Alles wat u moet weten over het spuiten van metaalbindmiddelen
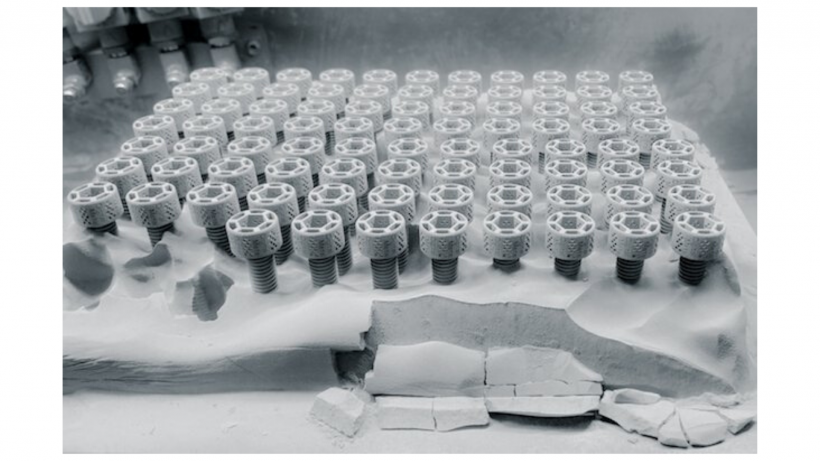
Afbeelding hierboven:de M5-schroeven 3D geprint met het systeem van Digital Metal [Image credit:Digital Metal]
Het stralen van metalen bindmiddelen ondergaat een renaissance. In de afgelopen tien jaar zijn veel nieuwe bedrijven een concurrentiemodus ingegaan, elk met zijn eigen kijk op deze technologie.
Dergelijke activiteiten worden gedeeltelijk gevoed door de vele lucratieve kansen die deze technologie biedt. Ten eerste kan de hoge snelheid en precisie van het proces voor het spuiten van metaalbindmiddelen ertoe bijdragen dat het een nieuwe productiemethode voor grote volumes wordt.
Maar welke ontwikkelingen zorgen voor het succes van deze technologie?
Vandaag zullen we kijken naar hoe het stralen van metalen bindmiddelen is geëvolueerd en waarom het van de grond komt als een nieuwe productietechnologie.
De oorsprong van het spuiten van metaalbindmiddelen
De oorsprong van de technologie voor het stralen van metaalbindmiddelen gaat terug tot 1993, toen het Massachusetts Institute of Technology (MIT) een op inkjet gebaseerd proces ontwikkelde om driedimensionale objecten te maken met behulp van metaalpoeders.
Interessant is dat de term "3D-printen" oorspronkelijk werd bedacht door MIT met betrekking tot technologie voor het stralen van metaalbindmiddelen.
Productiebedrijf, Extrude Hone Corporation, verkreeg in 1996 een exclusieve licentie voor de technologie van MIT. Sindsdien heeft het bedrijf metaalbinderstraalsystemen ontwikkeld en op de markt gebracht, met de eerste 3D-printer, ProMetal RTS‐300, die in 1999 aan Motorola werd geleverd.
ExOne, dat in 2005 is afgesplitst van Extrude Hone Corporation, bleef tot het begin van 2010 het enige bedrijf dat diensten en systemen voor het spuiten van metaalbindmiddelen aanbood. Op dat moment begonnen de vroege MIT-patenten voor de technologie af te lopen, waardoor nieuwe bedrijven op de markt kwamen.
Sindsdien is het stralen van metaalbindmiddelen nieuw leven ingeblazen met een visie om deze technologie echt geschikt te maken voor productie in verschillende sectoren.
Hoe werkt het spuiten van metaalbindmiddel?
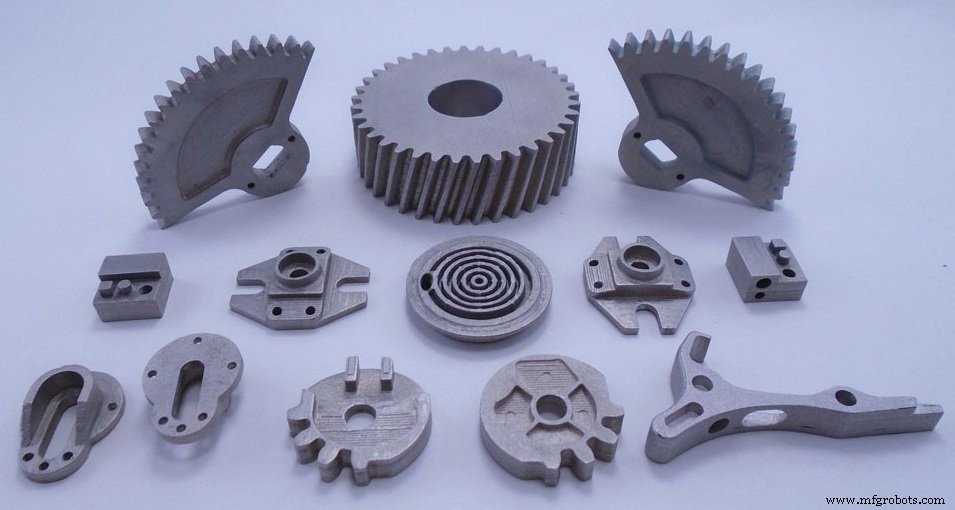
Bij het spuiten van metaalbindmiddelen wordt selectief een vloeibaar bindmiddel aangebracht om poederdeeltjes laag voor laag met elkaar te verbinden.
Het proces begint met het verspreiden van een dunne laag poeder, waarbij printkoppen strategisch druppeltjes bindmiddel in het poederbed afzetten. De drukplaat zakt dan en er wordt nog een laag poeder uitgestrooid.
Het proces herhaalt zich totdat het onderdeel compleet is, met ongebruikt poeder (ongeveer 95%) gerecycled.
Bij metal binder jetting blijven delen die net zijn bedrukt in een fragiele groene staat en hebben ze een volgende nabewerking nodig, zoals sinteren en infiltratie, om het onderdeel te versterken.
Naast metalen kan bindmiddelstralen ook werken met een reeks andere materialen, zoals zand en keramiek.
Nabewerkingsstappen voor het spuiten van metaalbindmiddelen
Traditionele bindmiddelstraaltechnologie werkt door een printkop te gebruiken om een vloeibaar bindmiddel op poederlagen aan te brengen.
Bij het printen van metalen met Binder Jetting-technologie zullen de onderdelen echter verschillende nabewerkingsstappen vereisen, aangezien ze aanvankelijk in hun groene staat worden bedrukt, wat betekent dat ze lage mechanische eigenschappen hebben en vaak zwak en broos zijn. De nabewerkingsfase is bedoeld om de onderdelen te versterken en omvat uitharden, sinteren, infiltratie en andere afwerkingsprocessen.
Door uitharden wordt de sterkte van de groene delen vergroot, zodat ze veilig van het printbed kunnen worden verwijderd. Tijdens het proces worden de onderdelen gedurende enkele uren uitgehard in een oven op ongeveer 200°C, wat resulteert in veel sterkere onderdelen.
Ondanks de uitharding zullen uw metalen onderdelen nog steeds zeer poreus zijn. U kunt de porositeit van de onderdelen echter aanzienlijk verminderen door sinter- of infiltratieprocessen. Meestal vindt het sinterproces plaats in een oven met een gecontroleerde atmosfeer, waar het onderdeel 24-36 uur bij ongeveer 100 ° C wordt verhit en het bindmiddel wordt weggebrand. Dit helpt om de metaaldeeltjes samen te smelten en resulteert in een sterk metalen onderdeel met een lage porositeit. Sinteren kan echter een niet-homogene krimp van het onderdeel veroorzaken en kan moeilijk te voorspellen zijn - hier moet dus rekening mee worden gehouden in de ontwerpfase.
Om een hoge dichtheid te bereiken, moet het onderdeel worden geïnfiltreerd om de holtes op te vullen die zijn achtergelaten door het bindmiddel dat wordt weggebrand. Dit wordt meestal gedaan door gesmolten brons aan te brengen om de resterende holtes in het onderdeel te infiltreren. Het ondergaan van deze nabewerkingsstappen zal de mechanische eigenschappen van het metalen onderdeel aanzienlijk verbeteren; bronsinfiltratie van roestvrij staal kan bijvoorbeeld een uiteindelijke dichtheid van 95% bereiken.
Ten slotte, hoewel optioneel, kan het onderdeel worden gepolijst en geplateerd met goud of nikkel, wat een esthetisch aangename oppervlakteafwerking mogelijk maakt.
Waarom neemt metaalbinderjetting een vlucht als productietechnologie?
Metalen bindmiddelstralen biedt een aantal unieke voordelen, waardoor de toepassing ervan voor productietoepassingen wordt vergemakkelijkt.
Ten eerste smelt het metaalpoeder tijdens het printproces niet door bindmiddelstralen, waardoor problemen met de opbouw van restspanningen worden geëlimineerd.
Ten tweede zijn er geen ondersteunende structuren nodig voor het spuitproces van het metaalbindmiddel, omdat geprinte delen omgeven zijn door los, ongebruikt poeder. Beide voordelen helpen om de nabewerking tot een minimum te beperken.
Bovendien zijn binder jetting-machines goedkoper dan 3D-printers op basis van SLM- of DED-processen. Een reden hiervoor is dat ze geen dure lasers of elektronenstralen gebruiken.
Nieuwere spuitmachines voor metaalbindmiddelen kunnen ook metaalspuitgieten (MIM) -poeders gebruiken. Deze zijn aanzienlijk goedkoper dan metaalpoeders die speciaal zijn ontwikkeld voor 3D-printen, die doorgaans in lage volumes worden geproduceerd met behulp van dure productiemethoden zoals gasverneveling.
Door over te schakelen op MIM-poeders kunnen fabrikanten daarom de bedrijfskosten voor deze technologie verder verlagen.
Naast goedkopere grondstoffen biedt binder jetting de mogelijkheid om zeer nauwkeurige onderdelen te printen met mechanische eigenschappen die vergelijkbaar zijn met die van traditioneel vervaardigde metalen componenten.
Ten slotte is de snelheid van het spuitproces met metaalbindmiddel doorgaans sneller dan die van andere metalen 3D-printprocessen. Al deze voordelen gecombineerd resulteren in een zeer schaalbare en productievriendelijke technologie.
De nieuwste ontwikkelingen op het gebied van het stralen van metalen bindmiddelen
De jaren 2010 markeren een nieuw tijdperk voor het stralen van metalen bindmiddelen. Van startups tot meer gevestigde spelers, een aantal bedrijven is actief op zoek naar de grenzen van wat momenteel mogelijk is met metaalbindende jettingtechnologie.
ExOne blijft innoveren
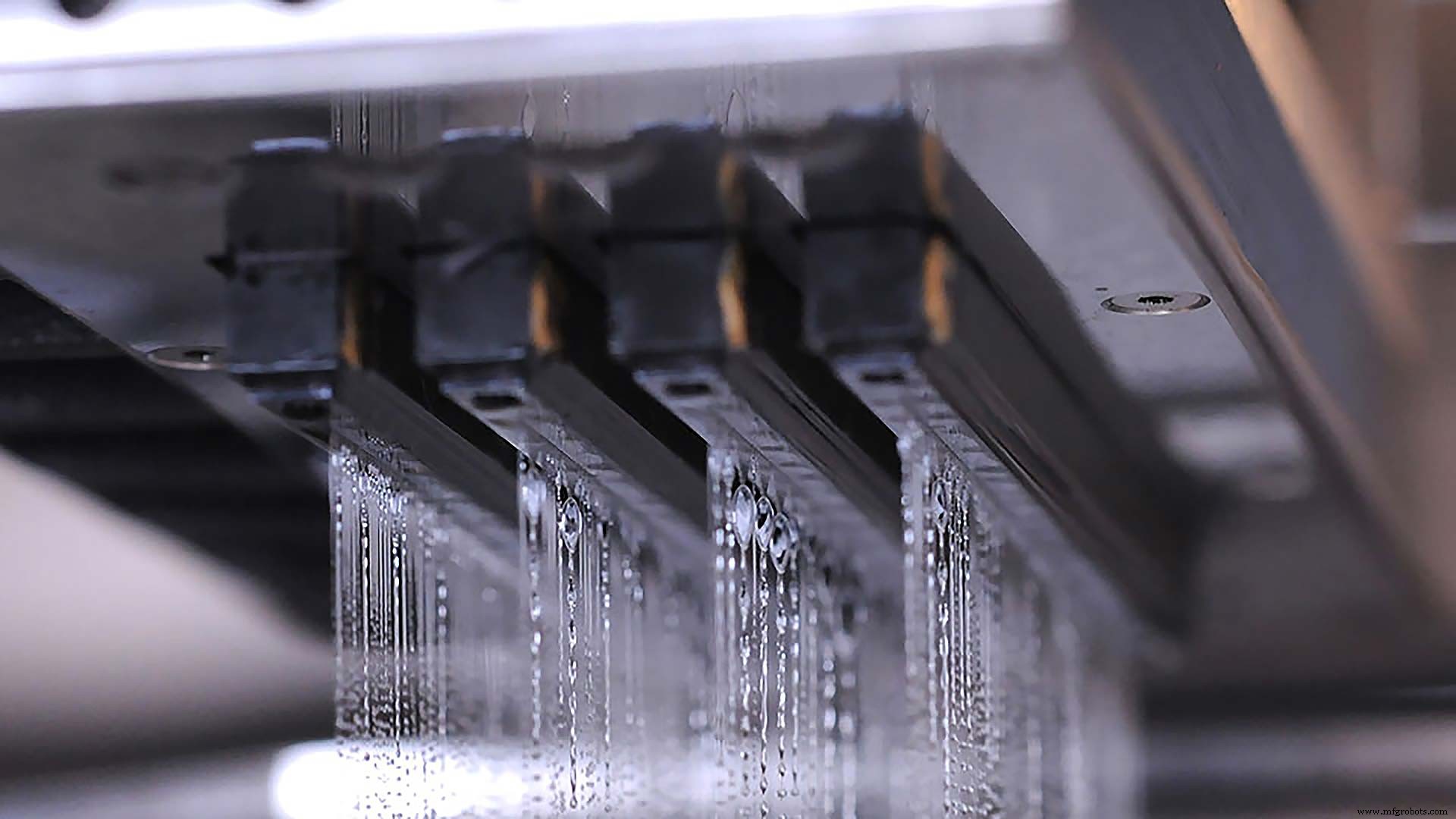
ExOne is een van de oudste spelers in de arena voor het stralen van metalen bindmiddelen. In de loop van zijn geschiedenis heeft ExOne vier metalen binder jetting-systemen gelanceerd, waarbij elk een evolutie is ten opzichte van de vorige.
Zo introduceerde het bedrijf in 2018 de Innovent+, waarmee op ExOne een nieuwe generatie metaalbinderstraalsystemen werd gemarkeerd. Hoewel het systeem langzamer is dan de vorige M-Flex 3D-printer van ExOne, heeft het twee nieuwe belangrijke functies.
Ten eerste is het uitgerust met een ultrasone overcoater, ontwikkeld om de poedervloeibaarheid te verbeteren en materiaalwisseling te vereenvoudigen. ExOne zegt dat de nieuwe recoater de meest geavanceerde poederdoseringstechnologie op de markt vertegenwoordigt.
De recoater wordt geleverd met vier schermconfiguraties voor een grotere materiaalcompatibiliteit. Deze functie speelt in op een andere belangrijke ontwikkeling:de machine kan standaard MIM-poeders verwerken.
Andere 3D-printers van metaal met poederbed, met name printers die een laser of een elektronenstraal gebruiken, hebben speciaal samengestelde poeders nodig om consistent te werken. Dergelijke poeders zijn echter vaak veel duurder dan materialen voor traditionele metaalverwerkingstechnologieën.
Door de Innovent+ in staat te stellen MIM-poeders te ondersteunen, kan ExOne kostenbesparingen en grotere materiaalflexibiliteit introduceren voor de gebruikers van zijn machines.
Het bedrijf blijft innoveren en heeft de technologie achter de Innovent+ opgeschaald naar een X1 25PRO 3D-printer op productieniveau. De machine, die vorige maand werd geïntroduceerd, kan maar liefst 10 verschillende materialen printen op zijn grote bouwvolume van 400 x 250 x 250 mm.
Met dit systeem wil het bedrijf de productie mogelijk maken van industriële metalen componenten met een hoge resolutie, nauwe toleranties en verbeterde oppervlakteafwerkingen.
Digital Metal:automatiseren van het spuiten van metaalbindmiddelen
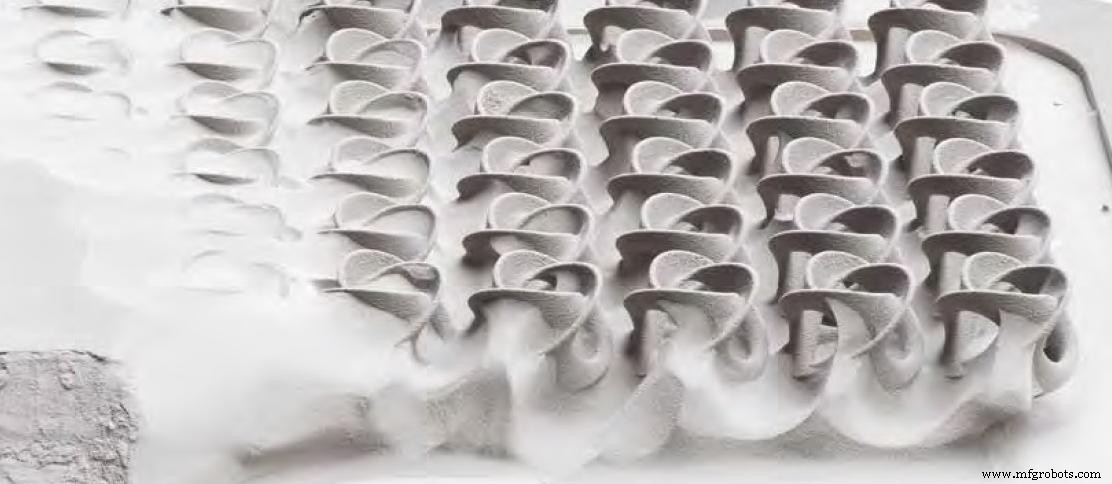
Een ander bedrijf dat zijn stempel drukt op de ontwikkeling van metaalbindmiddelstralen is Digital Metal, een dochteronderneming van een toonaangevende metaalpoederproducent Höganäs Group.
Digital Metal is opgericht in 2012 en begon in 2013 met het aanbieden van zijn metaalbinder-jetting-technologie als een service.
In 2017 lanceerde Digital Metal zijn DM P2500 3D-printer, bedoeld voor de serieproductie van kleine, complexe onderdelen.
De machine werkt door een laag metaalpoeder uit te strooien met een dikte van 0,042 mm. Een bindmiddel wordt vervolgens gespoten volgens de geometrie van het onderdeel. Dit proces is naar verluidt nauwkeurig en herhaalbaar, waardoor het zeer kleine maar ongelooflijk gedetailleerde onderdelen kan maken met een resolutie van 35 micron.
Het daaropvolgende sinterproces resulteert in een gemiddelde oppervlakteruwheid van Ra 6,0 micron, fijn genoeg voor veel eindgebruiksonderdelen en functies zoals interne kanalen.
Digital Metal zegt dat zijn metalen 3D-printers al meer dan 300.000 componenten hebben geproduceerd in verschillende industrieën, waaronder ruimtevaart, luxegoederen, tandheelkundig gereedschap en industriële apparatuur.
Om zijn technologie verder te ontwikkelen, heeft Digital Metal vorig jaar een volledig geautomatiseerd productieconcept gelanceerd.
Volgens dit concept zal een robot de meeste processtappen uitvoeren, zoals het voeden van de printer met bouwdozen en deze vervolgens verwijderen voor nabewerking. Het doel is om al het handmatige werk te elimineren om een continue productie van grote volumes mogelijk te maken.
Door deze productielijn zonder handen te lanceren, heeft Digital Metal een enorme sprong voorwaarts gemaakt met zijn metaalbindmiddel jetting-technologie.
HP's Metal Jet:3D-printen tot een kostenbesparende productiekeuze maken
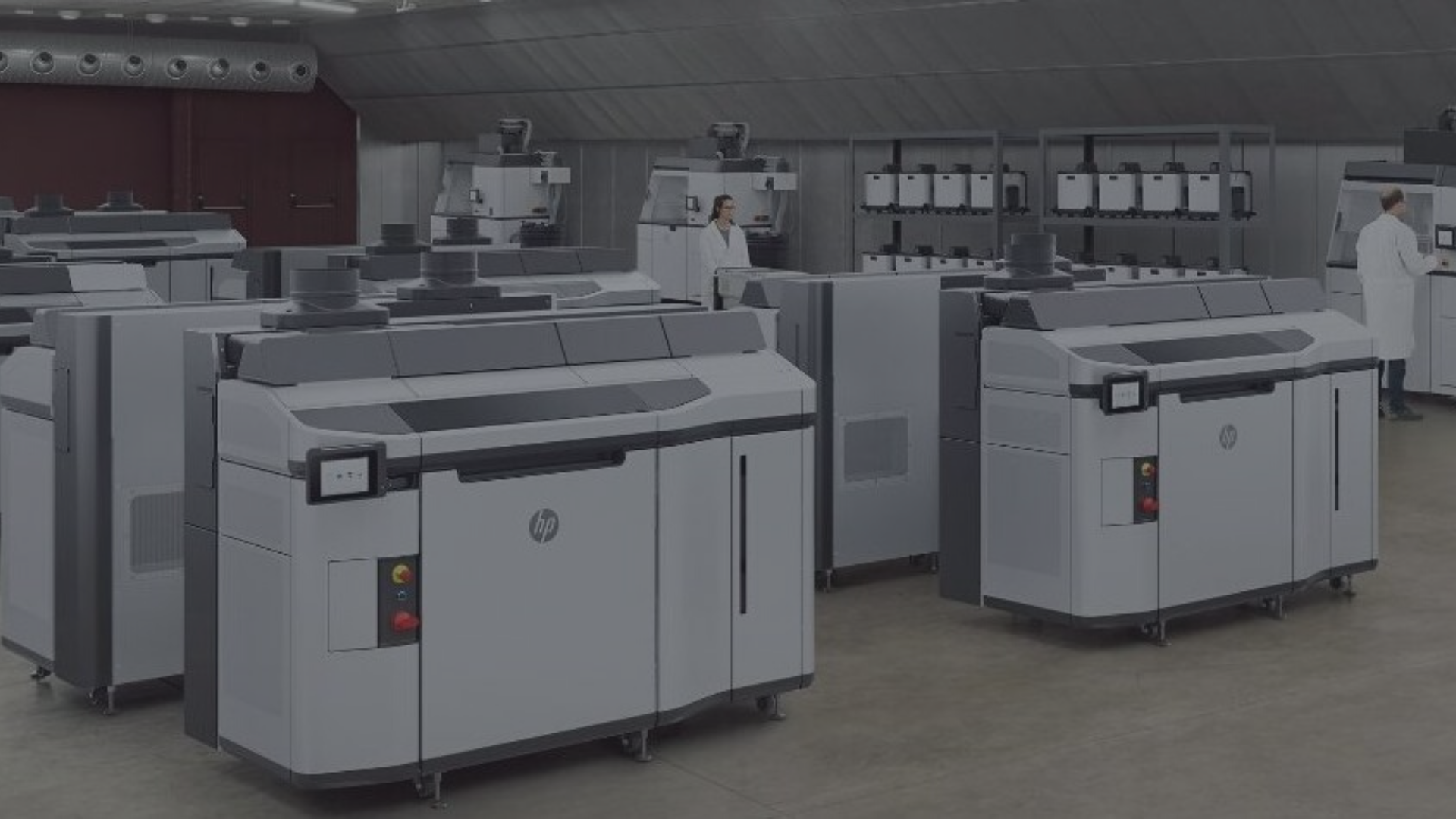
Na de onthulling van zijn Multi Jet Fusion-technologie voor polymeeronderdelen in 2016, introduceerde HP in 2018 de volgende uitbreiding van zijn additievenaanbod:een Metal Jet 3D-printsysteem.
De nieuwe metalen 3D-printer wordt aangedreven door binder jetting-technologie. Het unieke voordeel dat HP met deze technologie heeft geïntroduceerd, ligt echter in de innovatieve printkop- en inkttechnologie.
Hoewel binder jetting-technologie inherent snel is, heeft HP zijn kennis van printkoptechnologie toegepast om het nog sneller te maken. Het Metal Jet-systeem is uitgerust met 6 printkoppen met elk 5.280 nozzles. Het hebben van deze meerdere rijen spuitmondjes zorgt voor meer productiviteit en betrouwbaarheid voor de printer.
Bovendien heeft HP, door gebruik te maken van haar expertise in inkttechnologie, een innovatief bindmiddel ontwikkeld om het sinterproces sneller en goedkoper te maken.
“Bij metaalspuitgieten heb je doorgaans meer dan 10 gewichtsprocent bindmiddel dat moet worden uitgebrand. In ons geval hebben we minder dan 1%, wat een orde van grootte minder is, waardoor het sneller, goedkoper en veel eenvoudiger te sinteren is", zegt Tim Weber, HP's Global Head of Metals, in een interview met AMFG .
Deze gecombineerde vooruitgang resulteert in een metalen 3D-printer waarvan wordt gezegd dat deze besparingen en efficiëntie oplevert die vergelijkbaar zijn met conventionele productietechnologieën.
HP verkoopt de machine nog niet. In plaats daarvan heeft het bedrijf een service voor de productie van onderdelen gelanceerd die ernaar streeft de 3D-printer in 2020 commercieel beschikbaar te maken. Gezien de beweringen die HP heeft gedaan over Metal Jet, zou deze technologie de sleutel kunnen worden tot het ontsluiten van een duurzame waardepropositie voor 3D-metaalprinten in hoge -volumeproductie.
3DEO:Combineren van bindmiddelstralen en frezen
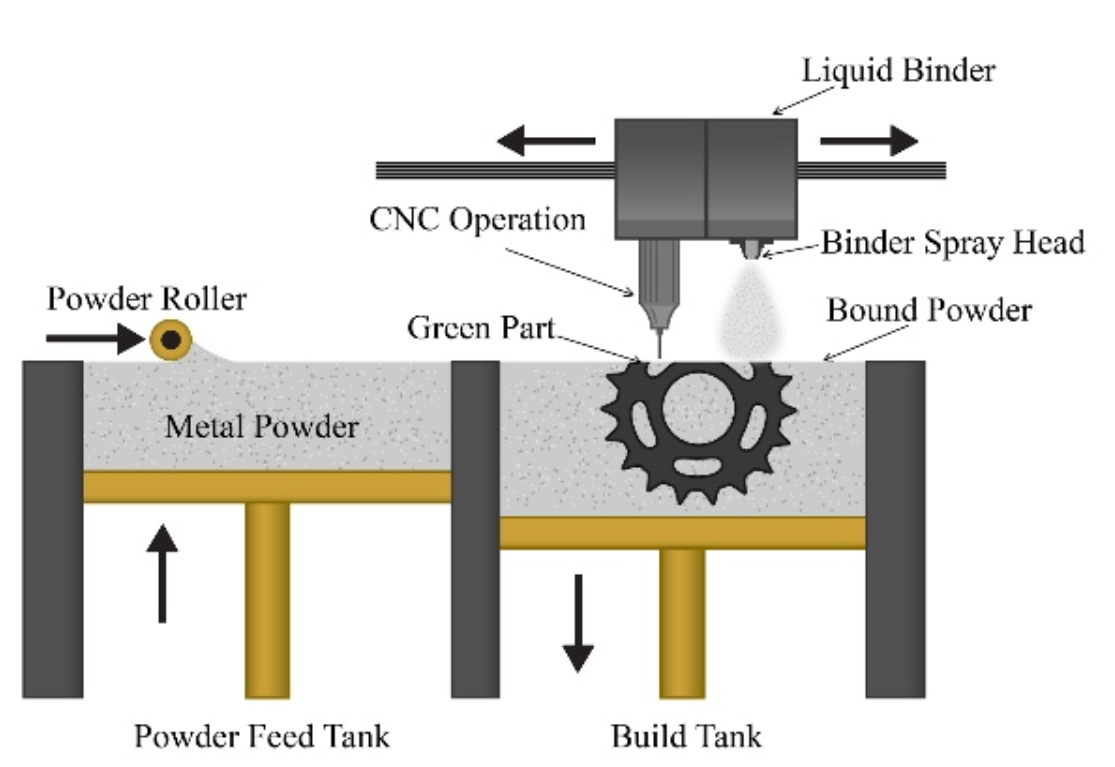
Veel bedrijven willen 3D-printen van metaal concurrerend maken met andere productietechnieken. Een voorbeeld van zo'n bedrijf is 3DEO, dat in 2016 werd opgericht met als doel om grootschalige productie mogelijk te maken door middel van metaalbindmiddelstralen.
Om dit te bereiken heeft het bedrijf het proces volledig opnieuw uitgevonden. In plaats van inkjet te gebruiken om selectief bindmiddel af te zetten, gebruiken de machines van 3DEO een gepatenteerd spuitsysteem om het bindmiddel gelijkmatig over de hele laag aan te brengen.
Het resultaat is een harde, dunne laag metaalpoeder die vervolgens wordt gemalen met behulp van micro-vingers. De CNC-bewerking snijdt de vorm van het onderdeel voor elke laag uit.
Deze technologie, Intelligent Layering genaamd, vertegenwoordigt het eerste voorbeeld van het combineren van binder jetting en CNC-frezen tot een hybride systeem. Door een dergelijke combinatie kan 3DEO na sinteren zeer nauwkeurige kleine metalen onderdelen maken met een dichtheid van meer dan 99,5%.
De Intelligent Layering-technologie van 3DEO wordt momenteel alleen aan klanten aangeboden via de productieservice van het bedrijf. Door zijn technologie te beperken tot zijn eigen productieservice, garandeert 3DEO een hoge kwaliteit van geprinte onderdelen terwijl het zijn platform zeer flexibel houdt.
Momenteel werkt 3DEO aan enkele van de grootste orders in de metaal 3D-printindustrie en heeft onlangs een inkooporder voor 28.000 onderdelen binnengehaald.
Hoewel het bedrijf niet van plan is om zijn machines te verkopen, dienen de groeiende productievolumes als een validatie van het vermogen van binder jetting om productieonderdelen te leveren die vergelijkbaar zijn met conventioneel vervaardigde componenten.
Desktop Metal:metalen onderdelen printen met een opvallende snelheid
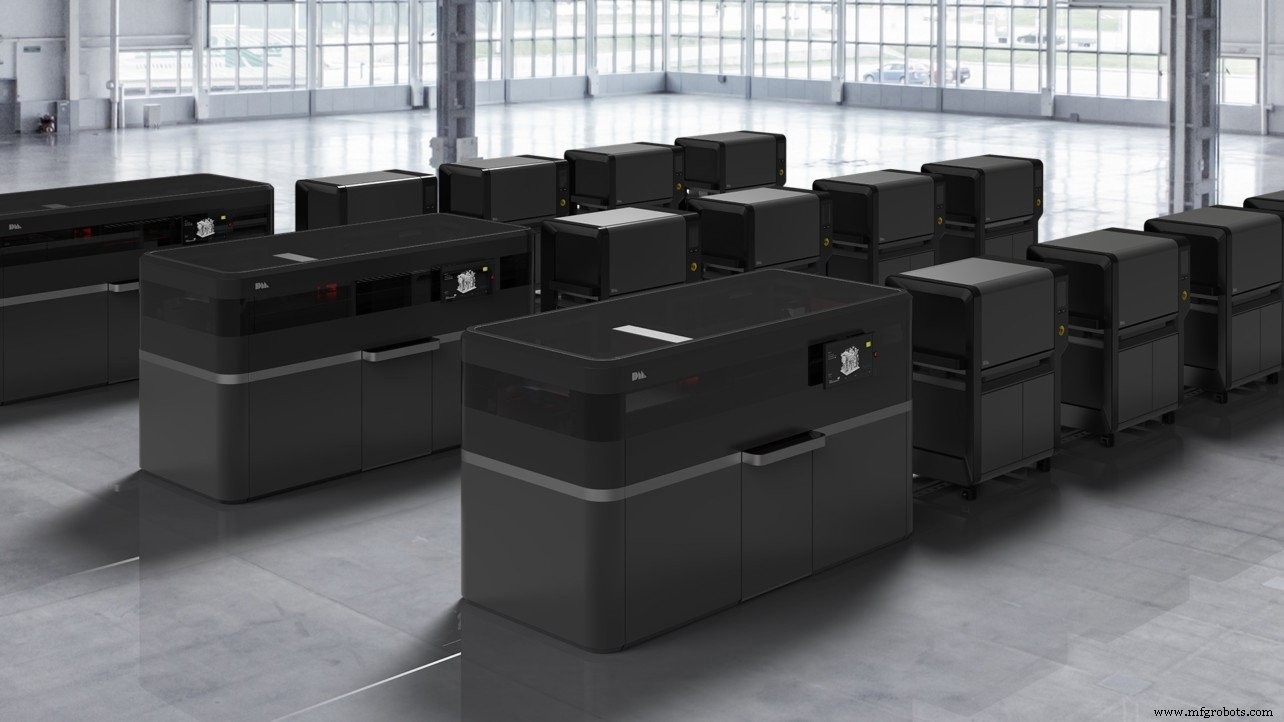
De in Boston gevestigde startup Desktop Metal is in 2015 opgericht met als doel de belofte van 3D-printen voor productie op grote schaal waar te maken. Om dit te bereiken heeft het bedrijf een extreem snel productiesysteem ontwikkeld.
De technologie achter de metalen 3D-printer is wat het bedrijf Single Pass Jetting (SPJ) noemt, een snellere versie van het typische binder jetting-proces.
Het systeem wordt geleverd met twee printkoppen over de volledige breedte, geavanceerde poederverspreiders en een antiballistisch systeem dat poeder en print effectief verspreidt in een enkele snelle doorgang over het bouwgebied.
Met een bouwvolume van 750 x 330 x 250 mm maakt dit bidirectionele systeem afdrukken met hoge resolutie mogelijk tot 12.000 cm3/uur, wat neerkomt op meer dan 60 kg metalen onderdelen per uur. Een dergelijke snelheid is orden van grootte sneller dan andere metalen 3D-printers op de markt, waardoor het ideaal is voor de productie van complexe metalen onderdelen in hoge volumes.
Bovendien is het productiesysteem het eerste binderjetsysteem dat is uitgerust met een industriële inerte omgeving met gasrecycling en terugwinning van oplosmiddelen voor het veilig printen van reactieve metalen. Dit opent de mogelijkheid om een breder scala aan metalen te bedrukken, bijvoorbeeld aluminium.
Met zijn productiesysteem heeft Desktop Metal de voordelen van metal binder jetting-technologie gemaximaliseerd door een aanzienlijke snelheidsverbetering toe te voegen.
Desktop Metal heeft zijn productiesysteem pas onlangs beschikbaar gemaakt voor aankoop, dus het zal enige tijd duren om te zien of de beweringen over de productiesnelheid worden bewezen. Maar als dat zo is, wordt het productiesysteem de snelste 3D-printer voor binderjetting die momenteel op de markt verkrijgbaar is.
Kijkend naar de toekomst
Metal binder jetting wordt een van de belangrijkste metaal 3D-printtechnologieën die geschikt zijn voor productie. Dit wordt mogelijk gemaakt door de unieke mogelijkheden van de technologie om hoge printsnelheden te bereiken en zeer nauwkeurige componenten te maken.
Een andere belangrijke ontwikkeling die het succes van het spuiten van metaalbindmiddelen stimuleert, is de compatibiliteit met reeds bekende en relatief goedkope MIM-poeders.
Een aantal bedrijven heeft het doorbraakpotentieel van metaalbinderstralen erkend en werkt nu hard om de kansen die het biedt te grijpen.
In de toekomst zullen we zien dat deze bedrijven het stralen van metalen bindmiddelen nog verder ontwikkelen. Uiteindelijk zal dit de technologie helpen om een waardevol deel van de totale productiemarkt te veroveren.
>>Lees meer over metaal 3D-printen in onze Definitive Metal 3D Printing Guide.
3d printen
- Alles wat u moet weten over vuurvaste metalen
- PLA 3D-printen:alles wat u moet weten
- Nylon 3D-printen:alles wat u moet weten
- Alles wat u moet weten over draadvonkbewerking
- Alles wat u moet weten over metaalgieten
- Alles wat u moet weten over een vijfassige freesmachine
- Alles wat u moet weten over de cilindrische slijpmachine
- Alles wat u moet weten over spoel snijlijn
- Alles wat u moet weten over Flash Welder
- Alles wat u moet weten over het rolproces
- Alles wat u moet weten over industriële metaalafwerkingsprocessen