Interview met expert:VELO3D's VP of Technology Partnerships over uitbreiding van de mogelijkheden van 3D-metaalprinten
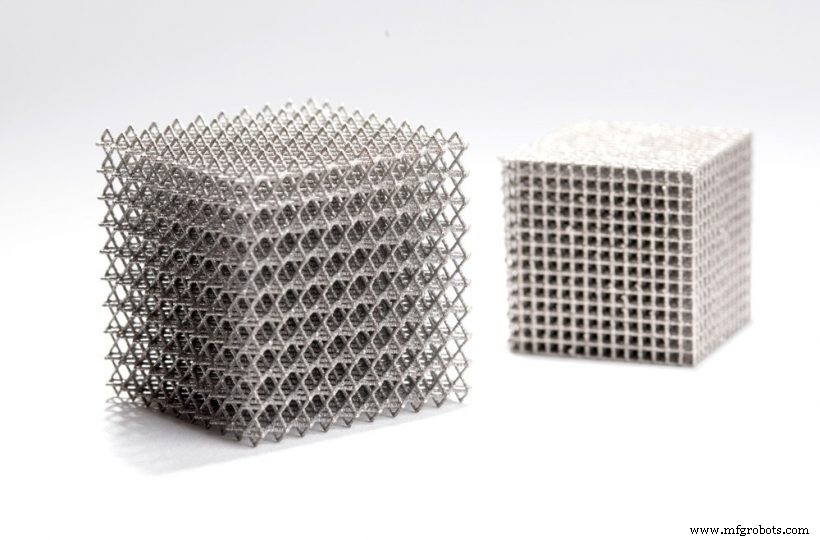
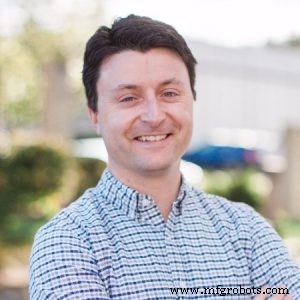
Metaal 3D-printen mag dan een innovatieve technologie zijn, het is niet zonder uitdagingen. Het is een proces dat tijdrovende ontwerpoverwegingen, nabewerking en een zekere mate van trial-and-error vereist om tot een succesvolle afdruk te komen. In een poging om deze en andere aanverwante uitdagingen op te lossen, heeft het in Californië gevestigde bedrijf VELO
3D
, onthulde vorig jaar zijn lasergebaseerde Sapphire metal 3D-printer.
Het resultaat van vier jaar ontwikkeling, de Sapphire-printer heeft twee belangrijke elementen:zijn Intelligent Fusion™-technologie en Flow printvoorbereidingssoftware. De twee functies werken hand in hand om potentieel baanbrekende voordelen te bieden, zoals verbeterde herhaalbaarheid en afdrukken zonder ondersteuning. Vooral dat laatste is mogelijk dankzij het vermogen van de Sapphire-printer om extreme uitsteeklengtes af te drukken zonder dat er ondersteunende structuren nodig zijn.
In het Expert Interview van deze week spreken we met Zachary Murphree, VP of Technology Partnerschappen bij VELO
3D
, om de waarde van zijn Intelligent Fusion™-technologie, zijn meest boeiende toepassingen en wat de toekomst biedt voor de metaal-AM-sector te bespreken.
Kun je me iets over VELO vertellen 3D ?
VELO
3D
werd opgericht met als doel de toepassingen voor metaaladditieve fabricage uit te breiden.
Een van de redenen voor de oprichting was de frustratie rond additive manufacturing die onze oprichter, Benny Buller, ervoer bij het maken van onderdelen voor productie. Metal AM kon sommige van de gemaakte beloften niet waarmaken, zoals complexiteit zonder kosten en het versnellen van het productontwikkelingsproces.
Er zijn een aantal grote discussiepunten rond metal AM die niet helemaal waar zijn. Een deel van ons doel is om die frustratie weg te nemen en het scala aan toepassingen uit te breiden, zodat metal AM zijn beloften echt waarmaakt.
Om dit doel te bereiken, hebben we het proces opnieuw bekeken om de fundamentele fysica ervan te begrijpen. Door het proces volledig te begrijpen, hebben we een systeem ontwikkeld dat in staat is om dingen te printen die voorheen als niet-afdrukbaar werden beschouwd en het bereik van geometrieën uit te breiden die als kosteneffectief kunnen worden beschouwd voor additive manufacturing.
Zo hebben we onze twee belangrijkste producten ontwikkeld:de Sapphire-metaalprinter en Flow-software. Deze twee producten vormen het systeem dat het 3D-printen van onderdelen mogelijk maakt die met geen enkel ander systeem kunnen worden geproduceerd.
VELO 3D kwam vorig jaar uit de stealth-modus met de Sapphire-printer en lanceerde het bedrijf publiekelijk op de International Manufacturing Trade Show. Welke waarde brengt uw systeem op de markt?
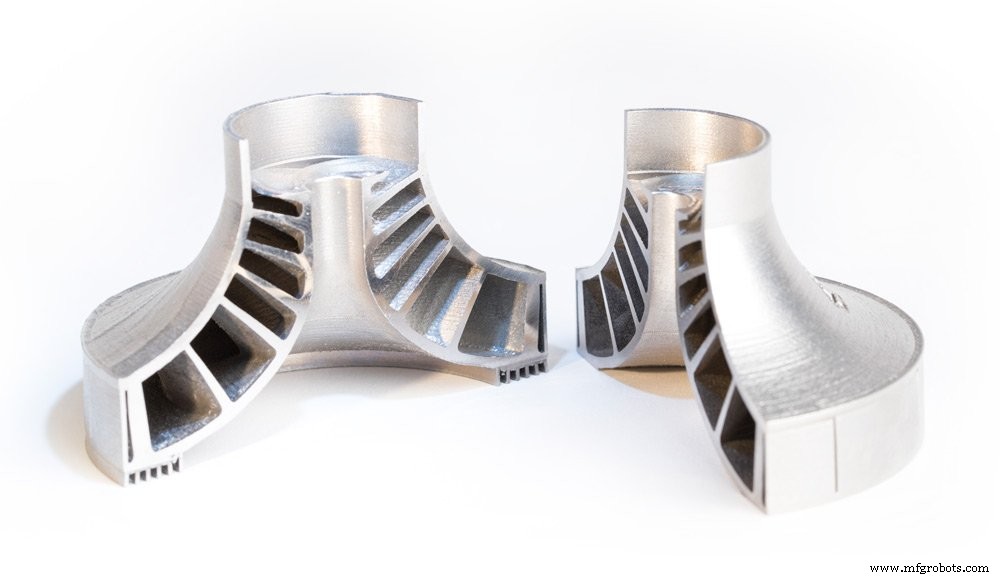
Een van de belangrijke dingen die we proberen te benadrukken, is dat onze technologie niet alleen de fysieke hardware is. De Sapphire-printer is het meest zichtbare onderdeel van onze oplossing, maar het is slechts één onderdeel. Om het systeem in staat te stellen te doen wat het kan, is onze Flow printvoorbereidingssoftware nodig. Het proces kan niet op andere systemen worden uitgevoerd; we moesten de hardware echt van de grond af ontwikkelen om de processen die we uitvoeren mogelijk te maken.
Deze combinatie stelt ons in staat om ondersteuningsvrije productie te realiseren, wat neerkomt op procescontrole. VELO
3D
is daar vanaf het begin op gefocust. Door het proces te beheersen en het in een zeer krap venster uit te voeren, zijn we in staat om onderdelen met zeer lage hoekuitsteeksels te printen zonder steunen.
Hoe werkt de technologie?
Het proces begint met de CAD-geometrie. We werken met de onderliggende CAD-geometrie en niet met tesselated bestandsformaten zoals een STL-bestand. Het CAD-bestand wordt eerst geïmporteerd in onze Flow printvoorbereidingssoftware.
Met de software kunt u het onderdeel oriënteren en steunen plaatsen — enigszins vergelijkbaar met wat kan worden gedaan met sommige van de bestaande softwareoplossingen. Maar wat hier anders is, is dat onze Flow-software zeer procesbewust is. Het feit dat het samen met de hardware is ontwikkeld, betekent dat het een zeer nauw geïntegreerd systeem is.
De software is ook in staat om factoren te voorspellen, zoals wanneer onderdelen zullen vervormen of wanneer ondersteuningsfouten optreden tijdens de bouw, en kan feedback geven over oriëntatie en ondersteuning zelfs voordat het printen is begonnen.
We hebben ook een vervormingscorrectiefunctie waarmee we de geometrie vooraf kunnen vervormen, zodat het onderdeel dat u aan het einde van de afdruk uit de machine haalt, de juiste geometrie heeft. Dit is thermische simulatiesoftware.
Het laatste onderdeel van de printvoorbereidingssoftware is de parametrering. Dit is, nogmaals, nauw geïntegreerd met de hardware, zodat we de parameters van het gereedschapspad kunnen definiëren op een manier die heel specifiek is voor de geometrie van een onderdeel. Deze parameters zijn veel genuanceerder dan wat je krijgt van sommige conventionele metaaladditieve productiesystemen.
Dit alles bij elkaar levert u een printbestand op dat veel procesintelligentie bevat. Daarom noemen we onze technologie Intelligent Fusion.
De Sapphire-printer is ontworpen om die bouwinstructies op een zeer gecontroleerde manier uit te voeren. Veel van het succes dat we hebben, is niet alleen gebaseerd op het zeer strak regelen van de atmosfeer, de kamer, het poederbed en de gasstroom, maar ook op het proces zelf.
Een van de dingen die we op het systeem hebben, is een gesloten smeltbad-controlesysteem waarmee we de doeltemperaturen kunnen bereiken om het proces succesvol te laten zijn. We hebben ook een contactloze recoater waarmee we onderdelen kunnen bouwen op manieren die niet mogelijk zijn op andere systemen.
Kunt u iets zeggen over de specifieke uitdagingen die uw technologie oplost?
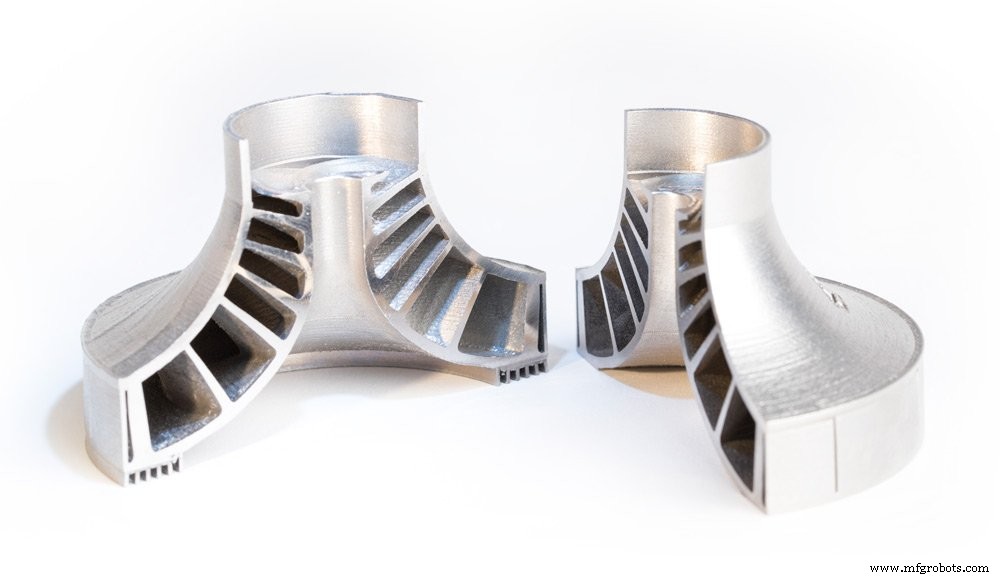
Terwijl ik met klanten sprak, heb ik zeker gezien dat ingenieurs graag metaal AM als fabricagetechniek gebruiken.
Maar ondanks dat het een dertig jaar oude industrie is, is er nog veel van onvolwassenheid in de manier waarop onderdelen worden vervaardigd, vooral als je het vergelijkt met gevestigde productiemethoden.
Als je onderdelen afdrukt, is het vaak moeilijk om ze in de eerste plaats bedrukbaar te krijgen. Veel daarvan komt neer op de geometrische beperkingen. Het grootste voorbeeld hiervan is de standaard 45-gradenregel, wanneer u geen niet-ondersteunde uitsteeklengten kunt afdrukken die minder dan 45 graden ten opzichte van horizontaal zijn. Hoewel dit de standaard is, hebben mensen het een beetje lager geduwd. Afhankelijk van het materiaal en de machine kun je tot 40 of 35 graden komen.
Hoewel er enige innovatie is geweest, is dit nog steeds een vrij fundamentele beperking. Het betekent dat u vaak steunen moet plaatsen op plaatsen waar het moeilijk, zo niet onmogelijk, is om ze achteraf te verwijderen.
Als je kijkt naar een slakkenhuis voor een pomphuis of een turbohuis, dat een torusvormig, hol donut-achtig onderdeel is, dan betekenen de steunen aan de binnenkant dat het geen goede kandidaat is voor metaal BEN.
Gehulde waaiers zijn een andere uitdaging. Mensen wilden al heel lang, maar hadden er moeite mee, om die onderdelen af te drukken.
In het domein van de gasturbine heb je blisks, bladen en statoraders die allemaal goede kandidaten zijn voor additieven, maar de hoeveelheid dragers die je moet toevoegen om ze succesvol af te drukken, maakt AM niet ideaal oplossing. Als dat niet zo was, zouden deze onderdelen echt een goede kandidaat zijn voor 3D-printen, omdat ze vrij moeilijk te vervaardigen zijn met andere methoden.
Dus door de grenzen van het ontwerp te verleggen met de mogelijkheid om af te drukken tot 5 -10 graden zonder enige ondersteuning met een goede oppervlakteafwerking, we maken veel verschillende toepassingen mogelijk.
Hoe positioneert u uw technologie naast andere metaal 3D-printtechnologieën?
Het hangt af van wat je doet. Er zijn toepassingen die nu behoorlijk succesvol zijn in metal AM. Misschien zou het een voordeel zijn om VELO . te gebruiken
3D
technologie zonder ondersteuning om de productie te versnellen. Maar uiteindelijk zijn er mensen die echt goede onderdelen op andere systemen printen.
Dus ik denk dat er in termen van additieven zeker ruimte is aan de tafel voor veel verschillende spelers. Als je de omvang van de AM-industrie vergelijkt met de omvang van de traditionele maakindustrie, dan hebben we nog veel ruimte om te groeien voordat het een honden-eet-hond-wereld wordt.
Hoewel we denken dat onze technologie veel van de huidige technologieën kan vervangen, betekent dat niet dat er ook geen ruimte is voor anderen.
In welke sectoren zie je de grootste groeimogelijkheden voor VELO 3D ?
Het is niet verwonderlijk dat lucht- en ruimtevaart een belangrijke industrie is, omdat ze een early adopter zijn van 3D-printen. De redenering is vrij duidelijk:ze maken hoogwaardige fabricage, ze hebben onderdelen die duur zijn om te produceren en hebben veel geometrische ingewikkeldheden, zodat ze kunnen profiteren van metaal AM.
En de lucht- en ruimtevaartindustrie is enorm. Er is voortstuwing, die je kunt opsplitsen in gasturbines of niet-luchtademhalingstoepassingen zoals raketmotoren, wat nog een heel goede toepassing is. Vervolgens heb je aerostructuren - eigenlijke structurele componenten - in de luchtvaart en satellietstructuren in de ruimte
Er zijn ook veel toepassingen aan de elektronische kant, met name rond behuizingen en radiofrequentiecomponenten. Warmtewisselaars zijn een ander onderdeel dat traditioneel moeilijk te vervaardigen kan zijn, afhankelijk van de geometrie. Dus in de ruimtevaart is er veel om na te jagen.
Dan is er de mogelijkheid voor metaal AM in industriële toepassingen, vooral omdat het enigszins lijkt op ruimtevaart. Hoewel ze niet zo waardevol zijn, kunnen de toepassingen vloeistofstroomcomponenten of andere onderdelen van het pomp-, verdeelstuk- en warmtewisselaartype omvatten.
Wat zijn enkele van de grootste pijnpunten die u ziet wanneer klanten contact met u opnemen?
De grootste uitdagingen liggen rond de geometrieën die kunnen worden afgedrukt.
Een ander belangrijk punt dat de industrie moet aanpakken om breder geaccepteerd te worden, is de variatie van deel tot deel. Als je een ingenieur bent die onderdelen voor metaal AM ontwerpt en het zijn cruciale componenten, dan moet je een behoorlijke slag slaan op je ontwerptoegestane om metaaladditief te kunnen gebruiken.
De reden daarvoor is dat de consistentie van het materiaal dat uit het systeem komt niet per se is wat u wilt dat het is. Je moet ontwerpen voor het zwakste deel dat je zou kunnen krijgen, wat betekent dat je sommige van de mogelijkheden van AM niet volledig benut, vooral als het gaat om lichtgewicht of prestatieverbetering. Je moet veel marges in je onderdeel hebben ingebouwd.
Een van de dingen die we ook proberen aan te pakken met ons systeem, en met veel van de ingebouwde metrologische mogelijkheden, is de part-to-part, build-to-build en variatie van machine tot machine, evenals de mechanische eigenschappen van het einddeel.
Dat is iets dat veel deuren zal openen omdat er nog steeds aarzeling is om metal AM te gebruiken, en mensen hebben niet 100% vertrouwen in wat ze aan het einde van de dag.
Welk advies zou je geven aan bedrijven die metaal AM-technologie willen toepassen, maar niet weten waar ze moeten beginnen?
Er zijn verschillende redenen om AM-technologie toe te passen. Sommige mensen hebben een zakelijke drive om gewoon metal AM te adopteren. Maar dat is niet per se iets dat leidt tot overtuigende gevallen voor metaaladditieven.
Ik denk dat het erg belangrijk is om een dwingende reden te hebben om metaaladditieven nodig te hebben. Vaak zullen bedrijven zeggen:"Wat als we exact hetzelfde onderdeel maken met metaaladditief? Hoe doen we kostenvergelijkingen? Stoppen we het allemaal in een matrix en zoeken we uit wat het meest kosteneffectief is?” Dat betekent niet per se profiteren van al die metaaladditieven.
Als het erop aankomt, is metaal AM een ander hulpmiddel in de productiegereedschapskist. Je moet de pijn hebben om de overgang te maken. Dus je moet een onderdeel hebben dat je moet maken, of dat je moeite hebt om te maken met een andere fabricagetechniek, of je hebt meer functionaliteit nodig van het eindproduct waarvoor je nieuwe functies en nieuwe geometrieën moet ontwerpen.
Hoe zou u de huidige staat van de AM-industrie omschrijven en hoe ziet u deze de komende vijf jaar evolueren?
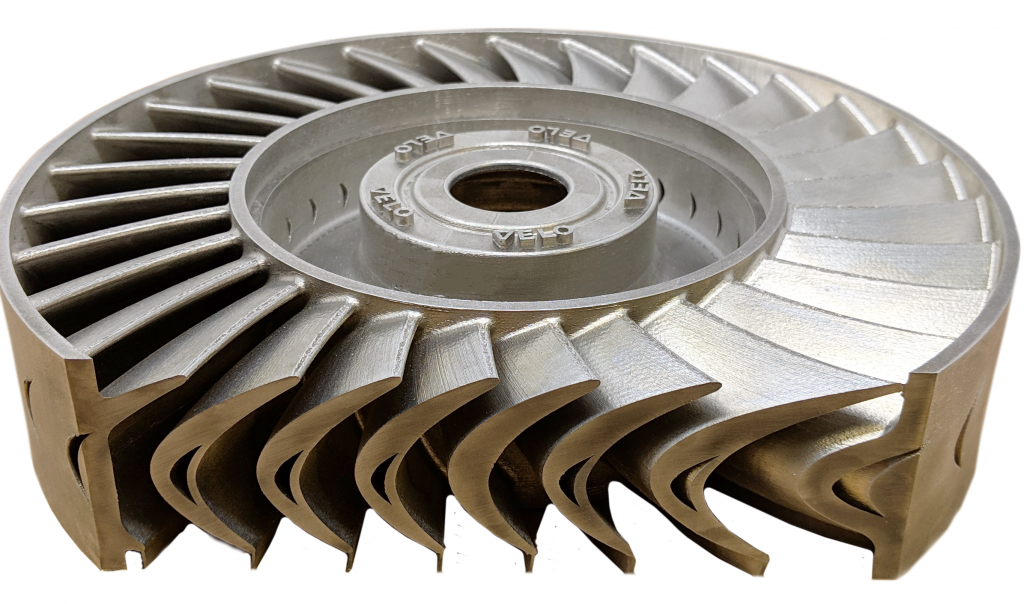
Metal AM wordt volwassener. Er zijn enkele duidelijke gevallen van bedrijven die succesvol in productie zijn gekomen. We bereiken een buigpunt en het aantal onderdelen dat daadwerkelijk in productie gaat, neemt toe.
Over vijf jaar zie je veel contractfabrikanten die aanzienlijk zijn opgeschaald en honderden van deze systemen op hun vloer hebben staan, die onderdelen produceren met langetermijncontracten voor productie. De industrie werkt daar al lang naartoe.
Mensen krijgen steeds meer vertrouwen in metaaladditief als oplossing. VELO
3D
is technologie zal daarin een grote rol spelen, omdat het ons doel is om de productie te versnellen en mensen vertrouwen te geven in de kwaliteit van een onderdeel dat aan het einde van de print uitkomt.
Met die twee dingen gecombineerd, kun je heel wat meer sollicitaties binnenhalen die vandaag misschien twijfelachtig zijn, maar echt goede kandidaten voor AM kunnen zijn.
Zijn er bepaalde trends waar je enthousiast over bent?
Er zijn nogal wat opwindende trends die we zien.
Een gebied waar ik bijzonder enthousiast over ben, is de ruimtemarkt, met name rond raketten en kleine satellieten.
Er zijn innovatieve bedrijven die snel itereren en snelle ontwikkelingscycli hebben. Ze zijn op zoek naar hoogwaardige eindonderdelen die goed zijn afgestemd op de mogelijkheden van VELO
3D
is Saffier systeem. Het is een markt die snel kan worden geadopteerd en die met een behoorlijk bedrag zal groeien.
Het andere geweldige is dat de markt veel aangrenzendheden heeft en zich ook voedt met de meer traditionele lucht- en ruimtevaartmarkt. Deze kleinere, snellere bedrijven kunnen de komende vijf jaar een aantal zaken regelen die de grote defensie-aannemers en ruimtevaartbedrijven zullen aantrekken.
Hoe ziet de materiaalontwikkeling eruit bij VELO 3D ? Zijn er plannen om uw materiaalportfolio verder uit te breiden?
Op dit moment printen we in Inconel 718 en Ti64. We proberen klantgericht te zijn, dus onze toekomstige materiaalontwikkeling zal worden aangedreven door sterke businesscases.
Er zijn sterke businesscases rond andere titanium en aluminium, maar niet noodzakelijk dezelfde materialen die de gebruikelijke aanbiedingen van andere metaal AM-fabrikanten zijn. We willen inspelen op specifieke klantbehoeften en reageren op wat de markt vraagt, in plaats van wat vandaag de dag noodzakelijkerwijs mogelijk is.
VELO 3D is onlangs een samenwerking aangegaan met Praxair. Wat betekent deze samenwerking voor jou?
We hebben een geweldige relatie gehad met Praxair Surface Technologies. Zij zijn een van onze gecertificeerde poederleveranciers.
We proberen ervoor te zorgen dat onze klanten toegang hebben tot hoogwaardige grondstoffen en Praxair is daar absoluut een leverancier van. Met hen werken we aan de ontwikkeling van nieuwe legeringen en zorgen we ervoor dat onze klanten tevreden zijn met de legeringen die ze van hun leveranciers krijgen.
Wat is de reactie van uw klanten sinds uw lancering?
Het is positief geweest. Ik krijg absoluut het gevoel dat onze klanten enthousiast zijn als ze zien wat we hier allemaal doen, en hoe we veel van de problemen hebben opgelost die bestaan met de software en de hardware rond metal AM . Dat spreekt van een klantgericht bedrijf:de uitdagingen begrijpen waarmee onze klanten worden geconfronteerd en oplossingen ontwikkelen om hun leven beter te maken.
Over het algemeen vind ik het heerlijk om rondleidingen te geven hier bij VELO
3D
, omdat de reacties altijd zo enthousiast zijn en mensen erg enthousiast lijken te zijn om de technologie te gaan gebruiken en in-house te gaan gebruiken.
Ten slotte, hoe ziet 2019 eruit voor VELO 3D ?
2019 wordt een heel spannend jaar voor VELO
3D
. We beginnen de markt te betreden en mensen worden zich steeds meer bewust van ons bedrijf en onze mogelijkheden. We zien dat zowel in de vraag naar het systeem als naar onderdelen die op het systeem en het systeem zelf zijn afgedrukt.
Voor ons wordt dit het jaar van technologie zonder ondersteuning, wanneer we echt begin mensen ertoe te brengen VELO . te ontwerpen
3D
in hun eindproduct.
Meer informatie over Velo
3D
, bezoek:www.velo3d.com
3d printen
- Vuurvaste metaalpoeders VS 3D-afdruktechnologie
- Interview met een expert:Dr. Alvaro Goyanes van FabRx
- Overwegend wat nieuwe metaalprinttechnologie betekent voor AM
- Interview met een expert:Dr. Bastian Rapp van NeptunLab
- Stereolithografie — de originele 3D-printtechnologie
- Interview met expert:Duncan McCallum, CEO van Digital Alloys over Joule Printing en de toekomst van Metal 3D Printing
- Expertinterview:Nanoe CEO Guillaume de Calan over de toekomst van keramisch 3D-printen
- Expert Interview:Ultimaker President John Kawola over de toekomst van 3D-printen
- Interview met expert:Simon Fried, medeoprichter van Nano Dimension over de opkomst van 3D-printen voor elektronica
- Metaal 3D-printen:waar zijn we vandaag?
- Interview met expert:hoofdtechnoloog van ANSYS over het bereiken van succesvol 3D-printen met metaal met simulatie