Interview met expert:Joachim Zettler, CEO van APWORKS, over het vinden van de juiste businesscase voor 3D-metaalprinten
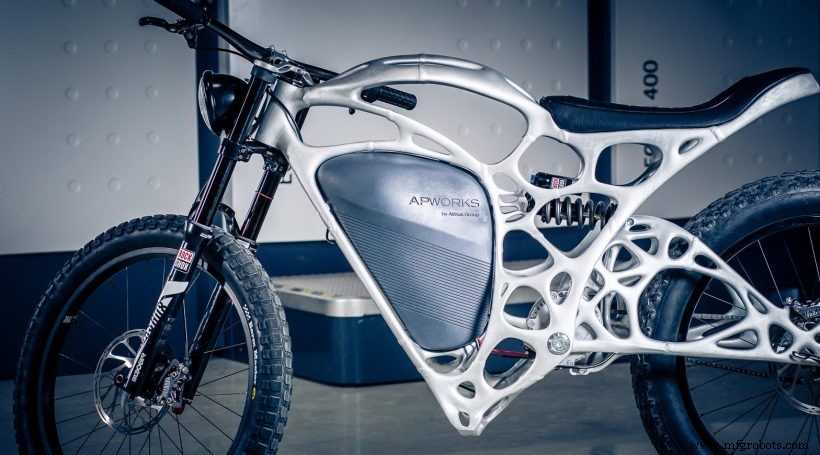
Als je nog nooit van APWORKS hebt gehoord, heb je waarschijnlijk wel gehoord van de Light Rider:'s werelds eerste ooit 3D-geprinte motorfiets. De elektrische motorfiets werd in 2016 onthuld door APWORKS en wordt geprezen om zijn lichtgewicht ontwerp, verbeterde prestaties en complexe geometrieën - een lichtend voorbeeld van wat kan worden bereikt met additieve fabricage.
Opgericht in 2013 als een spin-off van Airbus, is APWORKS een toonaangevende leverancier van metaaladditieve productieoplossingen. Het bedrijf bestrijkt het volledige spectrum van metaal AM, inclusief onderdeeloptimalisatie en gekwalificeerde serieproductie. Het bedrijf heeft ook zijn eigen zeer sterke aluminiumlegering, Scalmalloy®, ontwikkeld en gepatenteerd, die werd gebruikt voor het Light Rider-project.
Onlangs overgenomen door Premium AEROTEC, een eersteklas leverancier van metalen onderdelen voor Airbus-vliegtuigen (en een dochteronderneming van Airbus op zich), bedient APWORKS een breed klantenbestand dat voornamelijk de lucht- en ruimtevaart omvat, en robotica-industrieën.
Deze week spreken we met de CEO van APWORKS, Joachim Zettler, om te bespreken waarom bedrijven de juiste businesscase voor AM moeten vinden, waarom de technologie perfect is voor de auto-industrie en wat de toekomst in petto heeft voor de industrie als geheel.
Kun je me iets vertellen over APWORKS en je missie als bedrijf?
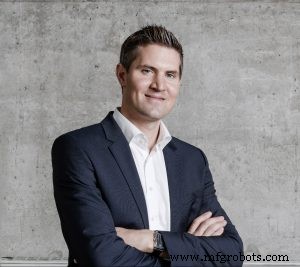
APWORKS werd in 2013 opgericht als een dochteronderneming van Airbus.
Vorig jaar zijn we overgenomen door Premium AEROTEC, een leverancier van lucht- en ruimtevaartfabricage. Premium AEROTEC is een eersteklas leverancier van Airbus en is een van de grootste lucht- en ruimtevaartfabrikanten ter wereld.
Premium AEROTEC heeft een sterke focus op additieve fabricage en dus was de stap vrij natuurlijk. En hoewel dit intern niets verandert voor APWORKS, hebben we nu een meer productiegerichte aandeelhouder in Premium AEROTEC.
Voor APWORKS is onze missie nog steeds dezelfde:we willen een totaalaanbieder zijn van additief vervaardigde industriële componenten voor onze klanten - en niet alleen van gereguleerde industrieën. Automotive is ook een vrij groot klantenbestand dat we bijvoorbeeld bedienen.
We zien onze rol ook als het opleiden van onze klanten, aangezien we klanten hebben die bij ons komen zonder enige voorkennis of ervaring met additive manufacturing.
Aan de andere kant, met de klanten die al een bepaalde kennis over additieven hebben, zorgen we ervoor dat we hen kunnen helpen bij het ontwikkelen van toepassingen die logisch zijn met de technologie.
Dit omvat het helpen bij het herontwerpen en optimaliseren van componenten en het daadwerkelijk produceren van onderdelen met additive manufacturing.
De omvang van de projecten waaraan we werken varieert enorm, van productie in kleine series tot projecten binnen de optiekbranche waar we circa 20.000 stuks per jaar produceren.
Dat is een ander deel van onze missie:een businesscase voor additieven in verschillende sectoren tot stand brengen en een voorkeurspartner worden voor onze klanten.
U noemde de automobielindustrie een belangrijke industrie voor APWORKS. Op welke manieren kan de auto-industrie profiteren van additive manufacturing?
Als we kijken naar motorsport of zelfs luxe voertuigen zoals Bugatti of Ferrari, dan zijn autobedrijven in deze sector doorgaans geïnteresseerd in het verkorten van de doorlooptijden, hetzij tijdens de productontwikkelingsfase, hetzij in een scenario met reserveonderdelen zoals de Formule 1, waar ze hoge kosten moeten maken. hoogwaardige functionele onderdelen vrij snel.
Naast de doorlooptijden, zou ik ook zeggen dat de kosten een ander probleem zijn voor de sector.
Met dit in gedachten is de vraag hoe je ervoor kunt zorgen dat zowel doorlooptijden als kosten worden verminderd met additief? Dit is belangrijk, zeker in vergelijking met traditionele manieren van produceren.
Deelconsolidatie is hier een belangrijk onderdeel van. Dit kan bijvoorbeeld betekenen dat u een onderdeel dat voorheen uit 10 afzonderlijke componenten bestond, in één keer kunt printen. Dit is geweldig, want het leidt tot minder kwaliteitscontroles en, natuurlijk, minder montagetijd.
Tegelijkertijd moeten we, als we een onderdeel voor additieven ontwerpen, ervoor zorgen dat deze componenten geoptimaliseerd. Deze optimalisatie leidt meestal tot betere prestaties en deze verbeterde prestaties zijn meestal een geweldige businesscase voor onze klanten.
Dat is ook waar de motorsport voortdurend naar kijkt:het verkorten van doorlooptijden is zeker nog steeds de belangrijkste drijfveer, maar dit wordt langzaamaan vervangen door meer prestatiegerichte problemen. Verrassend genoeg is gewichtsbesparing doorgaans geen drijvende factor bij het herontwerpen van componenten voor autobedrijven.
Vindt u dat bedrijven die op zoek zijn naar uw diensten al een goed begrip hebben van AM, of bevinden ze zich nog in de beginfase om te begrijpen wat er met de technologie kan worden gedaan?
De branche is de afgelopen jaren echt veranderd.
Toen we in 2013 met APWORKS begonnen, hadden de meeste van onze klanten heel weinig kennis over wat de technologie kan doen.
Interessant is dat, hoewel we nog steeds een aantal klanten hebben met weinig kennis van AM, we een groeiend aantal klanten hebben die zich bewust zijn van de voordelen van de technologie en wat ermee kan worden gedaan. Dit is geweldig omdat deze klanten echt begrijpen waar de businesscase ligt - en hoe ze het meeste uit additive manufacturing kunnen halen.
Voor onze klanten die meer informatie over additieven nodig hebben, kan dit een tijdrovend proces zijn. Ze moeten terug naar hun bedrijven, het idee van additief verspreiden en proberen een geschikt pad te onderzoeken dat zinvol is voor additief. Natuurlijk ondersteunen we onze klanten op die reis.
Als ik er een cijfer op moet plakken, zou ik zeggen dat ongeveer 60% van onze klanten zeer veel kennis heeft van AM. De overige 40% heeft nog behoorlijk wat scholing nodig.
U noemde het belang van een businesscase voor AM. Op welke manieren kunnen bedrijven de juiste toepassingen voor AM identificeren?
Er is geen antwoord op deze vraag; het is erg afhankelijk van de branche en de specifieke toepassing.
Bij onze klanten hebben we de neiging om vanaf nul te beginnen, met een greenfield-aanpak als het ware. We willen dus niet weten hoe het onderdeel er vroeger uitzag of welke productiemethode werd gebruikt. In plaats daarvan verzamelen we randvoorwaarden om te proberen een nieuwe multifysica te bedenken, geoptimaliseerd ontwerp met verbeterde prestaties - dat alleen kan worden bereikt met 3D-printen.
Onze klanten willen doorgaans dat we de doorlooptijden verkorten en materiaalbesparingen realiseren. Met deze informatie, wetende wat een klant wil, kunnen we eenvoudig vaststellen of er een business case te halen is. Vervolgens beperken we onze onderdeelselectietrechter om de onderdelen te selecteren die zinvol zijn om nader te bekijken. Afhankelijk van deze input en de verschillende wensen en eisen van de klant komen we meestal met een business case.
Er is al veel gezegd over de noodzaak van een andere ontwerpaanpak als het gaat om AM. Hoe gaat APWORKS om met de uitdaging van ontwerpen voor additive manufacturing?
Ten eerste proberen we ingenieurs te krijgen die goed zijn in ten minste één discipline van de additieve omgeving, of dat nu binnen ontwerp of productie is.
We geven ook prioriteit aan training. We bieden veel training on the job, waarbij we ervoor zorgen dat we ontwerpmogelijkheden combineren met de proceskennis die je nodig hebt om dienovereenkomstig te ontwerpen.
Dus het is nogal de opzet die we bij APWORKS hebben:onze medewerkers zijn niet alleen goed in ontwerpen, maar ze hebben ook min of meer een productie-achtergrond. Wat we ook ontwerpen, we kunnen het ook produceren.
Een uitdaging waarmee veel van onze klanten worden geconfronteerd, is dat hun ingenieurs vaak niet weten hoe ze moeten ontwerpen voor additieven. Daarom proberen we de kennis die we hebben ook over te dragen aan onze klanten.
Voor ons is deze aanpak logisch, want als je deze kennis eenmaal hebt overgedragen, zullen bedrijven meestal bij je terugkomen omdat ze meer kennis hebben en zijn in staat om sneller te bewegen.
We zien dit als een kans voor APWORKS, want zelfs op universiteiten, althans in Duitsland, wordt ontwerp voor AM nog steeds niet echt algemeen onderwezen, althans niet voor zover ik weet.
Vorig jaar onthulde APWORKS zijn zeer sterke metaalpoeder, Scalmalloy®. Wat zijn enkele voordelen van het materiaal - en heeft u plannen voor verdere materiaalontwikkeling in de toekomst?
Het unieke verkoopargument van Scalmalloy® is dat het een hoge sterkte combineert met een hoge mate van vervormbaarheid. Meestal hebt u ofwel een bros materiaal dat erg sterk is of een erg ductiel materiaal dat relatief zwak is. Scalmalloy® combineert het beste van twee werelden.
We krijgen wel eens de vraag van klanten of we materialen op maat kunnen ontwikkelen. Met Scalmalloy® hadden we het geluk dat dit materiaal precies de materiaaleigenschappen onthult die we van een zeer sterke aluminiumlegering verwachtten.
We besteden echter meestal niet veel aandacht aan het helemaal opnieuw ontwikkelen van nieuwe materialen. In plaats daarvan nemen we bestaande materialen, zoals Ti6Al4V, AlSi10Mg en 316L, en gebruiken we de procesparameters van ons systeem om het materiaal af te stemmen op een specifieke gebruikssituatie.
Dit is veel effectiever dan steeds volledig nieuwe materialen te moeten ontwikkelen. We waren bijvoorbeeld in staat om een procesparameter te ontwikkelen die is geoptimaliseerd voor Ti64 om de uiteindelijke treksterkte met bijna 30% te verhogen, terwijl tegelijkertijd dezelfde rek bij breuk behouden blijft. Dit werd eenvoudig bereikt door de procesparameters dienovereenkomstig te variëren.
De manier waarop we materiaalontwikkeling benaderen is als volgt:een klant benadert ons met een bepaald probleem en we proberen de juiste ontwerpaanpak te vinden om het probleem aan te pakken. Die ontwerpaanpak is meestal gerelateerd aan het materiaal. Dus zelfs als we een vrij standaard materiaal zoals Ti64 gebruiken, kunnen we nog steeds experimenteren met de procesparameters om meer uit het materiaal te halen.
Op softwaregebied heeft APWORKS zijn AMXpert-software ontwikkeld. Kun je me meer vertellen over de software en waarom je deze hebt ontwikkeld?
De software die we gebruiken heeft twee hoofddoelen. De eerste is om klanten een manier te bieden om snel aanbiedingen en offertes in ons systeem te krijgen.
U kunt de geometrie uploaden, het gewenste materiaal selecteren en u krijgt een offerte, of u kunt het zelfs direct bestellen. Het is dus een verwerkingssysteem.
Ten tweede kunnen klanten de software gebruiken om hun onderdelenportefeuilles te screenen. U kunt eenvoudig honderdduizenden onderdelen en geometrieën uploaden. Het systeem is gekoppeld aan onze interne kennisdatabase, waar alle opdrachten die we in de afgelopen vijf jaar hebben afgedrukt, worden opgeslagen.
Deze database bevat analyses van alle opdrachten die we in het verleden hebben uitgevoerd, inclusief wat er in het verleden mislukte, welke combinatie van materiaal en ontwerp zinvol is, minimale wanddikte enzovoort. In wezen komt het met al deze lessen die we hebben geleerd in de jaren dat we AM gebruiken.
We staan onze klanten toe om AMXpert gratis te gebruiken, omdat we klanten willen informeren over hun onderdeelselectieproces, zodat ze gemakkelijk de onderdelen kunnen identificeren die zinvol zijn om met additief te produceren.
Zijn er succesverhalen die u kunt delen?
Helaas is veel van het werk dat we doen vertrouwelijk.
We hebben echter veel werk verzet binnen de mode-industrie. We hebben ook onderdelen geproduceerd voor verschillende Formule 1-teams, voornamelijk in prototyping, evenals onderdelen voor de robotica-industrie. Tooling voor automotive is een andere populaire toepassing.
Misschien is ons meest gepubliceerde project tot nu toe onze Light Rider-fiets die we in 2016 hebben ontwikkeld. De Light Rider is 's werelds eerste 3D-geprinte motorfiets en maakt gebruik van ons Scalmalloy®-metaal. Het is een lichtgewicht elektrische motorfiets en 30% lichter dan traditioneel gemaakte elektrische motorfietsen.
In eerste instantie wilden we een interessante etalage zijn, maar we hebben nu veel klanten die de motor willen kopen! De vraag voor ons is, zoals altijd, het vinden van de businesscase om de fiets commercieel te verkopen, vooral omdat het vrij duur is om te produceren.
Maar wie weet, misschien zie je over een paar jaar de Light Rider op straat.
Kwesties rond certificering en kwaliteit van onderdelen zijn twee belangrijke gespreksonderwerpen in de branche. Zijn dit uitdagingen die je ook bent tegengekomen bij APWORKS?
Ik denk dat de industrie nog steeds bezig is deze dingen uit te zoeken. Het kunnen voldoen aan bepaalde kwalificatiecriteria is vooral belangrijk als u additieven wilt gebruiken in sterk gereguleerde markten zoals de ruimtevaart.
Grote OEM's hebben allemaal bepaalde kwaliteitscriteria en daar moet u als leverancier aan voldoen.
Soms zijn deze eisen afkomstig van bestaande technologieën zoals smeden, gieten en verspanen , maar worden gewoon toegepast op AM zonder zelfs maar te denken dat dit waarschijnlijk een heel andere manier van produceren is. Dit maakt het af en toe best uitdagend.
Als je onderdelen hebt die vandaag en morgen worden gesmeed en je wilt ze printen, dan moet je natuurlijk aan dezelfde materiaaleigenschapscriteria voldoen met je 3D-geprinte onderdeel, wat bijna onmogelijk is.
Maar met de juiste aanpak en bepaalde kwaliteitskennis kan het.
En na verloop van tijd zullen we zien dat er meer normen worden ontwikkeld voor AM. Een van de uitdagingen op dit moment is dat er simpelweg nog niet genoeg regels zijn voor AM. De industrie probeert bijvoorbeeld productieprocessen te standaardiseren en hoe verschillende productiemethoden zouden moeten werken. Dit omvat niet alleen hoe de machines werken, maar ook poederkarakterisering, hoe de nabewerkingsketen eruit moet zien, welke training de machinebedieners moeten hebben, enzovoort.
Voor degenen die nog niet bekend zijn met 3D-printen met metaal, hoe kunnen ze er zeker van zijn welke technologie ze moeten overwegen voor een specifieke toepassing?
Voor bedrijven is dit vaak een complex vraagstuk.
Als klein of middelgroot bedrijf dat nog niet bekend is met additieven, kunt u het net als de meeste andere bedrijven doen — een printer kopen en misschien een adviesbureau inhuren om u te helpen de juiste onderdelen en de juiste juiste beslissingen.
Maar deze aanpak kan vaak een verspilling van tijd en geld zijn, omdat bedrijven niet eerst een businesscase voor AM hebben ontwikkeld. We hebben dit keer op keer gezien, waarbij bedrijven alleen in 3D-printers hebben geïnvesteerd om te ontdekken dat ze geen businesscase hebben, hun machines niet belasten - en uiteindelijk bitter teleurgesteld worden.
Dus voordat ik geld uitgeef of in machines investeert, raad ik bedrijven aan eerst met anderen te praten die met succes 3D-printen hebben gebruikt om winst te maken. Leer van degenen die al in het gebied zijn geslaagd en zeer goed geïnformeerd zijn over AM.
Hoe ziet u de AM-industrie de komende vijf jaar evolueren?
De industrie evolueert meer en meer en evolueert naar industrialisatie.
Terwijl de industrie industrialiseert, rijst de vraag hoe nu geld te verdienen met de technologie. Het gaat niet meer om R&D; het gaat om het maken van een businesscase met de technologie.
Terwijl we zien dat steeds meer klanten kennis van AM krijgen, zijn we er sterk van overtuigd dat de industrie op weg is naar serieproductie. Sterker nog, dat is wat we dagelijks doen.
Bovendien wordt er meer onderwijs gegeven door universiteiten en bedrijven zoals APWORKS, en we zien steeds meer toepassingen opkomen die vanuit zakelijk oogpunt gewoon logisch zijn.
Wat hierbij helpt, is het feit dat de machines jaar na jaar verbeteren. Hoe efficiënter en productiever de machines, hoe makkelijker het is om een businesscase voor uw toepassing te realiseren.
Dat gezegd hebbende, additief zal altijd een productiemethode zijn voor nichetoepassingen. Ik geloof niet dat het ooit verspanen of zelfs gieten zal vervangen.
Maar als je me deze vraag over vijf jaar opnieuw zou stellen, zou ik zeggen dat we niet alleen veel meer toepassingen hebben voor additief, maar het is echt een genormaliseerde productiemethode geworden, zoals gieten of machinaal bewerken.
Ten slotte, wat houdt de rest van 2019 in voor APWORKS?
Tot nu toe hebben we ons toegewijd aan het opleiden van ons klantenbestand en het helpen van hen bij het produceren en ontwerpen van geoptimaliseerde onderdelen en producten met additive manufacturing. Dit zal niet veranderen.
Maar wat is veranderd, is dat we als bedrijf meer productgedreven worden. Naast het productiewerk dat we voor onze klanten doen, willen we ons ook richten op het uitbrengen van ons eerste product. Details zijn nog steeds vertrouwelijk, maar we zijn momenteel bezig met het ontwikkelen van een nieuw product dat AM op de best mogelijke manier gebruikt.
We zijn ook gericht op uitbreiding. Op dit moment opereert APWORKS voornamelijk vanuit Europa, maar we willen als bedrijf snel opschalen. Om dit te bereiken, streven we ernaar om dit jaar onze aanwezigheid in de VS te vergroten, om onze klanten ter plaatse ondersteuning te bieden.
Ga voor meer informatie over APWORKS naar: https://apworks.de/
Expertinterviews
AMFG's Expert Interviews-serie toont innovatieve bedrijven en individuen die helpen de toekomst van additive manufacturing vorm te geven. Neem voor meer informatie over deelname aan de serie contact op met marketing@amfg.ai.
3d printen
- Scalmalloy:het nieuwste hoogwaardige materiaal voor 3D-metaalprinten
- Interview met expert:Duncan McCallum, CEO van Digital Alloys over Joule Printing en de toekomst van Metal 3D Printing
- Expertinterview:Nanoe CEO Guillaume de Calan over de toekomst van keramisch 3D-printen
- Expert Interview:Ultimaker President John Kawola over de toekomst van 3D-printen
- Hoe Ford Motor Company 3D-printen voor de auto-industrie innoveert:interview met experts van Harold Sears
- Interview met expert:Simon Fried, medeoprichter van Nano Dimension over de opkomst van 3D-printen voor elektronica
- Interview met expert:CEO van PostProcess Technologies over het oplossen van het knelpunt in de nabewerking voor additieve productie
- Interview met expert:AMendate over zijn geautomatiseerde topologie-optimalisatiesoftware voor 3D-printen
- Interview met expert:Nanci Hardwick, CEO van MELD Manufacturing, over het benutten van het potentieel van de productie van metaaladditieven
- De juiste tools vinden voor prototyping met een beperkt budget
- De zaak voor 3D-printen in de productie