Fysische dampafzetting (PVD)
Het aanbrengen van coatings op materialen is een van de meest gebruikte strategieën in de industrie om hun eigenschappen te verbeteren. Door afzetting van coatings , kan een breed scala aan eigenschappen van een materiaal worden verbeterd, van tribologisch tot esthetisch oogpunt.
In de blog van vandaag presenteren we een technologie die een groot potentieel heeft bij het aanbrengen van coatings. Deze technologie is physical vapour phase deposition (PVD) .
Wat is fysieke dampafzetting of PVD?
De oorsprong vanfysieke dampafzetting (PVD) komt voort uit de combinatie van elektriciteit, magnetisme en de kennis van chemie in de gastoestand.
Het concept van fysieke dampafzetting ontstond toen coatings die in een vacuümatmosfeer werden aangebracht in opkomst waren. In deze jaren vonden verschillende ontwikkelingen plaats in technologieën zoals sputteren of plasma, waarbij chemische reacties in de damptoestand, thermische verdamping en de beheersing van energiebronnen een rol speelden.
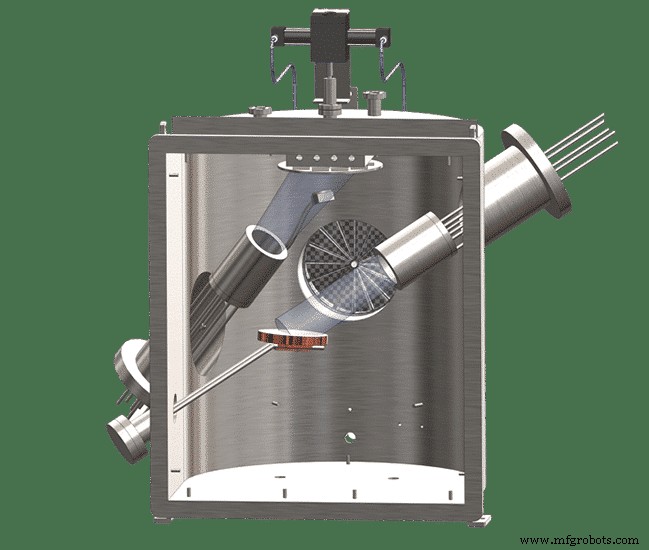
De PVD-techniek is een proces waarbij een dunne filmdepositie plaatsvindt op het oppervlak van een materiaal, waarbij atoom voor atoom op het substraat groeit . De fysieke depositie van damp bestaat uit een fysisch-thermisch botsingsproces die het te deponeren materiaal, het doelwit genaamd, transformeert in atomaire deeltjes, die in een gasvormige plasmatoestand naar de substraten worden geleid door een vacuümatmosfeer, waarbij een fysieke coating wordt gegenereerd door condensatie van geprojecteerde atomen.
Door PVD aangebrachte coatings hebben meestal een dunne dikte, die kan variëren van atomaire lagen (minder dan 10 angstrom (Å) tot 0,1 nanometer (nm)) tot coatings van enkele microns (dikte van een haarvezel).
Wat zijn de meest gebruikte PVD-technologieën?
Ondanks het feit dat het proces van verdamping en ionisatie van het doelwit, dat uiteindelijk de coating op het substraat zal vormen, altijd fysiek van aard zal zijn (vandaar de naam van fysieke dampafzetting), zijn er verschillende technologieën die PVD gebruiken voor de sollicitatie. van coatings.
De belangrijkste en meest gebruikte PVD-technologieën zijn:
-
Kathodische afzetting of sputteren
In dit type PVD-technologie maakt de versnelling van ionen door middel van plasma het mogelijk dat deze inslaan op het oppervlak van het objectief om de afgifte van deeltjes daaruit te produceren. De ionen brengen hun kinetische energie over naar het oppervlak van het doelwit en verdampen. Dit type PVD wordt gekenmerkt door de afzetting van verbindingen die ontstaan wanneer het doelwit reageert met het in het plasma aanwezige gas. Het meest kenmerkende voorbeeld is de afzetting van titaannitride (TiN), waarbij het aanwezige gas stikstof is en het doel titaan is, die beide reageren om een coating van TiN te veroorzaken.
-
Thermische verdamping
Dit type PVD-methodologie wordt gekenmerkt door het feit dat het doelwit verdampt door een vacuümverwarmingsproces en een dampstroom vormt die het substraat in de proceskamer raakt, wat resulteert in hechting van de coating. In dit proces speelt de vacuümatmosfeer een speciale rol omdat deze vervuiling van de gevormde coating voorkomt.
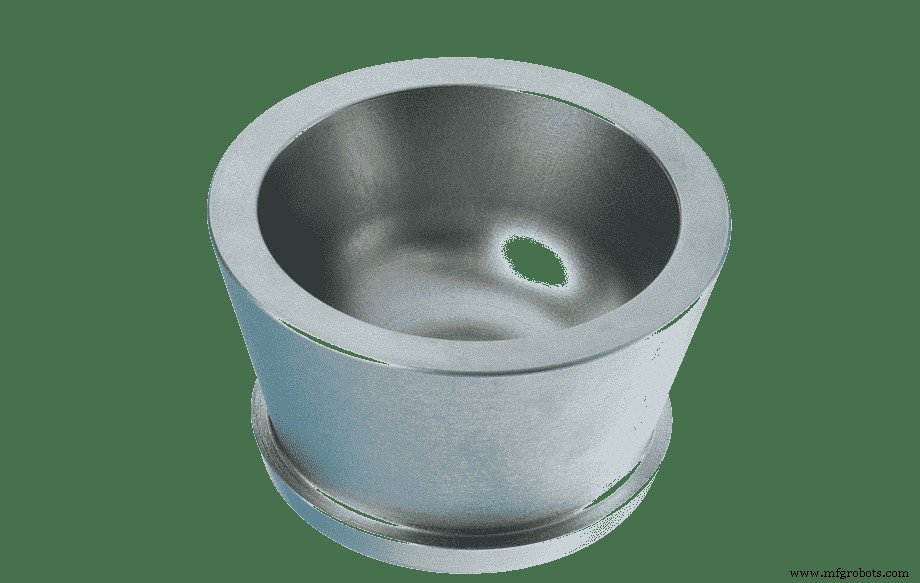
-
Boogafzetting
Bij deze PVD-technologie wordt een boog van elektrische stroom met hoge intensiteit en lage spanning toegepast, waardoor de temperatuur stijgt totdat de deeltjes van het objectief sublimeren en sterk geïoniseerd verdampen in de vacuümkamer. De geïoniseerde deeltjes worden naar het substraat geleid door een potentiaal aan te leggen. Bij boogafzetting kan het doel fungeren als een kathode (kathodeboog) of een anode (anodische boog), afhankelijk van de aard en de te verkrijgen coating. Net als sputterdepositie kunnen coatings met bepaalde samenstellingen worden bereikt door de doelionen te laten reageren met een reactief gas.
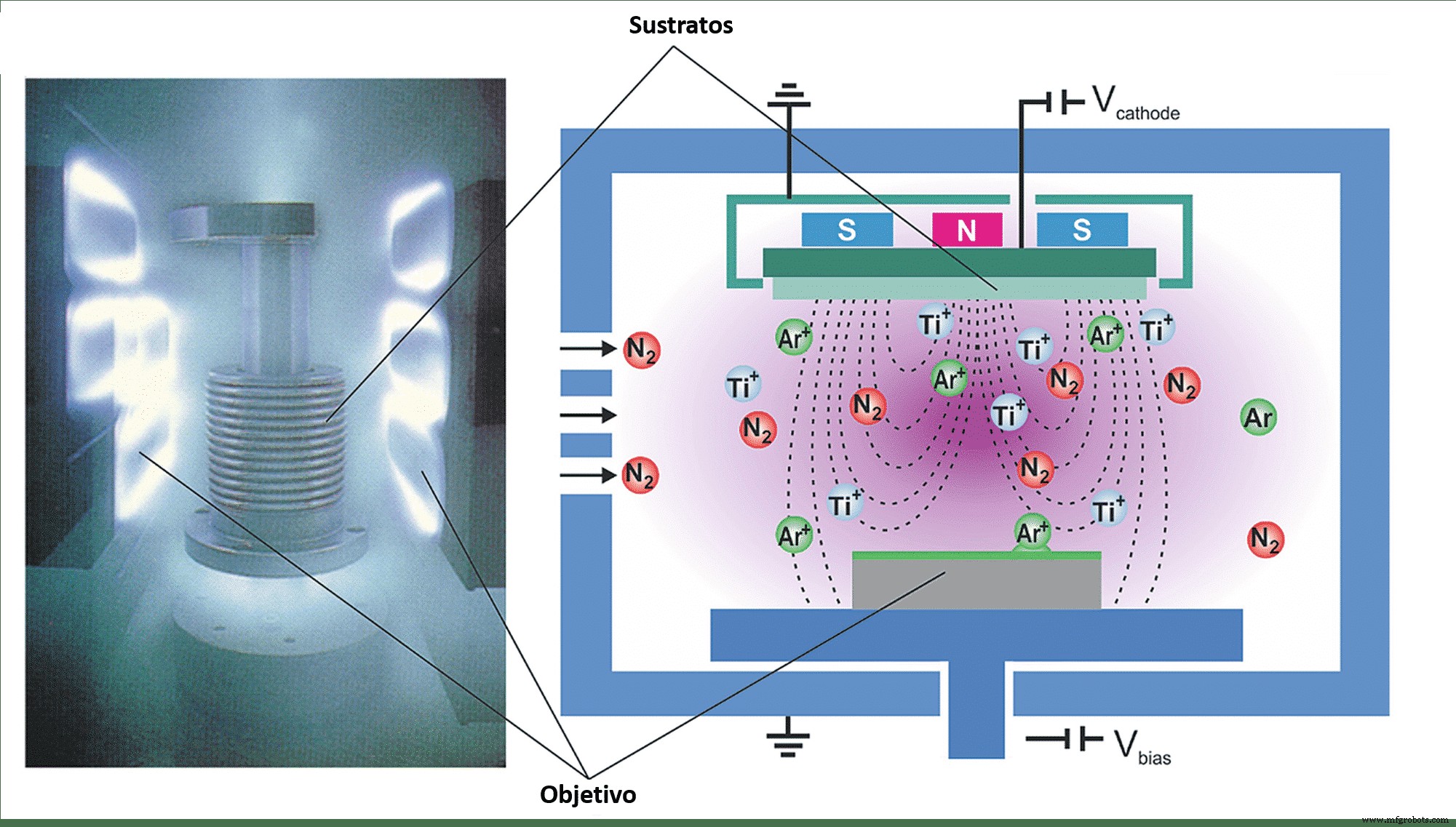
-
Ionenafzetting (e-beam)
Bij deze PVD-techniek vindt de verdamping van het doel plaats met dezelfde processen als eerder gezien (sputteren, thermische verdamping of elektrische boog). Het verschil ligt in het gebruik van een hoogenergetisch inert ionenbombardement (gewoonlijk argon) om de op het substraat verkregen coating te controleren en te wijzigen. Het belangrijkste kenmerk van deze techniek is dat het mogelijk is om pure metalen coatings te verkrijgen zonder atomaire verontreiniging.
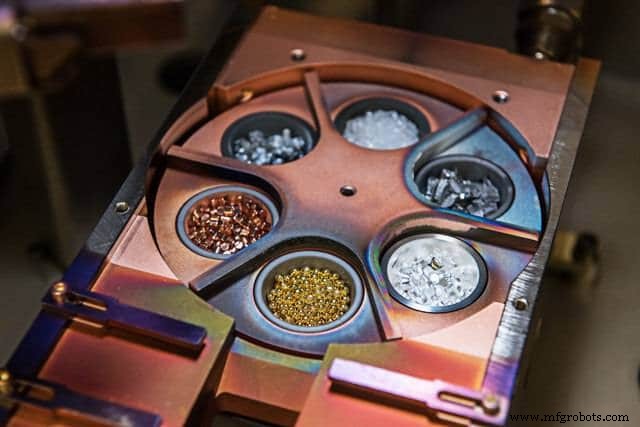
Voor- en nadelen van PVD
Tegenwoordig hebben we een breed scala aan technieken voor het afzetten van coatings. Elk van hen heeft specifieke toepassingen, met hun voor- en nadelen.
Vervolgens presenteren we de belangrijkste voordelen van fysieke dampafzetting.
- Het vereist geen gebruik van chemische reagentia of reiniging nabehandelingen, dus het heeft een zeer lage impact op het milieu.
- PVD kan worden toegepast op elk type anorganisch materiaal.
- De door PVD verkregen coatings hebben een uitstekende hechting, weerstand en duurzaamheid.
- De PVD-techniek zorgt voor een goede controle over de samenstelling en dikte van de coatings.
De belangrijkste nadelen van PVD zijn:
- Het PVD-proces maakt gebruik van complexe apparatuur, met zeer hoge kosten
- De productiesnelheid van PVD-coatings is traag in vergelijking met andere coatingdepositieprocessen.
- De PVD-techniek is beperkt in substraten met complexe geometrieën
PVD-applicaties
Aangezien we PVD aan het begin van deze blog hebben geïntroduceerd, is het de moeite waard om de precisie en zuiverheid te benadrukken die wordt geboden door fysieke dampafzetting om coatings te verkrijgen. De belangrijkste PVD-toepassingen die momenteel in gebruik zijn, zijn als volgt:
- Metalen coatings voor halfgeleider eigenschappen aan een substraat die dat in eerste instantie niet zijn.
- Magnetisch filmcoating.
- Coatings voor decoratief doeleinden, veel gebruikt op het gebied van sieraden.
- Coatings voor zonneglazen of spiegels, die fungeren als optisch interferentiebarrières of reflecterend barrières.
- Geleidende lagen van palladium of koolstof, voor elektronenmicroscopiemonsters.
- Hoge hardheid coatings van composietmaterialen, slijtvast en corrosie , veel gebruikt voor de verbetering van mechanische gereedschappen.
Projecten uitgevoerd met PVD-technologie door ATRIA
Hieronder zullen we u enkele van de projecten laten zien die zijn uitgevoerd door het ATRIA-team waarbij de verkregen coatings werden gebruikt door PVD:
- Ontwikkeling van gouden kleuren met behulp van fysieke dampafzettingstechnologie . In dit project was het doel om verschillende tinten gouden kleur te verkrijgen op metalen ondergronden. Om dit uit te voeren, werd de optimalisatie van het PVD-proces van verschillende metalen doelen en reactieve gassen uitgevoerd. Zoals te zien is op de foto, werd het verkregen van een intens goud tot een lichter goud met roze tinten.
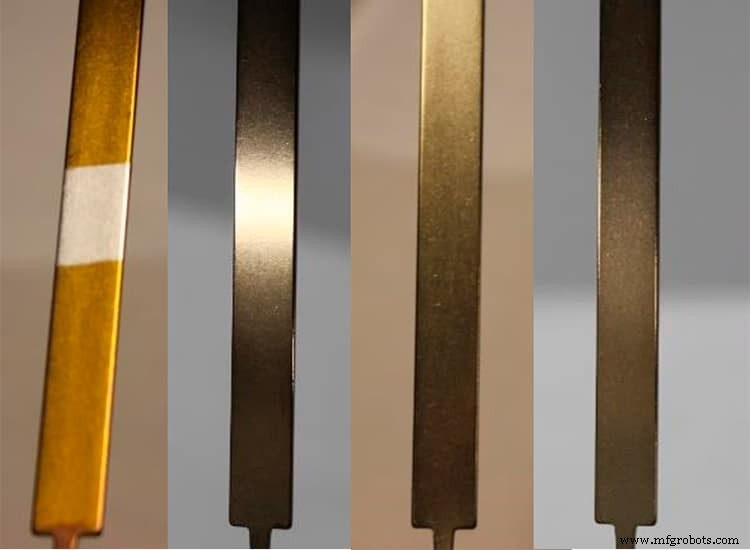
- Ontwikkeling van metaalfilms als barrières tegen corrosie . In dit project vond onze corrosie plaats op een metalen substraat dat was gecoat met verschillende metalen lagen bij blootstelling aan bepaalde omgevingsomstandigheden. De door ATRIA voorgestelde oplossing was het ontwikkelen van een inerte metallische coating onder deze omgevingsomstandigheden en afgezet door middel van PVD. Het doel van deze coating is om een grote weerstand te bieden tegen slijtage en corrosie
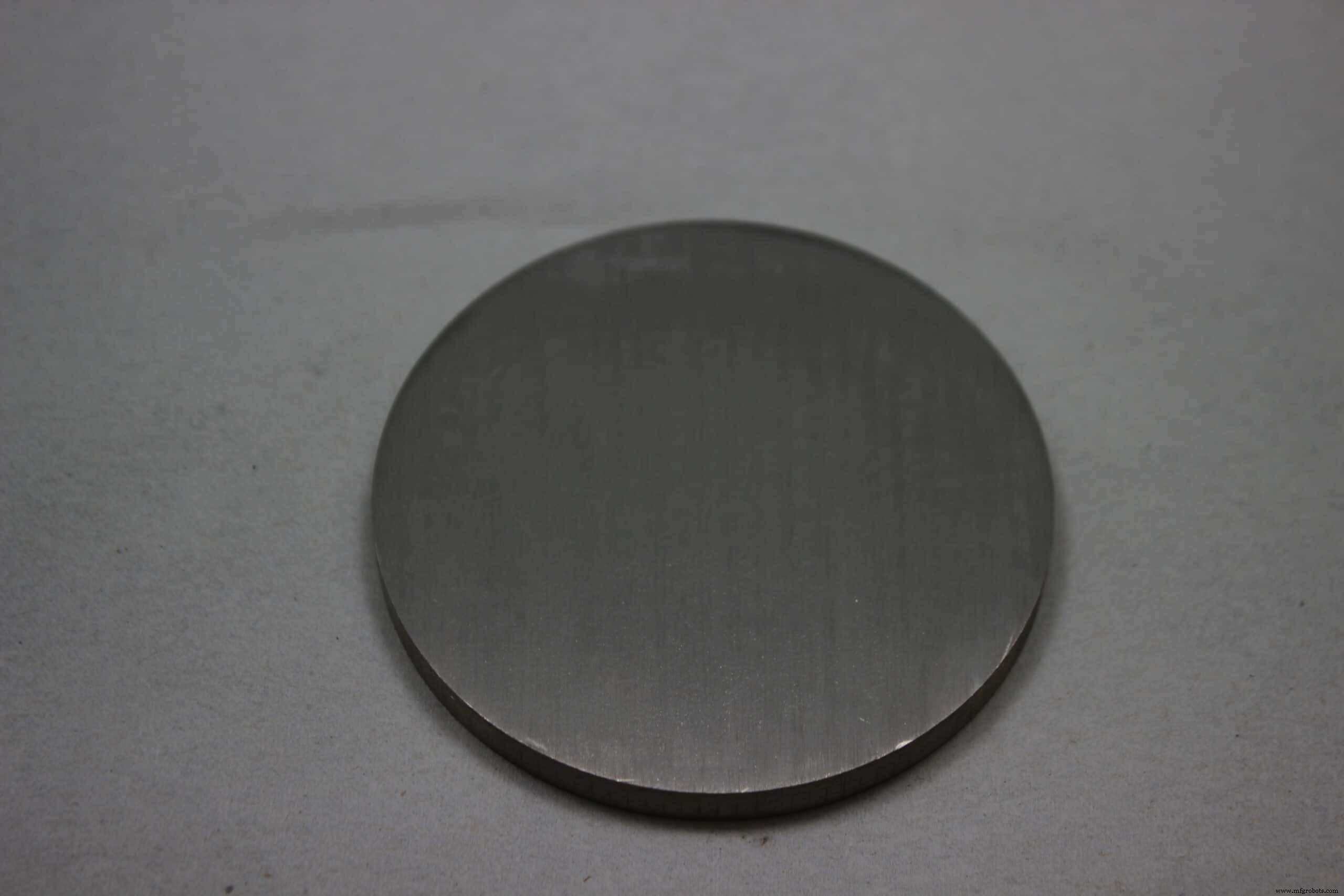
Wilt u in al uw projecten coatings aanbrengen door middel van fysische dampafzetting? Wilt u de eigenschappen van uw materialen verbeteren door middel van PVD-technologie? Neem contact met ons op!
Samengesteld materiaal
- Wat is chemische dampafzetting?
- Printen versus CNC-machines
- om te stoppen met het breken van vingerfrezen
- om problemen met een e-stop voor een CNC-machine op te lossen
- t is SFM in bewerking?
- es van koelvloeistof voor CNC-bewerking
- Kunstmatige Intelligentie Robots
- M2M of Machine to Machine communicatie, wat is het?
- Industriële automatie
- Hyperspectrale camera's
- Computer visie