Industriële productielijn voor het recyclen van thermoplastische polymeren en composieten tot organoplaat
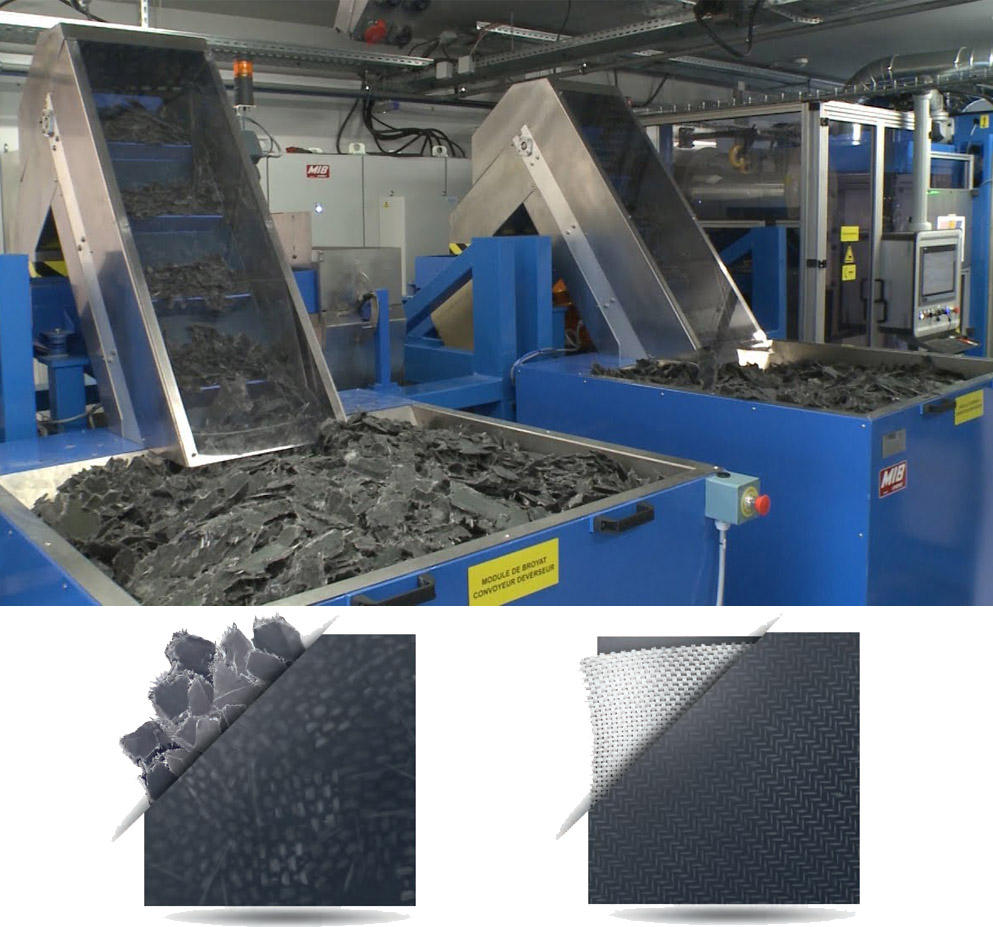
Cetim (Nantes, Frankrijk) staat al bekend om zijn QSP (Quilted Stratum Process) voor geïndustrialiseerde productie (<1 minuut cyclustijd) van thermoplastische composietonderdelen, en ook om zijn QSD (Quilted Stratum Design)-software die dergelijke onderdelen optimaliseert , inclusief het hergebruiken van productieschroot in het onderdeel. De derde technologie is een modulaire productielijn voor het omzetten van thermoplastisch schroot met en zonder vezelversterking in organoplaatpanelen met gewenste eigenschappen en kosten.
Pilotlijn bij Cetim Grand Est
Dit recyclingproces van thermoplastisch composiet is ontwikkeld door Cetim Grand Est (Mulhouse, Frankrijk). Opgericht in 1977 als Cetim Cermat, fuseerde het in 2018 met CRITT Matériaux Alsace om technologische ondersteuning te bieden aan bedrijven in de Elzas-Lotharingen en de Champagne-Ardenne-regio's van Frankrijk. "Cetim Grand Est is verantwoordelijk voor recyclingtechnologieën voor polymeren en thermoplastische composieten", legt Clément Callens uit, business unitmanager bij Cetim Grand Est voor het in Mulhouse gevestigde Industry of the Future-team, inclusief projecten voor thermoplastische processen en online monitoring. "We hebben vijftien mensen in deze divisie en werken samen met universiteiten en bedrijven uit een breed scala van industrieën, waarbij we interdisciplinaire teams creëren om uitdagende problemen op te lossen."
"De pilootproductielijn die we in Mulhouse hebben opgezet, is ontwikkeld om de wereld te laten zien dat dit innovatieve thermomechanische proces voor het recyclen van productieafval mogelijk is", vervolgt Callens. “Deze lijn is qua filosofie vergelijkbaar met QSP:een geautomatiseerd systeem dat flexibel en modulair is, waardoor bedrijven de technologie op een efficiënte en kosteneffectieve manier kunnen inzetten. We ontvangen eigenlijk schroot van de QSP-lijn in Nantes, of van andere klanten, en upcyclen het vervolgens tot verschillende organoplaatmaterialen en panelen, met als doel de integriteit van de composieten te behouden voor betere prestaties in vergelijking met traditionele materialen en traditionele gerecyclede composieten.”
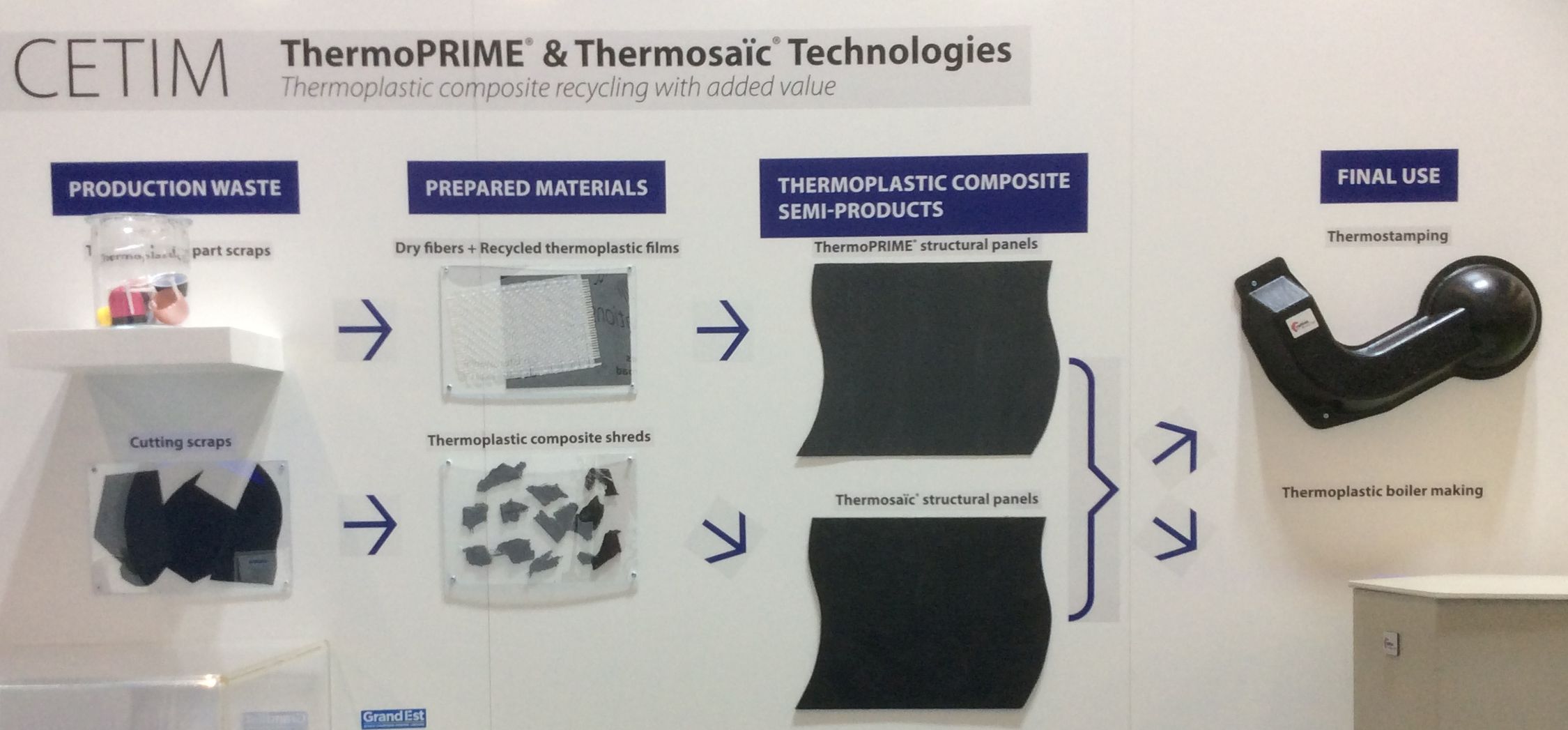
Thermosaïc en ThermoPRIME
De lijn combineert twee verschillende benaderingen:Thermosaïc en ThermoPRIME.
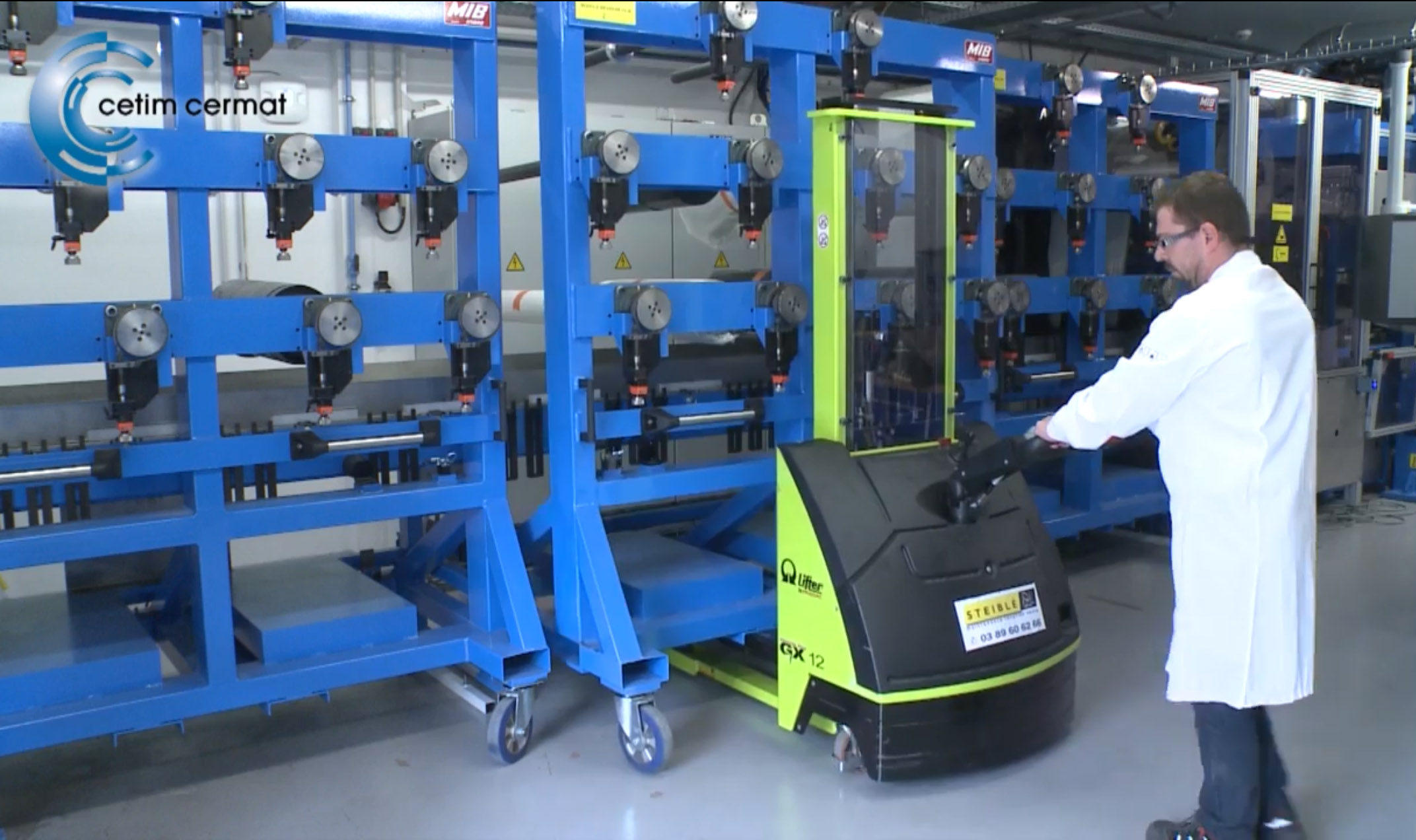
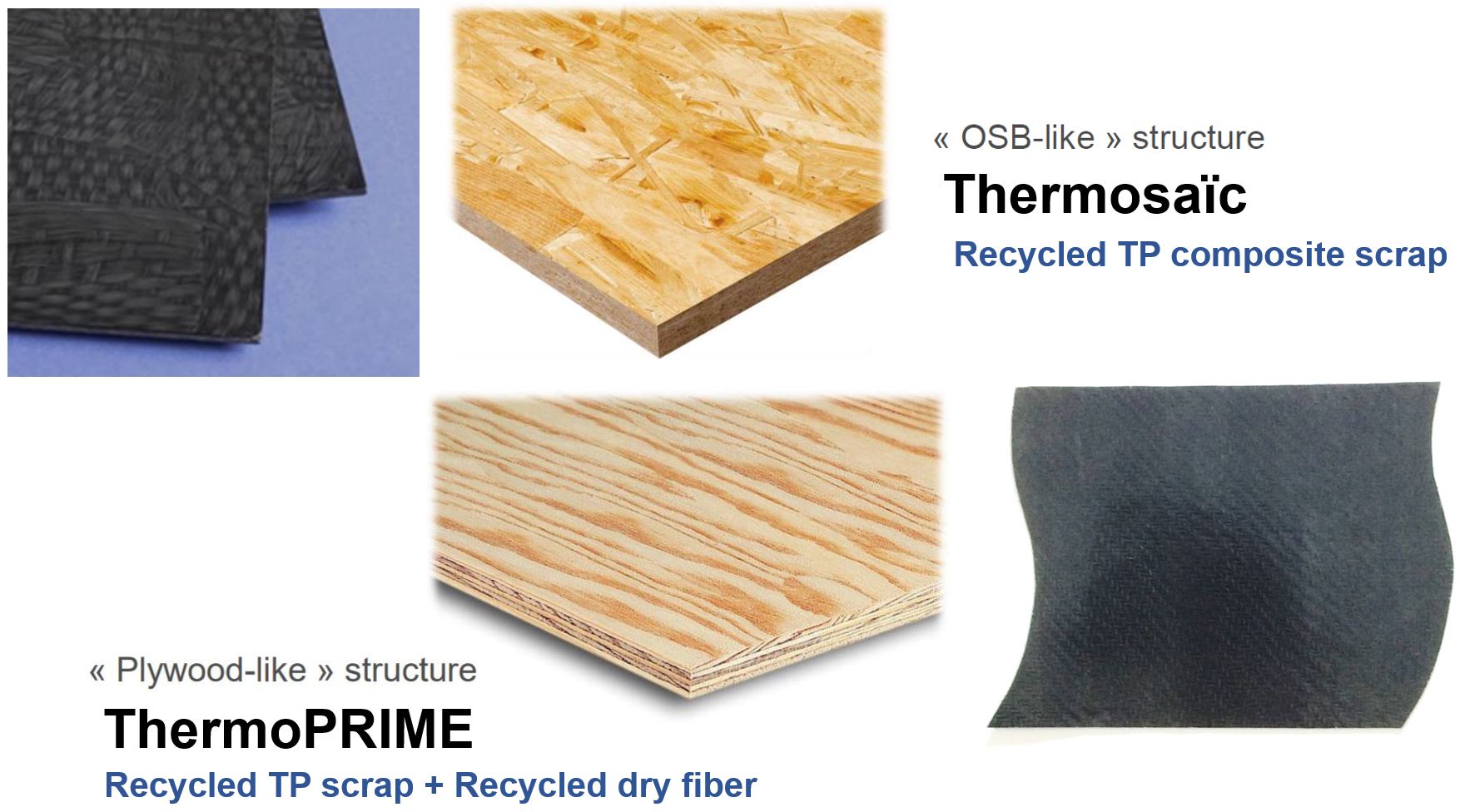
Thermosaïc neemt productieschroot van thermoplastisch composiet van het snijden en trimmen (of van afgedankte onderdelen), versnippert het grof en gebruikt vervolgens een thermomechanisch proces om de snippers om te zetten in organoblad. "We noemen het een composiet structureel paneel", zegt Callens, "maar het is eigenlijk net organoblad." De term organoblad ontwikkeld in Europa om weefselversterkte thermoplastische prepreg, semipreg of preconsolidated blanks te beschrijven die thermogevormd en omgevormd kunnen worden tot composietonderdelen. Thermosaïsche producten zijn quasi-isotroop en de vezellengte wordt zo lang mogelijk gehouden om de mechanische eigenschappen te maximaliseren. "Ze zitten tussen de korte vezelplaat en de klassieke organoplaat in", merkt Callens op. “Het doel van de technologie is om een goed compromis te vinden tussen de snippergrootte en de eigenschappen van het paneel, omdat je prestaties altijd moet koppelen aan kosten. Het proces moet flexibel en kosteneffectief zijn, dat wil zeggen goedkoper dan nieuw materiaal.”
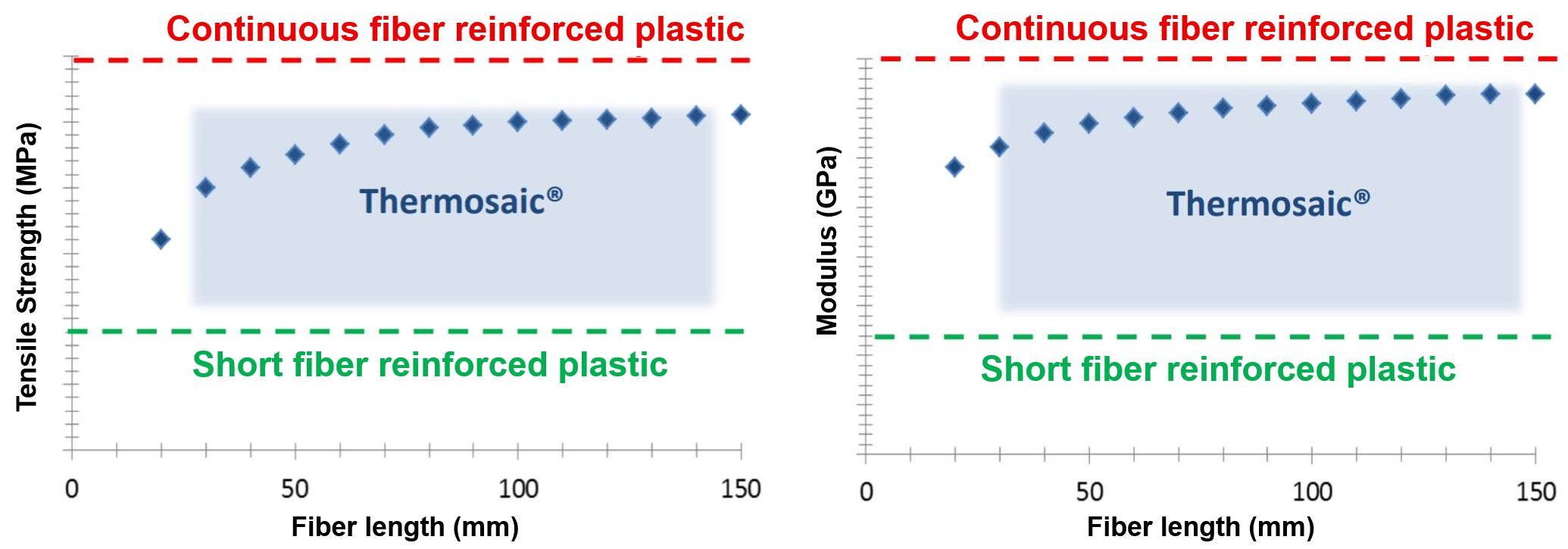
"We gebruiken dezelfde proceslijn om ThermoPRIME structurele panelen te maken", legt hij uit. “Het is hetzelfde basisconcept, maar in deze aanpak beginnen we met ongewapend thermoplastisch schroot of afgedankte onderdelen die zijn gerecycled tot folie. Er zijn al films op de markt die van verschillende materialen zijn gemaakt. Vervolgens voegen we nieuwe, natuurlijke, gerecyclede of andere droge continue vezels toe om een organoblad te produceren dat dezelfde eigenschappen heeft als nieuw materiaal, maar tegen lagere kosten. De vezelimpregnering maakt gebruik van een continu proces dat goedkoper is dan de batchverwerking van klassiek organoblad.”
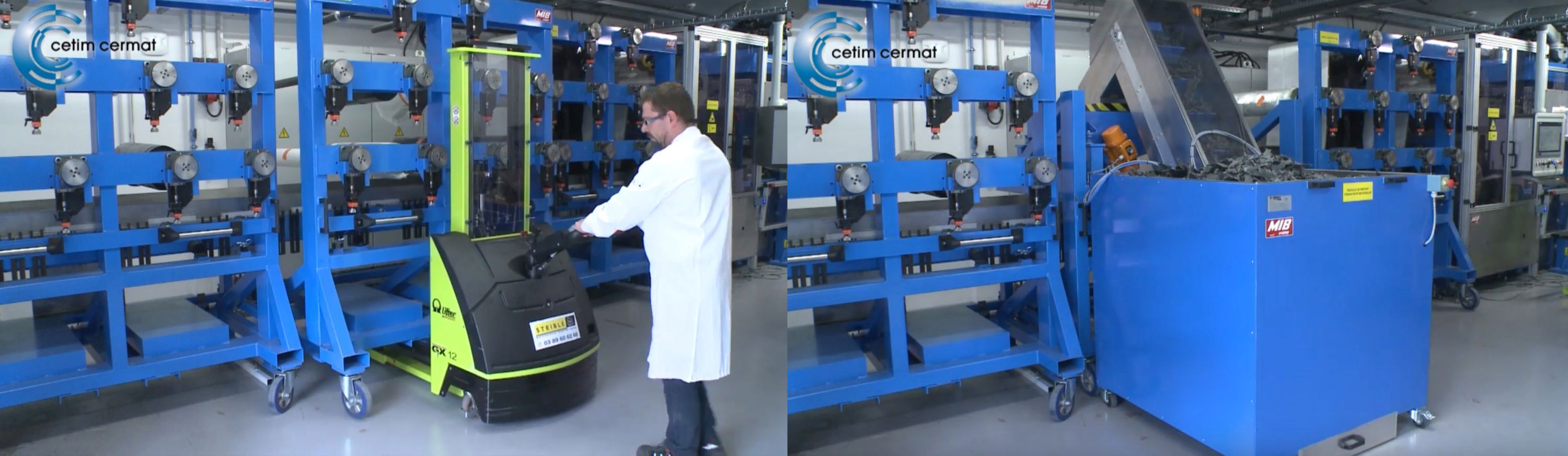
Demonstraties, kostenbesparingen en supply chain
Demonstraties tot nu toe hebben meer kostenbesparingen laten zien met hoogwaardigere thermoplasten zoals PEEK (polyetheretherketon) of PPS (polyfenyleensulfide) versus materialen zoals PP (polypropyleen), die al goedkoop zijn als nieuwe materialen. Naast deze polymeren heeft het team van Callens PA6 (polyamide6) verwerkt en verschillende soorten gerecyclede producten van glasvezelversterkt polymeer ontwikkeld, in samenwerking met bedrijven, bijvoorbeeld Porcher (Eclose-Badinières, Frankrijk), om produceren Thermosaïc- en ThermoPRIME-panelen. Het team werkt ook aan gerecyclede, met koolstofvezel versterkte polymeerpanelen.
Hoe ziet u de recyclingketen zich ontwikkelen? "We werken nu aan de overdracht van deze technologie aan de industrie, in samenwerking met Tier 1-leveranciers en materiaalfabrikanten", zegt Callens. “Cetim Grand Est werkt samen met de industrie om proof of concept en haalbaarheidsstudies te voltooien. Het werkt ook, in samenwerking met de partner van de machinefabrikant, om de lijn aan te passen aan de specifieke behoeften van klanten en samen met klanten om te helpen bij het definiëren van de optimale productiemodules en parameters.”
Thermosaïc en ThermoPRIME werden op JEC World 2018 erkend met de Innovation Award for Sustainable Development. Clément Callens zal naar verwachting op 12 mei meer details over deze technologie presenteren tijdens JEC World 2020 (Parijs, Frankrijk).
Hars
- BASF en Toray in leveringsovereenkomst voor productie van CFRT-tapes voor auto- en industriële toepassingen
- Thermoplastische honingraatsandwich voor overmolding tot dunnere lichtgewicht composieten
- Recycling:continu-vezelversterkte thermoplastische composieten met gerecycled polycarbonaat
- Aanpassen van ultrasone sensoren voor procesoptimalisatie en controle van composieten
- OTOMcomposite ontwikkelt software voor de productie van Composites 4.0 met behulp van laserondersteunde tapeplaatsing en -wikkeling
- Herverwerkbare, herstelbare en recyclebare epoxyharsen voor composieten
- Karl Mayer lanceert productielijn voor thermoplastische UD-tapes
- Thermoplastische deur een primeur voor autocomposieten
- LANXESS breidt productiecapaciteit voor continue vezelversterkte thermoplastische composieten uit
- TPAC en TPRC ontwikkelen recyclingproces voor thermoplastische composieten
- Consortium thermoplastische composieten streeft naar productie in hoog volume voor Automotive en Aerospace