Lekken in het vloeistofsysteem detecteren en voorkomen
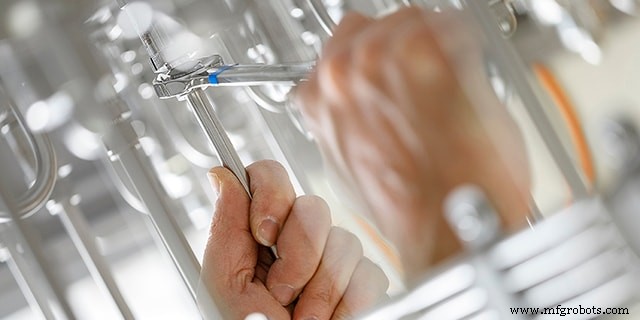
Veelvoorkomende oorzaken en kosten van vloeistoflekkage
Nick Iverson, Field Engineer, Noord-Amerika
Lekkage in het vloeistofsysteem is een veelvoorkomend verschijnsel in de meeste fabrieken. Omdat u verantwoordelijk bent voor het handhaven van de veiligheid en winstgevendheid van uw fabriek, kan zelfs het kleinste lek een probleem vormen. Daarom is het nuttig om te begrijpen hoe en waarom lekken optreden, hoe u ze kunt lokaliseren en testen, en uiteindelijk hoe u een strategie kunt ontwikkelen om lekken in de hele fabriek aan te pakken en te verminderen.
De kosten van lekken
Hoewel lekken vaak voorkomen in fabrieken, zijn er veel financiële redenen om lekken snel aan te pakken en een plan te ontwikkelen om toekomstige lekken te voorkomen.
- Elk jaar worden er naar schatting miljoenen liters hydraulische vloeistoffen verspild. Een enkele gallon hydraulische vloeistof kost ongeveer $ 40 USD.
- Verlies van vloeistofsmering kan leiden tot kostbare schade aan apparatuur, zoals voortijdige slijtage en machinestoringen.
- Planten verminderen hun productie-outputpotentieel elke keer dat ze een proces stopzetten om een lek te verhelpen. Deze uitvaltijd kan leiden tot aanzienlijk winstverlies.
- Uw team kan per ongeluk een product produceren dat niet aan de specificaties voldoet als gevolg van onjuiste instrumentkalibratie of bediening vanwege een lek. Dat materiaal moet dan opnieuw worden bewerkt, tegen een gereduceerde prijs worden verkocht of worden weggegooid.
- Oliedruppels van lekkage kunnen leiden tot een onveilige werkomgeving, met uitglijden en ongelukken tot gevolg. Vluchtige emissies kunnen ook duur zijn om te repareren en gevaarlijk voor de gezondheid van uw werknemers.
- Lekken kunnen leiden tot ernstige boetes voor niet-naleving als systemen en apparatuur de veiligheidsvoorschriften schenden.
- Het kost tijd en geld om lekken op te sporen en te repareren. Mogelijk moet u een speciaal team inhuren om giftige chemische lekken te beheren, wat mogelijk de kosten van een systeemonderbreking voor grondige inspectie met zich meebrengt.
Drie veelvoorkomende oorzaken van lekkage van het vloeistofsysteem
Het is misschien verrassend om te horen dat de meeste lekken niet het gevolg zijn van onderdelen die niet aan de normen voldoen. Ze treden eerder op als gevolg van menselijke fouten, hetzij door de installatie van een onderdeel of door de onderdeelselectie zelf. Het kiezen van de juiste componenten en het correct installeren ervan kan de veiligheid van de fabriek verbeteren en veel tijd en kosten besparen.
Om uw team te helpen lekken in uw fabriek beter te begrijpen en te verminderen, hebben de veldingenieurs van Swagelok de volgende drie meest voorkomende oorzaken van lekken gedocumenteerd:
- Onbetrouwbare metaal-op-metaal afdichtingen: Het maken en houden van zeer betrouwbare metaal-op-metaal afdichtingen kan moeilijk zijn, vooral na verloop van tijd. De richtlijnen van de fabrikant moeten nauwkeurig worden gevolgd om lekken te voorkomen bij het gebruik van deze afdichtingen. In sommige gevallen met kleppen wilt u misschien zelfs het onderdeel vervangen door een onderdeel met een zachte zittingafdichting, vooral wanneer het herhaaldelijk moet worden afgesloten van het gas.
- Onjuist geïnstalleerde buisfittingen: Door buisfittingen op de juiste manier te monteren, wordt de kans op lekkage aanzienlijk verminderd en de veiligheid van uw installatie vergroot. Zorg ervoor dat uw technici zijn getraind in het correct maken van een fitting, inclusief het correct oriënteren van de adereindhulzen en het gebruik van een spleetmeter om de juiste hoeveelheid pull-up te controleren.
- Slechte selectie, behandeling en voorbereiding van slangen: Uw slangkeuze en voorbereiding kan ook uw lekpotentieel vergroten. Slangmaterialen die niet compatibel zijn met de procesvloeistof of de externe omgeving zijn vatbaar voor corrosie, voortijdig falen en lekken. Bovendien kunnen ongelijk gesneden buizen of buizen die zijn ingedeukt, bekrast of niet zijn ontbraamd, de afdichting van de fitting in gevaar brengen.
Drie soorten lekken
Als u het type lek begrijpt, kan uw team de juiste corrigerende maatregelen bepalen om het aan te pakken. Hieronder identificeren de ingenieurs van Swagelok de drie soorten lekken die vaak voorkomen in vloeistofsystemen:
Echt lek: Een lek als gevolg van het falen van een drukbarrière om een systeemvloeistof te bevatten of te isoleren van de omgeving. Dit komt door scheuren in het materiaal of openingen tussen afdichtingsoppervlakken.
Virtueel lek: Het vrijkomen van inwendig opgesloten vloeistof in een vloeistofsysteem als gevolg van ontgassing van materiaal, geabsorbeerde of geadsorbeerde vloeistoffen, opsluiting in spleten of dode benen.
Permeatie: Een passage van vloeistof in, door en uit een drukbarrière die geen gaten heeft die groot genoeg zijn om meer dan een kleine fractie van de moleculen door een enkel gat te laten gaan.
Lekdetectiemethoden
Over het algemeen worden de meeste lektests uitgevoerd op een systeem onder druk - ofwel met echte procesvloeistof of met een surrogaatvloeistof zoals water, lucht, stikstof of helium. Voor praktische doeleinden kunnen testmethoden worden onderverdeeld in methoden die doorgaans worden uitgevoerd op geïnstalleerde apparatuur en methoden die vaker worden uitgevoerd op een werkbank (of in het laboratorium).
- Visuele tests: Dit is het meest fundamentele type lektest voor een vloeistofsysteem. Lekkages worden aangegeven door daadwerkelijke druppels of oppervlaktebevochtiging onder de lekken. Het wordt meestal uitgevoerd op geïnstalleerde apparatuur, maar het wordt ook vaak gebruikt op een tafel om slangassemblages te testen.
- Bubbeltesten: Dit is een eenvoudige, kosteneffectieve test voor gassystemen. Deze test maakt gebruik van een dunne film oppervlakteactieve stof (zoals Snoop) of onderdompeling in een waterbad. Het is een veel voorkomende test op zowel geïnstalleerde apparatuur als op een tafelmodel. Het wordt meer gebruikt om de aanwezigheid van een lek aan te geven dan om de hoeveelheid te meten en het vereist observatie op luchtbellen.
- Drukveranderingstests: Deze test wordt gebruikt voor zowel vloeistof als gas. De te testen apparatuur wordt gedurende een voorgeschreven tijd in een geïsoleerde toestand onder een voorgeschreven druk onder druk gezet. Lekkage resulteert in een geleidelijke drukval die meetbaar is. Een veelvoorkomend type drukveranderingstest is drukverval. Het wordt vaker uitgevoerd op een tafelblad, maar het kan ook worden uitgevoerd op geïnstalleerde apparatuur met zorgvuldige overwegingen om het ontwerp te testen. Deze test vereist minimale apparatuur en kan worden geautomatiseerd.
- Lucht ultrasone testen: Deze test wordt gebruikt op gassystemen. Het vereist een ultrasoon meetapparaat in de lucht dat kan worden gebruikt om de aanwezigheid van een lek te lokaliseren. Voor systemen onder druk kan deze test worden gebruikt om de leksnelheid te benaderen. Deze test kan ook worden uitgevoerd op niet onder druk staande systemen door gebruik te maken van een extra, binnenboord, geluidgenererend apparaat. Ultrasoon testen in de lucht wordt vaak gebruikt op geïnstalleerde apparatuur.
- Massaspectrometrie testen :Deze test wordt gebruikt op gassystemen. Een massaspectrometer wordt gebruikt om de aanwezigheid van sporen van gelekt gas te detecteren en de lekkage te kwantificeren. Het wordt bijna uitsluitend uitgevoerd met helium als surrogaat, in welk geval het Helium Leak Testing wordt genoemd. Buitenboordtests worden gebruikt voor systemen onder druk, terwijl binnenboordtests worden gebruikt voor vacuümsystemen. Deze methode wordt het meest gebruikt op werkbladen om zeer kleine lekken te identificeren.
Prioriteit geven aan lekken
Hoewel het niet mogelijk is om elk type lek in een fabriek meteen aan te pakken, kan uw team lekken categoriseren om prioriteit te geven aan onderhouds- en reparatiemogelijkheden.
- Gevaarlijke lekken: Elk lek dat een veiligheidsprobleem vormt, moet een topprioriteit zijn. Dit omvat lekken van schadelijke gassen en bijtende chemicaliën, evenals lekken die slip-/valgevaren veroorzaken. Laat uw risicomanagers eerst deze veiligheidsproblemen identificeren en stuur vervolgens uw beste onderhoudstechnici om ze meteen op te lossen.
- Dure lekken: Gezamenlijk kunnen alle lekken in uw installatie aanzienlijke kosten met zich meebrengen. Sommige lekken, zelfs kleine, kunnen echter verantwoordelijk zijn voor een aanzienlijk percentage van die kosten. Het repareren van een klein lek van duur argongas kan bijvoorbeeld drastisch grotere besparingen opleveren in vergelijking met het dichten van een groot lek van goedkopere perslucht. Ontdek hoe lekbesparingen snel kunnen oplopen.
- Overlast lekken: Ten slotte kunt u een breed scala aan kleine lekken hebben die geen veiligheidsrisico's opleveren en niet verantwoordelijk zijn voor grote verliezen. U kunt wachten om deze lekken met lage prioriteit aan te pakken wanneer uw onderhoudspersoneel niet wordt geplaagd met andere, meer kritieke taken.
We vinden het nuttig om ingenieurs en technici op te leiden – en om te scholen – in een verscheidenheid aan onderwerpen om hun vaardigheden bij het identificeren en aanpakken van verschillende soorten lekken te verbeteren. Training kan alles omvatten, van onderwijs over de juiste materiaalkeuze tot praktische cursussen voor het opbouwen van vaardigheden in het buigen van buizen en installatieprocedures voor buisfittingen. Gelukkig biedt Swagelok veel gespecialiseerde training- en opleidingsprogramma's om ervoor te zorgen dat uw fabriek veilig en efficiënt werkt. Wanneer uw getrainde team zich richt op het identificeren en stoppen van lekken, zal uw fabriek veiligere, meer kosteneffectieve operaties realiseren.
Neem contact op met uw lokale Swagelok-verkoop- en servicecentrum voor meer informatie over het identificeren en aanpakken van lekken en voor het trainen van uw team in best practices.
Industriële technologie
- Een algoritme trainen om vroege blindheid te detecteren en te voorkomen
- Een HACCP-plan maken om veiligheidsrisico's en terugroepacties te voorkomen
- Vier soorten cyberaanvallen en hoe u ze kunt voorkomen
- 5 technologieën om pompcavitatie te detecteren en te voorkomen
- Wat is lasporositeit en hoe kan dit worden voorkomen?
- Plannen voor en investeren in een nieuw CAD/CAM-systeem
- Belangrijkste oorzaken van machinestoringen en hoe ze te voorkomen
- Waarom en hoe een vacuümaudit uit te voeren?
- Lekken opsporen en verhelpen
- Hoe belangrijk is vloeistofzuiverheid in een hydraulisch systeem?
- Hoe de betrouwbaarheid van het hydraulische systeem te verbeteren