De staat van gerecyclede koolstofvezel
De zaak voor gerecyclede koolstofvezel is ingewikkeld. De industrie is gebouwd op de hoop problemen op te lossen, namelijk de wens om koolstofvezelafval van stortplaatsen te houden en een potentiële kloof tussen vraag en aanbod van koolstofvezel te dichten. Algemeen wordt geschat dat ongeveer 30% van de geproduceerde koolstofvezel als afval belandt. Ondertussen, aangezien waardevol materiaal op stortplaatsen belandt, zijn de meeste analisten het erover eens dat de jaarlijkse vraag naar het materiaal de huidige jaarlijkse productiecapaciteit in de komende jaren zou kunnen overtreffen. De gemiddelde geschatte wereldwijde vraag naar koolstofvezel is ongeveer 65.000-85.000 metrische ton per jaar, met een wereldwijde capaciteit van het typeplaatje (wat meer is dan de werkelijke capaciteit) van ongeveer 150.000 metrische ton, volgens schattingen gepresenteerd door Brett Schneider, president, wereldwijde vezels, Hexcel (Stamford, Conn., VS) en Dan Pichler, directeur van CarbConsult GmbH (Hofheim am Taunus, Duitsland) op de koolstofvezelconferentie van december 2018. Zoals gemeld door CW medewerker Amanda Jacob in maart, schatten sommige analisten dat de vraag naar koolstofvezel in 2022 het aanbod met ongeveer 24.000 ton zou kunnen overtreffen. (zie "Vertrouwen opbouwen in gerecyclede koolstofvezel".)
En hoewel commerciële leveranciers van gerecyclede koolstofvezel (rCF) wijzen op teruggewonnen en hergebruikt materiaal als een mogelijke oplossing voor deze vraag- en aanbodkloof, heeft de rCF-industrie haar eigen uitdagingen. Hoewel de technologie voor het recyclen van koolstofvezelcomposieten al enkele jaren bestaat en een product kan opleveren met mechanische eigenschappen die zeer dicht bij die van nieuw materiaal liggen, is de recyclingindustrie voor composieten relatief jong en bevindt zij zich nog in de beginfase van de ontwikkeling van markten voor de materialen het produceert uit recyclaat. Naarmate het vertrouwen in de kwaliteit van de door recyclers geproduceerde vezels toeneemt, zijn vragen over kosten en beschikbaarheid op de voorgrond gekomen. Misschien wel de grootste uitdaging voor de industrie is de bezorgdheid over de beveiliging van de toeleveringsketen.
"De technologieën zijn er echt en ze bestaan al een tijdje, maar de toeleveringsketen is gewoon niet doorgelicht", zegt Andrew Maxey, CEO van Vartega (Golden, Colo., U.S.). "Zonder de juiste stukken die bij elkaar komen, kun je de beste technologie ter wereld hebben, maar je hebt geen materiaal om te recyclen en je hebt geen producten om het in te stoppen."
Commerciële leveranciers beschouwen de lucht- en ruimtevaartindustrie vaak als een bron van productieschroot en afgedankt materiaal dat als recyclaat moet worden gebruikt, maar hoewel de hoeveelheid afval die door de lucht- en ruimtevaartindustrie wordt gecreëerd groot is in termen van wat er naar de stortplaats gaat, veel OEM's en fabrikanten zijn terughoudend geweest om erop te vertrouwen als een constante toevoerbron voor een productlijn met grote volumes.
Anderzijds wordt er enige vooruitgang geboekt. In december 2018 kondigde Boeing aan dat het koolstofvezelrecyclingspecialist ELG Carbon Fiber Ltd. (Coseley, V.K.) zal voorzien van uitgehard en niet-uitgehard koolstofvezelafval dat zal worden gerecycled voor gebruik in secundaire producten voor andere toepassingen voor de fabricage van composieten. De overeenkomst is de eerste formele materiaalleveringsrelatie tussen een koolstofvezelrecycler en een grote vliegtuig-OEM en lijkt een goed voorteken voor de industrie te zijn.
Het gaat niet alleen om milieuzorg
Het argument voor het gebruik van rCF gaat verder dan duurzaamheid. Lagere kosten zijn ook een voordeel. De rCF van ELG Carbon Fibre kost bijvoorbeeld ongeveer 40% minder dan nieuwe koolstofvezel van industriële kwaliteit. Andere commerciële leveranciers beweren dat hun materiaal ergens tussen de 20% en 40% goedkoper is dan nieuwe koolstofvezel. Bovendien is er voor veel toepassingen behoefte aan discontinue vezelformaten - wat een kans suggereert waar rCF een duurzamer en voordeliger alternatief zou kunnen bieden voor nieuw materiaal.
"Overal waar de industrie discontinue of gehakte koolstofvezel gebruikt, moet gerecyclede [vezel] de eerste overweging zijn", zegt Maxey. “We geven al dit geld uit om nieuwe koolstofvezel te maken in een continu formaat … waarom nemen we dat dan en gaan we het in stukken hakken om in thermoplast te stoppen? Als we al een discontinu formaat in die restjes hebben, is dat naar mijn mening het beste materiaal om te gebruiken voor die vormmassa's waar je het toch gewoon gaat hakken."
Bovendien is aangetoond dat de kwaliteit van de geproduceerde rCF in sommige gevallen vergelijkbaar is met die van nieuwe vezels. ELG Carbon Fibre, dat koolstofvezels terugwint met behulp van pyrolyse, zegt dat zijn vezel doorgaans ten minste 90% van zijn treksterkte behoudt zonder verandering in modulus. Vartega gebruikt een chemisch recyclingproces en beweert dat de vezel dezelfde mechanische eigenschappen heeft als nieuwe koolstofvezel. Shocker Composites (Wichita, Kan., V.S.) gebruikt een inline solvolyseproces om de vezel terug te winnen en claimt hoge kwaliteit zonder zichtbare schade aan vezels.
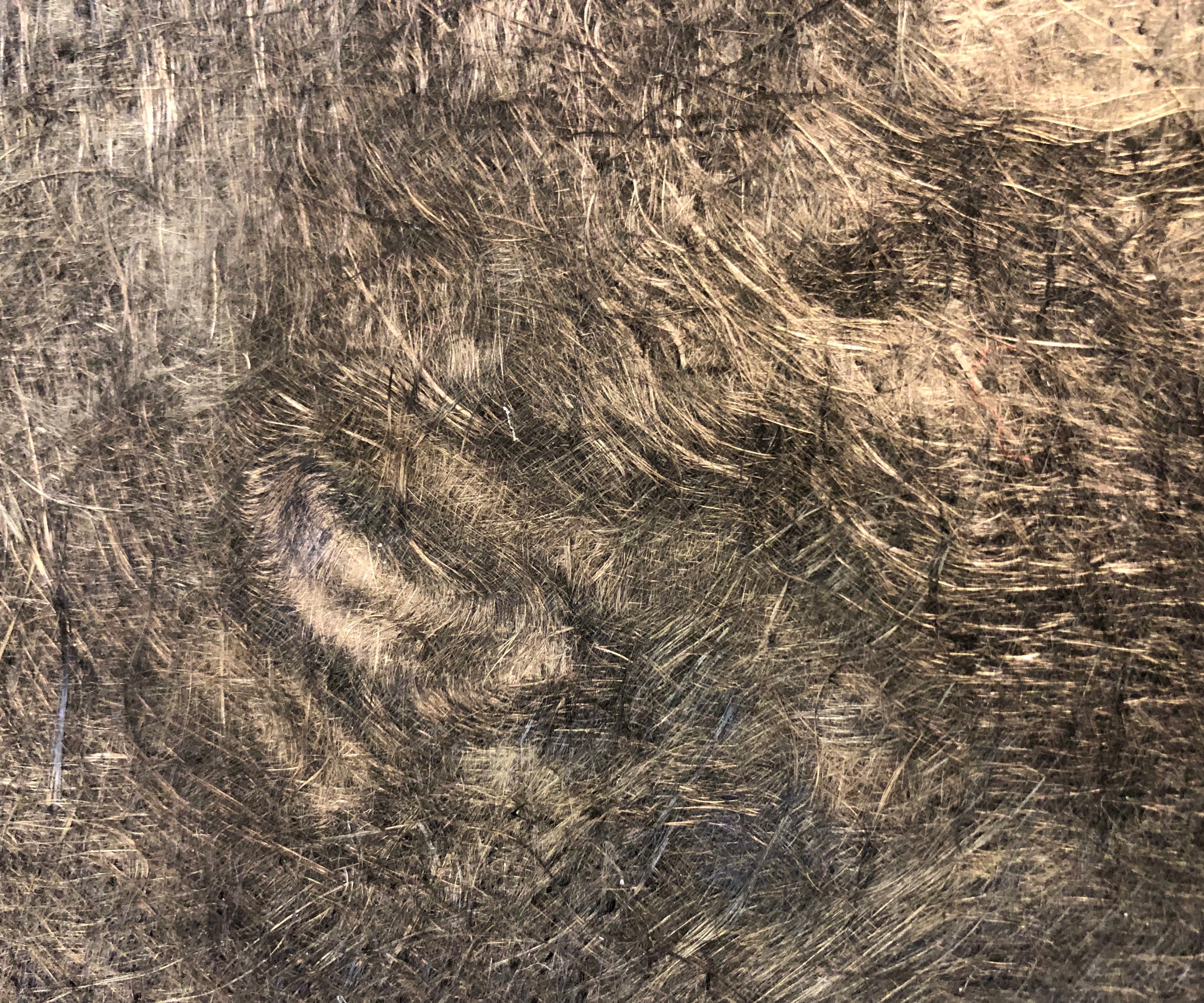
Gerecycleerde koolstofvezel nonwoven mat van ELG Carbon Fibre.
CW-foto | Scott Francis
Volgens Vamsidhar Patolla, Wichita State University Ph.D. student en oprichter van Shocker Composites, de uitdaging is om de kosten te verlagen tot een niveau dat vergelijkbaar is met dat van andere materialen zoals aluminium. "De verwerkbaarheid moet passen bij de productieschaal van grote volumes", zegt hij. Het proces van Shocker Composites biedt dit voordeel omdat het een inline proces is en geen batchproces. (Lees meer in het artikel “Duurzame, inline recycling van koolstofvezel.”)
Gezien de recente verbeteringen van de afgelopen jaren in rCF-verwerking en vezelkwaliteit, zijn commerciële leveranciers begonnen hun focus te verschuiven van het downcyclen van rCF naar producten met een lagere prestatie en meer naar het vinden van geschikte toepassingen die profiteren van de eigenschappen van het materiaal.
"We zullen nieuwe vezels nooit volledig vervangen, vooral niet in de lucht- en ruimtevaart waar hoge sterkte- en stijfheidsvereisten gelden, maar mensen komen op het idee dat gerecyclede vezels niet alleen gerecyclede vezels zijn met een zwak potentieel", zegt Benjamin Andrews, veldtechnicus. servicemonteur met ELG Carbon Fibre. “Het heeft zijn eigen voordelen die in sommige toepassingen superieur zijn aan nieuwe vezels. Drapeerbaarheid en oppervlakteafwerking zijn beide beter dan die van nieuwe vezels ... dit is niet alleen een herbruikbaar materiaal; dit is een materiaal dat zijn eigen voordelen heeft.”
Hoe zit het met auto's?
Als het op markten aankomt, lijkt de auto-industrie het meeste potentieel te hebben voor het gebruik van rCF. Het vermogen van het materiaal om lichtgewicht te combineren met een goede oppervlakteafwerking, maakt het een natuurlijke pasvorm voor carrosseriepanelen, om nog maar te zwijgen van verschillende interieurcomponenten. Commerciële leveranciers van rCF hebben lang met ingehouden adem naar de industrie gekeken, in de hoop op wijdverbreide acceptatie, maar een omslagpunt moet nog komen. Verwerkingstijd en kosten blijven struikelblokken voor de industrie.
Mark Mauhar, CEO van Carbon Conversions (Lake City, SC, VS), stelt dat deze zorgen een beetje een excuus zijn gezien de vooruitgang die is geboekt, en hij is van mening dat de belangrijkste belemmering voor acceptatie in welke markt dan ook in feite risicomijding is .
"Niemand wil de eerste zijn die een nieuw materieel ecosysteem adopteert", zegt hij. Hij benadrukt ook dat grootschalige adoptie van rCF door de auto-industrie niet noodzakelijkerwijs zelfs wenselijk is, en wijst erop dat adoptie door een tiental grote autoplatforms het wereldwijde aanbod van rCF snel zou kunnen verbruiken. Hij zegt dat de aanpak gericht moet zijn op nicheprogramma's, die op hun beurt de toeleveringsketen robuuster maken vanuit een zakelijk perspectief.
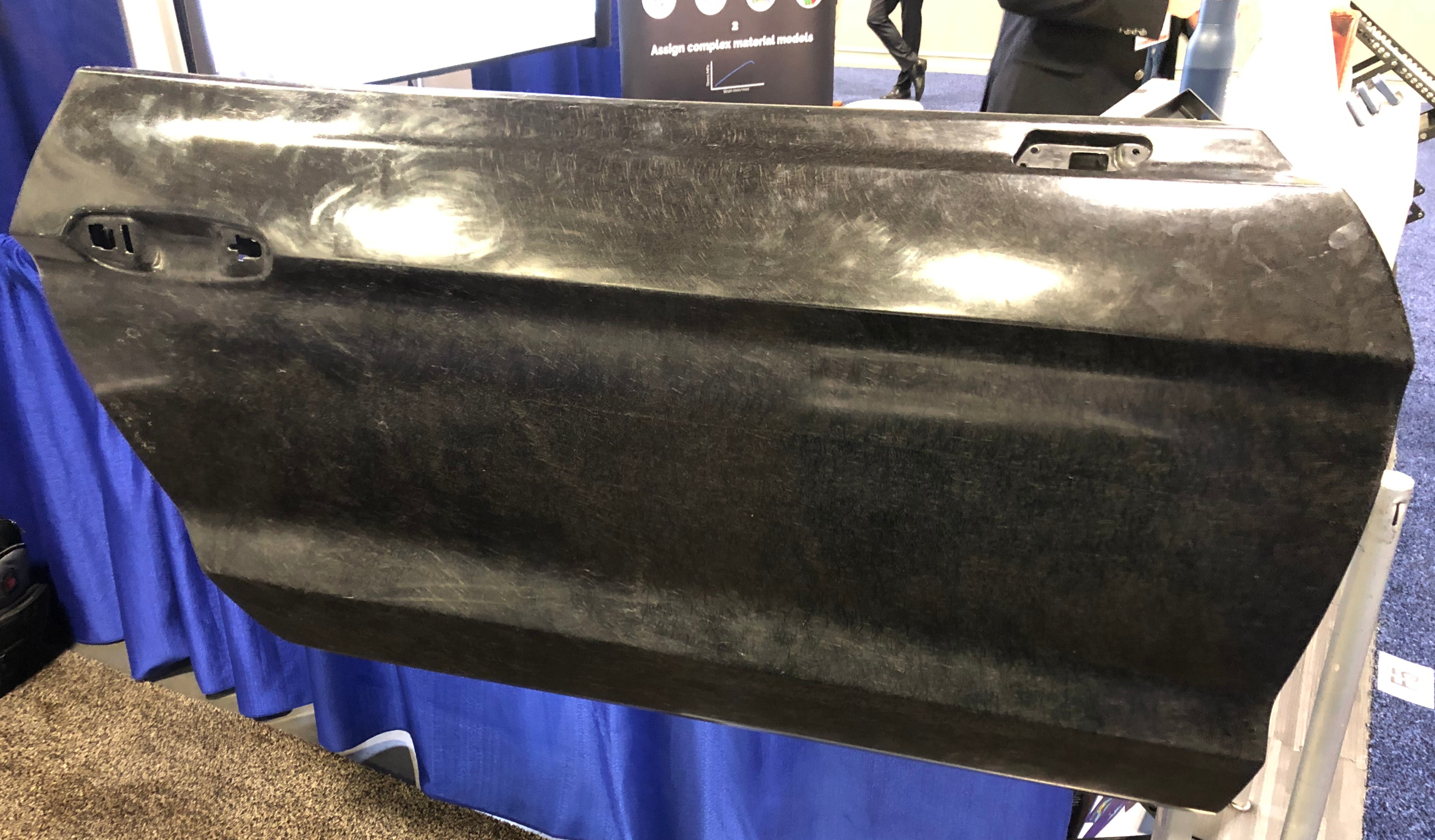
Autodeurpaneel gemaakt van prepreg gemaakt van Carbon Conversions' re-Evo MCF.
CW-foto | Scott Francis
"Het loont de moeite om slim te zijn over waar je het in de auto plaatst", zegt hij. "Specifieke onderdelen van specifieke automodellen kiezen die logisch zijn."
Mauhar heeft goede hoop dat de auto-industrie de eerste grote markt zal zijn die een behoorlijke fractie van de beschikbare gerecyclede koolstofvezel verbruikt. "In de komende 24 maanden zullen we daar wat beweging gaan zien", voorspelt hij.
Composieten vinden over het algemeen hun weg naar de auto-industrie stapsgewijs in de vorm van onderdelen zoals accukasten, drukvaten, bladveren en zelfs liftpoortsystemen. Het zou logisch zijn als rCF hetzelfde traject zou volgen.
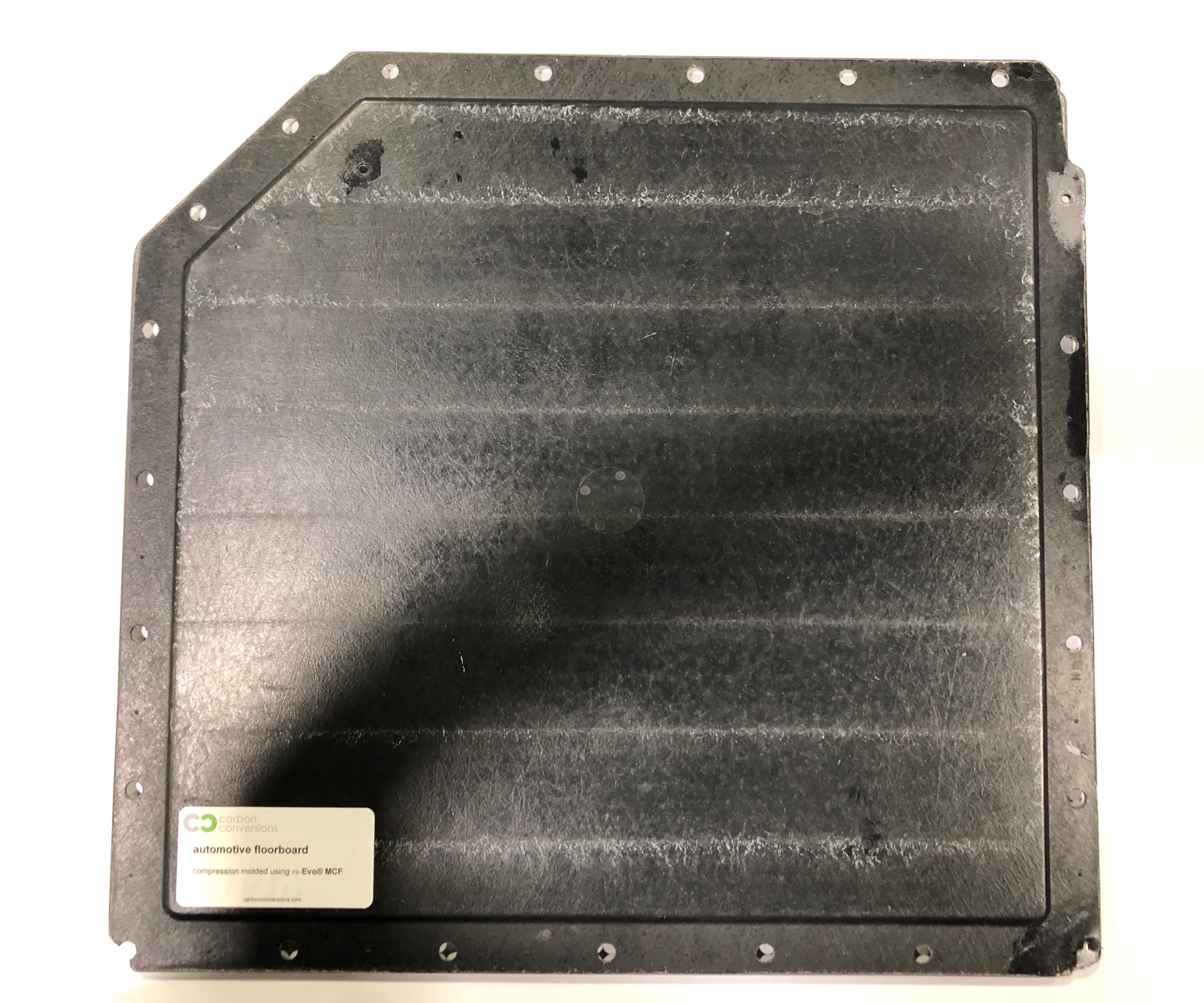
Deze geperste autovloerplaat maakt gebruik van de re-Evo MCF nonwoven mat van Carbon Conversions.
CW-foto | Scott Francis
Een interessant voorbeeld van een dergelijke nichebenadering is ProDrive Composites (Milton Keynes, VK), fabrikant van geavanceerde lichtgewicht composieten voor toepassingen variërend van auto- en motorsport tot ruimtevaart en defensie. Het bedrijf heeft samengewerkt met de University of Sheffield Advanced Manufacturing Research Center (AMRC, Sheffield, U.K.) en ELG Carbon Fiber aan zijn P2T (Primary To Tertiary)-proces, een nieuw proces dat een reactieve thermoplastische hars gebruikt voor de productie van recyclebare composietcomponenten. Een plastic monomeer wordt in de aanwezigheid van gerecyclede vezels met een katalysator omgezet om een uitgehard laminaat uit de autoclaaf te produceren.
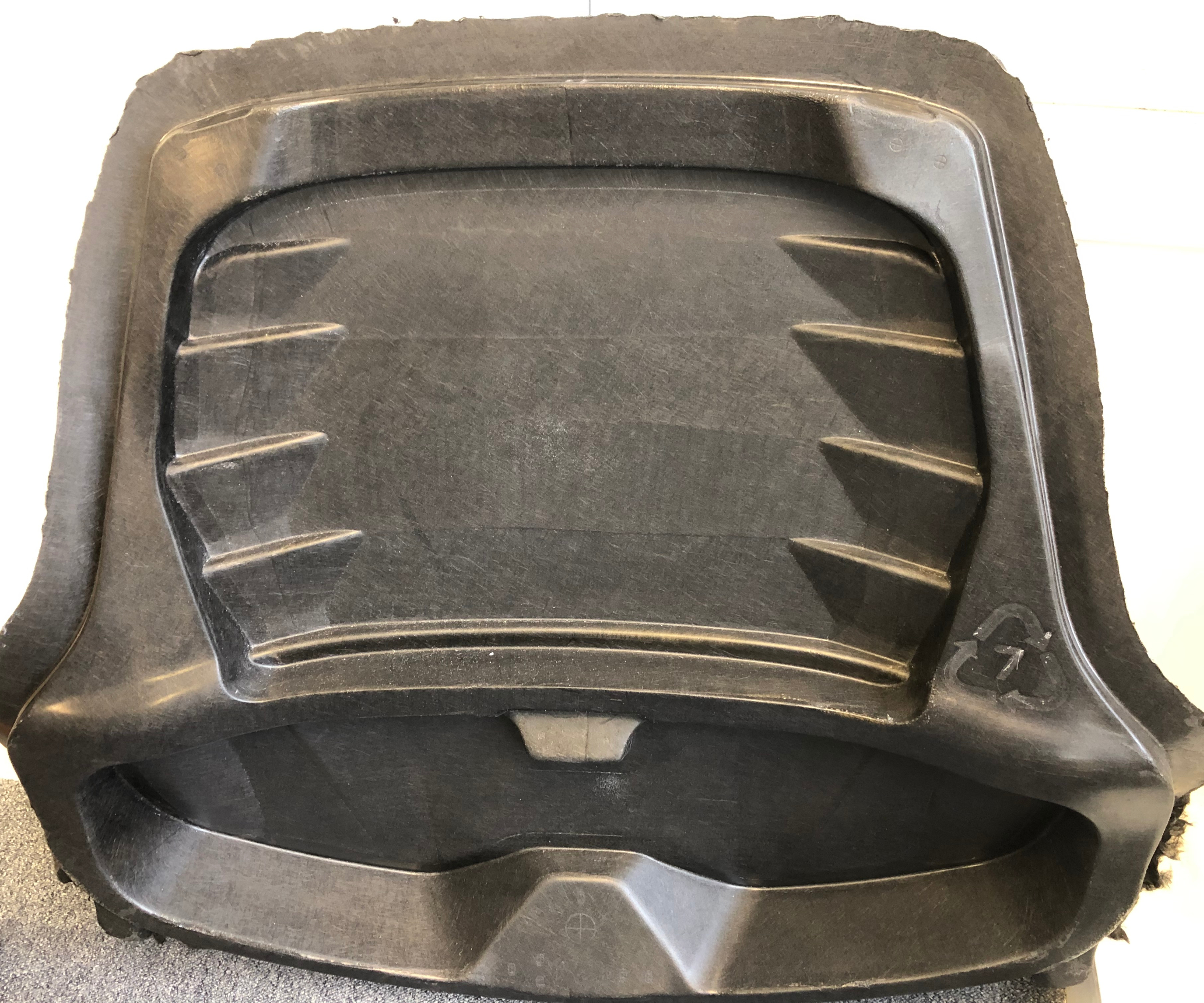
Voorbeeld van een tertiair onderdeel geproduceerd met ProDrive's P2T-proces.
CW-foto | Scott Francis
"[We] hebben aangetoond dat recyclebare composietpanelen kunnen worden geproduceerd tegen een tarief en tegen een prijs die geschikt is voor veel industrieën", zegt John McQuilliam, hoofdingenieur bij ProDrive Composites.
Het bedrijf zegt dat P2T toestaat dat een composietmateriaal drie of meer keer wordt gebruikt. Aan het einde van de levensduur van het primaire onderdeel kunnen de vezels en mogelijk de hars worden gerecycled, waardoor grondstof wordt geleverd voor een thermoplastisch secundair onderdeel, zoals een carrosseriepaneel. Wanneer dat onderdeel het einde van zijn levensduur bereikt, kan het worden gehakt en omgevormd tot nieuwe onderdelen. (Lees meer in het artikel "P2T-proces gepositioneerd voor recycling.")
Ondertussen leidt Vartega een project van het Institute for Advanced Composites Manufacturing Innovation (IACMI, Knoxville, Tenn., VS) gericht op de auto-industrie. De tweejarige technische samenwerking is bedoeld om de uitdagingen aan te gaan van het creëren van consistente, gerecyclede, met koolstofvezel versterkte thermoplasten voor gebruik in lichtgewichttoepassingen voor voertuigen. Maxey zegt dat het project vooruitgang boekt in de richting van een robuuste dataset die een volledige karakterisering van materialen biedt, van de vezelinterface tot de eigenschappen van afgewerkte onderdelen.
Als we kijken naar de auto-industrie, is het natuurlijk het beste om te wedden op gerelateerde opkomende technologieën. Elektrische voertuigen, autonome voertuigen en connectiviteitsaspecten in auto's brengen nieuwe onderdelen en toepassingsmogelijkheden waar composieten waarschijnlijk een grote rol zullen spelen.
Maxey geeft zijn beoordeling van waar de auto-industrie naartoe gaat:"Er is de afgelopen jaren veel gebeurd in de auto-industrie, waar de focus zal verschuiven van brandstofverbruik naar andere prioriteiten, afhankelijk van wat de regelgeving is en wat de [presidentiële] regering zegt,” zegt hij. "[We] zien geen grote terugval in lichtgewichten, maar misschien evolueert de motivatie ervoor. Ik denk dat wat je in de industrie zult zien, de focus is op lichtgewichten voor mobiliteitstoepassingen.”
Kan de ruimtevaart de cirkel sluiten?
De lucht- en ruimtevaartindustrie genereert het meeste koolstofvezelafval, en commerciële rCF-leveranciers kijken vaak naar de lucht- en ruimtevaartindustrie als een bron voor recyclaat. Overtollig materiaal, meestal niet-uitgeharde thermohardende composiet prepreg, wordt verzameld en de hars wordt verwijderd via warmte (pyrolyse) of een chemisch oplosmiddel (solvolyse) om vezels te verkrijgen die worden gemalen, gehakt of gepelletiseerd.
Naarmate de industrie steeds meer gebruik maakt van thermoplastische composieten (TPC's), biedt dat materiaal een nieuwe reeks recyclingmogelijkheden. Omdat thermoplastische polymeren kunnen worden omgesmolten en omgevormd, heeft de lucht- en ruimtevaartindustrie meer mogelijkheden om een deel van haar eigen schroot opnieuw op te nemen in secundaire toepassingen, waarbij mogelijk zowel vezels als matrix worden hergebruikt. Thomas de Bruijn, onderzoeker bij het Thermoplastic Composites Application Center (TPAC, Enschede, Nederland) - een R&D-centrum voor thermoplastische composieten dat samenwerkt met het Thermoplastic Research Centre (TPRC, Enschede, Nederland) op toegepast onderzoeksniveau - wijst op inspanningen in de industrie gemaakt om het materiaal intern te recyclen.
"Vanuit het oogpunt van haalbaarheid is voor thermoplastische composieten een interne aanpak veel logischer", zegt hij.
Volgens De Bruijn zijn vliegtuig-OEM's eerder geneigd om intern te recyclen dan zich te wenden tot een commerciële leverancier van rCF. De belangrijkste reden hiervoor is de traceerbaarheid. Het matchen van polymeertypes aan een bepaalde toepassing wordt veel moeilijker wanneer de aanvoer naar het buitenland wordt verplaatst.
Johan Meuzelaar, engineering stress specialist bij GKN Fokker (Hoogeveen, Nederland), denkt dat het antwoord is om te proberen zoveel mogelijk toepassingen te vinden binnen je eigen productieomgeving. "Als ik kijk naar het soort thermoplastische componenten dat we maken van nieuw materiaal, dan zitten er veel onderdelen in die we zouden kunnen recyclen", zegt hij. "[We zouden] zeker een aanzienlijke hoeveelheid afval kunnen gebruiken die we genereren."
"We hebben de faciliteiten al", voegt Guillaume Vincent, ingenieur thermoplastische composieten bij het TPRC, toe. Hij legt uit dat interne recycling binnen de normale procesketens past en dat het merendeel van de apparatuur al aanwezig is, waardoor dit de meest betaalbare optie is. "[Het] past in activiteiten die we hebben in een normale productieomgeving."
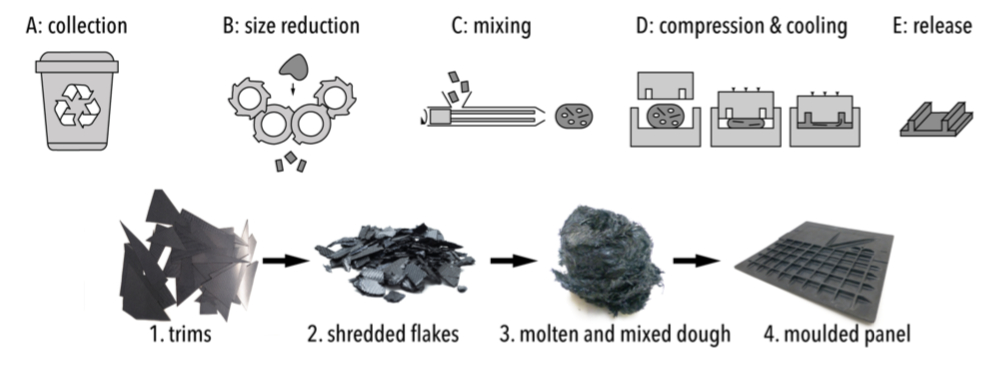
Bron | TPRC, TPAC
De Bruijn, Vincent en Meuzelaar zijn betrokken bij het TPC-Cycle project van TPAC en het TPRC. Het project is gericht op het hergebruik van productieschroot van de verwerking van thermoplastische composieten voor ruimtevaart en grootschalige toepassingen. Het doel is om de hoge mechanische eigenschappen van thermoplastische composieten te behouden en de algehele milieu-impact tegen een betaalbare prijs te verminderen. De TPC-Cycle heeft korte cyclustijden en zou de productie van complexe vormen mogelijk maken.
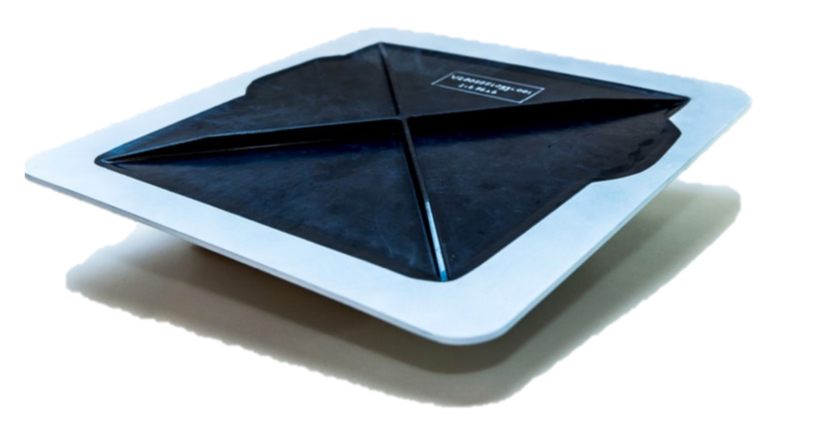
Demonstratortoegangspaneel voor helikopters ontwikkeld met behulp van het TPC-Cycle-proces.
Bron | TPRC, TPAC, GKN Fokker
Verschillende industriële partners, waaronder GKN Fokker, Toray Advanced Composites (Morgan Hill, Cali., VS; Nijverdal, Nederland), Cato Composite Innovations (Rheden, Nederland), Dutch Thermoplastic Components (Almere, Nederland) en Nido RecyclingTechniek (Nijverdal, Nederland) , zijn betrokken bij het TPC-Cycle-project, dat verschillende segmenten in de waardeketen vertegenwoordigt, van materiaal, fabricage, ontwerp en toepassing.
Volgens de Bruijn onderzoekt het TPC-Cycle-project nu het voltooien van kostenanalyses en levenscyclusanalyses om te bewijzen dat het proces economisch voordelig is.
Daarnaast stimuleren programma's zoals de gemeenschappelijke onderneming Clean Sky 2 (die wordt gefinancierd door het Horizon 2020-programma van de EU) O&O gericht op het sluiten van de kringloop voor ruimtevaartschroot. OEM's kijken naar de mogelijkheden om gerecycled fabrieksafval te gebruiken voor interieuronderdelen, toegangspanelen, kleine componenten en zelfs clips voor casco's en systeembeugels.
Dr. Bas Veldman, GKN Fokker-programmamanager voor de onderste helft van een thermoplastische multifunctionele rompdemonstrator, bevordert dit concept door een oproep tot het indienen van voorstellen in het kader van het Clean Sky 2-programma over clips en beugels te lanceren. Een belangrijk element in de ontwikkeling van de demonstrator is het verminderen van de impact op het milieu door het gebruik van fabrieksafval voor producten als frameclips en beugels. De demonstrator is ook bedoeld om bevestigingsmiddelen te vervangen door lassen, waardoor materialen, energie en kosten worden bespaard en tegelijkertijd wordt bijgedragen aan lichtgewicht.
Volgens Meuzelaar onderzoekt GKN Fokker hoe recyclingtechnologie onderdeel kan zijn van het romp van morgen-concept van het bedrijf. Hij zegt dat het concept mogelijk veel thermoplastische composieten zal gebruiken, wat op zijn beurt veel afval kan genereren dat kan worden gebruikt voor gerecyclede beugels, fittingen en niet-structurele onderdelen.
"De reden om naar een thermoplastische romp te kijken, zijn de kosten, en we denken dat dit een kosteneffectieve productiemethode is, die ook recycling omvat", zegt hij.
Meuzelaar zegt dat het doel op hoog niveau is om meer betaalbare en duurzamere producten in de lucht- en ruimtevaart te maken. Hoewel er stappen worden gezet in de richting van serieproductie in thermoplasten, levert dit ook afval op (zoals helaas het geval is voor composieten in het algemeen). Maar hij gelooft dat afval commercieel levensvatbaar kan zijn en zegt dat het mengen/persen met lage afschuifkrachten van TPC's van gerecyclede koolstofvezel ontwerpvrijheid biedt die niet wordt geboden door traditioneel lamineren met continue vezels. "Je krijgt veel extra opties om zeer interessante niet-structurele onderdelen te maken, zoals panelen, kleine stroomlijnkappen of systeembeugels die meestal in de ruimtevaart de neiging hebben om overmatig ontworpen te zijn in termen van gebruikte materialen, gebruikte legeringen en de gebruikte productiesystemen", hij legt uit.
Hij gelooft dat de kans vooral ligt in niet-structurele onderdelen van gemiddelde grootte en gemiddelde complexiteit, die nog steeds een aanzienlijk deel uitmaken van de totale kosten van de grotere componenten.
“Van gerecycled thermoplast gaan we de komende tijd geen vleugels maken”, zegt Meuzelaar. "Maar aan de binnenkant van de vleugel kunnen we onderdelen maken die economisch zinvol zijn."
Dat gezegd hebbende, is het een beetje ver weg om te voorspellen welke impact thermoplastische composieten zullen hebben op de recyclingindustrie.
"Het afvalpercentage zal waarschijnlijk afnemen door nieuwe productiemethoden zoals het plaatsen van tape of op maat gemaakte blanco's, die waarschijnlijk minder afval produceren dan de huidige typische nest- en stempelvormingsprocessen die we zien", zegt de Bruijn. "Maar over het algemeen denk ik dat er de komende jaren en decennia meer thermoplastisch afval.”
En hoewel deze belangstelling voor intern recyclen toeneemt, zal er altijd wat afval zijn dat niet bruikbaar is en dat fabrikanten niet in-house willen of kunnen recyclen. In dergelijke gevallen kunnen die materialen worden teruggewonnen door een materiaalleverancier. De tijd zal leren wat het toegenomen gebruik van thermoplastische composieten kan betekenen voor de supply chain. (Lees meer over het TPC-Cycle-project en het Clean Sky 2-initiatief in 'Gerecycleerde thermoplastische composieten voor productie'.)
Additieve fabricage
Additive manufacturing is een ander gebied dat potentieel heeft voor rCF. Shocker Composites heeft bijvoorbeeld zijn gerecyclede koolstofvezel gecompoundeerd tot 20-40% versterkt ABS-filament en het succesvolle gebruik ervan aangetoond met Cincinnati Inc.'s (Harrison, Ohio, VS) Big Area Additive Manufacturing (BAAM) 3D-printproces.
Daarnaast zegt Vartega dat het gebruik maakt van zijn koolstofvezelrecyclingtechnologie en expertise op het gebied van materiaalontwikkeling om polymeergrondstoffen te verbeteren voor de productie van additieven voor poederbedfusie. Het bedrijf heeft onlangs een National Science Foundation (NSF, Alexandria, Va., U.S.) Small Business Innovation Research (SBIR)-subsidie gekregen om onderzoek en ontwikkeling (R&D) in het gebied uit te voeren.
Vartega beweert ook een proces te ontwikkelen waarmee thermoplastische poeders kunnen worden versterkt met koolstofvezel, terwijl ervoor wordt gezorgd dat de materialen functionele onderdelen produceren in infraroodadditievensystemen. Deze vooruitgang zal naar verluidt digitale fabrikanten in staat stellen om het volledige potentieel van nieuwe op poeder gebaseerde hardwareplatforms te realiseren om onderdelen te produceren die vergelijkbaar zijn met spuitgegoten materialen bij middelgrote productiesnelheden.
"Door met koolstofvezel versterkte polymeerpoeders aan te bieden, zullen fabrikanten in sectoren zoals UAV [onbemande luchtvaartuigen] en medische protheses de voordelen van snel, complex en op maat gemaakt 3D-printen realiseren, terwijl ze ervoor zorgen dat hun materiaalkeuze de structurele integriteit vertoont die vereist is voor hun product”, zegt Alice Havill, chief operating officer bij Vartega.
Andere toepassingen
Ondertussen blijven andere markten en toepassingen ontstaan waarin gerecyclede koolstofvezel een rol kan spelen.
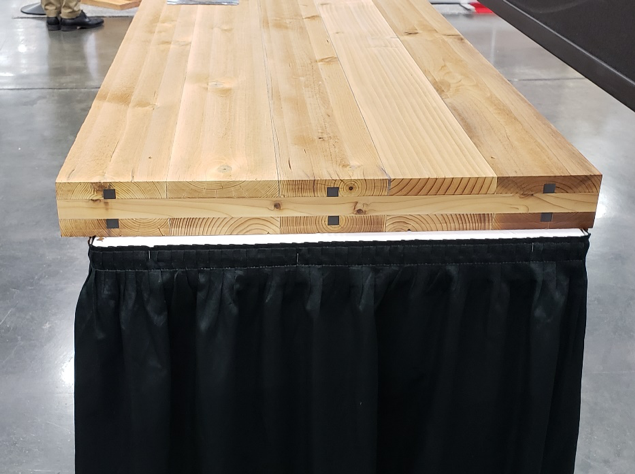
Dit cross-laminated hout (CLT) van constructiekwaliteit combineert thermisch gemodificeerd hout met gerecyclede koolstofvezel van het Composite Recycling Technology Center.
Bron | Het technologiecentrum voor composietrecycling
The Composite Recycling Technology Center (CRTC, Port Angels, Wash., U.S.) has been exploring use of recycled carbon fiber in a variety of products, from park benches to high-performance sporting goods to composite tubing. The company works with reclaimed uncured prepreg material from Toray Composite Materials America (Tacoma, Wash., U.S.) as well as rCF from ELG Carbon Fibre.
Dave Walter, CEO of the CRTC, points to the construction industry as an area of potential growth. The company recently developed a construction grade cross-laminated timber (CLT) under a patent-pending process that combines thermally modified lumber with recycled carbon fiber. The thermal modification process cooks off the sugars and lignin, providing rot and termite resistance, and then carbon fiber strips are integrated for strength.
The CRTC also uses recycled carbon fiber to create panels bonded with wood veneer. These panels showcase the beauty of wood with a strong, light and flexible substrate for various interior and exterior applications, as shown in the picture below from a 2019 installation at the Benaroya Hall in Seattle.
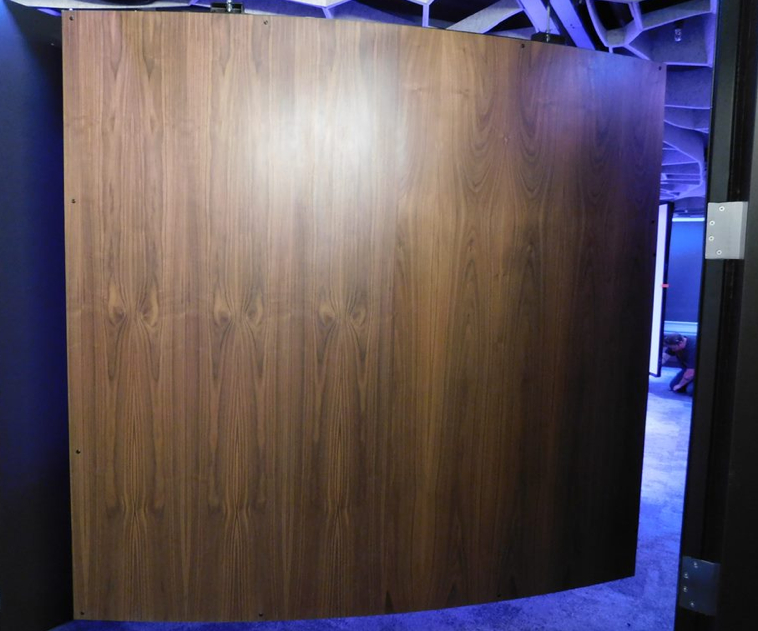
Octave 9 Raisbeck Music Center – Benaroya Hall (Seattle, Wash., U.S.)
Photo | The Composite Recycling Technology Center
A mind change for the industry?
Big changes often happen incrementally, and the relatively young recycled carbon fiber industry continues to slowly push forward. While downcycling of rCF continues, perceptions about the material are beginning to change. Quality of fiber has been proven and processes continue to evolve. Awareness of the necessity to recycle carbon fiber is high and more players are getting involved.
“The ELG and Boeing announcement was a really big deal; it helps everyone move the ball forward [and] to accelerate the supply chain connections,” says Maxey.
“We’re here to enable and connect the dots,” he adds, summing up the industry. “We have this enabling technology that sits in the middle of the supply chain, but its really about connecting that stranded asset in the waste stream to an unmet demand downstream.”
The biggest change, according to Mark Mauhar of Carbon Conversions, is that suppliers now want to be part of the solution. “Prior to two years ago we’d get multiple calls a week from suppliers about getting rid of scrap, but no interest in using the material,” he says. “Now, people are starting to walk the walk. Only recently, we are finally starting to see potential customers of reclaimed carbon fiber spend significant resources in cutting molding tools, building prototypes and mock-ups, solving process issues — all activities that are well down the line in terms of commercial adoption.”
Perhaps what it really boils down to is patience. Detlef Drafz, CEO at ELG Carbon Fibre, points out that it’s helpful to examine the recycling history for other legacy materials.
“For over 50 years, ELG has recycled raw materials for the stainless steel industry. With metal, it’s accepted that you use the scrap even in vacuum furnaces for turbine blades … it’s accepted that recycled metal is a raw material, which properly processed can just be used. That wasn’t common in the aerospace application 25 years ago; however, we established a supply chain in order to give the guarantees that the material performs. We do the same here,” he says.
Hars
- Koolstofvezel
- Hoe de medische industrie koolstofvezel gebruikt
- De voordelen van koolstofvezel in de luchtvaartindustrie
- Glasvezel versus koolstofvezel:wat zijn de verschillen?
- De top 5 van koolstofvezelgebruik in de sport
- De kosten van koolstofvezel:waarom de kwaliteit de moeite waard is
- De bestverkopende voordelen van bagage van koolstofvezel
- De voor- en nadelen van koolstofvezelringen
- Koolstofvezelinnovaties in de medische industrie
- Kan koolstofvezel worden gerecycled?
- Introductie van 's werelds eerste koolstofvezel smartphone