CSIRO:ontwikkeling van hoogwaardigere, sterkere en goedkopere koolstofvezels
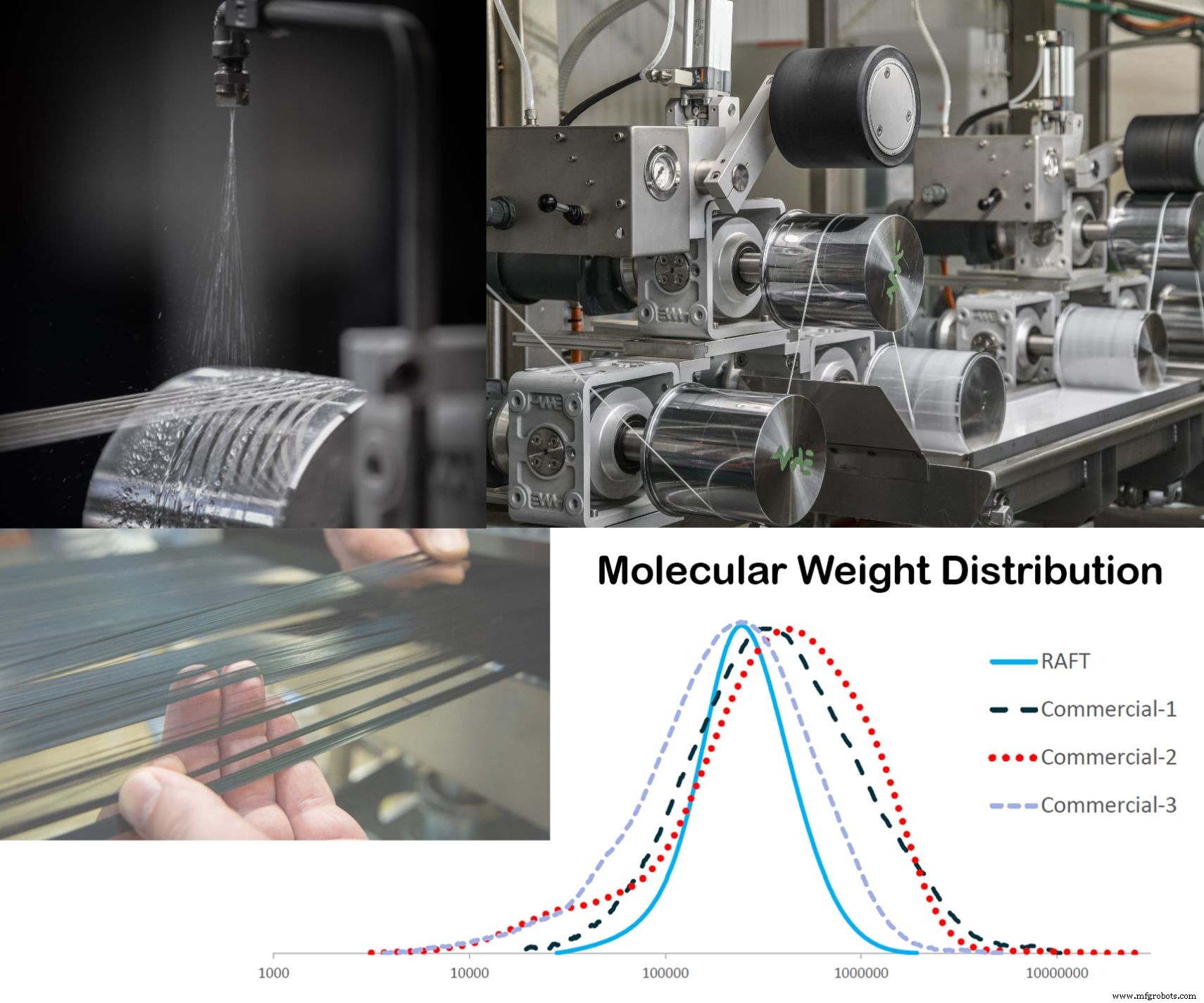
"CSIRO's werk is gecentreerd rond de eerste stappen in de productie van koolstofvezel, inclusief de polymerisatie van acrylonitril tot poly acrylonitril en vervolgens het spinnen en verder verwerken van PAN om een hoogwaardigere en goedkopere precursorvezel te produceren”, legt Abbott uit. PAN-productie is goed voor 50% van de kosten van koolstofvezel, maar 70-90% van de eigenschappen ervan. "De technologie van Deakin University omvat de laatste stappen in de productie van koolstofvezel, inclusief oxidatie en carbonisatie", vervolgt hij. "De technologie die ze in licentie hebben gegeven aan LeMond Composites (Oak Ridge, Tenn., V.S.) is bedoeld voor snelle oxidatie om de kosten van deze laatste stappen te verlagen."
Om zijn doelen voor koolstofvezel van de volgende generatie te bereiken, gebruikt CSIRO een reeks strategische hulpmiddelen:RAFT-polymerisatie, FLOW-chemieprocessen en CarbonSpec-metrologie. "Ons doel is om een koolstofvezel van ruimtevaartkwaliteit te produceren met 20% hogere sterkte", zegt Abbott, en hij merkt op dat het team tegen eind 2020 enkele eerste resultaten hoopt te hebben.
CSIRO koolstofvezelteam
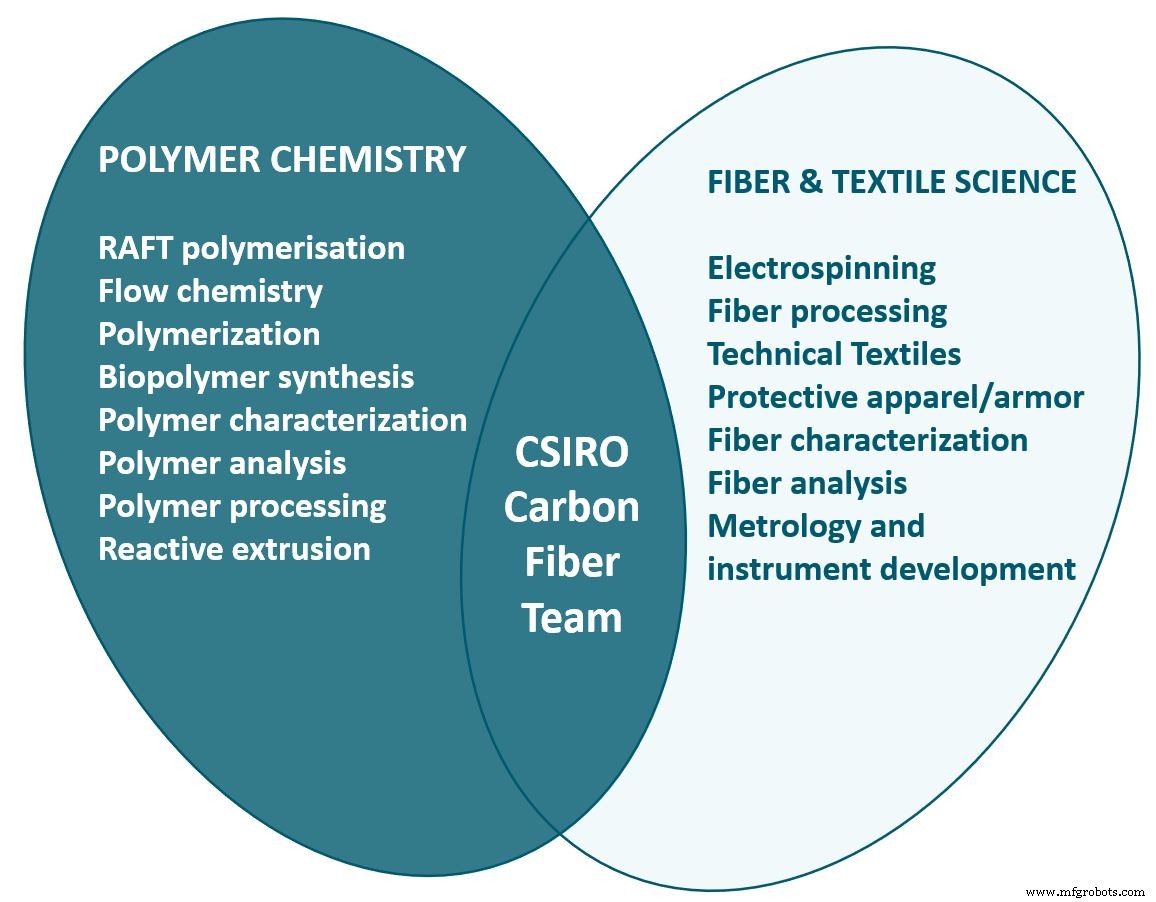
Met 5.000 medewerkers, 55 locaties, acht bedrijfseenheden en een budget van ongeveer $ 1 miljard, bestrijken CSIRO-projecten een breed scala aan onderwerpen - bijv. 3D-printen, biopolymeren, medische implantaten, slimme kleding, astronomie/ruimteverkenning - en omvatten meer dan 2800 partner per jaar. "CSIRO heeft Wireless LAN uitgevonden en gepatenteerd", legt Abbott uit, "en gebruikt die inkomsten om ander onderzoek te financieren."
Een van de 55 locaties bevindt zich in Silicon Valley, Californië. CSIRO US verbindt Australische onderzoekers met Amerikaanse projecten om wetenschappelijke vooruitgang te versnellen op gebieden als ruimtevaart, landbouw, waterbehoud, natuurbranden en slimme steden. Het doel is open innovatiepartnerschappen die diepgaande onderzoekscompetenties en ervaring met een breed scala aan echte problemen samenbrengen.
“In composieten ontwikkelt CSIRO nieuwe harsen en verwerkingstechnieken”, vervolgt hij. “We doen ook veel werk aan het modelleren van composieten en processimulaties en het meten van koolstofvezeleigenschappen. We hebben bijvoorbeeld nieuwe instrumenten ontwikkeld om de transversale modulus van koolstofvezel te meten, die we vervolgens invoeren om onze modellering en simulaties te verbeteren.”
"CSIRO heeft een strategische relatie van 30 jaar met Boeing", zegt Abbott. “In 2016 en 2017 werden we erkend als technologieleverancier van het jaar bij Boeing.” Het koolstofvezelteam van CSIRO werkt ook samen met de University of Southern Mississippi (Hattiesburg, Miss., V.S.).
Nat draaiende pilootlijn
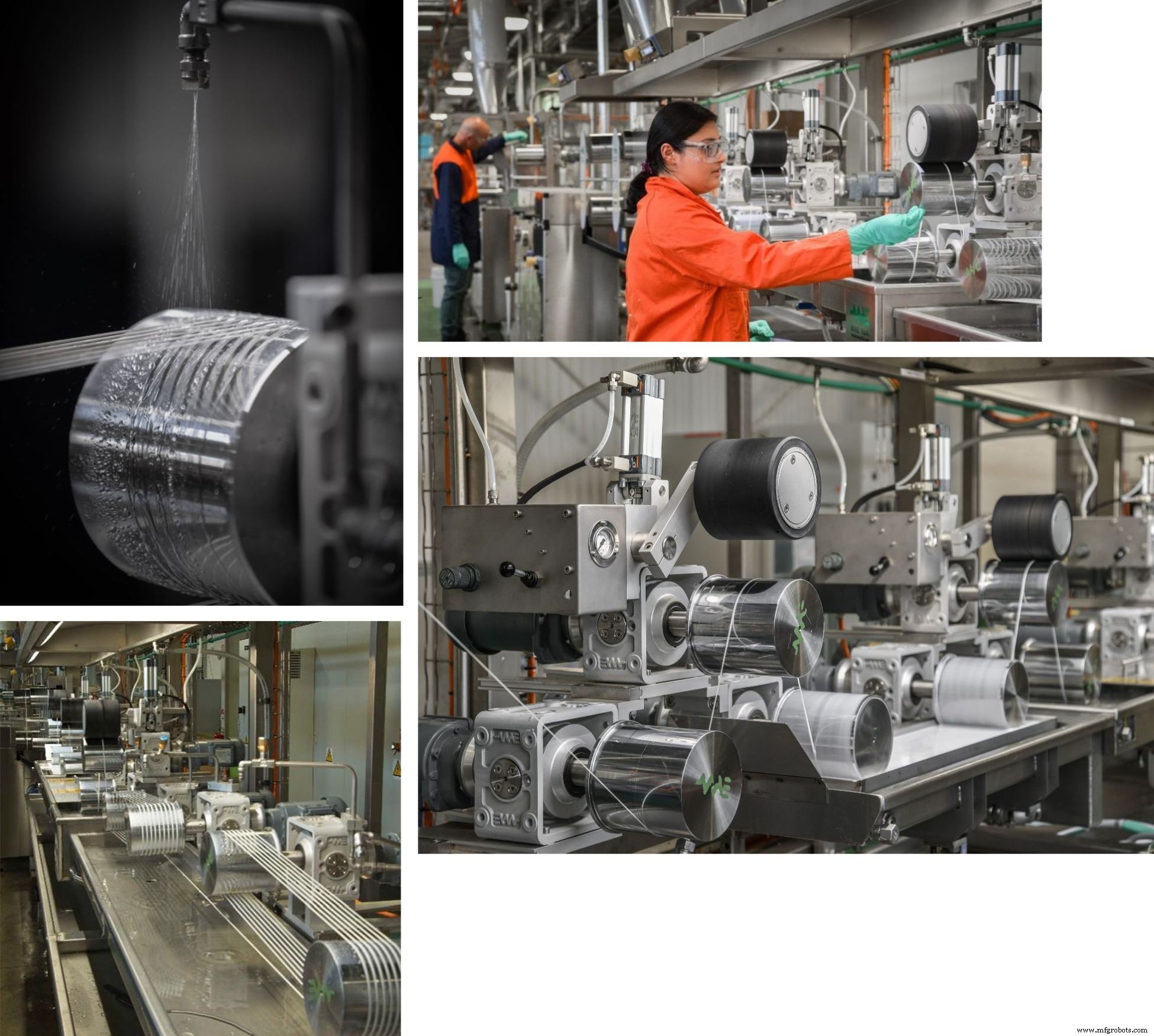
Om het nodige onderzoek naar koolstofvezelprecursoren af te ronden, moest CSIRO eerst een eigen natspinlijn opzetten. "Koolstofvezel wordt alleen gemaakt door een handvol fabrikanten over de hele wereld, die elk hun eigen geheime, gepatenteerde recepten hebben", verklaarde CSIRO-topman Dr. Larry Marshall bij de lancering van de nieuwe lijn in 2017. De pilootlijn is op maat gebouwd door MAE (Fiorenzuola d'Arda, Italië), een machinefabrikant die gespecialiseerd is in procesapparatuur voor polymeren en vezels. "Het is ontworpen als een commerciële lijn, maar op kleinere schaal", legt Abbott uit.
In een CSIRO-blog wordt de werking van de lijn beschreven aan de hand van de analogie van het maken van pasta. Net als deeg dat wordt gebruikt om pasta te maken, wordt een polymeeroplossing genaamd dope gebruikt om PAN-precursorvezels te spinnen. Net zoals pastadeeg wordt gekneed en vervolgens door een matrijs wordt geperst om lange, dunne strengen spaghetti te maken, wordt dope gemengd en vervolgens gecoaguleerd en door een spindop met meerdere gaten gesponnen om 500 tot 12.000 afzonderlijke strengen PAN-vezel te produceren - allemaal fijner dan mensenhaar . Deze vezels worden gewassen, op rollen gespannen, gestabiliseerd in een reeks oplossingen, gestoomd en gedroogd voordat ze worden gespoeld voor de carbonisatielijn bij Carbon Nexus.
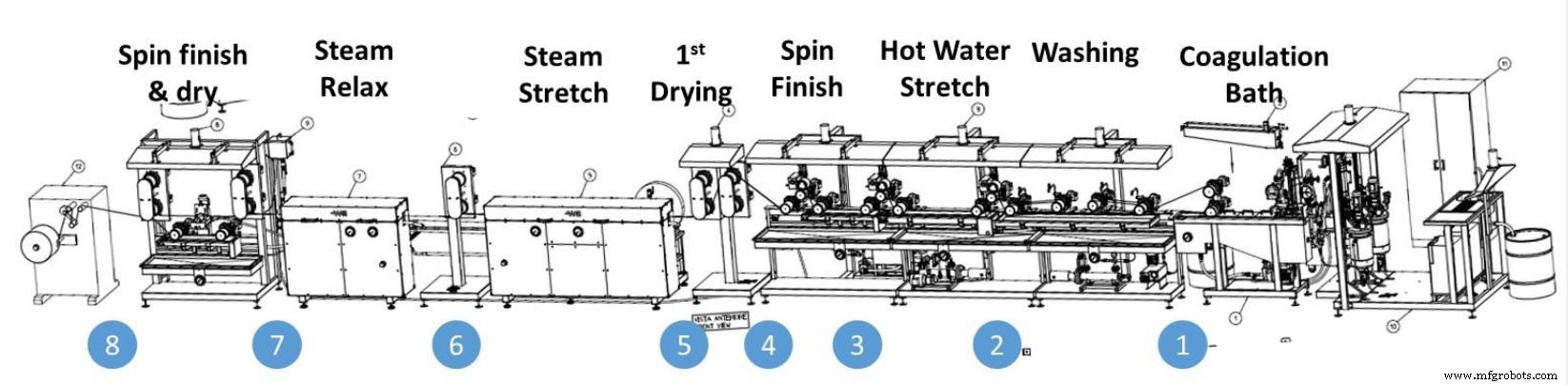
"Het heeft ons veel tijd gekost om volledig te begrijpen hoe we koolstofvezel en de grondstof voor precursoren kunnen maken", zegt Abbott. “Niemand wilde ons echt helpen, dus we moesten het grotendeels alleen leren. Nu hebben we echter volledige controle over het voorloperproces, wat essentieel is, en dan werken we met Carbon Nexus voor de carbonisatie.”
RAFT-polymerisatie
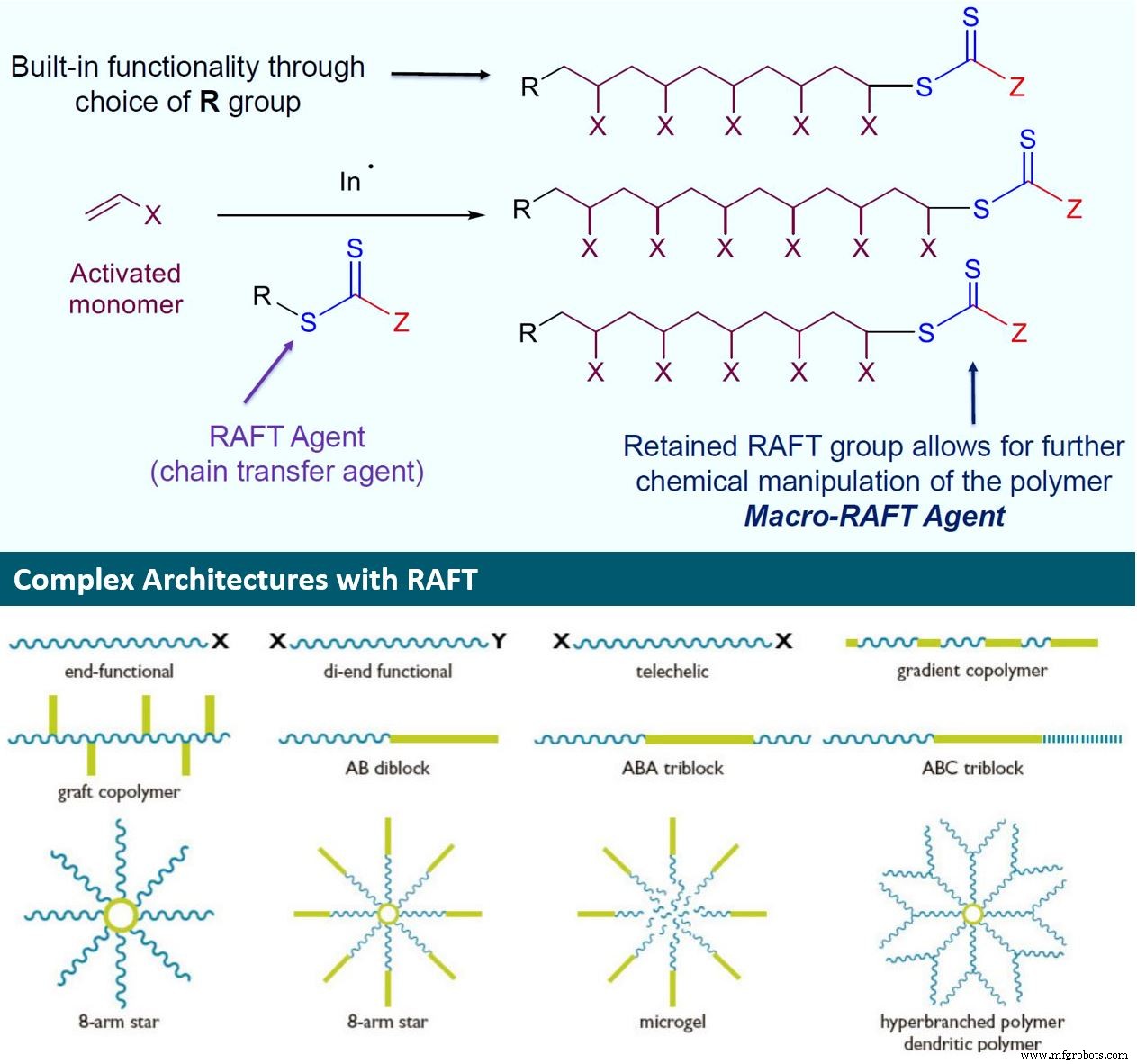
Een ander hulpmiddel dat CSIRO toepast, is de gepatenteerde en gecommercialiseerde RAFT-technologie (Reversible Addition-Fragmentation Chain Transfer). RAFT is een geavanceerde vorm van gecontroleerde polymerisatie door vrije radicalen die de synthese van op maat gemaakte polymeren mogelijk maakt met ongekende controle over samenstelling en architectuur. Hoewel toepassingen voor RAFT variëren van nieuwe medicijnafgiftesystemen tot industriële smeermiddelen en coatings, gebruikt het koolstofvezelteam van CSIRO het om controle uit te oefenen over het PAN-polymerisatieproces.
"Conventionele polymerisatie van monomeer tot polymeer produceert een brede polydispersiteit - met andere woorden, veel verschillende lengtes voor de polymeerketens", legt Melissa Skidmore, CSIRO-teamleider polymeerchemie, uit. “Als we echter een RAFT-middel toevoegen, krijgen we nu polymeerketens van bijna dezelfde lengte, en dus een veel smallere molecuulgewichtsverdeling. We gebruiken nog steeds dezelfde initiatoren, monomeren en oplosmiddelen, maar voegen alleen RAFT toe.”
"Het molecuulgewicht beïnvloedt de viscositeit van de spinoplossing", zegt Skidmore. "Traditioneel heeft een hoger molecuulgewicht in dope-oplossingen geleid tot gegroefde oppervlakken op de precursorvezels. Het toevoegen van RAFT verlaagt de viscositeit van de dope-oplossingen, wat leidt tot een hogere belading met vaste stoffen. Het verwijderen van het polymeer met zeer hoog molecuulgewicht van het polymeer kan resulteren in een betere moleculaire uitlijning in de vezel en verbeterde eigenschappen.” Ze voegt eraan toe dat een laag moleculair gewicht een weekmakend effect heeft op vezels. "RAFT produceert PAN-polymeren die dichtere, meer uniforme voorlopervezels kunnen produceren met minder structurele defecten. Dit zou ook kunnen bijdragen aan een snellere verkoling en lagere kosten.”
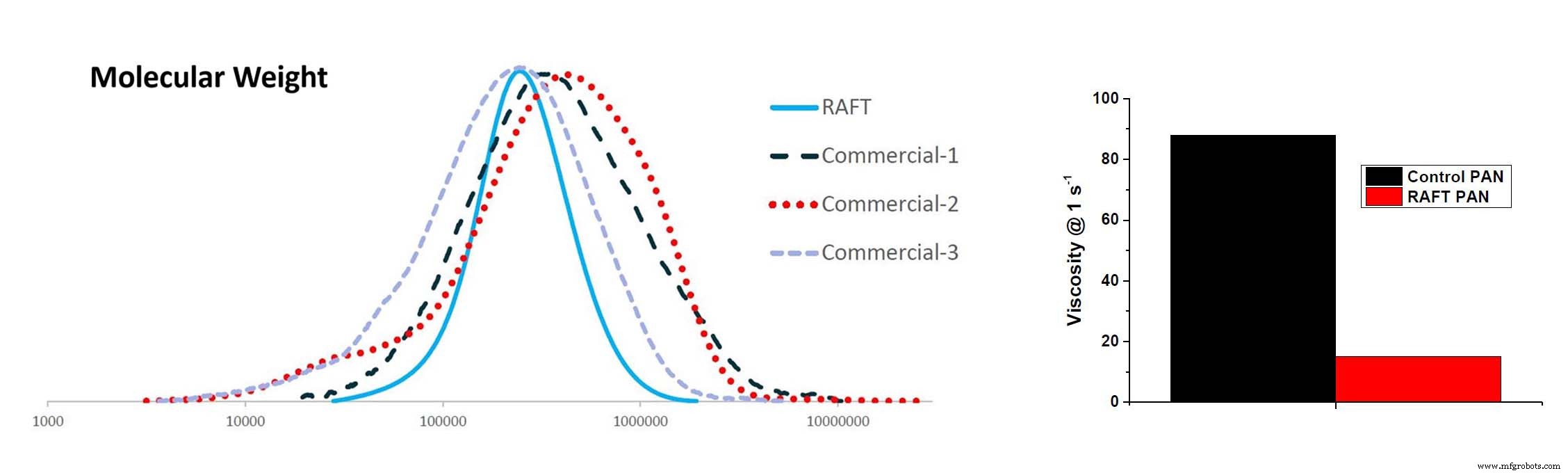
"Dit geeft ons ook toegang tot complexe polymeerarchitecturen", merkt Skidmore op. "RAFT maakt verdere chemische manipulatie van de polymeergroep mogelijk." Een voorbeeld van waar dat van pas komt, is wanneer de dope-oplossing wordt gemanipuleerd om te coaguleren tot vezels. "Er is een delicaat evenwicht tussen de ideale eigenschappen van de dope-polymeeroplossing en de coagulatieomstandigheden", voegt ze eraan toe. “Het polymeer bestaat voor 95% uit PAN en voor 5% uit additieven. Omdat RAFT-polymeren zich anders gedragen, denken we dat we sommige van de traditionele additieven kunnen verlagen en een hoger percentage kunnen omzetten in high-solid vezels, wat leidt tot minder defecten. We zijn dit nu aan het testen.”
Hoewel het momenteel niet de belangrijkste focus is, is RAFT ook buitengewoon interessant vanwege zijn vermogen om functionaliteit toe te voegen tijdens polymerisatie. Onderzoekers hebben bijvoorbeeld gekeken naar het maken van composieten met een hoog adsorptievermogen voor CO2-opvang (d.w.z. CO2 zou hechten aan de moleculaire oppervlakken van de composiet). Multifunctionele composieten zijn al in trek bij fabrikanten van vliegtuigen en elektrische voertuigen. Nieuwe soorten PAN- en koolstofvezels met toegevoegde functionaliteiten kunnen een belangrijke oplossing worden voor toekomstige composieten.
Continu FLOW-proces
"Met RAFT krijgen we controle over de polymerisatie", zegt Abbott. “Met FLOW hebben we meer controle over de vezelvorming.”
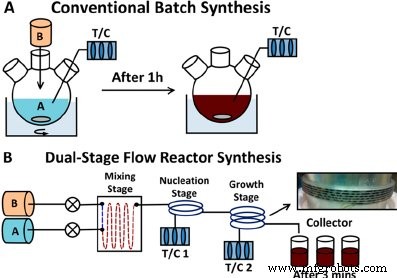
FLOW zet polymerisatie om in een continu in plaats van een batchproces. Abbott en Skidmore leggen uit dat de batchreactoren die momenteel worden gebruikt goed ingeburgerd zijn, eenvoudig te installeren en efficiënt in het mengen en bewaken van de reactiekinetiek, maar ze vereisen ook een groter volume dan continue procesreactoren, wat betekent dat het opzetten op industriële schaal duur is. Deze batchreactoren met een groter volume zijn ook inefficiënt wat betreft ruimte- en energieverbruik. Continue procesreactoren zijn kleiner en goedkoper, eenvoudig op te schalen, energiezuiniger en bieden superieure procescontrole en betere reproduceerbaarheid in vergelijking met batchverwerking. Omdat ze echter een toegewijde, doorlopende lijn zijn, zijn ze minder flexibel in het schakelen tussen verschillende parameters en producten.
Er zijn ook voordelen op het gebied van veiligheid en duurzaamheid. "Op dit moment is de productie van PAN vanuit milieuoogpunt niet duurzaam, vooral met betrekking tot de toxiciteit", zegt Skidmore. "Door het polymerisatieproces continu te laten verlopen, wordt de veiligheid verbeterd, omdat de reactieve stoffen die giftig, geurig en ontvlambaar zijn, worden geïsoleerd en verwerkt door geautomatiseerde apparatuur. Dit zal echter de complexiteit van de lijnen vergroten, die wel een hogere mate van monitoring en controle vereisen.” Hoewel het verdere ontwikkeling vereist, beschouwt Abbott FLOW-polymerisatie als een positief punt:"Koolstofvezel is inherent variabel, dus alles wat u kunt doen om deze variabiliteit te verminderen, verbetert de eigenschappen."
CarbonSpec – maatregel om te beheren
Het laatste hulpmiddel in de koolstofvezelbenadering van CSIRO is CarbonSpec. "Het is eigenlijk metrologie die we hebben ontwikkeld om de vezels die we produceren te testen en de relatie tussen eigendom en materiaal beter te begrijpen", legt Pierlot uit. “Als je het niet kunt meten, kun je het ook niet verbeteren. We zijn ook beter in staat om koolstofvezeleigenschappen te voorspellen met een minimale hoeveelheid PAN- en koolstofvezelmetingen.”
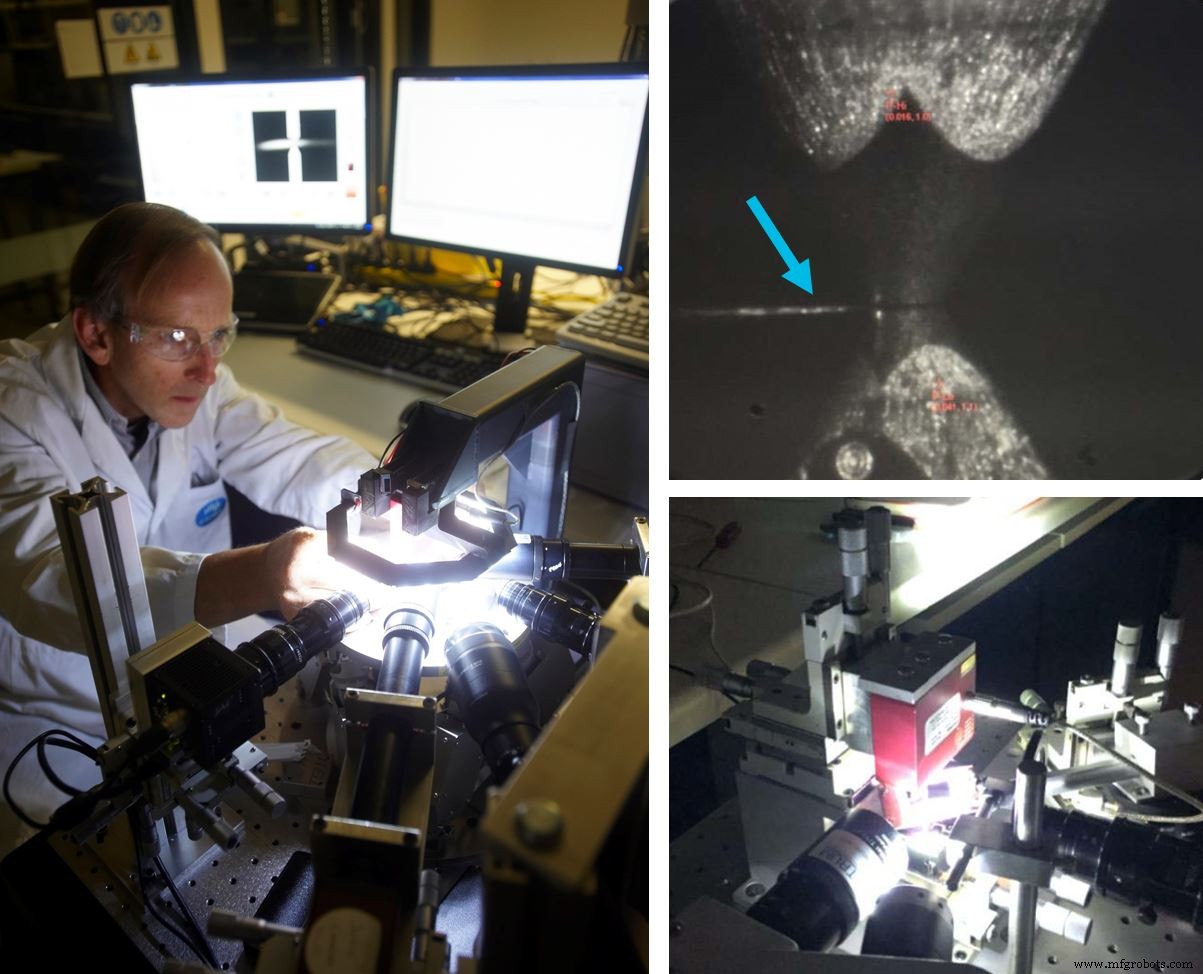
“In de koolstofvezelindustrie is het standaard om synchrotron X-ray Computed te gebruiken
tomografie (CT) om de microstructuur van je vezels te bepalen”, zegt Pierlot. (Een synchrotron is een deeltjesversneller ter grootte van een voetbalveld die zeer heldere röntgenstralen genereert die naar een aangrenzende bundellijn worden gestuurd voor beeldvorming, enz.) ontwikkeld voor het scannen van de microstructuur van individuele PAN-precursoren en koolstofvezels. Een microstructuurkaart van individuele vezels met een diameter van slechts 5 micron wordt binnen enkele minuten bereikt. Het SAXS-signaal helpt de porieontwikkeling in vezels te begrijpen, terwijl het WAXS-signaal helpt bij het identificeren van de kritische microstructuurparameters voor het optimaliseren van de vezelmodulus. Door beide signalen tegelijkertijd te gebruiken, kunnen we de mechanische sterkte en stijfheid bewaken en optimaliseren in elke fase van het productieproces, van PAN-dope tot koolstofvezel.”
Pierlot merkt op dat het team binnen CarbonSpec ook nieuwe instrumenten en testmethoden ontwikkelt. “We meten bijvoorbeeld de transversale modulus en sterkte naast de normaal gerapporteerde axiale eigenschappen van de vezels. We denken dat we de nieuwe methode die we hiervoor hebben ontwikkeld kunnen gebruiken om ook de axiale druksterkte te meten.” Dit laatste is lange tijd een uitdaging geweest omdat de diameter van een enkele koolstof- of PAN-vezel erg klein is (5-10 µm), waardoor het moeilijk is om een echte axiale drukspanning uit te oefenen zonder knikken te veroorzaken.
20% sterkere koolstofvezels van de volgende generatie
"We hebben meer inzicht gekregen in het omzetten van polymeer in vezels en maken nu commerciële vezels", zegt Abbott. "We passen deze technologische hulpmiddelen toe op andere precursorpolymeren om SIROPAN te maken, de CSIRO-versie van PAN met RAFT. We kunnen nu kilo's van die vezels maken."
"De volgende stap is om de voordelen van het gebruik van RAFT-polymeren te beoordelen", vervolgt hij. "We maken nog steeds PAN, maar we kunnen het molecuulgewicht beter beheersen en verhogen, terwijl we de viscositeit verlagen, wat sterkere koolstofvezel kan produceren." Hoeveel sterker? "We weten het nog niet zeker, maar ons doel is 20% sterker", zegt Abbott. "We weten dat 10% sterker niet voldoende is om de voorloper financieel haalbaar te maken - 20% is volgens de industrie het minimum dat nodig is."
- Ontwikkel nieuwe voorloperpolymeren via RAFT (hoogwaardige polymeren of andere eigenschappen)
- Commercieel concurrerende polymeerprocessen (FLOW) ontwikkelen
- Begrijp de omzetting van polymeer in vezels (nat spinnen) voor lagere kosten en hogere eigenschappen
- Begrijp de invloed van precursoreigenschappen op koolstofvezeleigenschappen, voorspel koolstofvezeleigenschappen beter en optimaliseer het proces op basis van deze metingen en voorspellingen (CarbonSpec)
- Produceer op maat gemaakte koolstofvezels voor specifieke eindtoepassingen door de PAN en gecarboniseerde vezel te engineeren
"De koolstofvezelindustrie groeit elk jaar met 10%", zegt Abbott. "We willen graag samenwerken met gevestigde en/of nieuwe spelers in de industrie die geïnteresseerd zijn in het verbeteren van de kwaliteit, prestaties, kosten en duurzaamheid van koolstofvezel."
"We testen zes verschillende precursorformules en zullen deze carboniseren bij Carbon Nexus", voegt Skidmore toe. “We hopen eind dit jaar resultaten te hebben. Het duurt even om van het RAFT-polymeer een witte vezel te krijgen en dan door carbonisatie.”
Abbott voegt toe:"We willen sterke resultaten tegen het einde van het jaar, maar we doen dit voor de lange termijn."
Dit onderzoek wordt ondersteund door het Science and Industry Endowment Fund.
vezel
- Koolstofvezel
- Koolstofvezels:verleden, heden en toekomst
- 3 voordelen van een horloge van koolstofvezel
- 5 verrassende koolstofvezelproducten
- Kan koolstofvezel worden gerecycled?
- Voordelen van koolstofvezelschoenen
- Innovatief gebruik van koolstofvezel
- Koolstofvezel in ruimtevaarttoepassingen
- Koolstofvezel in automobieltoepassingen
- Hoe wordt koolstofvezel gemaakt?
- Koolstofvezel beschermt tegen piraten