De voordelen van op analyse gebaseerde productengineering
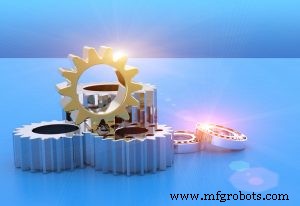
Een blik op hoe systeemsimulatie en IoT-mogelijkheden de datafeedbacklus kunnen sluiten.
Nadat een product is verkocht, krijgen productingenieurs doorgaans weinig feedback over de prestaties in het veld. Dat hoeft niet meer zo te zijn. Met de juiste oplossing kunnen productfabrikanten systeemsimulaties en IoT-mogelijkheden combineren om productontwerpen te verbeteren en vervolgens oplossingen uit te vaardigen met behulp van simulaties op basis van echte belastingsgevallen.
RTInsights heeft onlangs gesproken met Jasmin Klein, Global Portfolio Development, en Christian Binkowski, Cloud Solution Manager, van Siemens om de voordelen te bespreken van het opnemen van een datafeedbacklus tussen productingenieurs en het apparaat in het veld om realtime productoptimalisatie, digitale tweelingen en meer. Hier is een samenvatting van het gesprek.
RTInsights:wat is op analyse gebaseerde productengineering?
Klein: Op analyse gebaseerde productengineering stelt gebruikers in staat om live prestatiegegevens van een product of machine in het veld te nemen en deze terug te zetten in het productsimulatiemodel om het productontwerp te verbeteren. Met de live productiegegevens die worden teruggevoerd naar het model, wordt een digitale tweeling met gesloten lus gecreëerd.
Deze digitale tweeling kan vervolgens worden gebruikt om het ontwerp van het product actief te verbeteren. Als een product bijvoorbeeld problemen begint te krijgen, kunt u er een nauwkeurige simulatie op uitvoeren met behulp van de live gegevens en beginnen met het identificeren van de oorzaak van een probleem. Nu de problemen volledig zijn begrepen, kunnen de vereiste wijzigingen in het ontwerp worden aangebracht voor toekomstige iteraties. De impact van de wijzigingen kan ook nauwkeurig worden geverifieerd met behulp van het nauwkeurigere simulatiemodel met de echte gegevens van de machine.
RTInsights:wat zijn de voordelen van het gebruik van op analyse gebaseerde productengineering?
Klein: Met nauwkeurige simulaties kunnen ontwerpers niet alleen betere beslissingen nemen, maar het vermindert ook de tijd en kosten om nieuwe ontwerpen op de markt te brengen. De noodzaak voor prototyping is bijna geëlimineerd. Bedrijven hebben het vermogen om gebruikersgerichte producten te ontwikkelen die voldoen aan de behoeften van de klant en de klanttevredenheid verhogen. Ze kunnen leren van de problemen in het veld door echte data te gebruiken, de fouten te simuleren en het ontwerp te verbeteren. Op deze manier kunnen ze productproblemen elimineren, tijd en geld besparen door de productvalidatietijd te verkorten en over-engineering te voorkomen. Samen verbetert dit de algehele efficiëntie.
RTinsights: Welke oplossing biedt Siemens op dit gebied?
Binkowski: Siemens heeft MindSphere®, de industriële IoT as a service-oplossing, die producten, machines en systemen van allerlei soorten en merken met elkaar verbindt. Deze oplossing verzamelt, aggregeert, beheert en analyseert prestatiegegevens. Specifiek voor de MindSphere Analytics-Based Product Engineering-oplossing, is MindSphere naadloos geïntegreerd met Simcenter TM Amesim TM software via een speciaal gebouwde connector. De MindSphere-applicatie gebruikt deze connector om live prestatiegegevens terug te sturen naar de simulatiemodellen.
(Simcenter Amesim-software simuleert alle verschillende soorten mechatronische systemen. Het wordt geleverd met talloze bibliotheken en oplossingssjablonen voor machines, auto's, batterijen, schepen en meer.)
Zodra u een verbinding tot stand hebt gebracht tussen beide systemen, kunt u de tijdreeksgegevens selecteren die u wilt verkennen. Als er bijvoorbeeld een probleem is in het veld, wilt u misschien 20 minuten voor of rond dat incident simuleren. U kunt in MindSphere het tijdsbestek selecteren en MindSphere genereert een simulatiepakket en draagt dit over aan Simcenter Amesim. Vervolgens wordt de simulatie uitgevoerd en als dat eenmaal is gebeurd, kun je de simulatieresultaten bekijken in MindSphere.
RTinsights: Kun je voorbeelden geven van gebruiksscenario's en successen?
Klein: Ik zou beginnen met een algemeen gebruik. Tegenwoordig wordt een machine in de meeste gevallen naar de klant verzonden en krijgt de productmanager nooit informatie over de prestaties van de machine in het veld om het productontwerp te verbeteren. Wanneer er een probleem is, wordt contact opgenomen met de ondersteuning en wordt het probleem bij de klant opgelost. De informatie van de support komt meestal niet bij de product engineer terecht, of wordt pas veel later doorgestuurd. Vanwege deze hiaten moet de productingenieur een hypothesegestuurd ontwerp ontwikkelen, wat resulteert in over- of onderengineering. Uiteindelijk betekent dit dat niet aan de eisen van de klant wordt voldaan of in de toekomst niet zal worden voldaan.
De op analyse gebaseerde engineeringaanpak van MindSphere biedt die feedbacklus om het productontwerp te veranderen en de prestaties in het veld te verbeteren.
Binkowski: Een ander voorbeeld is het optimaliseren van de prestaties van een bestaand product. Deze oplossing biedt de mogelijkheid om bepaalde parameters op het simulatiemodel rechtstreeks in MindSphere aan te passen. Als u bijvoorbeeld een product heeft dat op verschillende snelheden kan werken, kunt u testen welke snelheid het meest optimaal is. Met behulp van het bijgewerkte simulatiemodel om parameters uit te voeren, kunt u de machines testen met behulp van de huidige omstandigheden van de lijn.
Klein: Als we kijken naar een voorbeeld van een klant die machines verkoopt die zijn verbonden met een IoT-oplossing zoals MindSphere, kan die klant continu gegevens verzamelen, prestatie-inzichten op elk moment krijgen en vervolgens een probleem simuleren met behulp van deze informatie om het productontwerp te verbeteren.
De product engineer kan direct leren en conclusies trekken uit de live data van de machine. Dit zorgt er uiteindelijk voor dat de productingenieur een gebruikersgericht product kan ontwikkelen en de klanttevredenheid kan verhogen.
Een voorbeeld is Konecranes, een Fins bedrijf dat gespecialiseerd is in de fabricage en service van kranen en hijsapparatuur. Het heeft een digitale oplossing geïmplementeerd om het productontwikkelingsproces te versnellen en de product- en prestatiegegevens met elkaar te verbinden.
Het bedrijf gebruikt MindSphere en Teamcenter®, de digitale levenscyclusbeheersoftware van Siemens, om de digitale tweeling te benutten om het aantal prototypen dat ze moeten produceren te verminderen. Dit helpt hen om de efficiëntie te verhogen en ook de productvalidatietijd te verkorten. Door een digitale innovatie-oplossing te implementeren, versnelden ze het productontwikkelingsproces en verbeterden ze de samenwerking tussen de simulatietest- en engineeringorganisaties in hun bedrijf.
Internet of Things-technologie
- De vierde industriële revolutie
- De voordelen van het aanpassen van IIoT- en data-analyseoplossingen voor EHS
- De voordelen van interconnectiviteit op de werkplek
- De tastbare voordelen van VR in de technische ruimte
- Onderhoud in de digitale wereld
- Het IoT democratiseren
- De waarde van IoT-gegevens maximaliseren
- De waarde van analoge meting
- Tableau, de gegevens achter de informatie
- 3 verrassende voordelen van de cloud in IoT
- De toekomst van datacenters