Q&A:Semiconductor Manufacturing verleden, heden en toekomst
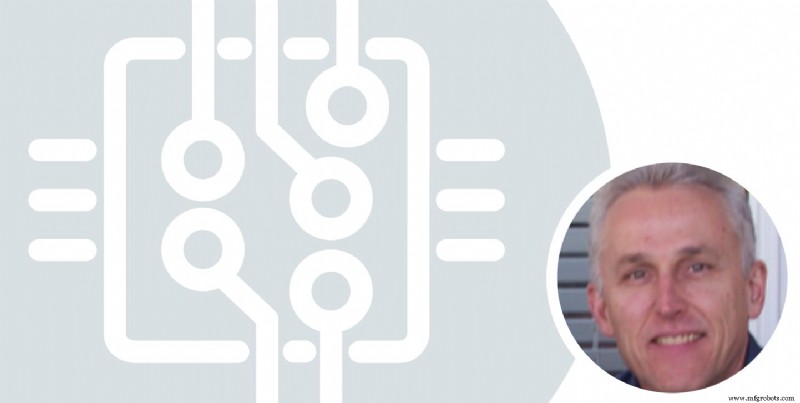
Halfgeleiderproductie, verleden, heden en toekomst:een vraag en antwoord met brancheadviseur Carl White
De wet van Moore, een concept dat voor het eerst naar voren werd gebracht door de mede-oprichter van Intel, Gordon E. Moore in 1965, voorspelde dat het aantal transistors op een geïntegreerde schakeling (of microchip) elke twee jaar zal moeten verdubbelen, terwijl de computerkosten met ongeveer bijna de helft, wat leidt tot een exponentiële groei van de rekenkracht. De halfgeleiderindustrie heeft hard gewerkt om dit paradigma bij te houden, maar het is niet eenvoudig om constant meer verwerkingskracht te leveren in minder ruimte, vooral wanneer concurrenten hetzelfde doel nastreven en de consumentenvraag naar geavanceerde technologie constant is.
Grotendeels dankzij de wet van Moore:"Ik voel de behoefte - de behoefte aan snelheid!" kan meer aanvoelen als een beschrijving van het dagelijks leven in de halfgeleiderindustrie dan als een quote van Top Gun . Dit was een van de vele belangrijke conclusies uit ons recente gesprek met veteraan Carl White, principal engineering consultant bij C.L. Witte Engineering Services, LLC. Na bijna 40 jaar werkzaam te zijn geweest in bedrijven in de toeleveringsketen van de halfgeleiderindustrie, bood Carl een goed perspectief op de niet-aflatende behoefte aan snelheid, zowel op het gebied van ontwikkeling als verwerkingskracht. Lees verder om erachter te komen wat hij te zeggen had over wat er in het verleden nodig was om snel genoeg te innoveren om de Wet van Moore bij te houden, met welke uitdagingen de halfgeleiderindustrie momenteel wordt geconfronteerd en wat we in de nabije toekomst kunnen verwachten.
Swagelok-referentiepunt (SRP): Bedankt dat je bij ons bent gekomen, Carl. Kun je beginnen met ons iets over je achtergrond te vertellen?
Carl White: Ik ben geboren in Arizona en heb industrieel technologiebeheer en werktuigbouwkunde gestudeerd aan de staat Arizona voordat ik in 1982 mijn carrière begon bij ASM, de OEM van de halfgeleiderverwerkingstool. Van daaruit ging ik werken bij Spectrum CVD, dat eigendom was van Motorola destijds; Materials Research Corporation, dat uiteindelijk onderdeel werd van Sony; Tokyo Electron, ook bekend als TEL; en uiteindelijk Applied Materials. Ik heb 28 van mijn 38 jaar in de halfgeleiderindustrie gewerkt in de OEM-ruimte en de andere 10 jaar voor een chipfabrikant - Motorola Semiconductor Products Group. Ik ging vorig jaar met pensioen bij ASM nadat ik de afgelopen 15 jaar aan ALD-technologie (atomic layer deposition) had gewerkt. Nu overleg ik met bedrijven in de branche.
SRP: Het klinkt alsof je een interessant perspectief hebt, omdat je veel hebt gewerkt aan de OEM-tools en chipfabrikanten van de industrie. Wat dreef je om je carrière hieraan te besteden?
CW: Het is een zeer snelle industrie. Technologie verandert voortdurend en dat vereiste creativiteit en continu leren voor degenen onder ons die in de ruimte werken. Er was geen kans om je te vervelen! Het was ook spannend om te zien hoe de ontwerpen waaraan ik werkte verandering teweegbrachten, aangezien halfgeleidertechnologie belangrijk is in zowat elke andere industrie.
SRP: Welke meta-trends heb je gezien als drijvende kracht achter de evolutie van de halfgeleiderindustrie?
CW: Vroeger was het het ruimteprogramma. Later werd het consumententechnologie. We gingen van rekenlinialen naar draagbare rekenmachines, naar pc's naar smartphones, en dat was mogelijk dankzij de evolutie van de halfgeleidertechnologie. Nu zien we de opkomst van A.I. en autonome voertuigen die veranderen. De enige constante was de behoefte om producten te produceren en informatie sneller over te brengen. Er is voortdurend nieuwe halfgeleidertechnologie nodig om aan de vraag naar meer rekenkracht te voldoen.
Er is ook de drive die voortkomt uit de concurrentie om leiderschap in halfgeleiderinnovatie. Het is niet alleen concurrentie tussen bedrijven, maar iets dat zich wereldwijd afspeelt. In de loop van de tijd hebben verschillende landen de ontwikkeling van halfgeleidertechnologie geleid, en die dynamische veranderingen leiden soms tot meer samenwerking op industrieniveau. Zo hebben 14 in de VS gevestigde halfgeleiderbedrijven zich in 1987 verenigd met de Amerikaanse overheid om SEMATECH, het chipproductieconsortium, te vormen in een poging de kwaliteit van de chips die ze produceerden te verbeteren om beter te kunnen concurreren op de wereldmarkt. Die versnelde vooruitgang in de halfgeleiderindustrie in de VS In die tijd probeerden veel bedrijven alles te doen ... chiptechnologie ontwerpen, produceren en verkopen. Ze leerden zich te specialiseren, wat leidde tot de oprichting van gieterijen die chips maken voor andere bedrijven, waardoor ook de vooruitgang van de industrie werd gestroomlijnd.
SRP: Kun je de relatie tussen chipdichtheid en de evolutie van de halfgeleidertechnologie en de elektronica die deze aandrijft uitleggen? Welke invloed heeft dat gehad op de apparatuur en componenten die nodig zijn om chips te produceren?
CW: Miniaturisatie is een constante behoefte om de Wet van Moore bij te houden. Om meer transistors op chips te krijgen, moet je ze steeds kleiner maken. U moet ook de apparatuur aanpassen aan de ontwikkelingen in het productieproces. Een belangrijk keerpunt was aan het eind van de jaren negentig, het begin van de jaren 2000, toen de industrie overstapte van siliciumwafels van 200 mm naar 300 mm als basis voor chips. De ontwikkeling van poorten met hoge K (diëlektrische constante) voor transistors van 45 nm (nanometer) die minder elektronenlekkage mogelijk maakten, was een nieuwe grote stap in het streven van de industrie naar miniaturisatie. Ik had het geluk om te werken aan de ontwikkeling van de apparatuur die Intel gebruikte om deze te produceren, dus de verandering was opwindend om te zien. Nu, voor het perspectief, werken bedrijven aan de productie van 5 nm-chips.
Over het algemeen hebben we bedrijven gezien die proberen over te stappen naar kleinere procesknooppunten, wat inhoudt dat ze kleinere afmetingen van halfgeleidertechnologieën produceren in een poging kleinere, snellere en energiezuinigere transistors te maken, zo snel als elke 18 maanden. Dit overtreft de voorspelling van de wet van Moore (elke twee jaar verhuizen naar kleinere procesknooppunten), want dat is wat concurrenten doen.
Halfgeleiderfabrikanten vertellen de OEM's van gereedschappen wat ze willen bereiken op het gebied van chipprestaties en welke productieprocessen daarvoor waarschijnlijk nodig zijn. De OEM's werken aan het maken van productieapparatuur die dat soort prestaties mogelijk maakt, en daarbij werken ze samen met bedrijven als Swagelok om bestaande componenten te vinden of om samen te werken aan de engineering van nieuwe componenten om hun tools mogelijk te maken. Deze samenwerking is van cruciaal belang als halfgeleiderbedrijven de snelheid van innovatie willen bijhouden, omdat het OEM's helpt de componenten te krijgen die ze vandaag nodig hebben en het helpt de componentenfabrikanten te anticiperen op de toekomstige behoeften van de industrie.
SRP: Drijft de marktvraag naar specifieke elektronicatoepassingen de innovatie van halfgeleiders aan, of loopt de vooruitgang van chiptechnologie meestal vooruit op de marktvraag?
CW: Het kan alle kanten op. Soms kan de algemene druk om de halfgeleidertechnologie voortdurend te ontwikkelen tot doorbraken leiden voordat de markt weet wat hij met de technologie moet doen. In de jaren negentig gingen de computermogelijkheden bijvoorbeeld snel vooruit, maar de softwarekennis en -vaardigheden die nodig waren om de volledige kracht van chiptechnologie te benutten, ontbraken, waardoor de toepassingen achterbleven bij de verwerkingscapaciteiten. Maar in andere gevallen kan er druk zijn om bestaande applicaties in staat te stellen meer te doen - we zien dat nu meer met de noodzaak om meer gegevensverwerking en A.I. toepassingen.
Fundamenteel hebben we drie tijdperken van vraag gezien. Van de jaren zestig tot de jaren tachtig ging het om het mogelijk maken van computers en rekenapparatuur. We hadden toen duizenden transistors op chips. Vanaf de jaren tachtig zagen we de nadruk verschuiven naar het mogelijk maken van mobiele technologie zoals laptops en mobiele telefoons. We hadden op dat moment miljoenen transistors op een chip. In de afgelopen tien jaar hebben gegevensoverdracht en -opslag de vraag gestimuleerd, omdat we technologie creëren die meer verbonden is (met de opkomst van het internet der dingen en slimme apparaten die de klok rond sociale interacties mogelijk maken) en datacentrisch (met trends als Big Data en machine learning creëren vraag).
SRP: Hoe heeft de aanhoudende vraag naar kleinere, maar krachtigere chips de prestatie-eisen beïnvloed van vloeistofsysteemcomponenten die worden gebruikt bij de productie van halfgeleiders?
CW: De verandering in de geometrie van halfgeleiderchips in de loop van de tijd heeft geleid tot de behoefte aan verschillende vloeistofsysteemproducten die worden gebruikt in het chipproductieproces. Vooral omdat transistors kleiner zijn geworden, is het van cruciaal belang om contaminatie in de verwerking te voorkomen, omdat dit de opbrengsten en de betrouwbaarheid van de chip kan beïnvloeden. Ongecontroleerde processen en contaminatie van componenten moeten worden vermeden. Als gevolg hiervan is de industrie overgestapt van balgkleppen (langere levensduur) naar membraankleppen (historisch schoner) die minder "dode ruimte" en volume ingesloten gas hebben, evenals minder bewegende delen.
Nu, met de release van de Swagelok ® ALD20-klep recentelijk zien we het voordeel van de hoge stroomcapaciteit die afkomstig is van een balgklep die nog steeds de ultrahoge zuiverheidsprestaties (UHP) biedt die nodig zijn in de moderne productie van halfgeleiders. Dit werd mede mogelijk gemaakt doordat de fabricagetechnieken in de loop van de tijd zijn verbeterd en omdat we ook toegang hebben tot verbeterde materialen, bijvoorbeeld hoogwaardig VIM-VAR-staal en corrosiebestendige legeringen. Er worden ook betere afwerkingstechnieken gebruikt, zoals elektrolytisch polijsten en passiveren, evenals betere tests voor productlanceringen dan vroeger. In het verleden heb ik sommige bedrijven naar de finish zien racen om eerst een technologie te lanceren, maar ze kwalificeerden hun componenten niet goed genoeg, en dat veroorzaakte problemen. Het is belangrijk om te weten dat producten uit de doos zullen werken zoals beloofd in de halfgeleiderruimte; componenten waarop u kunt vertrouwen dat ze consistent zijn en herhaalbare prestaties leveren, zijn van cruciaal belang.
SRP: Vergelijkbaar met een eerdere vraag, is het altijd de kleptechnologie geweest die verandert om nieuwe chipproductieprocessen mogelijk te maken, of heeft de vooruitgang van de halfgeleiderproductie de innovaties van het vloeistofsysteem gedreven?
CW: Veranderingen in het productieproces van halfgeleiders hebben zeker een rol gespeeld bij het bepalen wat we nodig hebben van UHP-kleppen en andere componenten van vloeistofsystemen. Wanneer u microchips maakt, bekleedt u doorgaans een kristallijne wafel, bijvoorbeeld silicium, door een reeks nauwkeurige doses met een voorlopergas in een depositiekamer om de wafel gelijkmatig te coaten voordat deze stolt. We gebruiken steeds vaker vloeibare en vaste precursorchemicaliën, sublimeren ze met behulp van hoge temperaturen en zorgvuldig gecontroleerde processen, en gebruiken vervolgens UHP-kleppen om ze op de wafels te doseren. Deze chemicaliën kunnen vaak onstabiel zijn en agressieve, corrosieve eigenschappen hebben, waardoor het moeilijk is om er effectief mee te werken.
We vertrouwen vaak op atomic layer deposition (ALD) en atomic layer etching (ALE) processen omdat chemische dampafzetting (CVD) en de voorlopers die we in dat proces gebruikten niet effectief genoeg kunnen worden gecontroleerd om chipproductie mogelijk te maken bij de kleine transistorgrootte die we hebben. zie vandaag. Het zijn deze veranderingen in processen en chemie - de industrie is bijvoorbeeld in de jaren negentig overgestapt op koperen interconnecties van aluminium vanwege de hogere geleidbaarheid - die componentenveranderingen noodzakelijk maken.
Al vroeg realiseerden OEM's van gereedschappen zich dat tegenvallende spaanopbrengsten vaak werden veroorzaakt door procesproblemen in plaats van defecte apparatuur. Vocht, reactieve chemicaliën die worden blootgesteld aan de atmosfeer, deeltjes die residu vormen in kleppen en voorkomen dat ze afdichten - dit waren allemaal uitdagingen waarmee de industrie te maken kreeg. We hebben geleerd terwijl we zijn geëvolueerd om procesuitdagingen te regelen, vaak door geavanceerde vloeistofsysteemcomponenten en systeemontwerpen. Dat heeft een positieve invloed gehad op onze resultaten, maar ook op de productieprocessen van chips en de prestatie-eisen van ondersteunende componenten.
SRP: Als dat een historisch beeld is van de evolutie van de productie van halfgeleiders, met welke uitdagingen wordt de industrie vandaag geconfronteerd en welke invloed heeft dat op de vereisten voor vloeistofsysteemcomponenten?
CW: Om de volgende fase van chipproductie te bereiken, hebben we betrouwbare productcontrole, herhaalbaarheid en consistentie van klepproductie nodig. Halfgeleidergereedschappen vereisen talrijke UHP-kleppen en het is moeilijk om perfect uniforme prestaties van klep tot klep te hebben, maar we hebben die productieconsistentie nodig. Het gaat niet alleen om een kwalitatief hoogstaand product, maar om diezelfde kwaliteit van ventiel tot ventiel.
Ook temperatuurverandering is van belang. We hebben consistente prestaties nodig bij hogere temperaturen en stroomsnelheden. Er ligt nu meer nadruk op de productie van 3D NAND-chips, wat betekent dat er meer materialen in diepere spleten op chips worden gelaagd omdat transistors op elkaar worden gestapeld, dus je moet meer precursormedia op de wafer gedoseerd krijgen - misschien 200 keer zoveel gas - om deze locaties effectief te coaten. Er zijn steeds krappere toleranties, en dat betekent minder ruimte voor variabiliteit.
"Om de volgende fase van chipproductie te bereiken, hebben we betrouwbare productcontrole, herhaalbaarheid en consistentie van klepproductie nodig."
SRP: Naast nauwkeurige dosering, temperatuurstabiliteit en stroomcapaciteit, wat heeft de industrie nog meer nodig van UHP-kleppen om te blijven voldoen aan de wet van Moore?
CW: We moeten ook gefocust blijven op reinheid en corrosiebestendigheid. Materiaalwetenschap is hier belangrijk. De ALD20-klep gebruikt bijvoorbeeld Alloy 22 (Hastelloy ® C22) in de balg, want dat is een materiaal dat bestand is tegen sterk corrosieve chemicaliën. Maar hoe geweldig het ook is, zelfs dit materiaal is niet ideaal in elk proces. Er kan een speciale coating nodig zijn om verschillende chemische stoffen aan te kunnen, aangezien de geometrieën kleiner worden en de voorloperchemicaliën agressiever worden. Het ontwikkelen van deze coatings kan moeilijk en duur zijn, maar we hebben steeds minder tolerantie voor corrosie in onze processen.
Daarom is het van cruciaal belang dat leveranciers van vloeistofsysteemoplossingen nauw samenwerken met zowel OEM- als halfgeleiderfabrikanten bij het ontwikkelen van nieuwe producten. Samenwerking was belangrijk toen Swagelok decennia geleden de eerste ALD-kleppen introduceerde, en het blijft belangrijker dan ooit. Soms betekent dit dat u moet werken met OEM's van gereedschappen, maar aangezien de eisen aan hun gereedschappen worden bepaald door chipfabrikanten, moet u soms ook rechtstreeks met de fabs werken. Het gaat erom samen problemen op te lossen en uit te zoeken wat zinvol is op basis van de ontwikkelingscycli van de betrokken bedrijven. Maar het is deze samenwerking die de technologie van morgen mogelijk maakt.
SRP: Hoe zag de samenwerking met leveranciers eruit tijdens je carrière? Hoe heb je het persoonlijk ervaren?
CW: In het begin van mijn carrière, toen ik bij ASM werkte, werkte ik samen met Swagelok aan de ontwikkeling van de Swagelok ® DH serie UHP membraanafsluiter. We hadden een klep nodig die zou presteren in een vacuüm bij 220º C en kleiner was dan wat er destijds op de markt was, zodat we meer kleppen in een kleine ruimte konden plaatsen om betere prestaties van onze ALD-gereedschappen te krijgen. Ik werkte met Swagelok Southwest en de bedrijfstechnische afdeling van Swagelok om opties te testen, en we kwamen uiteindelijk tot een geweldige oplossing. Het resultaat was een membraanklep met een ontwerp met dubbele zuiger, een nieuw smeermiddel om verontreiniging in een vacuümkamer te voorkomen en een extreme temperatuurbestendigheid die meer dan 10 miljoen cycli zou aanhouden.
Het was ook nuttig dat het Swagelok-team transparant was en bereid was om gedurende het hele proces testprotocollen en gegevens te delen, wat niet altijd het geval is met andere fabrikanten. Ook, zoals altijd het geval is bij gezamenlijke inspanningen, maken de mensen het verschil. Je wilt werken met mensen die het je gemakkelijk maken om van je werk te genieten, en het team waarmee ik aan dit project heb gewerkt was top. In mijn carrière in de halfgeleiderindustrie heb ik altijd gezocht naar zakelijke contacten die een win-winsituatie willen bij het omgaan met hun klanten, niet alleen een "wij winnen". Beide soorten bedrijven zijn er, dus ik heb altijd zorgvuldig gekozen.
SRP: Wat is de toekomst voor de halfgeleiderindustrie? Welke uitdagingen moeten worden overwonnen en wat kunnen we in de nabije toekomst verwachten?
CW: Een uitdaging voor de industrie zal zijn om aan de schaalbehoeften te voldoen. Nu we ons op 7 nm of 5 nm procesknooppunten bevinden, waar gaan we dan heen? Zijn de materialen en productiemogelijkheden aanwezig om de technologie verder te miniaturiseren? 3D NAND-stapeling is één oplossing:we zien meer halfgeleiders op elkaar gestapeld, waardoor drie keer het aantal transistors in één gebied kan worden verpakt in vergelijking met wat traditioneel is gedaan. Er wordt gewerkt aan nieuwe technologie om dit te vergemakkelijken, zoals selectieve depositie-technologie waarmee je alleen kunt deponeren waar je wilt op een wafer, in plaats van het hele oppervlak te coaten.
Ook de materialen veranderen. De industrie kijkt naar siliciumcarbide als basis voor wafels in plaats van silicium. Silicium is gemakkelijk te vinden en goedkoop, dus het werd op grote schaal toegepast, maar we konden zien dat materialen zoals germanium weer in gebruik komen, omdat verschillende materialen nodig zijn om transistors van stroom te voorzien in kleine afmetingen. Andere snelle, veelbelovende materialen zijn in de loop van de tijd onderzocht, maar de fabricageprocessen of chipvereisten hebben deze dure speciale materialen misschien niet economisch levensvatbaar gemaakt. Nu hebben we ze misschien nodig.
Niet alleen wafelmaterialen zullen moeten veranderen, maar ook onze processen:wat we deponeren, hoe we etsen, enzovoort. Nieuwere methoden zoals extreme ultraviolet lithografie (EUV) worden gebruikt, maar zodra we beginnen te werken aan transistors kleiner dan 5-3 nm, zal dat misschien niet veel langer werken. De kosten worden exponentieel hoger naarmate u kleiner wordt, dus we kunnen zien dat meer gespecialiseerde providers vasthouden aan het proberen bij te blijven met de wet van Moore in plaats van iedereen, omdat het te duur wordt om dit te doen.
SRP: Bedankt voor het perspectief, Carl. Heeft u nog een laatste wijsheid voor halfgeleiderprofessionals die het soort rollen vervullen dat u in het verleden hebt bekleed?
CW: Als één ding zeker is, is het dat we vooruitgang zullen blijven zien, ook al kunnen we nog niet altijd zien hoe het zal plaatsvinden. Het enige waar u op kunt rekenen, is de behoefte aan sterke relaties en samenwerking om te komen waar u heen wilt.
Wanneer u een gespecialiseerde behoefte heeft, is het niet altijd zo eenvoudig als een product van de plank kopen om hieraan te voldoen; soms moet je samenwerken met partners om een oplossing van de volgende generatie te ontwikkelen. Als u dat doet, zoek dan naar bedrijven die de technische capaciteiten en de collaboratieve mentaliteit hebben om u te helpen waar u heen wilt. U hebt medewerkers nodig die naar uw behoeften luisteren, nooit iets beloven wat ze niet kunnen doen, en die geen kwaliteit opofferen om u gelukkig te maken. Het is een risico dat u bij veel bedrijven loopt als u snel handelt, dus leer wie u kunt vertrouwen. Het opbouwen van relaties is het beste wat je kunt doen om resultaten op te bouwen.
“... zoek naar bedrijven met de technische capaciteiten en de manier van samenwerken om u te helpen waar u heen wilt. Je hebt medewerkers nodig die naar je wensen luisteren…”
SRP: Dank je, Carl! We stellen het op prijs dat u de tijd heeft genomen om uw kennis vandaag met ons te delen.
CW: Graag gedaan. Ik ben blij om te helpen.
Industriële technologie
- Digitale transformatie en de toekomst van de papierindustrie
- Het internet der dingen en de toekomst van productie
- Het verleden, het heden en de toekomst van LPWAN
- MFGis the Future:Phil Pasma
- Koolstofvezels:verleden, heden en toekomst
- Koolstofvezel in de lucht- en ruimtevaartindustrie:verleden, heden en toekomst
- Hoe ziet de toekomst van productie eruit?
- Milieu-impact van de productie van halfgeleiders en elektronica
- De toekomst van productie:top 7 trends in de sector
- Industrie 4.0-implementatie-uitdagingen in de lucht- en ruimtevaart- en defensieproductie
- Automatisering en de toekomst van digitale productie?