De techniek achter het Fast Radius-gezichtsmasker
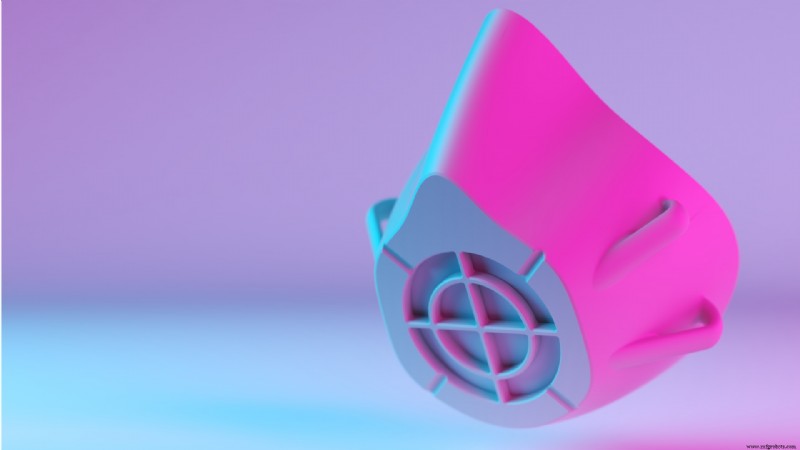
Door Izzy de la Guardia, Application Engineer, Fast Radius
Hoewel de wereldwijde pandemie veel kwetsbaarheden in onze toeleveringsketen aan het licht heeft gebracht, heeft het ook geleid tot innovatie. Met name 3D-printen heeft zowel professionals als hobbyisten in staat gesteld om hun angsten met ongekende snelheid en toegankelijkheid om te zetten in actie. We hebben dit uit de eerste hand ervaren bij het creëren van ons open-source ademhalingstoestelontwerp.
Hier is een kijkje in het proces en hoe we in slechts twee weken vier verschillende prototypes konden maken en drie gebruikerstestsessies konden uitvoeren door gebruik te maken van 3D-printen, een multifunctioneel team en de persoonlijke en professionele netwerken van ons bedrijf.
Snel prototypen en gebruikerstesten
Toen veel Amerikanen medio maart begonnen te schuilen, ontving Fast Radius meerdere verzoeken om 3D-geprinte ademhalingstoestellen te midden van groeiende bezorgdheid over PBM-tekorten. Ik werd op een vrijdagmiddag getikt door onze algemeen directeur, John Nanry, om de ontwerpinspanning te leiden om aan deze behoefte te voldoen. Uren later hadden we ons eerste ontwerp klaar om te printen, geïnspireerd op de open source-ontwerpen van Copper 3D en La Factoría 3D
De belangrijkste focus van ons ontwerp was de maakbaarheid van al onze interne additievenmachines (Stratasys FDM, Carbon DLS™ en HP Multi Jet Fusion) door te zorgen voor de juiste overhanghoeken en vacuümventilatie. We hebben die avond ons eerste prototype op Carbon DLS geproduceerd.
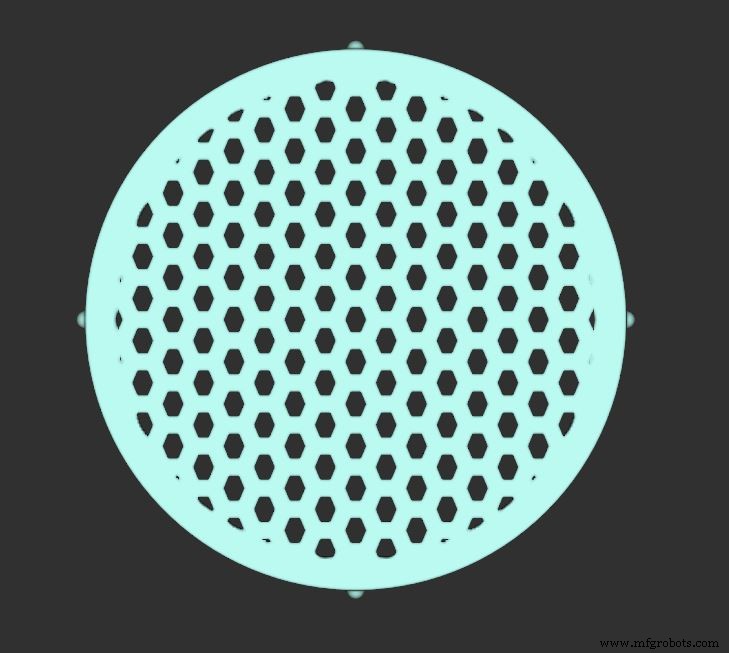
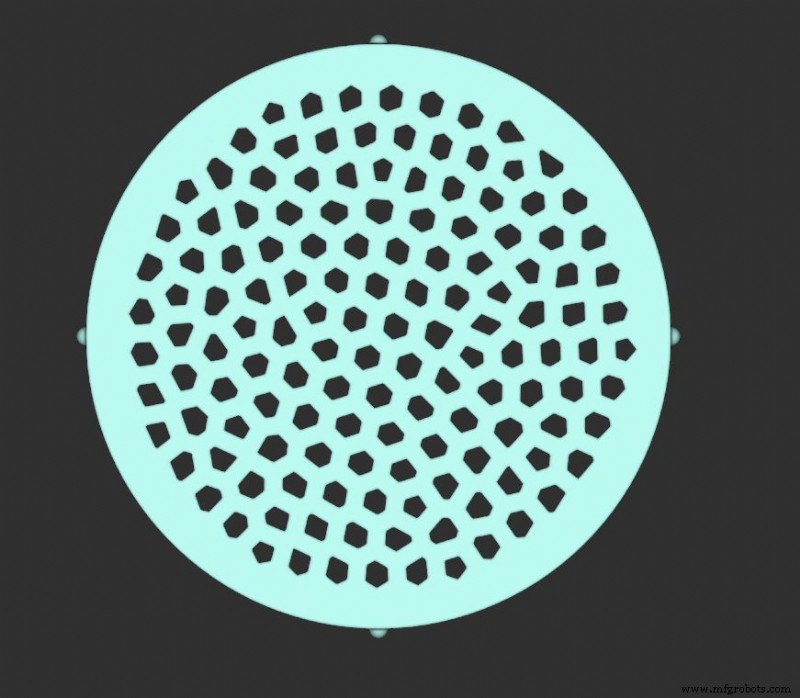
Geavanceerde ontwerptools zoals nTop Platform ondersteunden snelle iteratie, zoals het overschakelen van een voronoi-patroon naar een meer regelmatig hex-patroon dat voor hobby-FDM-printers gemakkelijker te hanteren was
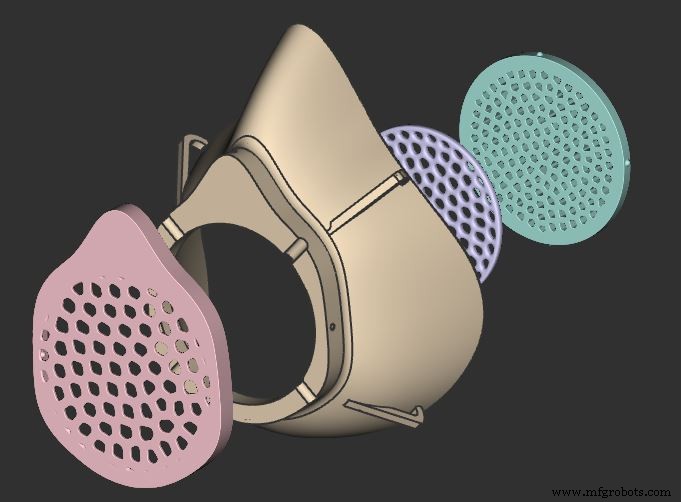
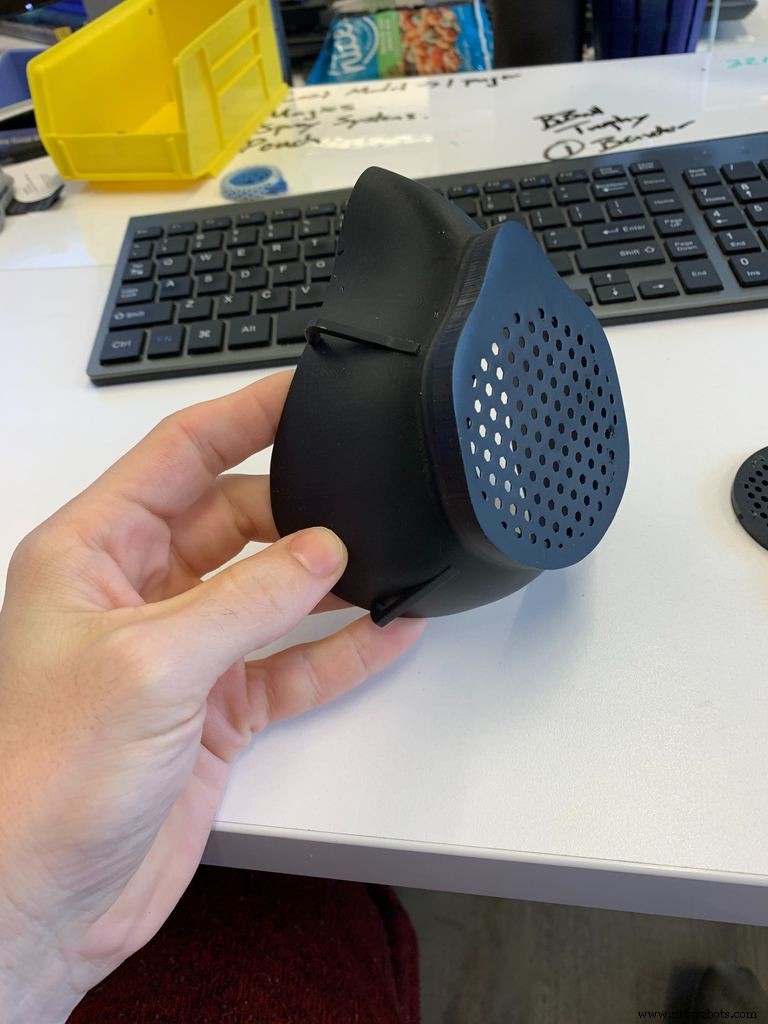
Ons eerste geprinte prototype omvatte FDM-vriendelijke overhangen en kanalen om vacuüm op DLS te voorkomen
Deze prototypes brachten verdere ontwerpwijzigingen met zich mee:het consolideren van de voorkant met het hoofdmaskerlichaam om als één stuk te printen, de riemlussen dikker te maken voor duurzaamheid en de dichtheid van het rasterpatroon te verminderen en het cirkelvormig te maken om gemakkelijker op FDM te kunnen printen. We konden zaterdagavond beginnen met het printen van onze tweede prototypes, slechts 24 uur na aanvang van het project.
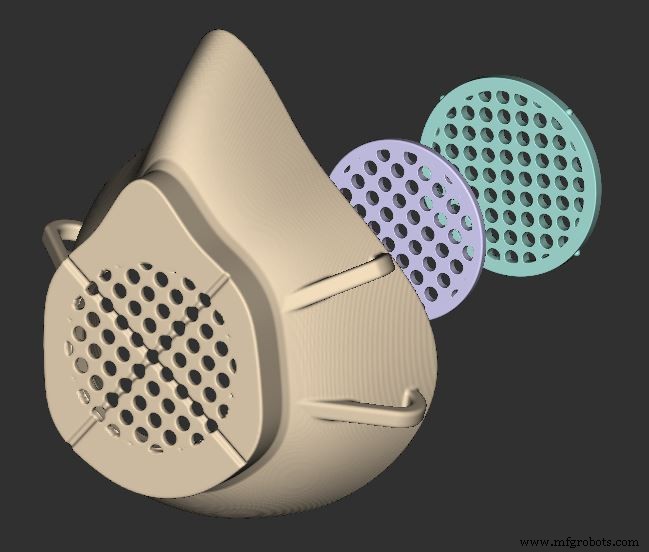
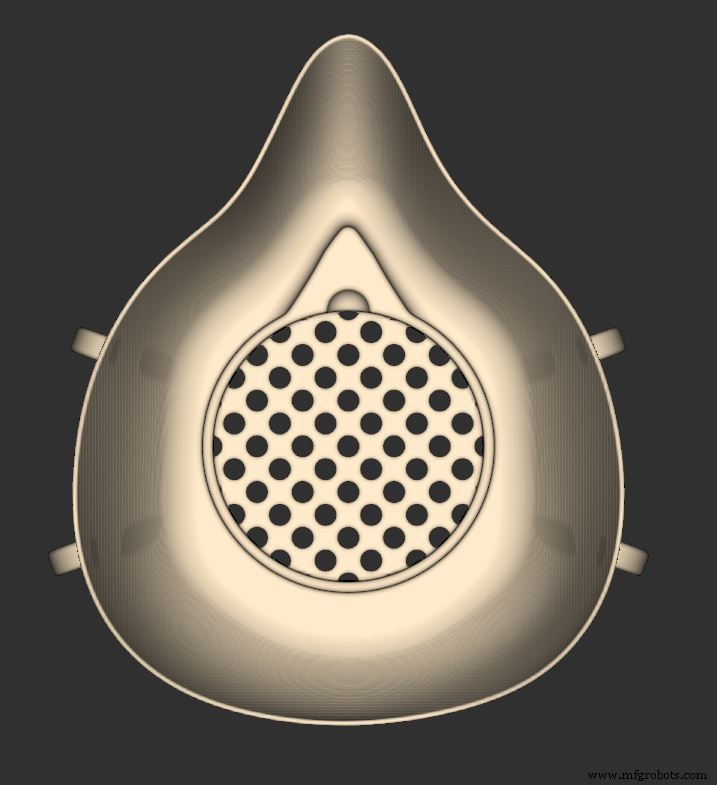
Ons tweede gedrukte prototype ontwerp geconsolideerde onderdelen (links). Binnenkant van masker met uitsparing om de vinger in te steken en het klikfilterdeksel (rechts) eruit te halen.
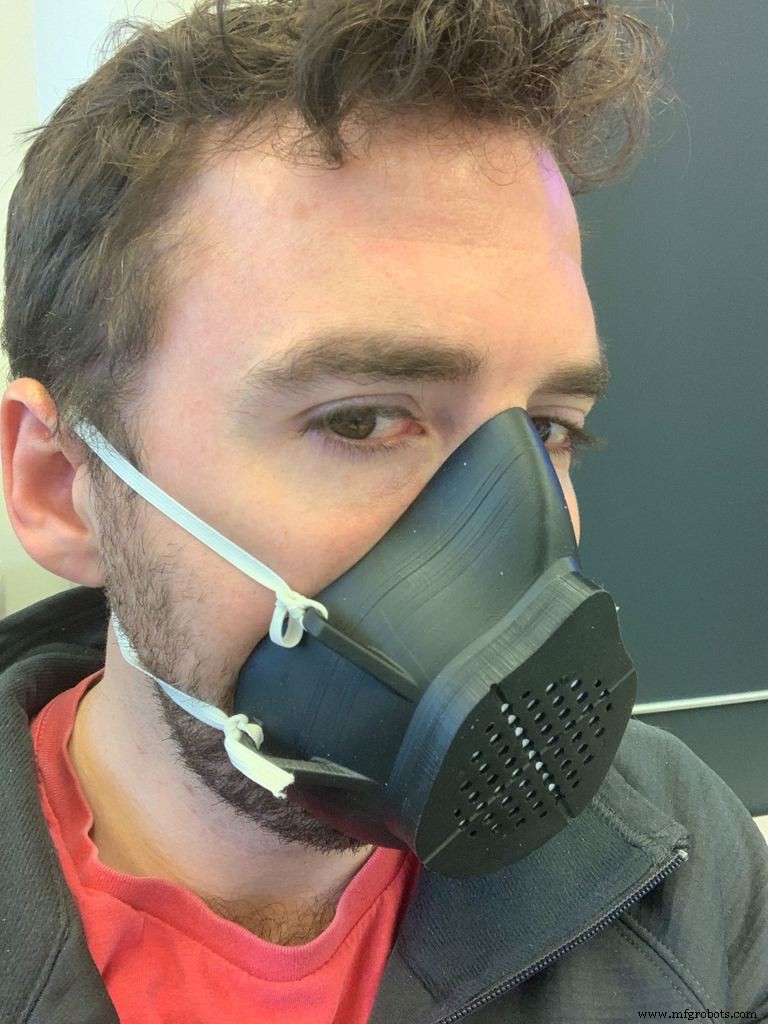
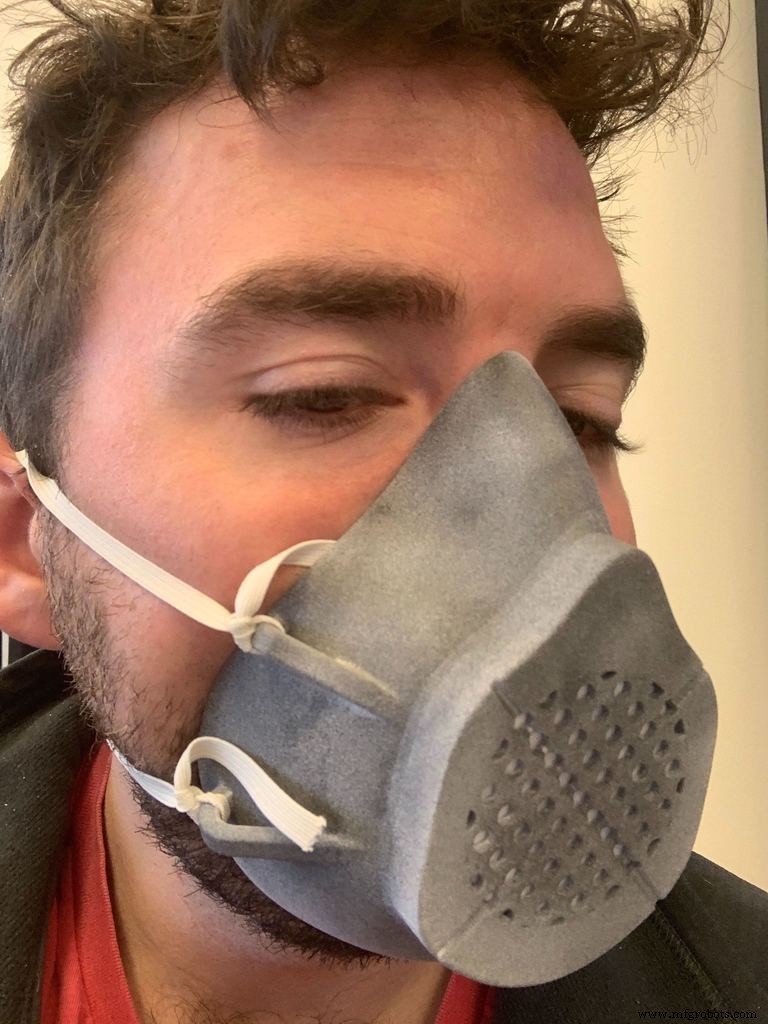
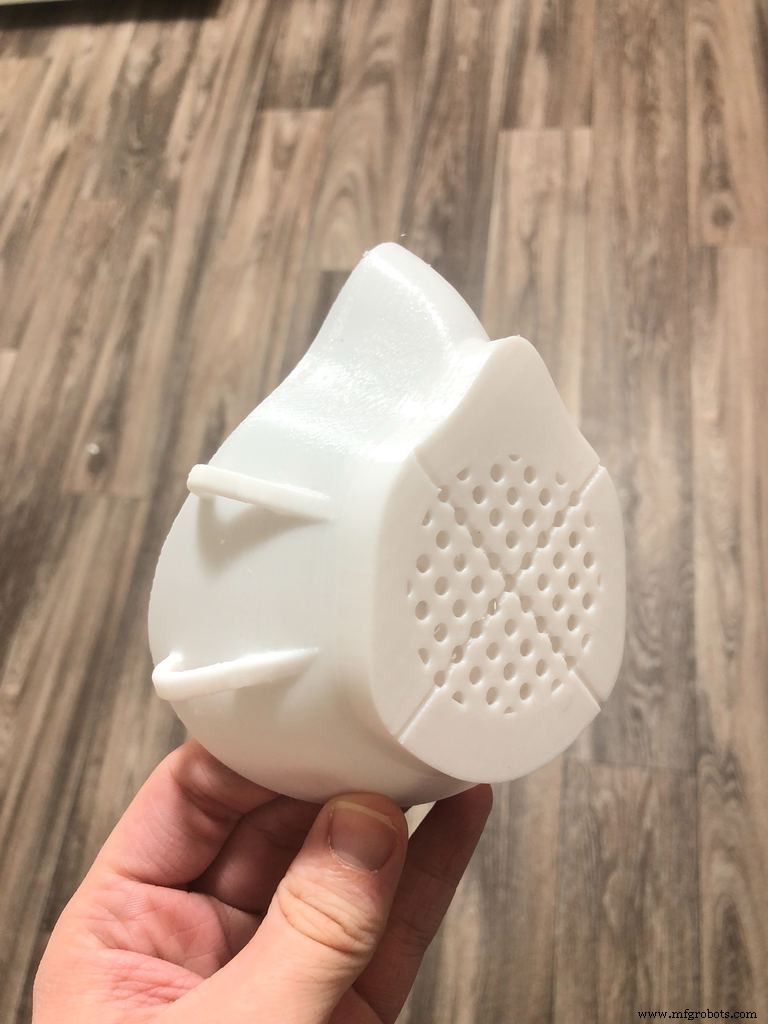
Tweede gedrukte prototype in Carbon RPU70 (links), HP PA12 (midden) en FDM-geprint PLA (rechts)
Parallel met het ontwerpproces hebben we gebruik gemaakt van ons netwerk om de behoefte aan gebruikerstesten beter te begrijpen en individuen te identificeren. In minder dan 24 uur brachten onze vrienden bij P33 ons in contact met een tiental artsen en medewerkers van een medische onderzoeksstichting om meer inzicht te krijgen in N95-maskers. Onze medewerkers namen ook contact op met de medische professionals die ze kenden. Op zondag, slechts twee dagen na de start van het project, voerden we fittests uit met ons tweede prototype bij 10 personen op vier locaties.
De volgende twee weken gingen verder in dit patroon - ontwerpen, afdrukken, testen, herhalen. Ons derde geprinte prototype bevatte een herontwerp van het filterretentiemechanisme. De offset halve cirkel omtrekgeometrie functioneert als een nok die het stuk op zijn plaats vergrendelt wanneer het door wrijving wordt gedraaid (zie hieronder). Er zijn twee lipjes die het deksel naar beneden drukken in de gedraaide of vergrendelde positie om een goede afdichting rond het filter te garanderen. We hebben een versie gemaakt met een hartvormig geperforeerd gebied om het masker minder intimiderend te maken. Beginnend met deze reeks prototypes, hebben we maskers in twee verschillende maten ontworpen en getest.
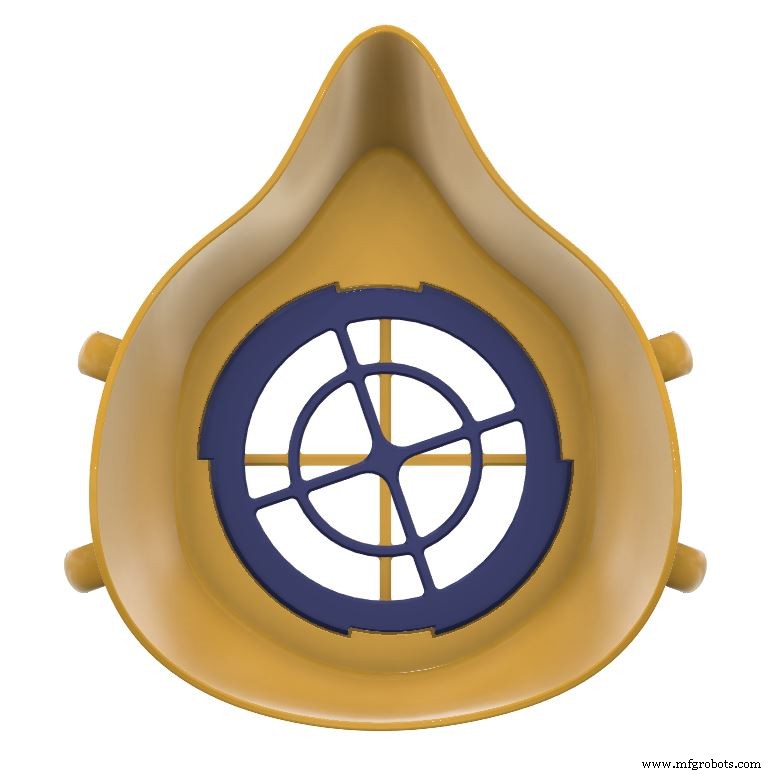
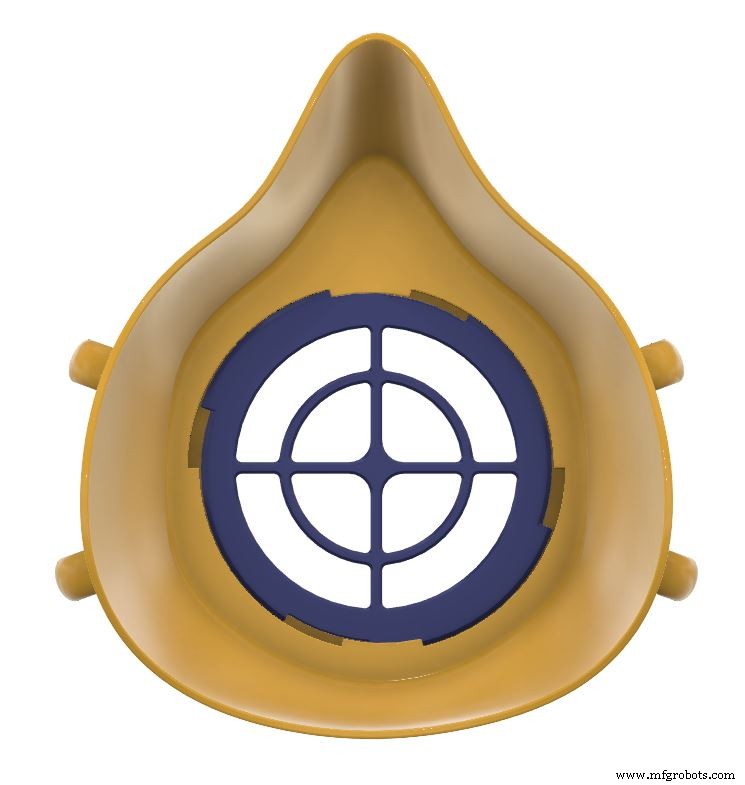
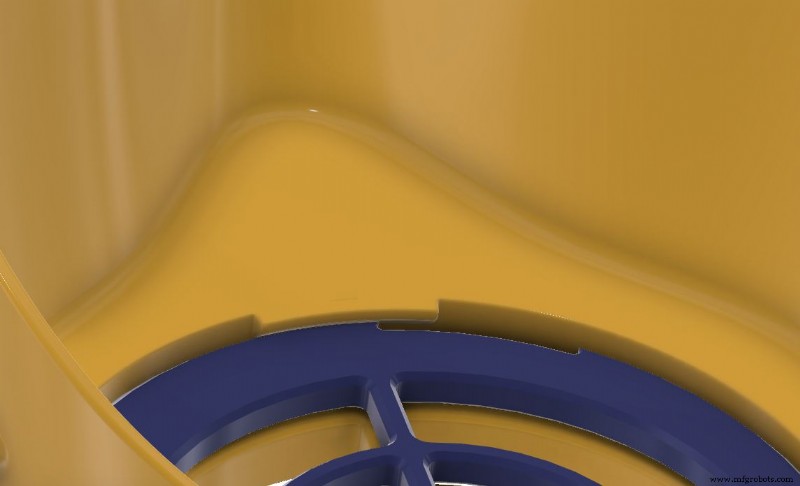
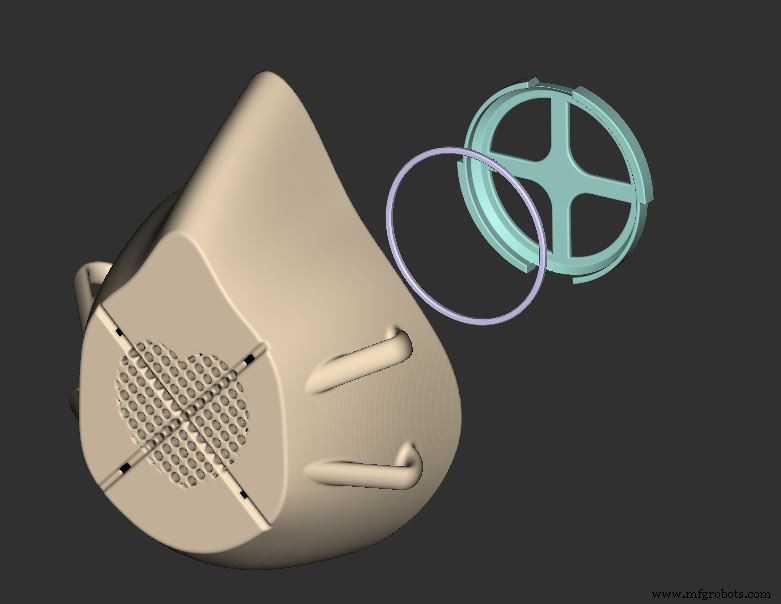
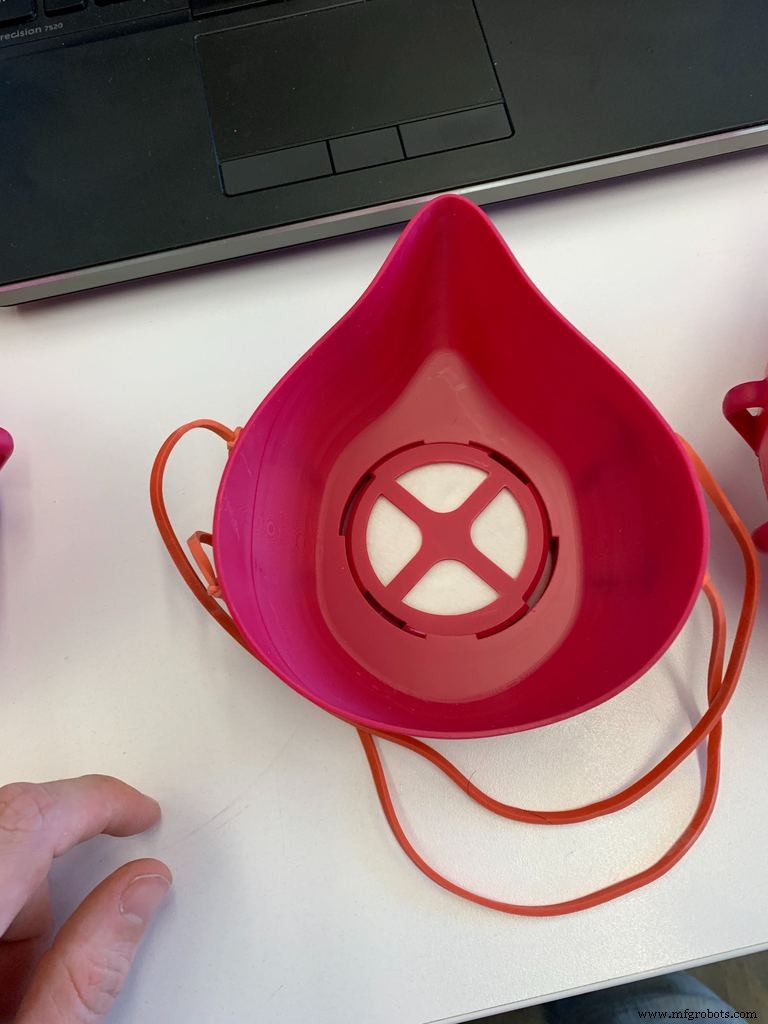
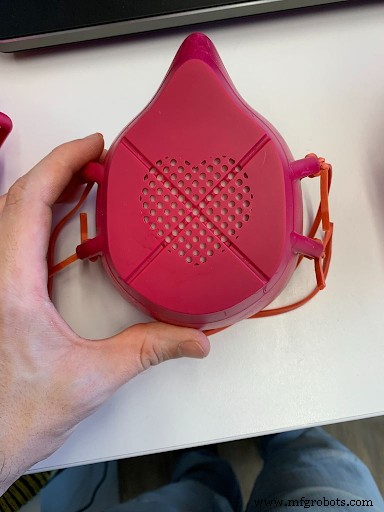
Derde gedrukt prototype ontwerp met draaidop.
Bij het vierde prototype waren we vooral bezorgd over het gemak van ademen en een goede pasvorm. Om dit aan te pakken, hebben we geprobeerd het geperforeerde gebied te maximaliseren en de dichtheid ervan te minimaliseren (helaas verliezen we het hart) om de weerstand tegen de luchtstroom te verminderen. We hebben ook de metingen voor de twee maten aangepast op basis van feedback van gebruikerstests. Op dit moment hadden we voldoende vertrouwen in de functie en de grootte van het masker om versie één uit te brengen als een open source-ontwerp.
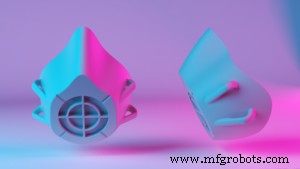
Ontwerp voor toegankelijkheid
Om het masker voor zoveel mogelijk mensen beschikbaar te maken, hebben we een open-sourceontwerp gemaakt dat op huishoudelijke 3D-printers kan worden vervaardigd. Deze beslissing voegde ontwerp- en materiaalbeperkingen toe. Een stijf masker kon zich niet aanpassen aan een grote verscheidenheid aan gezichtsvormen, dus hebben we onderzocht om een flexibel materiaal aan de binnenrand van het masker toe te voegen om de afdichting op het gezicht te verbeteren.
We hebben een prototype gemaakt van een eerste concept met SIL 30 op Carbon DLS. We gingen verder met het testen van vele methoden voor het creëren van een effectieve afdichting van het gezicht (hieronder beschreven), waaronder een gesneden handschoen, bedrukte en gegoten siliconen, vormbaar kostuummateriaal voor gezichtsprotheses, FDM-geprinte TPU- en PLA-afdichtingen en tochtstrips. Uiteindelijk hebben we gekozen voor tochtstrips, die biocompatibel, gemakkelijk schoon te maken en gemakkelijk te verkrijgen zijn.
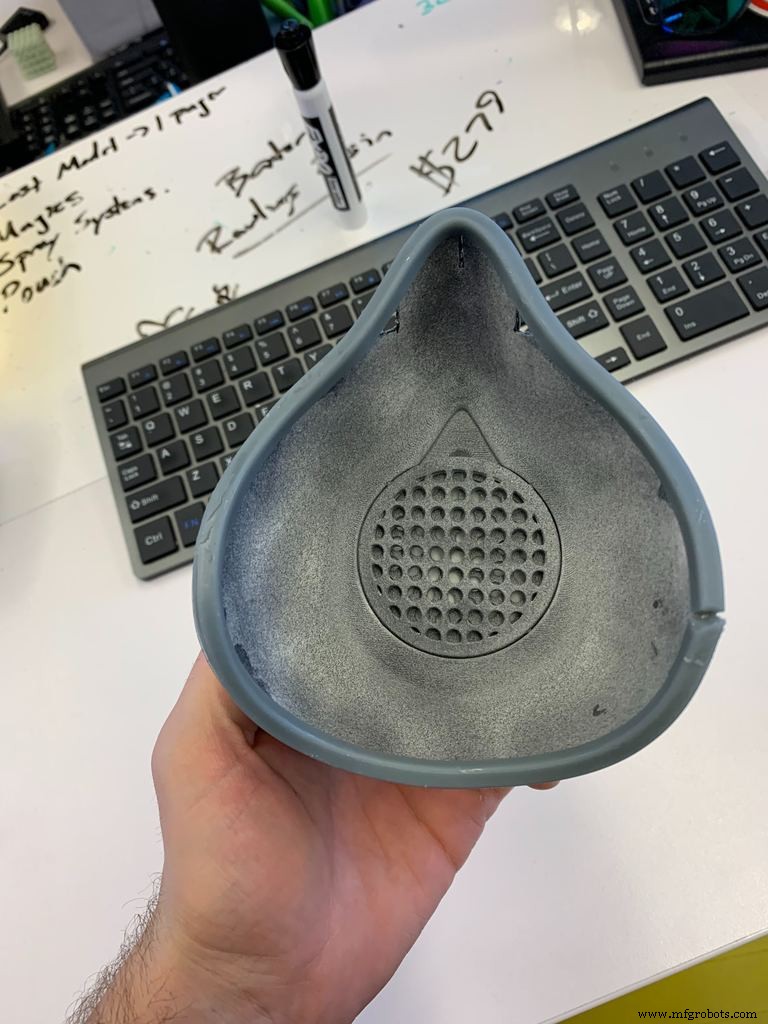
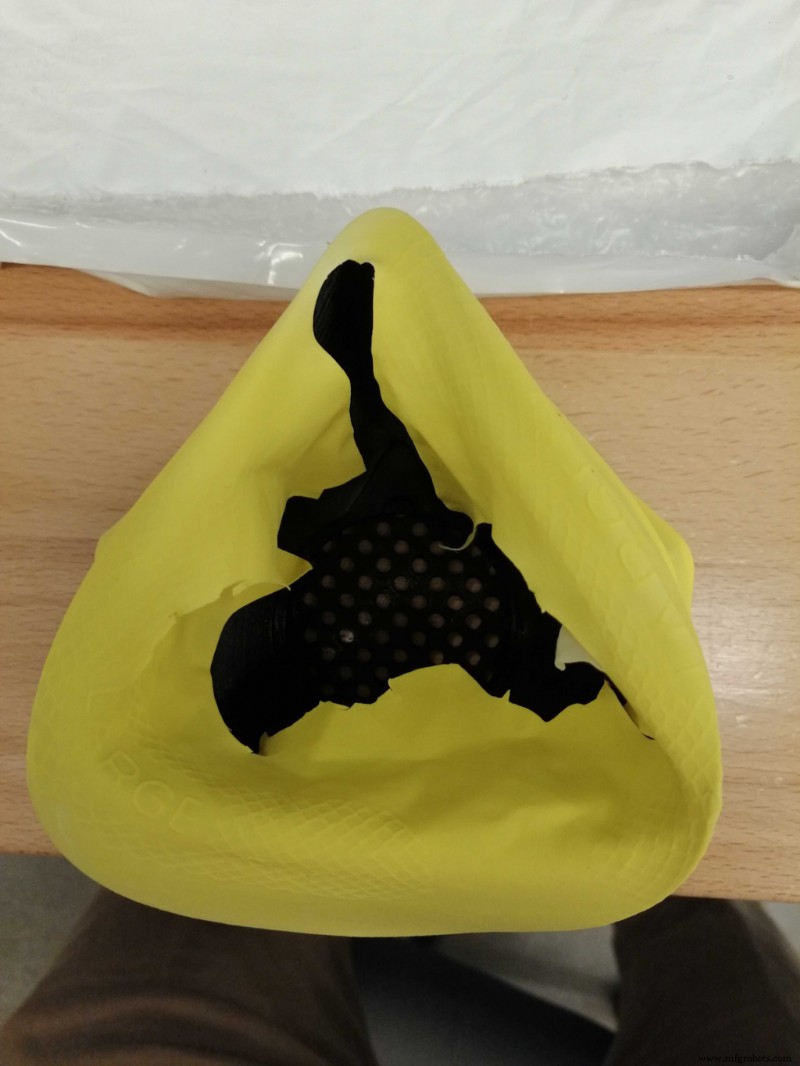
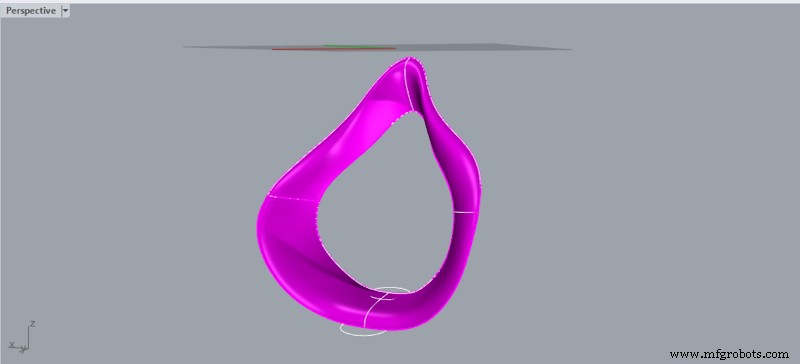
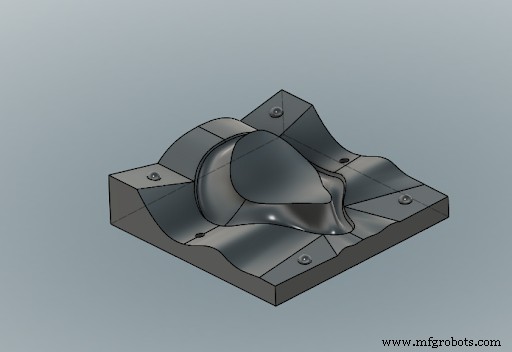
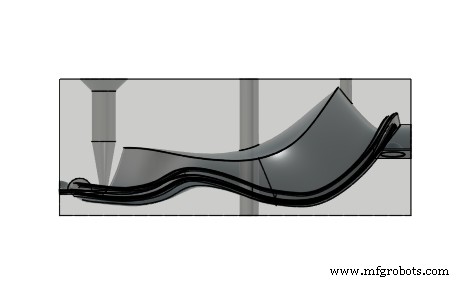
Mockup voor vormbare siliconen
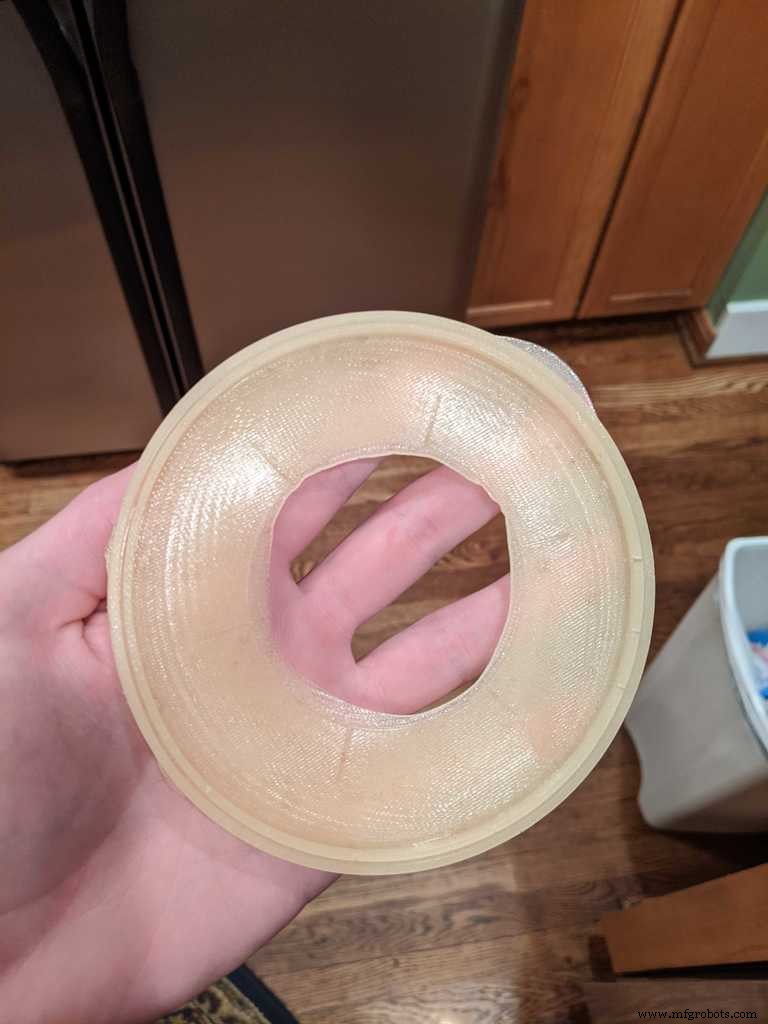
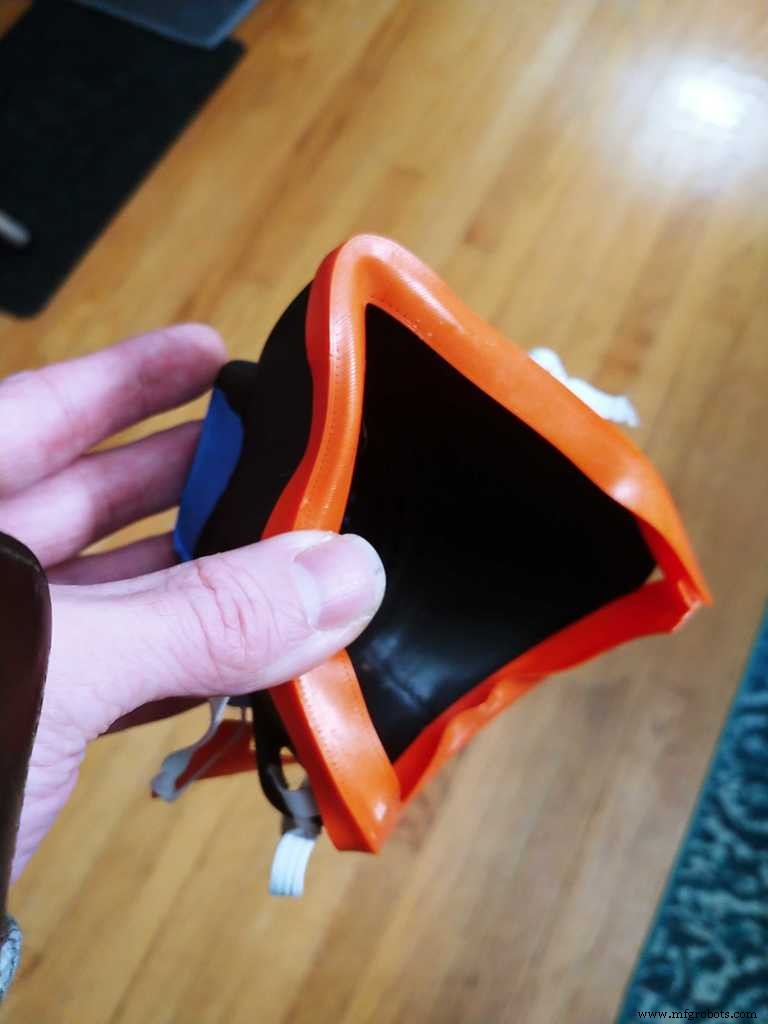
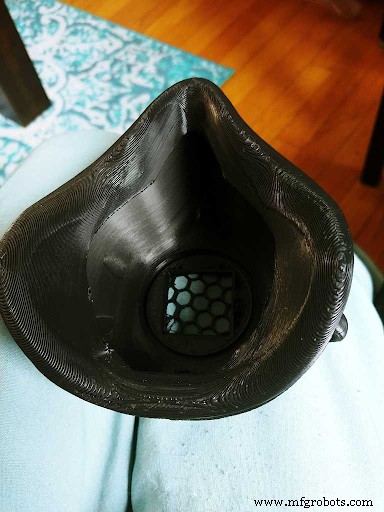
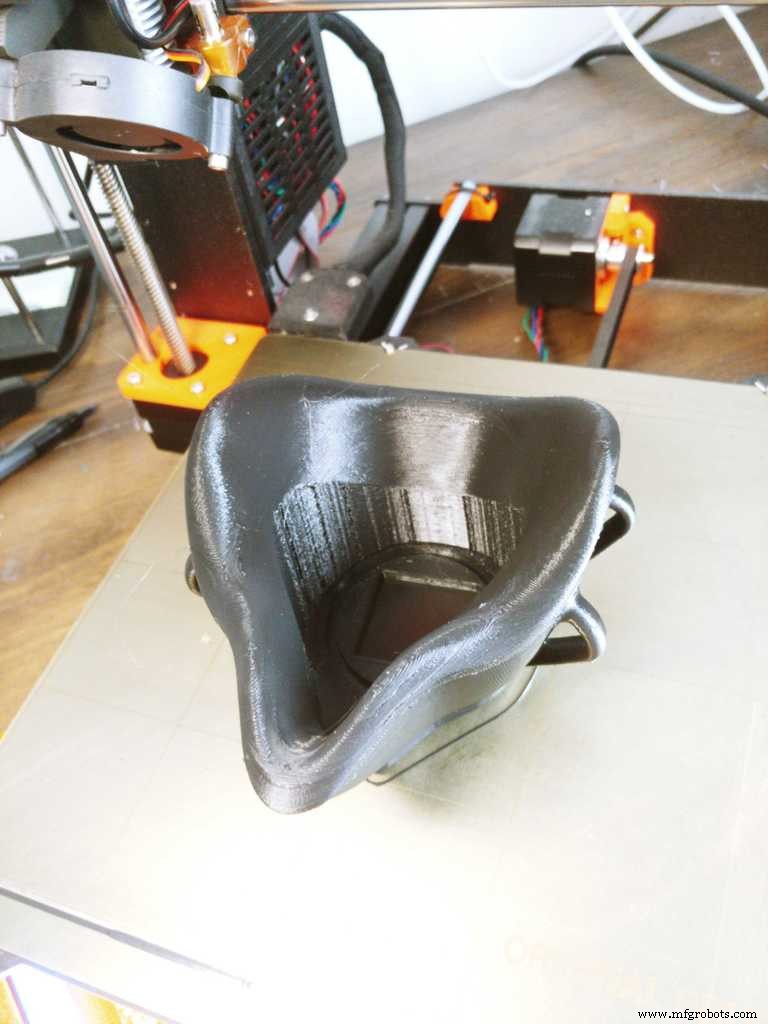
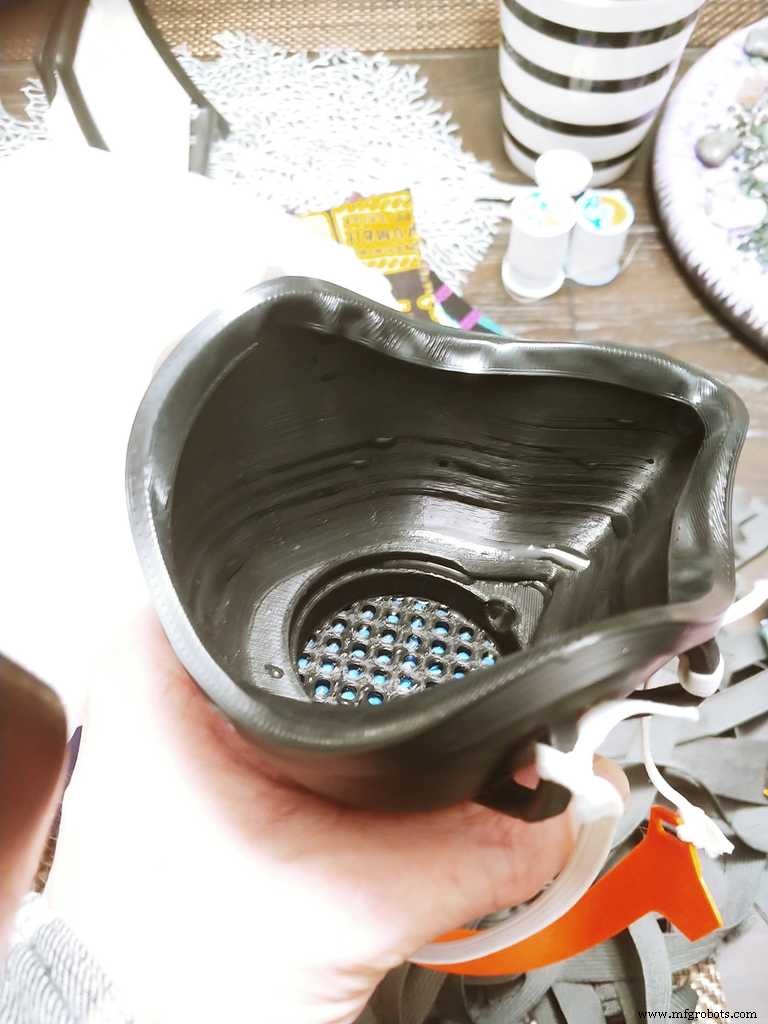
Geïntegreerde dunne PLA-afdichting
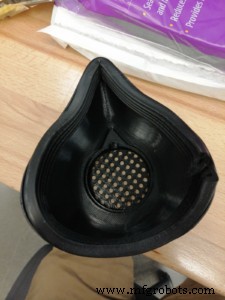
Snelle teamvorming
Ik schrijf de succesvolle snelle iteratie van dit project niet alleen toe aan de kracht van digitale ontwerptools en additieve fabricagetechnologie, maar ook aan de toewijding en diversiteit van het team dat we uit verschillende delen van het bedrijf hebben samengebracht. Daniel Baker (Manager of Manufacturing Engineering) gaf DFM-feedback en trok de hele nacht door om prototypes te printen en na te bewerken. Tim Ouradnik (Application Engineer) kocht afdichtingsmateriaal, assembleerde prototypes en reed heel Chicago door om gebruikerstests op sociale afstand uit te voeren. Uriah Foley en Eldon Whitis (labtechnici) testten thuis na kantooruren prototypes en verkenden geïntegreerde afdichtingen op hun persoonlijke 3D-printers.
Nick Tonini (programmamanager) zorgde voor eindeloos inventieve oplossingen en ontwerpfeedback. Jerry O'Leary (hoofdontwerper) heeft onze ontwerpen verbeterd en conceptweergaven gemaakt. Charlie Wood (manager Computational Engineering) gaf leiding aan het ontwerp van afdichtingen. Hallee Deutchman (Director of Materials and Manufacturing Technology) heeft contact opgenomen met onze partners en het juridische team voordat het ontwerp werd vrijgegeven. Sheila Seles (Senior Content Manager) en Austin Belisle (Content Specialist) hebben ons ontwerp verpakt, gepubliceerd en gepromoot.
De lijst met dankbetuigingen hierboven is niet alleen bedoeld om de personen die hebben bijgedragen aan dit proces te bedanken, maar ook om de kracht van de bedrijfscultuur te demonstreren om nieuwe dingen mogelijk te maken. We hebben aan dit project gewerkt buiten onze normale verantwoordelijkheden en teamstructuren om, omdat we een product wilden maken dat een impact zou kunnen hebben op de wereld buiten Fast Radius. Deze geest overschreed ook de bedrijfsgrenzen; we zijn dankbaar voor P33 en alle artsen die hun tijd en expertise hebben bijgedragen. Als we niets anders leren van deze pandemie, hoop ik dat we opzettelijk blijven streven naar het kweken van een cultuur van diversiteit, nederigheid en samenwerking terwijl we werken aan een antwoord op dringende wereldwijde uitdagingen.
Ons ontwerp is beschikbaar en klaar om af te drukken. Op onze website vindt u CAD-bestanden en instructies.
Klaar om uw onderdelen te maken met Fast Radius?
Start uw offerteIndustriële technologie
- De toekomst is…Samenwerking
- Functie in het MRO Magazine
- The Mark Two
- Achter de schermen van onze blog
- De effecten van COVID-19 op de productie
- De tastbare voordelen van VR in de technische ruimte
- Tableau, de gegevens achter de informatie
- Het verhaal achter onze populairste video
- De betekenis achter detectie van gedeeltelijke ontlading
- De waarheid achter smering en te veel smeren
- De toekomst van onderhoudstechniek