Lanxess, Kautex Textron verkennen D-LFT voor EV-batterijbehuizingen
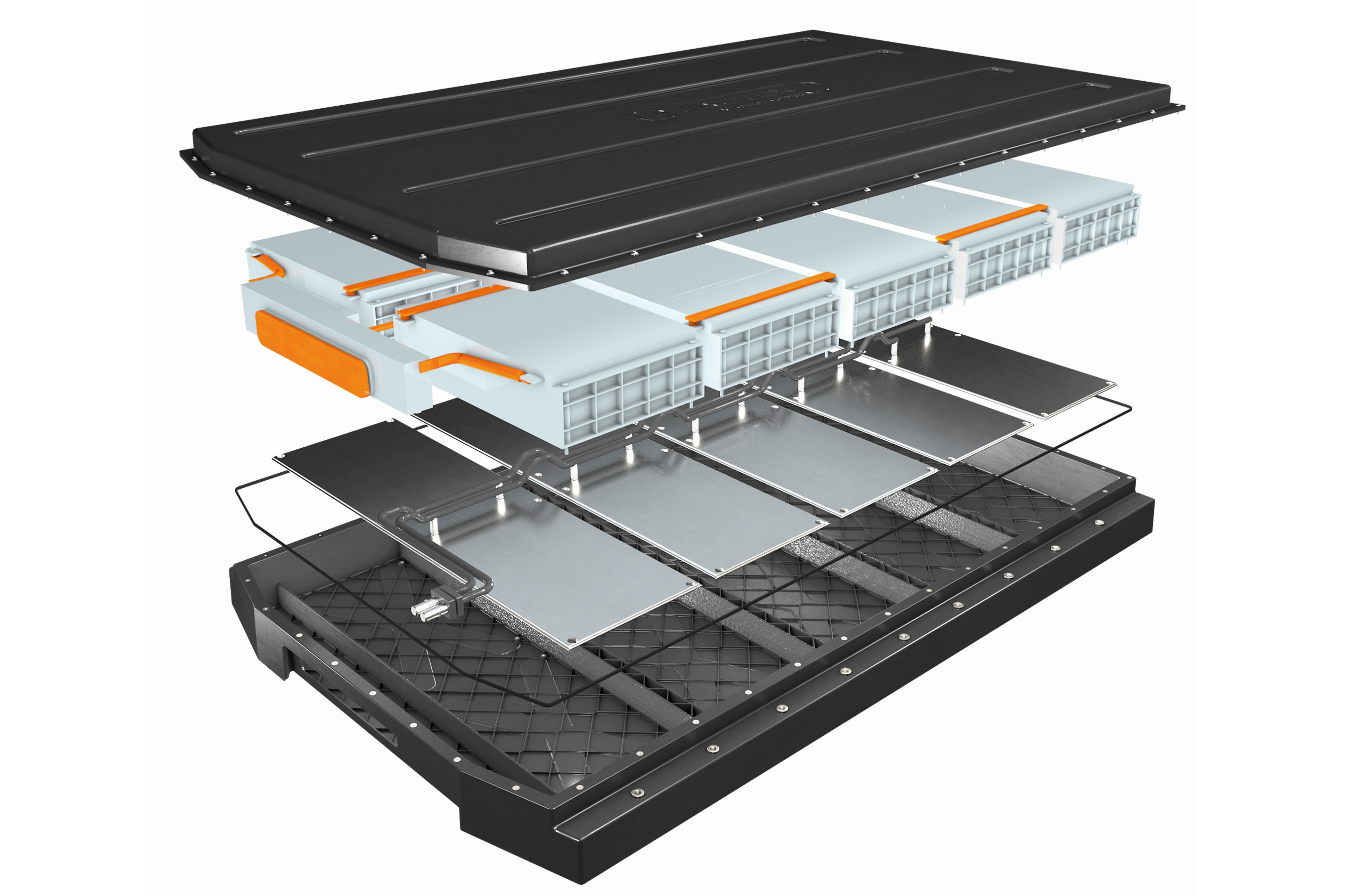
Speciaalchemiebedrijf Lanxess (Keulen, Duitsland) en Kautex Textron GmbH &Co. KG (Bonn, Duitsland), een bedrijf van Textron Inc. (Providence, RI, VS), werken al enkele jaren samen om de voordelen van technische thermoplasten ten opzichte van metalen in batterijbehuizingen voor elektrische voertuigen (EV's) in termen van gewichts- en kostenreductie, functionele integratie en elektrisch isolatiegedrag Samen hebben de bedrijven een bijna-serie technologiedemonstrator ontwikkeld in de haalbaarheidsstudie. Met een lengte en breedte van ongeveer 1.400 millimeter elk, is het systeem een groot formaat volledig plastic behuizingsonderdeel met een gewicht in het midden van de dubbele cijfers in kilogram.
"Als eerste stap hebben we volledig afgezien van het gebruik van metalen wapeningsstructuren, terwijl we bewijzen dat we deze complexe, grote componenten commercieel kunnen produceren", legt Felix Haas, directeur productontwikkeling bij Kautex Textron, uit. In de toekomst willen Kautex en Lanxess de resultaten van de samenwerking gebruiken om ontwikkelingsprojecten voor serieproductie aan te gaan met autofabrikanten.
De demonstrator is ontwikkeld op basis van de batterijbehuizing van een C-segment EV. Het bestaat uit een behuizingstray met crashstructuur, een behuizingsdeksel en een onderdoorrijdbeveiliging. De behuizingscomponenten kunnen worden geproduceerd in een ééntraps, direct langvezelig thermoplastisch (D-LFT) vormproces. Lanxess heeft zijn Durethan B24CMH2.0 PA6-hars geoptimaliseerd als materiaal voor de D-LFT-vormmassa; Kautex Textron vermengt de PA6 voor het proces met glasvezelrovings. Lanxess’ Tepex dynalite continu vezelversterkte thermoplast wordt toegepast als versteviging voor de behuizingsstructuur. "Het proces maakt kortere en dus zuinigere cyclustijden mogelijk dan de processen waarin staal of aluminium wordt verwerkt", legt Haas uit.
Vandaag de dag, zegt Lanxess, worden behuizingen voor hoogspanningsbatterijen voornamelijk gemaakt van geëxtrudeerde stalen of aluminium profielen. Afhankelijk van de voertuigklasse kunnen de lengte en breedte van de behuizing respectievelijk ruim 2.000 of 1.500 millimeter bedragen. De grootte, het aantal componenten en de talrijke fabricage- en montagestappen maken metalen behuizingen zeer kostenintensief. Zo vereisen complexe constructies gemaakt van strengpersprofielen veel secundaire werkstappen zoals lassen, ponsen en klinken. Bovendien moeten de metalen componenten in een extra processtap door kathodische dompelcoating tegen corrosie worden beschermd.
“Kunststoffen daarentegen kunnen hun ontwerpvrijheid ten volle benutten. Door functies zoals bevestigingsmiddelen en componenten voor thermisch beheer te integreren, kan het aantal afzonderlijke componenten van een batterijbehuizing aanzienlijk worden verminderd. Dit vereenvoudigt de montage en de logistieke inspanning, wat de productiekosten verlaagt”, zegt Dr. Christopher Hoefs, projectmanager e-Powertrain bij Lanxess.
Hoogspanningsbatterijbehuizingen moeten ook voldoen aan een aantal zeer hoge technische eisen, waaronder hoge stijfheid en sterkte, energieabsorptie bij een crash, vlamvertraging en integratie van de behuizingen in de voertuigstructuur, om er maar een paar te noemen. Lanxess meldt dat kunststoffen het potentieel hebben om aan veel van deze behoeften te voldoen. Het materiaal is corrosiebestendig en elektrisch isolerend, dit laatste zorgt voor een verminderde kans op kortsluiting in het systeem. De lage dichtheid van kunststoffen en hun potentieel voor lichtgewicht constructie leiden ook tot aanzienlijk lichtere behuizingen, wat onder andere het bereik van EV's ten goede komt.
“We blijven samenwerken aan het optimaliseren van de productie en het constructief ontwerp van de componenten. Het doel is om het grootste deel van het ontwikkelingswerk virtueel uit te voeren, om kosten te besparen bij het ontwerpen van prototypes en om de time-to-market van toekomstige seriecomponenten te verkorten”, zegt Hoefs.
Hars
- ISO 26262-certificering voor softwarecomponenten
- UL:testen van plastic componenten op ontvlambaarheid
- Plastic componenten:de weg vrijmaken voor auto-efficiëntie
- Glasgevuld PET voor exterieurcomponenten van auto's
- Lanxess voegt twee nieuwe productielijnen toe voor composietmateriaal Tepex
- Materialen:met lange vezels versterkte samengestelde verbindingen voor onderdelen van medische apparatuur
- Eigen TPE-verbinding voor hoogwaardige elektronische componenten
- Koolstofvezelversterkte PPA voor structurele auto- en elektronische componenten
- Lanxess biedt pigmentservice voor biologisch afbreekbare kunststoffen
- LANXESS breidt productiecapaciteit voor continue vezelversterkte thermoplastische composieten uit
- Materialen voor Invar 36-componenten