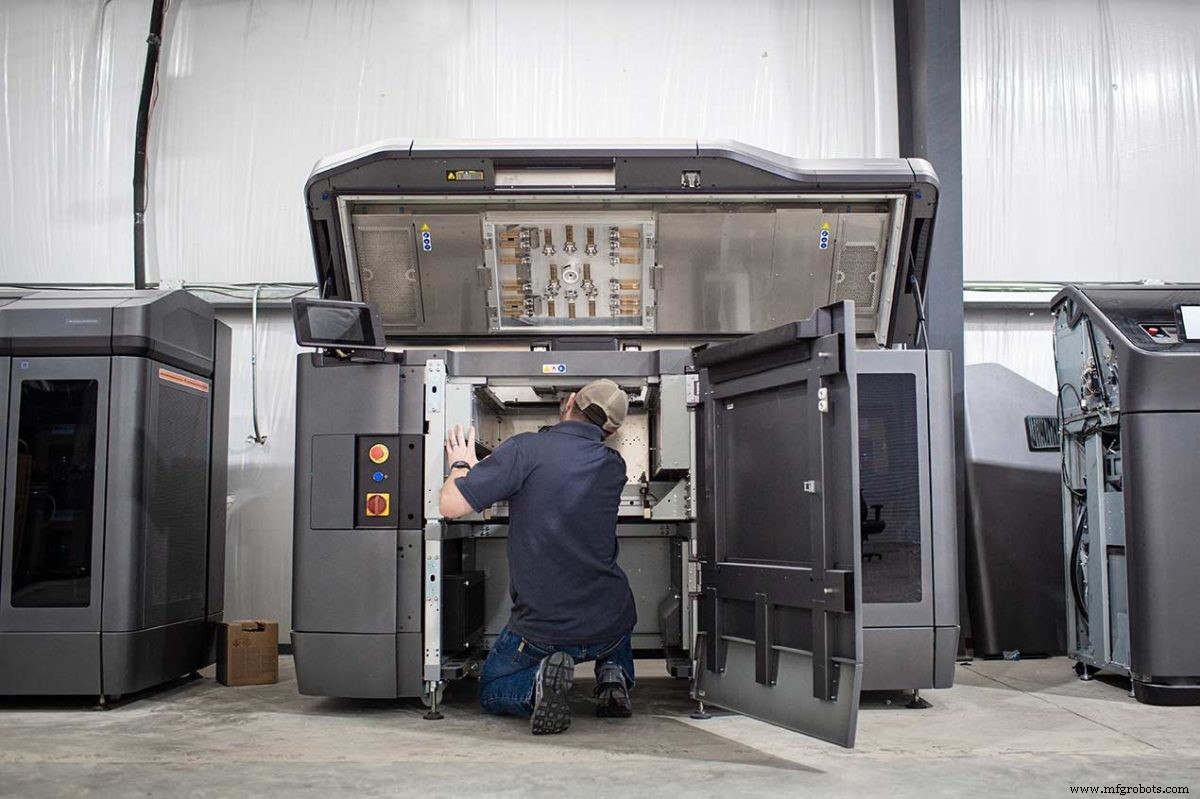
Soorten PBF-printers
Veel 3D-printers gebruiken PBF-technologie. De meest voorkomende soorten printers zijn selectieve lasersintering ( SLS ), direct metal laser sinteren (DMLS), selectief lasersmelten (SLM), HP's Multi Jet Fusion ( MJF ), high-speed sinteren (HSS) en elektronenstraalsmelten (EBM). SLS komt het meest voor voor kunststoffen, en DMLS en SLM komen het meest voor voor metalen.
-
SLS-printers produceren massieve plastic onderdelen met behulp van een laser om deeltjes samen te sinteren.
-
DMLS-printers maken poreuze metalen onderdelen met behulp van een laser om deeltjes samen te sinteren.
-
SLM-printers produceren massieve metalen onderdelen met behulp van een laser om deeltjes samen te smelten, niet alleen om ze te sinteren. Aangezien dit alleen mogelijk is als de deeltjes hetzelfde smeltpunt hebben, kan SLM alleen in afzonderlijke metalen printen, niet in legeringen.
-
MJF produceert massieve kunststof onderdelen door een combinatie van SLS en materiaalstraaltechnologieën. Nadat een laag plastic poeder over het bouwplatform is verspreid, zet een printkop met inkjetsproeiers selectief middelen af die het samensmelten bevorderen en remmen. Een krachtige infraroodstraal gaat dan over de laag en versmelt alleen de gebieden waar het smeltmiddel is aangebracht.
-
EBM produceert massieve metalen onderdelen met behulp van een elektronenstraal om deeltjes samen te smelten, maar onderdelen moeten in een vacuüm worden geproduceerd. Het proces kan alleen worden gebruikt met geleidende metalen.
-
HSS gebruikt een inkjetprintkop om een infraroodabsorberende vloeistof rechtstreeks op een dunne laag plastic granulaat te deponeren die over het verwarmde oppervlak van een bouwplatform wordt verspreid, waardoor het gebied wordt aangegeven waar sinteren gewenst is. Infraroodlicht wordt vervolgens gebruikt om het poeder onder de vloeistof tot een laag samen te smelten.
-
MJF gebruikt een inkjet-array om selectief fuseer- en detailleringsmiddelen aan te brengen op een bed van nylonpoeder, die vervolgens door verwarmingselementen worden versmolten tot een vaste laag.
Materialen voor poederbedfusie
SLS print in kunststoffen en nylon composieten, zoals Alumide, een combinatie van nylon en aluminium. Polypropyleen, een thermoplastisch polymeer, wordt ook steeds populairder voor zowel SLS als MJF.
Terwijl materialen blijven evolueren voor SLS, is nylon nog steeds het meest gebruikte materiaal. Er zijn tientallen verschillende nylons beschikbaar, maar PC, PEEK, PEKK, flexibele TPU's en composiet en versterkte nylons komen steeds vaker voor. Onderdelen worden meestal in wit bedrukt en kunnen in elke kleur worden geverfd.
MJF kan alleen printen in nylon. Omdat de fuser zwart is, konden onderdelen in het verleden alleen in grijs worden bedrukt. Tegenwoordig kunnen HP Jet Fusion 500/300 serie printers onderdelen echter in full colour en wit printen. Deze serie wordt uitgefaseerd maar zal nog jaren ondersteund worden.
Geometrische eigenschappen van poederbedfusie
PBF-printers kunnen groter worden gefabriceerd dan die voor vatfotopolymerisatie, maar zelfs grote PBF-printers overschrijden zelden 300 tot 400 mm in elke dimensie. Deze printers kunnen ook onderdelen in hoge resolutie printen. Omdat ongebruikt poeder als ondersteunend materiaal fungeert als printlagen worden opgebouwd, kan PBF onderdelen produceren van zeer complexe digitale modellen.
De potentiële complexiteit is hetzelfde voor MJF en SLS, waarbij beide betere resultaten behalen dan SLA. SLA heeft echter een nog hogere resolutie (de laaghoogte kan dalen tot 25 micron, terwijl SLS altijd afdrukt op 100 micron en MJF op 80 micron). MJF kan iets betere resoluties produceren dan SLS, maar SLS biedt een breder scala aan materialen
Voor metaal kan DMLS onderdelen printen met de hoogste beschikbare resolutie, gevolgd door SLM en vervolgens EBM.
Mechanische eigenschappen van poederbedfusie
PBF kan toleranties produceren die vergelijkbaar zijn met fotopolymerisatie in het vat, maar PBF-onderdelen zijn veel sterker. PBF kan functionele kunststof onderdelen produceren met de beste mechanische eigenschappen waartoe elke 3D-printtechnologie in staat is. MJF-afdrukken zijn iets sterker dan SLS en hebben ook een gladdere oppervlakteafwerking.
EBM-systemen produceren minder restspanningen dan DMLS en SLM, wat resulteert in minder potentiële vervorming. De metalen onderdelen van DMLS zijn niet zo sterk als die van SLM, omdat de poederdeeltjes alleen worden gesinterd en onderdelen licht poreus blijven. SLM-onderdelen kunnen echter mechanische eigenschappen hebben die vergelijkbaar zijn met traditionele productietechnologieën zoals machinale bewerking en smeden.
Alle PBF-afdrukken hebben een enigszins ruwe afwerking omdat ze zijn gemaakt van poeders, maar kunnen gemakkelijk glad worden gepolijst met een eenvoudige nabewerking.
Is poederbedfusie snel en kostenefficiënt?
PBF-marktconcurrentie blijft de prijzen drukken, maar het blijft duur. Voor metaal 3D-printen is het nog steeds extreem duur, meestal duurder dan CNC-bewerking. Voor kunststoffen zijn de kosten vergelijkbaar met fotopolymerisatie in het vat. MJF is meestal ongeveer 10 procent goedkoper dan SLS.
Als het gaat om lage volumes voor kunststoffen, zijn SLS en MJF langzamer dan vatfotopolymerisatie en FDM. Ze zijn echter het snelst voor grote batches omdat onderdelen direct op het bouwplatform worden afgedrukt.
Commerciële toepassingen:wat kunt u produceren met poederbedfusie?
Het vermogen om sterke functionele onderdelen te produceren, maakt PBF de voorkeurstechnologie voor het produceren van kleine hoeveelheden functionele plastic onderdelen in alle industrieën. Veelvoorkomende toepassingen zijn onder meer eenmalige industriële hardware zoals machineonderdelen, mallen, grepen en armaturen, evenals kleine productieruns van op maat gemaakte plastic componenten.
Omdat ze zo duur zijn, worden DMLS, SLM en EBM alleen gebruikt wanneer de geometrische complexiteit van een onderdeel te duur is om te worden bewerkt of groter is dan wat machinale bewerking kan opleveren. Door zeer complexe onderdelen te kunnen produceren, is PBF de go-to-technologie voor rapid prototyping.
Wat is materiaalstralen en hoe werkt het?
Materiaalstralen produceert onderdelen door kleine druppeltjes vloeibaar materiaal op het bouwplatform te spuiten en ze te laten stollen met warmte of licht. Net zoals bij het standaard 2D-inkjetproces, beweegt een printkop met honderden materiaalstralen over een bouwplatform, waarbij materiaal langs een X-as drager wordt afgezet, heen en weer vegen zoals de ruitenwissers op een auto en een hele laag in een enkele laag afdekken. pas.
Eén printkop kan jets dragen voor meerdere materialen, waardoor printen op meerdere materialen, full colour printen en wegwerpondersteuningsstructuren, zoals was, mogelijk is.
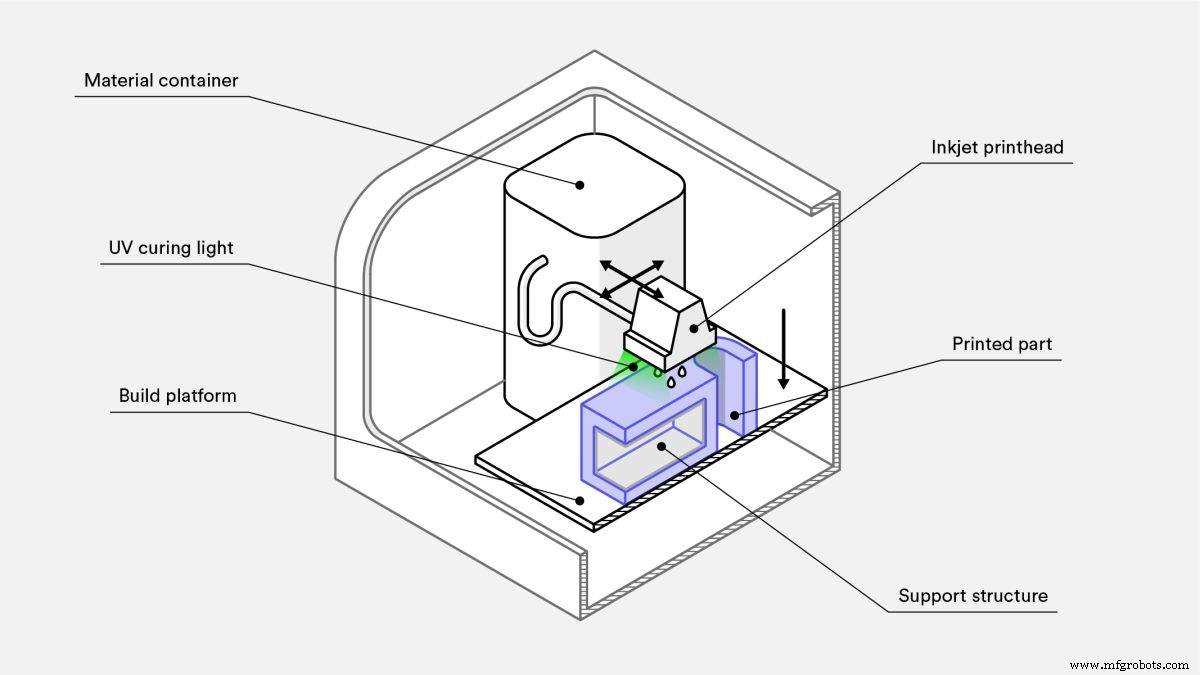
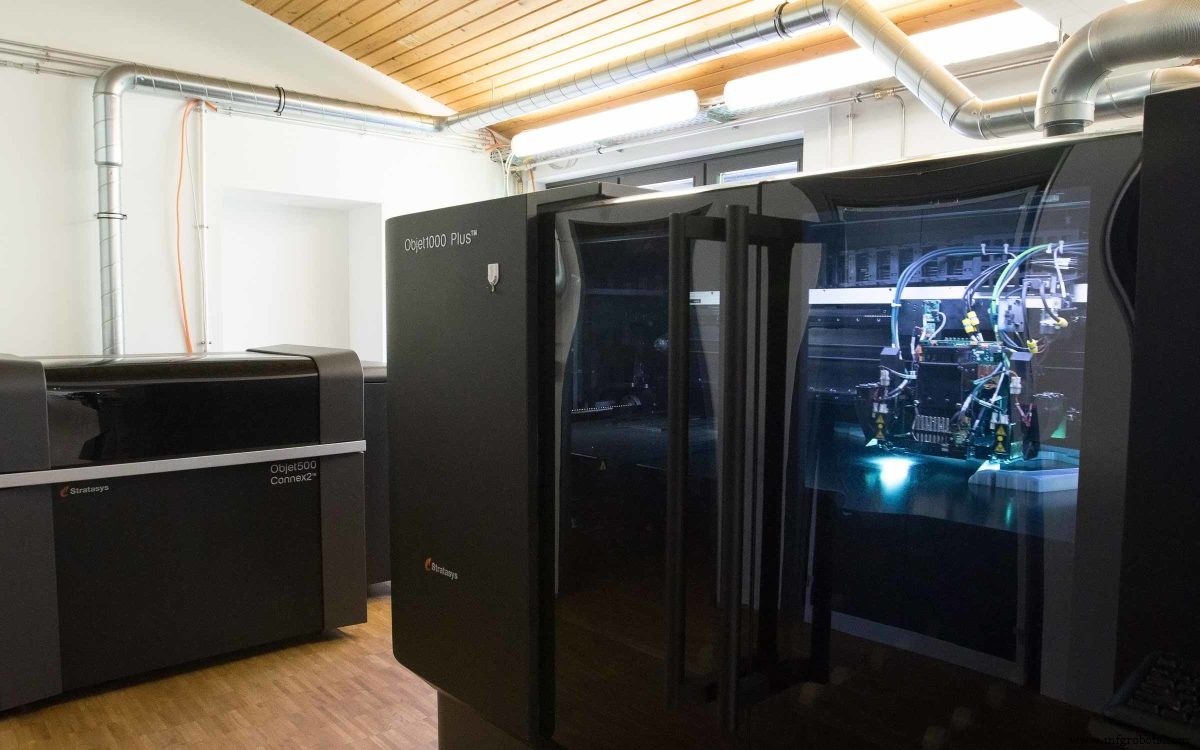
Soorten material jetting 3D-printers
Binnen de categorie material jetting zijn er een paar verschillende printtechnologieën. De drie meest voorkomende zijn PolyJet, NanoParticle Jetting (NPJ) en Drop-On Demand (DOD). Vanaf medio 2022 is PolyJet verreweg het populairst.
-
PolyJet, de eerste materiaalstraaltechnologie, is gepatenteerd en eigendom van Stratasys. Dit soort printers doseert vloeibare fotopolymeerhars en gemakkelijk te verwijderen ondersteuningsmateriaal van de printkop, die vervolgens wordt uitgehard door een UV-licht.
-
NPJ is een door XJet gepatenteerde technologie. In tegenstelling tot PolyJet, waarbij elke laag wordt uitgehard voordat de volgende wordt aangebracht, worden NPJ-prints uitgehard zodra alle lagen zijn aangebracht. Metalen of keramische nanodeeltjes worden gesuspendeerd in een vloeistof, die samen met ondersteunend materiaal door de printkop wordt neergeslagen. Warmte in de printer zorgt ervoor dat de suspensievloeistof verdampt wanneer elke laag wordt afgezet, waardoor er slechts licht gebonden metaal of keramiek en steunen achterblijven. Zodra de laatste laag voltooid is, wordt het dragermateriaal verwijderd en wordt het hele onderdeel gesinterd om alle nanodeeltjes te binden.
-
DOD is een technologie gepatenteerd door SolidScape (overgenomen door Stratasys). Het lijkt sterk op PolyJet, maar is speciaal ontwikkeld voor zeer nauwkeurig printen in was voor investeringsgieten en het maken van matrijzen, gericht op de sieradenindustrie. In tegenstelling tot PolyJet kan de printkop curven in hoge resolutie printen door zowel de x- als de y-as te bewegen. Nadat de materiaaldruppels zijn afgezet, wordt elke voltooide laag afgeschuimd met een vliegensnijder om een perfect vlak oppervlak te garanderen. Deze factoren verbeteren de uiteindelijke maatnauwkeurigheid.
Materialen voor materiaalstralen
Vanwege de verscheidenheid aan technologieën in de categorie is een breed scala aan materialen beschikbaar voor gebruik met material jetting-printers. De meest voorkomende zijn fotopolymeren, flexibele kunststoffen, gietwas, metalen en keramiek.
PolyJet-printers staan erom bekend dat ze full-color, multi-materiaal, multi-textuur prints kunnen produceren.
Geometrische eigenschappen van material jetting
Build-platforms kunnen behoorlijk groot worden:ze kunnen tot 1 vierkante meter groot worden en zijn bijna net zo groot als die in FDM worden gebruikt. Afzonderlijke onderdelen kunnen ook erg groot zijn en het hele printbed vullen. Aangezien er rondom het onderdeel volledig solide ondersteuningen worden opgebouwd, kunnen ze ook zeer complexe onderdelen produceren.
Mechanische eigenschappen van materiaal jetting
Material jetting-printers zijn zeer nauwkeurig en kunnen onderdelen met zeer hoge toleranties produceren, hoewel de sterkte van onderdelen doorgaans minder is dan wat FDM of PBF kan bereiken. De oppervlakteafwerkingen zijn zeer glad, maar er is ook een optie om in een matte omgeving te printen.
Is materiaal jetting snel en kostenefficiënt?
Ongeacht het type printer, materiaalstralen is eigenlijk vrij duur. De materialen zijn duur en de draagstructuren zijn solide geprint, waardoor er veel materiaalverspilling is per onderdeel.
Productiesnelheden zijn vergelijkbaar met PBF-printers.
Commerciële toepassingen:wat kun je produceren met material jetting?
Materiaalstralen is een dure 3D-printtechnologie, maar de extreem hoge maatnauwkeurigheid en gladde oppervlakteafwerkingen maken het de enige haalbare oplossing wanneer maatnauwkeurigheid of indrukwekkende beelden van cruciaal belang zijn. Dit is vaak het geval voor zeer realistische prototypes, anatomische modellen, complexe en zeer nauwkeurige gereedschappen, sieraden, medische hulpmiddelen en chirurgische hulpmiddelen.
Afdrukken op meerdere materialen wordt vaak gebruikt voor prototypes met haptische feedback, bijvoorbeeld een stevige behuizing met flexibele knoppen.
Wat is binder jetting en hoe werkt het?
Binder jetting produceert onderdelen door selectief een bindmiddel over een poederbed te deponeren. Het bouwplatform wordt eerst bedekt met een zeer dunne laag materiaalpoeder. Een printkop bedekt met inkjetsproeiers gaat er vervolgens overheen, waarbij een bindmiddel wordt afgezet waar de afdruk moet worden gevormd. Binder jetting-printers kunnen ook in kleur printen door gekleurde inkt achter het bindmiddel aan te brengen, voordat een nieuwe laag poeder de vorige bedekt.
Als de laatste laag klaar is, laat men het onderdeel uitharden in het poeder en laat het bindmiddel aan kracht winnen. Eenmaal uit de poederbak verwijderd, zijn sommige soorten materialen klaar. Als onderdelen echter voor functioneel gebruik zijn, moeten de meeste worden geïnfiltreerd en gesinterd, waardoor ze tot 40 procent krimpen.
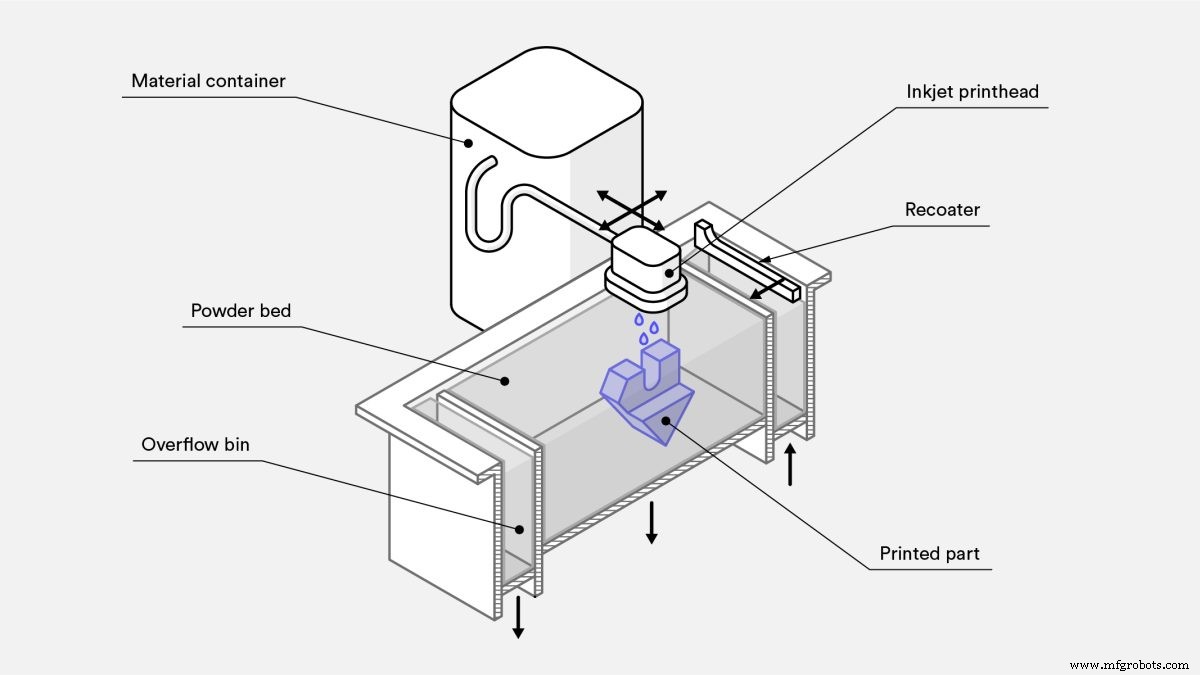
Soorten binder jetting 3D-printers
Binder jetting wordt bereikt door slechts één technologie, hoewel er veel verschillende soorten printers zijn, die zich onderscheiden door de soorten materialen en bindmiddelen die ze kunnen gebruiken.
Lees ons inleidende artikel over 3D-printen met binderjet voor meer informatie.
Materialen voor binder jetting
Omdat prints bij elkaar worden gehouden door een bindmiddel - in tegenstelling tot bindingen tussen deeltjes van het bouwmateriaal - kunnen veel materialen die kunnen worden gepoederd, worden bedrukt met binder jetting. De meest voorkomende materialen zijn zand, keramiek en metalen, maar ook kunststoffen kunnen worden gebruikt.
Geometrische eigenschappen van bindmiddelstralen
Binder jetting is het meest geschikt voor onderdelen die kleiner zijn dan een vuist.
Doordat het ongebruikte poeder dient als natuurlijke ondersteuningsstructuur zijn ook complexe onderdelen mogelijk. Een beperking is echter dat de dikte nooit meer dan 10 mm mag zijn, omdat de filtratie inconsistent kan zijn. Ook zijn de resoluties hoog, vergelijkbaar met PBF.
Mechanische eigenschappen van binder jetting
Binder jetting kan onderdelen produceren met goede toleranties, maar de uiteindelijke tolerantie kan moeilijk te voorspellen zijn, aangezien krimp optreedt bij nabewerking.
Vóór infiltratie zijn metalen onderdelen extreem zwak en kunnen ze afbrokkelen als ze niet voorzichtig worden behandeld. Na infiltratie zijn ze bijna volledig dicht, maar hun mechanische eigenschappen voldoen niet aan de hogere kwaliteit van traditioneel vervaardigde onderdelen.
De oppervlakteruwheid van deze metalen onderdelen is beter dan die met DMLS en SLM.
Is binder jetting 3D-printen snel en kostenefficiënt?
Binder jetting is een betaalbare technologie, die zelfs minder kost dan fotopolymerisatie in het vat en PBF. Printsnelheden zijn vergelijkbaar met PBF en in lijn met andere technologieën voor kleine oplagen, maar snel voor hogere volumes.
Commerciële toepassingen:wat kun je produceren met binder jetting?
Omdat het complexe onderdelen vrij snel en kosteneffectief kan produceren in een verscheidenheid aan kleuren, is binder jetting ideaal voor full-color prototyping. De prijs van binder jetting is lager dan die van materiaal jetting en ondanks de beperkingen van de mechanische eigenschappen kan het nog steeds resoluties bereiken die geschikt zijn voor de meeste prototypes.
Dit is ook een van de snelste en meest betaalbare technieken voor het produceren van complexe, zeer nauwkeurige metalen en keramische onderdelen. Er zijn veel verschillende poeders beschikbaar en printbedden kunnen relatief groot zijn. De mechanische eigenschappen van met bindmiddel gespoten metalen onderdelen komen niet overeen met de sterkte of toleranties van PBF-afdrukken, maar ze kunnen nog steeds functioneel zijn als ze worden geïnfiltreerd en gesinterd.
Bindmiddelstralen is vooral aantrekkelijk voor het maken van complexe afgietsels uit zand, omdat het grote, complexe geometrieën kan printen tegen relatief lage kosten. En het proces is eenvoudig genoeg om te worden geïntegreerd met de meeste traditionele gieterijprocessen.
Wat is directe energiedepositie en hoe werkt het?
Directe energieafzetting (DED) produceert onderdelen door kralen van gesmolten materiaal, dat meestal metaal is, in lagen aan te brengen. De technologie lijkt sterk op de technologie die wordt gebruikt in extrusieprinters van kunststof, maar dan voor metaal. Het uitgangsmateriaal, dat poeder of draad is, wordt continu door een mondstuk geduwd en gesmolten door een laser of een elektronenstraal of boog op het punt van depositie, waar het afkoelt en stolt.
Het mondstuk kan langs meerdere assen bewegen ten opzichte van het bouwplatform. Machines met drie assen volgen de vorm van een enkele dwarsdoorsnede van een afdruk langs de x-as en y-as, waarbij dwarsdoorsneden op elkaar langs de z-as worden gelegd om het volledige deel op te bouwen. Vijfassige DED-printers zijn niet beperkt tot het laag voor laag opbouwen van onderdelen, omdat ze materiaal vanuit elke hoek kunnen neerslaan. Dit betekent dat ze meer kunnen dan alleen onderdelen van de grond af opbouwen en vaak worden gebruikt om materiaal op meerdere zijden van bestaande objecten te deponeren.
DED wordt vaak directe metaalafzetting (DMD) genoemd. Er zijn ook veel verschillende eigen technologieën waarvan de namen vaak door elkaar worden gebruikt, ook al verschillen ze in hun materialen en energiebronnen.
Alle werken volgens zeer vergelijkbare principes. Laser Engineered Net Shaping (LENS) van Optomec is het bekendste voorbeeld van een technologie die poeders versmelt met een krachtige laser. Electron Beam Additive Manufacturing (EBAM) van Sciaky is het bekendste voorbeeld van een technologie die geëxtrudeerde draad versmelt met een elektronenbundel.
Soorten DED-printers
LENS maakt gebruik van een afzettingskop die bestaat uit een laserkop, poederdoseersproeiers en slangen voor inert gas. De laser gaat door het midden van het hoofd om een smeltbad op het bouwgebied te creëren en poeder wordt vanaf de zijkanten gespoten waar het wordt gesmolten en vervolgens gestold. Het inerte gas vormt een zuurstof- en vochtvrije mantel, die oxidatie van het oppervlak voorkomt en een betere laaghechting bevordert.
EBAM feeds metal welding wire through the nozzle and melts it with an electron beam at the contact point with the build area. Essentially, EBAM is FDM for metals.
Materials for DED
LENS technology can print in both metals and ceramics, although ceramics are by far the more common material in use. Available materials for both LENS and EBAM include almost any weldable metal, such as aluminum, steel, titanium, Inconel, tantalum, tungsten, nickel, and niobium.
Geometric properties of DED
Another key advantage of DED is the very large print bed sizes. It is not uncommon for large manufacturers to build customer DED printers with build envelopes that are multiple meters long along any dimension.
Support structures are possible but difficult because the large liquid melt pool at the deposition point does not allow for overhangs. The same attribute means complex geometries are also not possible. Resolution is very poor compared with other metal 3D printers. Powder particle sizes are between 50 and 150 microns and welding wire ranges from 1 to 3mm in diameter.
Sharp corners, for example, can only be achieved in post-processing, typically by a CNC mill. This is very common practice, as new material is built up with DED and then machined to the desired precision.
Mechanical properties of DED
The high amount of energy required to maintain a melting point at the point of deposition creates large thermal gradients that can cause a lot of residual stress, but DED produces fully dense parts with mechanical properties that are as good as forged metal parts.
The low resolution, however, means parts tend to have a poor surface finish, requiring secondary machining to achieve the most desired results.
Is DED fast and cost-efficient?
The two most important advantages of DED are print speed and material cost. All DED technologies are relatively fast at laying down material, with the fastest machines printing 11kg per hour, (albeit with very low resolution). The metal feedstock used is also cheaper than that used by other metal 3D printers.
The powders are usually commercial off-the-shelf (COTS) materials designed for welding and are widely available. But for simple parts, traditional manufacturing is still almost always cheaper.
Commercial applications:what can you produce with DED?
The three main applications of DED are part repairs, feature additions, and near-net-shape part production. Essentially a form of welding, DED can print onto existing parts. This makes it ideal for repairing broken parts and adding features that cannot be added via other processes. Tool repair is by far the most common use, and companies turn to DED when expensive machinery proves more cost-effective to fix than reorder, such as in heavy industry.
Because the resolutions are so low, most parts also require post-processing with a CNC mill. Parts are therefore printed near to net shape, with the expectation that they will be machined to proper tolerances. Because conventional manufacturing is almost always cheaper, near-net-shape DED printing is only used when traditional manufacturing is very slow, expensive, or simply not possible.
What is sheet lamination and how does it work?
Sheet lamination produces parts by stacking and laminating sheets of material cut to match a part’s single-horizontal cross-sections. In some printers, the sheets are first cut and then laminated. In most, the sheets are first laid and laminated and then cut to size.
Types of sheet lamination printers
This is one of the simplest methods of building up 3D models. Despite its simplicity, there are many different proprietary technologies based on material, lamination method, and cutting method. In most cases, the process is a simple variation of paper laminated object manufacturing (LOM). Ultrasonic consolidation (UC) is the only radically different technology, as it uses ultrasonic welding rather than a separate bonding agent.
-
LOM laminates sheets together with a bonding adhesive and then subtracts features layer by layer, using CNC milling, laser cutting, or water-jet cutting.
-
UC follows the same process at LOM, except the lamination is achieved through ultrasonic vibrations as a form of friction welding.
Materials for sheet lamination
Across all the different types of printers, there are many available materials:papers, most polymers, fiber-reinforced polymers, ceramics, and just about any metal. Multi-material layers can also be achieved with all these materials, provided each layer can be laminated and shaped with the same methods.
Using colored sheets enables full-color prints across the color spectrum.
Geometrics properties of sheet lamination
Sheet lamination print beds vary quite a lot in size, but are comparable to SLA and SLS printers. Large-format printers are not common.
Because the sheet cutting methods are relatively simple, highly complex shapes are not possible. However, because support structures are not necessary, internal structures are possible.
One additional design option is to lay embedded wiring between sheets. Most processes do not require heat, so expect a reduced risk of high temperatures destroying them. Typical layer resolution depends entirely on the material feedstock
Mechanical properties of sheet lamination
Dimensional accuracy and surface finishes are on par with what can be achieved with a simple CNC milling machine, laser cutter, or water-jet cutter. The weakness of the bond between sheets, however, means that these parts are unsuitable for structural or functional purposes.
Is sheet lamination fast and cost-efficient?
LOM is very cost-effective thanks to the ready availability of all the raw materials. The lack of pre-production preparation means the printers are also very fast.
What are the commercial applications of sheet lamination?
LOM was originally used in architecture for building models. Today its most common use is for highly detailed, colored objects, typically for proof-of-concept and look-and-feel prototyping.
Frequently asked questions
How do I decide the right 3D printing technology for my custom parts?
There are many factors to think about before settling on the right 3D printer for your manufacturing needs. These include functionality, materials required, cosmetic characteristics, process capabilities and many more. To start, check out this comprehensive resource on selecting the right 3D printing process, and remember that you can (and should) always test different printing methods before finding the one that's perfect for your custom parts.
What 3D printer is optimal for complex geometries.
For designs with complex geometries, we highly recommend opting for a powder bed fusion technology like SLS or MJF.
What do I do if several 3D printers work for my custom parts?
Oftentimes, several different 3D printing processes can produce your parts. If this ends up being the case, compare the cost and properties of each to determine the right manufacturing fit.
What 3D printing technology is right for functional polymer parts?
For functional polymer parts, go for thermoplastics ( SLS or FDM) over thermosets (SLA/DLP or material jetting).
What 3D printing technologies will give me the best cosmetic appearance?
For the best cosmetic quality, thermosets (SLA/DLP or material jetting) will give you the most impressive aesthetics.
What's the best 3D printing technology for metal parts?
Honestly, we recommend pivoting to CNC machining for producing metal parts, though if your designs are very complex, DMLS and SLM are viable alternatives to milling and turning.
3d printen
- Wat zijn technopolymeren en waarvoor worden ze gebruikt?
- Wat zijn de verschillende soorten nagels?
- De vele soorten polyurethaan en waarvoor ze worden gebruikt
- Wat zijn de soorten actuatoren
- Wat zijn de soorten persluchtdrogers?
- Wat zijn de meest voorkomende soorten onderhoudsladders?
- Wat zijn de verschillende soorten buisbuigen?
- Wat zijn de verschillende soorten onderhoudspersoneel?
- Graafmachines:wat ze zijn en typen die uw project kunnen helpen.
- Wat zijn de 7 soorten technologie?
- Wat zijn de verschillende soorten prototypes?