3 belangrijke componenten van strakke, functionele spuitgegoten ontwerpen
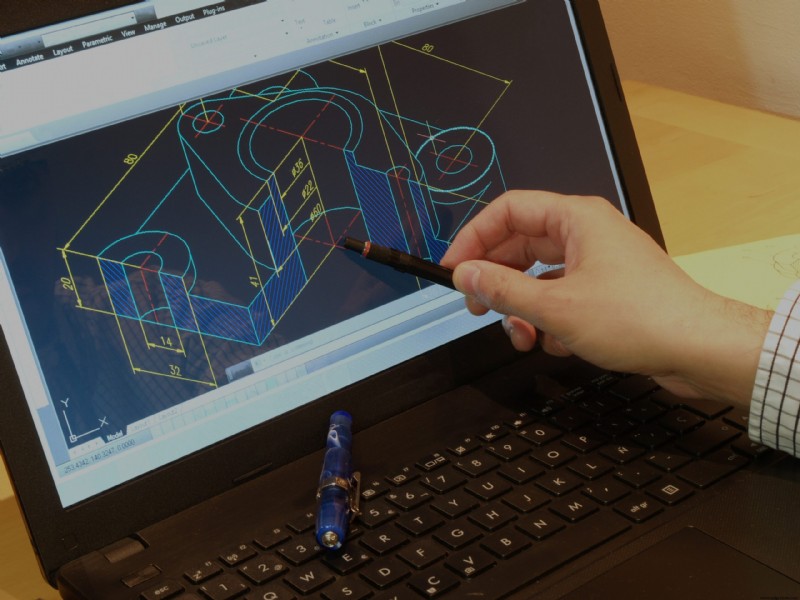
Spuitgieten is een populair productieproces voor de massaproductie van identieke kunststof onderdelen met goede toleranties. Tijdens dit proces worden thermoplastische vlokken of pellets omgesmolten en in een mal gespoten. Zodra het thermoplastische materiaal afkoelt en hard wordt, schieten de uitwerppennen het voltooide onderdeel uit de mal. Veel van de consumentenproducten die mensen dagelijks gebruiken, zijn spuitgegoten, van telefoonopladers tot auto-onderdelen tot Lego®-stenen.
Zodra de matrijs is vervaardigd, hebben ingenieurs een middel om complexe onderdelen consistent te reproduceren tegen zeer lage kosten per eenheid. Als zodanig is het perfectioneren van de malproductieprocessen van cruciaal belang. Hier is een spoedcursus voor het optimaliseren van het ontwerp van een spuitgegoten onderdeel — plus tips en trucs voor productontwerpers.
Drie tips en best practices voor het ontwerpen van spuitgietmatrijzen
Spuitgegoten onderdelen kunnen complexe geometrieën hebben en bieden productontwerpers een behoorlijke hoeveelheid ontwerpflexibiliteit. Het enige voorbehoud is dat productteams hun onderdelen moeten ontwerpen rond de specifieke vereisten van spuitgieten.
Het is een hele uitdaging om ontwerpaanpassingen te maken nadat het onderdeel al is vervaardigd. Als zodanig moeten productontwerpers het plastic onderdeel perfect ontwerpen voor spuitgieten om het risico op problemen met het gereedschapsontwerp te verminderen, de beste resultaten te behalen en de kosten te verlagen. Om schone, functionele onderdelen te ontwerpen, begint u met deze drie best practices voor spuitgieten:
1. Zorg voor consistente wanddiktes
De belangrijkste regel voor het ontwerp van spuitgietonderdelen is het beheren van de dikte van de mal. Niet-uniforme wanden kunnen ervoor zorgen dat het onderdeel kromtrekt als het thermoplastische materiaal afkoelt of dat er zinkvlekken ontstaan. Aanbevolen wanddiktes variëren afhankelijk van de gebruikte kunststof. Polyurethaan (PUR) heeft bijvoorbeeld een aanbevolen wanddikte van 0,080 inch tot 0,750 inch, terwijl polystyreen (PS) een veel kleiner bereik heeft van 0,035 inch tot 0,150 inch. Een goede vuistregel is om de wanddikte van een bepaalde mal tussen 1,2 mm en 3 mm te houden.
Als het onderdeel is ontworpen om verschillende diktes te bevatten, moeten productontwerpers de overgang daartussen zo soepel mogelijk maken. Dit zorgt ervoor dat het gesmolten plastic gelijkmatig in de vormholte stroomt. Een afschuining of filet die 3x zo lang is als het verschil in dikte zou voldoende moeten zijn.
Dikke secties in een spuitgietontwerp kunnen kromtrekken, zinken en andere defecten veroorzaken, maar soms zijn ze nodig voor complexe geometrieën. Productontwerpers kunnen dikkere secties in hun mallen opnemen terwijl ze zich houden aan de wanddiktebeperkingen door deze secties uit te hollen. Het opnemen van ribben in het onderdeel versterkt de holle delen en zorgt voor stijfheid.
De dikte van de ribben varieert afhankelijk van de gebruikte thermoplast, maar de ribben moeten altijd minder dan twee derde van de hoofdwanddikte zijn. Als de ribbe te dik is, veroorzaakt dit verzakkingen op het buitenoppervlak.
2. Elimineer ondersnijdingen die niet ontwerpkritisch zijn
Ondersnijdingen zijn kenmerken die voorkomen dat het spuitgegoten onderdeel netjes uit de mal wordt geworpen zonder enige structurele schade. Ondersnijdingen kunnen in verschillende vormen voorkomen:gaten, holtes of gebieden waar de uitlijning niet loodrecht op de scheidingslijn van de mal staat. De beste gok van een productontwerper is om ondersnijdingen helemaal te vermijden. Ze maken het ontwerp van de spuitgietmatrijs altijd duurder, gecompliceerder en arbeidsintensiever dan nodig is.
Toch zijn er een paar ontwerptrucs om ondersnijdingen aan te pakken. De eenvoudigste manier om een ondersnijding te fixeren, is door de scheidingslijn van de mal zo te verplaatsen dat deze de ondersnijding kruist. Deze tip is echter alleen van toepassing op ontwerpen met ondersnijdingen aan de buitenkant van de mal.
Bumpoffs, of het strippen van ondersnijdingen, zijn een optie als het kenmerk en het materiaal flexibel genoeg zijn om tijdens het uitwerpen over de mal uit te zetten en te vervormen. De bumpoff moet ver weg zijn van de ondersteunende structuren van de mal en een hellingshoek hebben tussen 30 en 45 graden.
Als laatste redmiddel kunnen side-actions of lifters ondersnijdingen repareren wanneer de mal niet opnieuw kan worden ontworpen om ondersnijdingen te voorkomen. Zijdelingse kernen zijn loodrechte inzetstukken die in en uit de mal schuiven als deze open en dicht gaat. Deze mechanismen verhogen de kosten en complexiteit aanzienlijk. Zelfs met deze oplossingen zouden ontwerpers ondersnijdingen helemaal vermijden en ondersnijdingen elimineren tijdens prototyping.
3. Ontwerp, concept, concept
Trekhoeken zijn ontwerpoverwegingen die het gemakkelijker maken om een spuitgegoten onderdeel netjes uit de mal te werpen. Dit klinkt misschien als een niet-essentieel ontwerpkenmerk, maar ontwerpen zijn van cruciaal belang voor het vervaardigen van functionele spuitgegoten onderdelen. Tochten helpen voorkomen dat het onderdeel beschadigd raakt bij vrijgave, verlagen de productiekosten, versnellen de productietijdlijnen, zorgen voor een uniforme oppervlakteafwerking en bieden een hele reeks andere voordelen. Zonder trekhoeken lopen productteams het risico hun dure mallen te beschadigen en een groot aantal verwerpbare onderdelen te produceren.
Ontwerpen moeten vroeg in het ontwerpproces worden verantwoord. Trekhoeken variëren afhankelijk van een aantal factoren die verband houden met het onderdeel, waaronder wanddikte, wanddiepte, materiaal en eventuele toepasselijke krimpsnelheden, textuur of uitwerpvereisten. Het is het beste om zoveel mogelijk diepgangshoek toe te passen. Productontwerpers moeten om te beginnen één graad diepgang per inch spouwdiepte opnemen, en zo nodig aanpassen voor de bovengenoemde factoren.
Zelfs als het lijkt alsof tocht een negatieve invloed kan hebben op de prestaties van het onderdeel, is het altijd beter tocht te hebben dan geen tocht. Onderdelen kunnen over het algemeen worden ontworpen met een diepgang van minimaal 0,25 graden, maar de kleinst mogelijke diepgang hangt af van de unieke geometrie en het materiaal van het onderdeel.
Krijg hulp van de ontwerpexperts
Deze korte lijst vormt slechts het oppervlak van belangrijke ontwerpoverwegingen voor spuitgegoten onderdelen. Productteams moeten ook rekening houden met factoren zoals scheidingslijnen, poortontwerp, poortlocatie en meer. De beste manier om onderdeelontwerpen te optimaliseren voor kosteneffectiviteit, productietijd en efficiëntie, is door samen te werken met een productie-expert die cruciaal advies kan geven tijdens het ontwerpproces.
De ontwerp- en engineeringexperts van Fast Radius kunnen u helpen om veelvoorkomende pijnpunten in matrijsontwerp te doorbreken, huidige ontwerpen opnieuw te optimaliseren of iets totaal nieuws te creëren. We kunnen u helpen uw ontwikkelingscyclus tot 90% te verkorten en uw time-to-market voor elk product te versnellen. Laten we nieuwe dingen mogelijk maken — neem vandaag nog contact met ons op.
Voor meer informatie over alles wat met spuitgieten te maken heeft, bekijk de gerelateerde blogartikelen in het Fast Radius resource center.
Klaar om uw onderdelen te maken met Fast Radius?
Start uw offerteIndustriële technologie
- Wat is Control Unit:Components &Its Design
- Ontwerpvoordelen van thermoplasten in pomp- en klepcomponenten
- De belangrijkste componenten van goede communicatie in crisissituaties
- Een schoon luchtfilter is de sleutel tot een schone dieselmotor
- Ontwerp voor productie:belang en belangrijkste principes
- Ontwerp van plaatwerkbehuizing:ontwerptips voor belangrijke behuizingen
- 5 belangrijke componenten van een vermogensbeheerkader
- Vlekkeloze prototypes en ontwerpen staan gelijk aan perfecte printplaat
- PCB-ontwerp voor radiofrequentiecircuit en elektromagnetische compatibiliteit
- Vereisten voor stencilontwerp voor QFN-componenten voor optimale prestaties van PCBA
- Spanningsbeheersing bij webverwerking – belangrijkste componenten