Koolstofvezel maakt eVTOL's voor luchttaxi's mogelijk
Deze blog is een reactie op een artikel van januari 2019 in WIRED magazine, dat beweert dat de productie van koolstofvezelcomposiet de ontwikkeling van elektrische voertuigen (EV)/verticale start- en landingsvliegtuigen (VTOL) voor de stedelijke mobiliteit en luchttaximarkt tegenhoudt. Ik ga hier over discussiëren, maar bied ook een aantal potentieel ontwrichtende nieuwe technologie aan, dus lees door tot het einde.
Hoewel ik de auteur toejuich omdat hij verslag doet van deze snel opkomende industrie en voor het wijzen op de noodzaak om te ontwerpen met de maakbaarheid in gedachten, is hij soms misleidend, hoogstwaarschijnlijk omdat hij niet erg goed op de hoogte is van de composietenindustrie. Bijvoorbeeld:
Hoewel dat technisch waar is, gaat Airbus tegen medio 2019 naar 60 A320-vliegtuigen/maand en Boeing is op weg naar 57 vliegtuigen/maand voor de B737, ook in 2019. Voor de A320 betekent dit de productie van drie 6,3 meter hoge met koolstofvezel versterkte kunststof (CFRP) verticale staartvlakmontages per dag en ook drie 12,45-m-overspanningen CFRP horizontale staartvlakassemblages per dag .
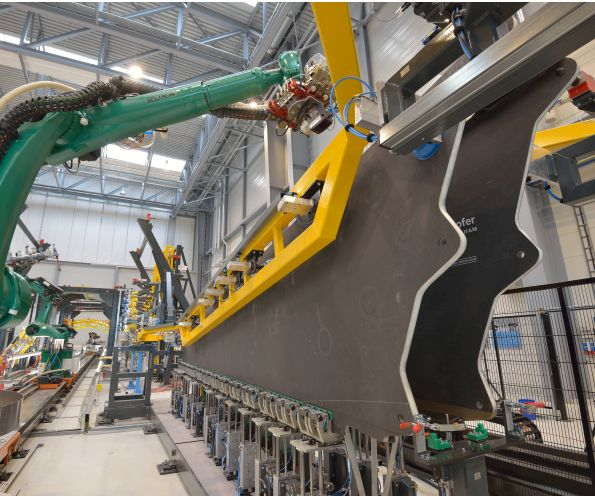
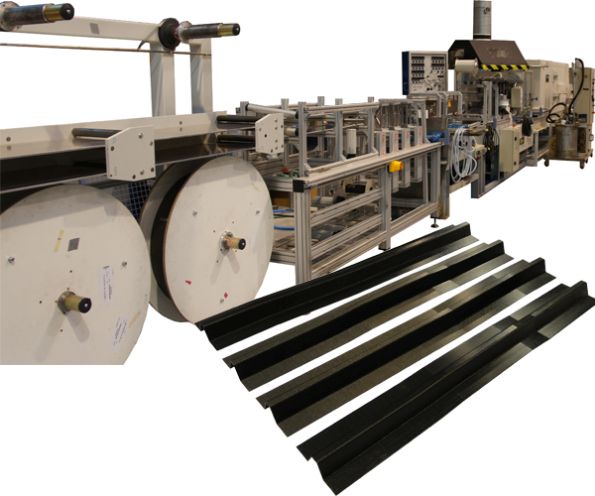
Ook heeft Airbus de ene technologie na de andere gekwalificeerd - veel met behulp van composieten en allemaal gericht op 60-70 vliegtuigen per maand - voor de volgende iteratie van de A320, de A320 Neo Plus genoemd. Deze composiettechnologieën omvatten een portfolio met harstransfervormen (RTM), compressievormen van plaatvormmassa (SMC) en thermoplastische composieten (TPC's) die cyclustijden hebben die gemakkelijk meer dan 700 vliegtuigen per jaar kunnen produceren. Enkele van de nieuwste technologieën in ontwikkeling verminderen de cyclustijden van CFRP-onderdelen van 4 uur tot 15 minuten of minder. De meeste nieuwe technologieën die Airbus heeft gekwalificeerd, zijn sterk geautomatiseerd, net als de nieuwe assemblagemethoden.
De auto-industrie heeft ook de weg vrijgemaakt voor een hogere massaproductie dan eVTOL's nodig hebben (WIRED genoemde verwachte vraag van 23.000 voertuigen tegen 2035). BMW verhoogt de productie van zijn i3 en i8 modellen - beide zijn voorzien van volledig CFRP-passagierscellen - van 130 tot 200 eenheden/dag en Audi-leverancier Voith Composites produceert de CFRP-achterwand voor de A8 met een snelheid van 150-300 eenheden/dag . Merk op dat de BMW i3 en i8 modules lijken erg op het hieronder getoonde casco voor de Airbus Helicopters EC 135 - beide fabrikanten bevestigen vervolgens externe en interne componenten aan dit frame.
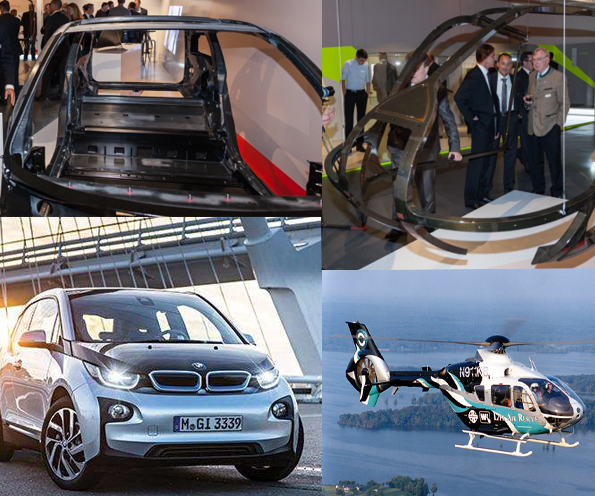
De carrosserieframes van de BMW i3 en i8 zijn zeer vergelijkbaar met die van de Airbus Helicopters EC135.
BRON: Mijlpalen van het toonaangevende cluster – overzicht en toekomstvooruitzichten, MAI Carbon, pp 36-7 (boven), BMW en Airbus-helikopter (onder).
Ondertussen is de Audi A8 achterwand is gemaakt met een cyclustijd van 5 minuten met behulp van RTM en geautomatiseerde plaatsing van droge koolstofvezeltape, op maat gemaakt in lengte en vezeloriëntatie om aan specifieke belastingen te voldoen, en variërend van een basis van 6 lagen (1,5 mm dik) tot 19 lagen (3,7 mm dik) waar lokale wapening is toegevoegd om te voldoen aan hoge puntbelasting. Dit enkele onderdeel levert 33% van de torsiestijfheid van de aandrijfcel bij 50% van het gewicht in vergelijking met een assemblage van drie tot vijf gelaste aluminium onderdelen.
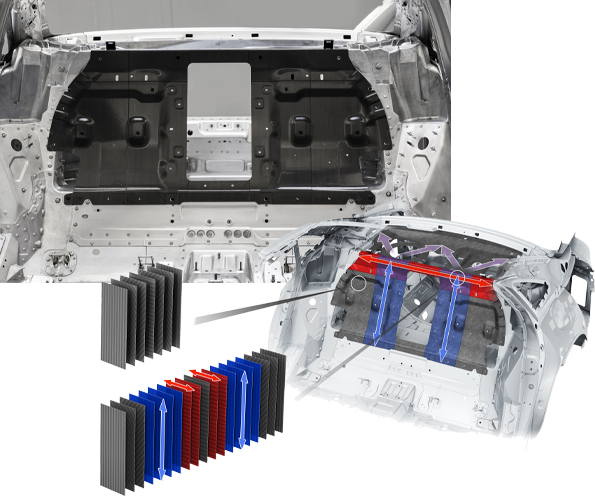
De Audi van 2019 A8 heeft een CFRP-achterwand die in 5 minuten is gemaakt van koolstofvezeltape.BRON:Audi en Voith Composites.
Thermoplasten
Maar deze voorbeelden maken niet eens gebruik van thermoplastische technologie, die de voorkeur geniet als de keuze voor het nieuwe middelgrote vliegtuig (NMA) van Boeing, dat naar verwachting vóór het tweede kwartaal van 2019 wordt aangekondigd. Thermoplastische onderdelen vliegen al sinds de jaren negentig in vliegtuigen, terwijl de ontwikkeling is voortgezet , waarbij Airbus en Europese Tier 1-leveranciers prototypes maken van steeds grotere vleugel- en rompsecties (met geïntegreerde verstijvers), dit jaar opschalen naar volledige rompdemonstraties. Merk op dat thermoplastische composieten ook lassen mogelijk maken, wat verdere mogelijkheden biedt om bevestigingsmiddelen en montage te elimineren.
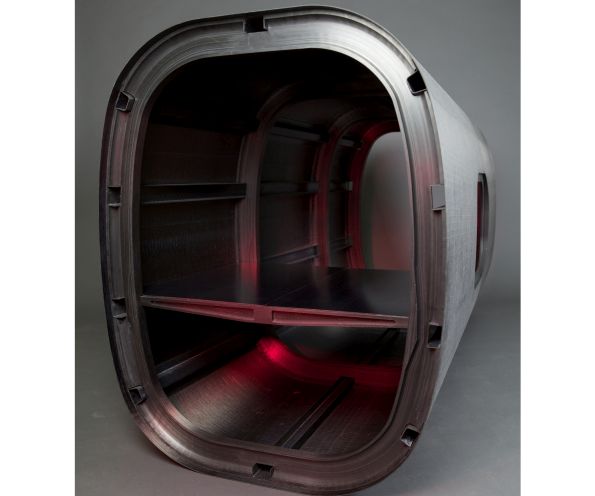
Automated Dynamics, nu onderdeel van Trelleborg Group , produceerde deze full-size, integraal verstijfde CF/PEEK helikopter staartboom in 2012 met behulp van in-situ consolidatie tijdens geautomatiseerde plaatsing van vezels, waardoor lange autoclaafcycli en bevestigingsmiddelen en lijmen werden geëlimineerd.
BRON:geautomatiseerde dynamiek, Trelleborg
De toeleveringsketen voor TPC-materialen en -verwerking is de afgelopen drie jaar snel samengesmolten, waarbij alle grote leveranciers van koolstofvezel nu thermoplastische tapes en overgegoten onderdelen met een lage cyclustijd produceren, gedemonstreerd door meerdere bedrijven voor zowel ruimtevaart- als automobieltoepassingen. Thermoplastisch lassen is ook door meerdere bedrijven gedemonstreerd.
Fragment uit "Overmolding as enabler for composites, aerospace to automotive", interview met Scott King bij composietfabrikant CCP Gransden:
CCP Gransden heeft zijn eenstaps thermovormen en thermoplastische composiet overmolding-technologie verfijnd om lichtgewicht, complexe componenten te produceren met typisch <2 minuten cyclustijden, met behulp van een breed scala aan polymeren en vezels. BRON:CCP Granden
Nieuwste technologie
Maar de technologie is sinds 2014 vooruitgegaan en omvat nu verschillende interessante ontwikkelingen:
Thermoplastische overmolded thermoharders
Het OPTO-Light-project bij AZL Aken demonstreerde overgegoten thermoplastische composiet (TPC) ribben en clips op een koolstofvezel/epoxy samengesteld onderdeel.
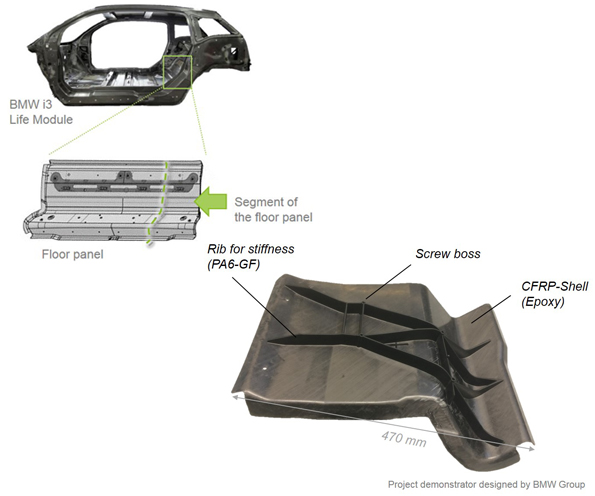
Overmolding + UD-belastingdragende pultrusies
Het MAI Skelett-project heeft overmolded TPC-pultrusies aangetoond in een proces van twee stappen en 75 seconden om een structureel dakelement/voorruitframe te produceren dat alle BMW i3 overtreft. onderdeelvereisten terwijl bevestigingen en clips worden geïntegreerd, evenals het veranderen van crashgedrag van brosse naar ductiele faalmodus voor verhoogde BIW-reststerkte.
Projectpartner SGL Carbon levert nu koolstofvezel met de juiste maatvoering voor oplossingen met één matrix die gebruik maken van de PP- of PA6-familie, inclusief pultrusies, organosheet en overmolding compound, evenals ontwerp- en procesexpertise voor de ontwikkeling van onderdelen, de laatste via hun Lightweight Applications Center (LAC, Meitingen, Duitsland).
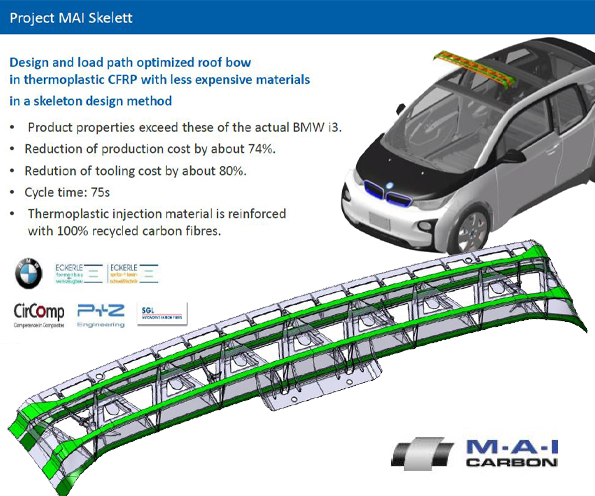
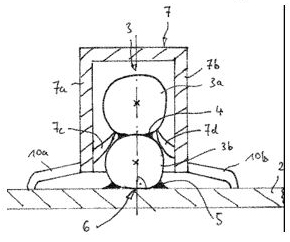
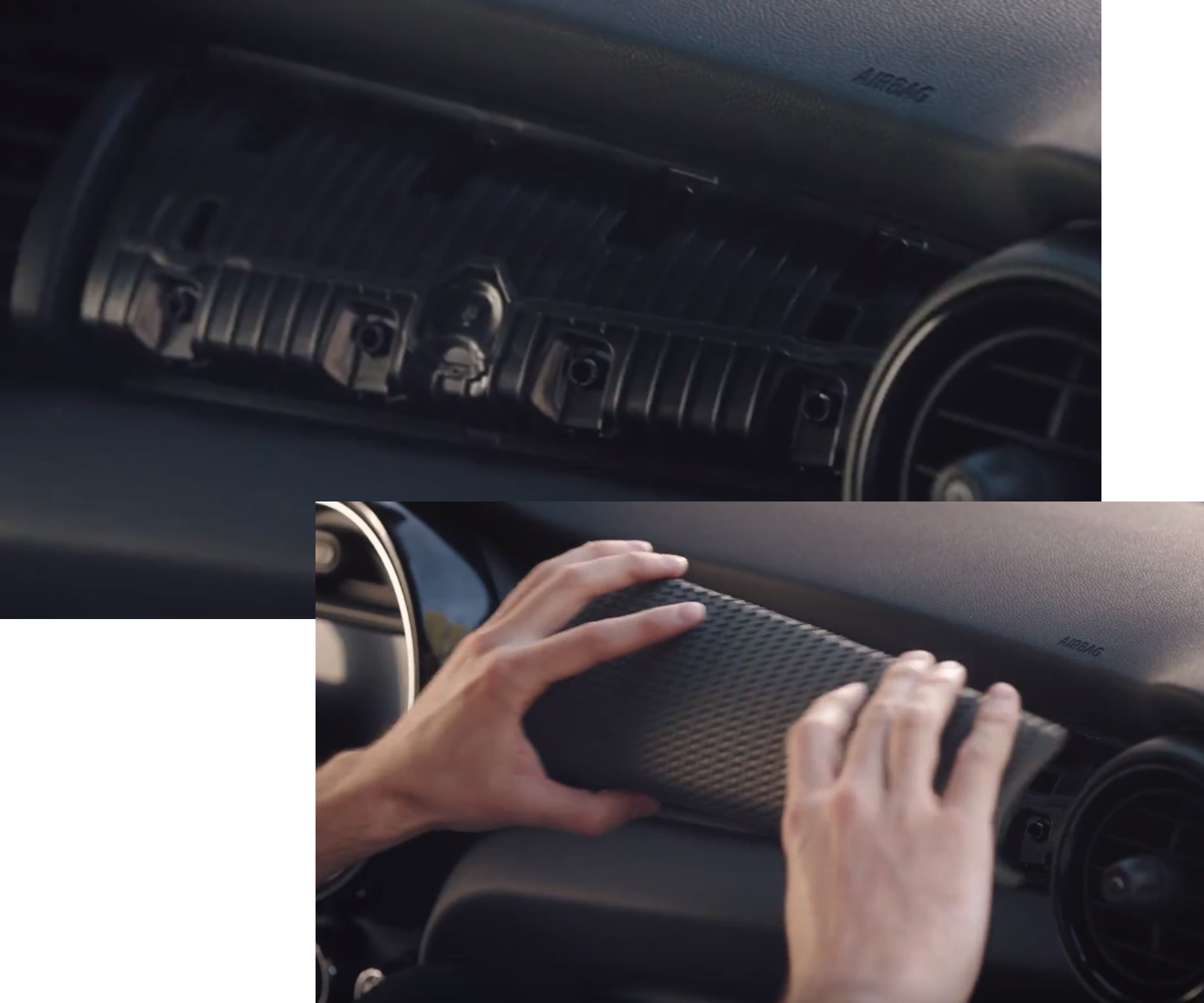
BMW's nieuwe gepatenteerde , zeer nauwkeurig bevestigingssysteem maakt gebruik van spuitgegoten of overgegoten clips (onder) en 3D-geprinte ballen (boven) zonder bevestigingsmiddelen, geboorde gaten of lijm. De onderste afbeeldingen laten zien hoe dit systeem het mogelijk maakt om op maat gemaakte 3D-geprinte interieurbekleding te "klikken" als onderdeel van het MINI Yours Customized-programma van 2019.
BRON:Patent DE 10 2013 214 269 B3 (boven)
https://www.youtube.com/watch?v=1pyxNKw-nf8 (onder)
Terug naar de WIRED artikel en zijn ongeïnformeerde claims:
Het is waar dat deze methode van CFRP-productie al vele jaren wordt gebruikt, maar het is ook waar dat zowel vliegtuig- als autofabrikanten al zijn overgestapt op meer geautomatiseerde, bijna nul afvalmaterialen en processen, evenals thermoplasten met bewezen voordelen in het elimineren van bevestigingsmiddelen, waardoor recycleerbaarheid/gerecycleerde inhoud en herstelbaarheid mogelijk wordt.
Op het einde, de WIRED auteur spreekt zijn hele proefschrift tegen omdat eVTOL-pionier ICON niet alleen van plan is verder te gaan met zijn CFRP-casco, maar ook onderdelen voor grotere vliegtuigen te produceren. Het is duidelijk dat koolstofvezel eVTOLS niet zal aarden, maar in plaats daarvan al een sleutelrol speelt in bedrijven die slimme engineering bevorderen voor een breed scala aan toekomstige voertuigen, zowel in de lucht als op de weg. Het gebruik van de nieuwste technologie is logisch, omdat al deze nieuwe voertuigen toch moeten worden gecertificeerd.
Een belangrijk punt was gemaakt in het artikel van Kyle Clark, CEO van BetaTechnologies:
Blue Force Technologies CEO Scott Bledsoe benadrukte ook het belang van aerodynamica, voortstuwing, styling, structuren en fabricage teams, elk met een gelijke zitplaats aan tafel tijdens elke stap van ontwerp en ontwikkeling.
Maar misschien wel het belangrijkste is om op de hoogte te blijven van waar de fabricage van composieten naartoe gaat en contact te leggen met de vele leveranciers van materialen, apparatuur en technologie die hun expertise willen delen en toekomstige toepassingen willen helpen ontwikkelen. Neem contact met ons op via CompositesWorld want dat is wat we doen:technische, betrouwbare verbindingen en informatie bieden.
Hars
- Koolstofvezel
- 3 redenen waarom fabrikanten van koolstofvezel binnenkort meer zullen doen
- Wat is koolstofvezel?
- De opkomst van koolstofvezelversterkte kunststoffen
- Koolstofvezelversterkte kunststof (CFRP)
- Is koolstofvezel geleidend?
- Fords Last GT wordt een limited edition koolstofvezel supercar
- Vernieuwde vliegtuigcabine van Pagani en Airbus heeft digitaal plafond
- Air Jordan 1 koolstofvezel sneaker is een must-have voor verzamelaars
- Glasvezel versus koolstofvezel
- Recycling van composieten - geen excuses meer