Arevo in 2018:geïndustrialiseerde productie van 3D-geprinte onderdelen met continue vezels
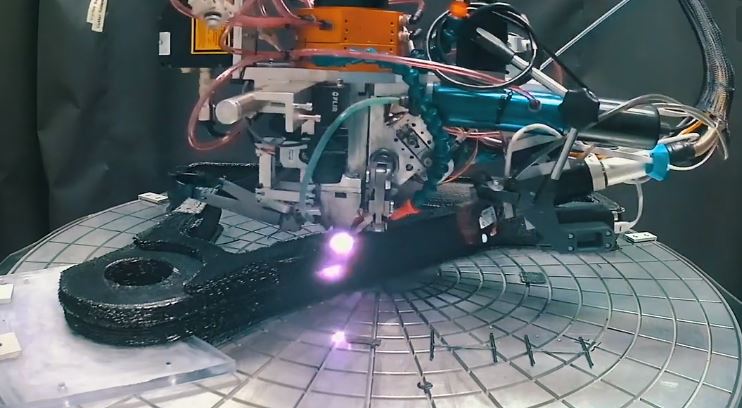
CW is sinds 2014 actief in Arevo (Santa Clara, CA, VS). Bekend om zijn gebruik van hoogwaardige thermoplastische polymeren, waaronder polyetheretherketon (PEEK), polyaryletherketon (PAEK), polyetherimide (PEI) en polyfenyleensulfide (PPS), was het bedrijf ook een leider in de ontwikkeling van closed-loop robotbesturing voor 3D-printen , waardoor plaatsing van glasvezel in de z-richting . mogelijk wordt en langs 3D-curven. Het bedrijf heeft een lijst met nieuwe ontwikkelingen, waaronder het directe energiedepositieproces (DED) met behulp van laserverwarming voor een 100-voudige verhoging van de productiesnelheid.
Nieuwe CEO en B-serie financiering
Jim Miller trad drie maanden geleden in dienst bij Arevo als CEO. Hij was een vroege Amazon-medewerker en werkte acht jaar bij Google, meest recentelijk als VP van wereldwijde activiteiten. "Ik heb eigenlijk het grootste deel van mijn carrière besteed aan het helpen van jonge bedrijven", zegt Miller. toepassingen.”
Het bedrijf heeft zojuist ook zijn Series B-financiering afgerond en heeft $ 12,5 miljoen opgehaald met Asahi Glass Co. (AGC, Tokyo, Japan) als leider in de ronde. "Ze zijn 's werelds grootste autoglasproducent", zegt Miller. “Ze hebben goede relaties in de auto-industrie en zien grote kansen voor nieuwe composiettechnologieën in de auto-applicaties .” Andere investeerders zijn In-Q-Tel (Arlington, VA, VS), Sumitomo Corporation (Tokyo, Japan) en Leslie Ventures. Miller zegt dat Sumitomo , een van de grootste Japanse conglomeraten en een leider in olie- en gastechnologieën, is geïnteresseerd in het toepassen van Arevo's 3D-printtechnologie in al zijn industriële activiteiten , waaronder bouw, transport, infrastructuur en energie.
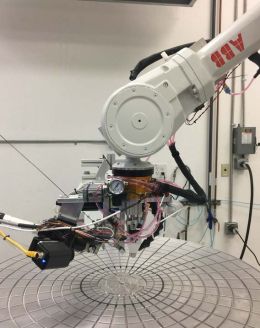
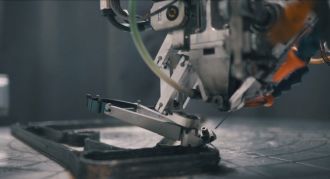
Arevo's productiecellen voor directe energiedepositie (DED) bestaan uit een industriële robot, een printkop met laserverwarming en een roterend bouwplatform. De printkop (rechts te zien tijdens automatisch snijden en herstarten) omvat apparatuur voor thermisch beheer en vision-systemen voor inspectie ter plaatse. BRON:Arevo.
Industriële productie van thermoplastische composieten
“Onze nieuwe productiecellen gebruiken een standaard industriële robot , een roterend bouwplatform en een laser voor verwarming ’, legt Molenaar uit. “We noemen het proces directe energiedepositie (DED).” In de laserveilige productiecel heeft de robot een printkop-eindeffector met eigen thermisch beheer apparatuur, op maat gemaakte elektronica en visiesystemen die inspectie ter plaatse . mogelijk maken . "Het proces is meestal hands-off/lights-out", zegt Miller. "Deze nieuwe cellen produceren een meer dan 100-voudige toename van de productiesnelheid." Chief Technical Office Wiener Mondesir vult aan:“De laser levert onbeperkte energie. We kunnen dat beheersen en sneller gaan om industriële productiesnelheden te bereiken." Maar Miller merkt op:"Het gaat er niet om hoe snel machines kunnen bewegen of hoeveel materiaal kan worden toegepast, want we bouwen complexe structurele composieten tegen een vierde van de kosten van traditionele composieten.”
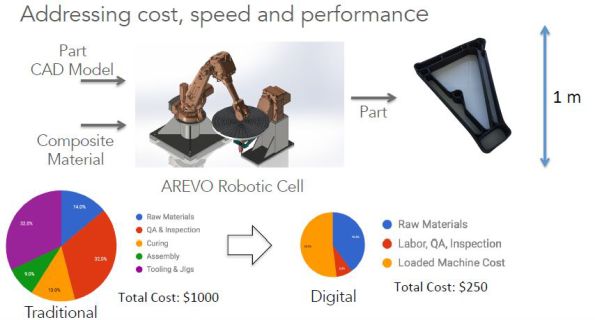
Niet-traditionele composietproductie — Het DED-proces van Arevo maakt naar verluidt de productie mogelijk van continue vezelversterkte thermoplastische composietonderdelen tegen ¼ de kosten van traditionele composieten. (Berekeningen gebaseerd op een stuk van 1 m.)
"We streven naar economisch haalbare fabricage van grootschalige thermoplastische composietonderdelen ’, zegt Molenaar. "We benaderen deze productie vanuit een niet-traditioneel composietperspectief." De printkop integreert echter wel verdichtingscapaciteit en de onderdelen voldoen nog steeds aan de traditionele kwaliteitseisen voor composieten. "We kunnen onderdelen van thermoplastisch composiet bereiken met een inhoud van veel minder dan 1% ', bevestigt Miller. "Arevo blijft zijn proces verbeteren en zal in de nabije toekomst voldoen aan mechanische eigenschappen voor primaire structuurvereisten."
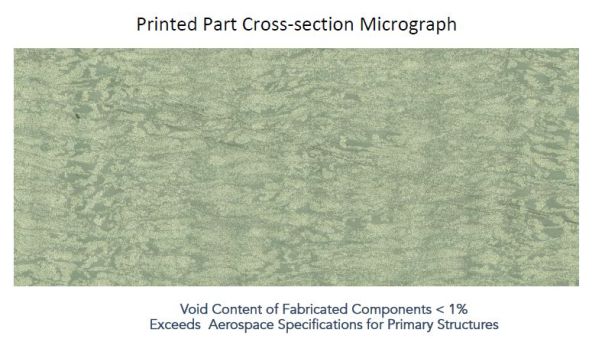
Pathfinder-software
Een deel van het "niet-traditionele composietperspectief" waarnaar Miller hierboven verwijst, is Arevo's investering in digitale ontwerp- en processoftware. "We hebben een hele workflow samengevouwen in de software”, zegt Miller. "Het kan een volledige 3D-analyse van het onderdeel bieden en de geoptimaliseerde vezeloriëntatie ontwikkelen met behulp van Additive FEA (AFEA)-modules. Een groot deel van ons succes wordt gedreven door de software en simulatie van de productie van onderdelen. We voeren het door de computer gegenereerde ontwerp uit via onze processimulatiesoftware en het toont de procesparameters, waaronder temperaturen, afdrukpad, kromtrekken en krimp van het gedrukte materiaal , evenals restspanningen. Dit stelt ons in staat om het proces echt te begrijpen en te optimaliseren om onderdelen van zeer hoge kwaliteit te produceren.”
Hij zegt dat de getuigenis van Arevo's software is dat de eigenschappen van gefabriceerde onderdelen binnen 5% van de gesimuleerde eigenschappen liggen, wat volgens Miller in feite neerkomt op het niveau van de foutmarge van de testmeting. Hij voegt eraan toe dat Arevo ook gebruikmaakt vanmachine learning op een unieke manier.
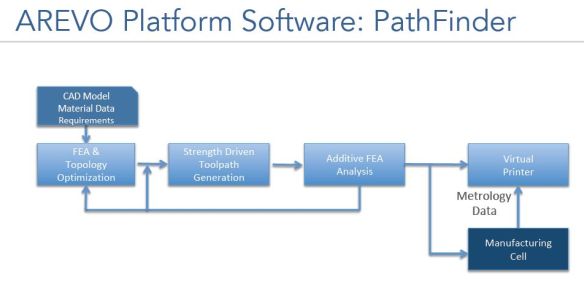
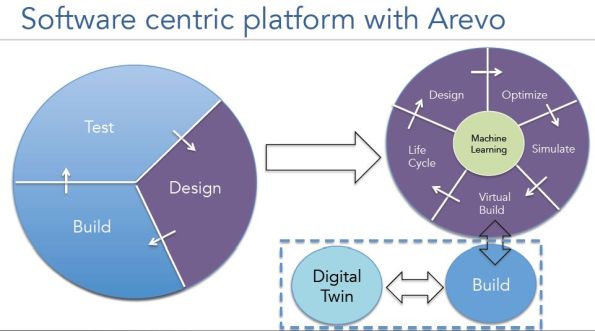
De mogelijkheden demonstreren
Nog maar een maand geleden toonde Arevo wat volgens haar de eerste 3D-geprinte fiets ter wereld is op het Sea Otter-evenement (19-22 april, Monterey, CA, VS). "Ons doel was om te demonstreren wat onze software en ons proces kunnen bereiken", legt Miller uit. "We werkten samen met het in Colorado gevestigde industriële ontwerpbureau Studio West om het ontwerp van het cantileverfietsframe te ontwikkelen .” Hij merkt op dat Studio West goed bekend is in de fietsindustrie en samenwerkt met enkele van de beste fabrikanten. "Ze gaven ons aanvankelijk een heel traditioneel frameontwerp", zegt Miller. “Maar we wilden laten zien hoe Arevo continue vezels op nieuwe manieren kan toepassen , dus we bleven met hen samenwerken door middel van verschillende iteraties.” Hij voegt eraan toe dat het Arevo-team de stijfheid en buiging van het fietsframe wilde optimaliseren, maar ook de nieuwe esthetiek wilde demonstreren die mogelijk is met zijn additieve fabricagetechnologie. "We kregen een heel uniek fietsontwerp", zegt Miller. Het fietsframe is gemaakt met continue 12K CF-sleepkabel en PEEK maar Miller zegt dat het ook mogelijk is om nylon te gebruiken.
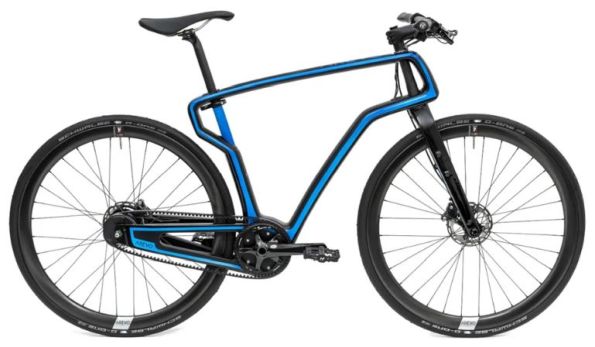
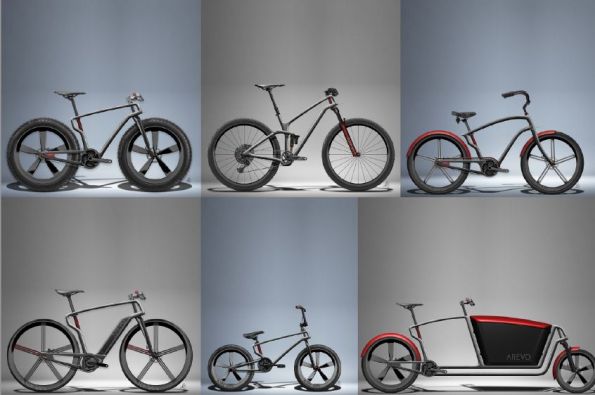
Arevo's 3D-geprinte CF composiet fietsframe kan gemakkelijk worden aangepast om te voldoen aan een breed scala aan producten voor de fietsmarkt, waaronder e-bikes, bakfietsen, ligfietsen, 3-wielen, kinderfietsen, dikke fietsen, BMX, cruisers en meer. BRON:Arevo.
Fietsframes zijn niet het enige voorbeeld van wat Arevo bereikt op het gebied van additieve fabricage van composieten. "Kleine robotica-bedrijven bouwen grote robots dat we helpen licht te worden tegen een fractie van de kosten van traditionele materialen”, zegt Mondesir. Arevo belicht ook waaier- en propellertoepassingen , waar gerapporteerde voordelen zijn:
- On-demand productie om voorraadkosten te beheren
- Hoger rendement versus metalen constructie
- Belastbaar met serviceomgeving
- Complexe geometrieën zijn niet mogelijk met legacy-productie.
Pad naar industriële productie
Miller zegt dat het eerste doel voor 2018 is om acht DED-productiecellen te installeren en capaciteit uit te bouwen om de achterstand op het gebied van productieonderdelen aan te pakken. . "We zullen dit jaar beginnen met het verzenden van producten in grote hoeveelheden", bevestigt hij. Het bedrijf werkt ook samen met strategische klanten aan belangrijke toepassingen en productontwikkeling. "Onze derde belangrijke focus is om door te gaan met het verfijnen van het depositieproces om snelheid te verhogen met behoud van kwaliteit en opbrengst”, zegt Miller. “We zullen ook onderdelen demonstreren met verschillende vezels en sleepmaten .” Hij zegt dat het DED-proces variabele sleepvorm en -diameter aankan, tot 24K sleep. "We kunnen printen met PEKK, PAEK, PPS en ook met glas en aramide continue vezels", voegt Miller toe.
Hoe zit het met printen met draad en glasvezel voor multifunctionele composietstructuren ? "Dat zou in wezen gewoon een andere vezel voor ons zijn", zegt Miller. Demonstraties van deze mogelijkheid zijn tot nu toe in het laboratorium geweest. "We kijken naar intellectueel eigendom en hebben lopende R&D op dit gebied", voegt hij eraan toe.
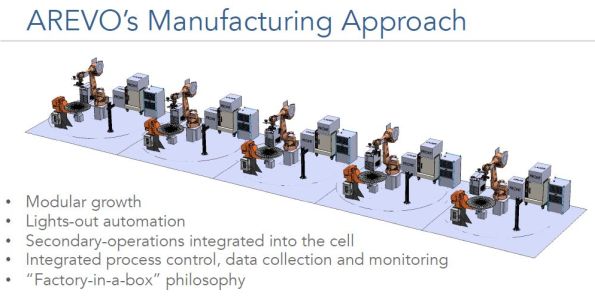
“Niets belet ons om meerdere slepen en/of banden te gebruiken ', stelt Molenaar. “En er is echt geen limiet tot welk formaat we kunnen printen. We maken een onderdeel van 2,5 m x 1,5 m voor een ruimtevaartbedrijf en kijken ook naar het samen gebruiken van meerdere robots . Het bedrijf heeft zijn DED-productiecellen ontwikkeld om modulair te zijn, zodat secundaire bewerkingen kunnen worden geïntegreerd, zoals afwerking, om hoogwaardige oppervlakken te produceren.
We kunnen onze printkoppen ook op industriële robots plaatsen, zodat onze technologie geïntegreerd kan worden in een bestaand proces of geheel nieuwe processen.” Hij wijst erop dat Arevo “niet in de printerbusiness zit, maar dit aanpassingsvermogen biedt kansen. Het bedrijf heeft 55 patenten uitgegeven, in behandeling of aanvragen in behandeling.
Hoe zit het met generatief ontwerp? Ziet Arevo zichzelf als een speler die deze nieuwe benadering van ontwerp en fabricage helpt realiseren? "Generatief ontwerp is heel anders dan wat we doen, omdat het kan eindigen met ontwerpen die moeilijk te produceren zijn, wat de kosten opdrijft", reageert Miller. “Onze aanpak is om optimalisatie voor productie op te nemen vooraan.”
Hars
- Koolstofvezelproductie en koolstofvezelonderdelen:wat zijn de basisprincipes?
- Aluminium onderdelen vervangen door 3D-geprinte koolstofvezel
- 2018:An IMTS Odyssey
- AON3D, Astrobotic om 3D-geprinte onderdelen naar de maan te sturen
- De kosten van 3D-printmaterialen met continue vezels verlagen
- Mafic USA verwacht de Amerikaanse basaltvezelproductiecapaciteit te verdubbelen
- Alltec breidt uit op Noord-Amerikaanse markt
- Covestro lanceert Maezio thermoplasten met continue vezels
- Continuous Fiber Manufacturing (CFM) met moi-composieten
- 3D-print composieten met continue vezels
- Software verbetert de nauwkeurigheid van 3D-geprinte onderdelen