Mijn robotcollega heeft het allemaal onder controle
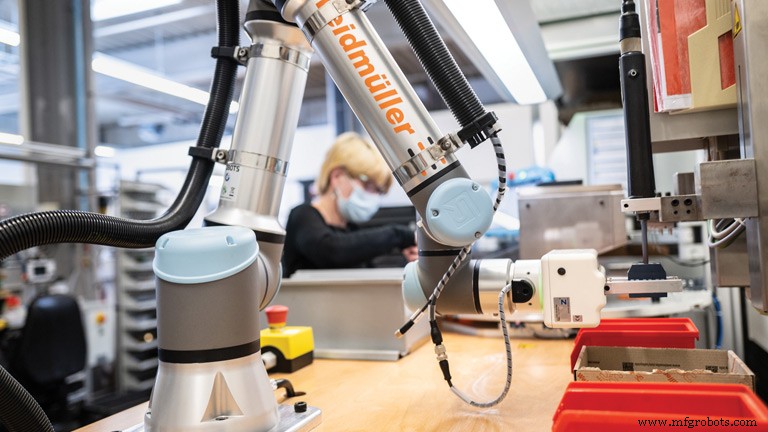
De hoge marktdynamiek, toenemende concurrentie door globalisering, maar ook demografische ontwikkelingen en het groeiende tekort aan geschoolde arbeidskrachten, stellen Duitse productiebedrijven voor grote hindernissen. Deze veranderingen hebben vooral invloed op het assemblageproces als laatste schakel in de waardeketen.
Een benadering om deze verandering tegen te gaan is het gebruik van de zogenaamde mens-robot-samenwerking (HRC). HRC-systemen worden echter nog steeds geassocieerd met hoge kosten, zowel in geld als in personeel, vanwege hun planningscomplexiteit. Er is behoefte aan eenvoudige en flexibele methoden waarmee bedrijven uit vele bedrijfstakken met een breed scala aan toepassingsrandvoorwaarden (complexiteit, variantie, hoeveelheden, enz.)
Onderzoeksproject SafeMate
In het SafeMate-onderzoeksproject, gefinancierd door het Duitse federale ministerie van Onderwijs en Onderzoek (BMBF) in het programma "Innovations for the Production, Service and Work of Tomorrow", werden strategieën en concepten ontwikkeld voor de introductie en het ontwerp van collaboratieve montagewerkplekken. De focus lag op veilige en geaccepteerde werkplekken waar medewerkers een hoge uitkering herkennen. Naast gerenommeerde Duitse bedrijven als Lenze, Lufthansa Sky Chefs, Miele en Sennheiser maakte ook het in Detmold gevestigde bedrijf Weidmüller deel uit van dit onderzoeksproject.
De Weidmüller Group is een wereldspeler en gespecialiseerd op het gebied van elektrische aansluittechniek en elektronica. Samen met zijn klanten geeft het vorm aan de digitale transformatie - met producten, oplossingen en diensten voor Smart Industrial Connectivity en het Industrial Internet of Things.
Met zijn producten is Weidmüller voornamelijk actief in de machinebouw, de procesindustrie, energieopwekking en hernieuwbare energie, transporttechnologie, bouwinfrastructuur en op het gebied van de fabricage van apparaten. Het bedrijf is al lang betrokken bij het onderwerp Industrie 4.0. en is naast SafeMate betrokken bij andere onderzoekssamenwerkingen.
Toen alles nog met de hand werd gedaan
Tot voor kort werd het assemblageproces voor elektromechanische componenten bij Weidmüller volledig handmatig uitgevoerd door medewerkers op de montagewerkplek.
Als onderdeel van Safe-Mate was een potentiële analyse - uitgevoerd door het team onder leiding van Weidmüller-procesingenieur Tobias Stuke - om de individuele taken te bepalen die door mens en machine worden uitgevoerd en zo een taakoptimale taakverdeling te creëren. Er werd onder meer vastgesteld dat robots erg goed zijn in het uitvoeren van de monotone, repetitieve en energie-intensieve taken van het plaatsingsproces zonder vermoeidheid. En ze kunnen dit met consistente nauwkeurigheid doen.
Maar het kan niet zonder mensen:mensen hebben speciale vaardigheden, bijvoorbeeld in het grijpen en verwijderen van kleine onderdelen van verschillende afmetingen van een stapel of doos. Ze kunnen ze beter herkennen en sorteren. Mensen zijn ook superieur aan hun robotcollega's als het gaat om correct voeren en het daaropvolgende inspectieproces.
Op basis van deze bevindingen werd het voorheen handmatige assemblageproces vervolgens gedeeltelijk geautomatiseerd in een eerste SafeMate-pilottoepassing met behulp van mens-robotsamenwerking (HRC). Het resultaat was een hybride assemblagewerkplaats waarin mens en robot parallel werken. De monotone en krachtintensieve taken worden uitgevoerd door de robot, terwijl de cognitief veeleisende taken worden uitgevoerd door de mens.
Mens-robot samenwerking
Bij collaboratieve robotica kunnen mens en robot hand in hand werken op één werkplek. Door de gevoelige besturingstechniek kan de robot nauw samenwerken met de mens zonder beschermende hekken. De toepassing vereist validatie om ervoor te zorgen dat de gevaren voldoende zijn geminimaliseerd. Dit kan als onderdeel van een kracht- en drukmeting door TÜV's, beroepsverenigingen, externe dienstverleners of zelfstandig door de integrator. Ook end-of-arm tools, zoals een grijper, kunnen op deze manier gevalideerd worden.
Voor de nieuwe hybride werkplek, voor de assemblage van elektromechanische componenten, is nu zo'n cobot van de Deense robotfabrikant Universal Robots (UR) naast de medewerkers geplaatst om naast hen te werken. Eerst monteert de collega de verbindingselementen. Vervolgens drukt de cobot de elektrische contactelementen in, sluit de connectorbehuizing aan en schroeft de aansluitcontacten vast. De productiviteit van de gehele hybride werkplek wordt verhoogd door de inzet van een collaboratieve robot en de resulterende reductie van tussenstappen of wachttijden in het montageproces. De focus van deze gedeeltelijke automatisering is om de machinebediener te ontlasten van tijdrovende en monotone tussenstappen en om een evenwichtige arbeidsverdeling tussen mens en robot te realiseren.
Een cobot met Zimmer HRC-grijper
Naast de selectie van een geschikte robot was ook een geschikte grijper nodig als onderdeel van het ontwerp van de werkplek. Grijptechnologie is namelijk een elementair onderdeel van elke robottoepassing. De HRC-02 grijper van de Zimmer Group, een grijperspecialist gevestigd in Rheinau, Duitsland, werd relatief snel gevonden. Zimmer Group heeft momenteel het grootste portfolio van HRC-grijpers ter wereld. De geselecteerde grijper is veilig en harmonieert perfect met de geselecteerde UR-robot.
De HRC-02 volledig elektrische servogrijper, speciaal ontworpen voor MRK-gebruik, heeft geen scherpe randen en is zo geconstrueerd dat, met zijn ronde vorm aan alle kanten, onbedoeld blijven haken vrijwel onmogelijk is. Bovendien heeft de HRC-02 een flexibel instelbare slag en grijpkracht, waardoor hij veel gevoeliger kan grijpen dan een conventionele grijper.
Deze functies in combinatie met een in de industrie bewezen ontwerp bieden de maximale veiligheid voor dit project. Alle HRC-grijpers van de Zimmer Group voldoen aan de hoge eisen van de beschermingsprincipes volgens ISO/TS 15066 (HRC-standaard) en zijn BG/DGUV-gecertificeerd.
Programmeren gemakkelijk gemaakt
In het SafeMate-project van Weidmüller lag een andere focus op het efficiënt en flexibel kunnen inzetten van de UR-cobot op de nieuwe hybride werkplek. Daarom is er ook aandacht besteed aan de eenvoudige bediening van de robot.
Het bedieningsgemak van de cobot was overtuigend, zeker in combinatie met de HRC-02 grijper. Het is tenslotte geen toeval dat alle grijpers van de Zimmer Group perfect kunnen werken met lichtgewicht UR-robots. Als UR+-partner toont Zimmer Group momenteel het grootste portfolio van UR-compatibele grijpers op de UR+-website.
Waar voorheen uitgebreid programmeerwerk en complexe programmeervaardigheden nodig waren, zijn de cobot van Universal Robots en zijn Zimmer-grijper zeer eenvoudig te bedienen. Het wordt rechtstreeks bestuurd of geprogrammeerd via het robotbedieningspaneel, dat intuïtief is ontworpen, vergelijkbaar met een smartphone-app.
Verhoogde productiviteit en tevredenheid
Het proefgebruik van de cobot op de afdeling werktuigbouwkunde van Weidmüller opent nieuwe mogelijkheden op het gebied van efficiëntie en flexibiliteit.
Dankzij deze nieuwe, hybride arbeidsverdeling en de eenvoudige bediening en eenvoudige installatie van de intelligente robot en zijn grijper kan de elektronicafabrikant het toenemende tekort aan geschoolde arbeidskrachten en de wereldwijde concurrentie nu wat meer opvangen. Naast de productiviteitsstijging waren er ook belangrijke niet-monetaire successen, zoals ergonomische werkplekoptimalisatie en algemene werkverlichting voor medewerkers.
Zo zouden krachtintensieve taken zoals het indrukken van de contactelementen (“latching”) en monotone taken aan de robot kunnen worden overgedragen. Deze hoge mate van acceptatie door de medewerkers werd ook bereikt door een participatief implementatieproces. Dit betekent dat medewerkers vanaf het begin betrokken waren bij het veranderingsproces rondom hun werkplek.
“Een bijzonder selectiecriterium voor de grijper van de Zimmer Group was dat de grijper, naast de technische kenmerken, al de geteste en gecertificeerde veiligheid voor HRC-systemen had, wat betekent dat we al aan de 'veilige kant' zaten - in de ware zin van het woord zin van het woord – voor ons aangrijpende technologieproject”, zegt Stuke.
Het is vooral belangrijk voor het bedrijf dat zijn medewerkers profiteren van samenwerking. De cobots met hun grijpers zijn bedoeld om verlichting te bieden.
Automatisering Besturingssysteem
- Voordelige, snelle montagerobot
- Sytrama plant Amerikaanse robotassemblage in nieuwe fabriek in Michigan
- Productieproces CNC-router
- Webinar:Automatiseer uw proces met Techman Robot
- ASM Assembly Systems gebruikt de Sawyer-robot van Rethink Robotics voor kwaliteitscontroles
- Software helpt NASA het programmeerproces van robots te automatiseren
- Het proces van een printplaatassemblage
- Laten we moedig gaan waar nog geen robot is geweest
- 8 stappen om uw procesbesturingssysteem te debuggen
- PLC versus DCS
- Stapsgewijs proces van loodvrije PCB-assemblage