Composiet 3D-printen:een opkomende technologie met een mooie toekomst
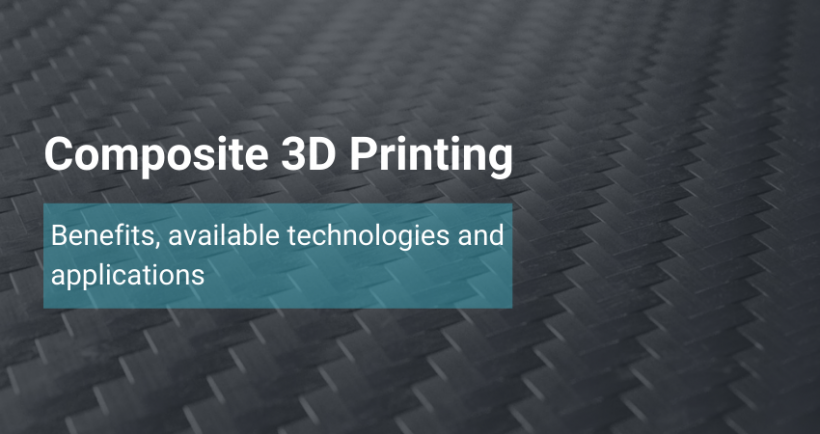
Composite 3D-printen is een jonge technologie, maar wel een met een enorm, grotendeels onbenut potentieel.
Volgens een SmarTech Analysis-rapport zal composiet 3D-printen in het komende decennium uitgroeien tot een bedrijf van bijna $ 10 miljard - op zijn zachtst gezegd een aanzienlijke groeimogelijkheid.
In In het artikel van vandaag gaan we dieper in op de voordelen die composiet 3D-printen biedt, de belangrijkste technologieën die op de markt beschikbaar zijn en de toepassingen – om erachter te komen wat de groei van deze opwindende industrie stimuleert.
Wat is een composiet?
Composieten bestaan doorgaans uit een kernpolymeermateriaal en een versterkend materiaal, zoals gehakte of continue vezels. Het composietmateriaal biedt een hogere sterkte en stijfheid in vergelijking met niet-versterkte polymeren. In sommige gevallen kan het zelfs metalen zoals aluminium vervangen.
Deze verbeterde materiaaleigenschappen maken composieten gewilde materialen voor gereedschaps- en eindgebruikstoepassingen in een groot aantal industrieën, zoals lucht- en ruimtevaart, auto's en industriële goederen plus olie en gas.
Wat zijn de voordelen van composiet 3D-printen?
Het vermogen om traditionele composietproductie te stroomlijnen en kosten te besparen, is een van de belangrijkste factoren die de groei van composiet 3D-printen stimuleren.
Er zijn talloze methoden voor het vervaardigen van composietcomponenten, naast 3d printen. De meeste hebben echter een aantal nadelen:de noodzaak voor het handmatig leggen van de lagen van een composiet en het gebruik van dure uithardingsapparatuur en gereedschappen, zoals mallen.
Dit maakt het proces van traditionele composietproductie erg arbeids-, hulpbronnen- en kapitaalintensief, wat betekent dat het moeilijk kan zijn om het op te schalen naar grote volumes.
3D-printen, op aan de andere kant maakt het mogelijk om het fabricageproces te automatiseren, aangezien het hele proces wordt aangestuurd door software en alleen handmatige invoer vereist in de nabewerkingsfase.
Continu versus gehakte vezels
Bij 3D-printen is het mogelijk om te printen met twee soorten versterkingsvezels, gehakt en continu. In het geval van gehakte vezels worden kleine strengen van minder dan een millimeter lang in het polymeermateriaal geïntegreerd. Het percentage gebruikte vezels en de thermoplastische basis bepalen hoe sterk het uiteindelijke deel is.
In het geval van continue vezels worden lange vezels gemengd met een thermoplast, zoals PLA, ABS, Nylon, PETG en PEEK tijdens het drukproces. Onderdelen die 3D-geprint zijn met doorlopende vezels zijn extreem licht, maar toch zo sterk als metaal.
In termen van soorten vezels die worden gebruikt, is koolstofvezel een van de meest populaire, gevolgd door glasvezel en Kevlar.
Samengestelde 3D-printtechnologieën op de markt
In 2020 blijft de markt voor composiet 3D-printen jong, met slechts een handvol bedrijven die composiet 3D-printoplossingen aanbieden. De meeste 3D-printers die composietmaterialen kunnen verwerken, zijn gebaseerd op het polymeer-extrusieproces, bekend als Fused Filament Fabrication (FFF).
In FFF beweegt een mondstuk boven het bouwplatform, waarbij een gesmolten plastic draad, een filament genaamd, wordt geëxtrudeerd en laag voor laag een object wordt gecreëerd.
3D-printen van filamenten die gehakte vezels bevatten, is eenvoudig en vereist alleen een mondstuk van gehard staal om schurende vezelstrengen te weerstaan. Als het echter gaat om continu printen van vezels, vereist het FFF-proces een tweede mondstuk om een enkele, ononderbroken vezelstreng afzonderlijk af te zetten.
Markforged:een pionier op het gebied van composiet 3D-printen
De continue vezel 3D-printmethode werd voor het eerst geïntroduceerd door Markforged in 2014, toen het bedrijf de Mark One lanceerde.
Hoewel de Mark One is vervangen door een nieuwe generatie 3D-printers, blijft de technologie hetzelfde:de printer is uitgerust met twee spuitmonden, één om plastic filament neer te leggen en de andere om tegelijkertijd koolstofvezelstrengen neer te leggen.
Nu, in 2020, biedt Markforged een reeks desktop- en industriële composiet 3D-printers, met de belangrijkste toepassingen in functionele prototyping en de productie van onderdelen en gereedschappen voor eindgebruik.
Desktop Metal's Micro Automated Fiber Placement-technologie
Desktop Metal is een ander bedrijf dat de FFF-technologie innoveerde om composieten te printen. In een beweging, vrij verrassend voor een bedrijf dat zich voorheen uitsluitend richtte op 3D-printen van metaal, lanceerde Desktop Metal in november 2019 de Fiber 3D-printer.
Een nieuw polymeer desktopsysteem combineert een traditionele Automated Fiber Placement (AFP) technologie met FFF naar 3D-printonderdelen verbeterd door continue vezels.
AFP-technologie is een geautomatiseerd productieproces voor composieten. Het omvat het verwarmen en verdichten van vezelversterkingen op typisch complexe gereedschapsmallen om continue vezelcomposietmaterialen te produceren. Desktop Metal heeft dit proces teruggebracht tot een desktopformaat en noemde zijn nieuwe technologie Micro Automated Fiber Placement (μAFP).
De μAFP werkt als de technologie van Markforged, maar in plaats van spoelen met vezels, gebruikt hij rollen vezeltape. Het kan koolstofvezel inbedden in nylon, PEEK en PEKK, en nylon kan ook worden geïntegreerd met glasvezel.
Om kleine composietonderdelen te maken, vertrouwen fabrikanten nog steeds voornamelijk op handlay-up. Dergelijke arbeidsintensieve processen vereisen technici, dure gereedschappen en veel tijd, die allemaal de totale productiekosten van een onderdeel verhogen.
Door μAFP te combineren met FFF in zijn nieuwe Fiber-systemen, streeft Desktop Metal om kleinere composietonderdelen gemakkelijker en goedkoper te produceren.
De Fiber kan worden gebruikt voor het produceren van mallen en armaturen, verschillende onderdelen voor eindgebruik, evenals alle componenten waarbij lichtgewicht een prioriteit is, zoals race-uitrusting.
Anisoprint's Composite Fiber Coextrusion-technologie
In dezelfde geest heeft Anisoprint, de Russische en Luxemburgse start-up, een op extrusie gebaseerd proces ontwikkeld dat het bedrijf Composite Fiber Coextrusion (CFC) noemt.
In tegenstelling tot de technologieën van Markforged en Desktop Metal, maakt CFC-technologie de versterking van kunststof met continue composietvezels direct tijdens het printproces mogelijk, niet in de pre-printfase. Deze benadering stelt gebruikers in staat om elk plastic te gebruiken dat ze willen (PETG, ABS, PC, PLA, Nylon, enz.) en de dichtheid van composietvulling te wijzigen.
Anisoprint's eerste machine was een Composer 3D-printer in desktopformaat . Onlangs onthulde het bedrijf ook de Anisoprint ProM IS 500, de industriële machine die is ontworpen om thermoplasten op hoge temperatuur te printen met continue vezelversterking. De Anisoprint ProM IS 500 heeft maximaal vier verwisselbare printkoppen voor het printen van composieten en puur plastic. Hiermee is het mogelijk om verschillende zones van het onderdeel te versterken met verschillende composieten (bijv. koolstof/basalt), afhankelijk van het doel van de gebruiker.
Wanneer het systeem eind 2020 officieel wordt gelanceerd, zal het een nieuwe stap voorwaarts betekenen, zowel voor composiet 3D-printen als voor geavanceerde polymeerproductie.
Composiet 3D-printen en robotica
Naast FFF 3D-printen hebben enkele bedrijven een aanpak ontwikkeld die composiet 3D-printen combineert met robotica. Een dergelijke combinatie zorgt voor meer flexibiliteit qua geometrie, aangezien de robotarm langs meerdere assen kan bewegen, en de mogelijkheid om grotere delen te printen.
Arevo is zo'n bedrijf dat een lasergebaseerde methode heeft ontwikkeld voor 3D-printen met koolstofvezel. Het proces omvat de afzetting van lagen van voorgeïmpregneerd continu koolstofvezelfilament, dat gelijktijdig wordt verwarmd met een laser, voordat een rol het op het bouwoppervlak comprimeert. Het proces lijkt op de Direct Energy Deposition-methode, die meestal wordt gebruikt met metaal.
In Arevo's proces wordt de depositiekop gemonteerd op een meerassige robotarm, waardoor het mogelijk wordt om 3D te printen in elke richting die het beste past bij het ontwerp van het onderdeel.
‘Als je naar 3D-printen kijkt, is het grootste deel van 3D-printen gebaseerd op lagen en worden de lagen afgezet in de X- en Y-vlakken. Als je kijkt naar de eigenschappen van onderdelen die met dat proces zijn gemaakt, hebben ze de neiging om in de Z-richting te lijden', zegt Wiener Mondesir, CTO bij Arevo.
Dankzij het gebruik van een robotarm heeft Arevo 'het probleem van de Z-sterkte geëlimineerd dat andere op lagen gebaseerde technologieën plaagt, omdat [zij] [materiaal] in de Z-richting kunnen neerleggen'.
Bovendien bieden 'robots een oneindige mogelijkheid om een enveloppe te bouwen, omdat we onze robots op het portaal kunnen plaatsen om ruimtevaartonderdelen te maken. Tegelijkertijd kan dezelfde robot een fiets maken'.
Arevo heeft dat laatste aangetoond door 's werelds eerste 3D-geprinte composiet fietsframe te ontwikkelen. Hieronder meer over deze zaak.
Continue composieten
Een ander bedrijf dat composiet 3D-printen en industriële robots combineert, is het in de VS gevestigde Continuous Composites. De methode, genaamd Continuous Fiber 3D Printing (CF3D), voert een rol droge koolstofvezel in een printkop, gemonteerd op een industriële robot met zeven assen. Binnen in de printkop is de vezel geïmpregneerd met een snel uithardende fotopolymeerhars en vervolgens geëxtraheerd door de eindeffector en onmiddellijk uitgehard met een krachtige energiebron.
Net als Arevo laat de zeven-assige arm de vezel toe op welke manier dan ook georiënteerd zijn om een onderdeel te creëren dat sterk is in alle richtingen. Interessant is dat, aangezien het uitharden van de hars gelijktijdig met de extrusie plaatsvindt, het CF3D-proces in de lucht kan printen, zonder ondersteuning.
Versterken:combinatie van composiet 3D-printen met Digital Light Processing
Zoals hierboven besproken, zijn onderdelen die in 3D zijn geprint met gehakte koolstofvezel zwakker dan die gemaakt met doorlopende koolstofvezel. De in Boston gevestigde start-up Fortify heeft echter zijn Digital Composite Manufacturing (DCM)-technologie ontwikkeld, wat bewijst dat dit niet altijd het geval is.
DCM is een nieuwe kijk op Digital Light Processing (DLP) ), waarin een projector wordt gebruikt om een lichtgevoelige hars in vloeibare toestand uit te harden. In het geval van DCM wordt de vloeibaar gemaakte hars gemengd met versterkende additieven, zoals gehakte koolstofvezel, die tijdens het drukproces worden uitgelijnd met behulp van een magnetisch veld.
'We hebben een techniek ontwikkeld waarmee we om vezels magnetisch te oriënteren in een vloeibaar medium. De onderdelen die we printen zijn in wezen de hoogste resolutie composieten die tot nu toe zijn geproduceerd. Met de magnetische assemblage zijn we in staat om meerdere eigenschappen zoals sterkte, stijfheid en thermische geleidbaarheid in drie dimensies binnen elke voxel te regelen', legt Fortify's CEO, Dr. Joshua Martin, uit in een interview met AMFG.
Een gebied waarop Fortify zich momenteel richt, is de ontwikkeling van composietgereedschap met zijn technologie.
'We betreden de markt voor [spuitgieten] zwaar omdat onze gereedschappen aanzienlijk meer schoten en cycli aankunnen dan concurrerende oplossingen.'
Vorig jaar haalde Fortify $ 10 miljoen op in een Series A-financiering en sloeg partnerschappen aan met twee chemiereuzen, Koninklijke DSM en Henkel. Gezien deze mijlpalen bevindt Fortify zich in een goede positie om zijn technologie naar de commercialisering te drijven, die gepland staat voor volgend jaar.
Onmogelijke objecten
Impossible Objects is een ander bedrijf dat innoveert op het gebied van composiet 3D-printen. In plaats van extrusie of robotica te gebruiken, heeft het bedrijf een geheel unieke aanpak ontwikkeld.
In het proces, genaamd Composite-Based Additive Manufacturing (CBAM), worden vellen vezelversterkingsmateriaal, zoals koolstofvezel, geleid onder een inkjetprintkop, die een vloeibare oplossing op het vel neerslaat, in de vorm van die laag.
Vervolgens wordt een laag polymeerpoeder op de plaat aangebracht. Het poeder plakt aan de plekken waar de vloeistof is afgezet. Het overtollige poeder wordt weggeblazen of opgezogen. Dit wordt laag voor laag herhaald totdat het object als een stapel vellen compleet is.
Deze stapel wordt vervolgens samengeperst en in een oven geplaatst, die het thermoplastische poeder versmelt, wat resulteert in een vezelversterkte thermoplastisch composiet.
Door het gebruik van inkjetprinten is de CBAM-methode veel sneller dan extrusieprocessen en is er ook de mogelijkheid om grote delen te printen. De nieuwste 3D-printer van Impossible Object, de CBAM-2, gelanceerd in 2019, kan onderdelen 3D-printen met vellen van ongeveer 30 cm x 30 cm.
De CBAM-2 kan werken momenteel met PEEK en Nylon 12 thermoplasten en lange vezels gemaakt van koolstof of glasvezel. Meer materialen, waaronder Nylon 6 en elastomeren, zijn onderweg.
Toepassingen voor composiet 3D-printen
Toepassingen voor composiet 3D-printen lopen het hele gamma, van prototyping tot tooling en fabricage van onderdelen voor eindgebruik.
Composiet 3D-printen gebruiken voor gereedschappen met grote bladen
In de lucht- en ruimtevaartindustrie kan het produceren van gereedschap een lang en duur proces zijn. Om deze uitdagingen het hoofd te bieden, wendde de Amerikaanse luchtvaartfabrikant Bell Helicopters zich tot Thermwood om grote mallen voor helikopterbladen te produceren.
Thermwood is een in de VS gevestigde fabrikant die Large Scale Additive Manufacturing (LSAM)-technologie heeft ontwikkeld die in staat is om grote composietgereedschappen te printen. Een van de unieke kenmerken van de LSAM 3D-printer van Thermwood is de hybride benadering van het produceren van onderdelen, waarbij additieve en subtractieve technologieën worden gecombineerd.
Om terug te komen op Bell:het bedrijf had een groot composietgereedschap nodig met een goede toleranties en het vermogen om autoclaafverwerking te weerstaan — een techniek die helpt bij het versterken van composietonderdelen die worden blootgesteld aan verhoogde druk en temperatuur.
LSAM was om twee hoofdredenen ideaal voor een dergelijke toepassing. Ten eerste kon het 6 m lange gereedschap worden vervaardigd uit een hoogwaardig koolstofversterkt PESU-materiaal, dat bestand is tegen hoge drukken en temperaturen. Ten tweede, aangezien LSAM een hybride technologie is, kan een onderdeel in 3D worden geprint en afgewerkt zonder dat er een tweede machine nodig is, wat het productieproces verder helpt versnellen.
Deze voordelen stelden Thermwood in staat om het gereedschap in slechts een paar dagen te vervaardigen, in tegenstelling tot de maanden die het zou kosten met traditionele processen.
Deze prestatie wijst op de nieuwe mogelijkheden die grootschalige composiet 3D-printing ontgrendelt voor grote en technisch complexe luchtvaartcomponenten.
Wärtsilä 3D print composiet hijsgereedschap
Wärtsilä, een bedrijf dat gespecialiseerd is in maritieme en energiemarkten, heeft een composiet X7 3D-printer van Markforged toegepast om een hijsgereedschap te vervaardigen. De tool is een op maat gemaakt stuk hardware waarmee het team enorm zware motoronderdelen, zoals zuigers, kan verplaatsen.
Het bedrijf maakte vroeger dergelijke gereedschappen uit massief staal, maar vond het proces te duur en koos voor 3D-printen van een polymeer hijsgereedschap versterkt met koolstofvezel. Het resulterende gereedschap was 75 procent lichter en kon 960 kg tillen. Wärtsilä is van mening dat het alleen al € 100.000 aan tooling heeft bespaard door over te stappen op composiet 3D-printen.
Dit voorbeeld illustreert ook de mogelijkheid om zware metalen die worden gebruikt om een onderdeel te vervaardigen, te vervangen door lichtere, maar even sterke, composietmaterialen.
Samengestelde fietsframes
Fietsframes zijn een van de meest succesvolle toepassingen van composiet 3D-printen in de fabricage van onderdelen voor eindgebruik. Fietsframes van koolstofvezel worden steeds populairder, omdat de eigenschappen van het materiaal zeer geschikt zijn voor de frameconstructie. Het materiaal is sterk, duurzaam en licht van gewicht, waardoor het een veelgevraagd alternatief is voor metalen fietsframes.
Koolstofvezelframes hebben echter twee grote nadelen:het materiaal is extreem duur en het fabricageproces is notoir arbeidsintensief.
Arevo overwint deze uitdagingen frontaal, met behulp van zijn robotica 3D-printproces. De aanpak van het bedrijf creëert een frame dat uniform sterk is in alle drie de dimensies. Deze functie onderscheidt de technologie van Arevo van traditioneel 3D-printen met filament, waarbij 3D-geprinte onderdelen de neiging hebben anisotroop te zijn wanneer ze voor het eerst worden geprint, wat betekent dat ze niet in alle richtingen even sterk zijn.
Dankzij deze technologie zegt Arevo het kan koolstofvezelfietsen produceren tegen concurrerende kosten van $ 300, vergeleken met vergelijkbare traditioneel vervaardigde fietsen, die een gemiddelde prijsklasse hebben van $ 1000 tot $ 2000.
De start-up werkt al samen met een paar fietsen bedrijven, waaronder Franco Bicycles en Pilot.
Nu 3D-printen van composietfietsen aan populariteit wint, voegt Arevo's technologie een nieuwe dimensie toe aan de fietsproductiesector.
Composite 3D-printen:de grenzen van composietproductie verleggen
Ondanks dat het een jonge technologie is, krijgt composiet 3D-printen steeds meer voet aan de grond in de maakindustrie. Het biedt een snellere en meer geautomatiseerde benadering voor het produceren van composietonderdelen, die lange tijd met de hand zijn gemaakt.
Composiet 3D-printen helpt bij het heroverwegen van de materiaalkeuze voor bepaalde toepassingen, waardoor fabrikanten metaal kunnen vervangen door duurzaam, goedkoper plastic. Ten slotte helpt het om het fabricageproces van composietonderdelen goedkoper te maken.
Gecombineerd suggereren deze voordelen dat composiet 3D-printen alleen maar zal groeien en rijpen om een standaardmethode te worden in de gereedschapskist van de composietfabrikant.
3d printen
- Een inleiding tot 3D-printen met plastic
- ACEO® onthult nieuwe technologie voor 3D-printen met siliconen
- 3D-printen met siliconen — is het zover?
- Aan de slag met keramisch 3D-printen
- 3D-printen met harsen:een introductie
- Een gids voor 3D-printen met titanium
- De zekering 1 afdrukken met de zekering 1
- 3D-printen met hoge snelheid met AION500MK3
- Impossible Objects werkt samen met BASF voor composiet 3D-printen
- Polyjet 3D-printen:technologieoverzicht
- Carbon DLS 3D-printen:technologieoverzicht