10 spannende 3D-printtechnologieën die de afgelopen 12 maanden zijn ontstaan
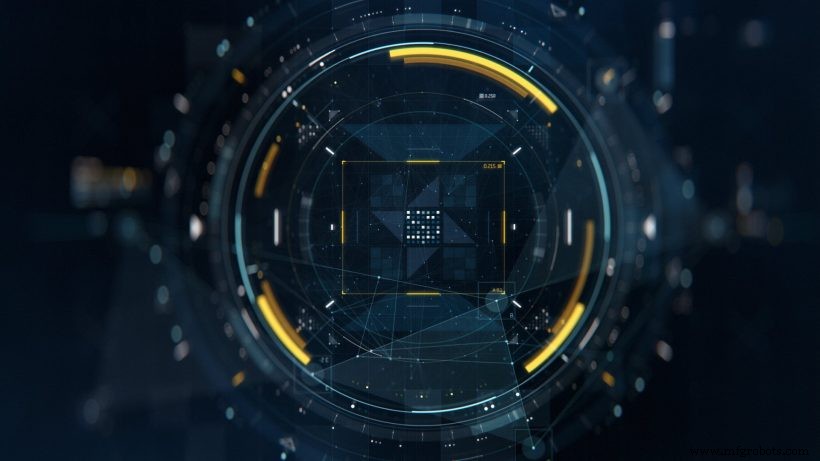
De 3D-printindustrie ontwikkelt zich in een verbazingwekkend tempo. In de afgelopen 12 maanden hebben een aantal bedrijven nieuwe technologieën aangekondigd en nieuwe machines gelanceerd, wat een opwindende toekomst voor de industrie aangeeft.
Om u te helpen op de hoogte te blijven van het laatste nieuws op het gebied van 3D-printen, vindt u hier onze lijst met 10 van de meest opwindende technologieën die onlangs zijn aangekondigd.
Metaal 3D-printen
1. Gelijktijdig afdrukken op meerdere niveaus van Aurora Labs
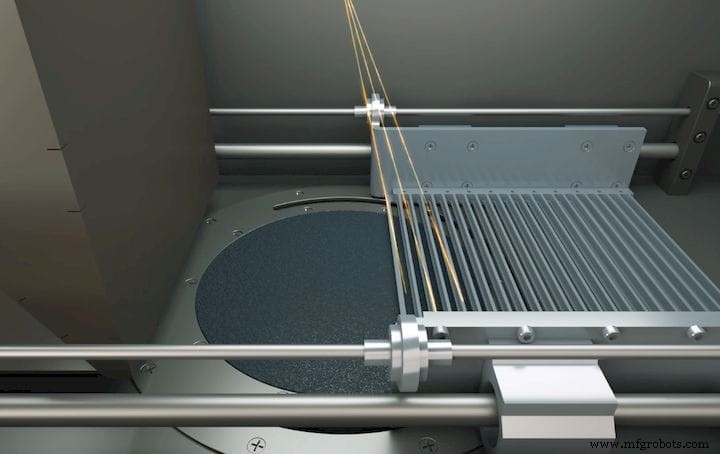
Hoewel het vooruitzicht om metalen onderdelen in 3D te printen met een snelheid van 1 ton metaal per dag misschien te mooi klinkt om waar te zijn, lijkt de Australische fabrikant van metalen 3D-printers, Aurora Labs, precies dat te bereiken.
Sinds 2014 ontwikkelt Aurora Labs een nieuwe metaal 3D-printtechnologie om metaal 3D-printen met veel hogere snelheden mogelijk te maken. De Multilevel Concurrent Printing (MCP™) werd voor het eerst onthuld op formnext 2018 en is gebaseerd op een bekende poederbedfusietechnologie, maar met een twist.
In tegenstelling tot traditionele poederbedtechnologieën waarbij één laag tegelijk wordt geprint, print MCP meerdere lagen tegelijk in één doorgang. Op formnext 2018 zei het bedrijf dat het in staat was om ongeveer 30 lagen tegelijk te printen, met als doel dit in de komende 12 maanden te verhogen tot 100 lagen.
Hoe werkt het?
De MCP-technologie heeft twee belangrijke elementen:een rasterachtig overschildermechanisme en meerdere laserstralen. Wanneer de print begint, schuift het recoater-mechanisme, dat meerdere hoppers heeft, over het printbed, waarbij elke hopper verschillende lagen poeder in één keer aflegt.
Terwijl één laag wordt aangebracht, wordt deze versmolten door een laser, die het poeder bereikt via de speciale openingen in de recoater. Tijdens diezelfde doorgang worden opeenvolgende lagen door lasers achtereenvolgens gedeponeerd en versmolten.
In wezen betekent dit dat meerdere lagen in één keer kunnen worden afgedrukt, waardoor de afdruktijd aanzienlijk wordt verkort.
In februari van dit jaar meldde het bedrijf dat het een afdruksnelheid van 113 had bereikt kilo per dag. Om de mijlpaal te illustreren, heeft Aurora Labs 3D een reeks 10 mm hoge titanium zeshoekige onderdelen geprint, wat slechts 20 minuten duurde.
Momenteel bereidt Aurora Labs zich voor op de commerciële lancering van zijn snelle productiesysteem aan het einde van het jaar. Zal het tegen die tijd een ton metaal per dag kunnen printen? De tijd zal het leren.
2. MELD Manufacturing's MELD-technologie
MELD Manufacturing Corporation heeft een nieuwe manier ontwikkeld om metalen in 3D te printen zonder ze te smelten.
De technologie, die al meer dan tien jaar in ontwikkeling is, werd vorig jaar voor het eerst onthuld met de introductie van MELD's grootschalige B8-automaat.
Hoe werkt het?
Het grootste verschil tussen MELD en andere metaal-AM-technieken is dat het een proces in vaste toestand is. Bij MELD worden metaalpoeders of -draden door een hol roterend gereedschap geleid, waarbij druk en wrijving het metaal vervormen en het in het materiaal eronder roeren.
Dit proces heeft veel unieke voordelen. Ten eerste creëert de MELD-technologie onderdelen die volledig dicht zijn, wat betekent dat ze geen daaropvolgende warmtebehandeling nodig hebben.
Ten tweede kan het proces niet alleen worden gebruikt om onderdelen te vervaardigen, maar ook om bestaande componenten te repareren en te coaten of om op maat gemaakte metaallegeringen te maken. Zoals Nanci Hardwick, CEO van MELD Manufacturing, aangeeft:
“Wij zijn de enige technologie die in staat is om zeer grote onderdelen te schalen en te bouwen of te repareren. Een andere unieke mogelijkheid is dat u een bestaand onderdeel kunt nemen, het in de machine kunt plaatsen en extra materiaal kunt toevoegen, of u nu een slijtvaste coating wilt op een zeer lichtgewicht materiaal, of u wilt het materiaal toevoegen om een versleten oppervlak te repareren. ”
MELD's 3D-printer heeft geen behuizing nodig en het proces vindt plaats in een open omgeving. Dit betekent dat er veel vrijheid is voor het maken van grotere onderdelen.
De technologie heeft echter enkele beperkingen. Een daarvan is de uitdaging van het printen van uitsteeksels. De technologie vereist ook aanzienlijke investeringen, aangezien de B8-machine $ 800.000 kost. Maar voordat ze zich committeren aan de investering, kunnen klanten de technologie uitproberen via de afdrukservice die MELD Manufacturing aanbiedt.
3. VELO 3D 's Intelligente Fusie
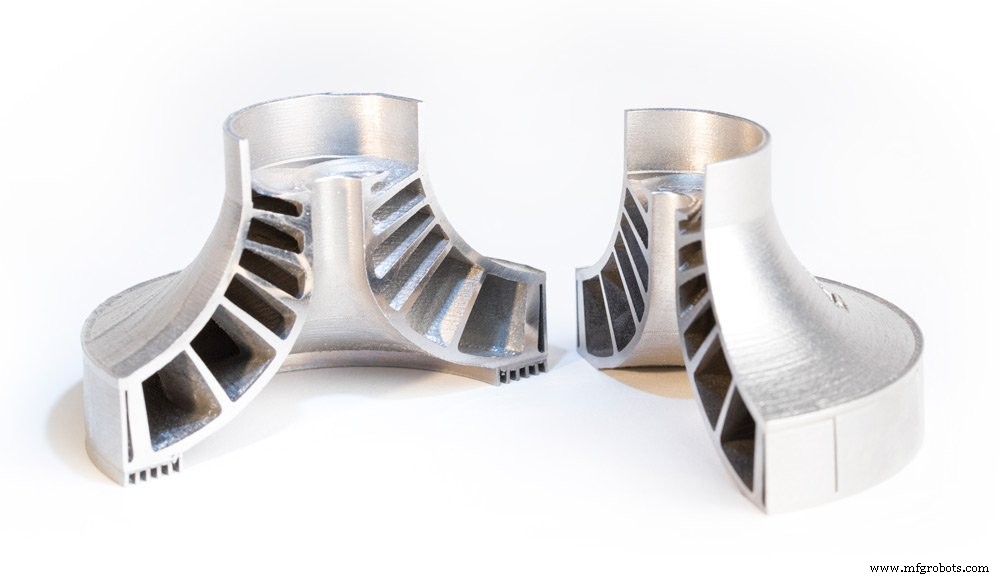
Het gebrek aan herhaalbaarheid en de noodzaak om ondersteunende structuren af te drukken zijn twee van de grootste uitdagingen van 3D-metaalprinten. VELO
3D
. uit Californië streeft ernaar deze uitdagingen op te lossen met zijn Intelligent Fusion-technologie.
Terwijl VELO
3D
werd opgericht in 2014, verscheen het bedrijf voor het eerst op de radar afgelopen herfst toen het zijn lasergebaseerde Sapphire 3D-printer onthulde. Intelligent Fusion™ vormt de ruggengraat van zowel de 3D-printer als VELO
3D
’s afdrukvoorbereidingssoftware, Flow™. Simpel gezegd, Intelligent Fusion™ maakt de nauwe integratie tussen hardware, software en het proces mogelijk.
Hoe werkt het?
Het systeem en de software zijn samen ontwikkeld om een nauw geïntegreerd proces te realiseren dat een aantal behoorlijk interessante functies in petto heeft.
De Sapphire 3D-printer is gebaseerd op een poederbedfusieproces, waarbij een laserstraal smelt en metaalpoeder laag voor laag versmelt tot een onderdeel. Het systeem is uitgebreid uitgerust met sensoren, waardoor het smeltbad met gesloten lus kan worden gecontroleerd en daardoor de consistentie van de onderdelen wordt verbeterd.
Aan de softwarekant, VELO
3D
heeft zijn Flow-software ontwikkeld om CAD-bestanden te gebruiken in plaats van STL-bestanden. Dit besluit heeft twee gevolgen. Ten eerste, aangezien het STL-formaat het oppervlak van een CAD-model met driehoeken benadert, resulteert het gebruik van CAD vanaf het begin in een hogere nauwkeurigheid.
Ten tweede kan de grootte van STL-bestanden erg groot zijn, wat de verwerking van bestanden omslachtig maakt. Door over te schakelen naar CAD als initiële bestandsindeling wordt de workflow voor de afdrukvoorbereiding dus eenvoudiger en sneller.
Bovendien is de Flow software ontwikkeld om zeer procesbewust te zijn. Dit betekent bijvoorbeeld dat het een simulatie kan uitvoeren voordat een afdruk start, en fouten kan voorspellen en voorkomen voordat ze optreden.
Combineer dit met Sapphire's closed-loop controlemogelijkheden, en u krijgt een zeer intelligent proces dat extreme betrouwbaarheid moet bieden.
Intelligent Fusion zou in staat zijn om succespercentages tot 90% te behalen bij de eerste afdruk, terwijl het aantal ondersteunende structuren drie tot vijf keer wordt verminderd.
Terwijl VELO3D doorgaat om de technologie te verbeteren en nieuwe klanten te werven, kijken we uit naar meer casestudies die de unieke mogelijkheden van VELO
3D
benadrukken ’s Intelligente Fusie.
4. HP's Metal Jet
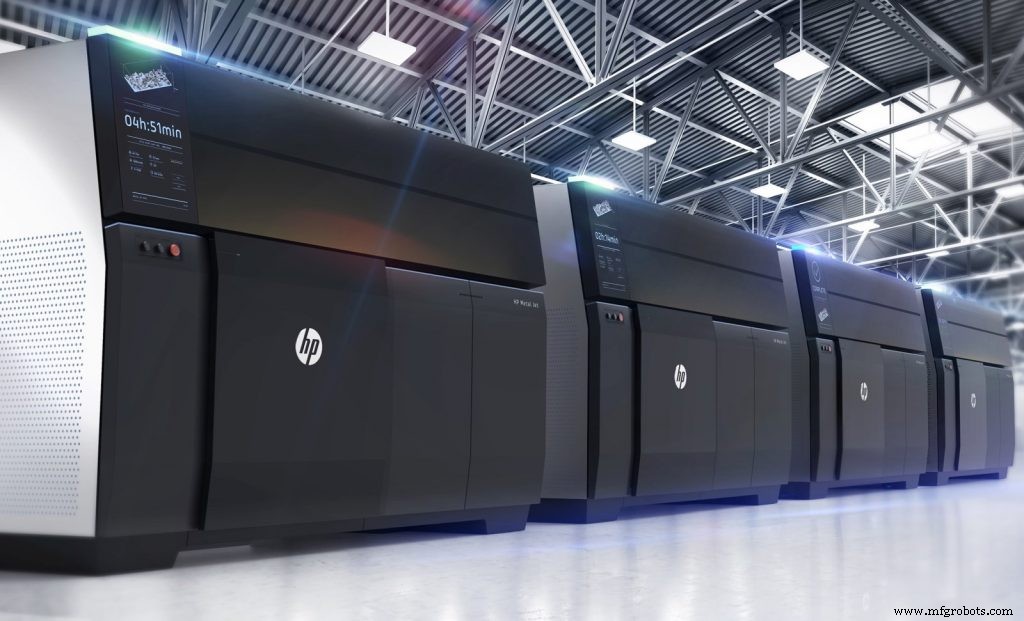
In de wereld van 2D-printen staan HP's printers synoniem voor hoge precisie en snelheid. In 2016 onthulde het bedrijf publiekelijk zijn overstap naar 3D-printen, met de lancering van zijn polymeer 3D-printer - Multi Jet Fusion.
Nadat HP zich aan de polymeerkant van 3D-printen heeft gevestigd, is het nu de metalen arena betreden en vorig jaar zijn Metal Jet 3D-printer aangekondigd. Het systeem is ontwikkeld om concurrerend te zijn met andere productiemethoden.
De technologie die dit mogelijk maakt, is Binder Jetting.
Hoe werkt het?
Bij Binder Jetting wordt een dun laagje metaalpoeder op het printbed afgezet. Een rij printkoppen beweegt boven het printbed en spuit kleine druppels van een bindmiddel - in wezen lijm - waar massief metaal nodig is. Wanneer een laag is voltooid, wordt een nieuwe laag poeder gelegd, gevolgd door een nieuwe doorgang van het bindmiddel.
Na het printen blijft het laatste deel in een "groene" staat en moet het een verhittingsproces ondergaan (sinteren genoemd) om het bindmiddel uit te branden en een dicht deel te creëren.
Dit proces heeft verschillende voordelen. Ten eerste is het snel. Met twee keer zoveel printkoppen in vergelijking met bestaande systemen, beweert HP dat zijn Metal Jet-printers tot 50 keer productiever zijn dan vergelijkbare binder- en lasersintermachines die momenteel op de markt zijn.
Ten tweede gebruikt het proces minder bindmiddel, waardoor het sinterproces sneller en goedkoper wordt.
“Bij metaalspuitgieten heb je doorgaans meer dan 10 gew.% bindmiddel dat moet worden uitgebrand. In ons geval hebben we minder dan 1%, wat een orde van grootte minder is, waardoor het sneller, goedkoper en veel eenvoudiger te sinteren is", zegt Tim Weber, HP's Global Head of Metals, in een interview met AMFG .
Interessant is dat Metal Jet enigszins lijkt op de technologie en waardepropositie achter het productiesysteem van Desktop Metal. Beide op binder jetting gebaseerde machines lijken de traditionele productie te verstoren door een grotere snelheid en schaalbaarheid mogelijk te maken. Desktop Metal beweert bijvoorbeeld dat zijn systeem meer dan 4 keer sneller is dan andere binder jetting-machines.
Terwijl het productiesysteem van Desktop Metal eerder dit jaar werd uitgebracht, staat de technologie van HP gepland voor een release in 2020 en is deze momenteel alleen beschikbaar via HP Metal Jet Production Service.
Zodra Metal Jet is uitgebracht, zal het spannend zijn om te zien hoe de twee systemen zich zullen verhouden in de overgang naar seriële AM-productie.
Polymeer 3D-printen
5. EOS's LaserProFusion
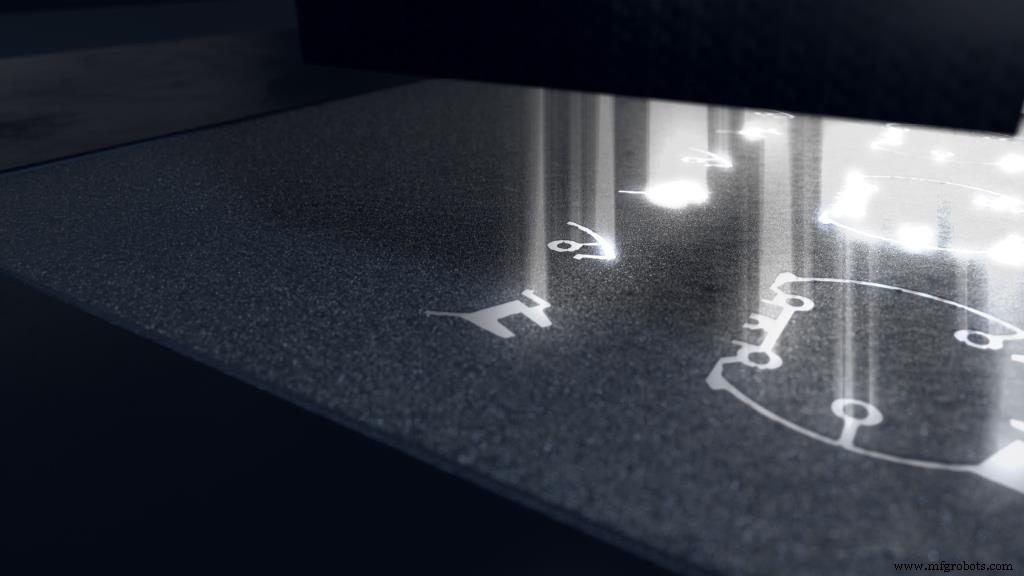
LaserProFusion is misschien wel een van de meest verwachte polymeer 3D-printtechnologieën. LaserProFusion, die in première ging op Formnext 2018, is een opkomend polymeer 3D-printsysteem van EOS dat belooft de 3D-productie van polymeer 10 keer sneller te maken dankzij de opname van een miljoen diodelasers.
EOS heeft een lange geschiedenis in polymeer 3D-printen, in het bijzonder met Selective Laser Sintering (SLS). In SLS wordt een laag poeder, meestal nylon, op een printbed gelegd en een laser vormt vervolgens de contouren van de dwarsdoorsnede van een onderdeel, waarbij poederdeeltjes samensmelten.
Terwijl de huidige SLS-machines een of enkele CO₂-lasers gebruiken, kan de LaserProFusion-technologie tot een miljoen diodelasers gebruiken. Hierdoor kan het systeem onderdelen maken, niet alleen met een hoge resolutie, maar ook met een veel hogere afdruksnelheid, wat in potentie kan concurreren met spuitgieten.
De technologie, die naar verluidt 8 jaar in ontwikkeling zou zijn geweest, zal echter niet eerder dan in 2021 worden vrijgegeven. Het wordt spannend om te zien welke impact LaserProFusion zal hebben als het zijn weg vindt de markt in.
6. Farsoon's Flight-technologie
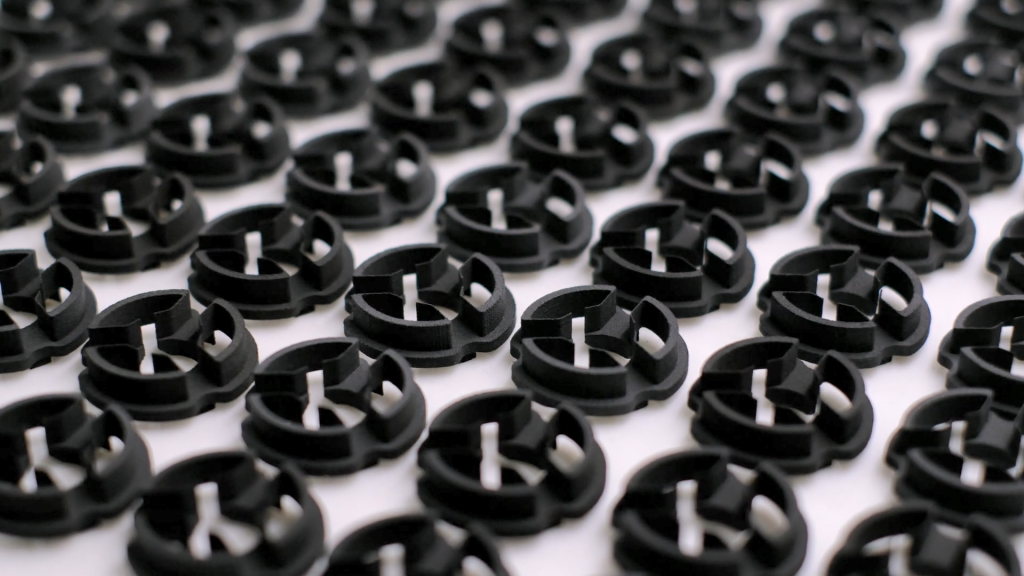
Een ander bedrijf dat een revolutie wil ontketenen in SLS-technologie is Farsoon. Om SLS nog sneller en nauwkeuriger te maken, maakt Farsoon gebruik van de kracht van een fiberlaser in zijn nieuwe Flight Technology.
Hoe werkt het?
In SLS wordt een laag poeder uitgespreid op een bouwplatform en vervolgens volgt een laser de contouren van één laag van een onderdeel, waarbij het poeder aan elkaar wordt gesinterd.
Om dit proces te verbeteren, heeft de Chinese fabrikant van 3D-printers een nieuw scansysteem ontwikkeld en, belangrijker nog, de standaard CO₂-laser vervangen door een fiberlaser.
Een fiberlaser systeem is in staat om meer vermogen aan het poederbed te leveren en de energieverdeling naar het materiaal te verbeteren. Dit komt omdat een fiberlaserstraal een kleinere laservlekgrootte mogelijk maakt. Dit vertaalt zich in de hogere vermogensdichtheid, waardoor het poeder in een kortere tijd kan worden gesinterd.
Gecombineerd resulteren deze voordelen in een scansnelheid van meer dan 20 m/s, wat ongeveer vier keer zo hoog is als bij vergelijkbare technologieën. Bovendien maakt het extra vermogen van een laser feature details zo klein als 0,3 mm mogelijk.
Ontworpen om de acceptatie van 3D-printen voor productie van grote volumes te stimuleren, is Flight Technology zeker een stap voorwaarts in deze richting.
7. Essentium's hogesnelheidsextrusie
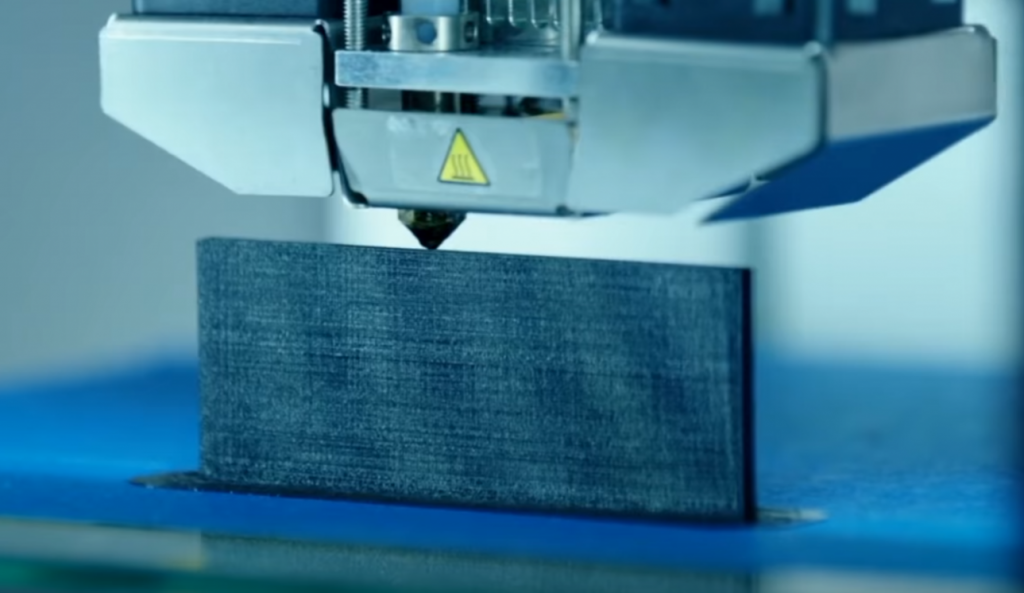
De in de VS gevestigde fabrikant van 3D-printers, Essentium, beweert de snelste 3D-extrusieprinter te hebben ontwikkeld.
Hoe werkt het?
Voor het eerst onthuld op Formnext 2018, is het High Speed Extrusion (HSE)-platform van Essentium gebaseerd op Fused Filament Fabrication (FFF)-technologie. In FFF wordt een thermoplastisch filament gesmolten en door een mondstuk geduwd, waarbij delen laag voor laag worden geprint. Een lange afdruktijd, met name voor grotere objecten, is een van de belangrijkste beperkingen van FFF.
Om deze uitdaging te overwinnen, bevat Essentium's HSE een aantal ontwerpkenmerken die het mogelijk tot een van de snelste beschikbaar.
De HSE maakt bijvoorbeeld gebruik van alle lineaire motoren, waardoor de printkop veel sneller (1 m/sec) en nauwkeuriger kan bewegen. Naar verluidt is het bewegingssysteem nauwkeurig tot op 30 micron positionering - vrij ongelooflijk bij dergelijke snelheden. Om de snelheid van het bewegingssysteem te evenaren, integreerde Essentium ook krachtige servomotoren in plaats van stappenmotoren.
Een ander element dat dit systeem vrij uniek maakt, is het eigen mondstuk van Essentium, de HSE Hozzle™, die in 3 seconden kan opwarmen van 20°C tot 500°C.
Naast de HSE-technologie heeft Essentium ook zijn FlashFuse-technologie ontwikkeld om zwakte van onderdelen in de Z-as (de richting waarin de lagen worden afgezet), een veelvoorkomend probleem met 3D-geprinte onderdelen te verhelpen .
De technologie omvat het neerslaan van een energiegevoelige gloeidraad en het aanleggen van een elektrische stroom. Deze stroom verwarmt het onderdeel, vormt de lagen effectief samen en creëert onderdelen die in alle richtingen even sterk zijn.
Gepland voor release later dit jaar, zal Essentium zijn FlashFuse- en HSE-technologie combineren in één enkel platform, genaamd de HSE 180•S.
Door de bewegingen, extrusie, temperatuur en, ten slotte, de sterkte van de onderdelen te optimaliseren, ligt Essentium op schema om een nieuwe maatstaf te zetten voor 3D-extrusieprinten.
8. Evolve Additive Solutions' STAP
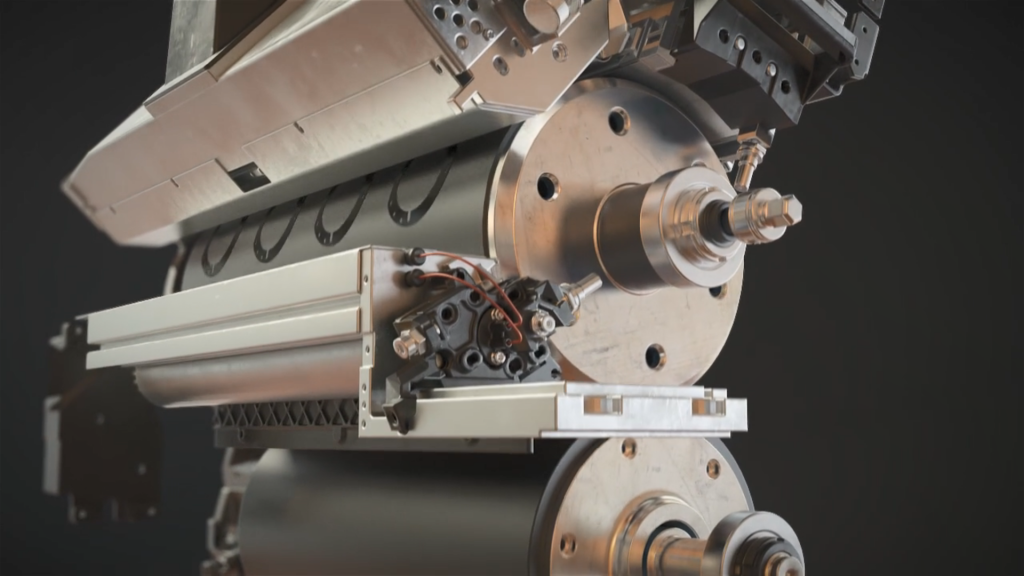
De verschuiving naar productie en het vermogen om te concurreren met traditionele productie is een veelvoorkomend thema voor veel 3D-printerfabrikanten. De spin-off van Stratasys, Evolve Additive Solutions, is geen uitzondering.
Evolve verscheen vorig jaar voor het eerst in de 3D-printscene met zijn Selective Toner Electrophotographic Process (STEP) — een technologie die het bedrijf al bijna tien jaar.
Hoe werkt het?
STEP is als geen ander bekend polymeer 3D-printproces dat momenteel op de markt verkrijgbaar is, in die zin dat het geen lasers gebruikt en ook geen plastic filamenten extrudeert. In plaats daarvan is het gebaseerd op dezelfde elektrofotografische printtechnologie die in veel kantoorprinters wordt gebruikt.
Het STEP-proces begint met het elektrostatisch opladen van een rol, die vervolgens over het poedermateriaal gaat, dat toner wordt genoemd. De ene laag toner plakt aan de rol en wordt vervolgens overgebracht op een transportband.
Op de transportband gaat het groeiende deel door een verwarmingseenheid, waar een nieuwe laag op de vorige wordt versmolten voordat de volgende laag materiaal wordt gelegd.
Deze technologie kan potentieel zeer hoge doorvoersnelheden mogelijk maken, waardoor het kosteneffectief is voor massaproductie 3D-printen.
Ook belangrijk is dat de 3D-geprinte onderdelen met behulp van het STEP-proces isotroop zijn, wat betekent dat ze sterk zijn in alle drie routebeschrijving. Dit is deels te wijten aan het feit dat de Evolve-machine niet alleen het onderdeel voorverwarmt, maar ook de volgende laag, wat resulteert in een superieure hechting tussen de lagen.
De technologie van Evolve zal naar verwachting pas commercieel beschikbaar komen 2020. Maar als dat zo is, kan het een geheel nieuwe manier zijn om polymeeronderdelen in 3D te printen.
9. Fortify's Fluxprint-technologie
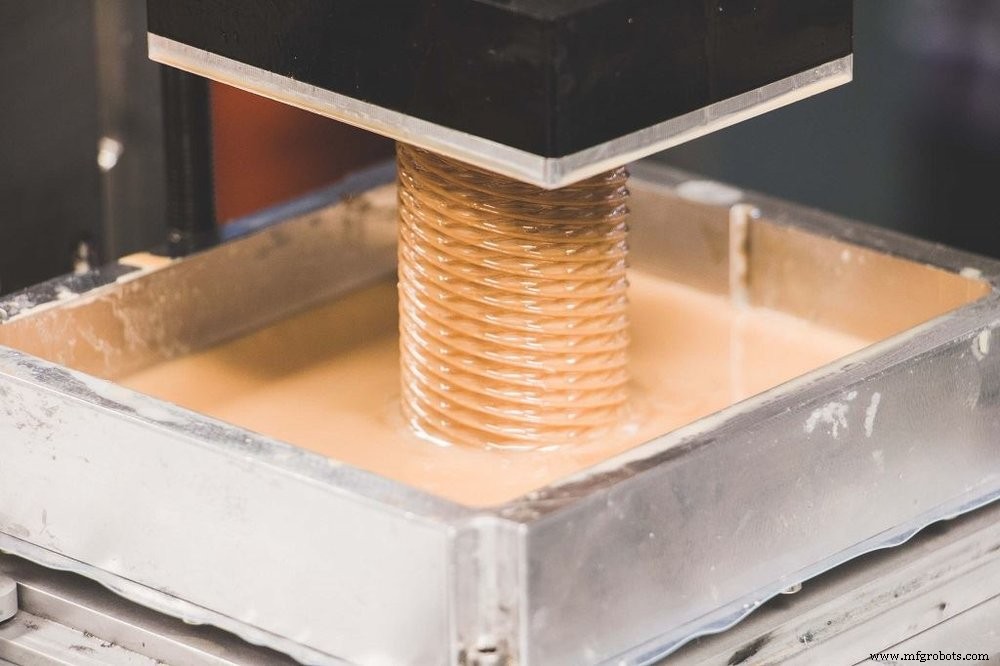
De in Boston gevestigde startup Fortify is onlangs op de markt gekomen met zijn unieke methode om extreem sterke, met vezels gevulde onderdelen te 3D-printen. Deze nieuwe methode wordt mogelijk gemaakt door Fortify's Fluxprint-technologie, die magnetische velden gebruikt om de uitlijning van vezels in een onderdeel te regelen.
Hoe werkt het?
De Fortify 3D-printer is gebaseerd op de Digital Light Processing-techniek, waarbij een digitaal lichtprojectorscherm wordt toegepast om polymeren die gevoelig zijn voor licht te laten stollen. Met het Fluxprint-proces worden de polymeren gemengd met gehakte vezels, die worden behandeld met een metalen coating.
Vervolgens wordt een magnetisch veld op de vezels aangebracht, waardoor ze zich kunnen oriënteren volgens de magnetische krachten.
In de volgende stap past de printer licht toe om één laag van een onderdeel uit te harden. Het proces herhaalt zich, laag voor laag, om de afdruk te voltooien.
Door de oriëntatie van vezels op elke laag te regelen, kan Fluxprint zeer stijve en sterke onderdelen maken. Deze technologie kan met name nuttig zijn voor het produceren van spuitgietmatrijzen en autogereedschappen.
Fortify wil zijn eerste commerciële 3D-printer in de komende 8 tot 12 maanden uitbrengen. We zijn verheugd om te zien hoe deze technologie vorm krijgt en we zullen in de toekomst zeker nog veel meer van Fortify horen.
10. Programmeerbare fotopolymerisatie van Origin
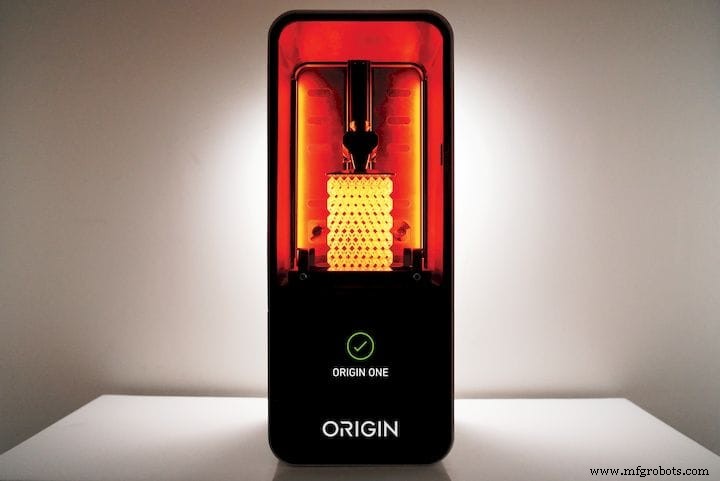
De in de VS gevestigde startup, Origin, kwam uit stealth op formnext 2018 met de ambitie om massaproductie mogelijk te maken met 3D-printen. Op de RAPID-beurs vorige maand zette Origin een stap om zijn belofte waar te maken en introduceerde de Origin One 3D-printer.
Op het eerste gezicht zou je denken dat de Origin One simpelweg nog een andere hars 3D-printer. Het geheim van de Origin One ligt echter in de machine. Het bedrijf heeft een Programmable Photopolymerisation (P3)-technologie ontwikkeld, die een hoge doorvoer, minder nabewerking en een veel groter aantal te printen materialen mogelijk maakt.
Hoe werkt het?
In tegenstelling tot de huidige 3D-printers van hars, is P3 zuurstofvrij. De 3D-printer van Origin maakt gebruik van een inert gas, waardoor het printbed kan worden weggetrokken om de volgende laag met extreem weinig kracht te bouwen. Door de kracht te verminderen, kan de machine een hogere doorvoer bereiken.
Bovendien zegt Origin de benodigde nabewerkingstijd aanzienlijk te hebben kunnen verkorten door het uithardingsproces in zijn 3D-printer te integreren. Bij andere 3D-harsprinters vindt het uitharden meestal plaats in een gespecialiseerde unit, soms tot enkele uren.
Met P3 bereiken onderdelen tijdens het printen 99% van hun uiteindelijke eigenschappen. Vervolgens worden ze gewoon schoongemaakt en snel door een laatste UV-uithardend transportsysteem geleid dat gebruik maakt van een krachtige microgolffusielamp. Het proces zou niet meer dan vijf minuten duren, wat vrij opmerkelijk is.
Momenteel heeft Origin ongeveer 50 gevalideerde materialen die zijn geoptimaliseerd voor zijn P3-proces. Dit is bereikt dankzij Origin's open materiaalbenadering, die vertrouwt op chemische experts om de keuze aan materialen die beschikbaar zijn voor gebruikers uit te breiden.
Hoewel het bedrijf net is begonnen aan zijn reis om de productie te transformeren, heeft Origin's recente golf van partnerschappen met grote materiaalbedrijven en schoenenfabrikant ECCO suggereren dat ze een veelbelovende toekomst voor de boeg hebben.
Het potentieel van 3D-printen benutten
Ondanks dat ze zo divers zijn, hebben alle technologieën op onze lijst één gemeenschappelijk doel:3D-printen verder brengen van de oorsprong van prototypes naar volledige industriële productie. Om dit te bereiken zijn de technologieën ontwikkeld om sneller, nauwkeuriger en betrouwbaarder te zijn.
Het is duidelijk dat het enige tijd zal duren voordat deze beloften worden vervuld. Dat gezegd hebbende, leggen de opkomende technologieën de basis om 3D-printen voorbij de huidige beperkingen naar de mooie toekomst te duwen.
3d printen
- Scalmalloy:het nieuwste hoogwaardige materiaal voor 3D-metaalprinten
- 3D-printen in 2018:7 trends die de industrie hebben gevormd
- 10 spannende manieren waarop 3D-printen wordt gebruikt in de consumentengoederenindustrie
- Interview met expert:VELO3D's VP of Technology Partnerships over uitbreiding van de mogelijkheden van 3D-metaalprinten
- 10 spannende voorbeelden van 3D-printen in de auto-industrie in 2021
- Hoe volwassen zijn 3D-printtechnologieën voor metaal?
- Hoe de hardwaremarkt voor 3D-printen evolueert in 2020
- 9 Fortune 500-bedrijven die pionieren met het gebruik van industrieel 3D-printen
- De evolutie van HP's 3D-printtechnologie:van polymeer tot metaal AM
- De 6 belangrijkste vragen die de meeste mensen hebben over 3D-printen
- 4 factoren die de kosten van metaalproductie beïnvloeden